Технологическая схема промежуточной нефтеперекачивающей станции
ЭКСПЛУАТАЦИЯ НАСОСНЫХ И КОМПРЕССОРНЫХ СТАНЦИЙ
Гр. 65-01
1. Классификация компрессорных станций по давлению, производительности, по функциональному назначению.
По давлению:
Ø низкого давления от 0,3 до 2,5 МПа (от 3 до 25 кг/см ), используются на головных компрессорных станциях при транспортировке газа с истощённых месторождений и нефтяного газа с промыслов;
Ø среднего давления от 2,5 до 6 МПа (от 25 до 60 кг/см ), работают на промежуточных компрессорных станциях для увеличения пропускной способности газопроводов.;
Ø высокого давления от 6 до 35 МПа (от 60 до 350 кг/см ), используют для закачки газа в подземные хранилища.
Ø сверхвысокого давления свыше 35 МПа (свыше 350 кг/см ).
По производительности:
Ø малые станции — производительность до 1,7 м /с (100 м /мин);
Ø средние — производительность от 1,7 до 8,3 м /с (100 ÷ 500м /мин);
Ø большие — производительность свыше 8,3 м /с (500 м /мин).
По функциональному назначению:
Ø головные компрессорные станции (ГКС) устанавливаются непосредственно по ходу газа после газового месторождения. Назначением ГКС является создание необходимого давления технологического газа для его дальнейшего транспорта по магистральным газопроводам. Принципиальным отличием ГКС от линейных станций является высокая степень сжатия на станции, обеспечиваемая последовательной работой нескольких газоперекачивающих агрегатов (ГПА) с центробежными нагнетателями или поршневыми газомото-компрессорами.
|
|
Ø линейные (промежуточные) компрессорные станции устанавливаются на магистральных газопроводах, как правило, через 100-150 км. Назначением КС является компремирование (доведение) поступающего на станцию природного газа, с давления входа до давления выхода, обусловленных проектными данными. Тем самым обеспечивается постоянный заданный расход газа по магистральному газопроводу. В России строятся линейные газопроводы в основном на давление = 5,5 МПа и = 7,5 МПа.
Ø дожимные компрессорные станции (ДКС) устанавливаются на подземных хранилищах газа (ПХГ). Назначением ДКС является подача газа в подземное хранилище газа от магистрального газопровода и отбор природного газа из подземного хранилища (как правило, в зимний период времени) для последующей подачи его в магистральный газопровод или непосредственно потребителям газа. ДКС строятся также на газовом месторождении при падении пластового давления ниже давления в магистральном трубопроводе. Отличительной особенностью ДКС от линейных КС является высокая степень сжатия 2-4, улучшенная подготовка технологического газа (осушители, сепараторы, пылеуловители), поступающего из подземного хранилища с целью его очистки от механических примесей и влаги, выносимой с газом.
|
|
Около потребителей газа строятся также газораспределительные станции (ГРС), где газ редуцируется до необходимого давления (= 1,2; 0,6; 0,3 МПа) перед подачей его в сети газового хозяйства.
2. Классификация компрессорных станций по конструктивному исполнению.
Ø Компрессорные станции в традиционном исполнении. Основные и перекачивающие агрегаты и часть вспомогательного оборудования размещены в тяжелых капитальных зданиях, главным образом с железобетонным несущим каркасом. При этом большое число единиц основного и вспомогательного оборудования поступает с заводов – изготовителей не укрепленными блоками, а в виде отдельных частей и деталей с последующей их монтажной сборкой на строительной площадке. КС такого типа отличаются отличаются большой трудоёмкостью строительства и монтажа и длительными сроками их сооружения. В настоящее время не сооружают, но уже построенные находятся в эксплуатации.
Ø Блочно-комплектные компрессорные станции с размещением основных перекачивающих агрегатов в общих или индивидуальных зданиях;
|
|
Ø Полностью блочно-комплектные КС с размещением всех перекачивающих агрегатов и оборудования в блок- боксах или блок – контейнерах, включая блочно-модульные станции.
На всех строящихся магистральных газопроводах сооружают только блочно-модульные и блочно-комплектные КС. При этом степень блочности станций , т.е. степень насыщения их блочно-модульными и блочно-комплектными устройствами различная.
https://studfiles.net/preview/3579148/page:11/
Применяют два вида КС, имеющих разные технологические схемы:
Ø КС, оборудованные газомоторными поршневыми компрессорами (ГМК);
Ø КС, оборудованные центробежными нагнетателями с приводом от газотурбинных установок (ГТУ) или электродвигателей.
3. Назначение и состав сооружений компрессорных станций.
Назначение:
- очистка транспортируемого газа от механических примесей и жидкости;
- сжатие газа в центробежных нагнетателях или в поршневых машинах;
- охлаждение газа после сжатия в специальных охладительных устройствах;
- измерение и контроль технологических параметров;
- управление режимом работы газопровода путем корректировки технологического режима работы компрессорного цеха.
|
|
Состав:
Ø Основное технологическое оборудование КС – ГПА, составляющие компрессорный цех.
Ø Вспомогательное оборудование I группы:
- узел подключения КС к магистральному газопроводу; - технологические коммуникации с запорной арматурой;
- установки по очистке газа от пыли и влаги (пылеуловители и фильтр-сепараторы;
- оборудование для охлаждения газа после его компримирования (повышение давления компрессорами);
- оборудование системы смазки, уплотнения для центробежных нагнетателей, регулирования и защиты ГПА: оборудования системы охлаждения масла, оборудование системы подготовки топливного, пускового и импульсного газа.
- склады горюче-смазочных материалов; материалов и реагентов; оборудования; трубопроводов; арматуры и т. д.;
- ремонтно-эксплуатационные и служебно-эксплуатационные помещения;
- главный щит управления.
Ø Вспомогательное оборудование II группы: система водоснабжения, канализации, связи, телемеханики, электроснабжения, пожарной и охранной сигнализации, автоматического пожаротушения, молниезащиты, административно-бытовые помещения.
Рисунок 1 – Технологическая схема компрессорной станции с центробежными нагнетателями: 1 – магистральный газопровод; 2 – кран; 3 – байпасная линия; 4 – пылеуловитель; 5 – газоперекачивающий агрегат; 6 – продувные свечи; 7 – АВО газа; 8 – обратный клапан
Газ из магистрального газопровода (1) через открытый кран (2) поступает в блок пылеуловителей (4). После очистки от жидких и твердых примесей газ компримируется газоперекачивающими агрегатами – ГПА (5). Далее он проходит через аппараты воздушного охлаждения – АВО (7) и через обратный клапан (8) поступает в магистральный газопровод (1).
Рисунок 2. Устройство типовой КС.
1 - узел подключения КС к МГ; 2 - камеры пуска и приёма очистного устройства; 3 - установка очистки технологического пылеуловители и фильтры-сепараторы; 4 - установка охлаждения технологического газа; 5 - газоперекачивающие агрегаты; 6 - технологические трубопроводы обвязки КС; 7 - запорная арматура технологической обвязки агрегатов; 8 - установка подготовки пускового и топливного газа; 9 - установка подготовки импульсного газа; 10 - главный щит управления и система телемеханики; 11 - энергетическое оборудование.
4. Нагнетатели, применяемые на КС магистральных газопроводов. Обвязка нагнетателей.
Виды компрессоров:
Компрессор поршневой - высокие степени повышения давления и высокие абсолютные давления, переменные режимы, сравнительно небольшие потоки и мощности, нашли широкое применение на магистральных газопроводах и станциях подземного хранения газа (СПХГ).
Компрессор винтовой - высокие степени повышения давления при небольших абсолютных давлениях и небольших перепадах давления, переменные режимы, сравнительно небольшие потоки и мощности.
Компрессор центробежный - большие потоки и мощности, предпочтительно небольшие степени повышения давления и невысокие абсолютные давления, постоянные режимы. В настоящее время на КС магистральных газопроводов поршневые ГПА заменяются центробежными ГПА с авиационным приводом различных отечественных производителей.
https://studopedia.su/14_110004_vvedenie.html - схемы с поршневым и ц/б нагнетателем.
Обвязка нагнетателей компрессорного цеха может иметь три варианта. Полнонапорные нагнетатели соединяются между собой только параллельно. Неполнонапорные, создающие недостаточно высокое давление, обвязываются по различным схемам - параллельно, последовательно, по смешанной схеме соединения.
