Технологические расчеты цикличного транспорта
4.1 Общие сведения
Карьерный транспорт предназначен для перевозки горной массы от забоев к пунктам разгрузки и является связующим звеном в общем технологическом процессе.
Из всех этих видов в настоящее время наибольшие объемы горной массы на карьерах перевозятся автомобильным и железнодорожным транспортом.
4.2 Расчет подвижного железнодорожного транспорта
Технологический расчет железнодорожного транспорта заключается в определении полезной массы поезда, числа транспортных средств и их производительности, пропускной и провозной способности пути, а также организации движения поездов.
Весовую норму поезда определяют из условия равномерного движения по руководящему уклону с полным использованием тяговых возможностей локомотива, а также по условию трогания на уклоне по следующим формулам:
где Qв, Qт - масса прицепной части поезда соответственно для условия равномерного движения и трогания, т;
Рсц – сцепная масса локомотива, т;
– ускорение свободного падения, 9,81 м/с2;
y, yтр - коэффициент сцепления приводных колес локомотива с рельсами соответственно при равномерном движении поезда и при трогании с места (y = 0,22-0,24 и yтр = 0,24-0,28 – для электровозов постоянного тока, работающих от сети напряжения 3000 В;
y = 0,25-0,26 и yтр = 0,3-0,35 – для электровозов переменного тока и электровозов постоянного тока, работающих от сети напряжения 1500 В);
|
|
и
- основное удельное сопротивление движению на прямом горизонтальном участке пути соответственно локомотива и вагона (в приближенных расчетах допускается принимать
»
»
= 20-30 Н/кН для постоянных путей, для передвижных – на 20-25% больше), Н/кН;
- дополнительное удельное сопротивление движению от уклона пути (численно равно величине уклона пути, выраженного в промилях, например, при уклоне пути i = 25 о/оо
= 25), Н/кН;
- дополнительное удельное сопротивление движению от кривизны пути (для кривой с радиусом R ³ 300 м на постоянных путях
= 700/R, на передвижных -
= 1300/R;
для кривой с радиусом R < 300 м на постоянных путях =900/(100 + R); на руководящем уклоне, выполняемом, как правило, прямолинейным,
= 0), Н/кН;
- удельное сопротивление при трогании поезда с места для подвижного состава (на подшипниках скольжения
, на подшипниках качения
, здесь
– нагрузка от оси на рельсы, кН), Н/кН;
- удельное сопротивление от приведенного уклона, Н/кН; a=0,025¸0,05 – ускорение при трогании, м/с2.
Таблица 4.1 - Предпочтительные условия применения основных видов колесного транспорта
П о к а з а т е л и | Железнодорожный | Автомобильный | ||
тепловозы | электровозы | тяговые агрегаты | автосамосвалы | |
Тип месторождения | нагорное | глубинное | глубинное | глубинное, нагорное |
Залегание | горизонтальное, наклонное | горизонтальное, наклонное | наклонное, крутое | горизонтальное, наклонное, крутое |
Размер карьера в плане,км | 2-3 и более | 1-2 и более | 1-1,5 и более | 0,3-3 и более |
Глубина карьера, м | до 150 | до 180 | до 300 | до 150 |
Наклон транспортных коммуникаций, 0 о/оо | до 20 | до 40 | до 60 | до 80 |
Производственная мощность карьера, млн т горной массы в год | до 100 | до 150 | до 50 | до 70 |
Срок службы карьера, лет | до 25 | до 40 | до 25 | до 20 |
Дальность транспортирования, км | 5-8 | 7-10 | 3-7 | 0,5-6 |
