Состав сборочно-сварочного цеха
Крупные сборочно-сварочные цехи могут включать в себя следующие отделения и другие различные помещения и площади:
1. Производственное отделение.
1.1. Заготовительное отделение делится на участки.
1.1.1. Разметки металла.
1.1.2. Резки металла.
1.1.3. Станочной обработки.
1.1.4. Кузнечно-котельный.
1.1.5. Штамповочный
1.1.6. Слесарно-инженерный.
1.1.7. Очистки металла.
1.2. Сборочно-сварочное отделение.
1.3. Отделение.
1.3.1. Узловой сборки.
1.3.2. Общей сборки и сварки.
1.4. Участки.
1.4.1. Термической обработки.
1.4.2. Испытания готовой продукции.
1.4.3. Исправление дефектов.
1.4.4. Нанесение поверхностных покрытий и окончательной отделки продукции.
2. Вспомогательное отделение.
2.1. Цеховой склад металла погрузочно-разгрузочной площадки.
2.2. Промежуточный склад деталей и полуфабрикатов с участком их сортировки.
2.3. Межоперационные складочные участки и места.
2.4. Склад готовой продукции цеха с контрольно-упаковочными отделениями и погрузочной площадкой.
2.5. Кладовые электродов, флюсов, инструментов, приспособлений, запасных частей и вспомогательных материалов.
2.6. Мастерские (ремонтные, электромеханические, изготовления шаблонов).
2.7. Отделения (электромашинные, ацетиленовые, компрессорные, цеховая подстанция).
3. Административно конторские и бытовые помещения;
3.1. Контора цеха.
3.2 Гардеробы.
3.3. Туалет.
3.4. Душевые.
3.5. Буфет.
3.6. .
3.7. Медпункт.
ЗАГОТОВИТЕЛЬНОЕ ПРОИЗВОДСТВО
|
|
Приемы выполнения заготовительных операций
Литые, кованые и штампованные заготовки, поступающие на сварку, как правило, не требуют дополнительных операций. Детали же из проката после подбора по размерам и маркам сталей направляются на следующие операции: правку, разметку, резку, обработку кромок, гибку и очистку под сварку.
Листовой прокат требует правки в том случае, если производитель нарушает условия поставки, и при транспортировке возникли значительные деформации (рис. 2.1).
Рис. 2.1. Виды деформаций листовой стали:
а – волнистость; б – серповидность в плоскости; в – местные выпучены;
г – заломленные кромки; д – местная погнутость; е – волнистость поперек части листа
Правка осуществляется созданием местной пластической деформации и производится обычно в холодном состоянии.
Для устранения волнистости листов и полос толщиной от 0,5 до 50 мм используются листоправильные вальцы (рис. 2.2).
Рис. 2.2. Схема правки в листоправильных вальцах
Исправление достигается многократным пропусканием листа через валки.
Листы малой толщины (менее 0,5 мм) правят растяжением на прессах с помощью приспособлений или на специальных растяжных машинах.
|
|
Серповидность листовой и широкополосной стали в ограниченной степени поддается правке. Ее выполняют на многовалковых листоправильных вальцах с выкладыванием прокладок у вогнутой кромки.
Правку профильного проката производят на роликовых машинах, работающих по схеме листоправильных вальцов (рис. 2.3).
Рис. 2.3. Правка уголка Рис. 2.4. Правка прокатной
в углоправильных вальцах профильной стали (швеллера двутавров)
Для двутавров и швеллеров исправление в плоскости большего момента сопротивления производят изгибом на прессах (рис. 2.4).
При постоянном ходе толкателя 3 задаваемая деформация профиля 2 регулируется изменением расстояния между опорами 1. На таких прессах правят и толстолистовой прокат толщиной более 50 мм.
Разметка. Индивидуальная разметка трудоемка. Наметка по шаблонам более производительна, однако изготовление специальных шаблонов не всегда экономически целесообразно.
Оптический метод позволяет вести разметку без шаблона по чертежу. Имеются разметочно-маркировочные машины с пневмокернером, производящие разметку со скоростью 8–10 м/мин при погрешности ± 1 мм. В этих машинах применяется программное управление.
|
|
Без разметки можно обходиться в случае использования приспособлений для мерной резки проката, а также при тепловой резке машинами с фотокопировальной или программной системой управления.
Резка и обработка кромок. Прямолинейные кромки из листов толщиной до 40 мм можно получать с помощью гильотинных ножниц (рис. 2.5).
Верхний нож, опускаясь, производит скалывание металла. Погрешность размера при резке по разметке составляет ± 1,5…2,5 мм. Можно получить прямоугольный рез со скосом под сварку, используя специальные ножницы (рис. 2.6).
Рис. 2.5. Гильотинные ножницы
![]() | 1 – гидроцилиндр; 2 – упор; 3 – ножедержатель; 4, 6 – крепление; 5 – подвеска; 7 – прижим; 8 – регулируемый упор; 9 – нож для прямой резки; 10 – нож для резки под скос |
Рис. 2.6. Специальные ножницы
Листовые заготовки с непрямолинейными кромками толщиной
δ = 20…25 мм можно получать с помощью дисковых ножниц (рис. 2.7).
Рис. 2.7. Дисковые ножницы Рис. 2.8. Дисковые ножи
Для получения листовой заготовки заданной ширины с параллельными кромками дисковые ножи целесообразно располагать попарно на заданном расстоянии друг от друга (рис. 2.8).
|
|
При резке на ножницах металл подвергается значительной пластической деформации. Поэтому если кромка попадает в зону сварки в последующем и полностью проплавляется, то дополнительной обработки кромок не требуется. Если кромка остается свободной и работает при переменных нагрузках, то целесообразно удалить слой пластически деформированного металла последующей механической обработкой.
В некоторых случаях применяется резка гладким диском либо за счет трения, либо контактно-дуговым оплавлением.
Производительным является процесс вырубки в штампах.
Разделительная термическая резка менее производительна, чем резка на ножницах, но более универсальна и применяется для получения стальных заготовок разных толщин и конфигураций.
Все более широко применяется плазменно-дуговая резка, позволяющая обрабатывать любые металлы и сплавы. Использование сжатого воздуха в качестве плазмообразующего газа дает экономические и технические преимущества – высокое качество газа и большая скорость резки сталей малой и средней толщины (до 60 мм), недостаток воздушно-плазменной резки – насыщение азотом поверхностного слоя кромок, что приводит к образованию пор при сварке. Для устранения недостатка кромки зачищают стальной щеткой и подвергают механической обработке.