Обычно неполнонапорные машины в компрессорном цехе разбивают на группы. Внутри каждой группы нагнетатели соединяются последовательно, а группы между собой - параллельно.
Количество нагнетателей в группе соответствует числу ступеней сжатия газа на КС. Существующее оборудование позволяет иметь на станциях, одно-, двух- и трехступенчатое сжатие. Потребное количество ступеней сжатия в каждом отдельном случае определяется технико-экономическим расчетом (см. раздел 4.4).
Отмеченные особенности КС с неполнонапорными нагнетателями привели к появлению двух вариантов обвязки неполнонапорных машин - по смешанной схеме соединения и по коллекторной, схеме.
Центробежные нагнетатели компрессорных станций могут работать по следующим основным схемам: последовательная, последовательно-параллельная и коллекторная. Указанным схемам соответствует различная обвязка нагнетателей технологическими трубопроводами и запорной арматурой.
Наиболее простая из указанных схем – последовательная, характерная для неполнонапорных нагнетателей (степень сжатия 1,23…1,25). Иногда необходимо сжатии 2 и 3-х ступенсатое. Недостаток последовательной схемы – ограниченная пропускная способность турбоагрегатов, а также неравномерная нагрузка их; последние по ходу газа работают в более напряженном режиме.
Этого недостатка в значительной степени лишена схема с последовательно-параллельно подключенными центробежными нагнетателями, характерная для полнонапорных нагнетателей (степень сжатия 1,45-1,51). (рис. 8.2).
Рис. 8.2 Технологическая схема КС, оснащенная центробежными нагнетателями с последовательно-параллельным подключением. В данной схеме турбоагрегаты разбиты на две группы, а средний выполняет роль резервного и может работать как в первой, так и во второй группах. В каждой группе центробежные нагнетатели работают последовательно, в то время как группы в целом подключены к газопроводу параллельно. Подобная схема работы осуществляется и при большем числе турбоагрегатов. При этом число параллельно работающих групп увеличивается. Производительность газопровода можно регулировать, изменяя число параллельно работающих групп, а степень повышения давления, изменяя число турбоагрегатов, работающих в каждой группе. Недостатком параллельно-последовательной схемы можно считать то, что при ремонте среднего центробежного нагнетателя невозможна последовательная работа центробежных нагнетателей первой группы с нагнетателями второй группы. Эта схема имеет и другие существенные недостатки. Так, аварийный останов одного из турбоагрегатов группы влечет за собой останов второго агрегата; затруднен оперативный ввод в работу резервных турбоагрегатов, так как при этом возникает необходимость перестройки всей схемы с переключением большого числа кранов. Указанные недостатки особенно заметны при большом числе параллельно работающих групп.
Наиболее прогрессивна технологическая схема с коллекторной обвязкой центробежных нагнетателей (рис. 8.3).
Основные преимущества коллекторной схемы обвязки нагнетателей:
1. полная взаимосвязь турбоагрегатов в пределах каждой ступени сжатия;
2. сокращение числа запорных кранов большого диаметра (при наличии коллекторов отпадает необходимость в установке полнорасходных кранов 3);
3. уменьшение числа резервных турбоагрегатов;
4. повышение степени оперативности ввода резервных агрегатов в работу;
5. пониженная чувствительность системы к аварийному останову одного из турбоагрегатов, особенно при большом их числе.
5. Требования, предъявляемые к центробежным нагнетателям КС.
ГПА с центробежным нагнетателем широко применялись в CCCP и за рубежом на магистральных газопроводах в качестве основных агрегатов; их также используют для работы в качестве первой ступени сжатия на подземных хранилищах. Различают центробежные нагнетатели одноступенчатые (неполнонапорные) со степенью сжатия 1,23-1,25 и двухступенчатые (полнонапорные) -1,45-1,7. Центробежные нагнетатели характеризуются значительно большей, чем у поршневых компрессоров, производительностью (12-40 млн. м3/сутки). В них отсутствуют внутренние трущиеся части, требующие смазки (за исключением подшипников), создаётся равномерный (без пульсации) поток газа. Для их установки (в связи с малым весом и габаритами, а также уравновешенностью вращающихся частей) требуются меньшие помещения и сооружаются облегчённые фундаменты. При применении ГПА с центробежными нагнетателями вследствие их большой производительности упрощается технологическая схема компрессорных станций, уменьшается количество запорной арматуры и др. Недостаток неполнонапорных центробежных нагнетателей - необходимость включения в работу двух последовательно соединённых агрегатов для достижения степени сжатия газа 1,45-1,5. Это приводит к увеличенному расходу топливного газа в газотурбинной установке. Кпд агрегатов с центробежными нагнетателями до 29%, с регенератором тепла до 35%. Приводом ГПА служит газотурбинная установка или электродвигатель. В CCCP изготовливались ГПА с газотурбинным приводом мощностью 6, 10, 16 и 25 тысяч кВт.
К компрессору предъявляются те же требования, что и к двигателю. Помимо общих требований предъявляются и некоторые специфические: - обеспечение заданного секундного расхода воздуха; - обеспечение заданной степени повышения давления; - обеспечение устойчивой, т.е. без помпажа и пульсации, работы в широком диапазоне частоты вращения ротора.
Источник: http://refleader.ru/polpolotraty.html
Основные требования, предъявляемые к нагнетателям, эксплуатирующимся на станциях ПХГ — это минимальные утечки масла и повышенная надежность оборудования.
Требования к компрессорам. Должны обеспечить:
заданный расход;
заданную степень повышения давления;
заданный КПД (экономичность);
устойчивость работы;
надежность;
живучесть;
обеспечение заданного ресурса;
контролепригодность;
пожаробезопасность;
минимальная масса и габариты;
технологичность производства;
эксплуатационная технологичность;
минимальная себестоимость производства;
возможность развития;
экологические ограничения (по шуму).
6. Приводы компрессорных газоперекачивающих агрегатов (ГПА). Преимущества и недостатки.
Привод - это устройство для приведения в действие машин и механизмов, состоящее из источника энергии (двигателя), передаточного механизма и аппаратуры управления.
Приводы в зависимости от применяемых двигателей компрессоров подразделяют на:
Ø электропривод-(источником энергии является электродвигатель постоянного или переменного тока (синхронный или асинхронный);
Ø привод от двигателя внутреннего сгорания (источником энергии является поршневой
двигатель, работающий на газе);
Ø газотурбинный привод - источником энергии является газовая турбина.
Требования к приводам:
быть простыми по конструкции,
надежными в работе,
экономичными,
иметь высокую степень автоматизации, т. е. иметь способность привода автоматически приспосабливаться к изменяющимся в процессе работы условиям с обеспечением наиболее экономичного использования мощности.
1. На КС применяются асинхронные и синхронные электродвигатели мощностью от 400 до 12500 кВт типа СТД - 4000 - 2, СТД - 12500 - 2 и A3 - 4500 - 1500. Газоперекачивающие агрегаты имеют маркировку по типу электродвигателя, например: ГПА - СТД - 4000, ГПА - СТД - 12500. Преимущества: дешевые монтажные работы; большой ресурс, большая эксплуатационная надежность; эксплуатационные расходы на 50% меньше по сравнению с ГТД; простота автоматизации и управления, экологическая чистота, пожаробезопасность. Недостатки: ограниченность районов с дешевой электроэнергией; плохая приспосабливаемость к переменному режиму работы газопровода из-за постоянной частоты вращения (3000 об./мин).
2. Широко применяют в газовой и нефтяной промышленности для привода поршневые двигатели внутреннего сгорания в качестве горючего используют перекачиваемый газ. Перспективным направлением применения можно считать применение на компрессорных цехах при ПХГ, станциях низкотемпературной сепарации, газопроводах небольшой пропускной способности. Преимущества: большая степень сжатия; высокий КПД. Недостатки: малая единичная мощность; большая металлоемкость и сложность конструкции; малый межремонтный ресурс от 3-4 до 7-8 тыс. т; трудность полностью автоматизировать обслуживание.
3. Современные ГПА в большинстве используют в качестве привода газотурбинные двигатели (высокий КПД, большая удельная мощность и простота в эксплуатации по сравнению с поршневыми двигателями при условии больших расходов и небольшой степени сжатия ).
На КС нашли применение стационарные ГТУ с регенерацией теплоты, стационарные ГТУ без регенерации теплоты; конвертированные авиационные и судовые ГТД; комбинированные ГТУ, состоящие из авиационного газогенератора и стационарной силовой турбины.
