Флюсы и проволока для автоматической сварки
Расчет режимов сварки
1.4.1. Ручная сварка покрытыми электродами
Ручная дуговая сварка выполняется плавящимся или неплавящимся (угольным, графитовым, вольфрамовым, гафниевым) электродом. При сварке плавящимся электродом (рис. 1.6) дуга горит между ним и изделием. Формирование металла шва осуществляется за счет материала электрода и расплавления основного металла в зоне действия дуги. При сварке неплавящимся электродом для формирования металла шва в зону дуги извне подается присадочный материал.
Наибольшее применение получила сварка первым способом, т. е. плавящимся электродом. При этом используются электроды диаметром 1…12 мм. Однако основной объем работ выполняется электродами диаметром 3…6 мм.
![]() |
В табл. 1.1 приведены характеристики некоторых электродов общего назначения, наиболее распространенных в ремонтной практике для сварки и наплавки.
Таблица 1.1
Характеристика электродов
Тип электрода | Марка электрода | Коэффициент наплавки, г/А×ч | Разбрызгивание | Расход электродов, кг, на1 кг наплавленного металла КЭ |
Э42 Э42А Э46 Э46 Э46 Э50 Э50А Э50А | ОМА УОНИИ 13/45 АНО-3 МР-3 О3С-6 ДСК- 50 АНО- 9 УОНИИ 13/55 | 10…11 8,5 8,5 7,8 10,5 10,0…11,0 10,0 8,5…9,0 | Умеренное Умеренное Малое Умеренное Малое Малое Умеренное Умеренное | 1,45 1,60 1,60 1,70 1,60 1,40 1,70 1,70 |
К параметрам режима сварки относятся сила сварочного тока, напряжение, скорость перемещения электрода вдоль шва (скорость сварки), род тока, полярность и др.
|
|
Диаметр электрода выбирается в зависимости от толщины свариваемого металла, типа сварного соединения и положения шва в пространстве.
При выборе диаметра электрода для сварки можно использовать ориентировочные данные (табл. 1.2).
Таблица 1.2
Зависимость диаметра электрода
от толщины свариваемого металла
Толщина листов, мм | 1…2 | 3 | 4…5 | 6…10 | 10…15 | 15 и более |
Диаметр электрода, мм | 1,6…2,0 | 2,0…3,0 | 3,0…4,0 | 4,0…5,0 | 5,0 | 5,0 и более |
В многослойных стыковых швах первый слой выполняют электродом диаметром 3…4 мм, последующие слои – электродами большего диаметра.
Сварку в вертикальном положении проводят с применением электродов диаметром не более 5 мм. Потолочные швы выполняют электродами диаметром до 4 мм.
При наплавке изношенной поверхности должна быть компенсирована толщина изношенного слоя плюс 1…1,5 мм на обработку поверхности после наплавки.
Сила сварочного тока, А, рассчитывается по формуле
, (1.1)
где К – коэффициент, равный 25…60 А/мм; – диаметр электрода, мм.
Коэффициент К в зависимости от диаметра электрода принимается в соответствии с табл. 1.3.
|
|
Таблица 1.3
Зависимость коэффициента К от диаметра электрода
![]() | 1…2 | 3…4 | 5…6 |
К, А/мм | 25…30 | 30…45 | 45…60 |
Силу сварочного тока, рассчитанную по формуле (1.1), следует откорректировать с учетом толщины свариваемых элементов, типа соединения и положения шва в пространстве. Если толщина металла S 3
, то значение
следует увеличить на 10…15 %. Если же S
1,5
, то сварочный ток уменьшают на 10…15 %.
При сварке угловых швов и наплавке значение тока должно быть повышено на 10…15 %. При сварке в вертикальном или потолочном положении значение сварочного тока должно быть уменьшено на 10…15 %.
Для большинства марок электродов, используемых при сварке углеродистых и легированных конструкционных сталей, напряжение дуги = 22…28 В.
Расчет скорости сварки, м/ч, производится по формуле
(1.2)
где – коэффициент наплавки, г/А×ч (выбирают из характеристики принятого электрода);
– площадь поперечного сечения шва при однопроходной сварке (или одного слоя валика при многослойном шве), см2;
– плотность металла электрода, г/см3 (для стали
= 7,8 г/см3).
Масса наплавленного металла, г, для ручной дуговой сварки рассчитывается по формуле
, (1.3)
где – площадь поперечного сечения шва, см2;
– длина шва, см.
|
|
Расчет массы наплавленного металла при ручной дуговой наплавке производится по формуле
=
, (1.4)
где – площадь наплавляемой поверхности, см2;
– требуемая высота наплавляемого слоя, см (с учетом припуска на последующую обработку).
