Определение припусков на обработку по стадиям, установление промежуточных размеров с допусками статистическим методом на заданную поверхность
Промежуточные припуски по стадиям выбираются по таблицам, которые имеются в технологических справочниках.
Выбор припусков на обработку одной (указанной в задании) поверхности. Затем следует определить промежуточные размеры с допусками. [14,188-232], [23,581-608]. Пример выполнения и оформления расчета представлен в таблице 10.
IIоследовательность обработки записывается в таблицу 10 от заготовки до окончательной обработки. На каждом технологическом переходе записываются параметры шероховатости (Ra) и поле допуска (Td) (Данные для расчета берутся из таблицы 9 «План обработки поверхностей». Допускается эти две таблицы объединить в одну.
В графе «Точность обработки» проставляются поля допусков, а также предельные отклонения на заданные операции, которые выбираются по таблицам ЕСДП СЭВ (СТ СЭВ 145-75) или [4,192] Выбор операционных припусков производится по таблицам литературы [14].
Таблица10
Обрабатываемая поверхность | Последовательность обработки поверхности | Точность обработки | Шероховатость обработки поверхности, Ra | Операционные припуски, 2Z0 | Операционные размеры с предельными отклонениями |
Припуск на первую стадию обработки( черновую) определяется по формуле, через общий припуск на данную поверхность детали.
(1)
Для получения операционного размера по стадиям обработки необходимо к операционному размеру последующей стадии прибавить припуск на обработку последующей стадии (для вала):.
|
|
Di=Di+1+2Zi+1 (2)
Для отверстия :
Di=Di+1-2Zi+1 (3)
Определение припусков на обработку по стадиям, установление промежуточных размеров с допусками расчетно-аналитическим методом на заданную поверхность (по указанию руководителя)
Аналитический расчёт операционных припусков на каждый переход производится по методу, изложенному в работе профессора В.М. Кована.
При этом расчёте руководствуются тем правилом, когда высота микронеровностей Rz глубина поверхностного дефектного слоя h и суммарные пространственные отклонения Då берутся по результатам предшествующего технологического перехода.
Значения величин, входящих в формулу минимального промежуточного припуска выбираются по таблицам (исключение: суммарные пространственные отклонения Då рассчитываются).
|
|
Промежуточные размеры рассчитывают в последовательности обратной выполнению технологического процесса обработки поверхности, т.е к исходному расчетному размеру поверхности готовой детали последовательно прибавляют (для наружных поверхностей ) или вычитают (для внутренних поверхностей) промежуточные припуски.
На каждый промежуточный размер нужно указать квалитет, предельные отклонения и указать параметр шероховатости.[14, 175-196]
Выполнение подраздела необходимо выполнить по методическим указаниям к практической работе №3
Четвертый этап ( Проектирование маршрутного технологического процесса. Выбор оборудования)
Проектирование маршрутного технологического процесса.
Эту работу необходимо вести так, чтобы разработанный маршрутный технологический процесс отвечал установленному типу производства.
При проектировании маршрутного технологического процесса необходимо ориентироваться на типовые технологические процессы, имеющиеся в настоящее время для деталей многих классов. Типовые технологические процессы излагаются в книгах по технологии машиностроения для различных отраслей и в справочниках [4], [1], [6], [22].
Студенты могут воспользоваться заводскими технологическими процессами по обработке аналогичных деталей, а также общими положениями проектирования технологических процессов механической обработки деталей машин, рекомендуемыми курсом «Технология машиностроения» Технологический процесс должен соответствовать современному уровню машиностроения. В нем должны быть применены прогрессивные методы обработки.
|
|
Пользуясь основными положениями технологии машиностроения, предусматривают в первую очередь операции обработки технологических базовых поверхностей, затем следует ряд черновых, чистовых и отделочных операций, причем в серийном и массовом производстве необходимо отделять черновые операции от чистовых, чистовые от отделочных и т.д.
При составлении маршрутной технологии следует проверить и убедиться:
а) в правильности выбора технологических баз и обосновать их выбор;
б) правильности чередования механических операций и правильности включения в процесс термических, слесарных, моечных, контрольных и других операций;
в) в обеспечении принятым технологическим процессом получения
требуемой точности и шероховатости обрабатываемых поверхностей в соответствии с требованиями чертежа;
|
|
При составлении технологического маршрута обработки детали (установлении порядка операций) руководствуются следующими общими положениями:
1) назначают операции, исходя из конструктивных форм, размеров детали и типа производства;
2) в первую очередь обрабатывают поверхности детали, которые будут служить базами для последующей обработки;
3) после базовых поверхностей обрабатывают поверхности, с которых снимают наибольшие слои металла;
4) отделочные операции выполняют в конце технологического процесса обработки;
5) операции механической обработки увязывают с термическими операциями.
Конструктивные формы и размеры детали служат исходными факторами, определяющими характер и последовательность обработки детали. Так, черновую обработку деталей типа тел вращения проводят на токарных станках, а детали с плоскими поверхностями обрабатывают на фрезерных и строгальных станках. Чистовую обработку деталей типа тел вращения ведут на круглошлифовальных станках, а деталей с плоскими поверхностями - на плоскошлифовальных станках. Зубья на зубчатом колесе с внутренними зубьями могут быть получены только методами зубодолбления или протягивания.
