Пример очистных сооружений для очистки сточных промышленных газов.
ЦИКЛОН
Широкое распространение получили обеспыливающие устройства, в которых для осаждения частиц используется центробежная сила. В современных усовершенствованных конструкциях циклонов возможно достаточно эффективно улавливать твердые или капельные частицы размером от 5 мкм и больше. Улавливание пыли в циклонах основано на использовании инерции частиц. Циклон относится к устройствам грубой (предварительной очистки) газового потока, с КПД = 0,6 – 0,9.
Рисунок Е.1. Общий вид циклона НИИОгаз
Общая схема циклона представлена на рис. 1.1. Циклон состоит из конической части 1, цилиндрической части 2, выхлопной трубы 3, винтообразной крышки 4, газохода очищенных газов 5, улитки для вывода газа 6 (возможно исполнение циклонов без улитки), входного патрубка 7, пылевыпускного отверстия 8, бункера 9, пылевого затвора 10. Газовый поток со взвешенными в нем твердыми частицами вводится с большой скоростью по касательной к стенке цилиндрической части циклона, где делает несколько спиральных витков в сторону пылеотводящего отверстия, 6а затем по внутренней спирали движется к выхлопной трубе. При входе в циклон взвешенные в потоке частицы по инерции движутся по своим первоначальным траекториям, а затем под воздействием аэродинамических сил их траектории искривляются. Те из частиц, масса которых достаточно велика, успевают достичь стенок циклона, т.е. отделяются от потока. Под влиянием силы тяжести и увлекающего действия осевого движения отделившиеся частицы опускаются и через пылевыпускное отверстие поступают в бункер, где они оседают.
|
|
Рисунок Е.2. Аэродинамические схемы циклонов:
На рис. 1.2 показаны разновидности циклонов одного назначения. Каждый циклон имеет свои конструктивные и эксплуатационные особенности, которые необходимо учитывать при выборе пылеулавливающего устройства. Циклоны СИОТ не имеют цилиндрической части корпуса, а выхлопная труба введена непосредственно в конус. Особенностями этих циклонов являют- ся также треугольное сечение входного патрубка и небольшая высота. 78 Широко распространенный ранее циклон ЛИОТ по эффективности уступа- ет другим рассмотренным циклонам. Характерная особенность циклонов ВЦНИИОТа – расширяющаяся коническая часть с внутренним дополнительным конусом, что уменьшает абразивный износ нижней части конуса. Это достигается в результате того, что за цилиндрической частью устраивается не традиционная сужающаяся коническая, а расширяющаяся в виде конфузора часть. Кроме перечисленных применяют циклоны «Матрешка», называемые так потому, что внутри циклона расположен дополнительный циклон меньшего размера. Циклон "Матрешка" по эффективности, металлоемкости и сложности конструкции также уступает другим циклонам. В связи с многообразием существующих циклонов были проведены их сравнительные испытания по единой методике, разработанной во ВНИИОТе. В результате исследований установлено, что из цилиндрических циклонов НИИОгаз наиболее эффективен циклон ЦН-11, поэтому этот циклон включен в унифицированный ряд для изготовления. Циклон удобен для компоновки в группы, имеет небольшие размеры. Циклон «Матрешка» наименее эффективен для улавливания пыли, кроме того, он наиболее металлоемкий и сложный в изготовлении. В промышленности строительных материалов применяют циклоны различных типов: НИИОгаз, ЦКТИ, ЛИОТ, СИОТ и ВЦНИИОТ. В настоящее время наибольшее распространение получили циклоны НИИОГАЗ, которые могут быть цилиндрическими и коническими. К цилиндрическим циклонам НИИОГАЗ относятся аппараты типа ЦН-11, ЦН-15, ЦН-15У и ЦН-24. Их отличительной особенностью является удлиненная цилиндрическая часть корпуса, расположение крышки входного патрубка соответственно под углами 11, 15 и 24° к горизонтали. Циклоны ЦН-15У имеют несколько меньшую высоту и более низкие технико-экономические показатели по сравнению с другими аппаратами