Зона крупных разноосных кристаллов,4– усадочная раковина,5– усадочная рыхлость
В последние годы, появились не только вертикальные установки для разливки стали, но и установки с изгибом слитка. Наиболее популярна сейчас установка радиальной непрерывной разливки, схема которой показана на (рис. 3), которая может быть размещена в габаритах существующих сталеплавильных цехов.
Слитки непрерывной разливки по сравнению со слитками, полученными в изложницах, имеют более чистую поверхность; кроме того, из-за большой скорости охлаждения они характеризуются мелкой структурой и менее развитой химической неоднородностью, минимальной по продольной оси слитка. Однако и эти слитки имеют свои дефекты; наиболее часты продольные и поперечные наружные трещины, появляющиеся при нарушении скорости вытягивания слитка, которая может измениться от 0,4 до 10 м/мин.
Непрерывная разливка на разливочной машине обеспечивает не только качественный слиток и резко уменьшает потери металла в отходы, но значительно облегчает условия работы и резко повышает производительность труда как при разливке стали, так и при дальнейшей обработке слитков. Одноручьевая установка непрерывной разливки позволяет получить от 20 до 150 т/ч слитков (в зависимости от их сечения и формы).
Вторым фактором, обеспечивающим повышение качества стали, в последнее время стало ее вакуумирование перед разливкой и вакуумная разливка в слитки. Вакуумирование стали, перед разливкой проводят в ковше, помещая его в вакуумную камеру. Отливка слитков в вакууме применяется главным образом для высококачественных и некоторых высоколегированных марок стали. Она требует довольно сложной организации и оборудования.
|
|
Рис. 3. Схемы установки для непрерывной разливки стали
а– вертикальная разливка;б– радиальная разливка;
2. Пластическая деформация металлов. Упругая и пластическая деформации. Полиморфизм металлов.
Деформацией называют процесс изменения формы и размеров тела под действием приложенных к нему нагрузок. Различают деформацию упругую (обратимую) и пластическую (остаточную). Упругой называют такую, при которой после снятия нагрузок тело восстанавливает свою первоначальную форму. Эта деформация (далее "деформация" - "Д") сопровождается изменением расстояний между атомами в кристаллической решетке в пределах ее параметра. Пластической деформацией называют такую, при которой после снятия внешней нагрузки тело не восстанавливает первоначальную геометрическую форму и размеры. "Д" сопровождается смещением одной части кристалла по отношению к другой на расстоянии, значительно превышающем расстояние между атомами в кристаллической решетке. Пластической "Д" всегда предшествует упругая "Д". Таким образом, общая пластическая деформация в момент действия нагрузки всегда состоит из упругой и пластической "Д". Упругая "Д" после снятия нагрузки исчезает. "Д" имеет важное практическое значение поскольку процессы обработки металлов давлением основаны на деформации заготовок. "Д" сопровождается не только изменением формы и размеров тела. Одновременно с этим в металле появляется внутреннее напряжение и происходит изменение его механических и физико-химических свойств. Величина и характер деформации зависят от пластических свойств металла. Пластичность металлов примерно может быть оценена относительным удлинением и относительным сужением при испытании образцов на растяжение. К характеристикам пластичности металлов относится также ударная вязкость, показывающая работу разрушения при изгибании надрезанного образца, отнесенную к его площади сечения в месте надреза.
|
|
Полиморфизм это такое явление, когда материал в одном интервале температур или давлений имеет одну кристаллическую структуру, а в других интервалах – другую. Иными словами с изменением температуры или давления наблюдается изменение кристаллической структуры материала. Температуру и давление, при которых происходит смена кристаллической структуры материала, называют соответственно температурой и давлением полиморфного или аллотропического превращения.
|
|
Различные кристаллографические модификации одного материала принято обозначать буквами греческого алфавита α, β, g, δ, ε, σ и т.д. Модификацию, наблюдаемую при самых низких температурах, обозначают буквой α, при более высоких температурах – β, и т.д.
Ярким примером полиморфизма у неметаллических материалов является наличие двух кристаллографических модификаций чистого углерода, известных как алмаз и графит. Оба материала являются идентичными по химическому составу и отличаются лишь кристаллической структурой. В результате свойства алмаза и графита оказываются существенно различными. Графит это мягкий, хрупкий и непрозрачный материал, в то время как алмаз является одним из наиболее твёрдых минералов, встречающихся в природе, и, как правило, прозрачен.
