Хранение шлифовальных и отрезных кругов
Вид, тип круга* | Наружный диаметр круга, мм | Способ хранения без тары (обозначен знаком ×) | ||||||
в ящике или коробке | на ребре | стопкой высотой не более, мм | ||||||
300 | 600 | 1000 | ||||||
Шлифовальные круги типов ПП, ПВ, ПВД, К, ПВК, ПВДК | До 100 | × | – | – | × | – | ||
Более 100 | – | × | – | – | × | |||
Шлифовальные круги типов 2П,3П | Все диаметры | – | – | – | × | – | ||
Шлифовальные круги типа ПН | – | × | – | × | – | |||
Шлифовальные круги типов ЧК, ЧЦ, ПВДС | До 200 | – | – | – | × | – | ||
Более 200 | – | – | – | – | × | |||
Шлифовальные круги типов Т, 1Т | Все диаметры | – | – | × | – | – | ||
Шлифовальные круги типов ПП, ПВ, Д для ручных машин | До 100 | × | – | × | – | – | ||
Более 100 | – | × | – | × | – | |||
Шлифовальные круги типов 5П, ЧЦ, ЧК для ручных машин | Все диаметры | – | – | × | – | – | ||
Отрезные круги | До 150 | – | – | × | – | – | ||
От 150 до 300 | – | – | – | × | – | |||
Более 300 | – | – | – | – | × | |||
*)ПП – прямого профиля; ПВ – с выточкой; ПВД – с двусторонней выточкой; К – кольцевые; ПВК – с конической выточкой; ПВДК – с двусторонней конической выточкой; 2П – с двусторонним коническим профилем; 3П – с коническим профилем; ПН – с запрессованными крепежными элементами; ЧК – чашечные конические; ЧЦ – чашечные цилиндрические; ПВДС – с двусторонней выточкой и маточиной; Т и 1Т – тарелчатые; Д – отрезные; 5П – с опущенным центром.
|
5.1.43. Абразивные шеверы необходимо хранить в стопках на стеллажах на расстоянии не менее 1 м от отопительных приборов.
Полировальные тканевые и кордовые круги необходимо хранить при температуре не ниже плюс 2 °С, абразивные шеверы – при температуре не ниже плюс 15 °С.
Пасты должны храниться при температуре, не выше:
– плюс 25 °С и относительной влажности воздуха до 90 % – твердые абразивные;
– плюс 25 °С – жидкие абразивные;
– плюс 30 °С – эльборовые.
5.1.44. Гарантийный срок хранения с момента изготовления не должен превышать:
– 3 мес. – для абразивных жидких паст;
– 6 мес. – для шлифовальных кругов на бакелитовой и вулканитовой связке, отрезных кругов на бакелитовой связке, брусков и сегментов на бакелитовой связке;
– 12 мес. – для отрезных кругов на вулканитовой связке, фибровых дисков, шлифовальной шкурки и изделий из нее, полировальных сезалевых кордовых кругов, абразивной твердой и эльборовой паст, абразивных шеверов.
5.1.45. При перевозке шлифовальных кругов в пределах предприятия их необходимо защищать от повреждения, что достигается подкладыванием под них буферной подушки из упругого материала (резины, пенопласта, войлока и т.п.) и применением для их перевозки тележек на рессорах и колесах с резиновыми ободами, дно и борта которых обшиты упругим материалом.
|
|
Круги необходимо перевозить стопками высотой до 500 мм, и между кругами диаметром 500 мм и более прокладывать амортизирующие прокладки толщиной не менее 0,5 мм и диаметром не менее 1/2 диаметра перевозимых кругов.
5.1.46. Запрещается при выполнении работ с применением абразивного и эльборового инструмента:
– работать боковыми (торцевыми) поверхностями шлифовального круга, – если он не предназначен для выполнения этого вида работ;
– тормозить вращающийся шлифовальный круг нажатием на него каким-нибудь предметом;
– применять насадки на гаечные ключи и ударный инструмент – при закреплении шлифовального круга;
– применять рычаг для увеличения усилия нажатия обрабатываемых деталей на шлифовальный круг – на станках с ручной подачей изделий;
– выполнять работу без применения смазочно-охлаждающей жидкости (СОЖ) – для инструмента, предназначенного для работы с применением СОЖ.
5.2. Требования к ручному электрифицированному инструменту и к выполнению работ с его применением
5.2.1. Ручной электрифицированный инструмент (далее – электроинструмент) должен соответствовать требованиям ГОСТ 12.2.013.0.
|
|
5.2.2. На корпусах электроинструмента необходимо указывать инвентарные номера и даты проведения следующих проверок, а на понижающих и безопасных изолирующих трансформаторах (далее – разделительных трансформаторах), преобразователях частоты и защитно-отключающих устройствах – инвентарные номера и даты проведения следующих измерений сопротивления изоляции.
5.2.3. При выполнении работ с использованием электроинструмента необходимо применять электроинструмент следующих классов:
а) I – электроинструмент, у которого все детали, находящиеся под напряжением, имеют изоляцию, а штепсельная вилка – заземляющий контакт. У электроинструмента такого класса допускается, чтобы все находящиеся под напряжением детали имели основную, а отдельные детали – двойную или усиленную изоляцию;
б) II – электроинструмент, у которого все детали, находящиеся под напряжением, имеют двойную или усиленную изоляцию. Электроинструмент такого класса не имеет устройств для заземления.
Номинальное напряжение электроинструмента классов I и II не должно превышать:
– 220 В – для электроинструмента постоянного тока;
– 380 В – для электроинструмента переменного тока;
|
|
в) III – электроинструмент на номинальное напряжение не выше 42 В, у которого ни внутренние, ни внешние цепи не должны находиться под другим напряжением. Электроинструмент такого класса должен питаться от безопасного сверхнизкого напряжения, создаваемого:
– автономным источником питания;
– путем преобразования более высокого напряжения с помощью разделительного трансформатора или преобразователя с разделительными обмотками.
5.2.4. Электроинструмент, питающийся от электрической сети, должен быть оснащен несъемным гибким кабелем (шнуром) со штепсельной вилкой.
Несъемный гибкий кабель электроинструмента класса І должен иметь жилу, соединяющую заземляющий зажим электроинструмента с заземляющим контактом штепсельной вилки.
Кабель в месте ввода в электроинструмент класса І необходимо защитить от истираний и перегибов эластичной трубкой из изоляционного материала. Трубка должна закрепляться в корпусных деталях электроинструмента так, чтобы она выступала из них на длину не менее пяти диаметров кабеля.
Трубка на кабеле не должна закрепляться вне электроинструмента.
5.2.5. Для присоединения однофазного электроинструмента шланговый кабель должен иметь три жилы: две – для питания, одну – для заземления.
Для присоединения трехфазного электроинструмента необходимо применять четырехжильный кабель, одна из жил которого предназначена для заземления.
Эти требования относятся только к электроинструменту с заземленным корпусом.
5.2.6. Доступные для прикосновения металлические детали электроинструмента класса І, которые могут попасть под напряжение в случае повреждения изоляции, должны соединяться с заземляющим зажимом.
Электроинструмент классов II и III не подлежит заземлению.
Заземление корпуса электроинструмента необходимо выполнять с помощью специальной жилы питающего кабеля, которая не должна одновременно быть проводником рабочего тока.
Запрещается использовать для заземления корпуса электроинструмента нулевой рабочий провод.
Штепсельная вилка электроинструмента должна иметь соответствующее количество рабочих и один заземляющий контакт. Конструкция вилки должна обеспечивать опережающее замыкание заземляющего контакта – при включении и более позднее размыкание – при его отключении.
Штепсельные вилки электроинструмента класса III должны иметь конструкцию, которая исключает возможность сочленения их с розетками на напряжение выше 42 В.
5.2.7. Переносные понижающие трансформаторы, разделительные трансформаторы и преобразователи должны иметь на стороне высшего напряжения кабель со штепсельной вилкой для присоединения к электрической сети. Длина кабеля не должна превышать 2 м, а его концы должны прикрепляться к зажимам трансформатора с помощью:или пайки (сварки), или болтового соединения.
На стороне низшего напряжения трансформатора должны быть гнезда под штепсельную вилку.
5.2.8. Корпуса преобразователей, разделительных и понижающих трансформаторов, в зависимости от режима нейтрали электрической сети, питающей первичную обмотку, необходимо или заземлить, или занулить в соответствии с требованиями подраздела 1.7 "Правил устройства электроустановок".
Вторичную обмотку понижающих трансформаторов необходимо заземлить.
Не допускается заземление вторичной обмотки трансформаторов или преобразователей с раздельными обмотками.
5.2.9. К работе с электроинструментом класса І в помещениях с повышенной опасностью поражения электрическим током и вне помещений должны допускаться работники, имеющие по электробезопасности группу не ниже II, а к работе с электроинструментом классов II и III – работники с группой I.
Работники, допущенные к работе с электроинструментом, должны предварительно пройти обучение и проверку знаний правил безопасной работы и иметь запись в удостоверении о допуске к выполнению работ с применением электроинструмента.
Электротехнические работники, имеющие по электробезопасности группу II и выше, допускаются к работе с электроинструментом без записи в удостоверении на право выполнять специальные работы.
5.2.10. Каждый раз при выдаче электроинструмента необходимо проверить:
– комплектность и надежность закрепления деталей;
– исправность кабеля и штепсельной вилки, целостность изоляционных деталей корпуса, рукоятки и крышек щеткодержателей, наличие защитных кожухов и исправность их – проверяются внешним осмотром;
– четкость работы выключателя;
– работу на холостом ходу;
– исправность цепи заземления между корпусом электроинструмента и заземляющим контактом штепсельной вилки – для электроинструмента класса I.
Кроме того, при выдаче электроинструмента должны выдаваться: или средства индивидуальной защиты (диэлектрические перчатки, галоши, коврики), или разделительный трансформатор, или преобразователь с раздельными обмотками, или защитно-отключающее устройство.
Запрещается выдавать для работы электроинструмент, который не отвечает хотя бы одному из вышеперечисленных требований или с просроченной датой периодической проверки.
