Выбор температуры горячего воздуха и типа воздухоподогревателя
Оптимальная температура горячего воздуха определяется по характеристикам сжигаемого топлива, а для угольных котлов – еще и по типу шлакоудаления. При сжигании малореакционных углей типа антрацит или тощий необходим высокий температурный уровень процесса горения. Опыт эксплуатации паровых котлов на донецком АШ показал, что для надежного воспламенения и умеренных потерь с механическим недожогом температуру горячего воздуха следует поддерживать на уровне 400–450 °С. При меньшей температуре горячего воздуха не только увеличиваются потери q4 но и снижается диапазон нагрузок, при котором надежно выходит жидкий шлак без подсветки угольного факела мазутом или газом.
При сжигании каменных углей с более высоким выходом летучих (в топках с жидким шлакоудалением) температуру горячего воздуха можно снизить до 350–400 °С. Если при этом окажется, что по условиям сушки топлива требуется менее горячий воздух, то в пылесистему можно подать смесь горячего воздуха и слабоподогретого, после первой ступени трубчатого воздухоподогревателя.
Для котлов, оборудованных топками с твердым шлакоудалением температура горячего воздуха может быть еще ниже – 300–350 °С. Однако при сжигании высоковлажных топлив (бурые угли или фрезторф) необходимо обеспечить сушку топлива в процессе размола и транспорта пыли к горелкам. В таких случаях (при замкнутой системе пылеприготовления) для сушки топлива можно воспользоваться смесью воздуха и дымовых газов, тем более что снижение концентрации кислорода до 15% решает проблему взрывоопасности систем пылеприготовления.
|
|
Температура горячего воздуха, оптимальная по условиям сушки и организации топочного процесса, – важный, но не единственный фактор, определяющий необходимость и характеристики воздухоподогревателя. Дело в том, что за экономайзером температура продуктов сгорания составляет 350–400°С. Воздухоподогреватель позволяет использовать теплоту этих газов: температура уходящих дымовых газов за счет теплоотдачи в воздухоподогревателе снижается до 120–160 °С, что значительно повышает КПД котла.
Нагреваемая среда в воздухоподогревателе содержит в основном двухатомные газы (О2 и N2), а также небольшое количество водяных паров. Нагревающая среда – продукты сгорания – всегда содержат большее количество водяных паров и трехатомные газы (СО2 и SО2). Поэтому объем и теплоемкость дымовых газов всегда выше, чем у воздуха. Именно поэтому воздух в воздухоподогревателе нагревается быстрее, чем охлаждаются в нем продукты сгорания (рис. 13). В результате, по мере нагревания воздуха, температурный напор (от которого зависит интенсивность теплообмена) уменьшается. С учетом этого температура уходящих газов определяется не температурным напором между рабочими средами на холодной стороне воздухоподогревателя (где она больше), а экономически обоснованной разностью температур на горячей стороне (где она минимальна). Обычно в этом месте разность температур составляет 30–40 °С, и дальнейшее повышение температуры горячего воздуха становится невыгодным из-за слишком низкого теплообмена, что требует чрезмерного увеличения поверхности воздухоподогревателя.
|
|
Рис. 13. Изменение температурного напора в процессе подогрева воздуха
Многолетний опыт проектирования котельных установок на разных видах топлива позволяет сделать следующие выводы:
• при сжигании малореакционных углей, когда требуется подогревать воздух до 400–420 °С, температура уходящих газов не может быть меньше 140–150 °С;
• на газомазутных котлах (при температуре горячего воздуха 300–360 °С) температура уходящих газов составляет 130–140 °С;
• на котлах, сжигающих высоковлажные бурые угли, оптимальной оказывается температура уходящих газов 150–170°С.
По конструктивному выполнению все воздухоподогреватели можно разделить на рекуперативные (обычно – стальные, трубчатые) и регенеративные (вращающиеся, с попеременным нагреванием стальных листов горячими газами и охлаждением воздухом). Трубчатый воздухоподогреватель (ТВП) прост в изготовлении, но требует большого расхода металла (рис. 14). Воздух проходит с внешней стороны стальных труб диаметром 30–40 мм. Горячие дымовые газы проходят внутри этих труб, которые своими концами приварены к трубным доскам. В котлах большой мощности для снижения габаритов воздухоподогревателя часто применяют двухпоточную (по воздуху) схему (рис. 15,а), а в некоторых случаях – многоканальную (рис. 15,б).