типа ЦН. К коническим циклонам относится циклон СИОТ и циклоны НИИОгаз типа СДК-ЦН-33, СК-ЦН-34 и СК-ЦН-34М. Они отличаются от циклонов типа9 ЦН длиной конической части, наличием спирального входного патрубка и малым отношением диаметров выхлопной трубы и корпуса циклона (соответственно 0,334, 0,340 и 0,22). Циклон СК-ЦН-34М применяют для улавливания пылей с высокими абразивными свойствами или слипаемостыо. Потери давления в этом циклоне значительно выше, чем в других конических циклонах. Циклон СЦН-40 является цилиндро-коническим циклоном НИИОгаз и обладает более высокой степенью очистки по сравнению с известными циклона- ми типа ЦН-15, ЦН-11, СК-ЦН-34, УЦ-38. Вынос пыли из циклона СЦН-40 в 2,5 раза меньше, чем из циклона ЦН-15 и в 1,5 раза меньше по сравнению с ци- клонами СК-ЦН-34 и УЦ-38 при равных энергозатратах. Циклоны СЦН-40 имеют относительно высокую скорость газа в пристенной зоне (до 24 м/с), по- этому при улавливании липкой пыли менее подвержены забиванию конуса ци- клона. Абразивный износ циклона СЦН-40 при одинаковых производительности и сопротивлении в 1,25 раза ниже, чем у циклона ЦН-15. Длина цилиндрической и конической части циклона равна 1,6 диаметра. В последнее время длину конической части циклона принимают равной 2,0 диаметра. Циклоны СЦН-40 целесообразно устанавливать в тех случаях, когда требуется повышенная степень очистки газов и гидравлическое сопротивление не лимитируется. Например, степень очистки воздуха в циклоне диаметром 1,0 м от кварцевой пыли с медианным размером частиц 10 мкм, плотностью 2,6 г/см3 при плановой скорости 1,6 м/с и температуре 20 С составляет 93 % при начальной запыленности до 1000 г/м 3 . Цилиндрические циклоны относятся к высокопроизводительным, а конические – к высокоэффективным аппаратам. Диаметр цилиндрических циклонов обычно не превышает 2000 мм, а диаметр цилиндрической части конических - 3000 мм [3]. Циклоны изготовляют правого и левого вращения газового потока. Согласно ГОСТ 9617-67 для циклонов принят следующий ряд диаметров: 200, 300, 400, 500, 600, 700, 800, 900, 1000, 1200, 1400, 1600, 1800, 2000, 2400 и 3000 мм
|
|
|
|
|
|
Скруббер Вентури.
Очистка газов от примесей с помощью скрубберов относится к мокрым способам очистки. Этот способ основан на промывке газа жидкостью (обычно водой) при максимально развитой поверхности контакта жидкости с частицами аэрозоля и возможно более интенсивном перемешивании очищаемого газа с жидкостью. Данный метод позволяет удалить из газа частицы пыли, дыма, тумана и аэрозолей (обычно нежелательные или вредные) практически любых размеров. Аппараты мокрой очистки газов, или скрубберы, широко распространены, так как отличаются высокой эффективностью очистки от частиц мелкодисперсной пыли с размером более 0.3 - 1.0 мкм, а также возможностью очистки от пыли горячих и взрывоопасных газов. В практике используют два способа захвата частиц пыли жидкостью:
1. -каплями жидкости;
2. -пленкой жидкости.
Для реализации процесса очистки газа каплями жидкости запыленный газ промывают диспергированной жидкостью. Частицы пыли захватываются каплями жидкости и выводятся из газового потока. При движении капли в пространстве, заполненном дымовым газом, осаждение пыли на капле происходит в основном вследствие кинематической коагуляции, обусловленной движением капель жидкости и частиц пыли с различными скоростями.количество уловленной пыли пропорционально относительной скорости движения капли, расходу орошающей жидкости и концентрации пыли в газе и обратно пропорционально диаметру капель жидкости.
Скрубберы Вентури предназначены для очистки газов от мелкодисперсной пыли, их охлаждения и увлажнения. При использовании в качестве орошающей жидкости химических реагентов скруббер Вентури может быть использован для улавливания газообразных примесей.[1]
Скрубберы Вентури состоит из(рис.1):
- трубы Вентури (т.в.);
- каплеуловителя.