5.2.11. Перед началом выполнения работ с применением электроинструмента необходимо проверять:
– дату проведения последней периодической проверки электроинструмента;
– соответствие напряжения и частоты тока электрической сети напряжению и частоте тока электродвигателя электроинструмента, указанным на табличке;
– надежность закрепления рабочего исполнительного инструмента (сверл, абразивных кругов, дисковых пил, ключей-насадок и т.п.).
5.2.12. При выполнении работы с электроинструментом класса І необходимо обязательно применять средства индивидуальной защиты (диэлектрические перчатки, галоши, коврики и т.п.), – за исключением следующих случаев:
– только один электроинструмент питается от разделительного трансформатора;
– электроинструмент питается: или от автономной двигатель-генераторной установки, или от преобразователя частоты с разделительными обмотками;
– электроинструмент питается через защитно-отключающее устройство.
В помещениях без повышенной опасности поражения работников электрическим током необходимо применять диэлектрические перчатки, а в помещениях с токопроводящими полами – также и диэлектрические галоши или коврики.
5.2.13. Разрешается выполнять работы с применением электроинструмента классов II и III без применения индивидуальных средств защиты в помещениях без повышенной опасности поражения работников электрическим током.
5.2.14. В сосудах, аппаратах и других металлических сооружениях с ограниченной возможностью перемещения и выхода из них разрешается работать с электроинструментом классов І и II при условии, что только один электроинструмент получает питание от автономной двигатель-генераторной установки, разделительного трансформатора или преобразователя частоты с разделительными обмотками, а также электроинструментом класса III. При этом источник питания (трансформатор, преобразователь и т.п.) должен находиться вне металлического сосуда, а его вторичная цепь не должна заземляться.
5.2.15. Запрещается подключать электроинструмент напряжением до 42 В к электрической сети общего назначения через автотрансформатор, резистор или потенциометр.
5.2.16. При выполнении работ в подземных сооружениях (колодцах, камерах и т.п.), топках и барабанах котлов, конденсаторах турбин, баках трансформаторов и в других емкостях трансформатор или преобразователь частоты, к которому присоединен электроинструмент, обязательно должен находиться вне этих сооружений или емкостей.
5.2.17. Подключать (отключать) вспомогательное оборудование (трансформаторы, преобразователи частоты, защитно-отключающие устройства и т.п.) к электрической сети (от сети), проверять это оборудование, устранять неисправности, разбирать и ремонтировать инструмент, кабель, штепсельные соединения и т. п. должны специально подготовленные работники, имеющие по электробезопасности группу не ниже III.
5.2.18. Кабель электроинструмента необходимо защитить от случайного повреждения и соприкосновения его с горячими, сырыми и масляными поверхностями.
Не разрешается натягивать, перекручивать и перегибать кабель, питающий электроинструмент, ставить на него груз, а также допускать пересечение этого кабеля с тросами, кабелями и рукавами для газосварки.
5.2.19. Устанавливать рабочую часть электроинструмента в патрон и изымать ее из патрона, а также регулировать электроинструмент разрешается только после отключения его от электрической сети штепсельной вилкой и полной его остановки.
5.2.20. Во время работы электроинструмента стружку или опилки следует удалять специальными крючками или щетками – только после полной остановки электроинструмента; запрещается удалять стружку или опилки руками.
5.2.21. Запрещается работать с электроинструментом с приставных лестниц.
При выполнении работ с электродрелью предметы, подлежащие сверлению, необходимо надежно закреплять.
Не разрешается прикасаться руками к вращающемуся режущему инструменту.
5.2.22. При сверлении электродрелью с использованием рычага для прижима необходимо следить, чтобы конец рычага не опирался на поверхность, с которой он может соскользнуть.
Не разрешается использовать вместо рычагов случайные предметы; рычаги должны иметь инвентарные номера и храниться в инструментальной кладовой.
5.2.23. Запрещается обрабатывать электроинструментом мокрые и обледеневшие детали.
5.2.24. Работник, выполняющий работу с применением электроинструмента, не должен оставлять без надзора подключенный к электросети электроинструмент, а также передавать его работникам, не имеющим права выполнять работу с его применением.
5.2.25. Запрещается работать с электроинструментом, который:
– не имеет защиты от действия капель или брызг, – если работа выполняется в условиях действия капель и брызг, а также на открытых площадках во время снегопада или дождя;
– не имеет распознавательных знаков (капля в треугольнике или две капли). Работать с таким электроинструментом разрешается вне помещения только в сухую погоду, а во время снегопада или дождя – под навесом на сухой земле или настиле.
5.2.26. При внезапной остановке электроинструмента (исчезновение напряжения в сети, заклинивание подвижных частей и т.п.) его необходимо отключить от электрической сети выключателем.
При перемещении электроинструмента с одного рабочего места на другое, а также во время перерыва в работе и после ее окончания электроинструмент необходимо отсоединить от электрической сети с помощью штепсельной вилки.
5.2.27. Работать с электроинструментом в случае, когда работник почувствует хотя бы слабое действие тока, запрещено. В этом случае работу необходимо немедленно прекратить, а неисправный электроинструмент сдать для проверки и ремонта.
5.2.28. Работать с электроинструментом, у которого закончился срок периодической проверки, не разрешается; запрещено также работать с электроинструментом при возникновении хотя бы одной из следующих неисправностей:
– повреждение штепсельного соединения, кабеля или его защитной трубки;
– повреждение крышки щеткодержателя;
– нечеткая работа выключателя;
– искрение щеток на коллекторе, сопровождающееся появлением кругового огня на его поверхности;
– вытекание смазки из редуктора или вентиляционных каналов;
– появление дыма или запаха, характерного для горящей изоляции;
– появление повышенного шума, стука, вибрации;
– поломка или появление трещин в корпусной детали, рукоятке, защитном ограждении;
– повреждение рабочей части электроинструмента;
– исчезновение электрической связи между металлическими частями корпуса и нулевым защитным штырем штепсельной вилки.
5.2.29. Электроинструмент, разделительные и понижающие трансформаторы, преобразователи частоты, защитно-отключающие устройства и кабели-удлинители должны периодически, не реже 1 раза в 6 мес., проходить проверку, включающую:
– внешний осмотр;
– проверку работы на холостом ходу – не менее 5 мин;
– измерение в течение 1 мин мегомметром на напряжение 500 В сопротивления изоляции, которое должно быть не менее 1 МОм, – при включенном выключателе;
– измерение сопротивления обмоток электроинструмента и токоведущего кабеля относительно корпуса и наружных металлических деталей;
– измерение сопротивления между первичной и вторичной обмотками трансформатора, а также между любой из обмоток и корпусом;
– проверку исправности цепи заземления – для электроинструмента класса I. Исправность цепи заземления должна проверяться с помощью устройства на напряжение не более 12 В, один контакт которого подключается к заземляющему контакту штепсельной вилки, а другой – к доступной для прикосновения металлической детали электроинструмента (например, к шпинделю). В случае исправного электроинструмента такое устройство должно показывать наличие тока.
5.2.30. После капитального ремонта электроинструмента или ремонта его электрической части электроинструмент должен проходить следующие испытания:
– проверку правильности сборки – внешним осмотром и трехразовым включением и выключением выключателя у подключенного на номинальное напряжение электроинструмента. При этой проверке не должно быть отказов пуска и остановки;
– проверку исправности цепи заземления (для электроинструмента класса І);
– испытание изоляции на электрическую прочность;
– обкатку в рабочем режиме в течение не менее 30 мин.
5.2.31. После капитального ремонта электроинструмента сопротивление изоляции между находящимися под напряжением деталями и корпусом или деталями должно быть:
– 2 МОм – для основной изоляции;
– 5 МОм – для дополнительной изоляции;
– 7 МОм – для усиленной изоляции.
5.2.32. Электрическую прочность изоляции электроинструмента необходимо испытывать в течение 1 мин следующими напряжениями переменного тока частотой 50 Гц:
– 1000 В – для электроинструмента класса I;
– 2500 В – для электроинструмента класса II;
– 400 В – для электроинструмента класса III.
При проведении испытаний электроды испытательной установки необходимо прикладывать: или к одному из токоведущих контактов штепсельной вилки и к шпинделю, или к металлическому корпусу, или к фольге, наложенной на изготовленный из изоляционного материала корпус электроинструмента.
При проведении испытаний выключатель должен быть включен.
5.2.33. При вводе в эксплуатацию, а также после капитального ремонта понижающих и разделительных трансформаторов, преобразователей частоты и защитно-отключающих устройств изоляцию их обмоток необходимо в течение 1 мин испытывать повышенным (испытательным) напряжением, прикладываемым поочередно к каждой из них. При этом остальные обмотки необходимо электрически соединить с заземленными корпусом и магнитопроводом.
Испытательное напряжение должно быть следующее:
– 550 В – при номинальном напряжении вторичной обмотки трансформатора и преобразователя частоты напряжением до 42 В;
– 1350 В – при номинальном напряжении соответственно первичной и вторичной обмоток трансформатора и преобразователя частоты 127 – 220 В, при напряжении питающей сети защитно-отключающего устройства 127 – 220 В;
– 1800 В – при номинальном напряжении соответственно первичной и вторичной обмоток трансформатора и преобразователя частоты 380 – 400 В, при напряжении питающей сети защитно-отключающего устройства 380 – 400 В.
5.2.34. Результаты проверок и испытаний электроинструмента, понижающих и разделительных трансформаторов, преобразователей частоты, защитно-отключающих устройств и кабелей необходимо записывать в "Журнал учета, проверки и испытаний электроинструмента и вспомогательного оборудования к нему" по форме, приведенной в приложении 4 к настоящим Правилам. Журнал должен вести назначенный распоряжением по подразделению предприятия работник, отвечающий за сохранность и исправность электроинструмента.
5.2.35. Хранить электроинструмент и вспомогательное оборудование к нему необходимо в сухом помещении, оборудованном специальными стеллажами, полками, ящиками, обеспечивающими его сохранность. При хранении электроинструмента необходимо выполнять требования к условиям его хранения, указанные в паспорте.