Преимущества: низкая стоимость установленного киловатта при компактно сти агрегата; высокая быстроходность; простота регулирования нагрузки за счет переменной частоты вращения; способность заметно увеличивать располагаемую мощность в холодные времена года; простая автоматизация обслуживания.
Недостатки: умеренная экономичность старых и некоторых выпускаемых ГТУ; потребность в организации снабжения запасными частями для узлов; ограниченный срок службы; трудоемкость ремонт.
7. Узел подключения компрессорной станции (КС) к магистральному газопроводу (МГ).
Узел подключения КС к МГ (8) (Рис.5) обеспечивает поступление газа в КЦ по входному газопроводу (всасывающему шлейфу) и подачу его в МГ после компримирования по выходному газопроводу (нагнетательному шлейфу).
Рис.5
Узел включает проходные краны 7, 8, 20, свечные краны 17, 18, охранные краны 19(А), 21 (Б), перепускные краны 36 (22), Збр (22р), дроссель Д.
Входной кран 7 - предназначен для подачи газа в цех, его постоянное положение - "открыт" при работе КЦ. Кран 7 имеет обводной кран 7р с дросселем, предназначенный для заполнения газом всей системы КЦ. Только после выравнивания давления в МГ и технологических коммуникациях КЦ (с помощью крана 7р) производится открытие крана 7. Это делается во избежание гидравлического удара на шаровой кран большого диаметра.
Выходной кран 8 - предназначен для подачи газа в МГ после его компримирования и охлаждения. Выходной кран 8 также имеет обводной кран 8р и дроссель. Перед краном 8 устанавливают обратный клапан. Его назначение - предотвратить обратный поток газа со стороны МГ при возможной неисправности крана 8.
Секущий кран 20 - обеспечивает нормальную работу КЦ при компримировании. Он рассекает МГ на части низкого и высокого давления. При работе КЦ кран 20 закрыт: При открытом положении крана 20 газ проходит мимо КЦ. Диаметр крана 20 должен соответствовать диаметру МГ.
Свечные краны 17,18 предназначены для сброса газа в атмосферу из всех трубопроводов и коммуникаций КЦ при аварийных (или запланированных) остановках КЦ.
Охранные краны 19,21. Их назначение - отключение всей КС в аварийных ситуациях (в частности, при авариях в районе узла подключения, разрыве газопровода между охранным краном и секущим краном 20).
Краны 36, обводной кран 3бир и дроссель "Д" образуют большое станционное кольцо - пусковой контур КЦ. Установлены на перемычке между выходным (за установкой охлаждения) и входным газопроводом КЦ. Большое станционное кольцо используется для противопомпажного регулирования КЦ (с помощью перепуска охлажденного газа с выхода на вход) при изменении режима МГ.
Дроссельный кран "Д" ограничивает расход газа при работе по большому станционному кольцу. Предназначен для создания необходимого сопротивления пускового контура КЦ (перепада давления между входом и выходом). Иначе ГПА будут работать в зоне больших объемных расходов газа, при которых резко возрастут усилия на роторы нагнетателей. Степень открытия крана "Д" определяется опытным путем при его наладке во время монтажа КЦ. Иногда вместо крана используют дроссельную шайбу определенного диаметра.
Обводной кран 3бир используется при небольших изменениях расхода КЦ, обеспечивая удаленность режима работы КЦ от зоны помпажа.
Узлы приема и запуска очистного поршня (5,6) (Рис5) предназначены для приема поршня, запущенного в МГ на предыдущей КС, а также запуска поршня по ходу газа в сторону последующей КС. Запуск поршня производят периодически для удаления мехпримесей и влаги из МГ. В результате обеспечивается увеличение пропускной способности МГ до проектной и снижается перерасход топливного газа ГПА.
Блок очистки технологического газа (7) предназначен для очистки транспортируемого газа от мехпримесеи и капельной влаги перед поступлением его в нагнетатель. В его состав входят масляные или циклонные пылеуловители с технологической обвязкой и запорной арматурой.
Блок охлаждения газа (3) предназначен для охлаждения технологического газа, нагреваемого в процессе сжатия в ЦБН (средний нагрев газа в группе ЦБН составляет 35 - 40°С). Блок обеспечивает поддержание температуры газа на выходе из КЦ в пределах до 40 - 45°С. Блок состоит из аппаратов воздушного охлаждения газа (АВОг) и технологической обвязки с запорной арматурой.
Узел 6-х кранов (4) (Рис5) состоит из нескольких кранов. Количество 6-х кранов соответствует количеству полнонапорных ГПА или группы ГПА с неполнонапорными нагнетателями. Их устанавливают на специальных перемычках между выходными шлейфами до (иногда после) АВОг и входными шлейфами после крана 7. При открытых 6-х кранах газ после ЦБН поступает на вход ПУ.
Узел 6-х кранов предназначен:
- для обеспечения загрузки ГПА при запуске, поддерживая минимально допустимую степень сжатия ЦБН во время работы ГПА до загрузки в"трассу";
- регулирования при защите ЦБН от помпажа при различных режимах работы КЦ. Например, при последовательной работе нагнетателей в случае аварийной остановки одного ГПА степень сжатия газа в выходном коллекторе КЦ будет больше степени сжатия другого ГПА. Нагрузка на второй нагнетатель возрастет, он попадет в помпаж;
- отключения ГПА из режима работы в "трассу" и переход на режим работы "кольцо".
Кран 6 может иметь обводной регулирующий кран 6р. Его используют при небольших изменениях расхода газа через ЦБН. Способ плавного регулирования режима работы ЦБН также обеспечивает необходимую удаленность режима работы нагнетателя от зоны помпажа и называется байпасированием.
Все краны технологической схемы КЦ имеют дистанционное управление с главного щита управления (ГЩУ). И все краны КЦ, кроме крана 20, имеют автоматическое управление от ключа "Аварийный останов КЦ".
8. Система очистки газа от механических примесей.
На компрессорных станциях газопровода предусматривают очистку газа от механических примесей (твердых и жидких частиц). Масло систематически попадает в газопровод через компрессоры и центробежные нагнетатели, установленные на компрессорных станциях. Очистка газа перед подачей его в газопровод крайне необходима. Твердые частицы, находящиеся в газе, попадая в поршневые компрессоры, ускоряют износ поршневых колец, клапанов и цилиндров, а в центробежных нагнетателях - износ рабочих колес и самого корпуса нагнетателя. Кроме того, они разрушают арматуру, установленную на линейной части газопровода, на компрессорных и газораспределительных станциях. Жидкие частицы воды и копденсата, скапливаясь в пониженных местах, сужают сечение газопровода и способствуют образованию в нем гидратных и гидравлических пробок.
Промышленные пылеулавливающие аппараты в соответствии с принципами очистки газа разделяют на две группы: сухого отделения пыли и мокрого отделения пыли. К аппаратам сухого отделения пыли относят:
1) гравитационные сепараторы (степень очистки 70-80 %);
2) циклонные пылеуловители (степень очистки 85-98 %);
3) фильтры и фильтр-сепараторы (степень очистки до 99%, очищают поток газа от капель воды и конденсата). Принцип действия аппаратов сухого отделения пыли состоит в искусственном осаждении пыли под действием сил тяжести и в результате снижения скорости течения газа. К аппаратам мокрого отделения пыли относят масляные пылеуловители, в которых очистка газа происходит при помощи промывки газа жидкостью. Такие пылеуловители наряду с циклонными нашли широкое применение в газовой промышленности. Достоинство масляных пылеуловителей высокая степень очистки газа (97-98%). Недостатки большая металлоемкость, большое гидравлическое сопротивление, унос промывочной жидкости, в качестве которой применяют соляровое масло. [3]
9. Масляные, циклонные пылеуловители. Фильтры – сепараторы.
Рисунок 1. Масляный пылеуловитель.
1 - сепараторное устройство; 2 - выходной патрубок; 3-5 - контактные и дренажные трубки; 6 - люк; 7 - входной патрубок; 8 - отбойный козырек.
Масляный пылеуловитель представляет собой вертикальный цилиндрический рассчитанный на максимальное рабочее давление газа в газопроводе. Пылеуловитель состоит из трех секций: нижней промывочной 1 (от нижнего днища до перегородки 8), в которой все время поддерживается постоянный уровень масла; средней осадительной 2 (от перегородки 8 до верхней перегородки), где газ освобождается от крупных частиц масла, и верхней отбойной 1 (от перегородки 6 до верхнего днища), где происходит окончательная очистка газа от масла.
