Расчёт ленточно-колодочного тормоза
В буровых лебедках применяют ленточно–колодочные тормоза, в которых вследствие деформации ленты при довольно большой толщине колодок происходят их неравномерные прилегания к поверхности шкива. В ленточно–колодочном тормозе лента нажимает на тормозной шкив через систему отдельных колодок из фрикционного материала. Такие тормоза рассчитывают, подобно ленточным, по формулам трения гибких тел. Однако сила трения в колодочно–ленточном тормозе изменяется не непрерывно, а скачкообразно, поэтому расчетные формулы при ограниченном числе колодок отличаются от формулы Эйлера.
Расчетная схема ленточно–колодочного тормоза приведена на рисунке 8, удельная нагрузка по длине колодки распределяется неравномерно, как показано на рисунке 9, и тормозной момент, создаваемый отдельной колодкой МН, Н·м
,
где RБ – радиус шкива тормоза, м,
RБ = DТ / 2,
φ – угол охвата одной тормозной колодки, рад;
ρ – угол трения, рад;
n – число колодок
Полный тормозной момент МТ, Н∙м, создаваемый тормозом на одном шкиве, можно выразить так
,
Тангенциальная сила торможения FТ, Н
Рисунок 3 – Расчетная схема тормоза: а – простой ленточный; б – ленточно–колодчный; 1 – колодка; 2 – шкив; 3 – лента; 4 – рычаг; l – длина рычага; α – угол охвата; r – радиус кривошипа; ψ – угол поворота тормозного рычага; φ – угол охвата одной колодки; βС и βН – угол между сбегающей и набегающей концами ленты и тангенциальной линией; γС и γН – угол приложения тангенциальной силы на сбегающей и набегающей колодках; RБ, RО, RН, RC – радиусы наружных поверхностях барабана, колодок и лент набегающей и сбегающей
|
|
Рисунок 4 – Расчетная схема колодки тормоза: а – расчетная схема набегающего конца ленты; б расчетная схема сбегающего конца ленты
В связи с тем, что уточненный расчет ленточно–колодочного тормоза довольно трудоемок, в КБ заводов его рассчитывают на ЭВМ. Для этого исходная информация для расчета заноситься в бланк исходных данных для ЭВМ.
Программа для расчета на машине строиться так, чтобы она выдавала все необходимые величины для сбегающего и набегающего концов ленты. Для анализа действующих нагрузок расчеты ведут для минимальных и максимальных значений коэффициента трения.
При минимальном коэффициенте трения усилия на органах управления тормозом будут максимальные, и они принимаются для расчета элементов на прочность.
Важными параметрами ленточных тормозов являются скорость трения колодки о шкив, удельная нагрузка, от которых зависит ширина тормоза и износ колодок и тормозной поверхности шкива.
Скорость трения на тормозном шкиве UШ, м/
|
|
,
где uт – кратность полиспаста талевой системы
Наибольшее давление между лентой и тормозным шкивом возникает на поверхности контакта набегающего конца ленты со шкивом, и, постепенно уменьшаясь, оно достигает минимального значения на контакте сбегающего конца ленты со шкивом.
Удельная наибольшая нагрузка между колодкой и шкивом ρmax, МПа ,
где В – ширина ленты тормоза, м,
Удельная наименьшая нагрузка между колодкой и шкивом ρmin, МПа
,
Длина соприкосновения колодок со шкивом L, м
Площадь поверхности трения ПТР, м2
,
Средняя удельная нагрузка ρср, МПа
,
Допускаемое максимальное значение ρср зависит от свойства выбранных материалов шкивов и колодок тормозных лент. Для наиболее широко используемых в настоящее время материалов 0,1 ≤ ρср ≤ 0,7 МПа. Более высокие удельные нагрузки ускоряют износ тормозных колодок и снижают долговечность тормоза.
