Оборудование, инструменты и материалы для выполнения работы
Микроскопы МИМ-7, МИМ-8, твердомер ТК-2М с шариковым наконечником, коллекция микрошлифов технически чистого железа после деформации и после деформации и отжига.
Задание
1. Изучить, зарисовать и объяснить микроструктуру недеформированного образца и образцов, подвергнутых холодному пластическому деформированию с различными степенями деформации.
2.
|
3. Рассчитать по формуле А.А. Бочвара температуру рекристаллизации и рекристаллизационного отжига для технически чистого железа. Принять коэффициент α равным 0,4.
4. Используя данные табл. 9.1, построить график зависимости твердости после отжига для образцов, предварительно деформированных на 70%, от температуры отжига. Сделать вывод по графику о температуре рекристаллизационного отжига и сравнить ее с расчетной.
5. Изучить микрошлифы образцов после возврата, первичной и собирательной рекристаллизации, зарисовать их, описать сущность явлений.
6. Написать отчет по работе в соответствии с вышеуказанными пунктами задания.
Таблица 9.1
Технологическая карта пластической деформации и рекристаллизации
технического железа
Номер образца | Степень деформации ε, % | Температура нагрева, оС при отжиге, выдержка 30 мин | Твердость HRB |
0 | 0 | Без нагрева | 50…55 |
1 | 5÷6 | То же | 58…62 |
2 | 10 | То же | 65…70 |
3 | 30 | То же | 80…82 |
4 | 70 | То же | 86…89 |
5 | 10 | 350 | 62…66 |
6 | 30 | 350 | 76…79 |
7 | 70 | 350 | 83…87 |
8 | 10 | 450 | 60…63 |
9 | 30 | 450 | 74…76 |
10 | 70 | 450 | 81…83 |
11 | 10 | 700 | 50…54 |
12 | 30 | 700 | 50…53 |
13 | 70 | 700 | 49…54 |
14 | 5-6 | 700 | 47…50 |
Контрольные вопросы
|
|
1. Что такое деформация?
2. Чем отличается пластическая деформация от упругой?
3. Как меняется строение металла в результате пластической деформации?
4. Чем отличается холодное деформирование металла от горячего деформирования?
5. Что такое наклеп? Как устранить наклеп?
6. Что такое возврат и его стадии – отдых и полигонизация?
7. Что такое рекристаллизация?
8. Какие виды рекристаллизации вы знаете?
9.
|
10. Что такое критическая степень деформации?
11. Как определить температуру рекристаллизации сплава?
12. От чего зависит размер зерна после рекристаллизации?
Лабораторная работа 10
Цементация стали
Цель работы: изучение технологии процесса цементации стали в твердом карбюризаторе, полученной микроструктуры поверхностного слоя, типовой термической обработки после цементации и свойств цементованных изделий.
|
|
Краткие сведения из теории
Цементация – один из видов химико-термической обработки изделий, представляющей собой диффузионное насыщение поверхностей деталей различными элементами с целью придания им особых свойств.
Цементация (науглероживание) – это процесс диффузионного насыщения поверхностного слоя стальных изделий углеродом в углеродсодержащей среде (карбюризаторе).
В случае массового производства широко применяют газовую цементацию в среде разнообразных углеродсодержащих газов, которая обеспечивает высокую производительность и возможность автоматизации процесса, а также упрощение последующей термообработки. Однако в случае мелкосерийного производства и в лабораторной практике разумно применять цементацию в твердом карбюризаторе.
Цель цементации и последующей термообработки – получение деталей повышенной выносливости с твердой, износостойкой поверхностью при сохранений вязкой, хорошо выдерживающей динамические нагрузки сердцевины.
