Часть 2. Технология конструкционных материалов
Тема 16. Производство чугуна, стали и цветных металлов
Понятие о структуре металлургического производства.
Сущность пиро-, гидро- и электрометаллургии. Доменное и внедоменное получение железа из руд. Руды и их подготовка к плавке. Технология сталеплавильного производства. Особенности мартеновской, кислородно-конвертерной и электродуговой плавки. Технология разливки и формирования слитков. Способы повышения качества сталей в процессе их производства.
Виды внепечной обработки стали. Сущность электрошлакового, вакуумно-дугового, лучевого переплавов и их комбинаций при получении сталей особо вязкого качества. Гранульная технология и ее особенности. Особенности металлургических процессов при выплавке меди и никеля. Сущность электролиза при выплавке алюминия и магния. Способы их рафинирования. Сущность металлотермии при производстве титана. Экологические проблемы металлургии.
Методические указания
Вначале необходимо рассмотреть структуру металлургического производства в целом, а затем изучить его основные процессы, ознакомиться с исходными материалами для производства чугуна, изучить виды руд, процентное содержание в них железа, марганца и других элементов, а также способы подготовки руд к плавке.
Нужно ознакомиться с флюсами, их видами, химическим составом и назначением, основными видами топлива, применяемого в металлургии. Особое внимание следует уделить изучению физико-химических процессов, протекающих в доменной печи, получению основных и побочных продуктов доменного производства, процессам прямого восстановления железа из руд, а также технико-экономическим показателям производства чугуна.
|
|
Изучая производство стали, прежде всего, необходимо ознакомиться с принципом работы современных конвертеров, мартеновских и электрических дуговых печей, подробно рассмотреть физико-химические процессы, протекающие в них при выплавке стали.
Следует изучить новейшие достижения в области производства стали: выплавку в вакуумных электрических печах, путем электрошлакового, плазменного переплава, рафинирование стали в ковше жидкими синтетическими шлаками и другие новые технологические способы.
Особое внимание нужно уделить кислородно-конвертерному способу получения стали, который в настоящее время является основным способом массового производства стали.
Затем следует рассмотреть существующие способы разливки стали, устройство сталеразливочного ковша и различные схемы разливки стали, принципиальные схемы установок непрерывной разливки стали (УНРС), а также способы вакуумной дегазации стали.
|
|
Кроме того, необходимо ознакомиться с устройством сталеплавильных агрегатов непрерывного действия (САНД) и технико-экономическими показателями выплавки стали различными способами.
Самым распространенным металлом в природе является алюминий. В настоящее время по размерам производства он занимает первое место среди всех цветных металлов.
Изучая производство алюминия, следует ознакомиться с алюминиевыми рудами: бокситами, нефелинами, алунитами, их составом.
Необходимо рассмотреть два основных процесса производства алюминия: получение глинозема из бокситов и неметаллического алюминия путем электролиза расплавленного глинозема, получаемого щелочными, электротермическими и другими способами.
Затем необходимо изучить схему и принцип работы электролизера, состав и назначение криолита, реакцию диссоциации молекул криолита и глинозема, а также реакции, происходящие при рафинировании хлором электролитическом рафинировании.
Магний, занимающий среди металлов шестое место по распространению, входит в состав очень многих минералов. В качестве сырья для получения магния используют карналлит, магнезит и доломит.
Необходимо изучить состав этих руд и способы их обогащения, подробно ознакомиться с электролитическими и термическими способами получения магния и его последующего рафинирования.
|
|
Медь - один из важнейших металлов. Сплавы на основе меди - латуни и бронзы - используются почти во всех областях машиностроения. Медь получают из медных руд двумя способами - пирометаллургическим и гидрометаллургическим, причем около 90 % первичной меди получают пирометаллургическим способом.
Следует разобраться в общей схеме пирометаллургического способа получения меди, изучить оборудование для обогащения медных руд. обжига рудных концентратов, плавки штейна и получения черновой меди, а также уяснить физико-химические процессы, протекающие при этом.
Особое внимание нужно обратить на новый прогрессивный способ обжига рудных концентратов в кипящем слое. В заключение следует разобраться в сущности огневого и электролитического рафинирования меди и ознакомиться с происходящими реакциями.
