Элементы связующих композиций
ХАРАКТЕРИСТИКА ХОЛОДНОТВЕРДЕЮЩИХ СМЕСЕЙ
1. ТРЕБОВАНИЯ К ХОЛОДНОТВЕРДЕЮЩИМ СМЕСЯМ
В области технологии литья в разовые формы основное направление развития в единичном и серийном производстве — постепенный переход к технологическим процессам, основанным на использовании холоднотвердеющих формовочных смесей (ХТС).
Холоднотвердеющие смеси (ХТС) и технологические процессы, основанные на их применении, за последние 10-15 лет стали основными в изготовлении стержней и форм при единичном и серийном производстве в промышленно развитых странах. И в России идет процесс внедрения ХТС взамен смесей, упрочняющихся при тепловой обработке в сушилах или за счет теплоты нагретой оснастки. Эти процессы используют при изготовлении отливок практически любой конфигурации из черных и цветных сплавов, они могут быть адаптированы к различным требованиям по производительности, качеству (включая чистоту, размерную и массовую точность, товарный вид и др.), возможностям инвестиций, экологическим и климатическим условиям, квалификации персонала.
Перечень технологий изготовления ХТС, рассматриваемых в данной книге, приведен в табл. 1.
1. Российские и зарубежные названия процессов изготовления стержней и форм
№ п/п | Российское название | Зарубежное название | Краткая характеристика связующего |
1 | Аминовый процесс | Cold-box-amine | Фенольно-изоцианатная композиция, отверждаемая газообразным амином |
2 | Смола-СO2 | Resol-СO2 | Фенольно-щелочная смола, отверждаемая продувкой углекислым газом |
3 | Эпокси-SCb | Epoxy-S02 | Эпокси-алкидная композиция, отверждаемая продувкой сернистым ангидридом |
4 | Альфа-сет-процесс | Alfa-set (α-set) | Самотвердеющая фенольно-щелочная смола, отверждаемая смесью органических эфиров |
5 | Бета-сет-процесс | Beta-set (β-set) | Фенольно-щелочная смола, отверждаемая газообразным метилформиатом |
6 | Пеп-сет-процесс | Pep-set | Самотвердеющая фенольно-изоцианатная композиция, отверждаемая жидким амином пиридиновой группы |
7 | С02-процесс | C02-process | Жидкое стекло, отверждае-мое продувкой углекислым газом |
8 | Самотвердеющие смеси | Процессы No-bake, или связующие с индексом NB | Фурановые, карбамидно-фурановые, полиуретановые смолы, отверждаемые органическими кислотами, смесью кислот, смесью эфиров, аминами |
9 | Смеси, отверж-даемые продувкой | Связующие №№ 1,2,3, 5, 7 с индексом С В | - |
В передовых по технологическому уровню странах:
|
|
США, ФРГ, Японии, Великобритании, Франции, Италии и др. –
полностью исключено применение формовочных смесей с глиной (табл. 2),
Кроме песчано-бентонитовых смесей для сырых форм.
|
|
Песчано-бентонитовые смеси для сырой формовки (далее ПГС) сохраняют лидирующие позиции преимущественно в изготовлении мелких и средних форм в массовом и крупносерийном производстве (автомобилестроение, транспортное машиностроение, сантехоборудование и др.).
создание автоматических формовочных линий производительностью 250...300 форм/ч и выше стало возможным благодаря разработке высокопрочных песчано-бентонитовых смесей.
Появление в последние годы механизированных комплексов изготовления средних и крупных форм, в том числе безопочных, стало возможным при появлении фурановых ХТС с низким (около 1 %) содержанием связующего при весьма высокой прочности и регулируемой скорости отверждения.
Опыт разработки и промышленного освоения ХТС показал, что коренное усовершенствование технологии литейной формы может быть достигнуто прежде всего путем создания принципиально новых типов смесей с новыми физическими и физико-химическими свойствами и соответствующих средств механизации и автоматизации.