Термическую резку используют и при создании скоса кромок, применяя два резака (при разделительной резке) или три – при двухстороннем скосе. После вырезки детали иногда нужно править.
Применяют лазерную резку. Преимущества – малая ширина реза (доли миллиметров) и возможность резки материала малой толщины (0,05 мм).
Механическую обработку на станках (кромкострогальных и торцефрезерных) производят:
– для обеспечения требуемой точности сборки;
– обработки фасок сложного профиля;
– удаления металла, обрезанного ножницами или термической резкой, когда это считается необходимым.
Гибка производится на листогибочных вальцах (с волнами длиной до 13 м) листовых элементов толщиной до 60 мм для получения деталей цилиндрической или конической формы.
При вальцовке в холодном состоянии отношение радиуса изгиба к толщине листа ограничивают допустимым значением пластической деформации. При гибки в вальцах концевой участок листа остается почти плоским.
Более правильное очертание концевого участка может быть получено либо калибровкой уже сваренной обечайки, либо предварительной подгибкой кромок под прессом или на листогибочных вальцах с толстым подкладным листом, согнутым по заданному контуру. Используют также двухвалковые вальцы с эластичным покрытием нижнего валка.
Листовые элементы со сложной пространственной поверхностью получают на специальных вальцах с валками переменного диаметра.
Для получения элементов оболочек больших размеров применяют штамповку взрывом.
При серийном и массовом производстве для получения элементов с поверхностью сложной формы используют холодную штамповку (для материалов δ до 10 мм). Высокая производительность, точность размеров и формы заготовок и низкая себестоимость возможна путем создания технологических штампосварных изделий.
При холодной гибки профильного проката и труб используют роликогибочные и трубогибочные станки. Если возникают трудности, связанные с нарушением формы поперечного сечения, используют станки гибочные с индукционным нагревом изгибаемой заготовки. Нагретый до 950…1000 ºС деформируемый участок имеет небольшую протяженность, обладает малым сопротивлением пластической деформации, что предотвращает образование гофров в зоне сжатия.
Детали из толстого листового металла получают на гибочных вальцах и на прессах в горячем состоянии.
Гофрирование повышает жесткость листов, его производят штамповкой, а не гибкой, чтобы поперечные кромки листов оставались плоскими.
Для очистки деталей и сварных узлов применяют механические и химические методы. Загрязнения, ржавчина, окалина удаляются с помощью дробеструйных или дробеметных аппаратов, используют и зачистные станки с рабочими органами: металлическими щетками, иглофрезами, шлифовальными кругами и лентами. Чугунная и стальная дробь размером от 0,7 до 4 мм применяется в зависимости от толщины металла.
В дробеструйных аппаратах дробь выбрасывается через сопло сжатым воздухом, в дробемётных аппаратах – лопатками ротора (в них производительность выше и дешевле очистка), но происходит износ лопаток. Очистка в обоих случаях осуществляется в камерах. Для крупногабаритных конструкций в мелкосерийном производстве применяют беспыльные дробеструйные аппараты, и можно обходиться без камеры.
Химическими методами производят обезжиривание и травление поверхности ванным и струйным методом. В первом случае (при ванном методе) детали последовательно опускают в ванны с различными растворами и выдерживают в каждом из них определенное время. Во втором случае последовательная подача растворов различного состава на поверхность деталей производится струйным методом, осуществляя непрерывный процесс очистки.
Химический способ эффективен, однако процесс очистки сточных вод при этом дорогостоящ.
Пассивирование или грунтовка предохраняет металл от коррозии (так же, как и очистка) и позволяет осуществлять сварку без удаления защитного покрытия.
Холодная деформация при изготовлении заготовок сопровождается уменьшением пластичности металла. Поэтому относительное остаточное удлинение δ наиболее деформированных волокон необходимо ограничивать. Например, согласно СНиП18-75 при холодной правке δ ≤ 1 %; при холодной гибке δ ≤ 2 %, что соответствует радиусу изгиба не менее 50 толщин листа при правке и не менее 25 толщин листа при гибке. Поэтому существуют предельные значения искривлений, исправление которых не допускается в холодном состоянии.
В случае необходимости создания более значительных деформаций правку и гибку деталей производят в горячем состоянии (900…1000 ºС) при этом происходят процессы рекристаллизации, и пластические свойства металла не снижаются.
Часто правке на вальцах подвергают сварные заготовки из двух или нескольких листов сваренных стыковыми швами. Для ограничения пластической деформации зоны сварного соединения усиление сварного шва должно быть минимальным. В ряде случаев усиление рекомендуется удалять.
Качество подготовки и сборки заготовок под сварку осуществляют внешним осмотром, который является во многих случаях достаточно информативным, наиболее дешевым и оперативным методом контроля.
Внешнему осмотру подвергают материал, который может браковаться при наличии вмятин, заусенцев, окалины, окислов, ржавчины и т.д. Определяется качество подготовки кромок под сварку и сборки заготовок – чистота кромок, соответствие зазоров допускаемым значениям, правильность разделки кромок. Для этого применяются специальные шаблоны или универсальный инструмент. Строгий контроль заготовок и сборки во многом обеспечивает качество сварки.
2.2. Примеры механизированных поточных линий
заготовительного производства
Прокат черных металлов поступает на предприятие, как правило, с окалиной, ржавчиной, жировыми загрязнениями, кроме того, металл поступает деформированным, поэтому перед использованием его необходимо подготовить: его правят, очищают, наносят покрытие. Для этих целей применяют автоматизированные поточные линии.
Пример. На Уральском заводе химического машиностроения используют поточную линию очистки и грунтовки металлов (рис. 2.9).
Рис 2.9. Поточная линия очистки и грунтовки металлов: 1 – входной роликовый конвейер;
2 – камера для подогрева листа; 3 – камера для дробеметной очистки листа; 4 – камера
нанесения грунтовки на лист; 5 – термическая транспортная камера; 6 – конвейер,
объединяющий позиции; 7 – выходной конвейер
Правка листа производится предварительно на вальцах, не входящих в состав линии. Особенностью этой линии является двухсторонняя дробеметная обработка листа, горизонтально расположенного на роликовом конвейере.
Механизированная поточная линия для подготовки проката
На этой линии можно очищать листовой и профильный прокат:
1. Лист подается на конвейер мостовым краном.
2. В камере для нагрева его нагревают до 100–110 оС и инжекторными газовыми горелками. При этом жировые отложения выгорают, и создаются необходимые эффективные условия для очистки от ржавчины и окалин.