Время горения дуги (основное время), ч, определяется по формуле
. (1.5)
Полное время сварки (наплавки) приближенно определяется по формуле
, (1.6)
где – время горения дуги (основное время), ч;
– коэффициент использования сварочного поста, который принимается для ручной сварки 0,5…0,55.
Расход электродов, кг, для ручной дуговой сварки (наплавки) определяется по формуле
, (1.7)
где – коэффициент, учитывающий расход электродов на 1 кг наплавленного металла (табл. 1.1).
Расход электроэнергии, кВт×ч, определяется по формуле
, (1.8)
где – напряжение дуги, В;
– сварочный ток, А;
– кпд источника питания сварочной дуги;
– время горения дуги, ч;
– мощность, расходуемая источником питания сварочной дуги при холостом ходе, кВт; Т – полное время сварки или наплавки, ч.
Значения η источника питания сварочной дуги и Wo можно принять по табл. 1.4.
|
|
Таблица 1.4
Зависимость η и W 0 от рода тока
Род тока | ![]() | ![]() |
Переменный | 0,8…0,9 | 0,2…0,4 |
Постоянный | 0,6…0,7 | 2,0…3,0 |
Выбор и обоснование источника питания сварочной дуги могут быть осуществлены по прил. 1 табл. 1, 3, 4.
1.4.2. Сварка и наплавка деталей в среде защитных газов
При сварке и наплавке в среде защитных газов в зону горения дуги под небольшим давлением подается газ, который вытесняет воздух из этой зоны и защищает сварочную ванну от кислорода и азота воздуха.
В зависимости от применяемого газа сварка разделяется на сварку в активных (СО2, Н2, О2, и др.) и инертных (He, Ar, Ar+He и др.) газах. Сварку (наплавку) можно осуществлять как плавящимся, так и неплавящимся электродами.
Наибольшее распространение при восстановлении деталей подвижного состава получили сварка и наплавка в среде углекислого газа СО2 с использованием плавящихся электродов (проволоки) с защитой сварочной ванны от воздуха углекислым газом. Такой способ является самым дешевым при сварке углеродистых и низколегированных сталей. Поэтому по объему производства он занимает одно из первых мест среди механизированных способов сварки плавлением.
![]() | При сварке (наплавке) в среде углекислого газа (рис. 1.7) из сопла горелки 2, охватывающей поступающую в зону горения дуги электродную проволоку 4, вытекает струя защитного газа 6, оттесняя воздух из сварочной ванны. В процессе сварки углекислый газ под действием высоких температур диссоциирует: 2СО2 « 2СО+О2.Поэтому сварка идет не в чистом углекислом газе, а в смеси газов СО2, СО и О2. В этом случае обеспечивается практически полная защита расплавленного металла от азота воздуха, но сохраняется почти такой же окислительный характер газовой смеси, каким он был бы при сварке голой проволокой без защиты от атмосферного воздуха. Следовательно, при сварке и наплавке в среде СО2 необходимо предусматривать меры по раскислениюнаплавляемого металла. Эта задача решается использованием сварочных проволок диаметром 0,8…2,0 мм, в состав которых входят элементы раскислители. Чаще всего это кремний (0,6…1,0 %) и марганец (1,0…2,0 %). Наибольшее распространение при сварке в среде СО2 нашли электродные проволоки Св-08ГС, Св-08Г2С, СВ-10ГС, Св-18ХГС и др. Кроме проволок сплошного сечения, часто используются порошковые проволоки типа ПП-АН4, ПП-АН5, ПП-АН8, ПП-3Х2В8Т и др. Сварка в среде СО2 имеет целый ряд преимуществ: высокую степень концентрации дуги и плотности тока, дающих минимальную зону структурных изменений металла; большую степень защиты сварочной ванны от воздействия внешней среды; существенную производительность; возможность наблюдения за формированием шва; сварки металла различной толщины (от десятых долей до десятков миллиметров); производства сварки в различных пространственных положениях; механизации и автоматизации технологического процесса; незначительную чувствительность к ржавчине и другим загрязнителям основного металла. |
Однако необходимо иметь в виду и её недостатки: сильное разбрызгивание металла при токе больше 500 А, что требует постоянной защиты и очистки сопла горелки; открытая мощная дуга дает интенсивное излучение и требует защиты сварщика; при значительных токах необходимо предусматривать охлаждение горелки; сварка осуществляется практически только на постоянном токе; требуется специальная проволока.