|
|
Таблица 4.2 - Технологические параметры карьерных электровозов и тепловозов
Показатели | Электровозы | Тепловозы | ||||||
переменного тока | постоянного тока | |||||||
Д-94 | Е-1 | 21-Е | 26-ЕМ | ТЭМ-2 | ТЭМ-3 | ТЭМ-7 | ТГМ6А | |
Сцепной вес, кН | 940 | 1500 | 1500 | 1800 | 1224 | 1270 | 1800 | 900 |
Часовой режим: мощность, кВт сила тяги, кН скорость, км/ч | 1650 200 30,0 | 2020 242 30,5 | 1510 198 28,0 | 2480 317 28,7 | 205 11,0 | 205 20,0 | 350 20,0 | 255 |
Номинальное напряжение, кВ | 10 | 1,5 | 1,5 | 1,5 | ||||
Длина по осям автосцепок, мм | 16400 | 21320 | 20960 | 21470 | 16970 | 16970 | 21500 | 14300 |
Нагрузка от оси на рельсы, кН | 235 | 250 | 250 | 300 | 204 | 210 | 225 | 225 |
Минимальный радиус кривой, м | 75 | 60 | 60 | 60 | 40 | 40 | 40 | 40 |
|
|
Таблица 4.3 - Технологические параметры тяговых агрегатов
Показатели | Тяговые агрегаты постоянного тока | Тяговые агрегаты переменного тока | |||||
ПЭ-2М | ПЭ-3Т | ОПЭ-1 | ОПЭ-1А | ОПЭ-1Б | ОПЭ-2 | ЕL-20 | |
Сцепной вес,кН | 3680 | 3720 | 3600 | 3720 | 3720 | 3720 | 3720 |
Состав тягового агрегата | ЭУ+МД+ +МД(БС) | ЭУ+ДС+ +МД(БС) | ЭУ+ДС+МД(БС) | ЭУ+МД+ +МД(2БС) | |||
Часовой режим: мощность, кВт сила тяги, кН скорость, км/ч | 5460/2570 694 28,9/3,6 | 5410/2160 662 29,5 | 6480 810 26,5 | 5325 662,4 29,8 | 5325 662,4 29,8 | 5325 662,4 29,8 | 5520 690 28,0 |
Наибольшая скорость, км/ч | 65,0 | 65,0 | 65,0 | 65,0 | 65,0 | 65,0 | 50,0 |
Номинальное напряжение сети, кВ | 3,0/1,5 | 3,0/1,5 | 10,0 | 10,0 | 10,0 | 10,0 | 10,0 |
Нагрузка от оси на рельсы, кН | 310 | 310 | 300 | 310 | 310 | 310 | 310 |
Длина по осям автосцепок, мм | 51306 | 51306 | 59900 | 51300 | 51300 | 51300 | 52300 |
Минимальный радиус кривой, м | 80 | 80 | 80 | 80 | 80 | 80 | 80 |
|
|
Примечание. ЭУ - электровоз управления; ДС - дизельная секция; МД - мотор-думпкар;
БС - бустерная секция
Таблица 4.4 - Техническая характеристика вагонов для перевозки карьерных грузов
Показатели | Д у м п к а р ы | Универсальные полувагоны | |||||||
6ВС-60 | ВС-85 | 2ВС-105 | ВС-136 | ВС-145 | 2ВС-180 | ПС-63 | ПС-94 | ПС-125 | |
Грузоподьемность, т | 60,0 | 85,0 | 105,0 | 136,0 | 145,0 | 180,0 | 63,0 | 94,0 | 125,0 |
Вместимость, м3 | 30,0 | 38,0 | 48,5 | 68,0 | 68,0 | 58,0 | 73,0 | 106,0 | 140,0 |
Масса, т | 27,0 | 35,0 | 48,0 | 67,5 | 78,0 | 68,0 | 22,7 | 32,9 | 46,9 |
Коэффициент тары | 0,45 | 0,41 | 0,46 | 0,5 | 0,54 | 0,38 | 0,36 | 0,35 | 0,375 |
Число осей | 4 | 4 | 6 | 8 | 8 | 8 | 4 | 6 | 8 |
Нагрузка на рельсы от оси, кН | 212,7 | 294,0 | 256,0 | 249,0 | 273,17 | 304,0 | 213,0 | 201,0 | 215,0 |
Ширина кузова наружная, мм | 3210 | 3520 | 3750 | 3460 | 3500 | 3460 | 3130 | 3200 | 3130 |
Высота от поверхности рельса, мм | 2860 | 3236 | 3241 | 3620 | 3635 | 3285 | 3482 | 3790 | 3970 |
Длина по осям автосцепок, мм | 11830 | 12170 | 14900 | 17630 | 17630 | 17580 | 13920 | 16400 | 20240 |
При движении по криволинейному уклону удельное сопротивление от приведенного уклона определяют по выражению
,
где - удельное сопротивление от уклона трогания, Н/кН.
Число вагонов (думпкаров) в составе поезда находят по меньшему из значений прицепной массы поезда Qв, Qт по выражению:
,
где – число думпкаров в составе поезда, шт.;
– собственная масса думпкара, т;
- фактическая грузоподъемность думпкара, т.
