Подготовка поверхностей перед нанесением покрытия
Металлические покрытия
Нанесение защитных покрытий – один из самых распространенных методов борьбы с коррозией. Эти покрытия не только защищают от коррозии, но и придают их поверхности ряд физико-химических свойств: твёрдость, износоустойчивость, электропроводность, паяемость, отражательную способность, обеспечивают изделия декоративную отделку и т.д.
По способу защитного действия металлические покрытия делятся на катодные и анодные.
Катодные покрытия имеют более положительные, а анодный более электроотрицательный потенциалы по сравнению с потенциалом металла, на который они нанесены. Так, например, медь, никель, серебро, золото, осажденные на сталь, являются катодными покрытиями, а цинк и кадмий по отношению к этой же стали – анодными покрытиями.
Необходимо отметить, что вид покрытия зависит не только от природы металлов, но и состава коррозионной среды. Олово по отношению к железу в растворах неорганических кислот и солей играет роль катодного покрытия, а в ряде органических кислот (пищевых консервах) служит анодом. В обычных условиях катодные покрытия защищают металл изделия механически, изолируя его от окружающей среды. Основное требование к катодным покрытиям – беспористость. В противном случае при погружении изделия в электролит или при конденсации на его поверхности тонкой плёнки влаги обнаженные (в порах или трещинах) участки основного металла становятся анодами, а поверхность покрытия катодом. В местах несплошностей начнется коррозия основного металла, которая может распространяться под покрытие.
|
|
Анодные покрытия защищают металл изделия не только механически, но главным образом электрохимически . В образовавшемся гальваническом элементе металл покрытия становится анодом и подвергается коррозии, а обнаженные (в порах) участки основного металла выполняют роль катода и не разрушаются, пока сохраняется электрический контакт покрытия с защищаемым металлом и через систему проходит достаточный ток. Поэтому степень пористости анодных покрытий в отличие от катодных не играет существенной роли.
В отдельных случаях электрохимическая защита может иметь место при нанесении катодных покрытий. Это происходит если металл покрытия по отношению к изделию является эффективным катодом, а основной металл склонен к пассивации . Возникающая анодная поляризация пассивирует незащищенные (в порах) участки основного металла и затрудняет их разрушение. Такой вид анодной электрохимической защиты проявляется для медных покрытий на сталях 12X13 и 12X18H9T в растворах серной кислоты.
|
|
Основной способ нанесения защитных металлических покрытий – гальванический. Применяют также термодиффузионный и механотермический методы, металлизацию напылением и погружением в расплав.
Для нанесения металлических защитных покрытий надо выбирать металлы, оксидный слой на поверхности которых делает их пассивными (А1, Zn, Sn, Cr, Pb, Ni), или металлы, пассивные по своим химическим свойствам (Au, Ag, Сu). Кроме того, надо учитывать условия эксплуатации изделия. Методы нанесения металлических защитных слоев на поверхность металлов весьма разнообразны и их можно, разделить условно на «горячие» или высокотемпературные и электрохимические. Покрывающий слой наносят различными методами:· горячее покрытие – кратковременное погружение в ванну с расплавленным металлом; · гальваническое покрытие – электроосаждение из водных растворов электролитов; · металлизация напылением; · диффузионное покрытие – обработка порошками при повышенной температуре в специальном барабане; · плакирование. Метод погружения в расплавленный металл Метод применим для нанесения покрытий из легкоплавких металлов на более тугоплавкие. Так покрывают стальные листы оловом, цинком и свинцом. Сущность метода сводится к тому, что в расплавленный металл, из которого хотят приготовить покрытие, через слой флюса, закрывающий поверхность жидкого металла, погружают стальной лист и вынимают его также через слой флюса или масла для того, чтобы поверхность сразу не окислилась. Цинк и олово в жидком состоянии хорошо смачивают поверхность, стали; для покрытия стали свинцом необходимо добавлять к нему некоторое количество олова, так как свинец плохо смачивает стальную поверхность.Цинк, смачивая поверхность железа, взаимодействует с ним, образуя интерметаллиды (FeZn7, FeZn3), обладающие значительной хрупкостью. Поэтому процесс ведут быстро, с тем чтобы слой интерметаллидов был максимально тонким и не вызвал хрупкости всего защитного слоя.Олово растворяет железо с образованием твердого раствора и интерметаллид FeSn2 обычно не образуется. Оловянный слой на луженом железе очень пластичен, так же как и свинцовый.Оценивая свойства луженого и оцинкованного железа, следует раздельно рассматривать механические свойства покрытия и его физико-химические свойства. Цинк по отношению к железу представляет собой анод и будет разрушаться в первую очередь сам, защищая железо от растворения, в то время как олово будет по отношению к железу катодом и повреждение покрытия вызовет усиленную коррозию железа.Однако из этого не следует, что всегда оцинкованное железо лучше луженого, так как при этом получаются разные механические свойства нанесенного покрытия. В процессе цинкования между железом и цинком образуются хрупкие прослойки интерметаллидов, которые могут при перегибе листа дать трещины, приводящие к отслою покрытия и его повреждению. При лужении железа слой олова получается пластичным, покрытие оказывается более прочным и выносит многократные перегибы листа без повреждения слоя.
