Краткие теоретические сведения
1.1 Мартенситное превращение в стали
Распад аустенита на феррито-карбидную смесь – диффузионный процесс, связанный с перераспределением углерода и железа, т.е. с диффузионным перемещением атомов на значительные расстояния, намного превышающие период решетки аустенита.
При охлаждении углеродистой стали с достаточно большой скоростью (сотни градусов в секунду) аустенит настолько сильно переохлаждается, что не распадается на смесь двух фаз, так как подвижность атомов при сильном охлаждении ниже точки А1 слишком мала. Но фиксации аустенита при комнатной температуре не происходит, так как в углеродистой стали, начиная с некоторой температуры, может существовать железоуглеродистая фаза, обладающая свободной энергией меньше, чем аустенит. Эта фаза называется мартенситом.
Мартенсит – микроструктура игольчатого вида, наблюдаемая в закалённых металлических сплавах и в некоторых чистых металлах, которым свойствен полиморфизм, основная структурная составляющая закалённой стали; представляет собой упорядоченный пересыщенный твёрдый раствор углерода в α-железе.
Превращение аустенита в мартенсит при охлаждении начинается и заканчивается при определенных для каждой марки стали температурах – температуре начала (МH) и конца (МК) мартенситного превращения.
1.2 Закалка
Закалкойназывается вид термической обработки, заключающийся в нагреве стали до температуры выше критической точки, выдержке и последующем быстром охлаждении со скоростью не ниже критической.
|
|
Критические точки– это температуры фазовых превращений. Различают равновесные (теоретические) и фактические критические точки.
Равновесные критические точки лежат на линиях диаграмм состояния и показывают температуры фазовых переходов в условиях чрезвычайно медленного изменения температур (нагрева или охлаждения).
Равновесные критические точки углеродистых сталей можно определять по метастабильной диаграмме "железо - цементит". На этой диаграмме равновесные точки, лежащие на линии PSK, обозначаются А1 и показывают температуру превращения перлита в аустенит при нагреве и обратного превращения при охлаждении. Равновесные точки, находящиеся на линии GS, обозначаются А3 и показывают температуры окончания растворения феррита в аустените при нагреве и начала его выделения из аустенита при охлаждении. Равновесные точки линии SE обозначаются Acm и показывают температуры окончания растворения цементита (вторичного) в аустените при нагреве и начала его выделения из аустенита при охлаждении.
Нагрев при закалке производится для перевода всей исходной структуры или определенной ее части в аустенит, который является исходной фазой для получения конечной структуры закаленной стали.
|
|
Выдержка необходима для выравнивания температуры по сечению детали и для полного установления необходимого фазового состояния.
Охлаждение при закалке должно производиться со скоростью не меньше критической для того, чтобы предотвратить протекание диффузионных процессов и переохладить весь исходный аустенит до температурного интервала мартенситного превращения.
Критическая скорость охлаждения(закалки) – это минимальная скорость охлаждения, при которой предотвращается диффузионный распад переохлажденного аустенита.
1.3 Выбор технологических параметров закалки
Температура закалки определяется исходя из массовой доли углерода в стали и соответствующего ей значения критической точки. Практически критические точки выбирают по справочникам или по диаграмме состояния "железо - цементит".
Температура нагрева при закалке tзак, °С, доэвтектоидных сталейопределяется следующим образом:
tзак = Ас3+ (30 – 50) | (3) |
Заэвтектоидные и эвтектоиднуюстали нагреваются при закалке до температуры tзак,°С,:
|
|
tзак = Ас1+ (30 – 50) | (4) |
Исходя из этого определяется положение оптимального интервала температур закалки углеродистых сталей на диаграмме состояния Fe – Fe3C.
Продолжительность нагрева и выдержки определяется размерами и конфигурацией деталей и способом их укладки в печи.
Охлаждение при закалке должно производиться в такой охлаждающей среде, которая обеспечивает скорость охлаждения не менее критической.
