Заходи при П1, П2, і К ремонтах
При поточному ремонті П1 виконуються роботи: Регулювання зазорів в вузлах обладнання і плавності ходу рухомих спорядженій машини; перевірка, підтяжка або заміна сальників, манжетів і ущільнень разйомів з’єднань; дрібний ремонт трубопроводів системи охолодження, змазки, гідравліки, пневматики та інших з заміною зношених вузлів; дрібний ремонт металоконструкції (кожухи, огородження, площадки, сходи, переходи та інші) з заміною окремих елементів; перевірка простукування і підтягуванням болтових з’єднань, крипіжних і фіксуючих деталей; збірка обладнання і опробування на холостому ході, перевірка на шум, нагрів биття і вібрацію у випадках, коли це оговорено технічною документацією; регулювання і насадження механізмів і машин, різноманітні види випробувань.
При поточному ремонті П2 виконують: пропарка скрубера та чистка від залишків; часткова заміна насадок, захисної футеровки корпусу, або кришки газової труби. Заміна з’єднувальної арматури, заміна форсунок. Перевірка фундаментних болтів.
При капітальному ремонті виконують такі операції: Заміна дерев’яно хордових насадок, повна заміна захисної футеровки. Заміна запорної арматури, заміна усіх ущільнень після пропарки проводять зварні роботи по відновленню металоконструкції та інші. Після ремонту пропарка обладнання. Перевірити роботу на холостому ході насоса і двигуна. Провести іспити скрубера.
|
|
Карта змащення, розрахунок мастила на рік
Мастильні матеріали почали застосовувати ще в стародавності, до розвитку нафтопереробної промисловості, змазували вузли тертя рослинними й
тваринними маслами.
У цей час ці масла використаються для виготовлення й додавання в мінеральні масла.
Мінеральні масла виготовляють із нафти шляхом його перегонки.
До сучасних мастильних матеріалів пред'являються наступні вимоги:
1 в'язкість;
2 температура загушення;
3 щільність масла;
4 корозійні властивості;
5 температура спалаху;
6 вспінювання.
Крім зазначених показників ураховують кольори, захід, кількість води, механічних домішок, зольність, сірчаність й ін.
Основні асортименти рідких масел: індустріальне масло, веретенне масло, машинне масло, трансформаторне, турбінне й ін.
Густі (консистентні) змащення одержують шляхом введення в мінеральне масло загущувачів; солі, жирних кислот, мило, парафін, графіт.
Основними асортиментами консистентних масел є: солідол, консталін, циатін, вазелін, змащення індустріальна.
Призначення змащення - скорочення витрати енергії на подолання сил тертя, відвід тепла від вузлів тертя, зменшення зношування тертьових поверхонь, продовження міжремонтного періоду.
|
|
Вибір змащувального матеріалу залежить від умов використання та температури навколишнього середовища.
Визначити кількість мастила:
де: К1=12; К2=353; dn=65мм – діаметр підшипника
Таблиця 2.1. – Карта змащення
Найменування вузла | Найменування мастильних матеріалів | Кількість точок змащення | Спосіб змащування | Періодичність і повна заміна | Кількість мастильного матеріалу |
Підшипник | И-13 Ціанін 203 Літол 24 Ціанін 221 | 2 | Масльонка, шприц | Поповнювати: 1 раз у 5 днів | 5,48кг на рік |
РОЗРАХУНОК ПОТУЖНОСТІ ПРИВОДА, ВИБІР ЕЛЕКТРОДВИГУНА
Q=400м2/год=0,11м3/с – продуктивність насосу;
Н=105м – напор;
n=1450 об/хв. – кількість обертів;
- ККД механізму
Визначення потужності на валу насоса
Приймаємо до установки електродвигун Р=160кВт; n=1450об/хв.
Визначаємо крутний момент на валу насоса:
Визначаємо діаметр вала під колесо з умов міцності на кручення. Матеріал вала Сталь 5 [ ] =20…40Н/мм2 допустиме напруження кручення.
Приймаємо
Визначаємо діаметр ступиці колеса
Приймаємо 130мм
Визначаємо коефіцієнт швидкохідності
При 60…100 приймаємо об’ємний ККД
приймаємо
Визначаємо розрахункову потужність з урахуванням утічки:
|
|
Визначаємо колову швидкість на виході
де: - коефіцієнт колової швидкості при n3=95.
Визначаємо зовнішній діаметр колеса
Приймаємо 445мм
Визначаємо швидкість входу води в колесі
де: Кс=0,14 – коефіцієнт швидкохідності входу при n3=95.
Визначаємо діаметр входу
Приймаємо Д1=204мм
Визначаємо радіальну швидкість колеса
де: =0,11 – коефіцієнт радіальної швидкості при n3=95.
Визначаємо ширину робочого колеса у виході:
- коефіцієнт ширини колеса при n3=95
тоді: =0,06×445=26,7мм
Приймаємо =26мм
Визначаємо ширину робочого колеса на вході:
Так, як радіальна швидкість Сч є величиною для даного рас ходу, то:
Приймаючи числові значення діаметра Д3 отримаємо відповідні значення на bx.
Визначаємо кількість лопаток:
Приймаємо z=8.
Визначаємо кінці вхідної кромки
де:
де: Кн=0,15 – коефіцієнт колової швидкості
Визначаємо діаметри в точках В і Н
Умова dн >dст – виконується dн =dст=90мм
Креслимо удільний профіль колеса
Проводимо вертикальну та горизонтальну осі колеса. Під кутом 3-4 градуси до вертикальної осі проводимо лінію штрихову.
Проводимо лінію паралельно вала на відстані 45мм.
Приймаємо значення Д4 відкладаємо їх на вертикальній осі і через отримані точки проводимо лінії, паралельні осі вала, на які відкладаються відповідні значення ширини. Через отримані точки проводимо плавну криву. Відкладаємо значення діаметрів находимо точки В і Н, проводимо вхідну кромку канатки робочого колеса.
|
|
Дата добавления: 2019-09-02; просмотров: 105; Мы поможем в написании вашей работы! |
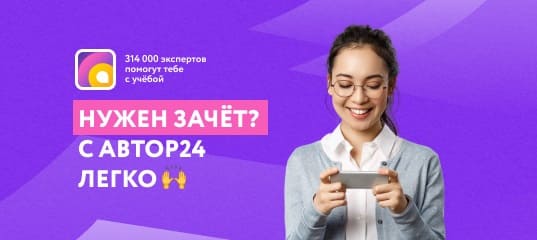
Мы поможем в написании ваших работ!