Цементации подвергают зубчатые колеса, распределительные валики, втулки, поршневые пальцы и другие детали из углеродистых и легированных сталей, содержащих до 0,3% С. Такие стали называют цементуемыми.
|
|
Основные параметры цементации:
· температура процесса – 880÷950 оС (чаще 910÷930 оС – выбор температур выше точки Ас3 в области аустенита обусловлен значительной растворимостью углерода в аустените и более активной диффузией атомов С в решетке γ-Fe);
· продолжительность цементации 6÷12 и более часов – в зависимости от толщины науглероженного слоя, причем в газовой среде скорость процесса выше, следовательно, продолжительность несколько ниже;
· толщина науглероженного слоя 0,4÷2 мм (в случае больших контактных нагрузок до 6 мм);
· максимальное содержание углерода на поверхности – 0,8÷1,1%.
|
При нагреве уголь в условиях недостатка кислорода взаимодействует с ним по реакции 2С + О2 → 2СО. Кроме того, оксид углерода СО образуется в результате реакции ВаСО3 + С→ ВаО + СО. На поверхности стальных деталей протекает ведущая процесс цементации реакция диспропорционирования 2СО → СО2 + С (атомарный). Образовавшийся углекислый газ, взаимодействуя с углем, вновь восстанавливается до СО и т.д.
|
|
Активный углерод адсорбируется насыщаемой поверхностью и диффундирует в глубь детали.
После медленного охлаждения детали от температур цементации науглероженный слой имеет сложное строение. В процессе охлаждения аустенит поверхностного слоя с содержанием углерода более 0,8% превращается в перлит и цементит вторичный в виде сетки (заэвтектоидная зона), содержащий около 0,8% С – в перлит (эвтектоидная зона), а менее 0,8% – в феррит и перлит (переходная доэвтектоидная зона). За толщину науглероженного слоя принимают суммарную толщину заэвтектоидной, эвтектоидной и половины переходной зоны. Кроме того, длительная выдержка при высоких температурах приводит к укрупнению зерна, что отрицательно сказывается на механических свойствах изделия.
Окончательные свойства деталей формирует термическая обработка, которая назначается после цементации.
Для удовлетворения особо высоких требований, предъявляемых к деталям ответственного назначения, последние подвергают сложной термической обработке, состоящей из двух последовательно проводимых закалок и низкого отпуска. Первую закалку осуществляют с температур 850÷900 (920) оС (на 30÷50 оС выше АС3 исходной стали). Эта полная закалка направлена на измельчение структуры сердцевины и на устранение сетки цементита на поверхности (если она образовалась), однако она не формирует окончательно твердость, поэтому ее можно заменить нормализацией. Вторая закалка с температур 750÷780 оС (несколько выше АС1 заэвтектоидной стали) является неполной и назначается для формирования высокой твердости на поверхности детали. В процессе нагрева мартенсит, полученный в результате первой закалки, распадается, что сопровождается образованием глобулярных карбидов, которые в определенном количестве сохраняются после второй закалки в поверхностной заэвтектоидной части диффузионного слоя, увеличивая его твердость. Окончательной операцией термической обработки является низкий отпуск при 160÷200 оС, уменьшающий остаточные напряжения и не снижающий твердости.
|
Детали менее ответственного назначения, а также изготовленные из наследственно-мелкозернистых сталей и имеющие на поверхности после цементации не более 0,8% углерода, подвергают более простой термообработке, состоящей из одной закалки и низкого отпуска.
Твердость HRC поверхности в окончательном варианте получается 58÷62, а сердцевины – 35÷40.
Дата добавления: 2019-07-17; просмотров: 146; Мы поможем в написании вашей работы! |
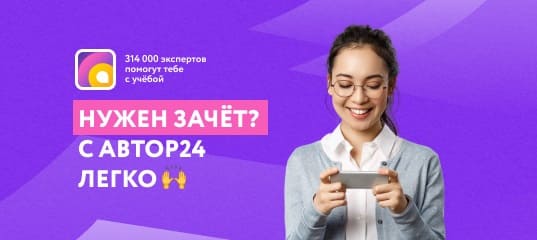
Мы поможем в написании ваших работ!