Классификация и маркировка штучных электродов
Саратовский государственный технический университет
Им. Гагарина Ю.А.
Кафедра «Сварка и металлургия»
МЕТОДИЧЕСКОЕ РУКОВОДСТВО
К практической работе №2
«Сварочные материалы. Сварочная проволока и штучные покрытые электроды»
По дисциплине
«Технология сварки плавлением»
Саратов 2015
Цель работы: Изучить основные требования к технологическим свойствам сварочных материалов. Требования к технологическим свойствам покрытых электродов. Правила обозначения покрытых электродов для ручной дуговой сварки. Основные марки покрытых электродов для ручной дуговой сварки сталей различных классов.
Литература, нормативная документация: ГОСТ 9466-75; ГОСТ 9467-75;
ГОСТ 10051-75; ГОСТ 10052-75; Презентация №2 (ИОС).
Общие методические указания
Сварочная проволока
Металл сварочных швов при сварке плавлением формируется в основном за счёт электродных материалов. Состав и диаметр сварочных проволок во многом определяет качество формообразования, деформационные процессы, коррозионную стойкость и усталостную прочность наплавленного металла.
Наиболее распространёнными материалами для дуговой сварки является:
· холоднотянутая проволока диаметром 0,3 – 12 мм;
· горячекатаная или порошковая проволока;
· электродные ленты (сплошного сечения, порошковые, металлокерамические);
· металлокерамические стержни и ленты;
|
|
· пластины (при сварке лежачим электродом).
Сварочную проволоку выпускают 75 марок, которые подразделяют на низко-, средне-, высокоуглеродистые, а также на низко-, средне-, высоко-легированные (ГОСТом 2246-70). Химический состав электродной прово-локи определяет состав металла шва и, следовательно, его механичес-кие свойства. Легирующие элементы в электродных материалах условно обозна-чают буквами:
Г - марганец (М n ) С – кремний (Si) Х – хром ( Cr ) Н – никель ( Ni ) | Ф – ванадий ( V ) В – вольфрам ( W ) Е – селен (Sе) Т – титан (Т i ) | К – кобальт (Со) Ц – цирконий ( Zr ) Ю – алюминий (А l ) М – молибден (Мо) | Р – бор (В) А - азот ( N ) Д – медь (С ) Б – ниобий ( Nb ) |
Буква «А» в конце условных обозначений марок низкоуглеродистых и легированных проволок указывает на повышенную чистоту металла по содержанию серы и фосфора.
Маркировка. Сварочные проволоки имеют условное обозначение: Э – для изготовления электродов; О – омеднённая; Ш – полученная электрошлаковым переплавом; ВД – вакуум-дуговым, ВИ – вакуум-индукционным. В маркировку электродных проволок вводят следующие буквенные обозначения: Д – холоднодеформированные, Г – горячедеформированные; КР - круглая форма сечения, ПР – прямоугольное сечение; М – мягкое, Т – твёрдое состояние; БТ – мотки или бухты, КТ – катушки, БР – барабаны, СР - сердечники, НД – немерной длины.
|
|
Поверхность проволоки должна быть чистой для сварки (без окалины, ржавчины, грязи и масла).
Сварочная проволока марки 2,5 Св-08ХГСМФА ВИ-Э-О – ГОСТ 2246-70 расшифровывается так: диаметр проволоки - 2,5 мм; в проволоке содержится: углерода - 0,08 %; хрома (Х), марганца (Г), кремния (С), молибдена (М) и ванадия (Ф) до 1% каждого элемента, с пониженным содержанием серы и фосфора (А); проволока выплавлена вакуумно-индукционным способом (ВИ); предназначена для электродов с омеднённой поверхностью.
Для сварки сталей предназначена проволока по ГОСТ 2246 –70* «Проволока стальная сварочная». В соответствии с этим ГОСТом выпускают низкоуглеродистую, легированную и высоколегированную проволоку диаметром 0,3; 0,5; 0,8; 1,0; 1,2; 1,4; 1,6; 2,0; 2,5; 3,0; 4,0; 5,0; 6,0; 8,0; 10,0; 12,0 мм.
По химическому составу электродная проволока подразделяется на малоуглеродистую, легированную и высокоуглеродистую.