5.2.36. Электроинструмент должен храниться в складских помещениях в упаковке; без упаковки электроинструмент может храниться только в случае размещения его в один ряд.
Транспортировать электроинструмент в пределах предприятия необходимо осторожно с соблюдением мер, исключающих возможность его повреждения.
Запрещается перевозить электроинструмент вместе с металлическими деталями и изделиями.
5.3. Требования к переносным ручным электрическим светильникам
5.3.1. Переносные ручные электрические светильники (далее – светильники) должны иметь рефлектор, защитную сетку, крючок для подвески и шланговый провод с вилкой; сетка должна быть укреплена на рукоятке винтами или хомутами. Патрон должен быть встроен в корпус светильника так, чтобы токоведущие части патрона и цоколя лампы были недоступны для прикосновения.
5.3.2. Штепсельные вилки светильников напряжением 12 и 42 В не должны подходить к розеткам электрической сети напряжением 127 и 220 В.
Розетки напряжением 12 и 42 В должны отличаться от розеток электрической сети напряжением 127 и 220 В.
5.3.3. Для питания светильников в помещениях с повышенной опасностью и в особо опасных необходимо применять напряжение не выше 42 В.
При наличии особо неблагоприятных условий, а именно: когда опасность поражения электрическим током усугубляется теснотой, неудобным положением работника, выполняющего работу, соприкосновением с большими металлическими заземленными поверхностями (например, работа в барабанах, газоходах, топках котлов, в туннелях), для питания светильников необходимо применять напряжение не выше 12 В.
5.3.4. Переносной понижающий трансформатор необходимо размещать вне барабанов, газоходов и топок котлов, туннелей и т. п.
Заземление корпуса и вторичной обмотки понижающего трансформатора, а также измерение сопротивления изоляции и испытание ее электрической прочности должны соответствовать требованиям пунктов 5.2.8, 5.2.30 и 5.2.34 настоящих Правил.
5.3.5. Не разрешается использовать автотрансформаторы, дроссельные катушки и реостаты для понижения напряжения питания светильников.
5.3.6. Для подключения светильников к электрической сети необходимо применять провод с медными жилами сечением от 0,75 до 1,5 мм2 с пластмассовой или резиновой изоляцией в поливинилхлоридной или резиновой оболочке, соответствующий требованиям ГОСТ 7399. Провод в местах ввода в светильник должен быть защищен от истирания и перегибов.
5.3.7. Провод светильника должен быть защищен от случайного повреждения и столкновения его с горячими, влажными и масляными поверхностями.
5.3.8. Перед выдачей светильников работники, выдающие и принимающие их, обязаны удостовериться в исправности ламп, патронов, штепсельных вилок, проводов и т.п.
5.3.9. Если во время работы обнаружится неисправность электролампы, провода или трансформатора, необходимо заменить их исправными, предварительно отключив их от электросети.
Ремонт светильников должны выполнять электротехнические работники в мастерской.
5.3.10. Переносные светильники необходимо хранить в сухом помещении.
5.3.11. Сопротивление изоляции светильников, находящихся в эксплуатации, необходимо измерять периодически, не реже 1 раза в 6 мес., мегомметром на напряжение 1000 В; сопротивление изоляции должно быть не менее 0,5 МОм.
5.4. Требования к ручному слесарно-кузнечному инструменту
5.4.1. Ручной слесарно-кузнечный инструмент повседневного применения должен закрепляться за работниками для индивидуального или бригадного пользования.
5.4.2. Бойки молотков и кувалд должны иметь гладкую, слегка выпуклую поверхность без косины, выбоин, сколов, трещин и заусенцев.
5.4.3. Рукоятки молотков, кувалд и другого инструмента ударного действия должны изготавливаться из сухой древесины твердых лиственных пород (березы, дуба, бука, клена, ясеня, рябины, кизила, граба) без сучков и косослоя или из синтетических материалов, обеспечивающих эксплуатационную прочность и надежность в работе; использование рукояток, изготовленных из древесины мягких и крупнолистных пород дерева (ели, сосны и т.п.), а также из сырой древесины, запрещено.
Рукоятки молотков, зубил и т.п. должны иметь по всей длине в сечении овальную форму, быть гладкими, не иметь трещин и к свободному концу рукоятки должны утолщаться (кроме кувалд) – для предотвращения выскальзывания рукоятки из рук работника при взмахах и ударах инструментом.
У кувалд рукоятка к свободному концу должна несколько утоньшаться; кувалда должна насаживаться на рукоятку в сторону утолщенного конца без клиньев.
Ось рукоятки должна быть строго перпендикулярна к продольной оси инструмента. Клинья для укрепления инструмента на рукоятке должны изготавливаться из мягкой стали; они должны иметь насечки (ерши). При забивании клиньев в рукоятки молотков они должны удерживаться клещами.
5.4.4. Не разрешается работать с инструментом, рукоятки которого посажены на заостренные концы (напильники, шаберы и др.) без металлических бандажных колец.
5.4.5. Рукоятки (черенки) лопат должны изготавливаться из древесины без сучков и косослоя или из синтетических материалов и надежно закрепляться в держателях, причем часть рукоятки, выступающую из держателя, необходимо срезать наклонно к поверхности лопаты.
5.4.6. Ломы должны быть прямыми с оттянутыми и заостренными концами.
5.4.7. Инструмент ударного действия (зубила, крейцмейсели, бородки, просечки, керны и др.) должен иметь гладкую затылочную часть без трещин, заусенцев, наклепа и скосов, и на его рабочем конце не должно быть повреждений. Длина инструмента ударного действия должна быть не менее 150 мм.
Угол заострения рабочей части зубила должен соответствовать обрабатываемому материалу.
Этот угол должен равняться:
– 70° – для рубки чугуна и бронзы;
– 60° – для рубки стали средней твердости;
– 45° – для рубки меди и латуни;
– 35° – для рубки алюминия и цинка.
Средняя часть зубила должна иметь овальное или многогранное сечение без острых ребер и заусенцев на боковых гранях, ударная – форму срезанного конуса.
Поверхностная твердость рабочей части зубила для выполнения кузнечных работ на длине 30 мм должна быть:
– от 54 до 58 HRC – для холодной рубки;
– от 50 до 55 HRC – для горячей рубки.
Твердость ударяемой части на длине 20 мм должна быть от 30 до 40 HRC.
5.4.8. При выполнении работ с применением клиньев или зубил с помощью кувалд работники должны использовать клинодержатели с рукояткой длиной не менее 0,7 м.
5.4.9. При работе с применением инструмента ударного действия работники должны пользоваться защитными очками – для предотвращение попадания в глаза твердых частиц, отлетающих от инструмента.
5.4.10. При использовании клещей необходимо применять кольца, размеры которых должны соответствовать размерам обрабатываемых заготовок. С внутренней стороны ручек клещей должен быть упор – для предотвращения сдавливания пальцев руки работника.
Поверхности металлических ручек клещей должны быть гладкими (без вмятин, зазубрин и заусенцев) и очищенными от окалины.
5.4.11. Работники должны работать отверткой, у которой ширина рабочей части (лопатки) отвечает размеру шлица в головке шурупа или винта.
5.4.12. Размеры зева (захвата) гаечных ключей не должны превышать размеры головок болтов (граней гаек) более чем на 0,3 мм.
Запрещается применять подкладки при зазоре между плоскостями губок и головок болтов или гаек, превышающем допустимый.
Рабочие поверхности гаечных ключей не должны иметь сбитых скосов, а рукоятки – заусенцев. На рукоятке ключа должен указываться его размер.
При откручивании и закручивании гаек и болтов в случае необходимости следует применять ключи с длинными рукоятками; удлинять рукоятки ключей допускается только дополнительными рычагами типа "звездочка". Не разрешается применять для удлинения гаечных ключей дополнительные рычаги, другие ключи или трубы.
5.4.13. Инструмент на рабочем месте необходимо размещать так, чтобы исключалась возможность его скатывания или падения.
Запрещается класть инструмент на перила ограждений или на неогражденный край площадки лесов, подмостей, а также вблизи открытых люков, колодцев и т.п.
5.4.14. Во время перемещения или транспортировки инструмента с острыми частями эти части должны быть защищены.
5.4.15. Весь ручной слесарно-кузнечный инструмент (как находящийся в инструментальной кладовой, так и выданный на руки) должен периодически, но не реже 1 раза в квартал, осматриваться ответственными инженерно-техническими работниками, назначенными распоряжением по подразделению, и при выявлении неисправностей изыматься из эксплуатации.
5.5. Требования к пневматическому инструменту и к выполнению работ с его применением
5.5.1. К работам с пневматическим инструментом в соответствии с ДНАОП 0.03.-8.07-94 "Перечень тяжелых работ и работ с вредными и опасными условиями труда, на которых запрещается применение труда несовершеннолетних" должны допускаться работники, прошедшие производственное обучение и проверку знаний по вопросам охраны труда в соответствии с ДНАОП 0.00-4.12-99 "Типовое положение об обучении по вопросам охраны труда".
5.5.2. Рабочая часть пневматического инструмента должна быть правильно заточена и не должна иметь повреждений, трещин, выбоин и заусенцев. Боковые грани инструмента не должны иметь острых ребер; хвостовик инструмента должен быть ровным, не иметь скосов и трещин, соответствовать размерам втулки, быть плотно пригнанным и правильно центрированным – для предотвращения самопроизвольного выпадения.
Запрещается работать с пневматическим инструментом при наличии люфта во втулке или применять подкладки (заклинивать) инструмент.
5.5.3. Клапан включения пневматического инструмента должен легко и быстро, без применения усилия, открываться и закрываться и не пропускать воздух в закрытом положении; этот клапан должен быть отрегулирован до начала работы пневматического инструмента.
5.5.4. Для пневматического инструмента необходимо применять неповрежденные гибкие шланги, которые должны присоединяться к инструменту и соединяться между собою с помощью ниппелей или штуцеров и стяжных хомутов; не разрешается закреплять шланги проволокой.
Места присоединения воздушных шлангов к пневматическому инструменту, трубопроводу и места соединения шлангов между собою не должны пропускать воздух.
