Определение действительного числа тарелок
Действительное число тарелок в ректификационных колоннах всегда больше теоретического числа, поскольку в реальных условиях равновесие фаз в результате контактного тепломассообмена на тарелках не достигается. Другими словами, коэффициент полезного действия тарелки всегда меньше единицы. Известно несколько методов расчета действительного числа тарелок. В данном случае мы используем графоаналитический метод, как наиболее простой и менее трудоемкий, хотя и несколько менее точный. В соответствии с этим методом действительное число тарелок определяется по уравнению:
(2.17)
здесь h - усредненный коэффициент полезного действия тарелки для всей колонны в целом [4, стр. 65];
N – теоретическое число тарелок.
По литературным данным к. п. д. тарелки изменяется в пределах h = 0,2 ¸ 0,9. При выборе значения к. п. д. тарелки можно пользоваться обобщенным графиком [4, стр. 32] зависимости к. п. д. от произведения относительной летучести a на динамический коэффициент вязкости m (в мПа*с) перегоняемой смеси.
Относительную летучесть определяют по формуле:
(2.18)
где, y* и x* - соответственно равновесные составы паровой и жидкой фаз на соответствующих тарелках (y*нк = 0,712, x*нк = 0,212).
y* и x* определяем из рис. 2 при средней температуре верха и низа колонны: .
Динамический коэффициент вязкости смеси определяется по формуле:
(2.19)
где, m - динамическая вязкость веществ (метанола, формальдегида и воды) при tср, Па*с;
|
|
М – молекулярные массы веществ (метанола, формальдегида и воды);
Тср – средняя температура в К (81,6 + 273 = 354,6°С).
Рассчитываем вязкость воды и метанола при tср.= 81,6°С:
Данные взяты из справочника [5, стр. 61 ].
При температуре 80°С вязкость равна 0,657 Па*с, а при температуре 100°С вязкость равна 0,234 Па*с, определяем вязкость при 81,6°С:
(0,657 - 0,234)/20*1,6 = 0,00003384 Па*с;
0,657 – 0,00003384 = 0,66 Па*с (вода).
При температуре 80°С вязкость равна 0,29 Па*с, а при температуре 100°С вязкость равна 0,24 Па*с, определяем вязкость при 81,6°С:
(0,29 – 0,24)/20*1,6 = 0,0000064 Па*с;
0,29 – 0,0000064 = 0,29 Па*с (метанол).
Вязкость формальдегида принимаем 0,91 кг*с/м2 из [6, стр. 78].
Переводим в Па*с:
0,91 кг*с/м2 = 0,000091 кг*с/см2,
1 кг*с/см2 - 9,8*104 Па
0,000091 - x
x = (0,000091*9,8*104)/1 = 8,918 Па = 8,918/3600 = 0,0025 Па*с.
КПД » 0,27;
ТЕПЛОВОЙ БАЛАНС
Тепловой баланс ректификационной колонны непрерывного действия с дефлегматором составляется для определения расхода греющего пара на процесс ректификации.
Приход теплоты:
1) с исходной смесью
(2.20)
2) с флегмой
(2.21)
3) с греющим паром
(2.22)
Расход теплоты:
1) с кубовым остатком
(2.23)
|
|
2) с парами низкокипящего компонента из колонны
(2.24)
3) с конденсатом греющего пара
(2.25)
4) потери теплоты в окружающую среду Qпот.
Таким образом,
(2.26)
Подставим в уравнение (2.26)
получим
(2.27)
где, W, P – производительность кубового остатка и дистиллята, кг/с;
R – флегмовое число;
Cpw, Cpf – теплоемкости кубового остатка и дистиллята, Дж/кг*К;
tw, tf – температуры кипения кубового остатка и дистиллята, °С;
rф – теплота парообразования флегмы, Дж/кг (rф = rp);
Iп – энтальпия пара, выходящего из колонны, Дж/кг.
Расход греющего пара в кубе
(2.28)
Расход греющего пара на нагревание исходной смеси в подогревателе:
(2.29)
Для выполнения тепловых расчетов необходимо определить теплоемкости исходной смеси, дистиллята и кубового остатка при температурах их кипения.
Рассчитываем теплоемкости метилового спирта при 64,8; 76,9 и 98,4°С:
При температуре 60°С теплоемкость равна 0,66 ккал/кг*град, а при 80°С теплоемкость равна 0,684 ккал/кг*град [5, стр.69].
Определяем теплоемкость при температуре 64,8°С:
(0,684 – 0,66)/20*4,8 = 0,00576;
0,66 + 0,00576 = 0,67 ккал/кг*град;
Срр = 0,67*4190 = 2807,3 Дж/кг*К.
Определяем теплоемкость при температуре 76,9°С:
(0,684 - 0,66)/20*16,9 = 0,02028;
|
|
0,66 + 0,02028 = 0,68 ккал/кг*град;
Срf = 0,68*4190 = 2849,2 Дж/кг*К.
