Получение порошков методом распыления расплава
Распыление расплава является относительно простым и дешевым технологическим процессом производства порошков металлов с температурой плавления примерно до 1600 ºС. Наиболее распространено распыление газовым потоком.
При такой схеме распыления на свободно истекающую струю металлического расплава направлен под углом к ее оси кольцевой газовый поток, создаваемый соплами, как бы охватывающими струю металла. В месте схождения всех струй газового потока, называемом «фокусом распыления», происходит разрушение струи расплава в результате отрыва от нее отдельных капель. На средний размер и форму образующихся частиц влияют мощность и температура газового потока, диаметр струи, температура, поверхностное натяжение и вязкость расплава. Кроме того, очень важно, в какой среде производят распыление, а также конструктивное оформление форсуночного устройства. В качестве газа используют инертный газ (азот, аргон, гелий) или воздух.
Получение металлических порошков из расплава основано на нарушении сплошности потока (струи) жидкости с первичным образованием прядей или капель под действием различных источников возмущений и их последующем разрушении (диспергировании) на дисперсные частицы энергоносителем. В настоящее время имеется много технологических способов диспергирования металлических расплавов, отличающихся схемами процесса и видом применяемого энергоносителя.
|
|
Многообразные технологические схемы по диспергированию металлических расплавов можно разделить на два основных вида:
· центробежное распыление
· форсуночное распыление
К центробежным относят разрушение вращающимися дисками (турбинками) и с цилиндрами с отверстиями (центрифугирование), через которые вытекает жидкость, дугой вращающегося плавящегося расходуемого электрода и др..
К форсуночному распылению металлических расплавов относят схемы с вертикальным расположением газовых или жидкостных форсунок и горизонтальным расположением газовых форсунок как одноструйных, так и многоструйных. К этим же схемам по принципу диспергирования расплавов можно отнести электрометаллизационный, плазменный (с «холодной плазмой»). Вне этих схем находятся методы: ультразвуковой, электроимпульсный, детонационный, с применением электромагнитного поля, электронного испарения – ионного или лазерным лучом.
Основные схемы форсуночного распыления жидких металлов и сплавов, имеют вертикальное или горизонтальное расположение форсуночных устройств. Наибольшее практическое применение при изготовлении порошков из расплавов распылением газами или жидкостями высокой энергии в промышленных масштабах получила схема с вертикальным расположением форсуночного устройства.
|
|
Схема с вертикальным расположение форсуночного устройства: 1- металлоприемник; 2- струя; 3- форсуночное устройство; 4- кольцевое сопло Лаваля; 5- газовые потоки; α/2 угол атаки струй расплава и газа
Применение высокотемпературных электропечей вакуумной плавки, плавки под защитными газами обеспечивает возможность получать расплавы жаропрочных и качественных сплавов высокой чистоты по примесям внедрения, с оптимальными физическими и технологическими свойствами (жидкотекучестью). Такие высокоперегретые расплавы характеризуются высокой склонностью к распылению на дисперсные частицы с различной формой: сферической, осколочной. Схема позволяет в широких пределах изменять скорости охлаждения жидких частиц путем применения специальных хладоагентов, подаваемых в зону охлаждения и кристаллизации частиц (микрослитков), свободного полета жидких частиц и получать более дисперсные микрослитки. Изменением условий теплообмена жидких частиц можно изменять скорость охлаждения с до
℃/с и получать структуры переохлажденных жидкостей (так называемы амортизированные структуры). По указанной схеме в серийных масштабах получают порошки коррозионностойких и инструментальных сталей, жаропрочных сплавов на основе Ni и Cr, ферросплавов, магнитных сплавов и пр.
|
|
Схема с вертикальным расположение форсуночного элемента многоструйного распыления: 1- струя расплава; 2- трубопроводы; 3- отверстия Лаваля; α/2 – угол атаки струй расплава газовым энергоносителем
Распылительные форсунки: а- со сплошной кольцевой щелью; б- со щелью типа сопла Лаваля; в и г- со сплошной кольцевой щелью конструкции ИНМ АН УССР; 1- наружная полость; 2- внутренняя полость; 3- кольцевая щель; 4- сливной стакан;
5-металлоприемник; д и е – конструкции КЗФ с прерывистой кольцевой щелью (шлицевые); 6- верхний фланец; 7- конус; 8- корпус форсунки; 9- нижний фланец; 10- вставка конуса; 11- сливной стакан; А- форсунка в сборе; С- форма вставки конуса с прерывистой щелью (для сравнения D- форма вставки конуса со сплошной щелью); DK- диаметр конуса B- «вставка» стакана
При распылении инертным газом, форма частиц получаемого порошка всегда сферическая, иногда с прилипшими частицами – «спутниками». Сферическая форма обеспечивает более высокую плотность паковки и хорошие свойства текучести. Если используется воздух, то форма частиц зависит от оксидных характеристик. Например: порошки из латуни и алюминия – неправильной формы, а медные порошки почти сферические. При использовании инертных газов можно свести к минимуму окисление. Однако, существуют ограничения для таких металлов и их сплавов как Al и Mg, у которых оксидные пленки трудно, а иногда и опасно удалять. В результате же распыления воздухом получают значительное окисление. Но и при распылении инертным газом в камере распыления всегда присутствуют пары воды, создающие окислительную атмосферу. В связи с этим частицы порошка загрязнены кислородом, азотом и водородом. Для улучшения свойств и удаления указанных примесей порошки, как правило, подвергают отжигу в восстановительной атмосфере.
|
|
Форма частиц порошков под микроскопом, полученные при распылении инертным газом
Дата добавления: 2019-07-15; просмотров: 2483; Мы поможем в написании вашей работы! |
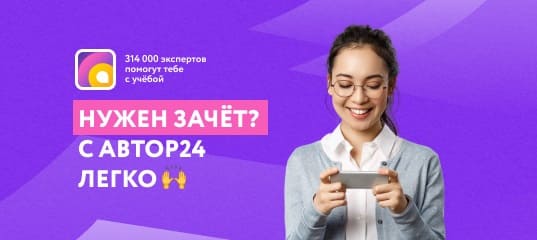
Мы поможем в написании ваших работ!