5.5.5. Перед присоединением гибкого шланга к пневматическому инструменту воздушную магистраль необходимо продуть, а после присоединения шланга к магистрали необходимо продуть также и гибкий шланг, свободный конец которого перед продувкой должен быть закреплен. Инструмент должен присоединяться к шлангу после прочистки сетки в футорке.
5.5.6. На воздухоподводящем трубопроводе должна быть запорная арматура.
Подсоединение шланга к магистрали и к инструменту, а также его отсоединение необходимо выполнять при перекрытой арматуре.
Гибкий шланг должен быть размещен так, чтобы исключалась возможность его случайного повреждения или наезда на него транспорта.
5.5.7. Не допускается при выполнении работ натягивать и перегибать шланги пневматического инструмента, а также пересекать их тросами, кабелями и рукавами газосварки.
5.5.8. Воздух к пневматическому инструменту необходимо подавать только после установки его в рабочее положение. Работа инструмента вхолостую допускается только при его опробовании – перед началом выполнения работ или при проведении ремонта.
5.5.9. Работать пневматическим инструментом ударного действия необходимо в защитных очках и с использованием рукавиц.
5.5.10. Запрещается работать с пневматическим инструментом с приставных лестниц.
5.5.11. Исправлять, регулировать и менять рабочую часть инструмента разрешается только при условии отсутствия в гибком шланге сжатого воздуха.
5.5.12. Работать с пневматическим инструментом необходимо с применением средств виброзащиты и управления, а также с применением глушителя шума.
Работники, выполняющие работу с пневматическим инструментом в зоне повышенного шума, должны использовать средства индивидуальной защиты (противошумные наушники, противошумные вкладыши типа "беруши" и антифоны).
5.5.13. Работать с пневматическим инструментом ударного действия разрешается с применением устройств, предотвращающих самопроизвольный вылет рабочей части инструмента при холостых ударах.
5.5.14. Запрещается при выполнении работ с пневматическим инструментом держать его за рабочую часть.
Нажим на пневматический инструмент необходимо осуществлять плавным постепенным усилием.
5.5.15. Переносить пневматический инструмент разрешается только за рукоятку; использовать шланг или рабочую часть пневматического инструмента для его перемещения запрещается.
5.5.16. Во время перерывов в работе, в случае обрыва или повреждения шлангов или пневматического инструмента необходимо немедленно прекратить доступ к нему сжатого воздуха (перекрыть запорную арматуру).
5.5.17. Гибкие шланги к пневматическому инструменту необходимо хранить в закрытом помещении при плюсовой температуре воздуха.
5.5.18. Рабочие части пневматических шлифовальных машин, пил и рубанков должны иметь защитное ограждение.
5.5.19. Пневматический инструмент, независимо от условий его работы и исправности, необходимо периодически, не реже 1 раза в 6 мес., разбирать, промывать, смазывать его детали, роторные лопатки – заправлять, а обнаруженные при осмотре поврежденные или сильно изношенные части – заменять новыми. После сборки инструмента необходимо проводить регулировку частоты вращение шпинделя на соответствие паспортным данным, а также в течение 5 мин проверять его работу на холостом ходу.
После проведения вышеуказанных работ, в случае положительных результатов испытания, необходимо сделать запись об исправности инструмента в журнале (форма журнала произвольная).
5.5.20. Вибрационные параметры, которые должны определяться в соответствии с ГОСТ 16519, ГОСТ 16844 и по стандартам на конкретные виды инструмента и заноситься в паспорт инструмента, а также шумовые характеристики пневматического инструмента необходимо контролировать после его ремонта, во время проведения которого инструмент разбирался.
При проведении испытаний после ремонта пневматического инструмента уровень звуковой мощности испытываемого инструмента не должен более чем на 6 дБ превышать уровень помех стационарного шумового фона.
6. Работы, выполняемые с применением грузоподъемных механизмов, грузозахватных органов и приспособлений
6.1. Общие требования
6.1.1. Грузоподъемные механизмы (тали, лебедки), съемные грузозахватные органы (крюки, грейферы), съёмные грузозахватные приспособления (стропы, захваты, траверсы и т. п.) и тару необходимо содержать и эксплуатировать в соответствии с ДНАОП 0.00-1.03-93 "Правила устройства и безопасной эксплуатации грузоподъемных кранов" и настоящими Правилами.
6.1.2. Грузоподъемные механизмы (лебедки, тали, кошки, блоки, полиспасты и т. п.), находящиеся в эксплуатации, должны иметь регистрационный или инвентарный номер (если механизм не подлежит регистрации в Госнадзорохрантруда), обозначение грузоподъемности и даты проведения следующего испытания.
Съемные грузозахватные приспособления должны иметь клеймо или прочно закрепленную металлическую бирку с обозначением номера, грузоподъемности и даты проведения следующего испытания.
6.1.3. К управлению грузоподъемными механизмами и грузоподъемными машинами и к обслуживанию их, к строповке грузов и к выполнению такелажных работ должны допускаться работники не моложе 18 лет, специально обученные и аттестованные в соответствии с требованиями ДНАОП 0.00-1.03-93 "Правила устройства и безопасной эксплуатации грузоподъемных кранов" и имеющие об этом запись в удостоверении о проверке знаний.
Работники основных профессий, которые по роду выполняемой работы связаны с эксплуатацией грузоподъемных механизмов и грузоподъемных машин, управляемых с пола, и с подвешиванием груза на крюк машины или механизма, должны знать смежную профессию по специальной программе.
Подготовка и аттестация машинистов кранов, их помощников, стропальщиков, слесарей и электромонтеров должна проводиться в соответствии с требованиями пункта 7.59 ДНАОП 0.00-1.03-93 "Правила устройства и безопасной эксплуатации грузоподъемных кранов".
Ремонт и обслуживание электрооборудования грузоподъемных механизмов должны проводить электротехнические работники, имеющие по электробезопасности группу не ниже III.
6.1.4. Место установки грузоподъемных механизмов и режим их работы должны соответствовать проекту проведения работ (ППР) на монтаж или ремонт оборудования.
Место работы грузоподъемного механизма должно определяться таким образом, чтобы было обеспечено пространство, необходимое для осмотра рабочей зоны и для маневрирования.
6.1.5. Вновь установленные грузоподъемные механизмы до пуска их в работу, а также такелажные схемы для перемещения грузов в целом должны проходить полное техническое освидетельствование, включающее осмотр, статические и динамические испытания.
При подъёме опор воздушных линий электропередачи допускается только осматривать такелажную схему и проводить статическое испытание её поднимаемым грузом.
6.1.6. Техническое освидетельствование грузоподъемных механизмов, грузозахватных органов, приспособлений, тары должен проводить инженерно-технический работник, осуществляющий на предприятии надзор за грузоподъемными машинами и механизмами, при участии работника, ответственного за их исправное состояние.
Проверять правильность запасовки и надежность закрепления канатов, а также обтяжки рабочим грузом после смены или перепасовки канатов должен работник, ответственный за содержание грузоподъемных машин и механизмов в исправном состоянии.
Грузоподъемные механизмы, поступившие на место эксплуатации в собранном виде, при наличии документа об их полном техническом освидетельствовании на заводе-изготовителе допускаются к эксплуатации на срок не более 12 мес. с предварительным осмотром (без проведения испытаний). В этом случае дату и результаты технического освидетельствования необходимо записать в паспорт механизма.
6.1.7. Каждый грузоподъемный механизм при техническом освидетельствовании должен проходить статическое испытание в течение 10 мин грузом, на 25 % превышающим его номинальную грузоподъемность, – с целью проверки прочности механизма и отдельных его элементов. Грузоподъемный механизм, выдержавший статическое испытание, подлежит динамическому испытанию.
Динамическое испытание грузоподъемного механизма должно проводиться грузом, на 10 % превышающим номинальную грузоподъемность механизма, – с целью проверки действия его тормозов.
Коэффициент запаса торможения тормоза, в зависимости от режима работы и рода привода грузоподъемного механизма, должен быть от 1,5 до 2,5.
Допускается проводить динамическое испытание рабочим грузом с повторным его подъёмом и опусканием.
Во всех случаях при обнаружении дефектов при проведении испытаний грузоподъемного механизма испытание необходимо прекратить и после устранения дефектов провести вновь.
6.1.8. Грузоподъемные механизмы (ручные и электрические тали, лебедки для подъёма людей и т. п.), подлежащие регистрации в Госнадзорохрантруда, должны проходить периодическое техническое освидетельствование в сроки, указанные в ДНАОП 0.00-1.03-93 "Правила устройства и безопасной эксплуатации грузоподъемных кранов".
Грузоподъемные механизмы, в том числе электро- и автопогрузчики, гидроэлектропогрузчики, штабелеры и т. п., не подлежащие регистрации в Госнадзорохрантруда, должны проходить периодическое техническое освидетельствование:
– полное – не реже 1 раза в 3 года, а механизмы, предназначенные для подъёма людей (лебедки, подъемники, вышки и т. п.), – не реже 1 раза в 12 мес.;
– частичное – не реже 1 раза в 12 мес.
При полном техническом освидетельствовании должны проводиться осмотр, статическое и динамическое испытания, а при частичном – только осмотр.
Самоходные вышки и подъемники, установленные на базе автомобилей, гусеничных и колесных тракторов, должны проходить техническое освидетельствование перед началом эксплуатации, периодически, а также после ремонта – в соответствии с требованиями, указанными в технической документации завода-изготовителя на данный вид вышки или подъемника. Кроме того, ежедневно перед началом выполнения работ необходимо проводить испытания – в соответствии с требованиями инструкции по эксплуатации на данный вид вышки или подъемника.
Внеочередное полное техническое освидетельствование грузоподъемных механизмов необходимо проводить после реконструкции их, ремонта металлических конструкций с заменой расчетных элементов или узлов, капитального ремонта или замены механизма, крюка и т. п.
После замены изношенных грузовых или других канатов, а также во всех случаях перепасовки канатов необходимо проводить проверку правильности запасовки и надежности закрепления концов каната, а также обтяжку канатов рабочим грузом.