Наиболее ярко полиморфизм проявляется у железа, которое при нагреве два раза меняет свою кристаллическую структуру.
При температурах ниже 768°С железо является ферромагнитным материалом, а при температурах выше 768°С – парамагнитным. Ранее считали, что изменение магнитных свойств железа связано с изменением его кристаллической структуры и поэтому ферромагнитное железо стали обозначать α-Fe, а парамагнитное – β-Fe. Позже выяснилось, что это не так. И то и другое железо имеют одинаковую ОЦК-структуру. Однако исторически сложившееся подразделение железа на α-Fe и β-Fe сохранили. В настоящее время железо с ОЦК-структурой, наблюдаемое в интервале температур до 911 ° С, называют α-железом.
|
|
В интервале температур от 911 до 1392 °С железо имеет ГЦК-структуру. Такое железо обозначают γ-Fe. ГЦК-структура отличается от ОЦК-структуры более высокой плотностью упаковки атомов. Поэтому при нагреве железа до температур выше 911°С наблюдается уменьшение размера (объёма) образца.
В интервале температур от 1392 до 1539°С железо вновь имеет ОЦК-структуру. Однако период кристаллической решётки этого железа чуть больше чем у α-железа. Такое железо обозначают δ-Fe.
При температурах выше 1539°С чистое железо плавиться и превращается в жидкий расплав.
Другим ярким примером полиморфизма металлов является полиморфизм олова. При температурах ниже -30°С белое и пластичное β-олово (β –Sn) превращается в свою α-модификацию, т.е. в α-Sn, которое является серым порошком. Не имея никакого представления о природе данного явления, его, в своё время, назвали «оловянной чумой».
Явление полиморфизма в очередной раз подчёркивает, что свойства материалов определяются не только их химическим составом, но и в значительной степени их структурой.
3.Испытание материалов на твёрдость. Определение микротвёрдости образцов.
Методы определения твердости в зависимости от скорости приложения нагрузки делятся на статические и динамические, а по способу ее приложения – на методы вдавливания и царапания. Методы определения твердости по Бринеллю, Роквеллу, Виккерсу относятся к статическим методам испытания.
Твердость - это способность материала сопротивляться вдавливанию в него более твердого тела (индентора) под действием внешних сил.
При испытании на твердость в поверхность материалов вдавливают пирамиду, конус или шарик (индентор), в связи с чем различают методы испытаний, соответственно, по Виккерсу, Роквеллу и Бринеллю. Кроме того, существуют менее распространенные методы испытания твердости: метод упругого отскока (по Шору), метод сравнительной твердости (Польди) и некоторые другие.
При испытании материалов на твердость не изготавливают стандартных специальных образцов, однако к размерам и поверхности образцов и изделий предъявляются определенные требования.
Твердость по Виккерсу (ГОСТ 2999-75) устанавливают путем вдавливания в металл индентора - алмазной пирамиды с углом при вершине 136° под действием постоянной нагрузки Р: 1; 2; 2,5; 3; 5; 10; 20; 30; 50 или 100 кгс и выдержки под нагрузкой в течение 10-15 с. Для определения твердости черных металлов и сплавов используют нагрузки от 5 до 100 кгс, медных сплавов - от 2,5 до 50 кгс, алюминиевых сплавов - от 1 до 100 кгс. После снятия нагрузки с помощью микроскопа прибора находят длину диагонали отпечатка, а твердость HV рассчитывают по формуле:
HV = 1,854*P/d2
где Р - нагрузка, кгс; d- диагональ отпечатка, мм.
Имеется таблица зависимости твердости от величины нагрузки и длины диагонали. Поэтому на практике вычислений не производят, а пользуются готовой расчетной таблицей. Твердость по Виккерсу HV измеряется в кгс/мм2, Н/мм2 или МПа. Значение твердости по Виккерсу может изменяться от HV2060 до HV5 при нагрузке 1 кгс.