Рисунок Е. Схема строения скруббера Вентури.
Структура скуббера
1. входной патрубок;
2. конфузор;
3. орошающее устройство;
4. горловина;
5. диффузор;
6. корпус каплеуловителя;
7. гидрозатвор.
8. выходной патрубок.
Работа скруббера Вентури основана на дроблении воды турбулентным газовым потоком, захвате каплями воды частиц пыли, последующей их коагуляцции и осаждении в каплеуловителе инерционного типа. В конфузоре осуществляется увеличение скорости газа, впрыск и дробление жидкости. В горловине за счет разницы скоростей капли и частицы пыли последние оседают на каплях жидкости. В диффузоре за счет снижения скорости восстанавливается часть давления, затраченного на создание высокой скорости газа в горловине. В каплеуловителе под действием центробежных сил осуществляется сепарация капель жидкости, осаждение их на стенку и отвод жидкости в виде шлама через гидрозатвор.
Входящий поток газа поступает в сужающуюся секцию, и по мере того, как площадь поперечного сечения потока уменьшается, скорость газа увеличивается (согласно Уравнению Бернулли). В то же время, сбоку по патрубкам в сужающуюся секцию (или в горловину) поступает жидкость.
Поскольку газ вынужден двигаться с очень большими скоростями в небольшой горловине, то здесь наблюдается большая турбулентность потока газа. Эта турбулентность разбивает поток жидкости на очень большое количество очень мелких капель. Пыль, содержащаяся в газе, оседает на поверхности этих капель. Покидая горловину, газ, перемешанный с облаком мелких капель жидкости, переходит в расширяющуюся секцию, где скорость газа уменьшается, турбулентность снижается и капли собираются в более крупные. На выходе из скруббера капли жидкости с адсорбированными на них частицами отделяются от потока газа.
Изменение скорости газа, капель и давления по длине трубы Вентури показано на графике:
Рисунок Е. Изменение скорости газа, капель и давления по длине трубы
Вентури
За счет сил аэродинамического сопротивления капли одновременно с дроблением получают значительное ускорение и в конце горловины приобретают скорость, близкую к скорости газового потока. В диффузоре скорости капель и газа падают, причем, вследствие сил инерции скорость капель больше скорости газа. Процесс очистки более интенсивно идет в конце конфузора и в начале горловины, где разность скоростей щк - щг наиболее значительна.
Параметры, достигаемые в трубе Вентури:
· степень очистки газа - 96-99%:;
· максимальная запыленность очищаемого газа - до 100 г/м3;
· размер частиц улавливаемой пыли - до 0,2 - 0,1 мкм;
· скорость газа в горловине - щг =100 - 170 м/с;
· удельный расход воды - 0,5 - 1,5 л/м3;
· перепад давления на трубе Вентури - до 20-30кПа (200-2000 мм в ст);
Высокая интенсивность процессов дробления и коагуляции капель, тепло и массообмена между каплями, газом и частицами пыли, нестационарность и неодномерность процесса не позволяет до настоящего времени создать надежную теорию расчета этого аппарата. Практические расчеты ведутся с использованием методов теории подобия и эмпирических зависимостей.
Скрубберы Вентури обеспечивают высокую эффективность очистки аэрозолей (до 99%) со средним размером частиц 1 - 2 мкм при начальной концентрации примесей до 100 г/м3.
Конструкции труб Вентури могут различаться:
1. по конфигурации поперечного сечения
- круглые ( при малых объемах очищаемых газов);
- щелевые;
- кольцевые;
При больших объемах газов применяют батарейные или групповые компоновки скрубберов Вентури.
2. по площади поперечного сечения:
- нерегулируемые;
- регулируемые;
Промышленно применяются две конструкции:
a).поворотные заслонки для регулирования щелевого сечения;
b).перемещение вдоль оси обтекателя для регулирования кольцевого сечения.