Крупными достижениями в указанном направлении были создание в начале 50-х годов СО2-процесса, разработка в 60-х годах жидких, пластичных, сыпучих ХТС на органической и не органической основе. Значительное развитие получили ХТС с синтетическими смолами. С их появлением оказалось возможным радикальное решение проблем ликвидации тяжелого ручного труда, перевода на поток изготовления стержней, резкого снижения трудоемкости и сокращения цикла изготовления форм, выбиваемости стержней, а также решение других технических и экономических задач. Новые процессы потребовали создания специальных средств механизации, существенно видоизменили всю технологическую структуру производства отливок.
|
|
Очевидно, что переход от одного вида смеси к другому в современном литейном цехе не только меняет технологию изготовления стержня или формы, но пронизывает почти все сферы производства от подготовки исходных материалов до регенерации смесей и финишной обработки отливок, оказывает прямое влияние на трудоемкость выбивки, обрубки и очистки, точность и долговечность отливок, другие качественные показатели.
Этим обусловлен многообразный комплекс требований, которым должна отвечать формовочная смесь в условиях современного производства. Их можно разделить на три группы: технические, санитарно-гигиенические и экономические.
|
|
Технические требования:
а) отверждение без нагрева при выдержке на воздухе или путем обработки внешними реагентами;
б) возможность регулирования скорости отверждения в пределах, определяемых характером производства;
в) высокая общая и поверхностная прочность, минимальная хрупкость;
г) минимальная работа уплотнения для обеспечения технологически необходимой плотности стержня или формы;
д) низкая гигроскопичность, минимальная растворимость связующей композиции в воде или органических растворителях, применяемых в составе противопригарных покрытий;
е) наличие комплекса высокотемпературных свойств, обеспечивающих получение отливок без дефектов, таких, как пригар, просечки, трещины, засоры, деформации, газовые раковины и пористость; ж) возможность регенерации известными методами;
з) легкая выбиваемость из отливок.
Санитарно-гигиенические требования:
а) минимальные выделения в окружающую среду токсичных веществ на всех стадиях технологического процесса изготовления отливок;
б) отсутствие неприятных или раздражающих запахов;
в) отсутствие вредного действия компонентов смеси на кожу при прямых контактах.
Экономические требования:
а) наличие сырьевой базы и мощностей по производству компонентов смеси на длительный период времени;
б) недефицитность и относительно низкая стоимость компонентов.
Перспективным является использование нескольких типов смесей, каждый из которых отвечает определенному минимуму требований литейного производства и имеет определенную область применения.
2. ОБЩИЕ ПРИНЦИПЫ РАЗРАБОТКИ ХТС
В общем случае в состав ХТС входят наполнитель, связующая композиция и специальные добавки. Эти компоненты полностью определяют технологические свойства смесей и условия их использования в производстве. Однако принципиальные особенности каждого типа ХТС зависят главным образом от состава и свойств связующей композиции, которая определяет:
- тип оборудования
-параметры технологического процесса изготовления стержня или формы
-качество поверхности отливок
-выбиваемость
-способ регенерации
В связи с этим разработка новых типов ХТС или усовершенствование известных преимущественно направлена на создание связующих композиций с заданными свойствами. Другой, значительно более простой задачей является сочетание их с наполнителями, которые могли бы обеспечить высокое качество поверхности отливок. К ним относятся кварцевый песок, дистен-силлиманит, циркон, хромит, хромомагнезит и др.
Связующая композиция
должна иметь два обязательных свойства — способность затвердевать без нагрева при выдержке на воздухе или обработке газообразными реагентами и высокую адгезию к наполнителю. В принципе этими свойствами обладает большое число органических и неорганических систем, к которым относятся многие виды синтетических и природных полимеров (смол, растительных, масел, сульфитно-дрожжевой бражки СДБ, цементов, силикатных стекол, водосолевых и кислотно-основных композиций и т. д.). Обобщение опыта, накопленного в строительстве, машиностроении (склеивании металлов, дерева, пластиков), изготовлении деталей машин и приборов из композиционных материалов, технологии огнеупоров, привело к созданию фактически новой отрасли технической науки—технологии получения и промышленного применения самозатвердевающих (или вяжущих) систем. Очевидно, что применительно к условиям литейного производства существуют широкие возможности получения ХТС с заданными технологическими свойствами. Однако для этого должны быть сформулированы основные принципы разработки соответствующих связующих композиций.
Связующая композиция состоит из собственно связующего, отвердителя, регуляторов скорости отверждения и добавок.
Связующее является основой композиции, тем элементом, который, затвердевая, образует мосты между зернами песка, обладая высокой собственной прочностью (когезионной) и адгезией к наполнителю.