При температуре 80°С теплоемкость равна 0,684 ккал/кг*град, а при 100°С теплоемкость равна 0,708 ккал/кг*град [6, стр. 78].
Определяем теплоемкость при температуре 64,8°С:
(0,708 – 0,684)/20*18,4 = 0,02208;
0,684 + 0,02208 = 0,71 ккал/кг*град;
Срw = 0,71*4190 = 2974,9 Дж/кг*К.
Рассчитываем теплоемкости формальдегида при 64,8; 76,9 и 98,4°С по формуле:
(2.30)
где, a, b, c – коэффициенты, взятые из [справ.], (а = 18,82; b = 58,38*102; с = -15,61*106);
Т – температура кипения исходной смеси, дистиллята и кубового остатка, в К.
При tp = 64,8°C; T = 337,8 K;
При tf = 76,9°C; T = 349,9 K.
При tw = 98,4°C; T = 371,4 K.
Теплоемкости исходной смеси, дистиллята и кубового остатка, представляющих смесь метилового спирта и формальдегида, определяются по формуле:
(2.31)
где, Cp – теплоемкости метанола и формальдегида, Дж/кг*К;
- массовый состав дистиллята, исходной смеси и кубового остатка.
Теплоту парообразования флегмы при t = 64,8°С (температура кипения метанола) определяем по метанолу и воде, т.к. формальдегида очень мало и им можно пренебречь:
(2.32)
где, rнк, rвк – теплоты образования метанола и воды, Дж/кг;
- массовый состав дистиллята.
|
|
Находим теплоту парообразования метанола при t = 64,8°С:
При температуре 60°С теплота парообразования равна 265 ккал/кг, а при 80°С теплота парообразования равна 252 ккал/кг [5, стр. 90].
(265 – 252)/20*4,8 = 3,12;
265 – 3,12 = 261,88 ккал/кг = 261,88*4,19 = 1097,28 кДж/кг.
Теплота парообразования воды принимается из [5. стр, 78]
r = 2336 кДж/кг (при Т = 68,7°С, т Р = 0,3 кг*с/см2).
Энтальпия пара, выходящего из колонны определяется по формуле:
(2.33)
Потери теплоты принимаем равными 3% от ее расхода в кубе.
Расход теплоты в кубе колонны с учетом тепловых потерь определяем по формуле (2.27):
Расход греющего пара в кубе колонны по формуле (2.28):
где, rгр.п = 2206*103 Дж/кг (определяется из справ. по tw=98,4°C при t = 119,6°С);
Принимая повышение температуры воды в холодильнике на 20°С, определяем расход воды:
в дефлегматоре по формуле:
(2.34)
где,
Cpв – теплоемкость воды, 4190 Дж/кг*К.
в холодильнике дистиллята
(2.35)
в холодильнике кубового остатка
(2.36)
Общий расход воды равен:
ТЕХНОЛОГИЧЕСКИЙ РАСЧЕТ
1. Определение объемов пара и жидкости, проходящих через колонну
Сначала определим мольные массы жидкостей и паров, средние мольные и массовые концентрации жидкостей и паров в колонне.
Средний мольный состав жидкости:
в верхней части колонны определяется
(2.37)
где, xf, xp – мольный состав исходной смеси и дистиллята.
в нижней части колонны по формуле:
(2.38)
где, xw, xf – мольный состав кубового остатка и исходной смеси.
Средний массовый состав жидкости:
в верхней части колонны по формуле:
(2.39)
где, - массовый состав исходной смеси и дистиллята.
в нижней части колонны
(2.40)
где, - массовый состав исходной смеси и кубового остатка.
Средняя мольная масса жидкости:
в верхней части колонны
(2.41)
в нижней части колонны
(2.42)
Мольная масса:
дистиллята по формуле:
(2.43)
исходной смеси:
(2.44)
кубового остатка
(2.45)
Средний мольный состав паров:
в верхней части колонны
(2.46)
в нижней части колонны
(2.47)
Средняя мольная масса паров:
в верхней части колонны
(2.48)
в нижней части колонны
(2.49)
Средняя плотность жидкости:
в верхней части колонны
(2.50)
где, - плотность метанола и формальдегида, кг/м3.
Плотности НК и ВК компонентов выбирают при средней температуре tср в нижней и верхней частях колонны:
(2.51)
Определяем плотность метанола по tср по данным взятым из справочника [4, стр. 68 ].
При температуре 60°С плотность равна 756 кг/м3, а при температуре 80°С – 736 кг/м3. Находим при температуре 70,9°С:
(756 – 736)/20*10,9 = 10,9;
756 – 10,9 = 745,1 кг/м3.
А при температуре 87,6°С:
(736 – 714)/20*7,6 = 8,36;
736 – 8,36 = 727,6 кг/м3.
Плотность формальдегида берем из справ.[4, стр. 57]: при температуре 70,9°С плотность равна 0,263 кг/м3, а при температуре 87,6°С – 0,131 кг/м3.