Никель является одним из важнейших легирующих элементов в сталях. Сырьем для его производства служат окисленные никелевые или сульфидные медно-никелевые руды.
Необходимо ознакомиться с технологией производства никеля из окисленных руд, усвоить электрическое рафинирование никеля, карбонильный способ извлечения никеля из медно-никелевых файнштейнов.
|
|
Титан по распространению в природе занимает четвертое место среди металлов и входит в состав более 70 минералов. К основным промышленным титановым минералам относятся рутил и ильменит.
Необходимо ознакомиться с устройством электропечи для получения четыреххлористого титана, технологическими процессами обогащения титановых руд, восстановления титана магнием из четыреххлористого титана, методами рафинирования титановой губки и получения титановых слитков.
Следует выяснить сущность различных способов получения титана, их отличия, преимущества и недостатки.
Особое внимание следует уделить изучению вопросов экологии, так как при производстве цветных металлов выделяется большое количество газов, паров и пыли, оказывающих вредное влияние на окружающую среду.
Литература: [4], с. 20-52, 25-58; [1], с. 16-80; [8], с. 13-18.
Вопросы для самоконтроля
1. Назовите руды, применяемые для производства чугуна, их химический состав. Какие вы знаете способы обогащения железных руд?
2. Какие виды топлива применяют при производстве чугуна? Укажите их теплотворную способность.
3. Назовите способы производства стали.
4. Изложите технологию выплавки стали скрап-рудным процессом основной мартеновской печи.
5. Объясните принцип работы индукционной печи для выплавки стали.
6. Объясните строение стальных слитков кипящей и полуспокойной стали. Перечислите дефекты стальных слитков.
7. Начертите схему электролизера для получения алюминия.
8. Охарактеризуйте сущность электролитического рафинирования.
Какая чистота алюминия достигается при этом?
9. Какие руды используют в качестве сырья для получения магния?
10. Назовите основные медные руды и способы их обогащения.
П.В чем сущность пирометаллургического способа получения меди?
11. Приведите схему ячейки электролизной ванны для получения никеля. Охарактеризуйте ее конструктивные особенности.
12. Нарисуйте схему электропечи для получения четыреххлористого титана. Объясните процесс его получения.
Тема 17. Основы технологии литейного производства. Классификация методов формообразования заготовок. Производство литых заготовок
Физические основы литейного производства. Литейные свойства сплавов. Основные этапы формообразования: заполнение форм расплавом, затвердевание, охлаждение. Влияние теплового, химического и механического взаимодействие металла и литейной формы на возникновение дефектов в отливках: недоливов, усадочных раковин, трещин, пор, искажений формы отливок. Внутренние напряжения в отливках. Одновременная и направленная кристаллизация. Принципы управления структурой и качеством отливок.
Классификация способов литья по материалу литейных форм, кратности применения, способам заполнения. Особенности процессов изготовления отливок в разовых формах (песчаных, оболочковых, по выплавляемым моделям). Материалы литейных форм. Способы обеспечения качества отливок.
Особенности процессов изготовления отливок в многократно используемых формах: кокилях, центробежным литьем, литьем под давлением. Принципиальные схемы процессов.
Алгоритм выбора способа изготовления отливок с учетом материала, массы, габаритных размеров, степени сложности, серийного производства и технологической возможности получения отливок требуемого качества.
Правила разработки чертежа отливок (с учетом требований государственных стандартов) и литейной формы в сборе. Прогнозирование механических свойств отливок по теплофизическим параметрам формообразования. Комбинированные методы (непрерывное литье и прокатка, литье и прессование и др.), обеспечивающие повышение производительности и качества заготовок. Основные виды термической обработки отливок.
Принципиальные особенности технологии получения качественных отливок из серого, высокопрочного, ковкого и антикоррозийного чугуна, низколегированных и высоколегированных сталей. Свойства отливок, области применения. Особенности литья медных, алюминиевых и магниевых сплавов. Способы контроля качества.