При полном использовании вместимости думпкара его грузоподъемность определяют по выражению:
,
где – паспортная геометрическая вместимость думпкара, м3;
– коэффициент наполнения думпкара «с шапкой», принимаем 1,12-1,17;
- плотность транспортируемой горной массы в целике, т/м3;
– коэффициент разрыхления породы в кузове думпкара, принимаем 1,25-1,35.
Возможны два случая, когда при
,
,
,
,
,
,
где – паспортная грузоподъемность думпкара, т;
– фактическая вместимость думпкара, м3.
В первом случае загрузку думпкара осуществляют по объему, а во втором - по паспортной грузоподъемности с недоиспользованием вместимости думпкара.
Фактический коэффициент тары думпкара определяют по выражению:
.
Количество вагонов в составе округляют до целого числа в меньшую сторону.
Тогда полезная масса груза в прицепной части поезда будет равна:
, т
где – полезная масса груза, перевозимого поездом, т.
Объем породы, перевозимой одним локомотивосоставом составит:
., м3
Длина локомотивосостава:
, м
где – длина думпкара по осям автосцепок, м;
– длина локомотива, м.
Число рейсов локомотивосостава за час:
где – продолжительность рейса, мин.
, мин
где – соответственно время погрузки и разгрузки локомотивосостава, мин;
– соответственно время движения в грузовом и порожнем направлениях, мин;
– время простоев локомотивосостава в ожидании погрузки, разгрузки и на остановках на раздельных пунктах за один рейс, принимаем 5-10, мин.
, мин
или
, мин
где – вместимость ковша экскаватора, м3;
– продолжительность цикла экскаватора, с;
– коэффициент наполнения ковша экскаватора;
– часовая производительность экскаватора, м3/ч.
, мин
где – продолжительность разгрузки думпкара, принимаем в летнее время 1,5-2 мин, в зимнее 3,-5 мин.
![]() | |
![]() |
где – средневзвешенная длина забойных передвижных путей на год максимального развития горных работ, км;
– средневзвешенная длина отвальных путей, принимают 1,5 – 2,0 км;
– длина стационарных поверхностных путей, равна расстоянию от карьера до отвала, км;
– длина транспортирования по стационарным путям во внешней и внутренних капитальных траншеях, км;
– соответственно средняя скорость движения по передвижным забойным, стационарным путям, в траншее, на поверхности, заезда на отвал, передвижным отвальным путям в грузовом направлении (
=15-20;
=25-30;
= 35-40), км/ч.
Техническая производительность локомотивосостава:
, м3/ч
Эксплуатационная производительность локомотивосостава:
- сменная:
, м3/смену
- суточная:
, м3/сутки
- годовая:
, м3/год
где – продолжительность работы железнодорожного транспорта в смену, ч;
– коэффициент использования локомотивосостава в течение смены, принимаем 0,85-0,95;
- число смен в сутки;
– число рабочих дней локомотивосостава в году.
4.3 Расчет автомобильного транспорта
Технологический расчет автомобильного транспорта состоит в обосновании типа автосамосвалов, определении их производительности и необходимого количества.
Тип автосамосвала рекомендуется выбирать исходя из дальности транспортирования горной массы из забоя к месту ее отвалообразования или складирования и рационального соотношения вместимостей кузова автосамосвала ( , м3) и ковша экскаватора (
, м3), применяемого на погрузке (табл. 4.5).
Таблица 4.5 - Условия применения автосамосвалов
Вместимость ковша экскаватора, м3 | Рациональное соотношение Va / E при расстояниях транспортирования, км | ||
1¸2 | 3¸4 | 5¸6 | |
3¸4 | 5,2 | 6,5 | 8,0 |
5¸6 | 5,0 | 6,0 | 7,5 |
8¸10 | 4,5 | 5,5 | 7,0 |
12,5¸16 | 4,2 | 5,0 | 6,5 |
20¸25 | 4,0 | 4,8 | 6,0 |
Число автосамосвалов, которое может эффективно использоваться в комплексе с одним экскаватором, определяется по формуле
![]() |
где – продолжительность рейса, мин;
– продолжительность погрузки автосамосвала, мин.
![]() |
где – соответственно время движения в грузовом и порожнем направлениях, мин;
– время разгрузки автосамосвала, мин;
– продолжительность маневрирования автосамосвала в забое и пункте разгрузки, мин.