в нижней части колонны
(2.52)
Средняя плотность пара по формуле:
в верхней части колонны
(2.53)
в нижней части колонны
(2.54)
Массовый расход жидкости:
в верхней части колонны
(2.54)
где, Р – производительность по дистилляту, кг/с;
R – флегмовое число.
в нижней части колонны
(2.55)
где, F – производительность по исходной смеси, кг/с;
Мp, Mf – мольная масса дистиллята и исходной смеси, кг/кмоль.
Массовый поток пара:
в верхней части колонны
(2.56)
в нижней части колонны
(2.57)
2. Расчет скорости пара и диаметра колонны
Допустимую скорость паров в колонне с колпачковыми тарелками находится по формуле:
(2.58)
где, - допустимая скорость паров, м/с;
dk – диаметр колпачка, м (выбираем из справ. [2, стр. 34 ] 80 мм = 0,08 м);
Ht – расстояние между тарелками, м (выбираем из справ. [2, стр. 25 ] 0,37 м);
- средняя плотность жидкости пара в верху и внизу колонны, кг/м3.
Для верхней и нижней части колонны предельная скорость паров в колонне определяется по формуле:
В соответствии с рекомендациями рабочую скорость паров в колонне определяем по формуле:
(2.59)
Рабочую скорость паров в верхней и нижней части колонны соответственно равна:
Диаметр колонны определяется по формуле:
(2.60)
где, G – массовый поток пара в верхней и нижней части колонны, кг/с;
- рабочая скорость паров в верхней и нижней части колонны, м/с;
- средняя плотность пара в верхней и нижней части колонны, кг/м3.
Ориентировочный диаметр верхней и нижней части колонны:
Тогда
Принимая ректификационную колонну с диаметром в верхней и нижней части, равным 1000 м. При этом действительная рабочая скорость пара при средней скорости паров будет равна:
(2.61)
По ОСТ 26 – 808 – 73 для колонны с диаметром 1000 м выбираем колпачковую тарелку, снабженную капсульными колпачками типа ТСК – Р со следующими конструктивными размерами: площадь поперечного сечения 0,78 м2; число колпачков 43 шт; шаг колпачков 110 мм; расстояние между тарелками 300 мм; площадь поперечного сечения паровых патрубков 0,088 м2; диаметр колпачка 80 мм; высота прорези 20 – 30 мм; длина линии барботажа 10,8 м; периметр слива Lc – 0,665 м ;сечение перелива 0,064 м2; свободные сечения тарелки 0,09 м2; относительная площадь прохода пара 11,5%; масса 57,8 кг [ ].
Расчет высоты колонны
Расчет высоты тарельчатой колонны рассчитывается по формуле:
(2.62)
где, - высота тарельчатой (рабочей) части колонны, м;
Zв – расстояние от верхней тарелки до крышки принимается равной 0,8 м (в зависимости от диаметра колонны);
Zн – расстояние от нижней тарелки до днища принимается 1,7 м (в зависимости от диаметра колонны);
Расчет тепловой изоляции
Основной целью расчета тепловой изоляции является выбор теплоизоляционного материала и расчет его толщины для минимизации тепловых потерь в окружающую среду и обеспечения требований техники безопасности. Обычно, расчет тепловой изоляции проводят из условия заданной температуры наружного слоя изоляции, которая не должна превышать 45°С. Толщину слоя теплоизоляционного материала определяют по уравнению:
(2.63)
где, t и tст – соответственно температура внутреннего слоя тепловой изоляции (температуру внутреннего слоя тепловой изоляции t можно принять равной температуре среды в колонне t = tср = 81,6°С) и tст = 45°С;
- тепловые потери в окружающую среду, Дж;
a - суммарный коэффициент теплоотдачи конвекцией и излучением, Вт/м2*К;
- коэффициент теплопроводности, Вт/м*К;
Fн – поверхность теплообмена, м2
Поверхность колонны определяется по формуле:
(2.64)
(2.65)
(2.66)
где, Fкол – поверхность колонны, м2;
Fкр – поверхность крышки, м2;
Dср – 1 м.
Величину тепловых потерь в окружающую среду можно рассчитать по уравнению теплоотдачи:
(2.67)
где, tокр - температура окружающей среды равна 5°С;
a - суммарный коэффициент теплоотдачи конвекцией и излучением,
.
Выбираем коэффициент теплопроводности из справ. [3, стр. 43 ] равный 0,076 Вт/м*К, материал – шлаковая вата.
Толщину слоя теплоизоляционного материала:
ГИДРАВЛИЧЕСКИЙ РАСЧЕТ
Основной целью гидравлического расчета является определение гидравлических сопротивлений, которые возникают в процессе прохождения пара через ректификационную колонну из куба через контактные устройства в дефлегматор. В целом общие потери напора для всех ректификационных колонн позволяют рассчитать необходимое повышение температуры кипения смеси в кубе колонны.