На самоходных вышках и подъемниках, прошедших техническое освидетельствование, должны наноситься даты проведенного технического, а также очередного периодического освидетельствования.
6.1.9. Съемные грузозахватные приспособления должны проходить:
– техническое освидетельствование – на заводе-изготовителе, а после ремонта – на предприятии, где они ремонтировались. При проведении технического освидетельствования съемные грузозахватные приспособления необходимо осматривать и испытывать в течение 10 мин нагрузкой, на 25 % превышающей их номинальную грузоподъемность;
– осмотр – перед выдачей грузозахватных устройств в работу, а также в процессе эксплуатации в установленные сроки, но не реже чем через 6 мес. – для траверс; через 1 мес. – для тары, клещей и других захватов; через 10 дней – для стропов, – за исключением редко используемых. Редко используемые съемные грузозахватные приспособления должны осматриваться перед выдачей их в работу.
Тару для перемещения грузоподъемными машинами мелкоштучных, сыпучих и других грузов после изготовления ее и перед применением необходимо осматривать в соответствии с утвержденной руководством предприятия инструкцией, определяющей порядок проведения осмотра, мероприятия по устранению обнаруженных повреждений, а также состав работников, которые должны выполнять эти работы.
Выявленные при техническом освидетельствовании и осмотре поврежденные съемные грузозахватные приспособления и тара должны отбраковываться и изыматься из эксплуатации.
Результаты осмотра съемных грузозахватных приспособлений должен записывать работник, ответственный за содержание этих приспособлений в исправном состоянии, в "Журнал учета и осмотра такелажных средств, механизмов и приспособлений", форма которого приведена в приложении 5 к настоящим Правилам, тары – в "Журнал периодического осмотра тары", форма которого приведена в приложении 1 к настоящим Правилам.
6.1.10. Разрешение на пуск в работу грузоподъемных механизмов, не подлежащих регистрации в Госнадзорохрантруда, а также на применение вновь изготовленных съемных грузозахватных приспособлений и тары должен выдавать: или инженерно-технический работник по надзору за грузоподъемными машинами и механизмами, или инженерно-технический работник, выполняющий его обязанности, или другой инженерно-технический работник. Разрешение должно выдаваться на основании документации завода-изготовителя и результатов технического освидетельствования.
6.1.11. Работник, проводивший техническое освидетельствование грузоподъемного механизма, должен записывать дату и результаты освидетельствования, а также сведения о выполненных ремонтах в "Журнал учета и осмотра такелажных средств, механизмов и приспособлений" по форме, приведенной в приложении 5 к настоящим Правилам.
6.1.12. Подавать электрическое напряжение на грузоподъемный механизм от внешней электрической сети необходимо с помощью вводного устройства, имеющего ручное и дистанционное управление для снятия напряжения.
6.1.13. Крюки, с помощью которых должны подниматься тяжеловесные грузы (массой более 3 т), должны быть вращающимися на закрытых шариковых опорах, – за исключением крюков специального назначения.
Крюки должны быть оборудованы предохранительными замками, – для предотвращения самопроизвольного выпадения съемного грузозахватного устройства.
6.1.14. Массу подлежащих подъёму грузов необходимо определять до подъёма их. Нагрузка на грузоподъемные механизмы и съемные грузозахватные приспособления не должна превышать их грузоподъемности.
6.1.15. Для грузов, имеющих специальные устройства (петли, цапфы, рымы), предназначенные для подъёма таких грузов в различных положениях, необходимо разрабатывать схемы строповки.
Для грузов, не имеющих специальных устройств (петель, цапф, рым), необходимо разрабатывать способы правильной строповки грузов, которые должны указываться в ППР.
Наиболее часто встречающиеся схемы строповки грузов должны вывешиваться на рабочих местах или выдаваться на руки стропальщикам и крановщикам.
Поднимать груз, на который не разработаны схемы строповки, необходимо в присутствия и под непосредственным руководством работника, ответственного за безопасное выполнение работ по перемещению грузов.
6.1.16. Грузы, подвешиваемые к крюку грузоподъемного механизма, необходимо надежно обвязывать канатами или калиброванными цепями – для обеспечения устойчивого положения груза при его перемещении, а также для предотвращения при выполнении этой работы падения отдельных частей этого груза (досок, бревен, прутков, труб и т. п.).
Стропить длинномерные грузы (длиной более 6 м) необходимо не менее чем в двух местах.
Для обвязки груза должны применяться чалочные приспособления, соответствующие массе поднимаемого груза, с учетом количества ветвей каната и угла наклона их к вертикали.
В этом случае канаты или цепи чалочных приспособлений необходимо накладывать на поднимаемый груз равномерно, без узлов и перекруток; если поднимаемый груз имеет острые грани, под канат или цепь необходимо подложить подкладки – для предотвращения повреждения строп.
Запрещается строповка поднимаемого груз за выступы, штурвалы, штуцера и другие устройства, не рассчитанные для его подъёма.
6.1.17. Не разрешается оставлять в местах проведения работ отбракованные и не имеющие бирки (клейма) съемные грузозахватные приспособления, а также немаркированную и поврежденную тару.
6.1.18. Все работники, не имеющие непосредственного отношения к проводимым в опасной зоне работам по подъёму и перемещению грузов, должны быть выведены из этой зоны.
6.1.19. Все проёмы в зоне перемещения грузов должны быть закрыты или ограждены и возле них должны вывешиваться предупреждающие знаки безопасности.
6.1.20. Поднимать тяжеловесные грузы (массой более 3 т) грузоподъемными механизмами необходимо под непосредственным руководством работника, ответственного за безопасное выполнение работ по перемещению грузов кранами и механизмами.
6.1.21. Груз при его перемещении в горизонтальном направлении необходимо предварительно поднять не менее чем на 0,5 м выше предметов, которые могут встретиться на его пути.
6.1.22. Грузы разрешается опускать на заранее подготовленное место, – чтобы исключить возможность их падения, опрокидывания или сползания. Для удобства извлечения стропов из-под груза на месте его установки должны укладываться прочные подкладки.
6.1.23. Запрещается опускать грузы на перекрытия, опоры и площадки – без предварительного расчета прочности несущих конструкций, а также запрещается перегружать их сверх допустимых нагрузок.
6.1.24. Запрещается оставлять груз в подвешенном положении, а также поднимать и перемещать работников не предназначенными для этого грузоподъемными механизмами.
В случае неисправности механизма, если невозможно опустить поднятый груз, опасную зону проведения работ необходимо оградить и вывесить предупреждающие знаки безопасности "Обережно! Небезпечна зона" ("Осторожно! Опасная зона").
6.1.25. При перемещении грузов грузоподъемными механизмами освещение рабочего места должно быть достаточным для безопасного выполнения работы.
6.1.26. Грузы необходимо поднимать строго отвесно; для этого крюк грузоподъемногомеханизма необходимо устанавливать непосредственно над грузом.
Подтягивать груз по земле или по полу крюком грузоподъемного механизма при наклонном положении грузовых канатов необходимо с применением направляющих блоков, обеспечивающих вертикальное положение канатов.
Не разрешается оттягивать груз во время его подъема, перемещения и опускания, выравнивать его собственным весом работника, выполняющего работу, а также направлять канат руками при наматывании его на барабан.
6.1.27. Не разрешается при работе грузоподъемного механизма освобождать с его помощью защемленные грузом стропы, канаты или цепи, а также работать при выведенных из действия или неисправных приборах безопасности и тормозах грузоподъемного механизма.
6.1.28. Запрещается выполнять грузоподъемными механизмами следующие работы:
– поднимать примерзший, засыпанный или защемленный груз;
– поднимать грузы при наклонном положении полиспаста, у которого верхний блок имеет жесткое закрепление;
– выполнять одновременно подъем или опускание двух грузов, находящихся в непосредственной близости один от другого.
6.1.29. Поднимать груз необходимо плавно, без рывков и раскачивания, не допуская его соприкосновения с предметами, которые могут встретиться на его пути, и без закручивания строп.
Поднимать груз необходимо так: сначала его следует поднять на высоту не более 300 мм, затем 2 – 3 раза опустить на 100 мм – для проверки надежности работы тормозов, устойчивости грузоподъемного механизма, правильности строповки и равномерности натяжения стропов, и только после этого груз следует поднять на требуемую высоту.
Для исправления строповки груз необходимо опустить.
Для разворачивания при подъёме или перемещении длинномерных и тяжеловесных грузов необходимо применять оттяжки-крюки соответствующей длины.
6.1.30. Все грузоподъемные механизмы, находящиеся в эксплуатации, необходимо периодически осматривать и ремонтировать в сроки, предусмотренные системой планово-предупредительных ремонтов, с записью результатов в "Журнал учета и осмотра такелажных средств, механизмов и приспособлений" по форме, приведенной в приложении 5 к настоящим Правилам.
Работник, ответственный за содержание грузоподъемных машин и механизмов в исправном состоянии, обязан обеспечить своевременное устранение выявленных неисправностей.
6.2. Требования к лебедкам и к выполнению работ с их применением
6.2.1. Место установки лебедок, способ закрепления их, а также размещение блоков должны указываться в ППР и удовлетворять требованиям ДНАОП 0.00-1.03-93 "Правила устройства и безопасной эксплуатации грузоподъемных кранов".
Место установки лебедок необходимо выбирать с соблюдением следующих требований:
– лебедка должна находиться вне зоны выполнения работ по подъему и перемещению грузов;
– место установки лебедки должно обеспечивать обслуживающим её работникам хорошее наблюдение за поднимаемым грузом;
– должны обеспечиваться необходимое закрепление каната и правильное его направление. Канат, идущий к лебедке, не должен пересекать дороги и проходы для людей. В случае, когда такое пересечение неизбежно, в местах прохода или проезда необходимо установить ограждения с предупреждающими знаками безопасности "Обережно! Небезпечна зона!" ("Осторожно! Опасная зона") и выставить наблюдающего.