![]() |
где Кр – коэффициент разрыхления породы в ковше, см. табл. 2.1;
Кн – коэффициент наполнения ковша, см. табл. 2.1.
![]() | |
![]() |
где – соответственно средневзвешенная длина временных забойных автодорог, дорог в траншее, магистральных дорог и отвальных автодорог, км;
– коэффициент, учитывающий разгон и торможение автосамосвала, принимаем 1,1;
– скорости движения автосамосвала в грузовом направлении по временным забойным, дорогам в траншее, магистральным дорогам и отвальным автодорогам, км/ч;
– скорости движения автосамосвала в порожнем направлении по отвальным автодорогам, магистральным дорогам, дорогам в траншее и временным забойным дорогам, км/ч.
Продолжительность разгрузки автосамосвала (включает время подъема кузова и время его опускания), продолжительность маневров
при погрузке автосамосвала (зависит в основном от схемы подъезда), продолжительность маневров при разгрузке автосамосвала выбираем из табл. 4.7.
Таблица 4.6 - Скорости движения движения автосамосвала и примерные длины автодорог
Дороги | Скорости движения автосамосвала, км/ч | Примерные длины автодорог, км | |
с грузом | без груза | ||
Магистральные щебеночные | 30¸32 | 36¸42 | 1,3÷1,6 |
Отвальные | 14¸17 | 16¸19 | 0,8÷1,2 |
Забойные | 11¸13 | 14¸15 | 0,3÷0,4 |
В наклонных выработках с уклоном 80 о/оо щебеночные | 12¸14 | 25¸30 | 0,6÷0,8 |
Производительность автотранспорта в значительной мере зависит от схемы подъезда автосамосвала к забою и установки его у экскаватора. В зависимости от размеров рабочей площадки и условий работы экскаватора возможен сквозной подъезд автосамосвала к экскаватору, подъезд с петлевым и тупиковым разворотами (рис. 4.1).
Таблица 4.7 - Продолжительность вспомогательных операций
Грузоподъёмность автосамосвала, т | Время на маневры при погрузке, мин | Время на маневры при разрузке, мин | Время разгрузки, мин tР | Время ожидания, мин tОЖ | |
Схема подъезда автосамосвала | |||||
сквозная и кольцевая tМП | тупиковая tМП | ||||
27 | 0,5 | 0,6 | 0,5 | 0,9 | 0,4 |
40 | 0,5 | 0,6 | 0,5 | 0,9 | 0,4 |
75 | 0,6 | 1,0 | 0,6 | 1,0 | 0,4 |
110 | 0,8 | 1,2 | 1,0 | 1,5 | 0,6 |
180 | 0,9 | 1,4 | 1,2 | 1,5 | 0,6 |
Сквозной подъезд применяется при наличии двух выездов с рабочего горизонта. Это самая простая и эффективная схема подъезда автосамосвалов к экскаватору.
Подъезд с петлевым разворотом используют при встречном движении автотранспорта и достаточной для разворота ширине рабочей площадки. Обычно время обмена самосвалов по этой схеме не превышает рабочего цикла экскаватора.
Рис. 4.1 - Схемы подъезда автосамосвалов к экскаватору: а – сквозная; б – с петлевым разворотом; в – с тупиковым разворотом
Подъезд с тупиковым разворотом используют в стесненных условиях при встречном движении автотранспорта, когда невозможно осуществить петлевой разворот. Чаще всего эту схему подъезда автосамосвала к забою применяют в тупиковых забоях при проведении траншей. При этом производительность автосамосвала, по сравнению с вышеприведенными схемами, на 10 ¸15 % ниже.
Рис. 4.2 – Схемы установки автомашин для погрузки в забое
Число рейсов автосамосвала в час
![]() |
Производительность автосамосвала:
- техническая
![]() |
- эксплуатационная
сменная ![]() | |
суточная ![]() | |
годовая ![]() |
где – коэффициент использования грузоподъёмности, принимаем 1,1-1,2;
– коэффициент разрыхления породы в кузове автосамосвала;
– плотность перевозной породы в целике, т/м3;
– продолжительность смены, ч;
– число смен в сутках;
– число рабочих дней в году;
- коэффициент использования автосамосвала в течение смены, принимаем0,7
0,8.
Число рабочих автосамосвалов для обеспечения эффективной работы сэкскаваторами определяется по формуле
![]() |
где – годовой грузооборот карьера, м3/год;
- коэффициент неравномерности работы транспорта, принимаем 1,1-1,5.