3. по величине гидравлического сопротивления:
- высоконапорные ( для очистки газов от субмикронных пылей, ДР до 30000Па);
- низконапорные (для очистки газов от крупнодисперсной пыли, охлаждения и увлажнения газов, ДР = 2000 - 5000 Па).
4. по способу подвода жидкости:
- центральный (форсуночный) подвод жидкости в конфузор;
- периферийное орошение в конфузоре или горловине;
- пленочное орошение;
- бесфорсуночное орошение (подвод жидкости за счет энергии газового потока).
С аэродинамической точки зрения оптимальной является конструкция трубы Вентури со следующими отношениями размеров ее элементов:
- угол сужения конфузора-б = 25 ч 28о;
- угол раскрытия диффузора - в = 6 ч 7о;
- длина горловины - lг = 0,15 ч 3 dг .
Варианты регулирования площади сечения
а) Регулирование кольцевого сечения перемещением обтекателя по оси;
б) Регулирование щелевого сечения поворотом заслонок.
Рисунок Е. Схема скрубберов Вентури с различным регулированием площади сечения
Способы подвода жидкости (рис.4):
а)Центральный форсуночный подвод
б)Периферийное орошение
в)Пленочное орошение
г)Бесфорсуночное орошение
Рисунок Е. Схемы скрубберов Вентури с различным подводом жидкостей
Скрубберы с трубами Вентури на сегодняшний день во всём производственно-технологическом секторе Мира являются наилучшими санитарными пылеочистными аппаратами комплексной газоочистки.
Специальная конструкция труб Вентури позволяет успешно применять их для очистки дымовых газов от пыли, содержащих соли жесткости Ca, Mg и др., горячих сухих дымов способных вызывать отложения (инкрустации) в полых скрубберах, сероочистки. Прекрасно справляются с обеспыливанием горячих сухих газов без предварительного их охлаждения. Возможна очистка газов с высоким начальным пылесодержанием тонких фракций без опасения отложений в корпусе, засорений проточной части.
Скруббер Вентури - наилучший санитарный аппарат для очистки газов и дымов от взвешенных фракций: пыль, туман, возгоны, аэрозоли, пар смол, пары кислот и подобного. Скруббер Вентури применяется в различных отраслях промышленности: в черной и цветной металлургии, химической и нефтяной промышленности, промышленности строительных материалов, энергетике.
Основной проблемой эксплуатации данного вида технических устройств является абразивный износ стенок скруббера, возникающий вследствие высоких скоростей газа, которые в горловине могут достигать значений 430 км/ч. Твёрдые частички или капли жидкости, двигаясь с такой скоростью и соударяясь со стенками, вызывают быструю эрозию стенок. Износ может быть уменьшен, если стенки горловины изнутри покрыть карбидом кремния, для удобства сделав внутреннюю втулку из этого вещества сменной. Износ может также происходить в колене в нижней части скруббера. Для уменьшения износа здесь, дно колена, ведущего в разделитель, заполняют слоем той же жидкости, которую подают в скруббер в верхней части. Частички и капельки жидкости попадают в этот слой, и ударные нагрузки на стенки уменьшаются. Также недостаток этого способа газоочистки - образование больших объёмов шлама.
Однако мокрые пылеуловители имеют ряд преимуществ перед аппаратами других типов:
отличаются сравнительно небольшой стоимостью и более высокой эффективностью улавливания взвешенных частиц по сравнению с сухими механическими пылеуловителями;
могут быть применены для очистки газов от частиц размером до 1 мкм
могут не только успешно конкурировать с такими высокоэффективными пылеуловителями, как рукавные фильтры и электрофильтры, но и использоваться в тех случаях, когда эти аппараты обычно не применяются, например, при высокой температуре и повышенной влажности газов, при опасности возгорания и взрывов очищенных газов, в качестве теплообменников смешения.
Перечисленные преимущества аппаратов мокрого пылеулавливания позволяют широко их применять в системах пылеочистки сушильных установок, особенно во вторых ступенях очистки.