3. В камере имеются два дробеметных аппарата. Чугунная дробь или металлический песок сдуваются струей воздуха из вентилятора, попадают в бункер, оттуда винтовыми конвейерами подаются на элеватор. Элеваторами – в сепаратор, отделяющий пыль от дроби, и из сепараторов очищенная дробь или песок вновь подаются в дробеметные аппараты. После очистки лист по роликовому конвейеру поступает в камеру для нанесения грунтовки. Камера состоит из каркаса, обшитого стальными листами, гидрофильтра с сепаратором для очистки удаляемого воздуха от окрасочной пыли, передвижных кареток с краскораспылителями. В качестве защитного покрытия использовались, например МС-067 или водорастворимые консерванты – водорастворимые ингибиторы коррозии, например нитрат натрия (NaNO3 ). Применение этого консерванта не требует наличия в камере окраски взрывозащитного оборудования. Загрунтованный лист сушат в сушильно-транспортной камере, которая снабжена приточной и вытяжной вентиляцией. После этой операции лист подается на следующие рабочие места.
Размеры очищенных листов:
1) длина 4–10 м;
2) ширина 1,5–3,5 м;
3) толщина от 6 до 90 мм;
4) скорость транспортирования до 3 м в минуту;
5) мощность линии 280 кВт.
Линия для получения фланцев
Фланцы – это соединительная часть труб, представляющая собой кольцо тореидального типа. Применяют их в химическом аппаратостроении. При существующих технологиях фланцев имеются недостатки:
1) большое отклонение форм и размеров в связи с присутствием больших припусков на механическую обработку;
2) большое время на межоперационные транспортировки из-за отсутствия единого технологического потока.
На участке (рис. 2.10) выполняются следующие операции:
1) мерная резка полосовых заготовок;
2) гибка заготовок из полосы в кольца;
3) сварка торцов на машине для стыковой контактной сварки;
4) снятие грата;
5) низкотемпературный отжиг колец из углеродистой стали или высокотемпературный отжиг колец из коррозионно-стойкой стали в печи шахтного типа;
6) калибровка колец;
7) контроль качества.
Рис. 2.10. Линия для получения фланцев:
1 – стеллаж накопитель; 2 – стенд для мерной резки полосок; 3 – гибочно-обкатные машины; 4 – машина для контактной сварки К-607; 5 – транспортная тележка с поворотным столом;
6 – установка для снятия грата; 7 – кассеты для укладок заготовок фланцев; 8 – шахтные
печи; 9 – рабочее место для УЗК; 10 – краны штабилеры-перегружатели; 11 – краны
штабилеры-перегружатели; 12 – коллектор-накопитель
Заготовки и прокат со стеллажа накопителя длиной до 9 м поступает на параллельный расположенный стенд для мерной резки полос с помощью термической резки. В гибочно-обкатных машинах полосы гнутся в холодном состоянии. Контактная сварка расположена рядом с гибочной, далее – установка для снятия грата, который снимается одновременно с двух сторон. После снятия грата заготовки краном укладывают в кассеты, они поступают в шахтные печи. После печей – калибровка, УЗ контроль, и заготовки поступают в коллектор накопителя.
Технические данные:
Производительность 18–20 штук в час. Внутренний диаметр заготовки –600–2200. Размеры поперечного сечения – 25/60 и максимальное – 100/110. Мощность линии – 490 кВт.
2.3. Комплексная механизация и автоматизация
в заготовительном производстве
Несмотря на широкое использование машин и механизмов, эффективность их использования в условиях индивидуального и мелкосерийного производства на заготовительном участке нередко оказывается низкой. Это объясняется большим объемом ручного труда при выполнении транспортных и установочных операций. Поэтому снижение доли ручного труда возможно путем повышенного использования механизмов.
Приведем несколько примеров рациональной организации в заготовительном производстве.
Схема участка приемки и складирования листового металла в условиях мелкосерийного производства показана на рисунке 2.11.
железнодорожный путь |
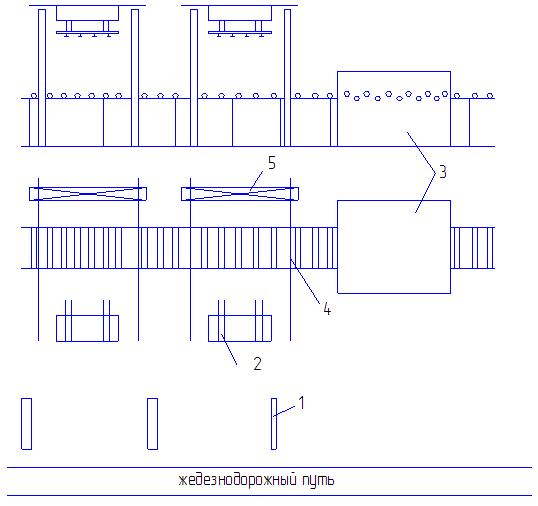
Рис. 2.11. Участок приемки и правки листового металла:
1 – сортировочные площадки; 2 – мостовые краны; 3 – листоправильные вальцы;
4 – рольганг; 5 – перегрузочные мосты
Горизонтальное складирование в пачки выполняют по габаритам и маркам металла. Краны оснащают траверсами с электромагнитами или вакуумными захватами.
Листы правят при поступлении на склад и хранят в выправленном состоянии. Это повышает производительность труда за счет увеличения партии листов одинаковой толщины.
В серийном производстве, например на судостроительных предприятиях, операции очистки металла, грунтовки, сушки, маркировки, разметки, резки выполняются на автоматизированных поточных линиях.
С выходом рольганга листы автоматически снимаются кантователем и в вертикальном положении транспортируются через последовательно расположенные камеры подогрева, дробеметную, грунтовки листов в электростатическом поле, терморадиационной сушки и выдаются в накопитель. Операции выполняются в автоматическом режиме и контролируются одним рабочим-оператором с пульта управления.
На участке тепловой резки заготовок резка листов толщиной более 2 мм с криволинейными кромками производится следующим образом.
По предварительно составленной программе с помощью чертежного устройства в масштабе 1:10 вычерчиваются чертежи основных деталей. Масштабные копии деталей вручную размещают в пределах масштабных контуров листа с учетом технологических требований и экономного использования материала. Компоновка производится на специальных столах, оборудованных системами присоса и координатомерами, для снятия координат характерных точек, необходимых для программирования резки. Описание карты раскроя в виде таблицы включает в себя кодовые номера детали, координаты двух точек каждой детали в системе координат листа, направление обхода каждой детали. Эти данные вводятся в ЭВМ, и на перфоленте выдается рабочая программа вырезки всего листа. Затем производится контрольное вычерчивание карты раскроя на чертежном устройстве, подключенном к ЭВМ. Подача листов осуществляется по рольгангам на раскроечных платформах (рис. 2.12).
