СПОСОБЫ ОЧИСТКИ СЖАТОГО ВОЗДУХА
Воздух очищают методом фильтрации и осушки, а также применением силовых полей. В некоторых устройствах и системах используют комбинированный способ, последовательно применяя, например, силовые поля и осушку или осушку и фильтрацию.
Предварительная очистка сжатого воздуха с использованием инерционных сил реализуется с помощью центробежных очистителей. В них загрязнители выходят из потока, совершающего спиральное движение, под действием центробежных сил (циклонные очистители). Преимуществами таких очистителей являются: постоянство степени очистки, незначительные потери давления, небольшие размеры, низкая стоимость.
Процесс очистки сжатого воздуха от загрязнителей вследствие их взаимодействия с элементами пористой перегородки называется фильтрацией. В качестве фильтрующих материалов широко применяются металлокерамика, керамика, тонкие и сверхтонкие волокна (естественные и искусственные), активированный уголь и другие материалы. Металлокерамические материалы отличаются высокой прочностью, температурной стойкостью, возможностью изготовления фильтров сложной формы, хорошей обрабатываемостью, возможностью восстановления способности фильтровать после загрязнения. Они применяются в фильтрах с тонкостью фильтрации 40…5 мкм для очистки воздуха от грязи, трубной окалины, ржавчины и конденсата [2, 3].
Волокнистые фильтрующие материалы (войлок, фетр, ткани, бумага, стекловолокно) имеют самое широкое применение – от очистки всасываемого компрессором воздуха до сверхтонкой очистки воздуха (со степенью фильтрации 99,9999 %) в фармацевтической и пищевой промышленностях. При высокой концентрации загрязнителей волокнистые фильтры быстро засоряются. Поэтому для увеличения продолжительности их работы перед ними часто устанавливают фильтры грубой очистки из металлокерамики. Так, например, в фильтрах тонкой и сверхтонкой очистки (с тонкостью фильтрации 1…0,01 мкм) применяют фильтроэлементы из боросиликатного стекловолокна. Получаемый при этом 1…2 класс чистоты воздуха достигается использованием предварительной очистки воздуха до среднего размера пор 5 мкм.
|
|
Тонкость фильтрации 0,003 мкм получают, последовательно фильтруя воздух с помощью боросиликатного стекловолокна и активированного угля. В этом случае, с целью увеличения долговечности фильтров, воздух предварительно очищают фильтром с тонкостью фильтрации 1 мкм и осушают.
При необходимости сжатый воздух осушают методами охлаждения, редуцирования и адсорбции. В процессе охлаждения воздух становится насыщенным и часть влаги, равная разности между действительным ее содержанием в воздухе и содержанием, соответствующим насыщению воздуха при данной температуре, выпадает в виде жидкости. Охлажденный воздух непосредственно перед его применением можно подогреть, что предотвратит конденсацию паров воды и масла в процессе работы пневмосистемы (в пескоструйных и дробеструйных машинах). Понижение давления сжатого воздуха приводит к уменьшению относительной влажности, что может быть использовано для осушки сжатого воздуха, из которого предварительно удалена капельная жидкость. Адсорбционная осушка сжатого воздуха основана на свойстве природных или искусственных пористых материалов избирательно концентрировать на поверхности водяной пар, количество которого возрастает с понижением температуры и увеличением его концентрации в сжатом воздухе. В технике находят широкое применение адсорбенты: активная окись алюминия, силикагели, искусственные цеолиты. Они отличаются высокой механической прочностью и небольшими энергозатратами при регенерации.
|
|
УСТРОЙСТВА ПОДГОТОВКИ СЖАТОГО ВОЗДУХА
Предварительное знакомство с устройствами подготовки сжатого воздуха в п. 4.1 дает представление о их назначении. Здесь рассматриваются схемы и конструктивные особенности этих элементов.
|
|
Фильтры
Фильтр-влагоотделитель (рис. 4.3, а) с тонкостью фильтрации 40…5 мкм имеет сменный металлокерамический фильтрующий элемент 1. Воздух подается в отверстие 2 фильтра и, проходя через дефлектор 3, получает винтовое движение. Под действием центробежных сил твердые загрязнители отделяются от потока, проходят мимо отражателя 4 и падают на дно фильтра. Мелкие загрязнители, не отделившиеся от потока, фильтруются металлокерамическим элементом 1. Мельчайшие капельки влаги собираются на фильтроэлементе в более крупные капли, которые под действием силы тяжести стекают на дно корпуса фильтра. Обратному движению загрязнителей вместе с потоком, со дна к фильтроэлементу, препятствует отражатель 4. Чистый воздух выходит к потребителю из отверстия 5. Скопившаяся в фильтре жидкость 6 выпускается через внутренние отверстия клапана 7 после отвертывания пробки 8.