|
|
|
|
Это старейший и наиболее простой метод нанесения цинка, олова, свинца на стальные листы и проволоку.
Покрытия образуются достаточно толстые, практически беспористые, но неравномерные по толщине. К недостаткам метода относится также сравнительно большой расход цветных металлов: помимо избыточной толщины защитного слоя, часть металла безвозвратно теряется вследствие угара (окисления кислородом воздуха).
В настоящее время метод погружения вытеснен другими, более экономичными методами, например методом гальванического осаждения.
Металлизация напылением
Метод нанесения расплавленного металла на поверхность защищаемой конструкции с помощью струи сжатого воздуха или инертного газа. Проволока металла, который наносится в качестве защитного слоя, подается в ацетиленокислородное пламя, в дуговой или плазменный разряд — металл плавится и частично испаряется. Мельчайшие капли и пары металла струей газа транспортируются на поверхность изделия и кристаллизуются на ней. Поверхность изделия должна быть тщательно очищена, так как иначе не будет прочного сцепления нанесенного слоя с металлом изделия. Частицы расплавленного металла, двигаясь с большой скоростью, ударяются о поверхность основного металла, сцепляются с ней, образуя металлическое покрытие. Метод пригоден для нанесения покрытий на неметаллические материалы. Распылять можно многие металлы. Разработаны методы распыления высококачественных сталей, что позволяет не изготовлять все изделия из этого ценного материала. Однако чаще всего на сталь напыляют анодные покрытия – цинк, алюминий. Иногда наносят покрытия с подслоем. Расплавление металла и его распыление производят специальными аппаратами - шприц-пистолетами.
Метод нанесение пленок защитного металла путем совместного проката. Метод приемлем только для листов и некоторых профилей проката (пруток, угольник и т. д.).
Этот способ нанесения покрытий очень удобен, но при изготовлении из плакированного металла изделий встречаются технологические трудности.
Покрытие образуется в результате совместной прокатки, горячей прессовки, нагрева под давлением двух металлов, один из которых играет роль защитного слоя. Толщина покрытия обычно составляет 10-20% от толщины основного металла.
Сцепление слоев очень хорошее, так как обеспечивается диффузией при одновременном действии температуры и давления.
Защитные свойства покрытия при неповрежденной поверхности практически не отличаются от свойств плакирующего металла.
Изготовление жаростойких биметаллов способствует значительной экономии высоколегированной стали.
Гальванические покрытия
Электрохимические методы нанесения металлических покрытий основаны на электролизе. Металлические защитные слои в этом случае осаждаются на поверхности изделия, которое в электролизере представляет собой катод и находится под отрицательным потенциалом. Покрытие должно иметь мелкокристаллическую структуру и быть сплошным — без пор и трещин. Разработаны определенные режимы осаждения, обеспечивающие эти качества покрытий (температура, плотность тока и состав электролита). Для получения мелкозернистой структуры в состав электролита вводят поверхностно-активные вещества и органические добавки, препятствующие росту отдельных кристаллических зерен (декстрин, ализариновое масло и т. д.).Гальванический метод осаждения защитных металлических покрытий получил очень широкое распространение в промышленности. По сравнению с другими способами нанесения металлопокрытий он имеет ряд серьёзных преимуществ: высокую экономичность (защита металла от коррозии достигается весьма тонкими покрытиями), возможность получения покрытий одного и того же металла с различными механическими свойствами, легкую управляемость процесса (регулирование толщины и свойств металлических осадков путем изменения состава электролита и режима электролиза), возможность получения сплавов разнообразного состава без применения высоких температур, хорошее сцепление с основным металлом и др.
Недостаток гальванического метода – неравномерность толщины покрытия на изделиях сложного профиля.
Электрохимическое осаждение металлов проводят в гальванической ванне постоянного тока. Покрываемое металлом изделие завешивают на катод. В качестве анодов используют пластины из осаждаемого металла (растворимые аноды) или из материала, нерастворимого в электролите (нерастворимые аноды).
