Нанесение гальванических покрытий
В машиностроении для защиты изделий от коррозии используют гальваническое осаждение многих металлов: цинка, кадмия, никеля, хрома, олова, свинца, золота, серебра и др. Применяют также электролитические сплавы, например Cu-Zn, Cu-Sn, Sn-Bi и многослойные покрытия.
Наиболее эффективно (электрохимически и механически) защищают черные металлы от коррозии анодным покрытием цинком и кадмием.
Сравнительно высокая стойкость цинка в атмосфере, его доступность и дешевизна обеспечили ему очень широкое применение для защиты стальных листов, проволоки, крепежа деталей машин, водопроводных труб, резервуаров и др. В морских условиях цинковые покрытия разрушаются относительно быстро.
Кадмий дороже цинка, но более стоек в кислых и нейтральных средах, растворах хлоридов. В атмосфере промышленных городов кадмиевые покрытия менее стойкие, чем цинковые. Поэтому кадмирование чаще используют для защиты черных и цветных металлов в условиях морского климата или при воздействии жидкой среды, содержащей хлориды.
Осаждение цинка и кадмия проводят из простых и комплексных электролитов. Первые, как более производительные, но обладающие худшей рассеивающей способностью, применяют для нанесения металла на изделия простой формы (стальные листы, проволока и др.), вторые – при осаждении на изделия сложного профиля, где важна равномерность покрытия.
Примерами простых электролитов цинкования и кадмирования, работающих при комнатной температуре, являются следующие, г/л:
|
|
1) ZnSO 4 *7 H 2 O 200-250; Na 2 SO 4 *10 H 2 O 50-100; Al 2 ( SO 4 )3*18 H 2 O 20-30; декстрин 10; pH =3,5-4,5; плотность тока 1-4 А/дм2;
2) CdSO 4 *8/3 H 2 O 40-60; ( NH 4 )2 SO 4 30-40; Al 2 ( SO 4 )3*18 H 2 O 25-30; желатина 0,5; pH =2,5-4,5; плотность тока 1-4 А/дм2.
В качестве комплексных электролитов чаще других используют цианистые электролиты следующих составов, г/л:
1) ZnO 10-18; NaCN 20-30; NaOH 50-70; Na 2 S 0,5-5, плотность тока 0,5-1 А/ дм2;
2) CdO 25-40, NaCN 80-130, NaOH 20-30, Na2SO4*10H2O 40-60;
плотность тока 0,5-2 А/ дм2.
Очень распространены никелевые покрытия. Их широко применяют для защиты изделий от коррозии и для декоративной отделки в машиностроении, приборостроении, автомобильной, медицинской и электронной промышленности, при изготовлении предметов бытового потребления. Никелевые покрытия весьма стойки в атмосфере, в растворах щелочей и некоторых органических кислот, что обусловлено сильно выраженной способностью никеля к пассивации в этих средах.
Так как никель более благородный по сравнению с железом металл, то защита от коррозии никелевыми покрытиями возможна только при отсутствии в них пор. Поэтому используются либо толстые покрытия (25-35 мкм), либо в сочетании с другими металлами, например, наносят подслой меди 25-30 мкм, затем 10-15 мкм никеля.
|
|
Чаще всего никелирование осуществляют из электролита состава, г/л: NiSO 4 *7 H 2 O 260-300; H 3 BO 3 30-35; NiCl 2 *6 H 2 O 40-60 с блескообразующими и выранивающими добавками (1,4-бутиндиола 0,12-0,16 г/л, сахарина 0,7-1,3 г/л, фталимида 0,08-0,1 г/л).
Очень эффективно трехслойное никелирование, при котором осаждают три слоя никеля из различных по составу электролитов. Нижний слой никеля матовый или полублестящий из электролита с органическими добавками, не содержащими серы. Его толщина составляет примерно 2/3 от суммарной толщины покрытия (~ 20мкм). Затем наносят слой никеля толщиной 1-2 мкм, содержащий 0,14-0,2% S. В третьем, в верхнем зеркально-блестящем слое находится около 0,05 % S.
Из-за повышенного содержания серы в среднем слое, его потенциал более электроотрицателен по отношению к верхнему и нижнему слоям. Будучи активным анодом он сильно замедляет разрушение верхнего и особенно нижнего слоев: коррозия распространяется горизонтально вдоль границы блестящего и полублестящих слоев.
Никелирование может быть осуществлено химическим путем без подвода к покрываемой детали электрического тока. Основными компонентами электролита являются соли никеля, восстановитель (гипофосфит, борогидрид и др.) и добавки, стабилизирующие раствор и препятствующие протеканию восстановительного процесса в объеме электролита. Никель осаждается в результате восстановления его ионов восстановителем, например гипофосфитом натрия:
|
|
NiCl2 + 2NaH2PO2 + 2H2O = Ni + 2NaH2PO3 + 2HCl + H2
Процесс проходит на поверхности стальной детали, являющейся катализатором реакции восстановления.
Кроме железа каталитически активны никель, кобальт, алюминий, палладий. Для химического осаждения никеля на медь и медные сплавы поверхность этих металлов должна контактировать с никелевой или алюминиевой проволокой.