а) б) в)
Рис. 4.3
В фильтре тонкой очистки (рис. 4.3, б) фильтроэлемент 1 выполнен из боросиликатного стекловолокна. Сжатый воздух подводится к отверстию 2, проходит внутрь фильтроэлемента, очищается боросиликатным стеклово- локном и выходит из отверстия 3. Большой объем фильтроэлемента позволяет получить больший расход воздуха и продлить срок работы фильтра. Жидкость (конденсат), скапливающаяся на дне корпуса фильтра, представляет собой масляно-водяную смесь. При большой скорости потока сжатого воздуха она может вспениваться и уноситься потоком в выходное отверстие фильтра. Во избежание этого не следует увеличивать расход воздуха через фильтр больше, чем указано в его паспорте.
|
|
Конденсат может сливаться из фильтра не только вручную, но и автоматически. Автоматический конденсатоотводчик (рис. 4.3, в) состоит из поплавка 1, верхнего клапана 2, трубки 3, пружины 4, поршня 5 и нижнего клапана 6. Когда уровень конденсата поднимется на величину, при которой выталкивающая сила преодолеет вес поплавка и давление воздуха на верхний клапан, он откроется и сжатый воздух по сверлениям в поплавке и отверстие в трубке 3 будет поступать в полость 7. Равновесие сил на поршне 5 нарушится, он опустится и откроет нижний клапан 6. Конденсат будет вытесняться сжатым воздухом в приемную емкость. Снижение уровня конденсата приведет к опусканию поплавка, закрытию верхнего клапана, подъему поршня и закрытию нижнего клапана
Засорение фильтроэлемента определяют по перепаду давления (0,04…
0,07 МПа, в зависимости от типа и размера фильтра), для чего в фильтры устанавливают дифференциальные манометры. Поскольку перепад давления на фильтроэлементе зависит не только от степени его засорения, но и от расхода сжатого воздуха через фильтр, от давления на входе, то момент засорения определяют при заданных в паспорте значениях расхода и давления.
Редукционные пневмоклапаны
Редукционные клапаны поддерживают на постоянном уровне давление на выходе не зависимо от изменения его на входе и от расхода сжатого воздуха. Клапан (рис. 4.4) состоит из корпуса, в котором смонтированы мембрана 1, дроссельный клапан 2, пружина дроссельного клапана 3, уплотнение дроссельного клапана 4, шток 5, уплотнение 6, пружина 7. Сжатый воздух подводится в отверстие клапана слева (по чертежу), проходит через дроссельную щель клапана, образованную острой кромкой корпуса и верхней плоскостью дроссельного клапана 2, и отводится из правого отверстия. Сопротивление дроссельной щели приводит к понижению давления отводимого сжатого воздуха, а автоматическое регулирование величины дроссельной щели позволяет поддерживать это давление на постоянном уровне. Требуемый уровень давления задается настройкой силы пружины 7 вручную, с помощью винта 8. Сила пружины действует на мембрану 1 сверху, а снизу на мембрану действует сила, создаваемая давлением отводимого сжатого воздуха (отрицательная обратная связь).
При изменении давления отводимого воздуха мембрана прогибается и через шток 5 изменяет величину дроссельной щели, стабилизируя отводимое давление. Высокая точность настроенного давления обеспечивается сбалансированным дроссельным клапаном. Уплотнение 4 изолирует подклапанную полость от подводимого высокого давления, а отверстие в штоке 5 соединяет ее с надклапанной полостью, находящейся в зоне низкого давления.