Циклонный пылеуловитель представляет собой аппарат вертикальной цилиндрической формы со встроенными циклонами и состоит из трех технологических секций: распределения поступившего газа, очистки газа и сбора жидкости и механических примесей. Неочищенный газ поступает через боковой входной патрубок, к которому приварены пять циклонов, расположенных звездообразно по кругу. За счет центробежной силы происходит отбрасывание и осаждение влаги и механических примесей, которые удаляются из аппарата автоматически через дренажный штуцер. Рисунок 3. Циклонный пылеуловитель.
1 - корпус; 2 - патрубок; 3 - выходная труба; 4 - бункер.
Циклонный пылеуловитель состоит из двух секций: нижней - отбойной и верхней - осадительной. Циклонный пылеуловитель представляет собой аппарат вертикальной цилиндрической формы со встроенными циклонами и состоит из трех технологических секций: распределения поступившего газа, очистки газа и сбора жидкости и механических примесей, Неочищенный газ поступает через боковой входной патрубок, к которому приварены пять циклонов, расположенных звездообразно по кругу. На предприятиях больше всего отдают предпочтение масляным пылеуловителям, потому что качество очистки больше чем циклонных пылеуловителях. [1]
Гравитационные сепараторы могут быть вертикальными и горизонтальными. Они работают по принципу выпадения взвеси под действием силы тяжести при уменьшении скорости потока газа. Вертикальные гравитационные аппараты имеют лучшие условия очитки, чем горизонтальные, рекомендуется для сепарации газов, содержащих крупные частицы пыли. Гравитационные сепараторыобладают небольшой эффективностью и малой производительностью по газу. Для повышения производительности и эффективности их работы необходимо увеличивать габариты.
Рисунок 2. Горизонтальный гравитационный сепаратор.
1- сепарационные насадки; 2 - сепарационные решетки; 3 - сетчатые каплеуловители.
10. Эксплуатация пылеуловителей.
При эксплуатации пылеуловителей обслуживающий персонал осуществ-
ляет следующие основные операции:
- ежесменную проверку исправности арматуры, контрольно-измери-
тельных приборов и предохранительных устройств;
- постоянный контроль над технологическими режимами работы пыле-
уловителей, их соответствие паспортным данным;
- периодический контроль работы аппаратов за показаниями приборов с
регистрацией в журнале расхода газа, давления, температуры, перепада давле-
ний и числа продувок (через каждые 2 часа);
- постоянный контроль при минусовых температурах окружающего воздуха
за работой системы обогрева аппаратов, трубопроводов, арматуры и КИПиА;
- контроль за автоматическим сбросом жидкости и механических приме-
сей из сборника, в исключительных случаях проводят кратковременную про-
дувку аппарата вручную с периодичностью не реже 4 раза в сутки.
Аппарат немедленно останавливают:
- при превышении в нём максимально допустимого давления и перепада
давлений;
- при неисправности предохранительного клапана, манометра и невоз-
можности его замены;
- при обнаружении в основных элементах аппарата трещин, выпучин,
значительных утолщений стенок, пропусков или потения в сварных швах, течи
в болтовых соединениях;
- при разрыве прокладок;
- возникновения пожара, непосредственно угрожающего аппарату;
- забивка гидратами циклонов.
К разборке аппарата, остановленного для внутреннего осмотра, чистки и
ремонта, приступают только после полного освобождения его от газа, жидкости
и механических примесей; отключения аппарата от технических трубопроводов
заглушёнными с ясно видимыми хвостовиками; продувки его инертным газом;
пропарки; помывки водой и продувки чистым воздухом.
Ледяные и гидратные пробки в аппарате устраняют разогревом их паром
или горячей водой.
11. Система охлаждения газа на КС – аппаратов воздушного охлаждения (АВО).
Компремирование газа на КС приводит к повышению его температуры на выходе станции, чтоможет привести к разрушению изоляции трубопровода, увеличивается объемный расход газа, снижается подача и увеличиваются затраты на компремирование. В северных районах страны газ надо охлаждать до отрицательных температур чтобы не протаивали грунты, иначе они вспучиваются, смещается трубопровод, что приводит к авариям.
Охлаждение газа на КС в настоящее время производится с помощью аппаратов воздушного охлаждения газа АВО. Рис. 11.1 План-схема обвязки аппаратов воздушного охлаждения газа:
1 - аппарат воздушного охлаждения газа; 2, 4, 6, 7 - коллекторы;
3 - компенсаторы; 5 - свечи; 8 - обводная линия
Глубина охлаждения технологического газа не может быть ниже температуры наружного воздуха, что особенно сказывается в летний период эксплуатации. Установка охлаждения газа должна быть общей для всех ГПА компрессорного цеха, иметь коллекторную обвязку и обводную линию. Количество АВО газа выбирается исходя из расчетной среднегодовой температуры наружного воздуха, среднегодовой температуры грунта и оптимальной среднегодовой температуры охлаждения газа. Последняя принимается на 10…15°С выше расчетной среднегодовой температуры наружного воздуха.
Рис. 11.2. Схема подключения аппарата воздушного охлаждения (при нижнем расположении вентилятора):
1 - воздушный холодильник газа 2АВГ-75; 2 - свеча; 3, 4 - коллекторы входа и выхода газа
По принципу работы АВО представляют собой теплообменники, состоящие из 2-х основных частей: поверхности охлаждения, и системы подачи воздуха, включая приводы вентиляторов. Охлаждаемым теплоносителем является сжатый до высокого давления природный газ, движущийся внутри трубок малого диаметра. Данные трубки имеют внешнее оребрение с целью интенсификации теплообмена, и обтекаются охлаждающим теплоносителем, в качестве которого выступает нагнетаемый вентиляторами атмосферный воздух. Оребренные трубки аппарата обычно разделены на несколько групп, называемых секциями. Каждый АВО, в зависимости от типа, может иметь от 1-го до 6-ти вентиляторов.
На КС аппараты воздушного охлаждения обычно объединяются в станции, в рамках которых несколько соединенных параллельно аппаратов АВО образуют блок. Основная проблема при эксплуатации АВО газа в том, что на наружных оребренных поверхностях АВО осаждаются загрязнения. Аппараты воздушного охлаждения газа - экологически чистые, не требуют расхода воды, относительно просты в эксплуатации.
12. Преимущества и недостатки аппаратов воздушного охлаждения (АВО).
Преимущества:
- АВО используются там, где применение других систем охлаждения (например, водой из-за отсутствия вблизи природных источников воды)технически не возможно или не целесообразно.
- Отсутствуют проблемы с коррозией и загрязнением, связанные с применением охлаждающей воды. – Сохраненяется чистота охлаждаемых сред благодаря замкнутым контурам;
–Можно устанавливать в любых климатических и природных зонах;
– Невысокие эксплуатационные затраты, просты в эксплуатации;
– Экологичность (практически отсутствует воздействие на окружающую среду);
- При выходе из строя вентилятора охлаждение идет за счет естественной конвенции (25-30% от необходимого съема тепла).
- Не требуют расхода воды, относительно просты в эксплуатации.
Недостатки:
- на наружных оребренных поверхностях АВО осаждаются частички органического (тополиный пух, цветочный пух, частицы сухой травы и др.) и неорганического происхождения (песок, пыль), слой окисла алюминия на оребренных поверхностях.
- высокая стоимость аппаратов
- разная производительность по временам года: в летний период года (высокие температуры газа и грунта, но низкая производительность); начало зимнего периода (высокая производительность, еще относительно высокая температура грунта и низкая температура воздуха);
- в зимние месяцы включение всех аппаратов на предыдущей КС приводит к охлаждению транспортируемого газа до температуры, которая может привести к выпадению гидратов;
- зависимость от работы предыдущей КС.
( не нашла в инете НЕДОСТАТКИ, сама придумала)
13. Эксплуатация аппаратов воздушного охлаждения газа (АВО).
- Регулировка расхода : механизмом поворота лопастей вентилятора.
- Регулировка температуры: водяными форсунками, установленными под вентилятором.
- защита от температурной деформации жестко закрепленных трубных решеток ослаблением крепления
- Следить за целостностью предохранительной сетки, защищающей поверхности труб или ребер.
- Поскольку трубные решетки закреплены достаточно жестко, то в процессе работы могут возникнуть температурные деформации или разность температуры рабочей среды и воздуха.
