Підвищення зносостійкості і методи ремонту деталей
Засоби відновлення валів: правка валів, наплавлення шийки, а потім зробити механічну обробку, введення додаткової деталі (втулки), відновлення під ремонтний розмір. Зношені шийки, цапфи, шпоночні канавки звичайно заварюють електрозварюванням з послідовним відпалом і обробкою. Якщо зношування незначне, то їх поновлюють механізацією.
Звичайно цементації піддають деталі з мало вуглецевих сталей, що містять 0,1-0,25% вуглецю. Для виготовлення великогабаритних деталей застосовують сталь, що містить 0,3-0,4% вуглецю.
У якості сталей, які підлягають цементації, знайшли широке застосування мало вуглецевих стали марок 08, 10, 15, 20.
Для високо навантажених деталей, серцевина яких повинна мати високі механічні властивості, а цементований шар підвищеною зносостійкістю, застосовують леговані сталі, серед яких найбільше поширення одержали сталі марок 15Х, 20Х, 12Х2Н4А, 12ХНЗ, 18ХГМ, 18ХГТ й ін.
Деталі на цементацію надходять відразу ж після обробки різанням або майже остаточно механічно оброблені й шліфовані із припуском під остаточне шліфування 0,05 - 0,15 мм.
Цементацію роблять у залізному ящику, що закриває кришкою. Розміри ящика залежать від розмірів деталей, однак не рекомендується вживати ящики більших розмірів, тому що в цьому випадку потрібно значно більше часу на нагрівання до необхідної температури.
Разом з деталями в ящик занурюють матеріал, називаний карбюризатором, тобто утримуючий вуглець. Кращим карбюризатором служить березове деревне вугілля зі шматками величиною 3-7 мм.
|
|
Для інтенсифікації процесу цементації вживають речовини, що активують (вуглекислий барій, соду, поташ, кокс, патоку й ін).
Як карбюризатори можуть бути використані також газ і рідина, тоді процес зветься газової або рідинної цементації.
Підлягаючої цементації поверхня деталі повинна бути ретельно втрамбована з усіх боків карбюризатором, тому відстань між деталлю й стінкою ящика, а також між окремими деталями в одному ящику не повинне бути менше 25 мм, що забезпечує нормальне диффундировання вуглецю в поверхню деталі.
Перед установкою в піч ящик закривають і герметизируют (обмазують кришку глиною), щоб перепинити доступ повітря, і доводять температуру печі до 700-720° С. Після цього повільно підвищують температуру в печі до 880-900° С, тобто до температури цементації. При цій температурі ящик витримують певний час. Уважають, що на нагрівання кожних 100 мм по глибині ящика потрібно 2 ч. Час же цементації залежить від заданої товщини цементованого шару й збільшується зі збільшенням останнього. Орієнтовно можна вважати, що на кожну 0,1 мм цементованого шару потрібно 1 ч.
|
|
Для визначення глибини проникнення вуглецю користуються «свідками». Так називають прутки товщиною 5-6 мм, виготовлені з того ж матеріалу, що й деталь, і вставляють у ящик. Пруток-свідок витягають, гартують, розламують і визначають глибину цементації. Якщо вона відповідає заданої, то процес цементації вважають закінченим. Ящик виймають із печі й прохолоджують. Піддані цементації деталі повинні ще пройти й термічну обробку, що полягає в нормалізації, загартуванні й відпустці. При цьому повинні бути дотримані певні умови, порушення яких може привести або до деформації деталі, або до часткової втрати властивостей цементованої поверхні. При застосуванні легованих деталей деформація деталей зменшується, їх піддають загартуванню не у воді, а в маслі.
У багатьох випадках цементації піддають не всю деталь, а окремі її ділянки, тоді на місця, не підмети зміцненню, наносять електролітичним способом тонкий шар міді (0,03 - 0,04 мм). У деяких випадках застосовують спеціальні обмазки або залишають на деталях припуск, видаляє згодом.
При зношені важелів гальм, може збільшитись діаметр в результаті тертя шарнірів та осей. Важелі знімають та відновлюють розміри отворів, а також використовують металізацію та наплавлення бабітом.
|
|
Дифузійна металізація ділиться на: алітування, хромування, силіцювання.
