Проверка долговечности подшипников
Введение
Редуктором называют механизм, выполненный в виде отдельного агрегата и служащий для понижения частоты вращения и повышения крутящего момента на выходе.
Редуктор состоит из корпуса (литого чугунного или сварного стального), в котором помещают элементы передачи - зубчатые колёса, валы,
Лист
Лист
подшипники и т.д. В отдельных случаях в корпусе редуктора размещают также устройства для смазывания подшипников и зацеплений (например, внутри корпуса редуктора может быть помещён шестеренный масляный насос или устройства для охлаждения (например, змеевик с охлаждающей водой в корпусе червячного редуктора).
Работа выполнена в рамках дисциплины «Теория механизмов и машин и детали машин» на основании задания кафедры механики. Согласно заданию, необходимо сконструировать соосный двухступенчатый цилиндрический редуктор с раздвоением мощности для привода
к исполнительному механизму с мощностью на выходе 3.6 кВт и частотой вращения 40 об/мин.
Редуктор выполняется в закрытом варианте, срок службы неограничен. Разработанный редуктор должен быть удобным в эксплуатации, должны максимально использоваться стандартизированные элементы, а также редуктор должен иметь как можно меньшие габариты и вес.
1. Подбор электродвигателя и энерго-кинематический расчёт редуктора.
Привод исполнительного механизма может быть представлен следующей схемой (Рис.1.1.)[1].
|
|
Рис. 1.1 - Схема передачи
Нам необходимо рассчитать все эти параметры. Кинематическая схема редуктора приведена на рис. 1.2.
Рис.1.2. - Кинематическая схема редуктора.
Заданная передача представляет собой двухступенчатый редуктор. Соответственно, рассматриваем 3 вала: первый – входной с угловой скоростью , моментом
, мощностью
, частотой вращения
; второй – промежуточный с
,
,
,
, и третий – выходной
,
,
,
1 Энерго-кинематический расчет редуктора.
Согласно исходным данных, об/мин,
КВт,
тогда:
.
Крутящий момент на третьем валу:
.
Коэффициент полезного действия редуктора:
КПД пары цилиндрических зубчатых колес
,
где
- КПД подшипников качения (см. таблица 1.1) [1],
тогда:
.
Требуемая мощность электродвигателя:
Зная общее КПД и мощность N3 на выходом валу, находим требуемую мощность двигателя, который сидит на первом валу:
.
Рекомендованное передаточное отношение для редуктора РЦД: umax=25
Находим частоту вращения двигателя :
nдв=n3*umax:
.
Принимаем по ГОСТу 19523-81 электродвигатель:
Тип 112МВ6, с параметрами:
;
;
%.(смотри табл. П.1- 1),
где s,% - скольжение.
Частота вращения ведущего вала редуктора:
.
Теперь можем заполнить первую строку таблицы: n1=nдв, , величину мощности оставляем равной требуемой, момент определяем по формуле:
|
|
.
Взяв его частоту вращения за n1, находим общее передаточное отношение.
Передаточное отношение редуктора:
.
Передаточное отношение ступеней редуктора:
Первая ступень
;
.
Частота вращения промежуточного вала:
;
Угловые скорости валов:
входящего:
;
промежуточного:
.
Определение вращающих моментов валов редуктора:
входящего:
;
промежуточного:
.
Проверка:
;
;
;
.
Результаты вычислений приведены в таблице 1.3.
Таблица 1.3. Значение параметров нагрузки валов редуктора
![]() | ![]() ![]() | ![]() ![]() | ![]() | ![]() | ![]() | ![]() | |
![]() | 949 | 99.4 | ![]() | 3.75 | | 5.4 | |
| 175 | 18.5 |
| 3.68 | |||
| 4.4 | ||||||
![]() | 40 | 4.2 | ![]() | 3.6 | |||
![]() | 23.7 |
2. Расчёт зубчатых колес редуктора
Для редуктора РЦД расчет зубчатых передач необходимо начинать с более нагруженой - второй ступени.