Ремонт.
1. Отключение аппарата от коммуникаций и слив теплоносителей.
2. Отключение аппарата от системы заглушками.
3. Промывка водой и пропарка.
4. Гидроиспытание (опрессовка). Испытание давлением (рабочим и ниже ДО, рабочим и выше ПОСЛЕ ремонта. Вакуумом – соединение труб с решетками.
5. Чистка (от соли, накипи, кокса, грязи, смолы):
- механическая с помощью сверл, фрез, буров, скребков, бойков, щеток, ершей. Трудозатратна, возможны повреждения поверхностей, проводится для разборных аппаратов.
- гидромеханическая:
o водоструйная чистка - энергией струи воды высокого давления (15…100МПа), удаляет ил, кокс, смолы; вода используется холодная и горячая; чистка производится в обе стороны; аппарат разбирается
o пескоструйная чистка - смесь воды с песком , смесь воздуха с песком, аппарат разбирается;
o гидропневматическая чистка - смесь воды с воздухом, может выполняться без разборки аппарата и при эксплуатации; разновидность – пневмогидравлический удар (перед ним отложения высушивают, после шлам удаляют промыванием водой)
- физико-химическая (холодной или горячей водой, керосином или соляровым маслом, органическими растворителями, кипячение, выжигание кокса , воздействие на осадок химическими реагентами), проста, экономична, проводится без разборки.
6. Развальцовка и приварка труб.
- развальцовка - холодная раздача концов труб.Технология развальцовки обеспечивает получение качественных соединений, работоспособных при давлениях до 15 МПа и температурах до 450 - 550оС для стальных труб, 250оСдля труб из цветных металлов и их сплавов. Трубы развальцовываются после их приварки, тем самым исключается возможность попадания смазочного масла с вальцовки на подлежащие сварке поверхности.
7. Ремонт трубных пучков.
Дефекты трубного пучка выявляются при гидроиспытании аппарата. Трещины и отверстия в трубах, расположенных снаружи трубного пучка, устраняют сваркой. Трубы со сквозными повреждениями, расположенными внутри пучка, забивают с обеих сторон металлическими пробками с конусностью 3-5о и длиной 40-50 мм.
8. Ремонт корпусов. Дефекты корпусов теплообменной аппаратуры устраняют правкой, сваркой, наплавкой или установкой заплат. Выпучены и вмятины на корпусе выправляют механическим способом. Раковины удаляют механическим способом или газорезкой с последующей наплавкой (заваркой). На некоторые виды трещин устанавливают заплаты.
После восстановления работоспособности деталей и узлов теплообменные аппараты собирают и подвергают опрессовке по трубному и межтрубному пространствам. Перед сборкой фланцевых соединений привалочные поверхности осматривают и тщательно очищают. Затяжку болтов выполняют в последовательности крест-накрест: вначале предварительную, затем окончательную затяжку.
14. Установка подготовки топливного, пускового и импульсного газа УПТПИГ. Назначение.
УПТПИГ — это установка, предназначенная для подготовки пускового и топливного газа для газотурбинного двигателя (ГТД) газоперекачивающего агрегата (ГПА), импульсного газа, используемого для перестановки затворов шаровых кранов компрессорной станции (КС), а также для редуцирования газа, предназначенного прочим местным потребителям.
Назначение УПТПИГ: и
§ подготовка топливного и пускового (при необходимости) газа в соответствии с нормативной документацией ГПА и технических условий ГПА;
§ очистка, осушка и редуцирование газа собственных нужд КЦ;
§ поддержание требуемого давления и расхода перед подачей его в камеру сгорания и на пусковое устройство;
§ подготовка (очистка и осушка) импульсного газа;
§ измерение и учет расхода газа.
Топливный газ ТГ - газ, потребляемый в качестве топлива для газоперекачивающих агрегатов.
Пусковой газ ПГ - газ, используемый для запуска газоперекачивающих агрегатов.
Импульсный газ ИГ – газ, отбираемый из технологических трубопроводов обвязки КС для использования в пневмогидравлических системах приводов запорной арматуры: пневмоприводных кранов технологического, топливного и пускового газов, для подачи газа к контрольно-измерительным и регулирующим приборам.
Для раскрутки турбины газотурбинного двигателя используется пусковой газ, подготавливаемый на УПТПИГ.
Для использования в качестве топлива в газотурбинном двигателе применяется топливный газ, подготавливаемый на УПТПИГ. Большинство трубопроводной арматуры, используемой на КС и требующей дистанционного управления, оснащается пневмоприводной арматурой по причине возможности использования более дешевой энергии природного газа из магистрального газопровода относительно электроэнергии. Для приведения затворов арматуры в движение пневмоприводы используют энергию импульсного газа, подготавливаемого на УПТПИГ.
Типовая схема УПТПИГ имеет :
o узел переключения служит для отключения технологических линий при необходимости замены оборудования в случае капитального ремонта, при необходимости отключении линии при снижении потребности в газе, а также для защиты потребителя от превышения давления в линиях подачи газа;
o узел очистки газа обеспечивает удаление механических примесей и жидкостей из газа (включает в себя фильтры-сепараторы, шаровые краны на входе и выходе);
o узел предотвращения гидратообразования обеспечивает исключение образования кристаллогидратов во внутренних полостях технологического оборудования (включает в себя подогреватели газа прямого нагрева или непрямого нагрева через теплоноситель, запорная арматура на выходе/выходе узла).
o узел редуцирования давления газа снижает и автоматически поддерживает заданное давления, подаваемого потребителю,регулирует давление до себя и после (включает в себя регуляторы давления, клапаны-отсекатели, шаровые краны на входе и выходе редуцирующих линий, КИП для замера и передачи параметров давления и температуры.);
o узел измерения расхода газа определяет количество и объем подаваемого пускового, импульсного, топливного, затворного и прочих видов газа, а также газа, расходуемого на собственные нужды УПТПИГ.;
o узел одоризации - придает характерный запах газу;
o система автоматического управления (САУ) УПТПИГ обеспечивает реализацию функций контроля и управления отдельными блоками и узлами и УПТПИГ в целом, как при работе при нормальном режиме, так и во внештатных ситуациях
15. Система топливного газа.
Система топливного и пускового газа предназначена для очистки, осушки и поддержания требуемого давления и расхода перед подачей его в камеру сгорания и на пусковое устройство (турбодетандер). Газ отбирается из различных точек технологических коммуникаций КС: на узле подключения до и после крана № 20, из выходного коллектора пылеуловителей и выходного шлейфа компрессорного цеха - перед аппаратами воздушного охлаждения газа.
Система топливного и пускового газа имеет блочное исполнение, и включает в себя следующее оборудование (рис. 1.19): циклонный сепаратор, или блок очистки, фильтр-сепаратор, или блок осушки, подогреватели, блок редуцирования пускового и топливного газа, трубопроводы, замерное устройство, краны № 9, 12, 14 и 15, а также стопорные и регулирующие клапаны топливной системы, пусковое устройство или турбодетандер (ТД).
Работа системы: газ, отбираемый из технологических коммуникаций КС, поступает на блок очистки или газосепаратор 1, где происходит его очистка от механических примесей. Далее газ поступает в фильтр-сепаратор 2, где происходит его более глубокая очистка от механических примесей и влаги. Затем газ поступает в подогреватель 3 , где подогревается до температуры 45-50 °С с целью обеспечения устойчивой работы блоков редуцирования и недопущения его промерзания, что может нарушить устойчивую работу системы регулирования ГТУ.
Перед блоком редуцирования газ разделяется на два потока: один направляется на блок редуцирования топливного газа 4, другой на блок редуцирования пускового газа 5.
Топливный газ редуцируется до давления 0,6-2,5 МПа в зависимости от давления воздуха за осевым компрессором ГТУ. После блока редуцирования топливный газ поступает в сепаратор 6, где происходит его повторная очистка от выделившейся при редуцировании влаги, и затем в топливный коллектор. В камеру сгорания топливный газ поступает через кран № 12, стопорный (СК) и регулирующий (РК) клапаны. Краны № 14 и 15 используются для запальной и дежурной горелки в период пуска агрегата.
16. Система пускового газа.