Однако метод мокрогообеспыливания имеет и ряд недостатков:
большие энергозатраты;
улавливаемый продукт выделяется в виде шлама, что связано с необходимостью обработки сточных вод и, следовательно, с подорожанием процесса очистки;
при охлаждении очищаемых газов, а также при механическом уносе из газоочистного аппарата газовым потоком капель жидкости пыль может осаждаться в газопроводах, системах вентиляции, дымососах. Кроме того, брызгоуносприводит к безвозвратным потерям орошающей жидкости в случае очистки агрессивных газов аппаратуру и коммуникации не обходимо защищать антикоррозионными материалами.
Сравнение мокрой очистки с сухой показывает, что мокрая очистка имеет меньшую стоимость (без шламового хозяйства) и, как правило, является более эффективной, чем сухая. Большинство мокрых пылеуловителей может применяться для улавливания самых мелких частиц, даже менее 1 мкм.
Мокрые пылеуловители по эффективности и другим показателям не уступают рукавным фильтрам и электрофильтрам, а по ряду показателей их превосходят (возможность очистки газов с высокой температурой и по вышенной влажностью, безопасность при улавливании пожаро- и взрыво опасных пылей).
Электрофильтр.
Электрофильтрование находит все большее применение для очистки воздуха от пыли. К преимуществам этого вида очистки относятся: возможность получения высокой степени очистки (до 99% и более), небольшое гидравлическое сопротивление (100 - 300 Па); независимость работы от давления газов; незначительный расход электроэнергии (0,1 - 0,8 кВт ч на 1000 м3 газа вместо 2 для других пылеуловителей); возможность очистки газов при высоких температурах и их агрессивности; широкий диапазон концентрации пыли (от долей грамма на 1м3 до 50 г/м3); полная автоматизация работы.
Метод основан на ударной ионизации газа в зоне коронирующего разряда. При этом происходит передача заряда ионов частицам примесей и осаждение этих частиц на осадительных и коронирующих электродах.
Принципиальная схема электрофильтра показана на рис. 1. Коронирующий электрод 2 выполняется в виде прутков или узких полос с иглами. Он изолирован от корпуса и земли, к нему подводятся от источника питания (выпрямителя) 1 отрицательный заряд высокого напряжения (20 - 90 кВ). Осадительный электрод 3 выполнен в виде трубы (или пластинки тонколистового материала), которая заземляется. В зазоре между коронирующим 2 и осадительным 3 электродами создается электрическое поле убывающей напряженности с силовыми линиями, направленными от осадительного к коронирующему электроду или наоборот. Напряжение к электродам подается от выпрямителя.
Изменение силы тока между электродами по мере роста напряжения показано на рис. 2.
По достижении напряжения на электродах критической величины (uкр) возникает коронирующий разряд. Процесс электростатического осаждения твердой частицы состоит из четырех основных стадий: ионизации газа, зарядки частицы пыли, перемещения частицы в электрическом поле и осаждения ее на электроде. Ионизация газа происходит за счет высокого напряжения, подводимого от источника электропитания к коронирующему электроду. Осадительные электроды заряжаются положительно.
![]() | ![]() |
Рисунок Е. Схема работы электрофильтра: 1- подвод тока высокого напряжения; 2- коронирующий электрод; 3-осадительный электрод; 4- заземление; 5- бункер для сбора пыли. | Рис. 2. Зависимость силы тока от напряжения между электродами |
Работа электрофильтра осуществляется следующим образом. Известно, что любой загрязненный воздух, поступающий в электрофильтр, всегда оказывается частично ионизированным за счет различных внешних воздействий (рентгеновских и космических лучей, радиоактивных излучений, трения, нагрева газа и др.). Поэтому он обладает проводимостью, что обусловливает возможность возникновения силы тока. Последняя зависит от числа ионов и напряжения между электродами. При увеличении напряжения в движение между электродами вовлекается все большее число ионов и сила тока растет до тех пор, пока в движении не окажутся все ионы, имеющиеся в газе. При этом сила тока становится постоянной (ток насыщения), несмотря на дальнейший рост напряжения. При некотором достаточно большом напряжении движущиеся ионы и электроны настолько ускоряются, что, сталкиваются с молекулами газа, ионизируют их, превращая нейтральные молекулы в положительные ионы и электроны. Образовавшиеся новые ионы и электроны ускоряются электрическим полем и в свою очередь ионизируют новые молекулы газа. То есть развивается ударная ионизация газа, возникает коронный разряд (ограниченный, как показано выше, на некоторую часть межэлектродного пространства). Он имеет место и у коронируюшего и у осалительного электродов, но коронирующий электрод имеет значительно большую внешнюю зону.