II ступень:
Выбор материала
Т.к. в задании нет особых требований в отношении габаритов передачи, выбираем материалы со средними механическими характеристиками (см. гл. III, табл.3.3 [1]): для шестерни: сталь 30ХГС до 150 мм, термическая обработка – улучшение, твёрдость по Бринелю НВ 260.
Для колеса: сталь 40Х свыше 180 мм, термическая обработка – улучшение, твердость по Бринелю НВ 230.
|
|
Допускаемое контактное напряжение для зубчатых колёс [формула(3.9) - 1]:
,
где - предел контактной выносливости при базовом числе циклов, КНL- коэффициент долговечности (при длительной эксплуатации KHL=1)
[SH]= 1,1 – коэффициент безопасности для улучшенной стали [1 - c.34].
Для углеродистых сталей с твердостью поверхностей зубьев менее НВ 350 и термической обработкой (улучшением):
;
Для косозубых колес расчетная допускаемое контактное напряжение определяется [1 - формула (3.10)]
для шестерни ;
для колеса .
Контактное напряжение .
Требуемое условие выполнено.
Межосевое расстояние определяем по формуле: .
В соответствии с [2] подберем коэффициенты KHβ, Ka.
Коэффициент KHβ учитывает неравномерность распределения нагрузки по ширине венца. KHβ=1.25.
Принимаем для косозубых колес коэффициент ширины венца по межосевому расстоянию:
yba=0.63.
Межосевое расстояние из условия контактной выносливости активных поверхностей зубьев[1 - формула 3.7]
. u=4,4 – передаточное число .
Ближайшее значение межосевого расстояния по ГОСТ 2185-66 (см. стр.36 лит. [1]).
Нормальный модуль зацепления принимают по следующим рекомендациям:
;
принимаем по ГОСТ 9563-60* (см.с.36, лит. [1]).
Примем предварительно угол наклона зубьев и определим числа зубьев шестерни и колеса [1 - формула 3.16] :
|
|
шестерни .
Принимаем , тогда для колеса
Принимаем .
Уточненное значение угла наклона зубьев
.
Основные размеры шестерни и колеса:
диаметры делительные:
, где
-- угол наклона зуба по отношению к образующей делительного цилиндра.
;
.
диаметры вершин зубьев:
;
;
Проверка межосевого расстояния: aw= ;
эта величина укладывается в погрешность ±2%, которую мы получили в результате округления числа зубьев до целой величины;
ширина колеса:
;
ширина шестерни:
.
Определим коэффициент ширины шестерни по диаметру:
.
Окружная скорость колёс и степень точности передачи:
.
При такой скорости для косозубых колес следует принять 8-ю степень точности по ГОСТ 1643-81(см. с. 32 – лит[1]).
Коэффициент нагрузки:
,
где - коэффициент ширины венца,
- коэффициент типа зубьев,
-
коэффициент зависимости от окружной скорости колес и степени точности их изготовления.(см. стр. 39 – 40 лит.[1])
По таблице 3.5 .
По таблице 3.4 .
По таблице 3.6 .
Таким образом,
.
Проверка контактных напряжений по формуле 3.6 лит.[1]:
,
т.к. <
- условие выполнено.
Силы, действующие в зацеплении [формулы (8.3) и (8.4) лит.1]:
окружная:
;
радиальная:
;
осевая:
.
Проверяем зубья на выносливость по напряжениям изгиба:
(формула (3.25) лит.1),
где ,
- коэффициент нагрузки(см. стр.43 лит1),
-- учитывает неравномерность распределения нагрузки по длине зуба,
-- коэффициент динамичности,
- учитывает неравномерность распределения нагрузки между зубьями. В учебном расчете принимаем величину
=0,92.
По таблице 3.7, [1] .
По таблице 3.8, [1] ,
тогда:
.