Передача с рольганга одного направления на другие производится подъемом секций роликов. Разметка на разметочно-маркировочной машине осуществляется пневмокерном. Исполнительная часть машины 7 представляет собой портал продольного хода, на котором смонтирована тележка поперечного перемещения, на которой находится построитель знаков с рабочим инструментом. Производится разметка линий последующей гибки листовых деталей и маркировка, после чего на тех же раскроечных платформах 5 заготовки подаются к машинам для тепловой резки 8 (типа «Кристалл» с цифровым программным управлением). По окончании резки заготовки выдаются в зону действия перегружателя-кантователя 9, у которого имеется траверса с большим числом магнитов (до 800 шт.), которая снимает все детали, а если необходимо, то кантует их для зачистки грата на 180º. Затем возвращает их в исходное положение и укладывает на ленточный транспортер. Механизированная сортировка вырезанных деталей обеспечивается сортировщиком с вакуумными или магнитными присосками на траверсе. Этот сортировщик управляется оператором и способен раскладывать все крупные детали (более 0,7×0,7 м) в пачки в зависимости от маршрута их дальнейшей обработки.
Рис. 2.12. Схема участка разметки-маркировки и термической резки листов:
1 – накопитель; 2 – толкатель; 3 – двусторонний кантователь; 4 – приемный рольганг;
5 – раскроечная платформа; 6 – подающие рольганги; 7 – разметочно-маркировочная
машина; 8 – машины для тепловой резки; 9 – перегружатель-кантователь; 10 – ленточный транспортер; 11 – рольганг съема разрезанного листа; 12 – кантователь для сброса отходов;
13 – возвратный рольганг
Детали меньшего размера отсортировываются в процессе перехода с транспортерной ленты на рольганг. Они комплектуются в контейнеры на шаговом транспортере-комплектаторе, работающем в полуавтоматическом режиме.
Платформа 5 выполняет роль функции газорезательного стола. Поэтому уборка шлака из зоны резки осуществляется на позиции 12 наклоном платформы 5 и сбросом отходов в бункер. Затем платформа возвращается рольгангом 13 на приемный рольганг 4.
Тяжелый ручной труд можно устранить при резке листов на механических ножницах, или связанный с подачей листа к ножам и уборкой отходов. Для этого используется комплекс механизмов, управляемых одним оператором (рис. 2.13).
Рис. 2.13. Механизация подачи листа к гильотинным ножницам
Захват листа, его разворот и укладку на подающую тележку 5 осуществляют с помощью универсального портального манипулятора 8, имеющего колонну 7 с траверсой 6 снабженной вакуумными захватами. Уложенный на холостой рольганг 2 лист с помощью прижимов 4 крепится к механизму подачи 3. Самоходная тележка 9 подает лист к ножам 1, после чего механизмом 3 производится точная установка листа.
При резке по разметке или с помощью указателя, скользящего по масштабной линейке управление ножницами и механизмом подачи осуществляется оператором с пульта управления.
При резке партии одинаковых деталей по упору процесс может быть полностью автоматизирован. Подача листа отключается конечными выключателями. Детали собирают в тележку, подкатываемую под ножницы. Перед обрезкой кромок тележку откатывают и обрезки падают в приямок, откуда механизм сталкивает их в бункер.
Комплексная механизация заготовительных операций может быть представлена схемой поточной линии труб большого диаметра, изготавливаемых на Челябинском трубопрокатном заводе (рис. 2.14).
а б
Рис. 2.14. Схема расположения оборудования заготовительного участка гибки труб большого диаметра: 1 – листоукладчик; 2 – ж/д платформа; 3 – приемный рольганг; 4 – кромкострогальный станок; 5 – кромкогибочный станок; 6 – цепной транспортер; 7 и 8 – прессы
С железнодорожной платформы 2 листоукладчиком 1 листы по одному подаются на приемный рольганг 3 и направляются в зону действия кромкострогального стана 4 двухсторонней строжки кромок и снятия фасок под сварку. Формовка листа осуществляется в три этапа:
1) подгибка кромок на кромкогибочном стане 5;
2) предварительная формовка на прессе 7;
3) окончательная формовка на прессе 8 (рис. 2.14б).
На выходе из стана подгибки кромок лист захватывается упором цепного транспортера 6 и подается под пресс 7, одновременно выталкивая ранее сформованную заготовку. Предварительная формовка под прессом (рис. 2.14а) производится ходом пуансона до упора в постель с помощью кулис с роликами. Потом заготовка выталкивается на промежуточный рольганг, откуда цепным транспортером подается на окончательную формовку.
3. КРАТКАЯ ХАРАКТЕРИСТИКА ОПЕРАЦИЙ
ТЕХНОЛОГИЧЕСКИХ ПРОЦЕССОВ ИЗГОТОВЛЕНИЯ
СВАРНЫХ КОНСТРУКЦИЙ
В состав технологических процессов изготовления сварных конструкций входят различные операции, основные из которых можно назвать заготовительными, сборочными, сварочными, контрольными, термической обработки, транспортными и т.д.
Рассмотрим более подробно некоторые из них.
Заготовительные операции и приемы их выполнения были рассмотрены выше (см. 2.1).
Сборочные операции
После выполнения заготовительных операций детали и элементы сварных конструкций поступают на сборку.
Сборкой называется процесс последовательного соединения деталей между собой в порядке, предусмотренном чертежом и разработанном технологическим процессом для последующей сварки.
Основная цель технологического процесса сборки заключается в определении рациональной последовательности сборки отдельных деталей, обеспечивающих выполнение технических требований на изготовление данного изделия при минимальных затратах материалов, труда и времени.
Сборка конструкций может производиться только из выправленных деталей и элементов, очищенных от заусенцев, грязи, масла, ржавчины, влаги. Перед сборкой (рабочий) слесарь-сборщик визуально проверяет соответствие деталей требованиям чертежа и технологического процесса. Сопрягаемые поверхности и прилегающие к ним зоны собираемых деталей шириной не менее 20 мм очищаются от загрязнений наиболее тщательно.