Общие потери давления DР на одной отдельно взятой тарелке составят:
(2.68)
где, DРс – сопротивление сухой тарелки, Па;
DРж – сопротивление слоя жидкости, Па;
DРs – сопротивление за счет поверхностного натяжения жидкости, Па.
Сопротивление сухой тарелки по формуле:
(2.69)
где, - средняя плотность пара в верхней и нижней части колонны, кг/м3;
- скорость пара в горловине колпачка, м/с (определяется по объемному расходу пара и поперечному сечению паровых патрубков).
Объемный расход пара равен:
(2.70)
где, S – поперечное сечение паровых патрубков равное 0,088 м2, берется из справ. [3, стр. 23 ];
V - объемный расход пара находится по формуле:
(2.71)
где, Мср – средняя мольная масса паров.
Объемный расход пара в верхней и нижней части колонны:
Скорость пара в горловине колпачка для верха и низа колонны:
Сопротивление сухой тарелки для верха и низа колонны:
Сопротивление слоя жидкости по формуле:
(2.72)
где, - средняя плотность жидкости в верхней и нижней части колонны, кг/м3;
g – 9,8 м/с2;
hs - высота барботажного слоя жидкости на тарелке, м (из справ. [3, стр. 56] равная 35,5 м = 0,0355 м).
Сопротивление за счет поверхностного натяжения жидкости - DРs для колпачковых тарелок незначительно и им допускается пренебречь.
Общие потери давления DР на одной отдельно взятой тарелке:
МЕХАНИЧЕСКИЙ РАСЧЕТ
Расчет
Исходные данные
D = 100 см – внутренний диаметр аппарата;
Р = 1 кг*с/см2 – расчетное наружное давление;
t = 100°С – расчетная температура;
= 1600 кг*с/см2 – допускаемое напряжение для стали 09Г2С при t = 100°С;
Е = 1,91*106 кг*с/см2 – модуль продольной упругости для 09Г2С при t = 100°С;
С = 0,35 см – толщина плакирующего слоя;
Е = 1,99*106 кг*с/см2 – модуль продольной упругости для стали 09Г2С при t = 20°С;
= 2800 кг*с/см2 – предел текучести для стали 09Г2С при t = 20°С.
Расчет обечайки
Обечайка нагружена наружным давлением.
Толщину стенки приближенно определяем по формуле:
(2.73)
Коэффициент К2 определяем по номограмме. Для этого находим К1 и К3:
К2 = 0,82,
Значит SR = 0,82 см.
Исполнительная толщина S ³ SR +C,
S ³ 0,82 + 0,35 + 0,156 = 2,806 см.
Принимаем исполнительную толщину S = 20 мм и укрепляем обечайку ребрами жесткости.
Условие применения формул:
Условие выполняется.
Расчетные параметры подкрепленной обечайки:
эффективная длина стенки обечайки:
где, l1 = 200 см – расстояние между двумя кольцами жесткости по осям;
t = 4,6 см – ширина поперечного сечения кольцами жесткости в месте его приварки к обечайке (рис 2.5)
l = 5,755 см;
h2 = 11 см;
IК = 174 см4;
Ак = 10,9 см2.
Эффективный момент инерции расчетного поперечного сечения кольца жесткости:
(2.74)
Коэффициент жесткости обечайки, подкрепленной ребрами жесткости:
(2.75)
Допускаемое наружное давление определяется из условия:
где, - допускаемое наружное давление, определяемое исходя из условия устойчивости всей обечайки;
- допускаемое наружное давление, определяемое исходя из условий устойчивости обечайки между кольцами жесткости.
(2.76)
где, - допускаемое наружное давление, определяемое из условия прочности всей обечайки;
(2.77)
=1,0 и
=1,0;
- допускаемое напряжение для материала колец (сталь ВСт3) при t=100°С;
- допускаемое наружное давление из условий устойчивости в пределах упругости;
(2.78)
где,
В2 = 0,0084.
Допускаемое наружное давление, определяется исходя из условий устойчивости обечайки между кольцами жесткости:
(2.79)
где, - допускаемое давление из условия прочности;
- допускаемое давление из условия устойчивости в пределах упругости.
(2.80)
(2.81)
где,
Значит, допускаемое наружное давление
Условие прочности:
18,52 кгс/см2 > 1 кгс/см2
Условие прочности выполняется.
Условие прочности при гидроиспытании:
где, - допускаемое давление при гидроиспытании;
Рпр – пробное давление гидроиспытания.
(2.82)
- допускаемое напряжение для гидроиспытания;
nt = 1,1 – коэффициент запаса прочности.
- коэффициент прочности сварных соединений.
но не менее 2 кгс/см2;
Значит принимаем Рпр = 2 кгс/см2.
Гидростатическое давление столба жидкости Рст = 4,9 кгс/см2. С учетом этого давления Пир = 6,9 кгс/см2.
