Проверка выбранного режима по прочности механизма подачи станка и мощности станка
Табличный метод расчета режима резания при точении
Рассчитать наивыгоднейшие режимы резания при точении согласно рисунка 2.1, a [1] и табл. 2.1, В-1[1] обработка без охлаждения.
Рисунок 1.1 (2.1, г [1])- Эскизы обработки
Таблица 1.1 -Исходные данные на токарную операцию
Обраб. матер. | σв, МПа | D, мм | d, мм | L, мм | l, мм | Шерохов. обработ. поверхности, мкм | Модель станка | Креплен. загот. | |
R а | Rz | ||||||||
Сталь 5 | 400 | 70 | 65 | 250 | 200 | 1,25 | 6,3 | 16К20 | Патрон-центр |
Выбор марки инструментального материала, конструкции и геометрии инструмента
Обрабатываемый материал Сталь 5 – сталь углеродистая обыкновенного качества (группа А) [2]. В качестве инструмента принимаем стандартный проходной отогнутый левый резец с пластиной из твердого сплава Т15К6 [1 табл. П.1.3 и табл. П.2.1] с геометрией режущей части: φ=45º; φ1=45º; α=10º; γ=10º; λ=0º; r=0,5 мм. Сечение державки Н В= 16
10 мм [1табл. П.2.1].
1.2 Выбор глубины резания t и числа проходов i
Припуск на обработку согласно данных задания
При чистовой обработке < 10 припуск
мм следует снимать за один проход, т.е.
. Если же припуск более 2 мм, то обработку производят за два прохода.
Для получения шероховатости Ra=1,25; Rz =6,3 мкм делаем два прохода: получистовой с глубиной резанья t1= Δ=1,7 мм и окончательный чистовой проход глубиной резанья t2= Δ=0,8 мм.
Выбор подачи
Подача, допустимая прочностью пластины твердого сплава [1табл. П.3.1], s=2,6 мм/об.
Подача, допустимая шероховатостью обработанной поверхности [1табл. П.3.4], соответственно до s=0,13 мм/об. Для данной стали с σв = 400 МПа значения подач умножать на коэффициент К s = 0,4; s=0,13∙0,4=0,052 мм/об
Величина подачи уточняется по станку; берется ближайшая меньшая подача. Для нашего станка 16К20: sкор = 0,05 мм/об
1.4 Расчет скорости резания V
Все коэффициенты для получистовой и чистового прохода будут браться из одной и той же таблицы.
Скорость резания , м/мин, при наружном продольном и поперечном точении и растачивании по формуле:
. (1.1)
Среднее значение стойкости Т при одноинструментальной обработке 30–60 мин. Т=60 мин.
Значения коэффициента С V показателей степени х, у и m [1табл. П.3.12]: С V =350; x=0,15; т=0,2; у=0,2.
Коэффициент , где значения коэффициентов [1табл. П.3.14–П. 3.19]:
КМV= (1.2)
Значения коэффициента Кги показатели степени nV в формуле [1табл. П.3.15]
КМV= =1,88
КМV=1,88; КПV=1; КИV=1,15;
К V = 1,88·1,0·1,15 = 2,16
Скорость резания при получистовом переходе 560,441 м/мин.
Скорость резания при чистовом переходе 627,529 м/мин.
Число оборотов шпинделя, об/мин,по формуле:
, (1.3)
где D – диаметр обрабатываемой поверхности, мм.
Число оборотов шпинделя уточняется по станку, и рассчитывается уточненная скорость резания.
Для получистового перехода
2638 об/мин.
Для чистового перехода
3073 об/мин.
Число оборотов шпинделя уточняется по станку [1табл. П.7.1]. Так как для токарно-винторезного станка 16К20 максимальное число оборотов 1600, принимаем для получистового и чистового перехода п=1600 об/мин , и рассчитывается уточненная скорость резания.
Действительная скорость резания для получистового перехода:
=339,8 м/мин.
Действительная скорость резания для чистового перехода:
=326,7 м/мин.
Проверка выбранного режима по прочности механизма подачи станка и мощности станка
Проверку будем проводить только для получистового перехода, более нагруженного по сравнению с чистовым.
При этом должны обеспечиваться неравенства и
. Для этого необходимо подсчитать составляющие сил резания Ру и Р z, Н, которые рассчитываются по формуле:
Px,у,z = .
, (1.4)
Постоянная Ср и показатели степени х, y , п [1табл. П.3.21].
Для тангенциальной составляющей Pz:
Ср =300; п=-0,15; х=1; у=0,75.
Для осевой составляющей Px:
Ср =339; п=-0,4; х=1,0; у=0,5.
Коэффициент . Значения составляющих К i [1табл. П.3.24]:
КМр= К r , (1.5)
КМр= =0,62;
Для тангенциальной составляющей Pz:
Кφр=1,0; Кγр=1,0; Кλр=1,0; К r р=0,87.
Для осевой составляющей Px:
Кφр=1,0; Кγр=1,0; Кλр=1,0; К r р=1,0.
Крz= 0,62·1,0·1,0·1,0·0,87= 0,54.
Кру= 0,62·1,0·1,0·1,0·1,0= 0,62.
77,63 Н.
По станку 6000 Н [1табл. П.7.2], т.е. условие
выполняется.
Для определения мощности резания необходимо подсчитать тангенциальную составляющую сил резания Р z формуле (1.3).
121,5 Н.
Зная величину Р z подсчитываем мощность резания, кВт, по формуле
, (1.6)
где Р z – тангенциальная составляющая силы резания, Н.
=0,67 кВт.
Мощность на шпинделе станка, кВт, рассчитывается по формуле
, (1.7)
где – мощность двигателя станка, кВт;
= 11 кВт [1табл. П.7.1];
η– КПД станка, η=0,81;
Кп – коэффициент перегрузки станка (Кп =1).
=8,91кВт,
Таким образом , т.е. 0,67<8,91 – условие выполняется.
Расчет машинного времени
Расчет машинного времени для получистового и чистового переходов Тм , мин, производится по формуле
, (1.8)
где L – общая длина прохода инструмента в направлении подачи, мм;
п – число оборотов заготовки в минуту;
s – подача, мм/об;
i – число проходов.
Общая длина прохода инструмента L , мм рассчитывается по формуле
, (1.9)
где l – длина обработанной поверхности, мм;
l1– величина врезания, мм (l1=2,5 мм):
l2 – величина выхода (перебега) резца, мм (l2=0 мм):
5,06 мин.
Дата добавления: 2019-07-17; просмотров: 549; Мы поможем в написании вашей работы! |
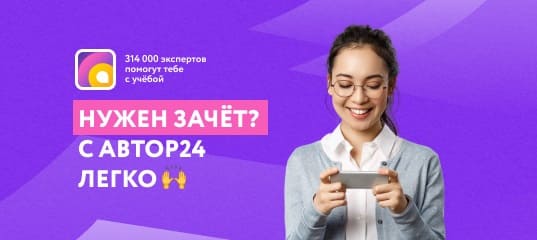
Мы поможем в написании ваших работ!