Инвентарный парк автосамосвалов с учетом находящихся в ремонте и техническом обслуживании
![]() |
где – коэффициент технической готовности парка автосамосвалов, принимаем 0,7¸0,8.
4.4 Параметры рабочей площадки
При определении параметров рабочей площадки следует исходить из того, что ширина рабочей площадки была минимальной. Чем меньше ширина рабочей площадки, тем меньше текущий коэффициент вскрыши, а значит и меньше себестоимость добычи единицы полезного ископаемого.
Ширина рабочей площадки (рис. 4.3):
- по наносам (рис. 4.3 а)
![]() |
- по взорванным породам (рис. 4.3 б)
![]() |
где – берма безопасности, м;
– ширина площадки для размещения дополнительного оборудования, принимаем 5
6 , м;
– ширина транспортной полосы, принимаем для автотранспорта в зависимости от ширины самосвала или грузоподъёмности автосамосвала, принимаем из таблицы 4.8 , для железнодорожного транспорта 5, м;
– расстояние от нижней бровки развала (уступа) до транспортной полосы, принимаем 0,5
1,0, м;
– ширина развала, м.
Берма безопасности:
,м
Рис. 4.3 - Схема к определению ширины рабочей площадки
Таблица 4.8 – Рекомендации по выбору ширины проезжей части автодорог
Грузоподъёмность автомобиля, т | 27-30 | 40-42 | 75-80 | 110-120 | 170-180 |
Ширина проезжей части карьерных автодорог, м |
| ||||
При одностороннем движении | 5,5-6 | 6,0-6,5 | 7,0-7,5 | 8,0-8,5 | 10-11 |
При двустороннем движении | 12-14 | 13-15 | 16-19 | 19-21 | 23-27 |
5 ОТВАЛООБРАЗОВАНИЕ ПРИ АВТОМОБИЛЬНОМ ТРАНСПОРТЕ
5.1 Общие сведения
Искусственная насыпь, образуемая в результате складирования пустых пород, называется отвалом, а совокупность производственных операций по приему и размещению вскрышных пород на отвале – отвальными работами.
По месту расположения отвалов относительно конечных контуров карьера различают внутренние (в контурах отвала) и внешние (вне контуров карьера) отвалы, по конструкции – одно- и многоярусные.
5.2. Параметры отвала при автомобильном транспорте
При транспортировании вскрышной породы на отвал автомобильным транспортом применяется бульдозерное отвалообразование, которое включает разгрузку автосамосвала на верхней площадке отвала, перемещение породы под откос отвала, ремонт и сооружение автодорог.
Существует два способа бульдозерного отвалообразования – площадной и периферийный (рис. 5.1).
При площадном способе автосамосвалы разгружаются по всей площадке отвала, затем площадь отвала планируется и укатывается катками или бульдозерами и автосамосвалами. Аналогичным образом отсыпаются последующие вышележащие слои.
Бульдозерный отвал в этом случае развивается в высоту. Из-за большого объема планировочных работ этот способ является более дорогостоящим, чем периферийный, поэтому он применяется редко, в основном при укладке мягких малоустойчивых пород (см. рис. 5.1, б).
При периферийном способе (рис. 5.1, а) автосамосвалы грузоподъемностью до 75 т разгружаются прямо под откос отвала, а большей грузоподъемности – на расстоянии 3¸5 м от верхней бровки откоса отвала. Затем эта порода бульдозером перемещается под откос, т.е. в этом случае отвал развивается в плане. Для исключения возможности падения автосамосвала с отвала при непосредственной разгрузке под откос у верхней бровки отвала устанавливают деревянные или металлические упоры для задних колес автосамосвала или отсыпают предохранительный вал высотой не менее 0,5 диаметра колеса автомобиля максимальной грузоподъемности, применяемого в условиях данного карьера.
Кроме этого, с этой же целью поверхность бульдозерного отвала по всему фронту разгрузки должна иметь уклон не менее 3о, направленный от бровки откоса в глубину отвала на длину базы работающих автосамосвалов (см. рис. 5.1, а).
Параметры отвала определяют в следующем порядке.