Таким образом, дроссельный клапан разгружен от действия разноссти подводимого и отводимого давлений. При повышении давления на выходе выше настроенного пружиной мембрана прогибается, между штоком 5 и жестким центром мембраны образуется зазор. Сжатый воздух проходит через него, отверстие в жестком центре мембраны и отверстие 9 в верхней крышке в атмосферу. Давление в надклапанной полости понижается до значения, настроенного пружиной 7.
Рис. 4.4
В редукционном клапане непрямого регулирования (рис. 4.5) кроме дроссельного клапана 1 со штоком, пружины 2, мембраны 3 и уплотнений имеется пилотный клапан 4 с мембраной 5. Пониженное постоянное давление на выходе редукционного клапана настраивается при помощи винта 6 и пружины 7, действующей на жесткий центр мембраны 5. Осевое отверстие 8 в жестком центре соединяет общую полость для мембран 3 и 5 с атмосферой. Нижний торец осевого отверстия закрывается штоком пилотного клапана. Конусная часть пилотного клапана и отверстие, в котором перемещается его шток, представляют регулируемый дроссель. Он понижает давление в межмембранной полости и поддерживает его постоянным. Регулируемый дроссель с мембраной 5 можно назвать редукционным клапаном первой ступени, дроссельный клапан 1 с мембраной 3 – редукционным клапаном второй ступени, а всю конструкцию – двухступенчатым редукционным клапаном.
Дроссельный клапан 1 закреплен на штоке, внутри которого выполнено осевое отверстие, закрываемое вверху уплотнением 9 жесткого центра мембраны 3. Подмембранная полость соединяется каналом с отводящим отверстием редукционного клапана.
Рис. 4.5
После подачи сжатого воздуха на вход клапана и при отсутствии его потребления на выходе редуцированное давление поддерживается на заданном уровне. Это достигается за счет утечек воздуха в атмосферу через отверстие в жестком центре мембраны 3 и осевое отверстие штока дроссельного клапана 1.
Когда идет потребление сжатого воздуха, жесткий центр мембраны 3 опускается, уплотняя осевое отверстие в штоке дроссельного клапана 1, а пилотный клапан 4 продолжает поддерживать постоянное, заданное пружиной 7, давление в межмембраной полости.
Маслораспылители
С помощью маслораспылителей в сжатый воздух вносится распыленное масло для смазывания трущихся поверхностей пневматических аппаратов.
В пневмосистемах, имеющих аппараты с материалами, разрушающимися от вносимых распылителями смазочных материалов, применение маслораспылителей не допускается. В стакан 1 маслораспылителя (рис. 4.6) заливается минеральное масло. Сжатый воздух подается в отверстие 2, проходит в отверстие 3 через окна 5 и эжекторное сопло 4. Через отверстия в корпусе и втулки 6 сжа
тый воздух подводится внутрь стакана 1, откуда через дроссель 7 он попадает внутрь стакана 8.
Рис. 4.6
В процессе работы, когда сжатый воздух проходит через маслораспылитель, на выходе эжекторного сопла происходит местное понижение давления. Под действием разности давлений над уровнем масла в стакан 1 и внутри колпачка 8 масло по трубке 9, через обратный клапан 10, по трубке 11 поступает внутрь колпачка. По осевому отверстию 12 оно попадает в эжекторное сопло и распыляется потоком воздуха.
Расход распыляемого масла, определяемый настройкой дросселя 7, зависит от расхода воздуха через маслораспылитель и от уровня масла в стакане 1. Стабилизация расхода масла при переменном расходе воздуха достигается применением автоматических устройств, поддерживающих постоянную скорость потока в эжекторном сопле 4. Исключить влияние изменения уровня масла в стакане на подачу распыленного масла можно с помощью дополнительной емкости, в которую масло подается из стакана. Из этой емкости масло транспортируется в эжекторное сопло.
Дата добавления: 2019-07-15; просмотров: 211; Мы поможем в написании вашей работы! |
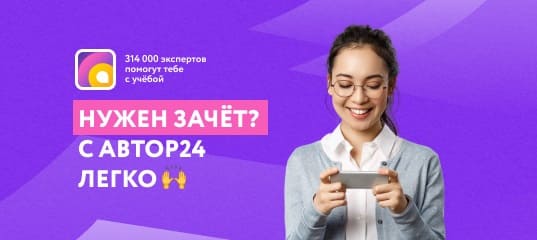
Мы поможем в написании ваших работ!