При сборке не допускается изменение формы конструкций и деталей, не предусмотренное технологическим процессом, а при кантовке и транспортировке – остаточное деформирование их. Перенос и кантовка краном тяжёлых и крупногабаритных конструкций и их элементов, собранных только на прихватках, без применения приспособлений, обеспечивающих неизменяемость их формы, не допускается.
В процессе сборки детали закрепляют прижимами в приспособлениях, кондукторах, а иногда устанавливают вручную по разметке перед прихваткой.
Сборку деталей под стыковое соединение рекомендуется производить с использованием сборочных приспособлений – стяжных планок, скоб и т.п. Назначение приспособлений – обеспечивать быструю и точную сборку, стыковку элементов с удобством прихваток и последующей сварки с максимальным количеством сварки в нижнем положении.
При сборке стыковых соединений колонн и балок на полках необходимо устанавливать выводные планки размером не менее 100 50 мм и толщиной, равной толщине стыкуемых элементов.
Прихватки, предназначенные для соединения собираемых деталей, должны размещаться в местах расположения сварных швов, за исключением мест их пересечения.
В производстве сварных конструкций предполагается, что чем больше серия изготавливаемых деталей, тем выше должна быть степень механизации сварочных операций.
Универсальные приспособления бывают переносные и стационарные. Элементы прижима заготовки в приспособлениях перед прихваткой применяют различные – рычажные, эксцентриковые, клиновые, стяжки, струбцины, пневмо- и гидравлические прижимы.
Стационарные приспособления по функциональному назначению бывают самые различные, но они также имеют определённые виды прижимов.
Операции сборки под сварку зачастую не представляют особых технических трудностей, но порядок и количество прихваток и их размеры влияют на качество сварной конструкции.
Прихватки должны быть не более 20 мм и сечением 0,5 мм от сечения будущего шва и только в перекрываемых участках шва. Сварочный ток при прихватках должен быть выше на 20 % от номинального, чтобы обеспечить чёткий провар при прихватке. Прихватки нужно выполнять «вразброс», по логике ожидаемых деформаций и внутренних напряжений.
При сборке сварных конструкций обеспечивается такое взаимное расположение деталей собираемого сварного узла, в котором они должны находиться в готовом узле. Порядок сборки, устанавливаемый технологом-сварщиком, указывается в картах технологического процесса. Зазоры при сборке должны строго соответствовать чертежу. Превышение кромки одного их элементов стыкового соединения над другим, если оно не предусмотрено и не оговорено специально в чертеже, допускается по всей длине шва не более 0,2δ элемента
(до 4 мм) и 0,15 толщины элемента (свыше 4 мм, но не более1,5 мм). Местные превышения кромок определяют по наименьшей толщине свариваемых деталей. Превышение кромок контролируется до сварки.
Прихватки выполняют покрытыми электродами в защитных газах и реже под флюсом. Площадь сечения прихваток не должна превышать 2/3 площади сечения рабочего шва и составлять не более 25–30 мм2. Длина каждой прихватки должна быть равна (4–5)δ соединяемых деталей в пределах 30 < l < 100 мм. Чем меньше толщина свариваемых деталей, тем меньше расстояние между прихватками. В решетчатых конструкциях каждый элемент прихватывают с двух сторон швами длиной 30–40 мм катетом не более 5 мм.
Наложение прихваток разрешается вне мест расположения швов для временного скрепления деталей. Эти прихватки после выполнения своего назначения удаляют, а места их размещения защищают. Применяют также сплошной шов небольшого сечения – технологический шов. Это значительно повышает стойкость металла рабочего шва против кристаллизационных трещин и предотвращает нарушения взаимного расположения деталей в процессе сварки из-за растрескивания прихваток. Сборочные прихватки выполняют сварочными материалами тех же марок, что и при сварке сварной конструкции. Требования к качеству прихваток установлены те же, что и к сварным швам.
В процессе сварки основного шва прихватки и технологические швы перевариваются. Для применения деталей перед сваркой и в процессе её применяют технологические гребенки, удаляемые по мере образования шва.
Рис. 3.1. Схема закрепления листов перед сваркой:
1 – технологическая гребенка; 2 – свариваемые листы
В зависимости от типа производства, особенностей конструкции и технологических условий сборку можно выполнять различными способами: по разметке, по шаблонам или первому изделию, по сборочным отверстиям, в приспособлениях – универсальных, специализированных и специальных. Сборку по разметке ведут без приспособлений, при этом расположение деталей определяют разметкой по чертежу, затем их скрепляют прихватками, съёмными фиксаторами и т.п. Производительность способа низкая, применяют его в единичном производстве. Сборка сварных конструкций по шаблонам или первому изделию более производительна.
Использование сборочного оборудования обеспечивает наибольшую точность сборки при минимальной трудоёмкости. Основным назначением сборочного оборудования является фиксация и закрепление свариваемых деталей. Это оборудование разделяется на сборочное и сборочно-сварочное. На изделие, размещенное в сборочном оборудовании, накладываются только швы прихватки, а для изделий, размещенных в сборочно-сварочном оборудовании, – возможна полная или частичная сварка.
Выбор оборудования определяется условиями технологического процесса и зависит от формы, размеров и требуемой точности собираемых изделий, типа производства, вида сварки и других факторов. При изготовлении сварных конструкций в сборочно-сварочном оборудовании изделие не подвергается переустановке и промежуточной транспортировке, однако оно дороже и сложнее сборочного оборудования.
Сборочное оборудование может быть универсальным и специальным. Универсальное – предназначено для широкой номенклатуры изделий, его используют в единичном и мелкосерийном производстве. Специальное оборудование применяется для одного или нескольких однотипных изделий. Оно обеспечивает высокую производительность и высокое качество изделий и применяется преимущественно в серийном производстве.
Сварочные операции
Сварочные операции могут выполняться ручной дугой штучными электродами, полуавтоматической и автоматической сваркой, и выбор этот зависит от условий работы, конструктивных особенностей изделия. Для удобства и облегчения сварочных работ промышленностью выпускается большая номенклатура вспомогательного сварочного оборудования, различающаяся по назначению, возможностям и грузоподъёмности.
Позиционеры и различные кантователи позволяют устанавливать изделие в удобном для сварки положении.
Манипуляторы обеспечивают широкий диапазон угла наклона изделия и поворота его в необходимой позиции, регулируемую (сварочную) скорость вращения планшайбы (стола), а также маршевую скорость – для ускоренного поворота – вращения закрепления на планшайбе сварного узла. Все вращатели, манипуляторы, позиционеры имеют электропривод с редукторной группой.