|
|
Рис. 14. Трубчатый воздухоподогреватель: 1 – стальные трубы; 2 и 6 – верхняя и нижняя трубные доски толщиной 20–25 мм; 3 – компенсатор; 4 – воздухоперепускной короб; 5 – промежуточная трубная доска; 7 и 8 – опорные рамы и колонны
Рис. 15. Схемы компоновки трубчатых воздухоподогревателей с различным подводом воздуха: а – двухпоточная схема по воздуху; б – многоканальный подвод воздуха; 1 – вход холодного воздуха; 2 – выход горячего воздуха
В регенеративных подогревателях (РВП) для подогрева воздуха используются твердые насадки (обычно – стальные листы), получающие теплоту от дымовых газов. Набивкой заполняют цилиндрический пустотелый ротор, который медленно вращается на валу с приводом от электродвигателя (рис. 16).
|
|
Рис. 16. Регенеративный воздухоподогреватель: 1 – вал ротора; 2 – подшипники; 3 – электродвигатель; 4 – набивка; 5 – наружный кожух; 6 – радиальное уплотнение; 7 – периферийное уплотнение; 8 – утечка воздуха
Такие воздухоподогреватели конструктивно сложнее ТВП, но они более компактны, требуют меньше металла и имеют меньшее аэродинамическое сопротивление.
К сожалению, РВП имеют и некоторые недостатки: требуются расход электроэнергии на собственные нужды и обслуживание механизма вращения (смазка и т. п.); из-за коробления гофрированных листов набивки подогрев воздуха осуществляется только до 300–350 °С; даже наиболее сложные уплотнения, разделяющие газовый и воздушный потоки, не избавляют от повышенных перетоков воздуха в газовый тракт котла.
При сжигании высокосернистых топлив для предотвращения низкотемпературной коррозии часто применяют комбинированный нагрев воздуха. Такая схема предполагает использование не только теплоты продуктов сгорания, но и низкотемпературную теплоту пара из системы регенерации турбины (рис. 17). До входа в трубчатый воздухоподогреватель устанавливают паровой калорифер, в котором высвобождается скрытая теплота парообразования отработавшего в турбине пара, что уменьшает потери теплоты в цикле. Но главная задача установки паровых калориферов – защита первых кубов трубчатого воздухоподогревателя от низкотемпературной коррозии.
Рис. 17. Схема предварительного подогрева воздуха в паровом калорифере: 1 – паровой калорифер; 2 – дутьевой вентилятор
Получение чистого пара
В котлах барабанного типа чистота получаемого пара в первую очередь определяется качеством котловой воды. Для поддержания допустимой концентрации солей (когда еще не происходит их выпадения из раствора) используется продувка котловой воды. Применяют непрерывную и периодическую продувку котла. Первая обеспечивает равномерное удаление из котла накопившихся растворенных солей. Осуществляют непрерывную продувку из мест их максимальной концентрации в барабане котла. Периодическая (через 12–16 ч) продувка применяется для удаления шлама, осевшего в различных местах (барабан, коллекторы котла).
Теплоту, содержащуюся в продувочной воде, удается частично сохранить за счет использования расширителей. Давление в расширителе меньше, чем в котле, поэтому часть продувочной воды испаряется, а образовавшийся пар направляется в деаэратор. Оставшаяся в расширителе вода сливается в дренажную систему, но предварительно проходит через теплообменник, где используется еще некоторая часть теплоты продувочной котловой воды.
Величина непрерывной продувки устанавливается по допустимой концентрации растворимых примесей в котловой воде. По Правилам технической эксплуатации (ПТЭ) величина непрерывной продувки меняется от 0,5 (при питании котла смесью конденсата и обессоленной воды) до 5 % (для ТЭЦ, у которых потери пара, отбираемого на производство, превышают 40 %).
Существует немного технологических процессов, которые вырабатывали бы продукт столь высокой степени чистоты, требумой для пара, вырабатываемого паровым котлом на тепловой электростанции. Так, для соединения натрия их допустимое содержание в паре не должно превышать 5 мкг/кг. Аналогичные жесткие требования предъявляются и по другим примесям. Обусловлено это большим количеством пара, вырабатываемого для питания турбины. В качестве примера можно привести следующие цифры. Для блока единичной мощностью 1200 МВт котел имеет паропроизводительность 3950 т/ч. По максимуму (при 100-процентной нагрузке и соблюдении указанных норм) из котла за год будет вынесено 1730 кг солей. В реальной практике (с учетом пониженных нагрузок, остановов на ремонт и т. д.) эта величина меньше. Но даже небольшая доля этих солей, отложившись в водопаровом тракте котла и проточной части паровой турбины, существенно повлияет на надежность и экономичность работы оборудования.
Рассмотрим процесс перехода примесей из котловой воды в насыщенный пар применительно к условиям работы барабанных котлов.