Технические характеристики полуавтоматов для сварки в защитных газах приведены в прил. 1 табл. 6, 7.
Диаметр электродной проволоки выбирается в зависимости от толщины свариваемого металла (табл. 1.5).
Таблица 1.5
Зависимость диаметра электродной проволоки
от толщины свариваемого металла
Толщина листов, мм | 1… 2 | 3…6 | 6…24 и более |
Диаметр электродной проволоки ![]() | 0,8…1,0 | 1,2…1,6 | 2,0 |
Расчет силы сварочного тока, А,производится по формуле
, (1.9)
где – диаметр электродной проволоки, мм; а – плотность тока в электродной проволоке, А/мм2 (при сварке в СО2 а = 110…130 А/мм2).
Напряжение дуги и расход углекислого газа выбираются в зависимости от силы сварочного тока по табл. 1.6.
Таблица 1.6
Зависимость напряжения и расхода
углекислого газа от силы сварочного тока
Сила сварочного тока, А | 50…60 | 90…100 | 150…160 | 220…240 | 280…300 | 360…380 | 430…450 |
Напряжение дуги, В | 17…28 | 19…20 | 21…22 | 25…27 | 28…30 | 30…32 | 32…34 |
Расход СО2, л/мин | 8…10 | 8...10 | 9…10 | 15…16 | 15…16 | 18…20 | 18…20 |
При сварке на токах 200…250 А длина дуги должна быть в пределах 1,5…4,0 мм. Вылет электродной проволоки составляет 8…15 мм (уменьшается с повышением сварочного тока).
Скорость подачи электродной проволоки, м/ч, рассчитывается по формуле
(1.10)
где – коэффициент расплавления проволоки, г/А×ч;
– сварочный ток, А;
– диаметр электродной проволоки, мм; j – плотность металла проволоки (для стали j = 7,8 г/см3).
Значение определяется по формуле
. (1.11)
Скорость сварки (наплавки) рассчитывается по формуле
, (1.12)
где – коэффициент наплавки, г/А·ч,
, где ψ – коэффициент потерь металла на угар и разбрызгивание. При сварке в СО2 ψ =
= 0,1…0,15; – площадь поперечного сечения одного валика, см2. При наплавке в СО2 принимается равной 0,3…0,7 см2; ρ – плотность металла проволоки, г/см3 (для стали ρ = 7,8 г/см3).
Масса наплавленного металла, г, рассчитывается по формулам:
· при сварке [формула (1.3)]
;
· при наплавочных работах
, (1.13)
где – объем наплавленного металла, см3;
– площадь поперечного сечения шва, см2; l – длина шва, см.
При определении необходимо учитывать припуск на последующую механическую обработку 2…3 мм.
Время горения дуги, ч, определяется по формуле (1.5)
.
Полное время сварки, ч, определяется по формуле (1.6)
,
где – коэффициент использования сварочного поста,
= 0,6…0,7.
Расход электродной проволоки, г, рассчитывается по формуле
, (1.14)
где – вес наплавленного металла, г; ψ – коэффициент потерь, ψ = 0,1…0,15.
Расход электроэнергии, кВт×ч, определяется по формуле (1.8)
,
где – напряжение дуги, В; η – кпд источника питания, при постоянном токе η = 0,6…0,7, при переменном – η = 0,8…0,9; Wo – мощность источника питания, работающего на холостом ходу. На постоянном токе Wo = 2,0…3,0, на переменном – Wo = 0,2…0,4.
Справочные сведения по оборудованию для сварки в СО2 приведены в прил. 1 табл. 6, 7.
1.4.3. Автоматическая сварка под флюсом
При сварке под флюсом (рис. 1.8) дуга горит между сварочной проволокой 1 и свариваемым изделием 5 под слоем гранулированного флюса 4. Ролики 2 специального механизма подают электродную проволоку в зону горения дуги 6.