Грузоподъёмность манипуляторов от 60 кг до 8 т и делится на десять различных типов. Специальные манипуляторы имеют грузоподъёмность до 100 т. Позиционеры имеют грузоподъёмность от 0,5 до 4 т.
Кантователи применяются для поворота нецилиндрических изделий вокруг оси. В зависимости от веса свариваемого узла они бывают с ручным и электрическим приводами.
В серийном производстве часто применяются сварочные кондукторы для некрупных узлов, в которых производится сборка, зажим деталей, а затем сварка в фиксированном положении.
Сварные конструкции, отвечающие любым эксплуатационным требованиям, могут быть изготовлены с применением существующих способов сварки, сгруппированных в 3 класса и 24 вида, входящие в них, каждый из которых включает ряд конкретных способов (ГОСТ 19521-7).
В качестве основных признаков, определяющих класс, принята форма энергии (термический, термомеханический, механический классы). Вид сварки определяется источником этой энергии.
Входящие в каждый вид способы сварки обладают определёнными техническими и технологическими возможностями сваривать те или иные по форме и размерам швы и соединения. Кроме того, осуществление каждого из способов сварки включает в себя определённые операции, состав и последовательность выполнения которых определяется конкретным способом сварки. Эти особенности являются основополагающими факторами, при анализе которых осуществляется выбор способа сварки применительно к созданию определённых сварных конструкций.
Исходя из методов выполнения операций, сопутствующих процессам сварки, их можно проводить вручную, механизировано по команде, подаваемой сварщиком-оператором, или автоматически.
В реальных условиях производства сварных конструкций широко используются не все, а только некоторые из существующих способов сварки.
Ведущее место занимают и будут занимать способы сварки плавлением – 62,9 % в 1980 г, 58 % (по приведённой трудоёмкости) в 1990 г. и 53 % в 2000 г. (что подтверждается многочисленными публикациями у нас и за рубежом). Следующие по объёму использования занимают контактные способы 32,6 %, 35,5 % и 39 % – соответственно.
В то же время возрастает применение специальных способов сварки – сварка трением, электронно-лучевая сварка, диффузионная и другие – 4,5 % в 1980 г, 6,6 % в 1990 г. и 8 % в 2000 г.
Способы сварки плавлением
Способы сварки плавлением в производстве сварных конструкций используются не в одинаковой степени. Наиболее распространены дуговые способы плавящимся электродом – сварка покрытыми электродами, полуавтоматические и автоматические способы сварки проволокой сплошного в среде защитных газов, под флюсом порошковой проволокой, самозащитной проволокой.
Дуговые способы обладают различными техническими характеристиками и экономическими показателями, поэтому выполняются с различной эффективностью.
В нашей стране в промышленности к началу 80-х годов соотношение было таково: 32 % – сварка штучными электродами, 51 % – полуавтоматическим способом сварки (в защитных газах сплошной и порошковой проволокой и под флюсом), 14 % – автоматической сваркой под флюсом и в защитных газах и около 3 % – другие дуговые способы сварки плавлением. В целом же по народному хозяйству доля РДС выше – 41 %, а суммарная доля автоматических и полуавтоматических способов сварки – 55 %.
Остановимся на общих характеристиках этих способов сварки.
РДС обладает относительно низкой производительностью. Коэффициент наплавки aн составляет 7–14 г/А·ч, в то время как при сварке под флюсом
14–20 г/А·ч и при сварке в СО2 12–24 г/А·ч. Применяя диаметр проволоки
3–6 мм, сварку ведут на токе 200–350 А, при этом плотность составляет
10–18 А/мм2. В то же время более производительная сварка под флюсом проводится в основном диаметром 2–6 мм на токах 200–1200 А при плотности
35–125 А/мм2. Повышение же скорости плавления металла при РДС за счёт увеличения диаметров электродов тока является нежелательным, так как приводит к ухудшению формирования шва, затрудняет сварку в вертикальном и потолочном положениях.
РДС относится к трудоёмким способам, поэтому выполняется рабочими более высокой квалификации.
Сварка покрытыми электродами имеет ряд разновидностей, характеризующихся различной производительностью. К ним можно отнести сварку электродами диаметром 8–10 мм, повышение производительности на 15–30 %, сварку спаренным электродом – на 20–40 %, при сварке пучком электродов – на 40–50 %. Имеют применение и другие разновидности, например добавление в покрытие проволоки железного порошка.
РДС достаточно универсальна, маневренна и имеет относительно низкие капитальные затраты, в то же время недостатки её при значительных объёмах применения отрицательно влияют на показатели производства сварных конструкций.
Полуавтоматические механизированные способы сварки сплошной и порошковой проволоками в защитных газах.
При изготовлении сварных конструкций предпочтение отдаётся полуавтоматической сварке в защитных газах. Сварка сплошной проволокой выполняется в СО2, в смесях СО2+Аr или СО2+Аr+О2.
Преимущества:
1) высокая степень концентрации энергии дуги, что увеличивает глубину проплавления, а при повышении скорости сварки имеет малую зону структурных превращений и вызывает малые деформации конструкций;
2) при полуавтоматической сварке можно выполнять швы без перерывов, уменьшить остановки, тогда отпадает необходимость заварки кратеров;
3) высокая производительность способа с малыми трудовыми затратами и расходом электронной проволоки;
4) проще техника сварки, так как ванна не закрыта шлаком.
Недостатки:
1) необходимость газовой защиты жидкой ванны;
2) малая маневренность из-за привязанности сварной горелки к подающему механизму полуавтомата и меньшей доступности в стеснённых местах в сварных конструкциях.
При сварке сплошной проволокой диаметром 1,2–1,6 мм на обратной полярности в чистом СО2 потери проволоки на разбрызгивание и угар могут достигать 10–12 %, это не только снижает эффективность способа, но и ухудшает формирование шва, вызывает дополнительные затраты на зачистку горелки и поверхности металла от брызг. Поэтому полуавтоматическую сварку сплошной проволокой производят в смесях Аr + (10–20 %) СО2 или 75 % Аr + 20 % СО2 + + 5 % О2, что снижает потери проволоки на разбрызгивание до 2,5–5 %. Существуют и другие меры борьбы с разбрызгиванием: сварка с оптимальной скоростью, поддержание постоянства длины дуги за счёт стабилизации напряжения источника питания, скорости подачи проволоки и вылета электрода, очистка проволоки от ржавчины, прокаливание её при Т = 200–250º в течение двух часов, выполнение сварки импульсной дугой.