6,9 кгс/см2 < 68,1 кгс/см2.
Условие прочности выполняется.
Расчет эллиптического днища
Днище нагружено наружным давлением. Расчетная толщина стенки определяется по формуле:
(2.83)
Предварительно принимаем Кэ = 0,9.
где, R = D – радиус кривизны в вершине днища.
Принимаем S1 = 10 мм.
Допускаемое наружное давление:
(2.84)
где, - допускаемое давление из условия прочности;
- допускаемое давление из условия устойчивости;
(2.85)
(2.86)
где, Кэ – коэффициент.
При
Кэ = 0,95.
Условие прочности:
Условие прочности выполняется.
Условие прочности при гидроиспытании
где, Рпр = 69 кгс/см2;
- допускаемое давление при гидроиспытании.
(2.87)
23,3 кгс/см2 > 6,9 кгс/см2.
Условие прочности выполняется.
Формулы (2.83) и (2.84) применимы при выполнение условий:
Условие выполняется.
Расчет укрепления отверстий
Расчетные диаметры:
для цилиндрической обечайки
DR = D = 100 см;
для эллиптического днища
где, x – расстояние от центра укрепляемого отверстия до оси эллиптического днища для верхнего днища x = 0.
для нижнего днища x = 40 см
Расчетный диаметр отверстия в стенке обечайки или днища при наличии штуцера с круговым поперечным сечением, ось которого совпадает с нормалью к поверхности в центре отверстия равен:
(2.88)
Для обечайки:
где, - добавка на минусовый допуск по толщине листа и на коррозию.
Для днища:
где, d – максимальный диаметр отверстия.
Условие применения формул:
для обечайки:
Условия выполняются.
для эллиптического днища:
0,404 < 0,5;
0,01 < 0,7.
Условие выполняются.
Расчетный диаметр одиночного отверстия, не требующего дополнительного укрепления, вычисляют по формуле:
(2.89)
для обечайки:
где,
К2 = 0,3 – коэффициент.
Значит, отверстия на обечайки под люк dy = 60 требует укрепления штуцером. При этом должно выполняться условие:
(2.90)
где, lIR – расчетная длина внешней части штуцера;
l3R – расчетная длина внутренней части штуцера;
S1 – исполнительная толщина стенки штуцера;
S1R – расчетная толщина стенки штуцера;
S3 – исполнительная толщина внутренней части штуцера;
lR – расчетная ширина зоны укрепления в окрестности штуцера;
S – исполнительная толщина обечайки;
SR – расчетная толщина обечайки;
dOR – расчетный диаметр отверстия, не требующего укрепления при отсутствии избыточной толщины стенки сосуда;
(2.91)
l1 = 20 см; S3 = S1 = 1,0 см.
Принимаем liR = 8,8 см.
(2.92)
- отношение допускаемых напряжений;
liR = 8,8.
Принимаем l3R = 3,1 см.
Принимаем l = 12,3 см.
Условие укрепления выполняются.
Для днища верхнего
dR = 40,36 см.
dR > d0.
Значит, отверстие dy = 400 на верхнем днище нужно укрепить штуцером. При этом должно выполняться условие по формуле (2.90).
Принимаем liR = 6,25 см.
Принимаем l3 = 2,1 см.
т.к. l = 0,
то
19,2 > 11,4
Условие выполняется.
Для нижнего днища
x = 40
Отверстие считается одинаковым, если ближайшее к нему отверстие не оказывает на него влияния, что имеет место, когда расстояние между наружными поверхностями соответствующих штуцеров удовлетворяет условию:
(2.93)
d = 24,4 см
24,4 < 29,5
Значит, эти отверстия взаимновлияющие.
Расчетный диаметр отверстия смещенного штуцера на эллиптическом днище:
(2.94)
Значит, отверстия на нижнем днище укрепления не требуют. Теперь проверим достаточность укрепления перемычки между отверстиями. Для этого определим допускаемое давление для перемычки:
(2.95)
где,
К1 =2;
Так как l1 и l2 величины большие, принимаем
так как
то
Значит, V = 0,59.
так как
Значит, условие укрепления выполняется.
Расчет массы аппарата
Масса тарелки:
(2.96)
Толщину выбираем в зависимости от диаметра (S = 10 мм = 0,01 м); Hk = 12 м.
Масса обечайки:
Масса раствора:
Масса крышки:
(2.97)
Масса аппарата:
G1(апп) = 12172,6 кг = 121726 Н.
Масса аппарата при гидроиспытании:
19450 кг – масса воды при гидроиспытании.
Расчет на ветровую нагрузку
В качестве расчетной схемы аппарата колонного типа принимают консольный упругозащемленный стержень. Аппарат по высоте разбивают на 7 участков. Вес каждого участка принимаем сосредоточенным в середине участка. Ветровая нагрузка, распределенная непрерывно по высоте аппарата, заменяется сосредоточенными горизонтальными силами, приложенными в серединах участков.