Алітування уявляє собою поверхневе насичення деталей алюмінієм з утворенням твердого розчину алюмінію в залізі. Воно застосовується переважно до деталей, що працюють при високих температурах, так як значно підвищує стійкість сталі при високій температурі (1000˚).
В радянському союзі розроблений прогресуючий спосіб алітування, що полягає в тому, що алюміній спочатку наносять на виріб розпиленням стиснутого повітря. Далі, нанесений шар алюмінію захищають жаростійкою обмазкою і проводять дифузійний відпал виробу при температурі 920˚С на протязі 3 годин. В процесі відпалу поверхневий шар виробу насичується алюмінієм на глибину в середньому 0,5мм. Попередні методи алітування (в розплавленому алюмінію, в порошкоподібних сумішах) мають суттєві недоліки в порівнянні з приведеним.
Дифузійне хромування проводять в порошкових сумішах, що складаються із ферохрому і шамоту, змочених соляною кислотою або в газовому середовищі при розчепленні парів хлориду хрому. Хромуванню підлягають в основному сталі з вмістом вуглецю не більше 0,2%. Хромований шар мало вуглецевої сталі незначно підвищує твердість, але володіє великою в’язкістю, що дозволяє хромовані деталі сплющувати чи прокатувати. Хромовані деталі мають хорошу корозійну стійкість в деяких агресивних середовищах (азотній кислоті, морській воді). Це дозволяє замінити ними деталі із дефіцитної високо хромової сталі.
|
|
Силіціювання – насичення поверхневого шару стальних виробів кремнієм, забезпечуючи підвищення стійкості проти корозії і ерозії в морській воді, азотній, сірчаній і соляній кислоті. Застосовується до деталей обладнання хімічної промисловості. Силіцьований шар уявляє собою твердий розчин кремнію в α-залізі. Існує силіціювання в порошкоподібних сумішах феросиліціювання, а також газове силіціювання в середовищі хлориду кремнію.
Осі можуть мати щілини, вгнутість закручування, можна заварити електродом з якісною обмазкою, після цього це місце обпалити та проточити до необхідного розміру, підвищити зносостійкість поверхнею загартування з нагрівом СВЧ та газовим вогнем, що збільшує витривалість в 2 рази та зміцнює поверхню. Ціль загартування – покращення властивостей. Загартування засноване на перекристалізації сталі при нагріві до температурі вище критичної; після достатньої витримки при цій температурі для завершення загартування потрібне швидке охолодження. Таким шляхом попереджують перетворення аустеніту в перліт.
Загартована сталь має не урівноважену структуру мартенситу, троститу чи сорбіту.
Зазвичай при загартуванні сталь різко охолоджують на мартенсит.д.ля пом’якшення дії загартування проводять відпуск.
При поверхневому загартуванні вище критичної температури нагрівається тільки тонкий шар деталі, а в середині метал майже не нагрівається. Після загартування деталі мають твердий поверхневий шар і в’язку серцевину.
Загартування за допомогою газової горілки відбувається так: Киснево-ацетиленове полум’я газової горілки з температурою біля 3200˚ направляється на поверхню деталі і швидко нагріває її до температури вище критичної. Вслід за горілкою із трубки на поверхню деталі направляється струйка води, загартовуючи поверхневий шар. Цей спосіб з успіхом застосовується для загартування поверхневого шару зубів великих шестерень, що підлягають швидкому зносу.
Дата добавления: 2019-09-02; просмотров: 102; Мы поможем в написании вашей работы! |
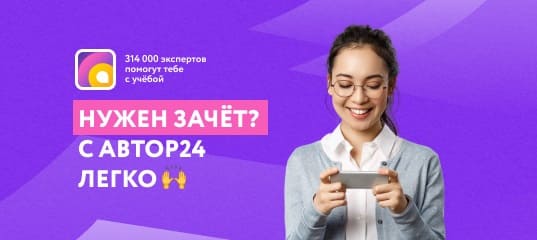
Мы поможем в написании ваших работ!