Размеры деталей определяют выбор типоразмера станка и в некоторых случаях и метод обработки. Так, зубчатые колеса малых модулей экономичнее изготовлять зубодолблением, а крупных модулей — зубофрезерованием червячными фрезами.
Тип производства влияет на выбор применяемых методов обработки и станков. Например, черновую обработку плоских поверхностей в условиях единичного производства чаще производят на строгальных станках, а в условиях серийного и массового - на фрезерных. Для изготовления мелких деталей типа тел вращения применяют при единичном производстве универсальные токарные станки, при серийном - токарно-револьверные, при массовом – токарные автоматы.
Обработка в первую очередь базовых поверхностей повышает точность последующей обработки. Характерным примером является предварительная обработка центровых гнезд при точении валов: последующая обработка валов ведется с использованием центровых гнезд в качестве баз.
При построении плана обработки стремятся к тому, чтобы каждая последующая операция была точнее предыдущей, поэтому в качестве первых операций механической обработки выбирают те, при выполнении которых снимают наибольшие слои металла. Это обусловлено, во-первых, тем, что при снятии больших слоев металла легче обнаружить дефекты заготовки (трещины, раковины, неметаллические включения и т. п.); во-вторых, при снятии больших слоев металла с заготовок вследствие перераспределения напряжений возможно коробление заготовок. При последующей чистовой обработке коробление будет минимальным.
Отделочные операции выполняют в конце цикла обработки для уменьшения возможности повреждения окончательно обработанных поверхностей. Отделочные методы обработки выбирают в зависимости от требуемых чертежом точности и класса шероховатости поверхности.
Операции механической обработки детали должны быть увязаны с термическими операциями. Наиболее часто закалку с низким отпуском проводят перед шлифованием, закалку с высоким отпуском (улучшение) — между черновой и чистовой обработками точением, фрезерованием, строганием. Перед процессом механической обработки заготовки (отливки, штамповки, поковки) обычно подвергают отжигу или нормализации.
Выбор технологических баз.
От правильного выбора технологической базы во многом зависит качество обработки детали. Необходимо стремиться к соблюдению двух основных условий: совмещению и постоянству баз. Особенно важно правильно выбрать базу при выполнении первой операции:
1) При выборе черновых баз базовых поверхностей следует руководствоваться следующими правилами:
- Черновая базовая поверхность должна обеспечивать устойчивое положение детали в приспособлении.
- У тех деталей, у которых в обработанном виде остаются необработанные поверхности, за черновые базы принимаются эти необработанные поверхности.
- У тех деталей, у которых все поверхности подлежат обработке, за черновые базы принимаются поверхности с минимальными припусками.
- Черновые базы должны быть ровными и чистыми.
- После выполнения первой операции черновая база должна быть заменена на чистовую.
2) При выборе чистовых базовых поверхностей следует руководствоваться следующими правилами:
- За чистовые базы принимаются основные поверхности, от которых заданы основные размеры до других обрабатываемых поверхностей;
- Необходимо использовать принцип совмещения баз, т.е. в ходе обработки на всех основных операциях в качестве установочных баз принимать одни и те же поверхности;
- Необходимо использовать принцип совмещения баз, т.е. в качестве установочной базы брать поверхность, которая является измерительной базой;
- Чистовая база должна быть выбрана так, чтобы в процессе выработки детали не было недопустимых деформаций от усилий резания и зажима;
- Выбранная чистовая база должна обеспечивать прочную и надежную конструкцию приспособления с удобной установкой, креплением и снятием обрабатываемой детали.
Рекомендации по выбору базирующих поверхностей приведены в учебниках по технологии машиностроения[ 3], [1], [12].
Выбор оборудования
Выбор станка производят, исходя из содержания операции, требований точности и шероховатости обработки, соответствие его производительности заданной программе выпуска деталей, соответствия мощности станка, мощности требуемой при обработке, соответствия размера рабочей зоны станка, размерам обрабатываемых деталей.
Выбор станков производят по каталогам и справочникам, исходя из содержания операций, типа производства, размера детали.
Литература [22]; [24]; [6].
При этом следует руководствоваться экономической точностью обработки на различных металлорежущих станках.
Данный этап работы завершается выполнением маршрутной карты.[4, 193-206]
Дата добавления: 2019-02-22; просмотров: 236; Мы поможем в написании вашей работы! |
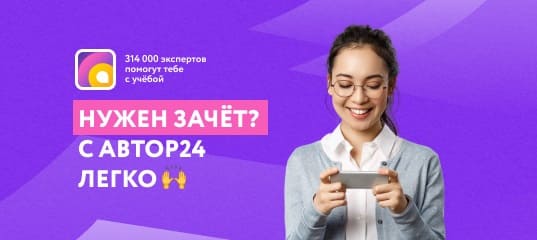
Мы поможем в написании ваших работ!