Методические указания
При изучении данной темы необходимо ознакомиться с основными методами получения заготовок литьем. Литейное производство имеет исключительно важное значение. Нет ни одной отрасли машиностроения и приборостроения, где бы ни применяли литые детали, так как этот способ изготовления изделий наиболее простой и дешевый.
Возможность использования сплава для получения отливок определяется его литейными свойствами, поэтому курсанты должны иметь четкое представление о жидкотекучести, усадке, склонности к ликвации и поглощению газов.
Необходимо изучить особенности заполнения форм расплавом, его затвердевание и охлаждение при производстве отливок из стали, чугуна и цветных сплавов. Следует внимательно рассмотреть характер и причины возникновения различных дефектов в отливках, а также способы их устранения.
Необходимо подробно изучить технологическую оснастку, применяемую для изготовления отливок, модельные комплекты для машинной формовки, виды песчано-глинистых и специальных формовочных и стержневых смесей, их механические, технологические и теплофизические свойства.
Затем следует перейти к изучению технологического процесса получения отливок, обратить внимание на особенность их конструкции и технологичность, ознакомиться с литниковой системой, назначением прибылей, изучить способы ручной и машинной формовки и схемы прессования, рассмотреть способы извлечения моделей из форм, ознакомиться с технологическим процессом машинной формовки, основным способом изготовления стержней.
Необходимо обратить внимание на недостатки ручной формовки стержней, изучить машинную формовку стержней в опорах на прессовых, встряхивающих и других машинах, устройство пескометов, пескодувной и пескоструйной машин. Следует знать основные технологические операции сборки и заливки форм, продолжительность охлаждения в форме затвердевшей отливки и температуру, при которой можно извлекать ее из формы, технологию извлечения и очистки отливок. Кроме того, серьезное внимание нужно уделить изучению дефектов отливок, подразделяемых на исправимые и на неисправимые, знать их виды.
При изучении специальных способов литья необходимо знать, что эти способы позволяют получить отливки повышенной точности, с низкой шероховатостью поверхности, минимальными допусками на механическую обработку, а иногда и без механической обработки.
Каждый специальный способ литья имеет свои особенности, определяющие области применения и экономическую эффективность. Надо знать преимущества и недостатки специальных способов литья для формообразования отливок в многократно используемых формах, технологические возможности этих способов.
Необходимо ознакомиться с технологией выплавки чугуна в вагранке и электрических печах, изучить особенности литейных форм, способы заливки чугуна в формы.
Кроме того, следует изучить области применения отливок различных металлов и сплавов, дефекты отливок и причины их возникновения, методы их дефектоскопии и исправления дефектов, а также требования, предъявляемые Российским морским регистром судоходства к отливкам из стали, чугуна, медных и алюминиевых сплавов.
В заключение следует уделить серьезное внимание комплексу мероприятий по улучшению санитарно-гигиенических условий труда и оздоровлению окружающей среды.
Литература: [4], с. 120-220; [1], с. 329-402; [5], с. 413-419; [6], с. 298-386; [8], с. 284-315.
Вопросы для самоконтроля
1. Охарактеризуйте схему технологического процесса изготовления отливок в песчаных формах.
2. Перечислите основные механические, технологические, теплофизические свойства формовочных смесей.
3. Опишите технологию изготовления формовочных смесей.
4. Назовите элементы литниковой системы, типы литниковых систем.
5. Опишите технологию машинной формовки в двух опоках.
6. В чем сущность литья по выплавляемым моделям?
7. Приведите классификацию дефектов отливок и назовите причины их возникновения.
8. В чем сущность литья в металлических формах?
9. Укажите особенности и области применения литья в металлических формах.
10. В чем сущность центробежного литья?
11. Чем характеризуется литье под давлением?
12. Приведите классификацию способов изготовления отливок и области их применения.
13. Перечислите основные литейные свойства сплавов.
14. Назовите основные дефекты отливок и причины их возникновения.
15. Укажите причины возникновения внутренних напряжений в отливках.
16. Перечислите основные виды термической обработки отливок.
17. Укажите режимы термической обработки отливок из белого чугуна для получения ферритной структуры ковкого чугуна.
18. Какие проводятся мероприятия в литейных цехах по оздоровлению окружающей среды?