Определение периода собственных колебаний
Период основного тона собственных колебаний аппарата постоянного сечения определяем по формуле:
(2.98)
где, (2.99)
где, I – момент инерции верхнего основного металлического сечения аппарата относительно центральной оси;
IF – минимальный момент инерции подошвы фундамента:
СF – коэффициент неравномерности сжатия грунта; выбирается в зависимости от плоскости грунтов по табл.16.
Так как АF = 11,1 м2 СF = 6*10-7 Н/м2.
Рабочие условия:
Е = 1,91*1011 Н/м2
Т0 = 1,65.
Гидроиспытаник
Е = 1,99*1011 Н/м2.
Т0 = 2,7.
Величины постоянные для всех состояний.
Аппарат
Таблица 14
Показатели | Участки | ||||||
1 | 2 | 3 | 4 | 5 | 6 | 7 | |
xi | 48 | 40 | 32 | 24 | 16 | 8 | 2 |
K | 0,7 | ||||||
![]() | 0,923 | 0,769 | 0,615 | 0,462 | 0,307 | 0,154 | 0,034 |
g0 | 450 | ||||||
Qi | 1,64 | 1,55 | 1,44 | 1,34 | 1,17 | 1 | 1 |
![]() ![]() | 0,9 | 0,65 | 0,44 | 0,27 | 0,12 | 0,04 | 0,015 |
mi | 0,47 | 0,485 | 0,5 | 0,53 | 0,56 | 0,6 | 0,6 |
Таблица 15 Площадки
Показатели | Участки | |||||||
1 | 2 | 3 | 4 | 5 | 6 | 7 | 8 | |
xj | 49,4 | 43,2 | 37 | 30,8 | 24,6 | 18,4 | 12,2 | 6 |
ξ | 2,3 | |||||||
![]() | 0,95 | 0,83 | 0,71 | 0,59 | 0,47 | 0,35 | 0,23 | 0,12 |
g0 | 450 | |||||||
Qj | 1,65 | 1,59 | 1,5 | 1,42 | 1,35 | 1,22 | 1,1 | 1 |
χj | 1,44 | 1,18 | 0,9 | 0,68 | 0,48 | 0,3 | 0,15 | 0,04 |
mj | 0,47 | 0,48 | 0,49 | 0,5 | 0,53 | 0,56 | 0,58 | 0,6 |
Определение изгибающего момента от ветровой нагрузки. Изгибающий момент в расчетном сечении следует определять по формуле:
(2.100)
где, Pi – ветровая нагрузка на i-м участке;
(2.101)
Pist – статическая составляющая ветровой нагрузки на i-ом участке;
(2.102)
Pidyn – динамическая составляющая ветровой нагрузки на i-ом участке;
(2.103)
Рабочее состояние
а) Статическая составляющая
Нормативное значение статической составляющей:
(2.104)
Значение g0, Qi, K из таблицы 14.
(2.105)
б) Динамическая составляющая
При ε = 0,083, ν = 0,73 (таблица 16), ξ = 2,3.
Gi – масса i-го участка.
G5 = 9000H.
Приведенное относительное ускорение центра тяжести i-го участка:
(2.106)
где, di – относительное перемещение i-го участка;
mK – из таблицы 14.
(2.107)
γ = 2/3 = 0,66.
Расчет приведенного относительного ускорения центра тяжести сводим в таблицу 16.
Таблица 16
Показатели | Участки | ||||||
1 | 2 | 3 | 4 | 5 | 6 | 7 | |
αi | 179,8*10-11 | 143,8*10-11 | 110,2*10-11 | 79*10-11 | 49*10-11 | 23,3*10-11 | 6,1*10-11 |
mi | 0,47 | 0,485 | 0,5 | 0,53 | 0,56 | 0,6 | 0,5 |
Pist | 12398 | 11718 | 10886 | 10130 | 8845 | 7560 | 3578 |
di*mi*Pist | 10,5*10-6 | 8,2*10-6 | 6*10-6 | 4,2*10-6 | 2,4*10-6 | 1,1*10-6 | 0,13*10-6 |
GK | 28181,5 | 9000 | |||||
αi2*GK | 9,11*10-14 | 5,8*10-14 | 3,4*10-14 | 1,8*10-14 | 0,68*10-14 | 0,15*10-14 | 0,0104*10-14 |
![]() | 30*10-14 | ||||||
![]() | 32,53*10-6 | ||||||
![]() | 108*106 | ||||||
ni | 28,2*10-3 | 22,6*10-3 | 17,3*10-3 | 12,4*10-3 | 7,7*10-3 | 3,7*10-3 | 0,96*10-3 |
При x0 = 0
При x0 = 4
в) Момент от ветровой нагрузки на обслуживающие площадки.
(2.108)
где, - сумма проекций профилей площадок.
≈ 3,9 м2.