По методу Бриннелля вдавливают в образец или изделие стальной закаленный шарик диаметром 10, 5 или 2,5 мм под действием нагрузок 3000, 1000, 750, 500, 250, 62,5 кгс и др. Полученный круглый отпечаток на образце измеряют под лупой и по таблицам находят величину твердости по Бринеллю, значение которой не превышает 450 НВ. Твердость по Бринеллю почти совпадает со значениями твердости по Виккерсу.
Метод измерения микротвердости регламентируется ГОСТ 9450-76. Испытание на микротвердость проводят вдавливанием в испытываемый образец четырехгранной алмазной пирамиды с углом при вершине 136º, таким же, как у пирамиды при испытании по Виккерсу. Отличительной особенностью испытания на микротвердость является применение малых нагрузок – от 0,05 до 5 Н, поэтому основной областью использования данного метода является определение твердости таких образцов и деталей, которые не могут быть испытаны обычно применяемыми методами (по Бринеллю, Роквеллу, Виккерсу). Микротвердость обычно определяют на малых деталях, тонких полуфабрикатах (ленты, фольга, проволока), в слоях, получающихся в результате химико-термической обработки, гальванических покрытий, отдельных структурных составляющих сплавов.
Определение микротвердости. При измерении микротвердости нагрузка составляет 5–500 гс (0,049–4,905 H), измерение диагонали отпечатка производят на микрошлифах металлографическим микроскопом. Запись значения микротвердости при использовании идентора в виде четырехгранной пирамиды с квадратным основанием при нагрузке 50 гс (0,49 Н) и диагонали отпечатка 10 мкм производится в виде Н50 = 927 (Н0,49 = 9094) в кгс/мм2 и (Н/мм2 ), соответственно. Твердость Н определяют по той же формуле, что и твердость по Виккерсу 2 0,189 d P H , если нагрузка Р выражена в (Н).
4.Поверхносная закалка стали
Для получения большой твёрдости в поверхностном слое детали с сохранением вязкой сердцевины, что обеспечивает износостойкость и одновременно высокую динамическую прочность детали, применяют поверхностную закалку.
Известно несколько способов быстрого нагрева поверхностного слоя (токами высокой частоты, лазером, электронно-лучевой, газо-плазменный и др.). Наибольшее применение нашёл индукционный нагрев ТВЧ.
Поверхностная закалка заключается в быстром нагреве поверхностного слоя обрабатываемой детали с последующим быстрым охлаждением. Быстрый нагрев создаёт резкий градиент температур: поверхность имеет температуру выше Ас3, а сердцевина – гораздо ниже.
После быстрого охлаждения поверхностные слои получают полную закалку, а сердцевина либо неполную, либо совсем не закаливается.
ТВЧ закалка легко поддаётся автоматизации, позволяет осуществлять нагрев со скоростями, в сотни и тысячи раз превышающими скорости нагрева в печах; поверхность не успевает окислиться и обезуглеродиться.
После поверхностной закалки и низкого отпуска поверхность изделий имеет твёрдость НRС 54…58 при высокой вязкости. Применяется для обработки коленчатых валов, шестерён, валков холодной прокатки и др.
5.Жаростойкость и жаропрочность. Жаропрочные и жаростойкие стали и сплавы. Состав, маркировка, применение
Жаропрочность – это способность металла сопротивляться пластической деформации и разрушению при высоких температурах.
Жаропрочные материалы используются для изготовления деталей, работающих при высоких температурах, когда имеет место явление ползучести.
Критериями оценки жаропрочности являются кратковременная и длительная прочности, ползучесть.
Кратковременная прочность определяется с помощью испытаний на растяжение разрывных образцов. Образцы помещают в печь и испытывают при заданной температуре. Обозначают кратковременную прочность =, например
300oС= 300МПа.
Прочность зависит от продолжительности испытаний.
Пределом длительной прочности называется максимальное напряжение , которое вызывает разрушение образца при заданной температуре за определенное время.
Например, = 200 МПа, верхний индекс означает температуру испытаний, а нижний – заданную продолжительность испытания в часах. Для котельных установок требуется невысокое значение прочности, но в течение нескольких лет.
Ползучесть – свойство металла медленно пластически деформироваться под действием постоянной нагрузки при постоянной температуре.