Отвердитель—это компонент, который вызывает отверждение связующего, но сам при этом не обладает связующими свойствами и не играет активной роли в затвердевшей структуре композиции. К отвердителям относятся, например, углекислый газ в СО2-процессе, эфиры в смесях с жидким стеклом, триэтиламин в смесях с полиуретановыми связующими. В тех случаях, когда отверждение носит каталитический характер, отвердитель называется катализатором, как, например, кислоты в смесях с фурановыми, фенольными и другими поликонденсационными смолами. В некоторых видах ХТС компоненты сочетают в себе функции связующего и отвердителя. Это относится, например, к цементным смесям (вода и цемент), фосфатным (окисел и кислота) и некоторым другим. В таких случаях следует говорить не о связующем и отвердителе, а о двухкомпонентом связующем. Регуляторами скорости отверждения служат ускорители и замедлители, которые, как правило химически активны к компонентам смеси.
К специальным добавкам относятся материалы, вводимые для улучшения выбиваемости, пластификации смесей, предотвращения поверхностных и газовых дефектов на отливках.
В табл. 1 приведены некоторые элементы связующих композиций, используемые в практике литейного производства.
Связующее или один из компонентов двухкомпонентного связующего должны иметь жидкую консистенцию при относительно низкой вязкости. Это условие обязательно, так как в формовочной смеси должна быть обеспечена максимальная однородность связующей композиции и равномерное распределение ее по зернам наполнителя. Наиболее удобны в технологическом отношении композиции, состоящие только из жидких компонентов. Применение порошков усложняет дозирующую систему в установках непрерывного действия, ухудшает качество перемешивания, сопровождается выделением пыли на подготовительных операциях.
Связующая композиция должна быть по возможности химически инертна к наполнителю. Такие материалы, как кварцевый песок, содержат примеси — глину, окислы щелочных и щелочноземельных металлов; в состав хромита и хромомагнезита входят щелочные окислы (СаО, МgО). Естественно, что свойства композиций, содержащих кислоты, например, с синтетическими смолами, изменяются при взаимодействии с такими наполнителями. Вследствие этого инертные к щелочам композиции имеют меньше ограничений по качеству исходных материалов.
Для всесторонней оценки перспектив и области применения определенного типа ХТС служат требования, перечисленные выше. Однако при разработке композиций первичными критериями должны быть скорость отверждения, прочность и выбиваемость смеси.
Таблица 1
Элементы связующих композиций
Связующие | Двух-компонентные связующие | Отвердители | Регуляторы скорости | Специальные добавки |
Жидкое стекло | - | СО2 Кремнефтористый натрий, эфиры | - | Органические добавки для улучшения выбиваемости |
Синтетические смолы | - | Органические и минеральные кислоты | Нафтенаты тяжелых металлов | Окислы железа, перлит, мочевина |
СДБ | - | Сильные окислители | - | - |
- | Цемент-вода | - | Хлористые соли, фосфаты | Органические добавки для улучшения выбиваемости |
- | Жидкое стекло-двухкальциевый силикат | - | Гипс, бура | - |
- | Окислы железа – ортофосфорная кислота | - | Лимонно-кислый аммоний, мочевина | - |
Принципиальное отличие ХТС от классических смесей заключается в том, что у них изменяются технологические свойства при выдержке готового стержня или формы. В связи с этим характеристики свойств определяют несколько раз через определенные интервалы времени, которые выбирают в зависимости от условий использования смесей. Если свойство смеси является переменным, то его величина, полученная при испытании, всегда сопровождается указанием времени от момента выпуска смеси из смесителя.
Критерий скорости отверждения зависит от предполагаемого характера производства. Если принять за критерий прочность, достигаемую смесью за определенный период времени, то для массового производства этот период может составить 40—60 с, для крупносерийного 5—10 мин, для единичного и мелкосерийного 30—40 мин. Опыт показывает, что во всех трех случаях смесь должна иметь прочность на сжатие для стержней 5— 15 кгс/см2, для форм 2—10 кгс/см2. Эти величины прочности, которые принято называть «манипуляторными», обеспечивают возможность проведения со стержнем или формой необходимых технологических операций (извлечение стержня из ящика или модели из формы, транспортировка, сборка и т. п.).