Тема 18. Основы технологии обработки металлов давлением
Сущность процесса пластического деформирования. Физико-механические основы формообразования заготовок. Зависимость силовых и деформационных параметров процесса от состава сплава, температуры, скорости деформации, сил трения. Понятие о горячей и холодной деформации. Явление одновременного протекания процессов упрочнения и разупрочнения (наклепа и рекристаллизации). Влияние температуры нагрева и скорости деформации. Основные схемы пластического деформирования. Показатели степени деформации. Классификация способов пластического деформирования.
Сущность процессов прокатки, прессования, волочения. Инструмент и оборудование. Основные группы профилей, понятие о сортаменте согласно государственным стандартам. Особенности получения сортового проката, бесшовных и сварных труб, периодических профилей.
Сущность процессов ковки и объемной штамповки. Структура поковок и штамповок. Степень уковки. Учет анизотропии свойств для повышения качества заготовок.
Ковка. Оборудование, инструмент. Объемная штамповка. Оборудование, инструмент. Разновидность объемной штамповки: в открытых, закрытых штампах, с двумя плоскостями разъема, штамповка выдавливанием и прессовкой. Области применения. Холодная объемная штамповка. Инструмент и оборудование. Листовая штамповка.
Сущность процесса, основные способы. Характеристика продукции, условия обеспечения качества.
Особенности штамповки заготовок различной формы. Принципы разработки чертежа поковки, штамповки (с учетом требований государственных стандартов).
Термическая обработка заготовок, полученных пластическим деформированием. Контроль качества изделий. Техника безопасности при пластическом деформировании металлов.
Методические указания
Производство заготовок пластическим деформированием отличается значительной экономичностью, высоким выходом годного металла и большой производительностью.
Сначала необходимо изучить сущность пластического деформирования, основанного на пластичности материалов, физикомеханические основы формообразования заготовок, включающие в себя неравномерность распределения напряжений и деформации в объеме деформируемого тела.
Затем следует выяснить физическую природу упругой и пластической деформации, ее влияние на структуру и свойства металлов.
Особое внимание следует обратить на нагрев металла при обработке давлением, так как он влияет на качество и стоимость продукции, на дефекты, возникающие из-за неправильного нагрева металла, на зависимость температуры начала и конца горячего деформирования от температуры
плавления и рекристаллизации, а также на режим охлаждения изделий, получаемых горячей обработкой давлением.
Около 90 % всей выплавляемой стали и большую часть цветных металлов подвергают прокатке, поэтому необходимо внимательно изучить сущность этого процесса, усвоить основные виды прокатки, условия захвата металла валками прокатного стана.
Кроме того, необходимо освоить основные способы производства труб, их сортамент, ознакомиться с устройством трубопрокатных станов.
При изучении прессования металлов необходимо выяснить сущность данного процесса и возможность его применения для обработки давлением легированных сталей с низкой пластичностью, цветных металлов и сплавов.
Следует рассмотреть методы прессования прутков, труб и профилей, уяснить преимущества и недостатки этих методов, ознакомиться с инструментом и оборудованием для прессования, выяснить роль смазки при осуществлении данного процесса.
Изучая технологический процесс волочения, следует выяснить его сущность, перечень операций, из которых он состоит, и последовательность их осуществления. Необходимо подробно ознакомиться с волочильным оборудованием.
Особое внимание надо уделить разработке технологического процесса ковки, составление чертежа поковки, выбору заготовки и оборудования для ковки, последовательности выполнения операций ковки, технологическим требованиям к деталям, получаемым из поковок. Необходимо изучить требования Правил Российского морского регистра судоходства, предъявляемых к стальным поковкам, предназначенным для судостроения и судового машиностроения.
По сравнению с ковкой штамповка имеет ряд преимуществ. Горячей объемной штамповкой можно получать поковки сложной конфигурации без напусков, что при ковке невозможно, изготовлять поковки сложной конфигурации и т. д.
Необходимо изучить сущность прямого, обратного, бокового и комбинированного выдавливания, преимущества холодной объемной штамповки перед горячей штамповкой, изучить оборудование и применяемый инструмент, последовательность выполняемых операций при осуществлении технологического процесса холодной штамповки.