При испытаниях образцы помещают в печь с заданной температурой и прикладывают постоянную нагрузку. Измеряют деформацию индикаторами.
При обычной температуре и напряжениях выше предела упругости ползучесть не наблюдается, а при температуре выше 0,6Тпл, когда протекают процессы разупрочнения, и при напряжениях выше предела упругости
наблюдается ползучесть.
В зависимости от температуры скорость деформации при постоянной нагрузке выражается кривой состоящей из трех участков (рис. 4).
Рис. 4. Кривая ползучести
1. ОА – упругая деформация образца в момент приложения нагрузки;
2. АВ – участок, соответствующий начальной скорости ползучести;
3. ВС – участок установившейся скорости ползучести, когда удлинение имеет постоянную скорость.
Если напряжения достаточно велики, то протекает третья стадия (участок СД), связанная с началом разрушения образца (образование шейки).
Для углеродистых сталей ползучесть наблюдается при нагреве выше 400oС.
Предел ползучести – напряжение, которое за определенное время при заданной температуре вызывает заданное суммарное удлинение или заданную скорость деформации .
Например,
МПа, где верхний индекс – температура испытания вoС, первый нижний индекс – заданное суммарное удлинение в процентах, второй – заданная продолжительность испытания в часах.
Жаростойкость (окалиностойкость) – это способность металлов и сплавов сопротивляться газовой коррозии при высоких температурах в течение длительного времени.
Если изделие работает в окислительной газовой среде при температуре 500..550oC без больших нагрузок, то достаточно, чтобы они были только жаростойкими (например, детали нагревательных печей).
Сплавы на основе железа при температурах выше 570oC интенсивно окисляются, так как образующаяся в этих условиях на поверхности металла оксид железа (вюстит) с простой решеткой, имеющей дефицит атомов кислорода (твердый раствор вычитания), не препятствует диффузии кислорода и металла. Происходит интенсивное образование хрупкой окалины.
Рис 5.Влияние хрома на жаростойкость хромистой стали
Для повышения жаростойкости в состав стали вводят элементы, которые образуют с кислородом оксиды с плотным строением кристаллической решетки (хром, кремний, алюминий).
Степень легированости стали, для предотвращения окисления, зависит от температуры. Влияние хрома на жаростойкость хромистой стали показано на рис 5.
Чем выше содержание хрома, тем более окалиностойки стали (например, сталь 15Х25Т является окалиностойкой до температуры 1100…1150oC).
Высокой жаростойкостью обладают сильхромы, сплавы на основе никеля – нихромы, стали 08Х17Т, 36Х18Н25С2, 15Х6СЮ.
Структуры таких жаростойких сталей подразделяются на:
-перлитные;
-мартенситно-ферритные;
-мартенситные;
-аустенитные.
Существует и подразделение жаропрочных сплавов на аустенитно-ферритные (мартенситные) и ферритные.
Производится такие марки мартенситных сплавов:
-4Х9С2 и 3Х13Н7С2 (такая марка стали используется в основном в клапанах автодвигателей, где температура поднимается до 850–950°С);
-Х6СМ, Х5М, 1Х8ВФ, 1Х12H2ВМФ, Х5ВФ (такой сплав подойдёт для производства деталей и узлов, которые должны работать 1000–10000 часов в границах температур 500 - 600°С);
-Х5 (такая марка используется для производства труб, которые будут работать при температуре ограниченной 650°С);
-1Х8ВФ (такой вид сплавов используют при изготовлении деталей паровых турбин, которые могут работать 10000 часов без потерь при температуре, которая не будет превышать 500°С).
При добавлении хрома в перлитные сплавы получаются мартенситные марки сплавов. К перлитным материалам можно отнести жаропрочные сплавы с маркировкой: Х7СМ, Х10С2М, Х9С2, Х6С. Производится их закалка при 950–1100°С, а затем при 8100°С производят отпуск стали, что позволяет создавать твёрдые конструкции со структурой сорбита.
Ферритные сплавы обладают мелкозернистой структурой, которую они получают после термообработки и обжига. В таких композициях, как правило, присутствует хром в процентном соотношении от двадцати пяти до тридцати трёх. Такие жаропрочные стали применяют производства теплообменников и пиролизного оборудования.