При установке лебедки в помещении ее раму необходимо закрепить стальным канатом: или за колонну здания, или за железобетонный или металлический ригель перекрытия здания, или за кирпичную стену. Диаметр и количество ветвей каната должны рассчитываться, исходя из грузоподъемности лебедки с коэффициентом запаса прочности не менее 6. Конец обвязывающего каната необходимо закреплять с помощью зажимов, количество которых определяется при проектировании, но их должно быть не менее трех. Шаг расположения зажимов и длина свободного конца каната от последнего зажима должны составлять не менее шести диаметров каната.
При установке лебедок на земле они должны закрепляться: или за якорь, или с упором и противовесом.
Устойчивость лебедки необходимо проверять расчетом.
Запрещается приваривать раму лебедки.
6.2.2. Лебедки, применяемые для подъёма и опускания передвижных лесов и люлек, должны соответствовать требованиям ДНАОП 0.00-1.03-93 "Правила устройства и безопасной эксплуатации грузоподъемных кранов". Они должны укрепляться на фундаменте или на раме лебедки должен быть крепко закрепленный к ней балласт – для обеспечения устойчивости лебедки при двойной рабочей нагрузке.
6.2.3. Запрещается, независимо от места установки лебедки – в здании или вне его, приваривать ручные рычажные лебедки к площадкам обслуживания оборудования, а также закреплять их к трубопроводам и их подвескам.
6.2.4. Не допускается выполнять работы лебедками, при осмотре которых обнаружены дефекты.
Должны изыматься из дальнейшей эксплуатации и заменяться исправными следующие детали лебедок:
– чугунные барабаны – при наличии трещин или отбитых краев реборд. В стальных барабанах допускается заваривать трещины и вставлять отбитые части реборд с соответствующей обработкой кромок трещин и места вставки этих частей;
– шестерни – при отсутствии части зубьев (одного и более) или при наличии трещин в любом месте (заваривание трещин не допускается);
– шестерни лебедок с ручным приводом – при износе зубьев более 20 % их первоначальной толщины и шестерни лебедок с электрическим приводом – при износе зубьев более допустимого. Запрещается наваривать и заваривать зубья;
– деформированные корпуса ручных рычажных лебедок, неисправные предохранительные детали, изношенные трущиеся детали тяговых механизмов (сжимы – желобчатые пазы и цапфы), а также деформированные фигурные вырезы серег и крюки;
– подшипники – при наличии трещин или отбитых краёв, а также втулки подшипников – при наличии в них зазора более 0,6 мм – для лебедок с электрическим приводом, а также при износе более 2 % первоначального диаметра – для лебедок с ручным приводом;
– поломанные детали тормоза и детали тормоза лебедок с электрическим приводом – при наличии в них разработанных отверстий, которые увеличивают "мертвый" ход более чем на 10 %. Размер "мертвого" хода должен проверяться при зажатых колодках;
– валы и оси лебедок с электрическим приводом – при наличии в них разработанных шпоночных канавок, раковин, наплывов, расслоений, трещин, а также при наличии зазора более 0,6 мм (после устранения задиров на шейках);
– валы лебедок с ручным приводом – при износе шеек более 4 % первоначального диаметра, криволинейности – более 3 мм на 1 м длины;
– храповики – при отсутствии зубьев или при наличии трещин;
– собачки – при наличии выщербленных мест на их упорной части;
– эластичные муфты – при наличии у них сломанных пальцев, изношенного тормозного шкива и задиров на тормозной поверхности;
– тормозные колодки – при наличии у них обкладок, изношенных более чем на 0,5 их первоначальной толщины.
6.2.5. Перед вводом в эксплуатацию, после капитального ремонта и периодически, через каждые 12 мес., лебедки должны проходить техническое освидетельствование в соответствии с требованиями ДНАОП 0.00-1.03-93 "Правила устройства и безопасной эксплуатации грузоподъемных кранов".
При проведении технического освидетельствования необходимо измерять сопротивление изоляции электрооборудования мегомметром на напряжение 1000 В, которое должно быть не менее 0,5 МОм, а также необходимо проверять надежность заземления корпусов.
Не допускается к дальнейшей эксплуатации и подлежит высушиванию электрооборудование лебедок, сопротивление изоляцию которых менее 0,5 МОм.
6.2.6. При техническом освидетельствовании испытание лебедок должно проводиться на специальном испытательном стенде, а при его отсутствии – на ровной специально оборудованной площадке, позволяющей провернуть под нагрузкой барабан лебедки не менее чем на два оборота.
При этом испытательная нагрузка лебедок должна соответствовать нагрузке, указанной в пункте 6.1.7 настоящих Правил.
6.2.7. Не подлежат динамическому испытанию тяговые лебедки с ручным и электрическим приводами.
6.2.8. При проведении статического испытания лебедок с электрическим и ручным приводом канат должен быть на последнем слое навивки. Для получения диаметра барабана, соответствующего последнему слою навивки, допускается обкладывать его деревянными брусками. Увеличенный диаметр барабана должен быть: D + 100 мм – для лебедок с тремя слоями навивки и D + 200 мм – для лебедок с пятью слоями.
Для испытания лебедки на барабане должны быть оставлены не менее пяти витков закрепленного на нем каната; оставшийся канат необходимо размотать и пропустить через отводные блоки испытательной схемы. Свободный конец каната следует закрепить к испытательному грузу. После этого груз необходимо поднять на высоту 100 мм и выдержать в таком положении в течение 10 мин.
Статическое испытание лебедок можно проводить также с помощью проверенного исправного динамометра, поддерживая в течение 10 мин соответствующую постоянную нагрузку.
При испытании лебедки с ручным рычажным приводом её можно подвешивать к треноге или к какой-либо другой конструкции, выдерживающей двойную нагрузку лебедки.
Лебедка считается выдержавшей испытание, если оставленный подвешенным испытательный груз самопроизвольно не опускается.
6.2.9. Статическое испытание лебедок, предназначенных для подъёма людей, должно проводиться нагрузкой, в 1,5 раза превышающей их грузоподъемность.
6.2.10. Динамическое испытание лебедок заключается в повторных подъёмах и опусканиях испытательного груза на высоту не менее 1 м. Такое испытание необходимо проводить не менее 6 раз. Подъём груза необходимо осуществлять в первом положении контроллера.
При проведении испытаний поднимаемый груз останавливают и проверяют отсутствие самопроизвольного его опускания. Затем груз поднимают из того положения, в котором он был остановлен (не опуская его на землю).
Тормозную систему лебедки проверяют остановкой груза на спуске. У лебедок с электрическим приводом груз опускают как с помощью электродвигателя, так и растормаживанием барабана при отключенном электродвигателе, проверяя при проведении этой операции надежность работы тормозов, отсутствие нагрева тормозных колодок выше 60 °С и всех подшипников выше 70 °С, отсутствие ненормального шума в работе зубчатых передач, подтёков и выбрасывания масла из подшипников, а также других дефектов.
6.2.11. При обнаружении дефектов при проведении испытаний лебедок испытание необходимо провести вновь после устранения этих дефектов.
Если при проведении испытаний не обнаружено неисправностей, лебедка считается выдержавшей испытания.
6.2.12. Работа с применением лебедок должна выполняться при условии:
– надежного закрепления лебедок на рабочем месте;
– исправности тормозов;
– исправности электропривода;
– наличия ограждения привода;
– надежного закрепления каната на барабане и правильной его навивке (без появления петель, послабления каната и т. п.).
Управлять лебедкой вручную необходимо с применением рукавиц.
Ремонтировать или подтягивать ослабленные соединения разрешается только после вывода лебедки из работы.
6.2.13. Металлические части лебедок необходимо заземлять "под болт" – для лебедок с электрическим приводом; для лебедок с ручным приводом такое заземление всех металлических частей необходимо выполнять в случае проведения работ на воздушных линиях электропередачи, находящихся под напряжением.
Запрещается приваривать заземление к раме лебедки.
6.2.14. Канат лебедки при правильной навивке должен ложиться на барабан ровными плотными рядами; расстояние между верхним слоем навитого каната и наружным диаметром реборды должно быть не менее двух диаметров каната. В нижнем положении грузозахватного органа лебедки на барабане должно оставаться не менее 1,5 витка каната, не считая витков, находящихся под зажимным устройством.
Для уменьшения опрокидывающего момента, действующего на лебедку, канат должен подходить к барабану снизу. Кроме того, положение набегающей на барабан ветви каната должно быть, по возможности, близко к горизонтальному положению и не более чем на 2° отклоняться от плоскости, перпендикулярной к оси барабана. Для этого, в случае необходимости, на подходах к лебедке канат должен пропускаться через один или несколько отводных блоков. Расстояние от оси барабана до оси ближайшего к лебедке отводного блока должно составлять не менее 20 длин барабана.
6.2.15. При подъёме грузов одновременно двумя лебедками конструкции лебедок необходимо подбирать так, чтобы скорости наматывания канатов на барабаны были одинаковыми. Поднимать груз необходимо под наблюдением работника, ответственного за безопасное выполнение работ по перемещению грузов, и при наличии ППР.
6.2.16. Канаты в местах присоединения их к люльке и барабану лебедки необходимо прочно закрепить. Движение канатов при подъеме и опускании люлек должно быть свободным.
Не допускается трение канатов о выступающие конструкции. Люльки, с которых работу не выполняют, необходимо опустить на землю.
6.2.17. Лебедки с ручным приводом должны быть оборудованы: или безопасными рукоятками, находящимися в зацеплении с приводным валом только при условии вращения их в сторону подъёма, или автоматически действующим грузоупорным тормозом, исключающим возможность самопроизвольного опускания груза.
Лебедки, не оборудованные автоматически действующим тормозом или безопасной рукояткой, разрешается применять только в качестве тяговых, что должно указываться в паспорте лебедки.
Рукоятки лебедок с ручным приводом должны быть оборудованы свободно проворачивающимися втулками.
6.2.18. При выполнении работ с применением лебедок с ручным приводом количество обслуживающих лебедку работников необходимо определять, руководствуясь конкретными условиями работы и расчетным усилием, которое работник, выполняющий работу с применением лебедки, должен прикладывать к рукоятке.
Усилие, прикладываемое к рукоятке одним работником, не должно превышать 120 Н (12 кгс); при кратковременной работе разрешается увеличивать усилие до 200 Н (20 кгс).