Государственным стандартом предусмотрен выпуск проволоки 77 марок. Маркируют ее, как и стали, с добавлением букв Св.
Например, проволока марки Св-10Г2А: первые буквы Св — сварочная проволока, первые две цифры — содержание углерода в сотых долях процента (0,1%), буква Г — марганец до 2%, буква А в конце маркировки указывает на повышенное качество металла с пониженным содержанием вредных примесей серы и фосфора.
|
|
Проволока марки Св-08ХГСМФ расшифровывается следующим образом: углерода 0,08%, хрома, марганца, кремния, молибдена, ванадия — до 1 % каждого.
Проволока поставляется в бухтах массой до 80 кг. На каждой бухте крепят металлическую бирку с указанием завода-изготовителя, условного обозначения проволоки, номера партии и клейма технического контроля. По соглашению сторон проволоку могут поставлять намотанной на катушки или кассеты.
Транспортировать и хранить проволоку следует в условиях, исключающих ее ржавление, загрязнение и механическое повреждение. Если же поверхность проволоки загрязнена или покрыта ржавчиной, то перед употреблением ее необходимо очистить. Проволоку очищают при намотке ее на кассеты в специальных станках, используя
наждачные круги.
Для удаления масел используют керосин, уайт-спирит, бензин и др. На некоторых заводах для устранения влаги применяют термическую обработку: прокалку при температуре 100-150°С . ЦНИИТМАШ рекомендует обрабатывать проволоку в 20%-ном растворе серной кислоты с последующей прокалкой при температуре 250°С 2-2,5 ч.
|
|
Необходимость в обработке электродной проволоки перед сваркой отпадает, если использовать омедненную проволоку.
Ленточный электрод,электродная лента – плавящийся электрод в виде непрерывной ленты. Используется преимущественно при механизированной наплавке.
Для сварки алюминия и его сплавов используют сварочную проволоку, выпускаемую по ГОСТ 7871-75 «Проволока сварочная из алюминия и алюминиевых сплавов».
Проволоку для сварки алюминия выпускают 25 марок, различного диаметра (0,8 – 12,5 мм). Пример условного обозначения тянутой (В) проволоки из алюминиевого сплава марки АМц в нагартованном состоянии (Н), диаметром 5 мм, в бухте (БТ):
В Св - АМц. Н 5,00хБТ ГОСТ 7871-75.
Классификация и маркировка штучных электродов
Штучные электроды для сварки представляют собой пруток из специальной проволоки, называемой стержнем электрода. В подавляющем большинстве случаев стержень изготавливают из низкоуглеродистой стали, на который нанесён слой покрытия.
Электроды диаметром 4, 5 и 6мм имеют стандартную длину 450ммэлектроды.
В общем случае электродное покрытие служит: а) для защиты металла сварочной ванны от воздуха, б) для раскисления и легирования наплавленного металла, в) для стабилизации горения дуги.
В соответствии с этим в состав любого электродного покрытия входят материалы, выполняющие соответствующие функции:
- шлакообразующие (например, марганцевая руда, гематит, гранит, мрамор, рутил и др.);
- флюсующие, т.е. придавать шлаку жидкотекучесть (плавиковый шпат);
- раскисляющие (ферросплавы элементов, обладающих большим сродством к кислороду);
- легирующие (ферросплавы различных элементов);
- стабилизирующие(материалы, содержащие элементы, обладающие низким потенциалом ионизации, например, мрамор, поташ, углекислый барий и др.).
Штучный электрод – термин, применяемый для обозначения плавящихся электродов в виде стержней, требующих частой замены в процессе ручной сварки, в том случае, когда они противопоставляются электродной проволоке.
Покрытый электрод, обмазанный электрод – плавящийся электрод, имеющий на поверхности покрытие из порошкообразных материалов, сцементированных клеящим раствором.
Электроды получают из холоднотянутой проволоки, электродной ленты или пластин. Их различают по следующим классификационным признакам:
по материалу, из которого они изготовлены; металлу, для сварки которого они предназначены;
- виду покрытия; химическому составу стержня и покрытия;
- характеру шлака, образующегося при расплавлении покрытия;
- механическим свойствам металла шва.