К ферритным сплавам относят такие маркировки материалов: 1Х12СЮ, Х28, Х17, Х18СЮ, 0Х17Т, Х25Т. Но их нельзя нагревать больше чем сто восемьдесят градусов иначе материал станет хрупким из-за своей крупнозернистой структуры.
Мартенситно-ферритные материалы отлично подходят для производства машиностроительных деталей, работа которых будет производиться при температуре в шестьсот градусов, причём длительное время.
6.Укажите назначение, определите температуры нагрева, время прогрева,скорость охлаждения и охлаждающие среды для:
-отжига;
-нормализации;
-закалки;
-отпуска стали.
Из углеродистой стали 50 толщина детали 60мм.
Таблица 1.
Вид термообработки | Назначение термообработки | Температура нагрева °С | Время нагрева, мин | Охлаждение | |
среда | скорость | ||||
Отжиг | Улучшаются механические свойства и выравнивается химический состав стали; улучшается обрабатываемость ее на станках; уменьшаются остаточные деформации; осуществляется подготовка структуры стали для последующей термической обработки, изменяются свойства наклепанного металла. | 750-770 | 90-120 | печь | медленное охлаждение со скорость 20-100С/ч |
Нормализация | Устраняются внутренние напряжения и наклеп, повышают механические свойства и подготовляют структуру стали для окончательной термической обработки | 830-850 | 90-120 | на воздухе | спокойный воздух |
Закалка на сорбит | Повышается твердость и износостойкость | 780-800 | 90-120 | масло, вода | быстрое охлаждение |
Продолжение Таблица 1 | |||||
Закалка на тростит | Повышается твердость и износостойкость | 780-800 | 90-120 | масло, вода | быстрое охлаждение |
Низкий отпуск | Смягчается действие закаливания, уменьшается или снимается остаточные напряжения, повышается вязкость, уменьшается хрупкость стали. | 200-300 | 90 | воздух, масло | медленное охлаждение |
Средний отпуск | Смягчается действие закаливания, уменьшается или снимается остаточные напряжения, повышается вязкость, уменьшается хрупкость стали. | 300-500 | 80 | воздух, масло | медленное охлаждение |
Высокий отпуск | Смягчается действие закаливания, уменьшается или снимается остаточные напряжения, повышается вязкость, уменьшается хрупкость стали. | 500-700 | 70 | воздух, масло | медленное охлаждение |
7. Расшифруйте марки и укажите назначение конструкционных материалов. А20, ВСт5, 08кп, АС45, У12А, 30М3ХФ, ШХ4, Р9М5К6, 9Х2Г, Х6В3Ф
А20-Сталь конструкционная повышенной обрабатываемости. Используют для изготовления мелких деталей машин и приборов, малонагруженных деталей сложной конфигурации, к которым предъявляются требования высокой точности размеров и качества поверхности, после цементации и цианирования — малонагруженных деталей, к которым предъявляются требования износостойкости и повышенного качества поверхности. Не применяется для сварных конструкций.
Химический состав (%): С(углерод) – 0,17-0,25; Si(кремний) – 0,15-0,35; Mn(марганец) – 0,7-1; S(сера) – 0,08-0,15; P(фосфор) – до 0,06; Cu(медь) – до 0,25;
ВСт5- Сталь конструкционная углеродистая обыкновенного качества. Используют для детали клепаных конструкций, болты, гайки, ручки, тяги, втулки, ходовые валики, клинья, цапфы, рычаги, упоры, штыри, пальцы, стержни, звездочки, трубчатые решетки, фланцы и др. детали, работающие в интервале температур от 0 до +425 °С; поковки сечением до 800 мм.
Химический состав (%): С(углерод) – 0,28-0,37; Si(кремний) – 0,05-0,17; Mn(марганец) – 0,50-0,80; Ni(никель)-до 0,5; S(сера) – до 0,05; P(фосфор) – до 0,04; Cr(хром) до 0,30;
08кп- Сталь конструкционная углеродистая качественная. Используют для прокладок, шайб, вилок, труб, а также деталей, подвергаемых химико-термической обработке — втулок, проушин, тяг.