6.2.19. Не разрешается при выполнении работ с применением лебедок с ручным рычажным приводом:
– находиться в плоскости качания рычага и под поднимаемым грузом;
– применять рычаг, имеющий бóльшую длину, чем предусмотрено техническими данными лебедки;
– переводить рычаг из одного крайнего положения в другое рывками.
При выполнении работ перемещаемый груз должен надежно закрепляться к крюку. Движение рукоятки обратного хода должно быть плавным, без рывков и заеданий; тяговый механизм и канат все время должны находиться на одной прямой.
6.2.20. Не разрешается выполнять работу с применением рычажных лебедок при проскальзывании каната в случае изменения направления движения рукоятки прямого хода, при свободном прохождении его в сжимах тягового механизма, а также при срезке предохранительных штифтов или фиксаторов.
6.2.21. Изменять ход с прямого на обратный при поднимании груза лебедками с электрическим приводом необходимо только после остановки лебедки, а при подходе груза к крайним положениям – после замедления хода.
При обнаружении дефектов в электроприводе (сильный нагрев электродвигателя, катушек электромагнита, резисторов, подшипников; сильное искрение щеток электродвигателя или появление дыма, запаха гари; ощущение действия тока при соприкосновении с деталями лебедки и т. п.) необходимо немедленно прекратить работу и отключить электродвигатели лебедки от сети питания.
6.2.22. Лебедки, предназначенные для подъёма людей, должны иметь конструкцию и схему управления в соответствии с требованиями ДНАОП 0.00-1.03-93 "Правила устройства и безопасной эксплуатации грузоподъемных кранов".
6.2.23. При эксплуатации лебедок необходимо своевременно смазывать все трущиеся части, – чтобы предотвратить преждевременный износ деталей лебедки.
6.2.24. Перед допуском к работе с применением лебедки необходимо проверить:
– наличие непросроченной даты технического освидетельствования лебедки;
– соответствие указанным в ППР: места установки, способа закрепления лебедки и размещения блоков;
– надежность закрепления каната к барабану лебедки, отсутствие косого натяжения и состояние каната, правильность расположения каната на блоках;
– исправность тормозов и электропривода;
– наличие ограждения привода.
Во время выполнения работы необходимо следить за исправностью лебедки, за правильным наматыванием каната лебедки на барабан, не допуская его соскальзывания на вал лебедки.
6.3. Требования к выполнению работ с применением талей и кошек
6.3.1. Корпуса электрооборудования талей необходимо заземлять.
Корпус кнопочного аппарата управления тали, управляемой с пола, должен быть: или выполнен из изоляционного материала, или заземлен не менее чем двумя проводниками. В качестве одного из заземляющих проводников можно использовать тросик, на котором подвешен кнопочный аппарат.
6.3.2. Пусковые аппараты ручного управления талями необходимо подвешивать на стальных тросиках такой длины, чтобы можно было управлять механизмом, находясь на безопасном расстоянии от поднимаемого груза.
При расположении аппарата управления ниже 0,5 м от уровня пола его необходимо подвешивать на крючок, укрепленный на тросике на высоте 1 – 1,5 м.
6.3.3. Механизм подъёма ручных талей необходимо оборудовать автоматическим грузоупорным тормозом. Тормоз должен обеспечивать плавное опускание груза при вращения тягового колеса под действием силы тяги и автоматическую остановку груза при прекращении действия силы тяги.
6.3.4. Запрещается закреплять ручные тали к трубопроводам и к их подвескам.
6.3.5. Электрические тали необходимо оборудовать концевыми выключателями – для обеспечения автоматической остановки механизма подъёма грузозахватного органа. Концевые выключатели должны устанавливаться так, чтобы при подъёме без груза после остановки грузозахватного органа зазор между ним и упором был не менее 50 мм.
Запрещается при подъёме груза электрическими талями доводить обойму крюка до концевого выключателя и использовать его для автоматической остановки.
6.3.6. Электрические тали с двухскоростным механизмом передвижения необходимо оборудовать тормозом на механизме передвижения.
Электрические тали грузоподъемностью от 1,0 до 5,0 т необходимо оборудовать двумя тормозами на механизме подъёма. Коэффициент запаса торможения электромагнитного тормоза должен быть не менее 1,25, а грузоупорного – 1,1.
На концах монорельса должны быть упоры, а на корпусе тали – упругие буфера – для предотвращение вывода электрической тали за пределы монорельсового пути.
6.3.7. Техническое состояние талей и кошек необходимо проверять перед каждым применением их.
Все трущиеся части ручных и электрических талей, а также кошек необходимо смазывать не реже 1 раза в месяц.
6.3.8. Техническое освидетельствование талей и кошек и сроки его проведения должны соответствовать тем же требованиям, которые предъявляются к грузоподъемным механизмам.
6.3.9. При техническом освидетельствовании и периодическом осмотре талей необходимо обратить внимание на: их чистоту; наличие смазки; состояние цепей, канатов, зубьев шестерен и звездочек; исправность шплинтов или расклёпок на концах главной оси; надежность зацепления цепей на звездочках и закрепления каната на барабане; износ поверхности качения ходовых роликов; расстояние между ребордами роликов и крайними кромками монорельсового пути; исправность электромагнитного тормоза электрических талей и степень износа фрикционных прокладок; состояние электродвигателей, электропроводки и контактов, аппаратов управления, токоприемника и концевого выключателя; отсутствие заеданий механизма и проскальзывания цепей; уровень шума, возникающего при работе тали.
Поверхности зубьев звездочек и шестерен, а также цепи должны быть без трещин, заусенцев и вмятин; пластинчатые цепи должны быть подвижными во всех шарнирных соединениях.
6.3.10. Подлежат замене следующие детали талей и кошек:
– шейки, имеющие трещины (заваривание не допускается);
– втулки в червячном колесе и в подшипниках червяка – при наличии зазора более 1 мм;
– червячная пара – при износе зубьев более 10 % их толщины, наличии трещин в червячном колесе или при отсутствии части зубьев;
– грузовая звездочка – при срабатывании зубьев более 10 % их толщины, а также при наличии трещин;
– фрикционные прокладки – при срабатывании более чем на 0,5 их первоначальной толщины;
– грузовые и тяговые цепи – при деформации отдельных звеньев;
– деформированные крюки.
6.3.11. Перед пуском в работу, после капитального ремонта и периодически, но не реже 1 раза в год, необходимо проверять состояние изоляции электрооборудования талей мегомметром на напряжение 1000 В. Сопротивление изоляции должно быть не менее 0,5 МОм.
Подлежит сушке электрооборудование талей, имеющих изоляцию с сопротивлением менее 0,5 МОм.
6.3.12. Испытание стационарных талей и кошек необходимо проводить на месте установки их. Переносные тали при проведении испытания подвешивают к треноге или к какой-либо другой конструкции.
При статическом испытании электрических талей испытательный груз необходимо поднять крюком механизма подъёма на высоту от 200 до 300 мм и удерживать в таком положении в течение 10 мин. Груз не должен самопроизвольно опускаться.
При статическом испытании ручных талей испытательный груз необходимо поднять на высоту, обеспечивающую полный оборот грузовой звездочки, и провести трехкратное плавное перемещение тали на длину, соответствующую не менее чем одному обороту ходового ролика.
Проверке подлежит работа автоматического грузоупорного тормоза тали, обеспечивающего плавное опускание груза при вращении тягового колеса под действием силы тяги, а также свободное поворачивание нижнего крюка тали без нагрузки.
При испытании кошек с подъёмом испытательного груза, как и при испытаниях талей, также необходимо провести трехкратное плавное перемещение кошки на балке в обе стороны на расстояние, соответствующее двум полным оборотам ходовых колес. При этом ручные тали и кошки должны опираться всеми ходовыми колесами на балку; также необходимо проверить отсутствие набегания и срыва цепей.
6.3.13. Динамическое испытание ручных талей и кошек заключается в повторных подъёмах и опусканиях испытательного груза на высоту не менее 1 м – с целью проверки исправности тормозов талей, плавности работы грузовой и тяговой цепей. Такое испытание необходимо проводить не менее 6 раз.
Динамическое испытание электрических талей заключается в двукратных подъёмах испытательного груза на высоту не менее 6 м с остановкой при каждом подъёме и опускании груза не менее 5 раз.
При динамическом испытании электрических талей необходимо проверить работу механизма подъёма и тормозов, прочность конструкции тали и проходимость ее по криволинейным участкам пути.
При проверке проходимости тали по криволинейным участкам пути она должна свободно проходить по ним с наименьшим для тали радиусом закругления на дуге 90° при движении в обоих направлениях.
Для талей с высотой подъёма груза менее 6 м необходимо проводить подъём испытательного груза на полную высоту.
При наличии двух тормозов на механизме подъёма талей грузоподъемностью 1 т и более проверку их действия необходимо проводить совместно и раздельно. Проверку действия тормозов талей грузоподъемностью 0,25 т и 0,5 т необходимо проводить совместно. Если один из тормозов грузоупорный, то при проведении его испытания выбег груза при опускании не должен превышать 800 мм.
Работу ограничителей подъёма и опускания груза необходимо проверить не менее трех раз.
6.3.14. При самопроизвольном опускании испытательного груза при проведении испытаний, выявлении набеганий, пропусков и скольжения цепи по звездочке и по тяговым колесам, трещин, разрывов и деформаций тали и кошки необходимо отбраковывать и изымать из эксплуатации.
6.4. Требования к выполнению работ с применением блоков и полиспастов
6.4.1. Блоки или полиспасты, предназначенные для выполнения грузоподъемных работ, необходимо выбирать по грузоподъемности.
Для оснастки полиспастов необходимо применять блоки одинаковой грузоподъемности.
При выборе блока диаметр ручья ролика должен превышать диаметр каната на 1 – 3 мм.
6.4.2. Грузоподъемность блоков и полиспастов должна указываться: или в паспорте завода-изготовителя, или на клейме крюка, или на обойме блока, или на металлической табличке, закрепленной к внешней щеке блочной обоймы.
