Методика оценки структуры и свойств сплава
Из полученных контрольных и после МИО литых образцов после удаления прибыльной части были вырезаны образцы для проведения механических испытаний и образцы для их последующей прокатки.
На рисунке 9 представлен чертеж образца для механических испытаний.
Рисунок 9 – Чертеж образца для механических испытаний
Все полученные образцы были испытаны на универсальной разрывной машине Testometric FS 150 kN AX. В результате были получены данные по их пределу прочности и относительному удлинению.
Далее на испытанных образцах проводились металлографические исследования с применением программно-аппаратного комплекса «SIAMS - 700».
Для этого элементы образцов залили в эпоксидную смолу «Супер – хват». Образец закреплялся на горизонтальной плоскости так, чтобы исследуемая поверхность и края оправки находились на одном уровне. Подготовленный образец подвергался шлифовке и полировке.
При переходе от одной зернистости шлифовальной бумаги к другой тщательно удалялась абразивная пыль с помощью промывки образца под проточной водой. При переходе на шлифовальную бумагу другой зернистости положение образца меняли путем поворота на 90°.
Качество подготовки шлифов контролировалось визуально. Поверхность
После полировки образец протравливали для более четкого выявления микроструктуры. Травление позволяет определить особенности кристаллического микростроения, характер и расположения дефектов. Микроструктура выявляется, как правило, погружением в реактив и периодическом осмотром поверхности шлифа после его промывки. Травление образца происходит при комнатной температуре в реактиве в течении 5-10 с, с последующей промывкой теплой водой и осмотром исследуемой поверхности. Операция повторяется до четкого выявления структуры.
|
|
На образцах для их прокатки с помощью механической обработки была удалена литейная корка (рис. 10), которая могла стать причиной их преждевременного разрушения из-за возможного наличия в ней различных неметаллических включений. После чего была произведена прокатка в горячем состоянии образцов.
Рисунок 10 – Внешний вид образцов для прокатки
Горячая прокатка образцов проводилась в следующей последовательности:
1. разогрев лабораторной печи до температуры 500°С;
2. после выхода печи на рабочий режим в нее загружались образцы и выдерживались в ней в течении 30 мин;
3. на прокатном стане устанавливались необходимые параметры для прокатки, а именно: скорости вращения валков 15м/мин и зазор между валками для первого перехода 10 мм, при начальной толщине всех образцов 13,5 мм;
4. на втором переходе раствор валков уменьшался с 10 мм до 7 мм, на третьем переходе – с 7 мм до 3,8 мм;
|
|
5. после каждого перехода образцы укладывались обратно в печь для поддержания их температуры.
Далее из полученных образцов были вырезаны 2 группы образцов под последующую холодную прокатку в 3 перехода с отжигом и без отжига.
Результаты образцов подвергшихся МИО
Результаты механических испытаний образцов после МИО приведены в табл. 10 и в виде графиков на рисунке 11.
Таблица 10 – Результаты механических испытаний
№ | σв , МПа | ∆, % |
0 | 114,84 | 3,066 |
1 | 134,86 | 3,587 |
2 | 140,66 | 3,075 |
3 | 104,33 | 1,953 |
4 | 105,89 | 2,144 |
5 | - | - |
6 | 102,64 | 1,907 |
7 | 93,87 | 1,735 |
8 | 126,26 | 3,231 |
9 | 103,98 | 2,120 |
10 | 103,98 | 2,120 |
Рисунок 11 – Графики предела прочности и относительного удлинения образцов
Также на рисунках 12 и 13 при показан анализ данных с помощью программы Statistica для предела прочности и относительного удлинения.
Рисунок 12 – Анализ с помощью программы для предела прочности
Рисунок 13 – Анализ с помощью программы для относительного удлинения
На рисунке 14, в качестве примера показана микроструктура характерных образцов.
Рисунок 14 – Микроструктура характерных образцов при разных параметрах энергии разряда и количестве импульсов
|
|
В табл. 11 представлены результаты влияния МИО на структуру лигатурного силумина с содержанием Si 20%.
Таблица 11 – Влияние МИО на структуру лигатурного силумина с содержанием Si 20%
Вид обработки | Энергия разряда МИУ, кДж | Количество импульсов, шт. | Средний размер кристаллов Siп, мкм |
Без обработки | - | - | 530 |
МИО | 1,5 | 4 | 282 |
1,0 | 7 | 106 | |
0,5 | 10 | 88 |
6 Результаты горячей прокатки образцов
Была произведена горячая прокатка обработанных образцов за 3 перехода. В процессе прокатки на образце №1 произошло растрескивание материала. Трещина проходит через половину образца. На других образцах имеются не большие трещины по краям кромки. Наиболее ровная и без растрескивания кромка получилась на образце №10. Внешний вид образцов после их прокатки показан на рисунке 15.
Рисунок 15 – Результаты горячей прокатки образцов
В результате визуального анализа полученных образцов можно сделать вывод о влиянии параметров МИО на характер растрескивания кромок. В ходе дальнейших исследований планируется вырезать из данных образцов соответствующие образцы для механических испытаний, а также образцы для последующей холодной прокатки до их разрушения с целью определения предельной степени деформации.
|
|
Результаты образцов после горячей прокатки приведены в табл. 12 и в виде графиков на рисунке 16.
Таблица 12 – Свойства образцов после горячей прокатки
№ | *Толщина образца, мм | *Ширина образца, мм | Предел прочности, МПа | Предел текучести, МПа | Относит. удлинение, % | *Электрическая проводимость, МСм/м |
0 | 3,76 | 19,94 | 136,94 | 113,09 | 11,57 | 23,2 |
1 | 3,87 | 20,23 | 150,93 | 149,52 | 6,43 | 22,6 |
2 | 3,75 | 19,87 | 143,16 | 126,62 | 11,78 | 23,1 |
3 | 3,76 | 20,27 | 140,44 | 135,97 | 7,75 | 20,3 |
4 | 3,665 | 19,94 | 136,36 | 131,08 | 8,24 | 23,2 |
5 | 3,59 | 19,81 | 139,12 | 122,43 | 10,76 | 20,7 |
6 | 3,86 | 19,89 | 151,7 | 151,09 | 5,87 | 24,2 |
7 | 3,81 | 19,63 | 149,63 | 149,3 | 5,35 | 18,6 |
8 | 3,82 | 20,13 | 163,95 | 154,42 | 6,6 | 23,2 |
10 | 3,825 | 20,16 | 158,51 | 156,45 | 7,23 | 23,5 |
Рисунок 16 – Свойства после горячей прокатки образцов
Также на рисунках 17 и 18 при показан анализ данных с помощью программы Statistica для предела прочности и относительного удлинения.
Рисунок 17 – Анализ с помощью программы для предела прочности
Рисунок 18 – Анализ с помощью программы для относительного удлинения
Дата добавления: 2019-03-09; просмотров: 170; Мы поможем в написании вашей работы! |
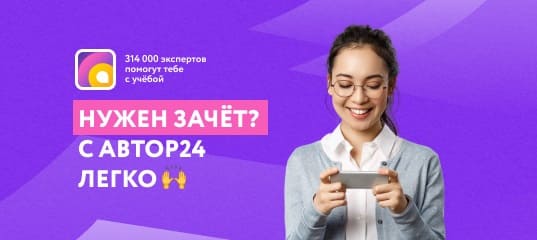
Мы поможем в написании ваших работ!