Обязательный компонент электролита - ион металла, осаждающийся на катоде. В состав электролита могут входить вещества, повышающие его электропроводность, регулирующие протекание анодного процесса, обеспечивающие постоянство pH, поверхностно-активные вещества, повышающие поляризацию катодного процесса, блескообразующие и выравнивающие добавки и др.
Гальваническое осаждение металла происходит в результате электрохимической реакции гидратированных ионов металла на катоде и вхождения образовавшихся атомов в состав кристаллической решетки покрытия. Общую схему процесса можно выпазить уравнением
[Me(H2O)X]n+ + ne = Me + xH2O
Одновременно с разрядом ионов металла может происходить реакция выделения водорода
2H+ + 2e = H2
На аноде происходят процессы электрохимического растворения металла электрода:
Me + xH2O = [Me(H2O)x]n+ + ne
и выделение кислорода
4OH- = O2 + 2H2O + 4e
Электроосаждение протекает по стадиям, важнейшими из которых являются:
1) доставка ионов металла из объема электролита к поверхности катода в основном благодаря диффузии и конвекции;
2) разряд гидратированных ионов металла, включающий частную или полную дегидратацию ионов и адсорбцию разрядившихся частиц на электроде;
3) перемещение (диффузия) разрядившихся частиц по поверхности электрода к местам кристаллизации (местам роста), вхождение атомов в кристаллическую решетку, образование и рост кристаллических зародышей.
Согласно современным представлениям электрокристаллизация происходит одновременно не по всей поверхности электрода, а сначала лишь на активных местах, получивших название мест роста. К ним относятся вершины углов и ребер кристалла, дефекты поверхностей катода (дислокации).
Сначала возникают кристаллические зародыши, которые затем растут вследствие присоединения разрядившихся атомов металла. Структура гальванического осадка определяется соотношением скоростей образования кристаллических зародышей и их роста. Чем выше относительная скорость образования зародышей, тем более мелкозерниста структура покрытия. Возникновение кристаллических зародышей сопряжено с большой затратой энергии по сравнению с их ростом. Поэтому повышение катодной поляризации способствует образованию мелкозернистых покрытий, которые обладают лучшими защитными свойствами.
Возможен процесс кристаллизации и без образования кристаллических зародышей. Он происходит при низкой поляризации на участках поверхности электрода, имеющих винтовые дислокации, которые и служат местом роста кристалла.
Скорость электроосаждения металла и величина поляризации (перенапряжения) лимитируется наиболее медленной стадией процесса. Ею может быть любая из рассмотренных выше стадий.
Структура гальванического покрытия, его физико-механические и защитные свойства определяются природой осаждаемого металла, составом раствора и режимами электролиза.
В зависимости от того, в каком виде ион разряжающегося металла находится в растворе, все электролиты делятся на комплексные и простые. Разряд комплексных ионов на катоде происходит при более высоком перенапряжении, чем разряд простых ионов. Поэтому осадки, полученные из комплексных электролитов, более мелкозернисты и равномерны по толщине. Однако у этих электролитов ниже выход металла по току и более низкие рабочие плотности тока, т.е. по производительности они уступают простым электролитам, в которых ион металла находится в виде простых гидратированных ионов.
Часто в растворы для электроосаждения металлов вводят поверхностно-активные вещества определенного класса. Они способствуют повышению катодной поляризации, что позволяет получать более плотные, мелкозернистые покрытия. В ряде случаев осаждение металла (например, олова, свинца из простых электролитов) при отсутствии добавок поверхностно-активных веществ вообще не происходит или осадки образуются в виде отдельных изолированных кристаллов. Поверхностно-активные вещества применяют также в качестве блескообразующих и выравнивающих добавок, обеспечивающих получение гладких и блестящих покрытий непосредственно в процессе электролиза без последующей механической полировки.
Повышение плотности тока увеличивает катодную поляризацию и скорость осаждения металла. Однако верхний предел ее ограничен эффектом дендритообразования, наступающим при достижении предельного тока, т.е. плотности тока, при котором скорости разряда ионов и доставки их к поверхности электрода равны.
Важную роль играет температура электролита. С ее повышением возрастает предельный ток, а, следовательно, и верхний предел рабочей плотности тока, увеличивается растворимость солей, электропроводность раствора, а для большинства металлов – и выход по току.
Количество осаждаемого металла пропорционально количеству прошедшего через электрод электричества. Поэтому толщину покрытия определяют на основании закона Фарадея:
L = (Кэ. i . h. t)/r. 1000 ,
где L – толщина покрытия, мм;
Кэ – электрохимический эквивалент, г/(А. ч);
h - выход металла по току, %;
i – катодная плотность тока, А/дм2;
r - плотность металла покрытия, г/см3;
t - продолжительность электролиза, ч.