Следует также рассмотреть способ холодной листовой штамповки, основные операции и последовательность их выполнения, изучить преимущества и недостатки листовой штамповки, примеры раскроя материала и изменения его формы при листовой штамповке и применяемый при этом инструмент. Следует также ознакомиться с основными разновидностями высокоскоростной листовой штамповки (штамповка взрывом, электрогидравлическая и электромагнитная), рассмотреть их преимущества и недостатки, целесообразность использования.
Применение того или иного способа изготовления заготовок пластическим деформированием определяется конкретными условиями и требованиями, предъявляемыми к готовым изделиям, и другими факторами, оказывающими влияние при их дальнейшей эксплуатации.
При изучении материала этой темы следует получить четкое представление о сущности каждого из способов, их преимущества и недостатки. Необходимо уделить серьезное внимание изучению вопросов охраны труда и окружающей среды при обработке металлов пластическим деформированием.
Литература: [4], с. 53-77, 59-146; [1], с. 406-502; [5], с. 406-412; [6], с. 390-444; [8], с. 318-354.
Вопросы для самоконтроля
1. Чем характеризуется формоизменение заготовок при холодном деформировании?
2. Охарактеризуйте процессы рекристаллизации и возврата (отдыха).
3. Что понимают под горячей деформацией заготовок?
4. Назовите сортамент проката, что он отражает?
5. Какие изделия изготавливают прессованием из цветных металлов?
6. Охарактеризуйте сущность процесса волочения прутков фасонных профилей, труб и проволоки. Начертите схемы этих процессов.
7. Назовите материалы, применяемые для изготовления волоки.
8. Назовите основное оборудование кузнечного производства.
9. Перечислите преимущества и недостатки штамповки по сравнению со свободной ковкой? Какой материал применяют для изготовления штампов?
10. Какие требования Российский морской регистр судоходства предъявляет к химическому составу стали для поковок?
11. С какой целью производят калибровку поковок?
12. С какой целью осуществляют термическую обработку поковок?
Тема 19. Основы технологии сварочного производства. Термическая сварка
Виды сварки плавлением: дуговая, плазменная, электрошлаковая, электронно-лучевая и лазерная. Основные схемы и сущность процессов, протекающих при сварке, параметры ее режимов. Типы соединений. Особенность формирования сварных соединений. Способы защиты от взаимодействия со средой. Инструмент, оснастка, оборудование. Требования автоматизации. Сварочные материалы.
Термические циклы сварки, изменение свойств и структуры в зоне соединения. Напряжения и деформации при сварке, их зависимость от закрепления, жесткости заготовок, теплового режима сварки и химического состава металла. Способы минимизации напряжений и деформаций конструктивными и техническими приемами. Дефекты сварных соединений. Управление качеством сварных соединений. Технологические возможности методов сварки.
Термическая резка металлов и сплавов. Основные условия резки. Виды резки: газокислородная, дуговая, плазменная и др. Техника безопасности и экологичность способов сварки и резки.
Методические указания
При изучении этой темы курсанты должны ознакомиться с видами сварки плавлением, уяснить сущность каждого из них.
Ручная дуговая сварка плавящимся электродом является самым распространенным способом дуговой сварки. Рассматривая его сущность, необходимо обратить внимание на состав электродов и их покрытия, режимы и схемы дуговой сварки, типы электродов, роль покрытия в формировании сварного шва.
Затем следует рассмотреть источники питания сварочной дуги постоянного и переменного тока, технологический процесс ручной дуговой и машинной сварки. Особое внимание следует уделить изучению статической вольтампернои характеристики дуги, внешней характеристики источника сварочного тока и соотношению характеристик дуги и падающей характеристики источника тока при сварке.
Все большее применение в промышленности находят новые способы сварки: автоматическая дуговая сварка под слоем флюса, дуговая сварка в защитном газе (аргонодуговая, сварка в углекислом газе), плазменная, электрошлаковая, электронно-лучевая, лазерная. Поэтому необходимо подробно ознакомиться с их технологическими процессами, используемым оборудованием, оснасткой и инструментом, уровнем автоматизации данных процессов.