Химический состав (%): С(углерод) – 0,05-0,12; Si(кремний) – до 0,03; Mn(марганец) – 0,25-0,5; Ni(никель)-до 0,3; S(сера) – до 0,04; P(фосфор) – до 0,035; Cr(хром) – до 0,1 ; Cu(медь)– до 0,3;
АС45-Сталь конструкционная углеродистая качественная. Используют для изготовления вала-шестерни, коленчатые и распределительные валы, шестерни, шпиндели, бандажи, цилиндры, кулачки и другие нормализованные, улучшаемые и подвергаемые поверхностной термообработке детали, от которых требуется повышенная прочность.
Химический состав (%): С(углерод) – 0,42-0,5; Si(кремний) – 0,17-0,37; Mn(марганец) – 0, 5-08; Ni(никель)-до 0,25; S(сера) – до 0,04; P(фосфор) – до 0,035; Cr(хром) – до 0,25 ; Cu(медь)– до 0,25; As(мышьяк) – до 0,08 Fe(железо) – 97.
У12А-Сталь инструментальная углеродистая. Преимущественно из неё изготавливают режущие инструменты, предназначенные для эксплуатирования в условиях низкой рабочей скорости, когда не происходит нагревание режущей кромки. К примеру, ручные метчики, надфили, машинные метчики, мелкоразмерные развёртки, плашки для крупов и прочее. Кроме того сталь У12 отлично подходит для изготовления измерительных инструментов несложной конфигурации, например, гладки калибры и скобы.
Химический состав (%): С(углерод) – 1,1-1,29; Si(кремний) – 0,17-0,37; Mn(марганец) – 0,17-0,28; Ni(никель)-до 0,25; S(сера) – до 0,018; P(фосфор) – до 0,025; Cr(хром) – до 0,2 ; Cu(медь)– до 0,25.
30М3ХФ- сталь инструментальная легированная. Применяется для штемпелей при холодной работе; ножей при холодной резке металла, обрезных матриц и пуассонов при холодной обрезке заусенцев; кернеров
Химический состав (%): С(углерод) – 0,7-0,8; Si(кремний) – 0,1-0,4; Mn(марганец) – 0,15-0,45; S(сера) – до 0,03; P(фосфор) – до 0,03; Cr(хром) – 0,4-0,7; V(ванадий) – 0,15-0,3.
ШХ4- конструкционная подшипниковая сталь. Используется для изготовления деталей с высокой контактной прочностью/ твердостью/ износостойкостью – кольца ж/д подшипников.
Химический состав (%):(%): С(углерод) – 0,95 – 1,05; Si(кремний) – 0,15 – 0,3; Mn(марганец) – 0,15-0,3; Ni (никель) – до 0,3; S(сера) – до 0,02; P(фосфор) – до 0,0027; Cr(хром) –0,35-0,5; Ti (титан) – до 0,01; Cu (медь) – до 0,25;
Р9М5К6- Сталь инструментальная быстрорежущая. Используется для обработки высокопрочных нержавеющих и жаропрочных сталей и сплавов в условиях повышенного разогрева режущей кромки: зуборезный инструмент, фрезы, фасонные резцы, зенкеры, метчики.
Химический состав (%): С(углерод) – 1-1,1; Si(кремний) – до 0,5; Mn(марганец) – до 0,5; S(сера) – до 0,03; P(фосфор) – до 0,03; Cr(хром) – 3-3,6 V(ванадий) – 02,3-2,7. Fe(железо) – 70;
9Х2Г- Сталь инструментальная легированная. Используется в рабочие и опорные валки для холодной прокатки металлов. Рабочие валки рельсобалочных, крупносортных и проволочных обжимных и сортовых станов для горячей прокатки металлов, подвергающиеся интенсивному износу и работающие в условиях минимальных или умеренных ударных нагрузок. Опорные составные валки листовых станов для горячей прокатки металла. Клейма, пробойники, холодновысадочные штампы, деревообрабатывающий инструмент и другие детали.
Химический состав (%): С(углерод) – 0,8-0,95; Si(кремний) – 0,25-0,45; Mn(марганец) – 0,15-0,4; Ni(никель)-до 0,35; S(сера) – до 0,03; P(фосфор) – до 0,03; Cr(хром) – 0,4-1,7 ; Cu(медь)– до 0,3;Fe(железо) – 95
Х6В3Ф-Сталь инструментальная штамповая. Резьбокатаный инструмент (ролики и плашки), ручные ножовочные полотна, бритвы, матрицы, пуансоны, зубонакатники и другие инструменты, предназначенные для холодной деформации, для дереворежущего фрезерного инструмента.