Система топливного и пускового газа предназначена для очистки, осушки и поддержания требуемого давления и расхода перед подачей его в камеру сгорания и на пусковое устройство (турбодетандер).Газ для этих систем, аналогично, как и для системы импульсного газа, отбирается из различных точек технологических коммуникаций КС: на узле подключения до и после крана № 20, из выходного коллектора пылеуловителей и выходного шлейфа компрессорного цеха - перед аппаратами воздушного охлаждения газа.
Система топливного и пускового газа имеет блочное исполнение, и включает в себя следующее оборудование (рис. 1.19): циклонный сепаратор, или блок очистки, фильтр-сепаратор, или блок осушки, подогреватели, блок редуцирования пускового и топливного газа, трубопроводы, замерное устройство, краны № 9, 12, 14 и 15, а также стопорные и регулирующие клапаны топливной системы, пусковое устройство или турбодетандер (ТД).
Работа системы: газ, отбираемый из технологических коммуникаций КС, поступает на блок очистки или газосепаратор 1, где происходит его очистка от механических примесей. Далее газ поступает в фильтр-сепаратор 2, где происходит его более глубокая очистка от механических примесей и влаги. Затем газ поступает в подогреватель 3, где подогревается до температуры 45-50 °С. Подогрев газа осуществляется с целью обеспечения устойчивой работы блоков редуцирования и недопущения его промерзания, что может нарушить устойчивую работу системы регулирования ГТУ.
Перед блоком редуцирования газ разделяется на два потока: один направляется на блок редуцирования топливного газа 4, другой на блок редуцирования пускового газа 5.
Пусковой газ, пройдя систему редуцирования, снижает свое давление до 1,0-1,5 МПа и поступает через краны № 11 и 13 на вход в турбодетандер, где расширяясь до атмосферного давления, совершает полезную работу, идущую на раскрутку осевого компрессора и турбины высокого давления.
17. Классификация НПС и характеристика основных объектов.
Классификация:
· головные (ГНПС), предназначены для приема нефтей с промыслов, смешения или разделения их по сортам, учета нефти и ее закачки из резервуаров временного хранения в магистральный трубопровод, для запуска в магистральный трубопровод очистных и диагностических устройств, для внутристационарных перекачек.
· промежуточные (ПНПС), для восполнения энергии, затраченной потоком на преодоление сил трения, с целью обеспечения дальнейшей перекачки нефти. При перекачке из насоса в насос не имеет резервуарных парков. Если же перекачка ведется через резервуары или с подключением резервуара, резервуарные парки имеются. На ПНПС также устанавливают системы сглаживания волн давления и защиты от гидравлических ударов. Они имеют в своем составе в основном те же объекты, что и головные, но вместимость их резервуаров значительно ниже, либо они отсутствуют. При отсутствии резервуарного парка на ПНПС имеются узлы учета, подпорная насосная. На ПНПС может применятся подкачка нефти из других нефтепроводов или попутных нефтепромыслов.
Объекты:
o основного (технологического) назначения
o объекты вспомогательного и подсобно-хозяйственного назначения.
К объектам первой группы относятся:
резервуарный парк;
подпорная насосная;
магистральная насосоная;
узел учета нефти с фильтрами;
основная насосная;
узел регулирования давления и узлы с предохранительными устройствами;
камеры пуска и приема очистных устройств;
технологические трубопроводы с запорной арматурой.
К объектам второй группы относятся:
понижающая электроподстанция с распределительными устройствами;
комплекс сооружений, обеспечивающих водоснабжение станции;
котельная с тепловыми сетями; инженерно-лабораторный корпус;
пожарное депо;
узел связи;
механические мастерские;
мастерские ремонта и наладки контрольно-измерительных приборов (КИП);
гараж;
складские помещения; административно-хозяйственный блок и т.д.
18. Технологические схемы НПС.
Т ехнологическая схема головной нефтеперекачивающей станции.
Нефть с промысла поступает на станцию через фильтры-грязеуловители, узел предохранительных устройств, узел учета и направляется в резервуарный парк. Здесь осуществляется ее отстаивание от воды и мехпри- месей, а также замер количества. Для откачки нефти из резервуаров используется подпорная насосная. Из нее через узел учета нефть направляется в магистральную насосную, а затем через узел регуляторов давления и камеру пуска средств очистки и диагностики - в магистральный нефтепровод.
I - камера приема средств очистки и диагностики;
II - площадка фильтров-грязеуловителей;
III - узел предохранительных устройств;
IV, VII - узел учета;
V - резервуарный парк;
VI - подпорная насосная;
VIII - магистральная насосная;
IX - узел регуляторов давления;
X - камера пуска средств очистки и диагностики;
XI - емкость сбора утечек с погружным насосом;
XII - байпасная (обводная) линия
Технологическая схема промежуточной нефтеперекачивающей станции
Она отличается от головной тем, что не содержит узлов учета, резервуарного парка и подпорной насосной. Соответственно, на таких НПС не выполняются операции учета и хранения нефти.
Соответственно, на таких НПС не выполняются операции учета и хранения нефти.
I - камера приема средств очистки и диагностики;
II - площадка фильтров-грязеуловителей;
III - узел предохранительных устройств;
IV - емкость для сброса ударной волны;
V - емкость сбора утечек с погружным насосом;
VI - магистральная насосная;
VII - узел регуляторов давления; VIII - камера пуска средств очистки и диагностики
19. Насосно-силовое оборудование станции.
При трубопроводном транспорте нефти используются центробежные насосы. Их два вида:
o основные насосы (используются на ГНПС и ПНПС), служат для непосредственного транспорта нефти.
o подпорные насосы (используются только на ГНПС (на их подпорных станциях)) и играют вспомогательную роль, служат для отбора нефти из резервуарного парка и подачи ее на вход основным насосам с требуемым давлением (подпором), предотвращающим кавитацию в основных насосных агрегатах, обеспечивая их устойчивую работу.
Основные и подпорные насосы устанавливаются соответственно в основной и в подпорной насосных.
В качестве привода насосов используются электродвигатели синхронного и асинхронного типа.
При обычном исполнении электродвигателей их устанавливают в отдельном зале, герметично изолированном от насосного зала специальной стеной. В этом случае место прохождения через разделительную стену вала, соединяющего насос и электродвигатель, имеет конструкцию, препятствующую проникновению через него паров нефти.
Основные насосы на НПС соединяются между собой главным образом последовательно. При этом допускается иметь не более трёх рабочих насосов, исходя из прочности агрегатов. В дополнение к трём рабочим насосам на станциях устанавливается по одному резервному агрегату. В отдельных случаях, например, при прохождении в одном коридоре нескольких нефтепроводов, на НПС параллельно уложенных магистралей помимо последовательного соединения насосов предусматривается возможность перехода к смешанной параллельно-последовательно схеме соединения всех четырёх агрегатов, включая резервный, а также переход к параллельной схеме работы насосов. Такие возможности предусматриваются на аварийный случай. При выходе из строя какой-либо НПС, соседняя с ней станция на параллельной магистрали переводится на смешанную или параллельную работу насосов. При этом к станции подключаются сразу два нефтепровода - собственный нефтепровод рассматриваемой станции и нефтепровод аварийной НПС. Отмеченное позволяет не прекращать перекачку по аварийному нефтепроводу и поддерживать его производительность на достаточно удовлетворительном уровне.
Подпорные насосы соединяются между собой только параллельно. В основном на подпорной станции используется один или два рабочих насоса и один резервный
При последовательном соединении насосов увеличивается напор и производительность. При параллельном режиме работы производительность увеличивается (если включены параллельно два нефтепровода), напор остается без изменений, т. е. параллельный режим работы насосных агрегатов используется при работе НПС на два параллельных нефтепровода.
20. Размещение насосов и двигателей в помещении НПС.
Фундаменты под НАСОС и ЭЛЕКТРОДВИГАТЕЛЬ могут быть:
· раздельные
· общие, при блочном исполнении агрегата.
Насосы, будучи жестко связаны с технологическим трубопроводом неразъемными сварными или фланцевыми соединениями, устанавливаются на фундаментах также достаточно жестко, без возможности их перемещений в дальнейшем. Насос подключается к трубопроводу через приемную и выкидную задвижки, между задвижками устанавливается обратный клапан.
Электродвигатели имеют подвижный вариант установки, что позволяет производить регулирование соосности валов и двигателей, необходимость в котором возникает в процессе эксплуатации.
Если двигатель имеет взрывозащищенное исполнение типа СДТП (продуваемое), то насос и двигатель располагаются в одном помещении, используются специальные вентиляторы, обеспечивающие подачу воздуха под крышку электродвигателя.