Распределение тока по поверхности изделия в гальванической ванне никогда не бывает равномерным. Это приводит к разной скорости осаждения, а, следовательно, и толщине покрытия на отдельных участках катода. Особенно сильный разброс по толщине наблюдается на изделиях сложного профиля, что отрицательно сказывается на защитных свойствах покрытия. Равномерность толщины осаждаемого покрытия улучшается с увеличением электропроводности электролита, ростом поляризации по току при повышении плотности тока, увеличением расстояния между катодом и анодом.
Способность гальванической ванны давать равномерные по толщине покрытия на рельефной поверхности называется рассеивающей способностью. Наибольшей рассеивающей способностью обладают комплексные электролиты.
Подготовка поверхностей перед нанесением покрытия
Получение покрытий, прочно сцепленных с основным металлом и с хорошим внешним видом, невозможно без тщательной подготовки поверхности. Перед нанесением покрытия детали должны быть очищены от окалины, ржавчины, окислов, жировых загрязнений. Даже совершенно чистые по внешнему виду детали необходимо обезжирить и подвергнуть травлению.
Различают механическую, химическую и электрохимическую обработку поверхности.
Механическая обработка – это удаление неровностей, царапин, заусениц с целью получения блестящей поверхности. Для этого используют пескоструйную обработку, шлифовку и полировку.
Химическая и электрохимическая обработка включает обезжиривание, травление, декапирование, электрохимическое полирование.
Химическое обезжиривание проводят в щелочных растворах и в органических растворителях.
В щелочных растворах жиры растительного и животного происхождения омыляются, разлагаясь на растворимые в воде соли жирных кислот и глицерина. Минеральные масла в щелочах не омыляются. Поэтому для их удаления в щелочные растворы для обезжиривания, содержащие кроме едкого натра, тринатрийфосфат и кальцинированную соду, вводят эмульгаторы и смачивающие добавки: синтанол, жидкое стекло. Например, для обезжиривания стальных деталей, загрязненных рабочими и консервационными маслами, используют раствор, содержащий, г/л: NaOH 5-35; Na3PO4 15-35; Na2CO3 15-35; синтанол ДС10 3-5. Температура процесса 60-800С, время обработки 3-20 мин.
Обезжиривание в органических растворителях (керосин, бензин, четыреххлористый углерод) сводится к растворению омыляемых и неомыляемых жиров.
Электрохимическое обезжиривание осуществляется на катоде или аноде в щелочных растворах примерно такого же состава, что и при химическом обезжиривании, но менее концентрированных. При этом значительно ускоряется процесс, и более полно удаляются жировые загрязнения.
Механизм обезжиривания сводится к понижению поверхностного натяжения и увеличению смачиваемости металла раствором вследствие поляризации электрода. Выделяющиеся пузырьки газа прилипают к капелькам масла, способствуют их отрыву и всплытию на поверхность раствора.
Недостаток катодного обезжиривания – наводороживание деталей, в результате чего возможно появление хрупкости. Поэтому нередко после катодного обезжиривания проводят короткое анодное обезжиривание.
Травление – удаление поверхностных оксидов химическим или электрохимическим способом.
Составы растворов для химического травления выбирают в зависимости от природы металла. Травление черных металлов чаще проводят в серной и соляной кислотах. Для борьбы с перетравливанием и наводороживанием (химическое травление в кислотах сопровождается выделением водорода) в травильные растворы добавляют ингибиторы травления. Их введение замедляет или прекращает растворение металла, не снижая скорости растворения оксидов.
Травление алюминия и его сплавов проводят в 5-10%-ном растворе HCl или 10-15% растворе NaOH с добавлением 30 г/л NaCl.
Электрохимическое травление основано на электрохимическом растворении металла и механическом отрыве оксидов пузырьками выделяющегося газа.
Декапирование – дополнительное травление изделий в течение нескольких секунд непосредственно перед процессом электроосаждения металла с целью удаления тонких пассивирующих пленок и активирования поверхности деталей.
Дата добавления: 2019-02-26; просмотров: 218; Мы поможем в написании вашей работы! |
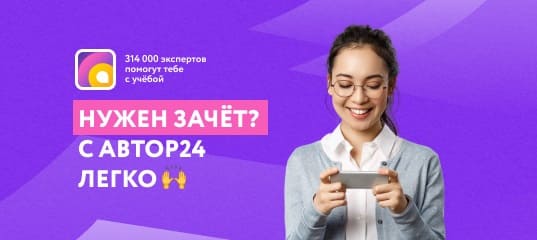
Мы поможем в написании ваших работ!