Таблица 6 - Температуры критических точек при нагреве сталей и их твердость после закалки
Марка стали | Массовая доля углерода, % | Температура, ˚C | Твердость правильно закаленной стали, HRC | |
АС1 | АС3 | |||
Углеродистые конструкционные стали | ||||
20 | 0,17 – 0,24 | 735 | 850 | 34 – 40 |
25 | 0,22 – 0,30 | 735 | 835 | |
30 | 0,27 – 0,35 | 730 | 820 | 42 – 48 |
35 | 0,32 – 0,40 | 730 | 810 | |
40 | 0,37 – 0,45 | 730 | 790 | 48 – 51 |
45 | 0,42 – 0,50 | 730 | 770 | |
50 | 0,47 – 0,55 | 725 | 760 | 54 – 60 |
55 | 0,52 – 0,60 | 725 | 755 | |
60 | 0,57 –0,65 | 725 | 750 | 60 – 62 |
Углеродистые инструментальные стали | ||||
У7 У8 – У13 | – – | 725 730 | 765 – | 62 – 64 63 – 65 |
Для применения расчетного метода необходимо определить, является ли тело термически тонким или термически массивным и каковы условия теплообмена при нагреве детали. В термически тонких телах время нагрева определяется, прежде всего, тепловым потоком, поступающим на поверхность изделия. В термически массивных телах внутреннее термическое сопротивление значительно влияет на продолжительность нагрева. Критерий, по которому тела подразделяются на термически тонкие и термически массивные, носит название критерия Био:
|
|
![]() | (5) |
где α – коэффициент теплоотдачи, характеризующий тепловой поток с поверхности изделия в окружающую среду;
λ – коэффициент теплопроводности материала детали;
X – характерный геометрический размер детали, равный расстоянию наиболее удаленной точки от поверхности, к которой подводится тепловой поток.
К термически массивным относят все изделия, у которых Bi > 0,15.
Коэффициент теплоотдачи для закалки:
α=61,1 ккал / (м2*час*град)
Коэффициент теплоотдачи для отпуска:
α=29,8 ккал / (м2*час*град)
Коэффициент теплопроводности материала детали:
λ=40
1.4 Отпуск стали.
Отпускомназывается термическая обработка, заключающаяся в нагреве закаленной стали до температуры ниже критической точки Ас1, выдержке и последующем охлаждении.
В зависимости от температуры нагрева различают три вида отпуска:
низкий отпуск 150 – 250°С,
средний отпуск 350 – 450°С,
высокий отпуск 500 – 650°С.
Выбор температуры отпуска зависит от того, в каких условиях будет работать изделие и, следовательно, какими свойствами оно должно обладать.
Комплекс термической обработки, состоящей из полной закалки и высокого отпуска конструкционных сталей, называется улучшением.
Для достижения этих свойств температуру отпуска необходимо назначать исходя из следующих закономерностей: при повышении температуры отпуска понижаются твердость и прочность и повышаются пластичность и ударная вязкость сталей.
Технология проведения отпуска состоит из нагрева образца до температуры соответствующего отпуска и выдержки при этой температуре.
Порядок выполнения работы
2.1 Определить режимы термической обработки партии зубчатых колес диаметром 100 мм выполненных из стали 45 и зубила размером 64 мм выполнного из стали У10.
2.1.1 Указать химический и фазовый состав стали
2.1.2 Определить температуры закалки и отпуска стали, время выдержки (1-2 минна один миллиметр наибольшего поперечного сечения образца))
2.1.3 Используя таблицу приложения А перевести твердость закаленной стали из единиц Роквелла в единицы Бринеля.
2.1.4 Посчитать предел прочности закаленной стали.
2.2 Вычертить в масштабе стальную часть диаграммы, обозначить область оптимального интервала температур закалки углеродистых сталей.
Определить критерий Био
2.4 Результаты занести в таблицу 7.
Таблица 7 – Результаты испытаний
Марка стали | Количество углерода в стали стали | Фазовый состав | Температура закалки, 0С | Время выдержки, мин | Механические свойства после закалки | Температура отпуска, 0С | Время выдержки, мин | Температуры критических точек | Критерий Био | |||
HRС | HB | Предел прочности σв, МПа | А3 | А1 | ||||||||
Содержание отчета
В отчете должны быть изложены:
1) номер лабораторной работы;
2) тема лабораторной работы;
3) цель работы;
4) обоснование выбора параметров закалки и отпуска;
5) вывод об изменении структуры и механических свойств после закалки и отпуска.
Контрольные вопросы
1 В чем сущность закалки?
2 Как меняются механические свойства в результате закалки?
3 Назначение нагрева, выдержки и охлаждения при закалке.
4 От чего зависит и как определяется общее время выдержки при закалке?
5 Основная структурная составляющая закаленной стали.
6 В чем сущность отпуск?
7 Какие причины обусловливают необходимость проведения отпуска?
8 Виды отпуска?
9 Чем определяется выбор температуры отпуска?
10 Влияние температуры отпуска на механические свойства стали.
Дата добавления: 2019-07-17; просмотров: 238; Мы поможем в написании вашей работы! |
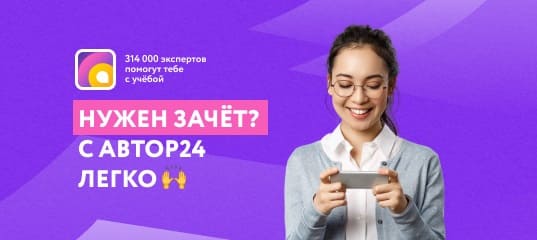
Мы поможем в написании ваших работ!