По назначению электроды используют для сварки конструкционных сталей:
- низко-, средне- и высокоуглеродистых сталей;
- низко-, средне- и высоколегированных;
- теплоустойчивых и коррозионностойких сталей;
- дуговой наплавки поверхностных слоев с особыми свойствами.
Покрытия электродов по функциональным свойствам делятся на стабилизирующие (тонкие) и защитные (толстые или качественные).
Стабилизирующие покрытия состоят из веществ, атомы которых легко ионизируются, чем поддерживают горение дуги, облегчают ее возбуждение. Такие покрытия толщиной 0,1—0,3 мм наносятся на проволоку. Они состоят, например, из 80—85% мела и 15—20% жидкого стекла или 70—80% титановой руды, 10% марганцевой руды, 9% калиевой селитры и 10% жидкого стекла.
Защитные покрытия служат для повышения устойчивости дуги, создания защитной оболочки из шлака, для предохранения от попадания кислорода и азота из окружающей среды, а также для введения в металл шва дополнительных легирующих элементов с целью улучшения его свойств. Защитные покрытия электродов позволяют получить достаточно прочный сварной шов без пор, раковин, шлаковых включений. Толщина защитного покрытия на обычных электродах составляет 0,7—2,5 мм. В качестве шлакообразующих добавок: используют полевые шпаты, рутил, карбонаты, алюмосиликаты и пр.
По технологическому назначению покрытия могут быть:
- шлакообразующими (состоят из окислов титановых и марганцевых руд, полевого и плавикового шпата, кварца и гранита);
- газообразующими (в их состав входят мел, мрамор, известняк, доломит, магнезит — вещества, выделяющие СО2 при нагреве);
- раскисляющими (в их составе ферромарганец, ферросилиций, ферротитан, алюминий и пр.);
- легирующими (состоят из Мn, Si, Cr, Ti, Cu и пр.).
По химсоставу защитные покрытия очень сложны. При подборе их состава некоторые химические элементы берут как основу, другие - как дополнение к ним.
По составу основных химических компонентов (веществ) защитные покрытия разделяются на:
Руднокислые — Р. Образует шлаки с компонентами, окисляющими металл (силикаты и титаны марганца и железа). Защитные газы образуются вследствие сгорания органических составляющих.
Рутиловые — Т. Образует шлаки с компонентами, практически не содержащими окислов железа (титанаты и силикаты марганца и железа).
Фтористокальциевые — Ф. Образует шлаки с компонентами, окисляющими металл (силикаты кальция и магния, а также плавиковыйшпат). Защитные газы возникают в результате диссоциации карбонатов.
Органические — О. Органические составляющие образуют защитные газы.
В качестве раскислителей в покрытие вводятся ферросплавы марганца.
Качественное покрытие, толстое покрытие – электродное покрытие, роль которого состоит, помимо повышения стабильности горения сварочной дуги, в осуществлении защиты, а также в выполнении ряда металлургических функций. Качественное покрытие способствует улучшению качества металла шва. Это покрытие наносится толстым слоем на поверхность электрода.
В покрытия чаще всего используют исходные компоненты в виде полевых шпатов, кварца, мела, жидкого стекла, окислов различных активных элементов..
Полевые шпаты – наиболее распространенные в земной коре алюмосиликаты натрия и калия. В сварочном производстве полевые шпаты используются для изготовления электродных покрытий.
Кварц,кремнезем SiO2 – двуокись кремния, один из наиболее распространенных минералов. В сварочном производстве используется в виде кварцевого песка для изготовления электродных покрытий и флюсов.
Меловое покрытие – стабилизирующее покрытие, состоящее из мела, замешанного на жидком стекле.
Жидкое стекло,растворимое стекло – водный раствор силиката натрия Na2О . (SiO2)m или силиката калия К2О . (SiO2)n, обладающий клеящими свойствами и применяемый в электродных покрытиях в качестве связующего и стабилизирующего компонента
Легирующие компоненты покрытий – компоненты электродных покрытий, обычно ферросплавы или окислы каких-либо легирующих элементов, вводимые для придания металлу шва необходимых свойств.