Такой переход осуществляется двумя путями: за счет попадания капельной воды в паровое пространство вместе с содержащимися в ней примесями и за счет прямого растворения примесей в паре. (Пар – это тоже Н2O, фигурально выражаясь, с более редко расположенными молекулами.) Вещества котловой воды в определенной степени растворяются в паре непосредственно.
Можно считать, что концентрация веществ в паре Сп пропорциональна концентрации этих веществ в котловой воде Св, то есть
Сп = kсум · Св. (4)
Коэффициент пропорциональности kсум включает в себя коэффициент уноса ω, обусловленный попаданием влаги в пар в виде капель (численно он равен влажности пара), и коэффициент распределения веществ, обусловленный растворимостью вещества в паре kp, что в итоге можно выразить так:
Cп = (ω + kp)·Cв. (5)
При низком рабочем давлении котла влажность – преобладающий фактор ω>>kp, а с приближением к критическому давлению увеличивается роль прямой растворимости kp>>ω.
При чисто барботажном процессе (всплытие парового пузыря и разрыв его на поверхности зеркала испарения) источником появления капельной влаги служат частицы разрывающейся пленки пузыря, а также выбиваемые из поверхности зеркала испарения капли за счет динамического воздействия остатков оболочки пузыря. При вводе пароводяной смеси в паровое пространство происходит дробление потока за счет кинетической энергии струи при торможении, а также прямого удара о твердую или жидкую поверхность в барабане.
Следует отметить некоторые важные закономерности, влияющие на растворимость веществ в паре. Коэффициент растворимости kp = Ср /Ср в (отношение концентраций растворенного вещества в паре к соответствующему количеству в воде) определяется отношением массовых плотностей пара и воды в состоянии насыщения, в степени и:
kp = (ρ''/ρ')n . (6)
Показатель и, названный координационным числом, отражает физикохимические свойства вещества (степень гидратации). Чем он больше, тем выше степень ионизации, лучше удерживается вещество молекулами воды и меньше растворимость в насыщенном паре. Эти вещества разделены на три класса:
1) n < 1. Слабые электролиты, наиболее растворимые в паре (из-за малой растворимости в воде их абсолютное количество в паре тоже мало);
2) n = 1÷3 (в частности, H2SiO3). Слабые электролиты, заметно растворимые в воде и в довольно большом количестве переходящие в пар;
3) n > 4. Наименее растворимые в паре. Растворимость сильно зависит от плотности
Спсум = (Свраст + Сввзв) ω + Свраст · kр. (7)
Здесь под kp понимается суммарный коэффициент распределения (ионов и молекул).
Для улучшения качества пара уменьшают количество примесей в воде (Св) улучшают сепарацию пара от воды (ω) и промывают пар более чистой (питательной) водой, чем котловая вода, из которой пар был получен.
На рис. 15 показана наиболее распространенная в современных энергетических котлах высокого давления схема внутрибарабанных устройств. Внутренний диаметр барабана таких котлов равен 1600 мм при толщине стенок, определяемой прочностным расчетом и обычно превышающей 100 мм. Ввод пароводяной смеси из экранов осуществляется с двух сторон приблизительно на уровне оси барабана в смесительный отсек и далее – во внутрибарабанные циклоны, в которых происходит первичная сепарация пара от воды. Пар выходит в паровой объем барабана, а вода – в водяной. Нормальный уровень воды в барабане поддерживается на 200– 250 мм ниже оси барабана. Над внутрибарабанными циклонами расположено паропромывочное устройство в виде плоского дырчатого листа с закраинами, куда подается половина питательной воды (вторая половина направляется непосредственно в водяной объем, в котловую воду). Отверстия в промывочном устройстве рассчитывают так, чтобы в рабочем диапазоне нагрузок паропромывочное устройство работало в «беспровальном» режиме то есть вес столба воды на промывочном листе уравновешивался бы скоростным напором парового потока, текущего через отверстия листа. Вода с отмытыми примесями сливается в водяной объем, смешиваясь с котловой водой. Пар, частично освобожденный от примесей котловой воды за счет промывки более чистой питательной водой, подвергается естественной сепарации от некоторой доли промывочной воды и далее через потолочный дырчатый лист поступает в пароотводящие трубы и пароперегреватель. Потолочный дырчатый лист выполняет в какой-то мере и роль дополнительного сепаратора капельной влаги, а также способствует выравниванию паровой нагрузки по длине барабана.