В тех случаях, когда используют двигатель обычного исполнения, насосы и двигатели устанавливаются в отдельных помещениях, отделенных стеной:
насосный зал является взрывоопасным помещением, т. к. здесь устанавливается оборудование во взрывоопасном исполнении.
в электрозале с помощью подпорных вентиляторов создастся избыточное давление.
При раздельной компоновке насосного агрегата применяются 2 способа сочленения насоса и электродвигателя:
- без промежуточного вала, герметизация прохождения вала через разделительную стенку обеспечивается сальниковым уплотнением;
- без промежуточного вала, герметизация прохождения вала через разделительную стенку обеспечивается созданием воздушной завесы с помощью безпромвальной вентиляции.
Соединение насосов на НПС может быть параллельным, последовательным или комбинированным. При параллельном включении (рисунок ниже) насосы имеют общие всасывающий и нагнетательный коллекторы. Поэтому напор группы насосов равен напору одного из них, а подача увеличивается в число раз, равное количеству работающих насосов. При последовательном включении (рисунок ниже) нефть проходит один насос за другим, получая в каждом из них приращение напора. Для предотвращения работы насосов самих на себя их всасывающая и нагнетательная линии разделены обратным клапаном, который пропускает поток, двигающийся слева направо, но закрывается для потока, двигающегося в обратную сторону.
На современных нефте- и нефтепродуктопроводах параллельное включение чаще применяется для подпорных насосов, а последовательное - для магистральных. Нередко встречается комбинированное (последовательнопараллельное) соединение насосов (рисунок ниже). При последовательном соединении насосов увеличивается напор и производительность. При параллельном режиме работы производительность увеличивается (если включены параллельно два нефтепровода), напор остается без изменений, т. е. параллельный режим работы насосных агрегатов используется при работе НПС на два параллельных нефтепровода.
Возможные схемы соединения насосов на НПС
а - параллельное; б - последовательное; в - комбинированное (параллельно-последовательное)
Обвязка насосов должна обеспечивать работу НПС при выводе в резерв любого из насосных агрегатов станции.
Обратный клапан устанавливается также после последнего по ходу магистрального насоса. Делается это для защиты магистральной насосной от гидравлических ударов в последующем участке трубопровода.
21. Система смазки насосно-силовых агрегатов.
Система смазки является принудительной – масло в подшипники подаётся под давлением.
В системе смазки основных агрегатов кроме штатного режима работы предусмотрен аварийный режим, при котором обеспечивается смазка подшипников при отказе одного из основных насосов системы. Смазка подшипников насосов и электродвигателей осуществляется централизованно. Предназначенная для этого система (рисунок ниже) состоит из рабочего и резервного маслобаков М-1, М-2, аккумулирующего маслобака ЕА, рабочего ШН-1 и резервного ШН-2 шестеренных насосов, фильтров для очистки масла Ф-1 - Ф-3, аппаратов воздушного охлаждения масла АВОМ-1 - АВОМ-3, а также системы трубопроводов, связывающих перечисленное оборудование с насосами НМ-1 - НМ-4 и электродвигателями ЭД-1 - ЭД-2.
ШН – насос шестерный; М - маслобак; АВОМ - аппарат воздушного охлаждения масла; Ф - фильтр; ЭД - электродвигатель; НМ - насос магистральный; ЕА - аккумулирующий бак
Работает система смазки следующим образом. Масло из основного маслобака М-1 забирается шестеренным насосом ШН-1 и прокачивается через фильтры Ф-1 - Ф-3. Поскольку одновременно со смазкой трущихся поверхностей производится и их охлаждение, далее масло охлаждается в аппаратах воздушного охлаждения АВОМ, откуда частично поступает в аккумулирующий бак ЕА, а частично подводится к подшипникам насосов и электродвигателей. Бак ЕА, расположенный выше уровня оси насосных агрегатов, предназначен для подачи масла к подшипникам самотеком в период, когда электроснабжение НПС прекращено, роторы насосов и электродвигателей еще продолжают вращаться.
Остальное оборудование системы смазки (кроме АВОМ) располагается в приямке на отметке заглубления около 2,2 м относительно пола насосной. Маслопроводы монтируются с уклоном в сторону маслобаков для обеспечения их самотечного опорожнения.
Возле насосной устанавливаются две подземные емкости объемом 5 м3 для масла: чистого и отработанного. Обвязка шестеренного насоса ШН-3 позволяет закачивать чистое масло в маслобаки М-1, М-2 и откачивать загрязненное масло в автоцистерну.
Температура подшипников насосного агрегата не должна превышать 60 °С. Поэтому температура масла после их прохождения не должна быть выше 55 °С, что требует поддержания температуры масла в коллекторе перед поступлением в подшипники не более 35 °С.
Маслоустановка выполнена со 100 процентным резервом. Запуск в работу маслонасосов осуществляется как в автоматическом режиме с АРМ в операторной, так и в ручном режиме по месту в электрозале.
22. Система сбора и отвода утечек, разгрузки концевых уплотнений.
Основные и подпорные насосы перекачивающих станций снабжены сальниковым или торцовым уплотнением. Для уменьшения их износа не исключает небольшой утечки нефтепродукта, предназначенного для смазки и охлаждения трущихся поверхностей.
Функции системы сбора и отвода утечек:
– централизованный сбор в ёмкость утечек нефти из концевых уплотнений насосов и других технологических объектов НПС;
– откачка всех утечек станции из ёмкости в приёмный нефтепровод станции.
Рис. 5Принципиальная схема системы сбора утечек
1 - всасывающий коллектор; 2 - насос магистральный; 3 - коллектор сбора утечек; 4, 8 - задвижки; 5 - емкость сбора утечек; 6 - погружной насос; 7 - обратный клапан
Сбор утечек от концевых уплотнений осуществляется через специальные трубопроводы, присоединённые к узлам уплотнений и отводящим утечки в подземную ёмкость. Откачка утечек из ёмкости производится насосами откачки
Система откачки утечек:
1. Система с разделенными ёмкостями
- первая схема: на прием центробежных насосов откачки утечек, а затем в коллектор приема НПС (участок трубопровода, имеющий меньшее давление)
- вторая схема: в емкость сброса ударной волны, а при максимальном уровне в этой емкости с помощью насосов откачки прием НПС.
2. Система с использованием общей емкости.
Откачка нефти из емкости производится погружными насосами непосредственно в коллектор НПС. Количество насосов составляет три или четыре, они способны развивать давление, превышающее давление приема НПС.
23. Подпорная насосная станция головной нефтеперекачивающей станции (ГНПС).
В состав сооружений головной НПС всегда входят резер-вуарный парк иподпорная насосная станция, совмещенная с основной насосной или расположенная в отдельном здании. Подпорная насосная служит для подачи жидкости на вход основных насосов, так как при откачке из безнапорных резервуаров основные насосы не в состоянии вести откачку без предварительного создания давления жидкости на их входе. На многих трубопроводах, находящихся в эксплуатации, промежуточные насосные станции также имеют емкости для нефти или нефтепродуктов и ведут откачку из этих емкостей.
На НПС магистральных нефтепроводов используется два вида технологических насосов – подпорные и основные.
Основными насосами оборудуются основные НС ГНПС и ПНПС. Данные насосы предназначены для непосредственного транспорта нефти. Подпорные насосы используются только на ГНПС (на их подпорных станциях) и играют вспомогательную роль. Они служат для отбора нефти из резервуарного парка и подачи ее на вход основным насосам с требуемым давлением (подпором), предотвращающим кавитацию в основных насосных агрегатах.
Современным типом подпорных насосов являются насосы НПВ (нефтяные подпорные вертикальные). Они выпускаются четырёх типоразмеров: НПВ 1250-60, НПВ 2500-80, НПВ 3600-90, НПВ 5000-120. Цифры в маркировке указывают на производительность (м3/ч) и напор насоса (м).
Данный тип насоса (рис. 3.12) размещается в стакане 1, расположенном под уровнем земли, практически на отметке трубопровода. Приводящий двигатель находится на поверхности.
Насос имеет центробежное рабочее колесо двухстороннего входа 2, с каждой стороны колеса по предвключенному литому колесу 4 типа шнек. Направляющие подшипники ротора – подшипники скольжения, они смазываются и охлаждаются перекачиваемой нефтью.