Следует также изучить типы соединений, сварочные материалы и особенности формирования сварных соединений при каждом способе сварки, рассмотреть структурные изменений металла в зоне термического влияния в результате воздействия тепловой энергии при сварке, ознакомиться с методами расчета параметров режима сварки. Кроме того, нужно изучить характер временных и остаточных деформаций и напряжений, возникающих при сварке изделий из-за неравномерного нагрева.
Самым распространенным способом термической резки сплавов является кислородная (газовая) резка. Необходимо внимательно изучить сущность процесса резки и последовательность его осуществления, применяемые материалы и оборудование.
В заключение следует ознакомиться с санитарно-гигиеническими требованиями и обязательными мероприятиями по технике безопасности, которые регламентируются "Системой стандартов безопасности труда" и другими нормативными документами, а также с требованиями Правил Российского морского регистра судоходства к сварке корпусов судов, изделий судового машиностроения и оборудования, сварочным материалам и контролю сварных соединений.
Литература: [4], с. 182-207, 221-240; [1], с. 505-555; [5], с. 472-513; [6], с. 445-472; [8], с. 355-394.
Вопросы для самоконтроля
1. Перечислите способы сварки плавлением.
2. Что понимают под статической вольтамперной характеристикой дуги?
3. Охарактеризуйте процесс ручной дуговой сварки.
4. По каким признакам осуществляется классификация электродов?
5. Какие покрытия применяют для электродов и с какой целью?
6. Охарактеризуйте процесс автоматической дуговой сварки под флюсом.
7. Изложите сущность дуговой сварки в защитном газе.
8. Охарактеризуйте процесс плазменной сварки.
9. Изложите сущность электрошлаковой сварки.
10. Приведите схему установки для электронно-лучевой сварки.
11. Назовите оборудование, используемое при газовой сварке.
12. Перечислите внешние и внутренние дефекты сварных соединений.
13. Каким образом осуществляют контроль качества сварных соединений?
14. Изложите сущность термической резки металлов и сплавов.
15. Назовите источники питания сварочной дуги.
16. Изложите сущность плазменно-дуговой резки.
Тема 20. Термомеханическая и механическая сварка
Методы сварки давлением: контактная, трением, взрывом, диффузионная в вакууме, ультразвуковая, конденсаторная и др. Основные схемы и сущность процессов, протекающих при сварке. Степень автоматизации, параметры ее режимов. Типы соединений. Инструмент, схемы оборудования, термические циклы. Степень изменения структуры и свойства в зоне сварки. Деформации и напряжения. Пайка. Виды пайки. Свойства паяных соединений. Техника безопасности при сварке и пайке.
Методические указания
Сварка давлением относится к термомеханическому и механическому видам сварки, включающим контактную сварку и ее разновидность.
В данной теме студентам следует усвоить физическую сущность явлений, протекающих в металле в термопластическом состоянии и при оплавлении, классификацию способов сварки давлением, получить четкое представление о циклах контактной сварки методами сопротивления и оплавления.
Далее необходимо изучить устройство и принцип работы машин контактной стыковой, точечной и шовной сварки, режимы их работы.
Особое внимание следует уделить изучению точечной и шовной сварки как наиболее распространенных видов контактной сварки.
Кроме того, нужно усвоить сущность специальных видов сварки; аккумулированной энергией, холодной, трением, диффузионной, ультразвуковой, взрывом, знать их преимущества, недостатки и области применения, изучить типы сварных соединений, структурные превращения в процессе нагрева и охлаждения зоны сварки.
Рассматривая технологический процесс пайки, следует выяснить его физическую сущность, изучить разновидности получаемых спаев, способы пайки в зависимости от используемых источников нагрева, применяемое оборудование, приспособления и припои.
Необходимо обратить внимание на подготовку поверхности изделий для пайки, знать состав применяемых флюсов и их назначение, характеристику припоев, их деление на группы.
Нужно уделить серьезное внимание вопросам охраны труда при сварке и пайке.
Литература: [4], с. 211-227, 254-269; [1], с. 505-555; [5], с. 472-513; [6],с. 473-485; [8], с. 369-376.
Вопросы для самоконтроля
1. Охарактеризуйте сущность контактной сварки.