Аэрозольные частицы (пылинки), поступающие в зону между коронирующим и осадительным электродами, адсорбируют на своей поверхности ионы, приобретая электрический заряд и получая ускорение, направленное в сторону электрода с зарядом противоположного знака.
Процесс зарядки частиц зависит от подвижности ионов, траектории движения и времени пребывания частиц в зоне коронирующего заряда. Известно, что в воздухе и дымовых газах подвижность отрицательных ионов выше, чем положительных, поэтому электрофильтры обычно делают с короной отрицательной полярности. Время зарядки аэрозольных частиц невелико и измеряется долями секунды.
Движение заряженных частиц к осадительному электроду происходит под действием: аэродинамических сил, силы взаимодействия электрического поля и заряда частиц, силы тяжести, силы давления электрического ветра.
При проектировании электрофильтров влиянием силы тяжести и электрического ветра пренебрегают.
Аэродинамические силы вызывают движение частиц по направлению движения газа со скоростью, близкой к скорости газа (0,5...2 м/с).
Сила взаимодействия заряженных частиц с электрическим полем является основной силой, вызывающей движение частиц к осадительному электроду.
Для процесса осаждения пыли на электродах весьма важно электрическое сопротивление слоев пыли. По его значению различают пыли с удельным сопротивлением:
- пыли с малым удельным сопротивлением (менее 10 Ом·м), которые при соприкосновении с электродом теряют свой заряд и приобретают заряд, знак которого соответствует знаку электрода, после чего между частицей и электродом возникает сила отталкивания, под действием которой частица стремится вернуться в газовый поток;
- пыли с удельным электрическим сопротивлением от 10 до 10 Ом·м, которые хорошо осаждаются на электродах и легко удаляются встряхиванием;
- пыли с удельным электрическим сопротивлением более 10 Ом·м, которые с трудом улавливаются в электрофильтрах, так как на электродах частицы таких пылей разряжаются медленно, что в значительной степени препятствует осаждению новых частиц. В реальных условиях удельное сопротивление пыли снижают увлажнением или химическим кондиционированием газа.
Основная масса пыли осаждается на положительном осадительном электроде, так как коронирующий электрод имеет значительно большую внешнюю зону и основная масса частиц приобретает отрицательный заряд.
Большое значение для бесперебойной работы электрофильтра имеет система удаления осажденной пыли из аппарата. В сухих электрофильтрах для очистки поверхности электродов от пыли используют механизмы встряхивания ударно-молоткового типа. Пыль ссыпается в сборные бункера 5 (см. рис. 1), откуда выводится в сухом виде или в виде пульпы. В мокрых электрофильтрах пыль с поверхностей электродов смывается водой вместе с уловленными каплями. Шлам удаляют из нижней части аппарата.
Повышение эффективности очистки газов, в электрофильтрах достигается лишь в том случае, когда осевшая на электродах зола при их встряхиваниий будет падать в бункер в виде относительно крупных конгломератов, состоящих из множества слипшихся под действием сил адгезии частиц. Для этого надо выбирать временные интервалы между импульсами (часто он назначается равным 3 мин)
Приложение Ж
Дата добавления: 2019-07-15; просмотров: 382; Мы поможем в написании вашей работы! |
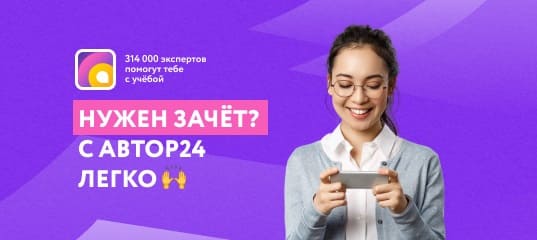
Мы поможем в написании ваших работ!