Удерживание ротора от перемещения в осевом направлении производится сдвоенными радиально-упорными шарикоподшипниками 6, имеющими консистентную смазку. Ротор насоса гидравлически уравновешен применением на нём центробежного колеса двухстороннего входа, уплотнение ротора 5 – механическое, торцевого типа.
Помимо насосов НПВ на ГНПС достаточно широко ещё используются подпорные насосы типа НМП (нефтяные магистральные подпорные). Эти насосы горизонтальные, наземной установки. Ротор их аналогичен ротору насоса НПВ, уплотнения торцевые, подшипники качения с кольцевой смазкой. Корпус спиральный с разъёмом в горизонтальной плоскости – подобен корпусу насосов НМ. Маркировка насосов НМП аналогична маркировке насосов НМ.
Рис. 3.12. Схема установки подпорного насоса
Подпорные насосы соединяются между собой только параллельно. В основном на подпорной станции используется один или два рабочих насоса и один резервный.
24. Узел предохранительных устройств.
Узел предохранительных устройств это площадка с предохранительными клапанами, которые обеспечивают понижение давления в приемном коллекторе за счет сброса части нефти в «Атмосферный» резервуар.
Предохранительный клапан это предохранительное устройство прямого действия типа ППК (предохранительный, пружинный, полноподъёмный клапан) и СППК (специальный, полноподъёмный, пружинный предохранительный клапан).
Предохранительные клапаны устанавливаются:
o на линии приёма НПС, предназначены для защиты технологического оборудования резервуарного парка от повышенного давления. Дополнительно, параллельно клапанам устанавливается задвижка. При давлении на приёме станции больше 0,5 - 0,8 МПа срабатывают предохранительные клапана и автоматически начинает открываться задвижка, которая установлена параллельно клапанам. При этом происходит сброс избыточного давления в один, из специально выделенных для этих целей, резервуаров.
o на трубопроводе между подпорной и основной насосной обеспечивают защиту подпорной насосной и резервуарному парку от избыточного давления, которое повышается при остановке основной насосной. Клапаны открываются при давлении больше 1,5-1,7 МПа.
Узел предохранительных устройств служит для предохранения приемного коллектора технологических трубопроводов НПС от чрезмерных давлений на приеме станции, возникающих при ее внезапных отключениях. В качестве предохранительных устройств используются либо система сглаживания волн давления, либо предохранительные сбросные клапаны. Сброс избыточного давления производится в безнапорные технологические емкости.
25. Узел учета количества нефти.
Узел учета количества нефти – это целостный комплекс приборов и деталей измерительного характера и спецоборудования. Устанавливают в самых разнообразных точках потока нефти. Узел учета нефти состоит из нескольких параллельных линий, каждая из которых включает следующие элементы: отсекающие задвижки, манометры, фильтры, струевыпрямитель, счетчик, термометр, отводы к контрольному счетчику или пруверу, контрольный кран. Повышение точности замера расхода достигается дополнительной очисткой нефти в фильтре, уменьшением турбулентности потока в струевыпрямителе (представляющем собой пучок параллельных трубок малого диаметра, помещенных в основную трубу), а также внесением температурной поправки на основе показаний термометра.
Назначение узлов учёта нефти (УУН):
o измерение физических параметров (расход нефтепродуктов, температура, давление, плотность, влагосодержание, солесодержание)
o измерение химических параметров (уровня качества нефти.
Товарная нефть - продукция нефтегазодобывающего предприятия, готовая к продаже, т.е. соответствующая требованиям государственного стандарта и накопленная в товарных резервуарах.
В настоящее время разработаны технологии сдачи нефти с помощью узлов учета, автоматизирующих трудоемкий процесс оценки количества и качества.
Схема одной из таких технологий приведена на рис. 25.
Рис.25. Схема узла учета нефти.
1- входной коллектор; 2- фильтры; 3- счетчики; 4- манометры; 5- термометры;
6- выходной коллектор; 7- пробозаборник;
8- счетчик; 9- плотномер; 10- влагомер; 11- пробоотборник;
12-расчетный блок; 13, 15-преобразователи давления; 14, 16-
термопреобразователи.
Узел учета состоит из двух блоков:
- блока измерительных линий БИЛ, предназначенного для измерения объемного расхода нефти;
- блока качества, предназначенного для определения параметров продукции (влажность, плотность, расход). Блок качества оснащен пробоотборником для отбора проб нефти для периодических лабораторных исследований.
26. Узел регулирования давления НПС.
Узел регуляторов давления служит для установления требуемого начального давления в обслуживаемом участке трубопровода.
Узел регулирования давления предназначены для регулирования давления методом дросселирования (изменения давления путем пропуска потока газа через сужающее или расширяющее устройство) потока нефти в целях поддержания давления — минимального (0,2) МПа на приеме и максимального (6,4….7,0 МПа) на выходе насосной станции. В качестве исполнительных устройств принимаются регулирующие заслонки с электрическим приводом во взрывозащищенном исполнении. Регуляторы давления устанавливаются на открытой площадке.
Возможно два режима управления регулирующей заслонкой - ручной и автоматический.
Система автоматического регулирования (САР) предназначена для поддержания безопасного давления нефти в трубопроводе при максимальной производительности. Система представляет собой сочетание объекта регулирования и устройства автоматического регулирования. Функциональная схема САР представлена на рисунке 1.4.
Регулирование напора и подачи насосов на НПС осуществляется дросселированием потока нефти регулирующим органом на выходе из насосной.
27. Резервуарные парки насосных станций.
На магистральных нефтепроводах резервуарные парки размещаются:
o на головной насосной станции;
o на границах эксплуатационных участков;
o в местах подкачки нефти с близлежащих месторождений или сброса нефти попутным потребителям.
Полезный объём резервуарных парков нефтепроводов определяется в соответствии с требованиями ВНТП 2-86.
Суммарный полезный объем резервуарных парков нефтепровода ориентировочно распределяется следующим образом:
−головная нефтеперекачивающая станция нефтепровода, в случае перекачки одного сорта нефти должна располагать емкостью в размере от двухсуточной до трехсуточной производительности нефтепровода.
−на НПС с емкостью, расположенных на границах эксплуатационных участков, в пределах которых требуется обеспечение независимости работы насосного оборудования, должна быть предусмотрена емкость в размере 0,3 – 0,5 суточной производительности нефтепровода. Эта емкость должна быть увеличена до 1,0 – 1,5 в случае обеспечения необходимости выполнения приемо-сдаточных операций.
−на НПС с емкостью, расположенных на разветвлении магистральных нефтепроводов, а так же на местах их соединения, должна быть предусмотрена емкость в размере 1,0 – 1,5 суточной производительности трубопровода большей производительности. Допускается увеличение размеров емкости на этих станциях до пределов, требуемых по расчету при последовательной перекачке нефти.
−распределение объемов парков в пределах нефтепровода (участка) может корректироваться из условия обеспечения независимой работы отдельных эксплуатационных участков при техническом обслуживании НПС и нефтепровода, создания емкости на конечных пунктах, а так же с учетом максимального сокращения времени простоя нефтепровода.
При нескольких параллельных нефтепроводах суммарный полезный размер емкости должен определятся от суточной производительности каждого нефтепровода.
При последовательной перекачке нефти объем резервуарных парков каждой НПС определяется размерами накопления каждого сорта в соответствии с принятой в проекте цикличностью перекачки.
В зависимости от количества трубопроводов, подключенных к резервуарам, различают однопроводную и двухпроводную (рисунок ниже) технологические схемы. В первом случае для приема и отпуска нефти используется один и тот же Трубопровод, во втором — разные. Для снижения скорости закачки нефти резервуары могут иметь несколько приемо-сдаточных патрубков.
Возможные схемы обвязки резервуаров:
а - для головных и промежуточных станций; б - для головных станций; I-IV - номера резервуаров
28. Промежуточные НПС, состав сооружений. Узел подключения.
Дата добавления: 2019-07-15; просмотров: 2358; Мы поможем в написании вашей работы! |
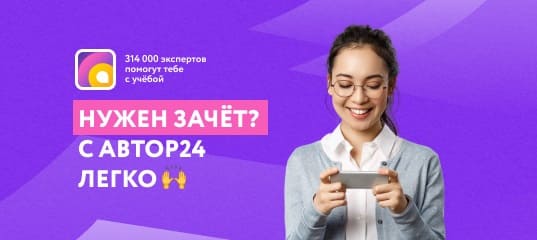
Мы поможем в написании ваших работ!