Площадь отвала:
![]() |
где – объем пород, подлежащих размещению в отвале за срок его существования, м3;
- высота отвала, принимаем на равнинной поверхности – до 30¸60 м; в гористой местности – до 100 м и более;
– коэффициент остаточного разрыхления породы в отвале, принимаем 1,06¸1,15;
– коэффициент, учитывающий использование площади отвала, принимаем при одном ярусе 0,8
0,9; при двух ярусах 0,6
0,7.
При известной площади, принятой форме и заданной одной из сторон отвала определяются размеры карьера в плане.
Среднее число автосамосвалов, разгружающихся на отвале в течение одного часа
![]() |
где – производительность карьера по вскрыше, м3/ч;
– коэффициент неравномерности работы карьера по вскрыше, принимаем 1,25¸1,5;
– техническая производительность автосамосвала.
Число автосамосвалов, одновременно разгружающихся на отвале:
![]() |
где – число автосамосвалов, разгружающихся на отвале в течение часа;
– продолжительность разгрузки и маневрирования автосамосвала, принимаем 1,5
2 мин.
Длина фронта разгрузки на отвале:
![]() |
где – ширина полосы по фронту отвала, занимаемая одним автосамосвалом при маневрировании, принимаем18
20 м.
![]() | Рис. 5.1 - Способы бульдозерного отвалообразования: а – периферийный; б – площадной; 1 – планировочный участок; 2 – резервный участок; 3 – разгрузочный участок |
Годовая производительность бульдозера:
![]() |
где – коэффициент использования бульдозера в течение смены, принимаем 0,8
0,9;
– продолжительность смены, ч;
– число смен в сутках;
– число рабочих дней бульдозера в году;
– часовая производительность бульдозера.
где – глубина слоя планировки, принимаем 0,2-0,4 м;
n – число проходов по одному месту, принимаем 2-3;
t – время, затраченное на проход по одной полосе, принимаем 35-50 сек;
F – площадь, планируемая бульдозером на 1 проход, мᵌ.
, мᵌ
где L – длина полосы, планируемой за 1 проход, принимаем 20-60 м;
В – длина отвала бульдозера, принимаем из тех. характеристики бульдозера;
– ширина перекрытия планируемых полос, принимаем 0,3-0,5 м.
Число рабочих бульдозеров на отвале (рабочий парк):
![]() |
где –часовой объем бульдозерных работ на отвале, м3/ч.
![]() |
где – коэффициент заваленности отвала породой, принимаем 0,5-0,7.
Общее количество бульдозеров (инвентарный парк) на отвале:
![]() |
где – коэффициент резерва, принимаем 1,3-1,4.
6 ОТВАЛООБРАЗОВАНИЯ ПРИ ЖЕЛЕЗНОДОРОЖНОМ ТРАНСПОРТЕ
Длина отвального тупика определяется по формуле:
, м
где - количество смен работы отвального тупика между двумя передвижками, см;
- ёмкость одного состава, м³;
- время смены, мин;
- коэффициент, учитывающий время на планировку отвального тупика, принимаем 0,6-0,8;
- коэффициент разрыхления породы;
- высота яруса отвала, м;
- шаг передвижки рельсового пути, м;
- время разгрузки состава, мин;
- время на обмен состава, мин.
6.1 Экскаваторные отвалы при железнодорожном транспорте
На экскаваторных отвалах в качестве механизмов для размещения породы в отвал после выгрузки ее из состава применяют механические лопаты и драглайны.
Технология отвалообразования с применением мехлопат имеет следующие особенности. Отвальный уступ высотой от 10— 15 до 20—40 м разделен на два подустуиа (рис. 6.1).
Экскаватор располагается на кровле нижнего нодуступа на 4—7 м ниже кровли верхнего подуступа, на которой находится железнодорожный путь.
Порода разгружается из думпкаров в приемную яму отвального экскаватора, имеющую длину 20—25 м, глубину (ниже горизонта установки экскаватора) 0,8—1 м и вместимость 200- 300 м³. Экскаватор переваливает эту породу в трех направлениях: вперед по ходу экскаватора, в сторону под откос отвала и назад, создавая при этом отвальную заходку, высота которой должна быть выше уровня железнодорожного пути па 0,5— 1 м. Это превышение рассчитано на усадку породы, вследствие которой высота отвала сохраняется одинаковой во всех заходках.
Ширина отвальной заходки, равная шагу переукладки железнодорожных путей, должна удовлетворять следующим условиям:
, м
, м
где - радиусы соответственно черпания и разгрузки экскаватора;
- длина фронта разгрузки (бункера), равная длине 1,5—2 думпкаров.