Мощность торможения NT, кВт
где µ – коэффициент трения тормозных колодок и шкива;
υш – скорость на ободе шкива при торможении, м/с
ni – частота вращения барабана лебедки при торможении, об/мин
Секундная удельная мощность трения при торможении NУД, кВт/м2
|
|
Эксплуатация комплекса АСП
При спуске труб порядок работы механизмов следующий.
I. Талевый блок находится в крайнем нижнем положении. Клинья удерживают колонну труб. Ключ АКБ находится в исходном положении. Механизм захвата освобождает свечу, находящуюся над центром скважины.
II. Талевый блок поднимается по свече, которая вверху удерживается центратором. Ключ АКБ свинчивает свечу с колонной труб.
Клинья удерживают колонну. Механизм расстановки свечей перемещает захват от центра скважины.
Талевый блок продолжает подниматься и начинает поднимать центратор. Ключ АКБ заканчивает свинчивать свечу с колонной труб. Клинья продолжают удерживать колонну. Механизм расстановки продолжает движение.
Талевый блок находится в крайнем верхнем положении. Элеватор удерживает колонну труб. Клинья подняты. Центратор в верхнем положении. Ключ АКБ находится в исходном положении. Механизм расстановки подводит захват к очередной свече, установленной на подсвечнике.
Талевый блок опускает колонну. Клинья подняты. Центратор опускается. Ключ АКБ в исходном положении. Механизм расстановки начинает перемещать свечу к центру скважины.
Талевый блок продолжает опускать колонну. Клинья подняты. Ключ АКБ находится в исходном положении. Механизм расстановки продолжает перемещать свечу к центру скважины.
|
|
Талевый блок находится в крайнем нижнем положении. Клинья удерживают колонну труб. Ключ АКБ находится в исходном положении. Механизм расстановки продолжает перемещать свечу к центру скважины.
При подъеме труб механизмы работают в обратной последовательности.
Рис.5.Работа механизмов АСП.
Предназначен для автоматизации спуско-подъемных операций при бурении на суше и на море. Он устанавливается по желанию заказчика на буровых вышках различных конструктивных исполнений.
Комплекс механизмов механизации и автоматизации спуско-подъемных операций (АСП и КМСП) позволяет механизировать все операции технологического процесса спуско-подъема свечей. Применение механизмов АСП сокращает время спуско-подъемных операций в сравнении с ручной расстановкой на 35--40%. Экономия времени достигается в первую очередь за счет совмещения отдельных операций. Управление комплексом АСП осуществляется одним человеком с пульта управления, который расположен на уровне подсвечника. Большинство узлов комплекса механизмов АСП унифицированы для всех типов буровых установок. Комплекс АСП для морских буровых установок предусматривает установку дополнительного механизма расстановки свечей и промежуточного магазина.
В состав комплекса АСП входят: центратор, механизм расстановки свечей, механизм захвата свечи, механизм подъема, пульт управления, подсвечник и магазин, автоматический универсальный элеватор. Комплексы рассчитаны на работу в комплекте с талевой системой специальной конструкции, автоматическим стационарным буровым ключом типа АКБ или КБГ, пневматическими клиньями, встроенными в ротор.
Сложная конструкция оборудования комплекса АСП, при правильных эксплуатации и обслуживании существенно сократит СПО, кроме того с использованием комплекса снижаются травматизм и опасность для жизни рабочего персонала.
Задача
Исходя из приведённых исходных данных (табл. 2) расчетным путём определите:
Задача 1. Максимальную нагрузку на крюке и выберите класс буровой установки.
Задача 2. Натяжение в подвижной ветви талевого каната при максимальной нагрузке на крюке.
Задача 3. Тип талевого каната по разрывному усилию с указанием полного его обозначения.
Задача 4. Максимальные и минимальные скорости движения крюка на подъём.
Задача 5. Мощность на барабане буровой лебёдки при максимальной нагрузке на крюке.