Рис. 18. Схема внутрибарабанных устройств современного котла высокого давления: 1 – ввод пароводяной смеси от испарительных поверхностей нагрева; 2 – смесительный отсек (для выравнивания нагрузки по длине барабана); 3 – внутрибарабанные циклоны с верхними «крышками» для улавливания капельного уноса (жалюзийные сепараторы, крышки с удалением пристеночной пленки и т. д.); 4 – паропромывочное устройство: каналы для слива промывочной воды в котловую и ограждения (на рис. не показаны), препятствующие проходу пара из циклонов мимо промывочного устройства; 5 – подача 50 % питательной воды на промывочное устройство; 6 – подача 50 % питательной воды непосредственно в водяной объем барабана; 7 – потолочный дырчатый лист; 8 – пароотводящие трубы промытого пара в пароперегреватель и на собственные устройства, потребляющие насыщенный пар; 9 – линия аварийного слива котловой воды до нижнего допустимого уровня в случае перепитки котла; 10 – отбор котловой воды для непрерывной продувки; 11 – линия ввода корректирующих растворов; 12 – отвод котловой воды в опускные линии циркуляционных контуров (иногда на входе в опускные трубы устанавливают жалюзи, препятствующие захвату паровых пузырей в опускную систему)
Кроме описанных устройств, способствующих обеспечению чистоты пара, в барабане размещены другие элементы конструкции: устройства аварийного слива котловой воды при случайной перепитке; устройства отбора воды в непрерывную продувку; система подачи в котел корректирующих растворов (например, фосфатов). Конкретное выполнение таких конструкций и их размещение определяются при рабочем проектировании.
Кроме промывочных устройств и внутрибарабанных сепарационных конструкций для улучшения качества пара, а также уменьшения потерь теплоты и количества теплоносителя с продувочной водой используют схему ступенчатого испарения. Сущность ее заключается в том, что циркуляционные контуры разделяют на «чистый» и «солевой» отсеки. В «чистый» отсек выделяется порядка 85 % испарительных поверхностей нагрева (экранных секций), пароводяная смесь из которых вводится в соответствующую (бо́льшую) часть барабана, а 15 % смеси – в «солевой» отсек, расположенный в конце барабана. Чистый и солевой отсеки разделены стенкой с окнами в водяной и паровой частях. Питательная вода подается в чистый отсек, а непрерывная продувка из него питает солевую часть схемы, откуда ведется окончательная непрерывная продувка. Переток воды из чистого отсека в солевой происходит за счет разницы уровней от сопротивления водоперепускного окна. Пар, вырабатываемый солевой частью контура после сепарации в солевой части барабана, поступает через окно в перегородке в чистый отсек и, смешиваясь с паром чистого отсека, подвергается промывке, после чего направляется в перегреватель.
Такая схема последовательного питания благодаря большой величине продувки чистого отсека (производительность солевого отсека плюс окончательная продувка) позволяет 85 % пара получать из воды с низким солесодержанием, то есть более высокого качества. Выработка дополнительного количества пара в солевой части увеличивает солесодержание котловой воды и, соответственно, продувки, то есть уменьшает расход продувки, а значит, снижает потери.
В ряде случаев не ограничиваются использованием двухступенчатой схемы испарения, выполняют ее трехступенчатой, замыкая контур третьей ступени на так называемые выносные циклоны, что еще более увеличивает эффективность работы системы.
Следует отметить: схема ступенчатого испарения, предложенная еще в 1937 г. отечественным теплоэнергетиком Э. И. Ромом, в значительной мере не утратила своей актуальности и до настоящего времени используется достаточно широко.
Список используемой литературы.
1. Котлы тепловых электростанций и защита атмосферы. С.Е. Беликов, В.Р. Котлер. Изд.центр «Аква-Терм», 2008г.
2. Котельные установки и парогенераторы. Часть 2. Оборудование и процессы. С.К. Корякин, Б.В. Лебедев. Изд.ТПУ, 2012г.
3. Паровые котлы тепловых электростанций. Резников М.И., Липов Ю.М. 1981г.
4. Парогенераторные установки атомных электростанций. Рассохин Н.Г. 1987г.
Дата добавления: 2019-07-17; просмотров: 1266; Мы поможем в написании вашей работы! |
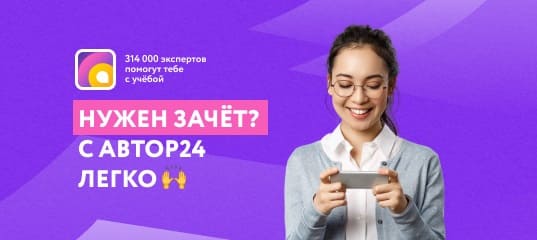
Мы поможем в написании ваших работ!