Кроме полуавтоматической сварки в защитных газах, при сварке швов сечением свыше 30 мм иногда применяют полуавтоматическую сварку под флюсом. Техника выполнения сварки при этом требует соответствующего навыка.
Исходя из техники сварки, производительности, трудоёмкости полуавтоматические способы во многих случаях целесообразно применять вместо РДС штучными электродами.
Автоматизированные способы сварки
Из этих способов наиболее широко применяется дуговая сварка сплошной проволокой под флюсом и в защитных газах, а также ЭШС.
В этом случае механизируются и автоматически выполняются все операции, сопутствующие сварке, за исключением ручного включения автомата в работу. Следует отметить, что в производстве сварных конструкций необходимы способы и оборудование с ручным уровнем механизации и автоматизации операции сварки. Эта необходимость вызвана различной эффективностью применения оборудования в конкретных условиях, которые диктуются конструктивными особенностями изделий, их серийностью, требованиями к ним и их производству и т.д.
Автоматические способы производительны, обеспечивают высокое качество сварных соединений. Несмотря на высокую производительность, высокое качество сварных соединений, экономию сварных материалов и электроэнергии они в производстве сварных конструкций применяются ещё недостаточно. Среди способов сварки плавящимся электродом на долю автосварки под флюсом и в защитных газах приходится 13,6 %, а на ЭШС всего 0,8 %. Это объясняется рядом обстоятельств, к основным из которых можно отнести следующие: недостаточную универсальность этих способов и технологичность создаваемых сварных конструкций, невозможность выполнения швов в труднодоступных местах, сложность сварки криволинейных швов и швов, располагающихся в различных пространственных положениях, необходимость создания специализированных рабочих мест и оснащение их соответствующим вспомогательным оборудованием и дополнительные затраты на это оборудование, исключающие нормативную окупаемость. Для более полного их использования необходимо создать соответствующие организационные условия и переоснастить действующие производства сварных конструкций.
В настоящее время развитие и расширение автоматизированных способов сварки осуществляется:
– за счёт применения различных по назначению и конструктивному исполнению подвесных сварочных автоматов и тракторов и автоматических манипуляторов с программным управлением – промышленных роботов.
Подвесные автоматы с полной автоматизацией сварочных операций управляются дистанционно по жёсткой программе и могут выполнять поиск шва, возбуждение процесса сварки, копирование шва, заварку кратера и возврат в исходное положение. Высокая производительность процесса и качества сварки ставит автоматические дуговые способы сварки плавящимся электродом вне конкуренции.
ЭШС может выполняться электродными проволоками, плавящимся мундштуком с различными присадками и т.д. Соединения в основном стыковые δ от 50 до 60 мм и практически до любых толщин. Такие соединения, кроме ЭШС, можно выполнять многопроходной дуговой сваркой в узкий зазор. При этом соединения обладают высокими свойствами, и для снятия остаточных напряжений требуется только высокий отпуск.
В отдельных случаях применяется автоматическая дуговая точечная сварка (АДТС). Она выполняется в СО2 при сварке деталей нахлесточных соединений δ = 5–6 мм без предварительной пробивки отверстий, а также под слоем флюса при сварке деталей больших толщин по предварительно высверленным отверстиям. Соединения качественные, процесс легко автоматизируется, могут выполняться без снятия окалины на горячекатаном прокате. Она оказывается более перспективной при изготовлении крупногабаритных плоскостных конструкций, где доступ сварочного инструмента возможен только с одной стороны.
Среди дуговых способов сварки имеется перспективный способ сварки неплавящимся электродом (вольфрамовым и др.) в среде инертных газов (в основном Ar). Им свариваются конструкции из Al, Mg, Ti сплавов, нержавеющих сталей. Соединения в основном стыковые, бортовые, толщина металла 3–4 мм без разделки кромок. С применением присадочной проволоки можно сваривать угловые швы в тавровых и нахлесточных соединениях, а стыковые – δ > 4 мм, но с обязательной разделкой кромок.
В группу сварки неплавящимся электродом входит и сварка угольным электродом, осуществляемая в СО2 или без защиты.
Контактная сварка
Контактная сварка включает множество различных способов. К основным из них относятся группы способов сварки – точечной, шовной, рельефной, стыковой. При этом по структуре и количеству выпускаемых в стране сварочных машин до 70–80 % занимает точечная и рельефная сварка, 5–10 % – шовная и 15–20 % – контактная стыковая. В США и Японии, например, точечную и рельефную сварки применяют больше (в большем объёме), чем стыковую.
Исходя из динамики применения контактной сварки удельный вес сварных конструкций, изготавливаемых с применением контактной сварки, увеличивается, и в 2000 году возрос с 32,6 % (1980 г.) до 39 %.
К достоинствам контактной сварки относятся высокая производительность, выполнение сварки без присадочных материалов, высокий уровень механизации и автоматизации сварочных операций, относительно простое и надёжное в эксплуатации сварочное оборудование. Кроме того, сварные соединения имеют высокое качество, при этом химический состав зоны соединения не изменяется (при точечной и шовной сварке) или изменяется незначительно (при стыковой сварке), швы получаются без пор, а при оптимальных режимах – и без трещин.
Точечной сваркой можно получать различные конструкции сварных соединений, например в автомобилестроении (рис. 3.2).
Рис. 3.2. Различные конструкции сварных соединений с помощью точечной сварки
Особенно широко она применяется при изготовлении штампосварных конструкций из холоднокатаной конструкционной стали с малым содержанием углерода с толщиной деталей от 0,5 до 2,5 мм и редко до 4 мм, не требующих очистки поверхностей от окалины в местах наложения точечных швов. Этим способом свариваются алюминиевые, магниевые, титановые и другие сплавы.
Применение контактной точечной сварки деталей толщиной 5–10 мм ограничено необходимостью обязательной очистки свариваемых поверхностей (например, при сварке горячекатаного проката с окалиной), а также интенсивным износом электродов, при этом изменяются режимы сварки, требуется частая переточка электродов.
Достоинства способа точечной сварки (высокая производительность и надёжность машин) предопределили области его применения – крупносерийное и массовое производство тонколистовых конструкций (например, при изготовлении кузовов легковых автомобилей, в сельскохозяйственном машиностроении, электротехнической промышленности, транспортном машиностроении и других отраслях промышленности).
Сварка осуществляется универсальными одноточечными, специальными многоточечными и подвесными клещами. В условиях крупносерийного и массового производства конструкций точечная сварка осуществляется в основном автоматическими многоточечными машинами, обычно встраиваемыми в автоматизированные поточные линии, в последние годы сварка всё чаще выполняется промышленными роботами.