Химические никелевые покрытия отличаются более высокой твердостью, так как содержат в зависимости от типа восстановителя фосфор (3-15%) или бор, имеют повышенную коррозионную стойкость. Главное достоинство процесса химического никелирования – равномерность толщины покрытия на любом рельефном профиле изделия.
Химическим путем никель может быть осажден на неметаллические материалы (стекло, керамику, пластмассы).
Хромовое покрытие наносят из раствора, содержащего CrO 3 250 г/л, H 2 SO 4 2,5 г/л; плотность тока 30-80 А/дм2, температура процесса 40-700С.
|
|
В зависимости от величины постоянного тока и температуры получаются блестящие и матовые осадки с различными механическими свойствами.
Из-за сильно выраженной способности к пассивации хром приобретает повышенную химическую стойкость и является катодными покрытием по отношении к стали. Он хорошо сопротивляется атмосферной коррозии, стоек в азотной кислоте, ряде органических кислот, в растворах многих солей, в том числе содержащих серу.
Хромовые покрытия характеризуются высокой твердостью (до 11000-13000 МПа), имеют красивый внешний вид и используются в качестве защитно-декоративных, износоустойчивых покрытий, а также для восстановления изношенных деталей машин и механизмов. Хромирование широко применяется при изготовлении режущего инструмента, валов, осей цилиндра, двигателей, лопаток паровых и водяных турбин и др.
Однако хромовые покрытия отличаются большой пористостью, склонны к растрескиванию. Поэтому в качестве защитно-декоративного покрытия осаждение хрома проводят в сочетании с другими металлами, например с медью, никелем.
Оловянные покрытия применяют главным образом для защиты от коррозии в приборостроении, где наряду с защитными свойствами необходимо обеспечить паяемость изделия.
Во многих пищевых средах в паре с железом олово является анодом. Продукты коррозии олова нетоксичны. Этим и объясняется применение этого дорогого металла для защиты от коррозии консервной тары.
Олово наносят из сернокислых и щелочных электролитов. Сернокислые электролиты содержат сернокислое олово, серную кислоту и добавки поверхностно-активных веществ (клей, крезол, препарат ОС-20), при отсутствии которых ион Sn2+ разряжается почти без поляризации.
В щелочных электролитах ион олова находится в виде комплексного аниона SnO32-. Эти электролиты (50-70 г/л Na2SnO3, 30-60 г/л NaOH) обладают очень высокой рассеивающей способностью.
Процесс электроосаждения металлов осуществляется в стационарных условиях, колокольных, барабанных ваннах, на полуавтоматических и автоматических линиях.
Корпус стационарной ванны обычно изготавливают из листовой стали с футеровкой внутренних стенок стойким в электролите материалом (винипласт, резина, эмаль, полиэтилен, фторопласт и др.). Нагрев или охлаждение электролита осуществляется с помощью водяной рубашки или змеевика. Ванны оборудуют механизмом для встряхивания катодных штанг, воздушными барбатерами.
Покрытие мелких деталей проводят во вращающихся колоколах и барабанах.
Полуавтоматические и автоматические линии представляют собой комплект ванн, где выполняются все операции нанесения однослойных и многослойных покрытий. Перемещение подвесок и барабанов с деталями осуществляется вручную или автоматически с помощью автооператоров и движущихся траверс. В автоматизированных линиях все операции гальванического процесса, кроме монтажа деталей на подвески и их разгрузки, выполняются автоматически по заданным режимам.
Алитирование.
Алитирование - процесс насыщения поверхностного слоя защищаемого материала алюминием. Цель - повышение окалиностойкости (жаростойкости) и сопротивления атмосферной коррозии. Алитирование стальных изделий (жаропрочные сплавы, идущие на изготовление клапанов автомобильных двигателей, лопаток и сопел газовых турбин) осуществляется в собранном виде, так как образующийся защитный слой хрупок и не допускает механической обработки.
Детали, очищенные от грязи и ржавчины, загружают в герметически закрывающийся ящик(реактор), засыпают реакционной смесью (50%Al-порошка ,45-48%Al2O3и 2-5%NH4Cl) и помещают в нагревательное устройство (печь). Время выдержки 3-4 часа, температура 950-1000оС.
Алитирование - один из самых надежных способов повышения жаростойкости стали от окисляющего действия кислорода при повышенных температурах.
Термохромирование .
Процесс термохромирования проводят при температуре 1000-1250 оС в смеси Cr-порошка, каолина(Al2O3*2SiO2*2H2O) и нашатыря. Образующийся в результате окисления слой оксидов сообщает металлу стойкость в воздушной и газовой среде содержащей соединения ванадия и серы до 1000оС. Термохромированный слой обладает повышенной износостойкостью. Слой поддается механической обработке.
Дата добавления: 2019-02-26; просмотров: 149; Мы поможем в написании вашей работы! |
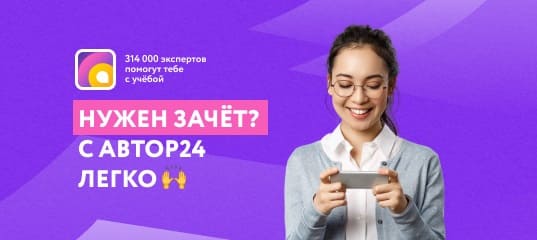
Мы поможем в написании ваших работ!