- учитывает форму зуба и зависит от эквивалентного числа зубьев
[формула (3.25 лит.1)]:
у шестерни ;
у колеса .
Для колеса принимаем =4.05, для шестерни
=3.60 [см. стр.42 лит. 1].
Допускаемое напряжение по формуле (3.24 лит. 1):
[sF]=
По табл. 3.9 лит. 1 для сатали 45 улучшеной при твердости НВ ≤ 350
σ0F lim b=1.8HB.
Для шестерни σ0F lim b=1.8·260=486 МПа;
для колеса σ0F lim b=1.8·230=468 МПа.
[SF]= [SF]' [SF]'' – коэффициент безопасности [см.пояснения к формуле(3.24)лит. 1], где[SF]'=1.75 (по табл.3.9 лит. 1), [SF]''=1 (для поковок и штамповок). Следовательно [SF] = 1.75.
Допускаемые напряжения:
для шестерни [σF1]= ;
для колеса [σF2]= .
Дальнейший расчет ведем для зубьев колеса, т.к. для них данное отношение меньше.
Определяем коэффициенты и
[см.гл III, лит. 1].
;
(для 8-ой степени точности).
Проверяем прочность зуба колеса [формула (3.25), лит 1]
;
,≤ 278МПа.
Условие прочности выполнено.
I ступень:
Выбор материала
Т.к. в задании нет особых требований в отношении габаритов передачи, выбираем материалы со средними механическими характеристиками.
Для шестерни: сталь 30ХГС до 150 мм, термическая обработка - улучшение, твёрдость НВ 260.
Для колеса: сталь 30ХГС свыше 180 мм, термическая обработка – улучшение, твёрдость НВ 230.
Нахождение межосевого расстояния:
Т.к. рассчитывается двухступенчатый соосный цилиндрический редуктор с раздвоением мощности, то принимаем: .
Нормальный модуль зацепления принимают по следующим рекомендациям:
;
принимаем по ГОСТ 9563-60* =3мм.
Примем предварительно угол наклона зубьев β=10о
Определим число зубьев шестерни и колеса:
,
тогда .
Уточним угол наклона зубьев:
, тогда β=17.
Основные размеры шестерни и колеса:
диаметры делительные находим по формуле:
;
;
;
диаметры вершин зубьев:
;
.
Проверка межосевого расстояния: aw= , эта величина укладывается в погрешность ±2%, которую мы получили в результате округления числа зубьев до целой величины, а так же округления значения тригонометрической функции.
Ширина колеса:
;
ширина шестерни:
.
Определим коэффициент ширины шестерни по диаметру:
.
Окружная скорость колёс и степень точности передачи:
.
При такой скорости для косозубых колес следует принять 8-ю степень точности по ГОСТ 1643-81.
Коэффициент нагрузки:
,
где - коэффициент ширины венца,
- коэффициент типа зубьев,
- коэффициент зависимости от окружной скорости колес и степени точности их изготовления.
По таблице 3.5 [1];
По таблице 3.4 ;
По таблице 3.6 .Таким образом,
.
Проверка контактных напряжений по формуле:
, т.к.
<
- условие выполнено.
Силы, действующие в зацеплении:[формулы (8.3) и (8.4) лит.1]
окружная:
;
радиальная:
;
осевая:
.
Проверяем зубья на выносливость по напряжениям изгиба [формула (3.25) лит.1]:
,
где - коэффициент нагрузки(см. стр.43 [1]),
- учитывает неравномерность распределения нагрузки по длине зуба,
- коэффициент динамичности,
- учитывает неравномерность распределения нагрузки между зубьями. В учебном расчете принимаем величину
=0,92.
По таблице 3.7 [1];
По таблице 3.8 ;
тогда:
. Коэффициент
следует выбирать по эквивалентному числу зубьев (см. с.46 [1]):
у колеса ;
у шестерни .