6.4.3. При подвешивании верхних неподвижных блоков полиспастов необходимо избегать бокового опирания обоймы верхнего блока на ригель или балку.
Не допускается перекос роликов верхнего блока относительно каната. Ролики блоков, а также крюки и петли на траверсах должны свободно прокручиваться.
6.4.4. При оснастке полиспастов должны выполняться следующие требования к месту закрепления каната:
– если количество нитей полиспаста (то есть суммарное количество роликов неподвижного и подвижного блоков) чётное, то конец каната необходимо закреплять к неподвижному блоку;
– если количество нитей полиспаста (суммарное количество роликов неподвижного и подвижного блоков) нечётное, то конец каната необходимо закреплять к подвижному блоку.
6.4.5. При сборке полиспастов и при подъёме грузов необходимо следить за тем, чтобы подвижная и неподвижная обоймы были параллельными.
Не допускается косое положение одного блока относительно другого – для предотвращения соскальзывания каната с блока.
6.4.6. Тяговый сбегающий конец каната должен направляться к лебедке так, чтобы он не выворачивал блок полиспаста и не вызывал его перекоса.
6.4.7. Отводные блоки рекомендуется применять разъемной конструкции, позволяющей запасовывать канат в блок в любом месте по его длине.
Размещать блоки необходимо так, чтобы проходящий через них тяговый конец каната не имел косого набегания на блок полиспаста, – для предотвращения его соскальзывания, что может привести к возникновению горизонтальных усилий, действующих на верхний блок полиспаста.
6.4.8. При выборе грузоподъемности отводных блоков (так же, как и при расчете чалочных канатов для привязывания их) необходимо учитывать угол между направлениями канатов.
6.4.9. Для длительного хранения блоки массой до 60 кг необходимо подвешивать за крюки, петли или скобы на прочных перекладинах, а более тяжёлые блоки – укладывать на полу на подкладках.
6.4.10. Блоки и полиспасты необходимо осматривать не реже 1 раза в 6 мес., а также перед каждым подъёмом груза, масса которого близка к грузоподъемности блока или полиспаста. Блоки и полиспасты для технического осмотра необходимо полностью разбирать.
Техническое состояние блоков и полиспастов необходимо проверять также внешним осмотром перед каждым применением их.
6.4.11. Перед применением блоков и полиспастов необходимо провести их внешний осмотр и убедиться в том, что они оснащены канатами, прошли испытание и имеют металлическую бирку с указанием номера блока или полиспаста, грузоподъемности и даты проведения следующего испытания.
Необходимо также проверить общее состояние блоков и их отдельных элементов (роликов, щек, подшипников), закрепление каната к блоку, наличие смазки роликов и вращение их на оси.
При осмотре необходимо обратить внимание на состояние внутренней поверхности зева крюка, где чаще всего могут возникнуть трещины, на состояние каната, которым оснащен полиспаст, и чистоту каналов для смазки в осях роликов.
6.4.12. Должны изыматься из дальнейшей эксплуатации и заменяться исправными следующие детали блоков и полиспастов:
– ролики, имеющие трещины, отбитые края, изношенные втулки (износ составляет 3 % и более диаметра оси), диаметр отверстия, превышающий первоначальный более чем на 5 %, а также износ радиуса ручья более 40 % его первоначального радиуса. При достаточной толщине стенки и равномерном износе втулки по окружности её можно оставить в эксплуатации – при условии замены оси осью большего диаметра;
– крюки, имеющие: трещины, деформацию, износ от стропового каната опорной поверхности в виде канавки глубиной более 10 % первоначальной высоты сечения крюка;
– траверсы, имеющие трещины и износ шеек более 10 % первоначального диаметра;
– оси блоков, имеющие износ, превышающий 5 % по диаметру. Если ось имеет равномерный износ по диаметру и не имеет неровностей на поверхности, ее можно оставить в эксплуатации – при условии замены втулок роликов;
– грузовые блоки, имеющие трещины на несущих планках, разработанные отверстия для осей и траверс.
6.4.13. Для проверки прочности блоков и полиспастов они должны не реже 1 раза в 12 мес. проходить статическое испытание грузом, масса которого на 25 % превышает их номинальную грузоподъемность.
При проведении такого испытания испытательный груз необходимо поднять на высоту от 100 до 200 мм и выдержать в этом положении в течение 10 мин, после чего осмотром проверить состояние блоков и полиспастов.
Статическое испытание блоков и полиспастов можно проводить также с помощью проверенного исправного динамометра, поддерживая в течение 10 мин необходимую постоянную нагрузку.
6.4.14. Для проведения испытаний блок или полиспаст необходимо оснастить канатом соответствующей грузоподъемности, который должен разматываться на всю длину.
Испытание однорольных блоков необходимо проводить на стендах для испытания такелажа или по схемам, приведенным на рисунке 2, а, б, в.
При проведении испытаний однорольных блоков с применением динамометра последний должен быть врезан:
– между якорем (по левую сторону) и блоком, – если грузоподъемность блока меньше грузоподъемности динамометра. В этом случае динамометр показывает полную непосредственно прикладываемую испытательную нагрузку;
– в одну из ветвей каната, огибающего блок и направленного к тяговому механизму, – если грузоподъемность блока больше грузоподъемности динамометра. При такой схеме динамометр будет показывать 50 % испытательной нагрузки (без учета КПД блока).
6.4.15. Испытание многорольних блоков должно проводиться так же, как и полиспастов (рисунок 2, г, д, е, ж).
Если грузоподъемность динамометра недостаточна для проведения испытаний полиспаста по схемам рисунка 2, г, д, должны применяться схемы, приведенные на рисунке 2, е, ж. При этом динамометр необходимо врезать в одну из ветвей каната, огибающих уравнительный блок, или в ходовую ветвь троса. В этом случае при определении испытательной нагрузки необходимо учитывать КПД всех роликов.
6.4.16. После окончания испытаний блоков необходимо провести их внешний осмотр, обратив особое внимание на состояние осей и втулок. Не допускается изгиб осей; заусенцы на осях и втулках должны отсутствовать. Не должно быть также трещин в крюках и щеках, заклинивания тросов между роликами и обоймой, разгибания крюка и т. п.
При выявлении вышеуказанных или других дефектов их необходимо устранить и испытание провести вновь.
Если при проведении испытаний неисправности или какие-либо другие дефекты не обнаружены, полиспаст или блок считают выдержавшим испытание.
После проведения испытаний на блоках и полиспастах необходимо прикрепить бирки с указанием номера блока или полиспаста, его грузоподъемности и даты проведения следующего испытания, а на концах канатов полиспастов – бирки с указанием только номера блока или полиспаста.
6.5. Требования к применению канатов, строп, цепей и шнуров
Требования к канатам
6.5.1. Стальные канаты, применяемые для такелажных работ и в грузоподъемных машинах, должны соответствовать требованиям действующих нормативных документов и иметь сертификат или копию сертификата завода-изготовителя в соответствии с требованиями ГОСТ 3241. При получении канатов, не имеющих указанного сертификата, они должны пройти испытание в соответствии с требованиями ДНАОП 0.00-1.03-93 "Правила устройства и безопасной эксплуатации грузоподъемных кранов".
![]() |
6.5.2. Стальные канаты, применяемые в качестве грузовых, стреловых, вантовых, несущих и тяговых, должны выбираться в соответствии с требованиями ДНАОП 0.00–1.03-93 "Правила устройства и безопасной эксплуатации грузоподъемных кранов".
При проектировании, замене, а также перед установкой на грузоподъемную машину разрывное усилие канатов должно проверяться по формуле:
, (1)
где – разрывное усилие каната в целом, Н, принимаемое по сертификату;
– наибольшее натяжение ветви каната, Н, указанное в паспорте крана;
– минимально допустимый коэффициент использования каната (минимальный коэффициент запаса прочности каната), определяемый по данным таблиц 6.1 и 6.2.
Если в сертификате об испытании указано суммарное разрывное усилие, величину можно определить умножением суммарного разрывного усилия на коэффициент 0,83.
Запрещается применять группу классификации механизма ниже М5 по ГОСТ 25835 при выполнении работ в опасных условиях (транспортировка расплавленного металла, шлака, ядовитых и взрывчатых веществ).
При установке канатов на лебедках, предназначенных для подъёма людей, расчет коэффициента Zp необходимо проводить так же, как для группы классификации М8.
6.5.3. Подъемные и тяговые канаты должны иметь двойные свивки с сердечником из волокнистого материала.
Подъемные канаты должны иметь также крестовые свивки.
Допускается применение канатов односторонней свивки, – если исключена возможность раскручивания каната или закручивания ветвей полиспаста.
Для тяговых канатов передвижения грузовой тележки, поддержек и опор должны применяться преимущественно канаты односторонней свивки.
6.5.4. Несущие канаты и способы закрепления их на опорах и в муфтах должны удовлетворять следующим требованиям:
– канаты должны иметь закрытую конструкцию и выполняться из одного куска. В качестве несущих канатов на крюковых кранах, предназначенных для монтажных работ, допускается применять многопрядные канаты с металлическим сердечником;
– несущий канат должен закрепляться на опорах с помощью шарнирных устройств, позволяющих регулировать его натяжение;
– при применении нескольких несущих канатов должно обеспечиваться равномерное натяжение их;
– несущий канат должен закрепляться в муфте клиньями или заливкой металлическим сплавом. На кранах с переменным пролетом допускается закреплять несущий канат зажимами. Такое закрепление должно рассчитываться на усилие, не менее разрывного усилия каната в целом.
Таблица 6.1.
Дата добавления: 2019-02-26; просмотров: 700; Мы поможем в написании вашей работы! |
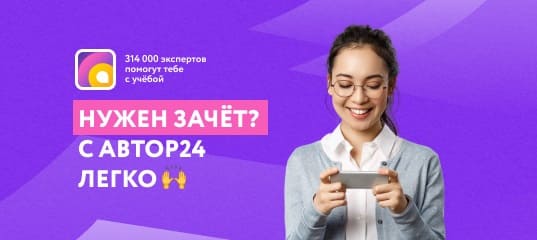
Мы поможем в написании ваших работ!