Таблица 2 - Исходные данные
№ | Проектная глубина бурения L,м | Диаметр БТ Dбт, мм | Вес 1 м БТ qбт,Н/м | Диаметр обсадной колонны Dок,мм | Вес 1 м обсадных труб qот,Н/м | Длина УБТ Lубт, м | Вес 1 м УБТ qубт, м | Оснастка талевой системы |
16 | 2600 | 127 | 235 | 168 | 465 | 240 | 98 | 4х5 |
К задаче 1
Определяется вес бурильной колонны:
где L - проектная глубина бурения,
-вес одного метра бурильных труб, Н/м,
-длина утяжеленных бурильных труб, м
-вес одного метра УБТ, Н/м
Определяется вес эксплуатационной колонны:
, кН
qот - вес 1 м обсадных труб, Н/м
Исходя из наибольшей нагрузки (принимая равной
или
)
С учётом коэффициента запаса к=1,5, определяется максимальная нагрузка на крюке. По полученному значению выбирается класс буровой установки из таблицы 3 с указанием допускаемой нагрузки на крюке и условной глубиной бурения.
Таблица 3 - Основные характеристики установок эксплуатационного и глубокого разведочного бурения
Параметры | Класс 4 |
Диапазон глубин бурения, м | 1600-2600 |
Допускаемая нагрузка на крюке Gкp, МН | 1,6 |
К задаче 2 Задачи должны сопровождаться расчетной схемой талевой системы.
Максимальное натяжение каната определяется по формуле:
, кН (3)
Здесь Q – номинальная нагрузка на крюке в т;
n – число роликов талевой системы;
β – коэффициент сопротивления шкива (β=1,03)
Запас прочности каната должен быть не менее 2,5. По нормам Американского нефтяного института запас прочности талевого каната принимается равным 5 для бурильных труб и 3 для обсадных труб. Для упрощения расчетов формула (3) заменяется следующей:
, кН (4)
где m – коэффициент, зависящий от оснастки
В Гипронефтемаше величины m для различной талевой оснастки сведены в таблица 4
Таблица 4 - Значения величин m
Оснастка талевой | Число рабочих струн | m |
системы | ||
2х3 | 4 | 0,262 |
3х4 | 6 | 0,177 |
4х5 | 8 | 0,137 |
5х6 | 10 | 0,112 |
6х7 | 12 | 0,084 |
С помощью формул (3) и (4) и табл. выбор талевого каната производят следующим образом.
Если принять номинальную нагрузку на крюке Q=160 т , оснастку талевой системы 4х5, коэффициент m=0,137, коэффициент запаса прочности К=4, тогда минимальное необходимое разрывающее усилие каната должно быть:
,
Величину натяжения ходовой ветви каната определяем из равенства:
Откуда
К задаче 3
Определяется величина разрывного усилия:
где k - коэффициент запаса прочности k = 3... 6.
По таблице 6 выбирается диаметр талевого каната с указанием его типа, разрывного усилия и пределом прочности проволочек.
Таблица 6 - Характеристика талевых стальных канатов ЛК-РО
Диаметр каната, мм | Площадь сечения, мм2 | Удельная масса, кг/м2 | Разрывное усилие каната в целом в кН при временном сопротивлении проволоки, МПа | Диаметр проволок внешнего слоя | |
1766 | 1960 | ||||
22 | 204 | 1,9 | 320 | 355 | 1 |
25 | 300,6 | 2,66 | 460 | 510 | 1,6 |
28 | 370,3 | 3,38 | 520 | 578 | 1,8 |
32 | 464,99 | 4,25 | 711 | 789 | 2 |
35 | 564,23 | 5,05 | 863 | 958 | 2,2 |
38 | 671,6 | 5,98 | 1027 | 1140 | 2,4 |
41,3 | 712 | 6,6 | 1120 | 1240 | 2,6 |
44,5 | - | 8,2 | 1200 | 1350 | 2,8 |
Выбираем диаметр каната = 35 мм, площадь сечения = 564,23 мм2
К задаче 4
Определяется максимальная и минимальная скорости намотки подвижной ветви каната на барабан:
где ,
- максимальные и минимальные частоты вращения барабана в минуту, об/мин по табл. 7; D - диаметр барабана талевой лебедки, м по таблица 7.