- коэффициент учитывающий форму зуба. Для колеса принимаем
=4,25 для шестерни
=3.6 (см. с.42 лит.1);
Допускаемые напряжения:
[sF]= (формула (3.24), 1).
По табл. (3.9), лит 1 для стали 30ХГС улучшенной при твердости НВ ≤ 350
σ0F lim b=1.8HB.
Для шестерни σ0F lim b=1.8·260=468 МПа; для колеса σ0F lim b=1.8·250=450 МПа.
[SF]= [SF]' [SF]'' – коэффициент безопасности [см.пояснения к формуле(3.24),1],где[SF]'=1.75 (по табл.3.9 лит. 1), [SF]''=1(для поковок и штамповок). Следовательно[SF]= 1.75.
Допускаемые напряжения:
для шестерни [σF3]= ;
для колеса [σF4]= .
Находим отношения :
для колеса: ;
для шестерни: .
Дальнейший расчет ведем для зубьев шестерни, т.к. для них данное отношение меньше.
Определяем коэффициенты и
[см.гл III, лит. 1]:
;
(для 8-ой степени точности).
Проверяем прочность зуба шестерни [формула (3.25), лит 1]
;
≤267МПа.
Условие прочности выполнено.
3. Предварительный расчёт валов редуктора.
Предварительный расчёт проведём на кручение по пониженным допускаемым напряжениям.
Ведущий вал:
диаметр выходного конца при допускаемом напряжении ,
.
Так как ведущий вал редуктора соединен с валом электродвигателя ( см. рис. 1.1), то необходимо согласовать диаметры ротора двигателя и вала.
Примем . Т.к. диаметр ротора двигателяdдв=32мм, а расхождения не должны превышать ±20%.
Конструкция ведущего вала(см. рис. 3.1):
Рис. 3.1- Конструкция ведущего вала.
Промежуточный вал:
диаметр выходного конца при допускаемом напряжении ,
,
Принимаем ближайшее значение из стандартного ряда [см. гл. VIII лит.1] .
Конструкция промежуточного вала(см. рис. 3.2):
Рис.3.2. – Конструкция промежуточного вала
Ведомый вал:
диаметр выходного конца при допускаемом напряжении :
.
Принимаем ближайшее большее значение из стандартного ряда .
Конструкция ведомого вала(см. рис. 3.3):
Рис. 3.3. – Конструкция ведомого вала
4. Конструктивные размеры шестерни и колеса.
При конструировании колеса руководствуемся [1] (см. с.148).
Конструкция колеса(см. рис. 5.1):
Рис. 4.1. – Конструкция колеса
Для промежуточного вала.
Шестерню выполняем за одно целое с валом ее размеры определены выше: ;
;
;
Колесо кованное (см. гл. X, табл.10.1 лит 1): ;
;
.
Диаметр ступицы :
;
длина ступицы:
,принимаем
.
Толщина обода: ,принимаем
.
Толщина диска: .
Толщина ребер: .
Фаска: .
Для ведомого вала.
Колесо кованное (см. гл. X, табл.10.1 лит 1): ,
,
.
Диаметр ступицы : ,
длина ступицы: , принимаем
.
Толщина обода: , принимаем
.
Толщина диска: .
Толщина ребер: .
Фаска: .
5. Основные элементы корпуса из чугуна
Для расчета корпуса редуктора воспользуемся [1](см. с.241).
Толщина стенок корпуса и крышки: ;
, принимаем
.
Толщина фланцев пояса корпуса и крышки:
верхнего пояса корпуса и пояса крышки: ;
;
нижнего пояса корпуса:
при наличии бобышки: .
Диаметр болтов: фундаментных:
; принимаем болты с резьбой М20;
крепящих крышку к корпусу у подшипников:
, принимаем болты с резьбой М16.
соединяющих крышку с корпусом:
, принимаем болты с резьбой М12.
6. Первый этап компоновки редуктора
Компоновку обычно проводят в два этапа. Первый этап служит для приближённого определения положения зубчатых колёс относительно опор и для последующего определения опорных реакций и подбора подшипников.