При x0 = 0
При x0 = 4
Изгибающий момент в сечении
y-y
z-z
Гидроиспытание
а) Статическая составляющая. Так как принятые расчетные величины Di = 3 м и hi остаются те же, что и в рабочем состоянии.
б) Динамическая составляющая
При ε = 0,138, ν = 0,75 (таблица 16), ξ = 2,8.
Gi – масса i-го участка.
Приведенное относительное ускорение по формуле (2.106). Относительное перемещение i-го участка по формуле (2.107).
γ = 0,66, Е = 1,99*1011 H/м2.
Расчет приведенного относительного ускорения центра тяжести сводим в таблицу 17.
Таблица 17
Показатели | Участки | |||||||
1 | 2 | 3 | 4 | 5 | 6 | 7 | ||
αi | 177,6*10-11 | 142,2*10-11 | 109,1*10-11 | 78,3*10-11 | 48*10-11 | 23,2*10-11 | 6,09*10-11 | |
mi | 0,47 | 0,485 | 0,5 | 0,53 | 0,56 | 0,6 | 0,6 | |
Pist | 12398 | 11718 | 10886 | 10130 | 8845 | 7560 | 3578 | |
αi*mi*Pist | 10,3*10-6 | 8,1*10-6 | 5,9*10-6 | 4,2*10-6 | 2,4*10-6 | 1,1*10-6 | 0,13*10-6 | |
GK | 307226 | 9000 | ||||||
![]() | 96,9*10-14 | 62,1*10-14 | 36,6*10-14 | 18,8*10-14 | 7,3*10-14 | 1,7*10-14 | 0,11*10-14 | |
![]() | 223,5*10-14 | |||||||
![]() | 32,13*10-6 | |||||||
![]() | 14,4*10-6 | |||||||
ni | 11,2*10-3 | 9*10-3 | 6,9*10-3 | 4,9*10-3 | 3,1*10-3 | 1,5*10-3 | 0,38*10-3 | |
При x0 = 0
При x0 = 4
в) Момент от ветровой нагрузки на обслуживающие площадки
Момент определяем по формуле (2.108).
При x0 = 0
При x0 = 4
Изгибающий момент в сечении
y-y
z-z
Расчет эксцентричного момента
G = 5000H.
где, Ркр – масса крана укосины (100 кг);
Q – масса грузоподъемного крана укосины (400 кг).
Расчетные изгибающие моменты
Сечение z-z
Сечение y-y
Выбор опоры
Qmax – максимальная приведенная нагрузка принимается равной, большей из двух значений.
или
Значит,
Ближайшее табличное значение: Qmax = 1500*103 кг*с.
Выбираем опору:
Опора ОСТ 26 – 467 -78.
Проверка аппарата на прочность
Расчет напряжений проводят для рабочих условий и условий гидроиспытания.
Рабочее условие
Сечение z-z
F = F1 = G1 = 12172,6 кг.
М = М1 = 3008527 кгс*см.
Р = 0 так как расчетное давление = 1 кгс/см2 наружное.
а) Продольное напряжение:
на наветренной стороне
(2.109)
на подветренной стороне
(2.110)
б) Кольцевые напряжения
(2.111)
в) Эквивалентные напряжения
на наветренной стороне
(2.112)
так как
на подветренной стороне
(2.113)
так как
Условие прочности на наветренной стороне
где, = 1600 кгс/см – допускаемое напряжение для материала аппарата (09Г2С) при t = 100ºС.
на подветренной стороне:
Условие прочности выполняется.
Гидроиспытание
Сечение z-z
F = F2 = G2 = 31622,6 кг.
М = М2 = 2248368 кгс*см.
Р = 6б9 кгс/см2 – давление гидроиспытания с учетом гидростатического давления.
а) Продольные напряжения
на наветренной стороне по формуле (2.109):
на подветренной стороне по формуле (2.110):
б) Кольцевые напряжения по формуле (2.111):
в) Эквивалентные напряжения
на наветренной стороне по формуле (2.112):
на подветренной стороне по формуле (2.113):
Условие прочности:
на наветренной стороне
на наветренной стороне
Условие прочности выполняется.
Проверка аппарата на устойчивость
Проверку устойчивости проводим для рабочих условий.
Условие устойчивости:
(2.114)
где, Р = 1 кгс/см2 – расчетное наружное давление;
= 2,25 кгс/см2 – допускаемое наружное давление;
F = G1 = 12172,6 кг – осевое сжимающее усилие;
- допускаемое осевое сжимающее усилие;
М = 3008527 кгс*см – изгибающий момент, действующий на колонну;
- допускаемый изгибающий момент.
Так как
то - допускаемое осевое сжимающее усилие из условия общей устойчивости в пределах упругости.
(2.115)
где, ny = 2,4 – коэффициент запаса устойчивости для рабочих условий.