Определяется максимальная и минимальная скорости движения крюка:
где nрс – число рабочих струн в оснастке по таблица 8.
Таблица 7- Техническая характеристика буровых лебедок
Показатели
| ВЗБТ | ПО «Уралмаш» | ||||
ЛБ-400
| ЛБ-750
| ЛБУ- | ЛБУ- | ЛБУ- | ЛБУ- | |
1200 | 1100 | 1700 | 3000 | |||
Номинальная мощность, кВт | 400 | 550 | 700 | 1000 | 1530 | 2200 |
Глубина бурения, м | 1600 | 2500 | 3200 | 5000 | 6500 | |
Диаметр каната, мм | 25 | 28 | 28 | 32 | 35 | 8 |
Размеры барабана, м: |
| |||||
диаметр | 0,6 | 0,7 | 0,65 | 0,75 | 0,835 | 0,935 |
длина | 0,866 | 1,2 | 0,40 | 1,35 | 1,445 | 1,54 |
Число рядов намотки каната | 3 | 3 | 4 | 4 | 4 | 4 |
Длина каната, наматываемого на барабан, м | 200 | 320 | 320 | 320 | 320 | 460 |
Число скоростей намотки каната | 4 | 4* | 6 | 6* | 6* | 2 |
Частота вращения, об/мин максимальная минимальная | 420 85 | 410 40 | 360 50 | 430 50 | 400 65 | 435 70 |
Скорость намотки каната, м/с максимальная минимальная | 15,0 3,0 | 13,6 1,36 | 16,4 2,1 | 20,2 2,3 | 18,6 3,0 | 21,6 3,5 |
Максимальное натяжение каната, кН | 125 | 200 | 217 | 290 | 340 | 475 |
Диаметр тормозного шкива, м | 1,00 | 1,18 | 1,18 | 1,45 | 1,45 | 1,6 |
Ширина колодки, м | 0,23 | 0,25 | 0,25 | 0,25 | 0,25 | 0,28 |
*Число скоростей при приводе от ДВС.
Таблица 8 - Основные характеристики талевых систем буровых установок по ГОСТ 16293-82
К задаче 5
Определяется полная мощность на барабане буровой лебёдки:
где = 0,9 – КПД подъёмного вала лебёдки;
– КПД талевой системы.
Список использованной литературы
1. https://library.fsetan.ru/doc/ipbot-040-2008-instruktsiya-po-promyishlennoj-bezopasnosti-i-ohrane-truda-pri-ekspluatatsii-i-obsluzhivanii-mashinnyih-klyuchej-kmbo/
2. https://studbooks.net/1560429/tovarovedenie/trebovaniya_bezopasnosti_ekspluatatsii_elevatorov
3. https://neftegaz.ru/tech_library/view/2146-Kompleks-mehanizmov-ASP-dlya-proizvodstva-spuskopodemnyh-operatsiy-pri-burenii-skvazhin
4. Новые буровые установки. Справочное пособие. Составители: В.Л. Архангельский, Ю.С. Аважанский, И.Б. Малкин. — М.: ВНИИБТ, 2014. – 163 Баграмов Р.А. Буровые машины и комплексы: Учебник для вузов. — М.: Недра, 2015.—501 с.
5. Северинчик Н.А. Машины и оборудование для бурения скважин. М.: Недра, 2016. 368 с.
Дата добавления: 2019-03-09; просмотров: 1236; Мы поможем в написании вашей работы! |
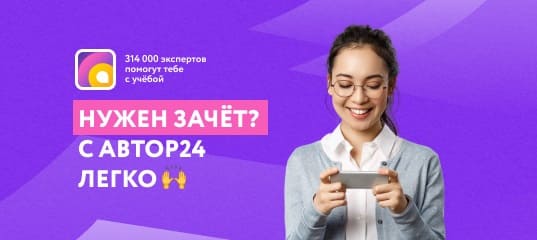
Мы поможем в написании ваших работ!