Карборундовый электрод – электрод из карборунда для кислородно-дуговой подводной резки. Снаружи он металлизируется сталью и имеет обычное минеральное покрытие, предназначенное для стабилизации дуги, а также гидроизоляционное покрытие.
У каждого покрытия имеется своё предназначение. Например, у руднокислых покрытий металл шва легируется через проволоку, а также введением в состав покрытия металлических порошков и ферросплавов.
Электроды с органическими покрытиями удобны для монтажных работ, когда необходимо накладывать швы во всех пространственных положениях, хорошо обеспечивают провар корня и формирование обратной стороны шва.
По механическим свойствам и химическому составу металла шва электроды подразделяются на четыре группы:
1. Электроды для сварки углеродистых и легированных конструкционных сталей обычной прочности, то есть при минимальном гарантированном временном сопротивлении шва на растяжение равном
s рш = (34 — 60) 107 Па (34 — 60 кгс/мм2) и повышенной прочности шва s рш = (70 — 150) 107 Па (70 — 145 кгс/мм2). Эти электроды обозначают сочетанием букв и цифр: Э34, Э42, 370, Э145. Буква Э указывает, что это электрод для дуговой сварки, а цифры — значения предела прочности металла шва s рш.
Для одновременного обозначения марок проволоки и электрода, его типа, диаметра и вида покрытия запись ведут группами через дефис. Например, индекс электрода:
Св-08ГС-АНО-7-Э50А-5,0-Ф ГОСТ 9467—75
расшифровывается следующим образом: Св-08ГС — марка электродной проволоки, АНО-7 — марка электрода, Э50 — тип электрода, А — указывает на повышенные пластические свойства металла шва, 5,0 — диаметр электродного стержня, Ф—фтористо-кальциевое покрытие; ГОСТ 9467—75— номер стандарта на данный электрод.
2. Электродные проволоки для сварки теплоустойчивых сталей гарантируют в наплавленном металле определенное содержание химических элементов. Поэтому в тип электрода вводят индекс гарантированного химического состава металла шва. Например, тип электрода Э-Х2МФБ расшифровывается так: Э — электрод, обеспечивающий в составе шва хрома до 2%, молибдена, ванадия и ниобия — до 1% каждого. Данные электроды имеют марки ЦУ-2М, ЦЛ-14, ЦЛ-27 и т. д.
3. Электроды для сварки высоколегированных сталей с особыми свойствами классифицируются по химическому составу наплавленного металла, содержанию ферритной фазы, стойкости сварного соединения против межкристаллитной коррозии и механическим свойствам наплавленного металла. При обозначении этих типов электродов кроме буквы Э добавляются буквы А (аустенитные) и Ф (ферритные).
4. Электроды для дуговой наплавки выпускаются 25 типов и характеризуются химическим составом наплавленного металла, его твердостью. К этой группе относятся электроды типа:
ЭН-70Х11-25, ЭН-90В9Х4Ф2-60.
Обозначения расшифровываются так: ЭН — электрод наплавочный, далее — химический состав шва и цифра после дефиса указывает твердость наплава (в первом случае 25 единиц HRC, а во втором — 60 HRC).
В зависимости от назначения электродов в покрытие вводят необходимое количество легирующих элементов.
В качестве связующих элементов обычно могут использоваться жидкое стекло: силикат натрия или силикат калия.
Для придания безокислительного характера плавления металла в качестве связующего материала используется алюминат натрия – Na 2 O . mAl 2 O 3 . nH 2 O. Такие покрытия называются основными.
Для повышения коэффициента наплавки в некоторые покрытия вводят железный порошок. В этом случае в обозначение покрытия вводят букву Ж (например, БЖ).
Дата добавления: 2019-02-22; просмотров: 767; Мы поможем в написании вашей работы! |
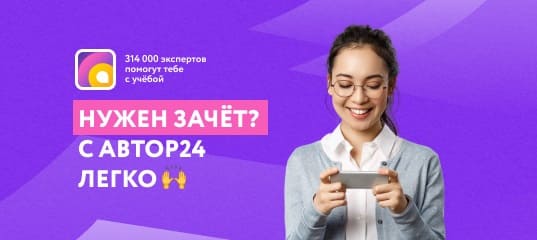
Мы поможем в написании ваших работ!