2. Назовите типы сварных соединений, выполняемых стыковой сваркой сопротивлением.
3. Изложите сущность точечной и шовной сварки.
4. Изложите сущность сварки аккумулированной энергией.
5. Охарактеризуйте оборудование для контактной сварки.
6. Изложите сущность холодной сварки.
7. Изложите сущность сварки трением.
8. Какой эффект используется для получения механических колебаний высокой частоты при ультразвуковой сварке?
9. Что представляет собой сварка взрывом?
10. Назовите области применения диффузионной сварки.
11. Какой процесс называют пайкой металлов и сплавов?
12. Охарактеризуйте сущность капиллярной и диффузионной пайки.
13. Чем отличается контактно-реактивная пайка от реактивно-флюсовой пайки?
14. Приведите классификацию способов пайки.
Тема 21. Свариваемость металлов и сплавов. Г новая сварка и резка металлов
Понятие о свариваемости. Признаки ограниченности свариваемости. Склонность к образованию трещин различной породы, порообразование. Причины хрупкости и разупрочнения при сварке. Обеспечение свариваемости материалов металлургическими, конструктивными и технологическими способами. Особенности сварки конструкционных сталей, чугуна, алюминиевых, магниевых, медных, титановых и никелевых сплавов, неметаллическихи композиционных материалов. Особенности и виды термической обработки сварных соединений. Контроль качества сварных соединений.
Методические указания
Свариваемость представляет собой сложную характеристику, зависящуюне только от механических свойств свариваемого металла, но и от технологического процесса сварки, режима сварки и свойства применяемых сварочных материалов.
Поэтому вначале необходимо усвоить понятие свариваемости, изучить зависимость от химического состава, структурного состояния сталей и цветных сплавов, структуры сварного соединения при сварке плавлением.
Особое внимание следует уделить оценке свариваемости низкоуглеродистых и строительных легированных сталей, среднеуглеродистых и высокоуглеродистых сталей, низко- и среднелегированных машиностроительных сталей и высоколегированных сталей. Серьезное внимание следует уделить изучению свариваемости чугуна, алюминия и его сплавов, магниевых сплавов, меди и ее сплавов, а также свариваемости тугоплавких металлов и сплавов.
Нужно выяснить причины возникновения дефектов в зависимости от степени концентрации напряжений, их влияние на прочность сварных соединений. Кроме того, необходимо ознакомиться с методами испытаний на свариваемость и классификацией сталей по свариваемости, описанными в справочной литературе, рассмотреть основные виды контроля качества сварных соединений: внешний осмотр, радиационный контроль, цветная дефектоскопия, проверка непроницаемости и др., изучить основные критерии неразрушающего контроля.
Литература: [4], с. 229-237, 204-207, 248-254, 273-281; [1], с. 548-556, 569-574; [5], с. 412-513; [6], с. 472-473, 494-506, 520-522; [8], с. 377-388.
Вопросы для самоконтроля
1. Дайте определение свариваемости.
2. Укажите особенности сварки низкоуглеродистых нелегированных и строительных низколегированных сталей.
3. Укажите особенности сварки чугуна.
4. Укажите основной недостаток свариваемости сталей ферритного класса.
5. Что затрудняет сварку алюминия и его сплавов?
6. Укажите особенности сварки магниевых сплавов.
7. Когда образуются горячие трещины?
8. Для каких сплавов характерны холодные трещины?
9. Укажите основной недостаток при сварке латуней.
10. Назовите типичные дефекты сварных соединений.
11. Перечислите основные виды неразрушающего контроля сварных соединений
Дата добавления: 2019-02-22; просмотров: 380; Мы поможем в написании вашей работы! |
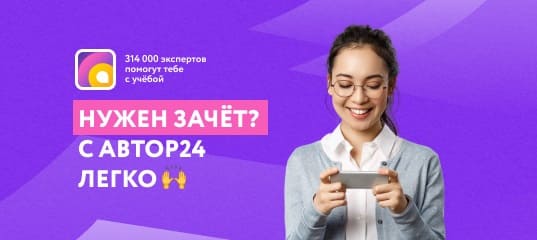
Мы поможем в написании ваших работ!