Допускаемый изгибающий момент рассчитываем по формуле:
(2.116)
где, - допускаемый изгибающий момент из условия прочности;
- допускаемый изгибающий момент из условия устойчивости в пределах упругости;
(2.117)
Условие устойчивости:
0,603 < 1.
Условие устойчивости выполняется.
Расчет опорной обечайки
Проверка прочности сварного шва, соединяющего корпус колонны с опорной обечайкой
Рабочее состояние
Fz = 12172,6 кгс.
Мz = 3008527 кгс*см.
а = S3 = 2,0 см.
= 1830 кгс/см2 – допускаемое напряжение для опорной обечайки (для стали 09Г2С при t = 20ºС);
= 1600 кгс/см2 – допускаемое напряжение для корпуса колонны (для стали 09Г2С при t = 100ºС);
= 0,9 – коэффициент прочности сварного шва.
211 кгс/см2 < 1440 кгс/см2.
Условие прочности сварного шва выполняется.
Гидроиспытания
Fz = 31622,6 кгс.
Мz = 2248368 кгс*см.
а1 = S3 = 2,0 см.
194 кгс/см2 < 229 кгс/см2.
Условие прочности сварного шва выполняется.
Проверка устойчивости опорной обечайки в месте выреза
Проверку ведем в сечении на конической части опоры вместе максимального отверстия d1 = 60 см.
(2.118)
D3 = 80 см; S3 = 1,5 см; S6 = 1,5 см; b3 = 1 см; di = 30 см.
Рабочее состояние:
Fy = 12172,6 кгс;
Мy = 3452993 кгс*см;
= 6918689 кгс;
= 19156200 кгс*см.
ψ1 = 0,97 при и
ψ2 = 0,87, ψ3 = 0,02.
0,33 < 1,0.
Условие устойчивости выполняется.
Гидроиспытание
Fy = 31622,6 кгс;
= 6918689 кгс;
Мy = 2559314 кгс*см;
= 19156200 кгс*см.
0,162 < 1,0.
Условие устойчивости выполняется.
Расчет диаметра патрубков
Расчет диаметра патрубков для подвода и отвода рассчитывается по уравнению:
(2.119)
Для расчета диаметров патрубков рекомендуется скорость потока в патрубке ω выбирать из таблицы [3, стр. 45].
1. Подача исходной смеси
Рассчитываем плотность смеси по исходному веществу:
Плотность метанола (НК) при tF = 76,9ºС равна 7391,1 кг/м3, а формальдегида (ВК) принимаем 0,248 кг/м3.
ω = 2 м/с.
2. Выход пара дистиллята
Плотность пара дистиллята вычисляется:
где, Т0 = 273 К;
Р = 427,5 мм рт. ст.;
Р0 = 760 мм рт. ст.;
tР = 64,8ºС;
Т = 64,8+273=337,8 К.
ω = 25 м/с.
3. Жидкость под давлением
где, плотность метанола при tP = 64,8ºС равна 751,2 кг/м3, а формальдегида 275 кг/м3.
ω = 2 м/с.
4. Жидкость самотеком (выход кубового остатка)
Рассчитываем плотность смеси кубового остатка:
где, плотность метанола при tw = 98,4ºС равна 715,8 кг/м3, а формальдегида 102 кг/м3.
ω = 0,8 м/с.
5. Жидкость кубового остатка
ω = 1 м/с.
6. Насыщенный водяной пар
Т = 98,4 + 273 = 371,4 К.
Полученные значения внутренних диаметров округляются до ближайшего большего стандартного диаметра труб и подбираются фланцевые соединения.
Основные размеры патрубков стандартных стальных фланцевых штуцеров в таблице 18.
Таблица 18
Dy, мм | DT, мм | До 0,6 МПа | |
ST, мм | HT, мм | ||
100 | 108 | 5 | 155;215 |
300 | 350 | 10 | 170;270 |
50 | 57 | 3 | 155;215 |
100 | 108 | 5 | 155;215 |
250 | 273 | 8 | 160;250 |
300 | 350 | 10 | 170;270 |
Фланцы для аппаратов стальные плоские приварные ОСТ 26 – 426 – 79 в таблице 21.
Таблица 21
D, мм | Py, МПа | Размеры, мм | Число отверстий z | |||||
Dф | DБ | D1 | h | S | d | |||
1000 | 0,3 | 1130 | 1090 | 1052 | 30 | 8 | 23 | 36 |
Дата добавления: 2019-07-15; просмотров: 1101; Мы поможем в написании вашей работы! |
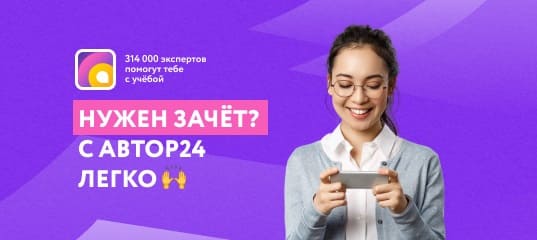
Мы поможем в написании ваших работ!