Рис. 6.1 - Схема отвалообразования с применением механической лопаты
Рис. 6.2 - Схемы отвалообразования с применением драглайна с нижней (а) и комбинированной (б) отсыпкой
Процесс отвалообразования драглайнами аналогичен процессу отвалообразования мехлопатами. Думпкары состава поочередно (по два-три вагона) разгружаются в приемный бункер, который периодически, по мере развития отвальной заходки, сооружается драглайном. Глубина приямка 4—8 м, а длина равна длине двух-трех думпкаров.
Наибольшее применение в практике горных работ получили однотупиковые схемы с нижней (рис. 6.2, а) и комбинированной (рис. 6.2, б) отсыпкой.
6.2 Бульдозерное отвалообразование при железнодорожном транспорте
При бульдозерном отвалообразовании (рис. 6.3) укладка породы в отвал осуществляется мощными бульдозерами. После возведения пионерной насыпи железнодорожные пути укладываются на расстоянии 4—5 м от бровки отвала. Ниже уровня путей на 1,5—2 м за счет подрезки бульдозером отвального откоса (до угла 60—80°) создается рабочая площадка, на которую из думпкаров выгружается порода, перемещаемая дальше к откосу отвала бульдозером. Минимальная ширина этой площадки должна быть достаточной для разворота бульдозера. Она зависит от схемы работы бульдозера и составляет 7—8 м. Длина приемной площадки должна быть равна примерно двум длинам состава. Площадка устраивается с небольшим (5—6°) уклоном в сторону отвального откоса.
Рис 6.3 - Схемы бульдозерного отвалообразования по железнодорожном транспорте
а – торцевая, б – фронтальная, в - смешенная
Применяют торцовую, фронтальную и смешанную схемы работы бульдозера на площадке. Наименование схемы определяется в зависимости от формы траектории перемещения породы из зоны разгрузки в отвал.
Торцовая схема целесообразна лишь при наращивании длины тупика, фронтальная — при малой ширине отвальной заходкн. Наиболее рациональна смешанная схема, при которой перемещение породы бульдозерами осуществляется в два приема. Вначале порода из навала перемещается в промежуточный штабель на расстоянии 6—8 м от приемного откоса, а затем при поперечных проходах бульдозера укладывается в отвал. При этой схеме производительность бульдозера на 30—35 % больше, чем при торцовой схеме.
Производительность бульдозеров зависит от дальности перемещения породы, ее кусковатости, схемы движения бульдозера при работе на площадке и, следовательно, от ширины рабочей площадки.
Годовая производительность бульдозера:
![]() |
где – коэффициент использования бульдозера в течение смены, принимаем 0,8
0,9;
– продолжительность смены, ч;
– число смен в сутках;
– число рабочих дней бульдозера в году;
– часовая производительность бульдозера.
где – глубина слоя планировки, принимаем 0,2-0,4 м;
n – число проходов по одному месту, принимаем 2-3;
t – время, затраченное на проход по одной полосе, принимаем 35-50 сек;
F – площадь, планируемая бульдозером на 1 проход, мᵌ.
, мᵌ
где L – длина полосы, планируемой за 1 проход, принимаем 20-60 м;
В – длина отвала бульдозера, принимаем из тех. характеристики бульдозера;
– ширина перекрытия планируемых полос, принимаем 0,3-0,5 м.
Число рабочих бульдозеров на отвале (рабочий парк):
![]() |
где –часовой объем бульдозерных работ на отвале, м3/ч.
![]() |
где – коэффициент заваленности отвала породой, принимаем 0,5-0,7.
Общее количество бульдозеров (инвентарный парк) на отвале:
![]() |
где – коэффициент резерва, принимаем 1,3-1,4.
Дата добавления: 2019-02-22; просмотров: 1028; Мы поможем в написании вашей работы! |
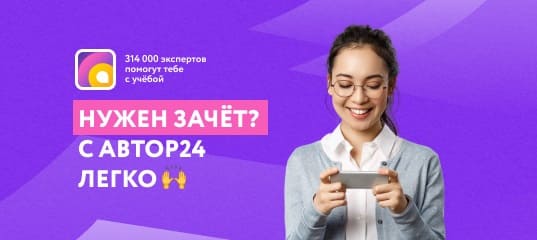
Мы поможем в написании ваших работ!