Прочность ХТС — максимальная величина, достигаемая к моменту заливки металла в форму. Обычно ее характеризуют прочностью смеси через 24 ч (024).
Для единичного и мелкосерийного производства оптимальное значение σв24=20— 40 кгс/см2 (стержни), 2—15 кгс/см2 (формы), для крупносерийного и массового—30—60 кгс/см2 (стержни), 2—15 кгс/см2 (формы).
Важной характеристикой связующей композиции является ее поведение при нагреве в интервале температур, соответствующем реальным условиям в литейной форме. Оно определяет высокотемпературные свойства смеси, ее влияние на качество отливок, возможности регенерации, газовыделение в окружающую атмосферу. Из этого комплекса наиболее важным является выбиваемость. О ней судят по прочности смеси после нагрева и охлаждения (остаточной прочности) или по данным специальных технологических испытаний. Для легкой выбивки необходимо, чтобы связующая композиция разупрочнялась в определенном температурном интервале, положение которого зависит от вида сплава, толщины стенок, массы и конфигурации отливки. Для крупного стального и чугунного литья, например, этот интервал составляет 400—800° С.
Скорость физико-химических процессов и структура образующихся продуктов в затвердевших композициях поддаются широкому регулированию. Этим обусловлено многообразие технологических вариантов изготовления стержней и форм из ХТС и исключительно большая область их применения.
Можно выделить три типа процессов отверждения ХТС; возможности применения каждого из них целесообразно оценить при разработке связующих композиций.
1. Отверждение на воздухе—для единичного и мелкосерийного производства.
2. Отверждение путем обработки смеси химическими реагентами-отвердителями—для единичного, серийного и массового производства.
3. Отверждение физическими методами — путем продувания холодным или нагретым воздухом, обработки электрическим током промышленной или высокой частоты, энергией СВЧ — для массового и крупносерийного производства.
Очевидно, что многие связующие или композиции могут использоваться во всех трех процессах.
Целесообразно разделить все связующие композиции на два крупных класса — органические и неорганические, имея в виду, что в смешанных композициях основная роль в формировании прочности смеси обычно принадлежит одному из компонентов, который является органическим или неорганическим. Такое разделение обусловлено принципиальными различиями в механизме отверждения органических и неорганических материалов, технологических свойствах смесей, особенно в их поведении при взаимодействии с металлом, условиях применения и даже структуре экономической эффективности. Практически в настоящее время разработка и применение ХТС с органическими и неорганическими связующими композициями представляет собой два самостоятельных направления в литейной технологии.
ОРГАНИЧЕСКИЕ СВЯЗУЮЩИЕ КОМПОЗИЦИИ
Для классификации органических композиций (табл. 2) выбраны три признака:
1) физико-химический механизм отверждения;
2) химическая характеристика связующего;
3) тип процесса отверждения.
Все поликонденсационные смолы (класс А) отверждаются кислотными катализаторами, из которых для смол типа 1, 2, 3 обычно используют сульфокислоты — бензолсульфокислоту, паратолуолсульфокислоту, их смеси и модификации, а для смол типа 4, 5 — ортофосфорную кислоту, а также сульфокислоты и так называемые кислоты Льюиса (хлористые соли металлов — FеCl2, FeCl3, А1С1з и т. д.). Отвердителями для смол класса Б служат амины (триэтиламин, диметилэтиламин) и нафтенаты тяжелых металлов Со, Рb, Sn в тех случаях, когда в результате отверждения образуются полиуретановые полимеры (смолы 1, 2). Смолы типа 3 отверждаются совместным действием нафтенатов тяжелых металлов и сильных окислителей—перманганатов, перборатов и т. п. Для отверждения смесей с СДБ Таблица 2
Дата добавления: 2019-07-15; просмотров: 274; Мы поможем в написании вашей работы! |
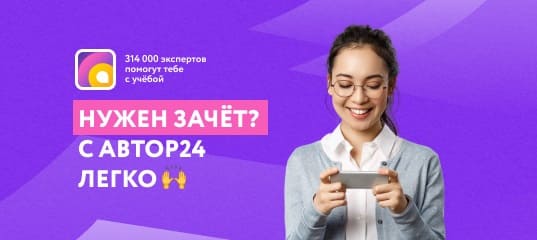
Мы поможем в написании ваших работ!