Динамику роста парка промышленных роботов, в состав которых входит 15 % роботов для контактной сварки, можно судить по данным зарубежной статистики: в 1975 г. – 9,9 тысяч штук, 1980 г. – 25 тысяч штук, 1990 г. – 120 и в 2000 г. – 220 тысяч штук, то есть промышленные роботы характеризуются как одно из основных средств в повышении уровня механизации и автоматизации производства сварных конструкций.
Рельефная сварка является разновидностью точечной сварки, при этом контакт между соединяемыми деталями создаётся не рабочими поверхностями электродов контактных машин, а местными выступами (рельефами) специально созданными на одной из свариваемых деталей. Форма сварных швов при рельефной сварке определяется формой выштамповок – контактируемых поверхностей на свариваемых деталях.
Сварка выполняется электродами с развитыми контактирующими поверхностями, соединения получаются без вмятин с хорошим внешним видом.
Шовной сваркой получают нахлёсточные и стыковые соединения. При сварке встык между роликом машины и поверхностью помещается тонкая полоска (фольга), которая совместно с торцами в процессе сварки расплавляется, заполняя зазор стыка. Шовная сварка применяется при изготовлении конструкций из листов толщиной до 1 мм (максимум – 2 мм). Скорость сварки до 300 м/час и более. Шовной сваркой изготавливают различные ёмкости, радиаторы для отопления жилых зданий, при изготовлении мембран, сильфонов в приборостроении.
Стыковая контактная сварка относится к одному из перспективных способов. В ряде случаев она заменяет дуговую сварку плавлением.
Применяют её для сварки различных по сечению профилей из сталей и сплавов, в том числе и разнородных. С использованием технологии импульсного оплавления на машине мощностью 800 кВт можно получать соединения деталей сечением 100–150 тысяч мм2. Способ получил широкое распространение при сварке железнодорожных рельсов, труб большого диаметра и других изделий.
Специальные способы сварки
В ряде случаев они эффективно используются вместо сварки плавлением и контактных способов, несмотря на небольшой темп роста и объём применения. Это относится к таким способам, как сварка трением, ЭЛС, сварка взрывом, диффузионная сварка, ультразвуковая и т.д., а также к различным видам пайки.
Электронно-лучевая сварка перспективна для сварки активных и тугоплавких металлов. К началу 1975 года в мире работали 1300–1400 установок, в 1980 г. – 6000 штук, к 2000 году их число достигло 10000 штук. Электронный луч обладает большой мощностью, изменяющейся в широком диапазоне, поэтому ЭЛС можно использовать и в электронике, и приборостроении, а также при изготовлении крупногабаритных изделий. Она широко используется в машиностроении, тракторном машиностроении – блок шестерён, детали коробки передач и т.д.
Сварка трением. В 1980 году мировой парк машин для сварки трением составлял 4500 штук. Она относится к одному из способов, который в последние годы интенсивно развивается во всех странах мира. Она применяется для сварки стыковых и Т-образных соединений, в которых круглые детали привариваются к плоским поверхностям (рис. 3.3). При этом необходимо, чтобы хотя бы одна деталь была телом вращения.
Рис. 3.3. Виды соединений при сварке трением
Способ производителен, обеспечивает высокое качество сварных соединений, хорошо поддаётся механизации и автоматизации; не требуется газовая и другая защита зоны сварки.
Диффузионной сваркой можно сваривать разнородные металлы и сплавы с резко отличающимися теплофизическими характеристиками, а также соединять малопластичные и тугоплавкие материалы.
К недостаткам можно отнести необходимость тщательной подготовки и подгонки соединяемых поверхностей, значительные затраты для сварки в вакууме.
Применяется диффузионная сварка в электронной промышленности для получения вакуум-плотных швов, термостойких и вибростойких соединений, можно приваривать, например, фольгу к массивной детали.
Ультразвуковая сварка применяется для сварки как металлов, так и пластмасс. Легко соединяются пластичные металлы (медь, алюминий, серебро и т.д.) между собой и в сочетании с малопластичными металлами (рис. 3.4). Можно выполнять сварку металлов со стеклом, керамикой. Особенностью является то, что не требует тщательной подготовки свариваемых поверхностей.
Для сварки применяются колебательные системы различных типов.
а б в
Рис. 3.4. Ультразвуковая сварка
Основной тип соединений – нахлёсточный. Сварка может выполняться точечными и непрерывными швами. Диапазон толщин – от микрон до 1 мм. Толщина второй детали может не ограничиваться.
Холодная сварка обеспечивается за счёт совместных пластических деформаций соединяемых деталей без внешнего нагрева, при этом температура, при которой происходит сварка, может быть сколь угодно низкой и даже отрицательной. Сваривают пластичные металлы, определяемые критерием свариваемости. Схемы сварки: точечная, шовная, стыковая. Точечной сваркой можно сваривать, например, листовой алюминий толщиной 0,1–10 мм; стыковой сваркой – провода площадью до 650 мм2.
Сварка пластмасс. Процесс сварки происходит в пределах температурного интервала сварки (ТИС) пластмасс Способы сварки: контактно-тепловая листов и труб, сварка газовым теплоносителем с присадочным и без присадочного материала, сварка ТВЧ, УЗС, трением, сварка лучом лазера и т.д.
Наплавка. Применяют для нанесения на поверхность изделия слоя материала с заданным составом и свойствами. Используется как при изготовлении новых деталей (например, клапанов двигателей внутреннего сгорания), так и при восстановлении изношенных деталей (например, колёсных пар железнодорожного подвижного состава). Для наплавки используют способы дуговой сварки. Широко применяются способы наплавки под флюсом, порошковыми проволоками и лентами. В настоящее время применяются различные специальные способы наплавки – вибродуговая, плазменная, газопорошковая, с индукционным нагревом, электрошлаковая, электроконтактная и др.
Дата добавления: 2019-07-15; просмотров: 1574; Мы поможем в написании вашей работы! |
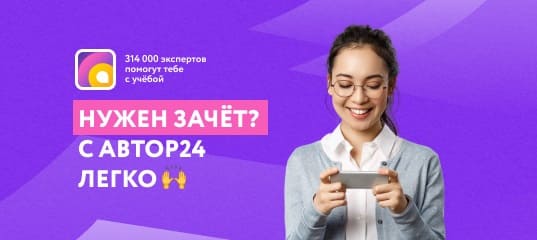
Мы поможем в написании ваших работ!