Компоновочный чертёж выполняем в одной проекции – разрез по осям валов при снятой крышке редуктора.
Примерно посередине листа параллельно его длинной стороне проводим горизонтальную осевую линию; затем две вертикальные линии – оси валов на расстоянии .
Вычерчиваем упрощенно шестерню и колесо в виде прямоугольников.
Очерчиваем внутреннюю стенку корпуса:
а) принимаем зазор между торцом шестерни и внутренней стенкой корпуса ; при наличии ступицы зазор берётся от торца ступицы;
б) принимаем зазор от окружности вершин зубьев колеса до внутренней стенки корпуса ;
в) принимаем расстояние между наружным кольцом подшипника ведущего вала и внутренней стенкой корпуса ; если диаметр окружности вершин зубьев шестерни окажется больше наружного диаметра подшипника, то расстояние А надо брать от шестерни.
Намечаем шарикоподшипники (см. табл. 6.1):
Табл. 6.1. – Шарикоподшипники радиальные однорядные
Условное обозначение подшипника | d | D | B | Грузоподъёмность, кН | |
Размеры, мм | C | Co | |||
208 | 40 | 80 | 18 | 32 | 17.8 |
205 | 25 | 52 | 15 | 14 | 6.95 |
213 | 65 | 120 | 23 | 56 | 34 |
Решаем вопрос о смазывании подшипников. Принимаем для подшипников пластичный смазочный материал. Измерением находим расстояния на ведомом валу: ;
.
Проверка долговечности подшипников
1.Ведущий вал (рис. 7.1). Из предыдущих расчётов:
,
,
.
Из первого этапа компоновки имеем: ;
.
Рис. 7.1. – Расчетная схема ведущего вала
Реакции опор:
в плоскости хz:
;
;
;
;
в плоскости yz:
;
;
;
;
Суммарные реакции:
;
.
Подбираем подшипники по более нагруженной опоре (опоре В). Намечаем радиальные шариковые подшипники №208:
,
,
,
.
Эквивалентная нагрузка по формуле:
, где
.
(вращается внутреннее кольцо);
-коэффициент безопасности для приводов (см.табл. 9.19 ,лит 1);
(см.табл. 9.20, лит 1),
тогда: .
Расчётная долговечность, млн. об.:
Расчётная долговечность, ч.: ,
что больше, установленных ГОСТ 16162-85.
Ведомый вал (рис. 7.2).
Из предыдущих расчётов: ,
,
.
Из первого этапа компоновки имеем: ;
.
Рис. 7.2. – Расчетная схема ведомого вала
Реакции опор:
в плоскости хz:
;
;
;
;
в плоскости yz:
;
;
;
;
Суммарные реакции:
;
.
Подбираем подшипники по более нагруженной опоре (опоре А). Намечаем радиальные шариковые подшипники №213: ,
,
,
.
Эквивалентная нагрузка по формуле:
, где
.
(вращается внутреннее кольцо);
-коэффициент безопасности для приводов (см.табл. 9.19 ,лит 1);
(см.табл. 9.20, лит 1),
тогда: .
Расчётная долговечность, млн. об.:
Расчётная долговечность, ч.:
,
что больше, установленных ГОСТ 16162-85.
Дата добавления: 2019-07-17; просмотров: 224; Мы поможем в написании вашей работы! |
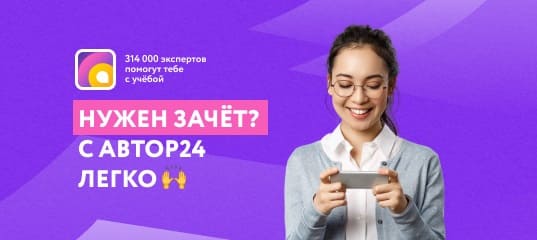
Мы поможем в написании ваших работ!