![]() | Сварочный ток переменный или постоянный (прямой или обратной полярности) подводится к проволоке с помощью скользящего контакта 3, а к изделию – постоянным контактом. Сварочная дуга горит в газовом пузыре, который образуется в результате плавления флюса и металла. Кроме того, расплавленный металл защищен от внешней среды слоем расплавленного флюса 8. По мере удаления дуги от зоны сварки расплавленный флюс застывает и образует шлаковую корку 10, которая впоследствии легко отделяется от поверхности шва. Флюс засыпается впереди дуги из бункера слоем толщиной 40…80 мм и шириной 40…100 мм. Нерасплавленный флюс после сварки используется повторно. Расплавленные электродный и основной металлы 7 в сварочной ванне перемешиваются и при кристаллизации образуют сварной шов 9. Сварка под флюсом используется при изготовлении и ремонте конструкций и деталей ответственного назначения, которые должны надежно эксплуатироваться в условиях низких и высоких температур. Для рассматриваемого вида сварки и наплавки при ремонте подвижного состава наибольшее применение находят флюсы марок АН-348А, АН-348В, ОСЦ-45, АНЦ-1 и др. Такие флюсы рекомендуются для сварки низко- и среднеуглеродистых сталей. Для сварки и наплавки низко- и среднелегированных сталей используются флюсы АН-348А, АН-60, АН-22 и другие в сочетании с проволоками Св-08А, Св-08ГА и проволоками, легированными хромом, молибденом, никелем. В табл. 1.7 приведено назначение некоторых марок флюсов и проволок. |
Таблица 1.7
Флюсы и проволока для автоматической сварки
Марка флюса | Назначение флюса | Рекомендуемые проволоки |
АН-348А, АН-348В, АНЦ-1 | Сварка и наплавка изделий широкойноменклатуры из углеродистых и низколегированных сталей | Св-08; Св-08А; Св-08ГА; Св-10Г2 |
АН-60 | Сварка и наплавка углеродистых и низколегированных сталей | Св-08; Св-08ГА; Св-08ХМ; Св-10НМА |
АН-22 | Сварка и наплавка низко- и среднелегированных сталей | Св-08ГА; Св-08ХМ; Св-08ХМФ; Св-08ХГНМГА |
АНК-30 | Сварка и наплавка углеродистых и низколегированных сталей, в т. ч. хладостойких мелкозернистых повышенной прочности | Св-08, Св-08ГА, Св-08ХМ, Св-08ХМФ, Св-08ХГНМТА |
Технические характеристики аппаратов для автоматической сварки и наплавки под флюсом приведены в прил. 1 табл. 6.
Расчет сварочного тока, А, производится по формуле (1.9)
,
где – диаметр электродной проволоки, мм; а – плотность тока, А/мм2.
При сварке для более глубокого проплавления рекомендуется использовать высокие значения плотности тока в электродной проволоке
(а ≥ 40…50 А/мм2), а при наплавке для снижения глубины проплавления принимается а ≤ 30…40 А/мм2. Диаметр электродной проволоки желательно выбирать таким, чтобы он обеспечил максимальную производительность сварки (наплавки) при требуемой глубине проплавления. Зависимость силы сварочного тока и его плотности на глубину проплавления приведена в табл. 1.8.
Таблица 1.8
Влияние силы сварочного тока и его плотности
на глубину проплавления при автоматической сварке под флюсом
Диаметр электродной проволоки, мм | Сила, А, и плотность, А/мм2,сварочного тока | Глубина проплавления, мм | |||||
3 | 4 | 5 | 6 | 8 | 10 | ||
1 | Сила сварочного тока | 200 | 300 | 350 | 400 | 500 | 600 |
Плотность тока | 65 | 104 | 127 | 143 | 157 | 200 | |
2 | Сила сварочного тока | 300 | 350 | 400 | 500 | 625 | 750 |
Плотность тока | 43 | 50 | 57 | 71 | 89 | 107 | |
3 | Сила сварочного тока | 375 | 425 | 500 | 550 | 675 | 800 |
Плотность тока | 29 | 36 | 40 | 44 | 53 | 64 | |
4 | Сила сварочного тока | 450 | 500 | 550 | 600 | 725 | 825 |
Плотность тока | 23 | 26 | 28 | 31 | 37 | 42 |
Зависимость напряжения дуги от силы сварочного тока приведена в табл. 1.9.
Таблица 1.9
Дата добавления: 2019-07-17; просмотров: 227; Мы поможем в написании вашей работы! |
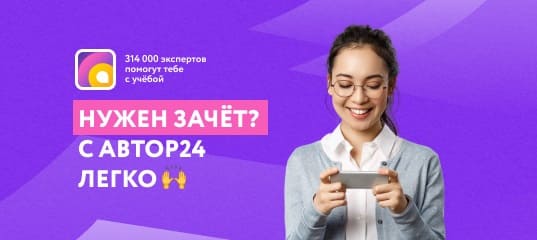
Мы поможем в написании ваших работ!