Химический состав (%): С(углерод) – 1,05-1,15; Si(кремний) – 015-0,35; Mn(марганец) – 0,15-0,4; Ni(никель)-до 0,35; S(сера) – до 0,03; P(фосфор) – до 0,03; Cr(хром) – 5,5-6,5 ; Cu(медь)– до 0,3;Fe(железо) – 89
8. Подберите марку сплава (материала) для:
-болта жаропрочного до 650ºС;
-крупного молотового штампа;
-заднего моста автомобиля;
-распределительного вала автомобиля;
-заливки подшипников скольжения коленвала двигателя автомобиля.
Болт жаропрочный до 650ºС.
20Х13 - энергетическое машиностроение и печестроение; турбинные лопатки, болты, гайки, арматура крекинг-установок с длительным сроком службы при температурах до 650 град; сталь мартенситного класса.
Крупный молотовый штамп.
5ХНМ- молотовые штампы паровоздушных и пневматических молотов с массой падающих частей свыше 3 т, прессовые штампы и штампы машинной скоростной штамповки при горячем деформировании легких цветных сплавов, блоки матриц для вставок горизонтально-ковочных машин.
Задний мост автомобиля
15ХГН2ТА- зубчатые венцы, шатуны, зубчатые колеса и т.д
Распределительный вал автомобиля.
18ХГТ- Улучшаемые или цементуемые детали ответственного назначения, от которых требуется повышенная прочность и вязкость сердцевины, а также высокая поверхностная твердость, работающие под действием ударных нагрузок.
Заливка подшипников скольжения коленвала двигателя автомобиля
Б83- Используется для изготовления баббитов в чушках, применяемых для заливки подшипников и других деталей; температура заливки 440-460°C; температура начала расплавления 240°C. Подшипники, работающие при больших скоростях и средних нагрузках; характеристика нагрузки - спокойная ударная.
.
ХГН2ТА
СПИСОК ЛИТЕРАТУРЫ
1. Материаловедение: учебное пособие / С. Богодухов, А. Проскурин, Е. Шеин, Е. Приймак ; Министерство образования и науки Российской Федерации, Федеральное государственное бюджетное образовательное учреждение высшего профессионального образования «Оренбургский государственный университет». - Оренбург : ОГУ, 2013. - 198 с.
2. Материаловедение: учебное пособие / Ю.П. Земсков, Ю.С. Ткаченко, Л.Б. Лихачева, Б.М. Квашнин. - Воронеж : Воронежский государственный университет инженерных технологий, 2013. - 199 с.
3. Материаловедение и технологии конструкционных материалов : учебное пособие / О.А. Масанский, В.С. Казаков, А.М. Токмин и др. ; Министерство образования и науки Российской Федерации, Сибирский Федеральный университет. - Красноярск: Сибирский федеральный университет, 2015. - 268 с.
4. Основы материаловедения: учебное пособие / Е.А. Астафьева, Ф.М. Носков, В.И. Аникина и др. ; Министерство образования и науки Российской Федерации, Сибирский Федеральный университет. - Красноярск : Сибирский федеральный университет, 2013. - 152 с.
5. Слесарчук, В.А. Материаловедение и технология материалов : учебное пособие / В.А. Слесарчук. - 2-е изд., стер. - Минск : РИПО, 2015. - 392 с.
Дата добавления: 2019-03-09; просмотров: 261; Мы поможем в написании вашей работы! |
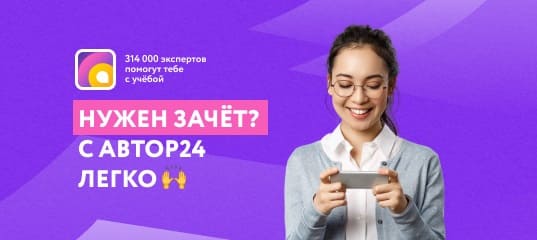
Мы поможем в написании ваших работ!