Text 7. Tests of Portland Cement
Test for soundness (i. e. assurance that the cement will not expand after setting is complete). The cement is made into & plastic mass with a specified water content, put into a small brass cylinder cut through on one side and provided with long wires or needles either side of the cut and boiled for 3 hours after being kept in water at 61 °F for 24 hours. The movement at the end of the needles shall not exceed 10 mm.
Test for setting time. The cement is gauged into a paste with a specified amount of water, put into a shallow circular mould and struck off level, and a needle 1 mm. square weighted to about half a pound is applied repeatedly. When this fails to penetrate completely, the time since gauged is known as the initial set. A needle with an annular attachment is then substituted for the plain needle, so arranged that the needle projects half a millimetre below the annular attachment. When the needle makes an indentation but the annular attachment does not, the time since gauging is known as the final set. The initial set should belong enough to enable mixing, transporting, placing and tamping of the concrete to be completed before setting begins. It should not be less than half an hour for slow-setting cement. (Rapid-setting cements can be supplied for special purposes, but these should not be used for reinforced concrete.) The final set should be not more than 10 hours.
Test for tensile strength. The cement is gauged with a standard sand in the proportion of 1 cement to 3 sand, and with 'a carefully specified quantity of water.
This paste is moulded into moulds of special shape to form a test specimen which is readily held in the jaws of a small testing machine. The central cross-section where fracture occurs is 1 in. square.
The specimens are kept in air (temperature about 61 °F and relative humidity at least 90 per cent) for 24 hours, then removed from the moulds and kept in water (temperature about 61 °F) till tested by breaking. The specimens are held in jaws of specified shape and tension applied at the rate of 100 lb./sq. in. in 12 seconds.
Test for compressive strength. Cubes are compacted by vibration in a special machine for 2 minutes, then kept in air at about 61 °F and 90 per cent relative humidity for 24 hours, and then in water at about 61 °F till tested. They are tested on their sides in a machine applying load at the rate of 5,000 lb./sq. in. per minute. No packing is used.
Some people hold that if the cement passes all the mechanical and soundness tests it is to comply with the chemical requirements, for which the tests are more difficult, especially in the field. The principal object of this test is to guard against an excess or inadequacy of lime in relation to silica, alumina and oxide of iron.
|
|
Vocabulary notes :
test for soundness | випробування на доброякісність |
is made into a plastic mass | його перетворюють на пластичну масу |
test for setting time | випробування на час тужавлення |
the cement is gauged into a paste | цемент перетворюється на тісто |
weighted to about half a pound | навантажена до 1/2 фунта ваги |
fails to penetrate completely | не зможе проникнути повніше |
the Initial set | початкове тужавлення |
slow- (rapid-) setting cement | цемент, що повільно (швидко) тужавіє |
test for tensile strength | випробування на опір розтягу |
a test specimen | зразок для випробування, дослідний зразок |
the central cross-section | центральний попереч ний переріз |
relative humidity | відносна вологість |
pass ... soundness tests | пройти випробування на доброякісність |
guard against an excess or inadequacy | захист від надлишку чи непридатності |
Text 8. Properties And Manufacture of Concrete
A concrete structure, either plain or reinforced, maintains a unique position among the various systems of modern construction. With few exceptions it is the only type of structure that is completely manufactured from its component raw materials on the site of the work. In most instances, the quality of its essential raw materials is decidedly variable. Structures built of steel, stone masonry, or various other materials are composed of elementary units which are partially or entirely prefabricated in factories or shops. These other materials are fitted or assembled on the work by skilled mechanics, but concrete is usually manufactured at the site of the structure by unskilled laborers. The designer of reinforced- concrete structures should remember this. He must know the useful properties and practical limitations of the materials with which his plan will be constructed. With this knowledge he should plan the work in such a manner that desirable results are easily and correctly attained in the field.
|
|
Definition and Description of Concrete. Concrete is an artificial stone, cast in place in a plastic condition. Its essential. ingredients are cement and water which react with each other chemically to form another material possessing structural strength. A mixture of cement and water is termed cement paste. In order to increase the volume of artificial stone produced from a definite amount of cement it is customary to add inert filler materials known as aggregates. A large amount of cement paste to which has been added a small amount of fine aggregate, to produce a mixture of fluid consistency, is called grout. When the amount of fine aggregate is increased to the extent that the mixture loses its fluidity and behaves as a cohesive plastic, the resulting mixture is termed mortar. With the further addition of coarse aggregate, the mixture is called concrete.
It is a custom of long standing to designate these mixtures in terms of the relative volumes of cement, fine aggregate, and coarse aggregate of which they are composed; The ingredients are always indicated in the same order: cement first, fine aggregate next, and coarse aggregate last. For example, a 1:2:4 concrete is a mixture of 1 cu. ft. of cement, 2 cu. ft. of fine aggregate., and 4 cu. ft. of coarse aggregate plus a non-specified amount of water sufficient to produce a plastic consistency. A proportion given as 1:3 is intended to mean a mixture of cement and fine aggregate plus an indefinite amount of water but without the addition of coarse aggregate. Such a mixture would be classified as mortar.
|
|
This system of specifying concrete proportions by volume is rapidly becoming obsolete on major works but is still used for small projects. The current practice of progressive engineers is to indicate the proportions of materials in the same order but by weight and, frequently, to indicate the amount of water to be used.
Water, cement, and aggregates when mixed together in properly predetermined proportions produce concrete that is a plastic ma s capable of being poured or cast into molds. These molds, which are actually called forms, must be built of such size and shape as to restrain the plastic mass until it solidifies. With few exceptions the forms must be constructed in such a manner that the concrete, when poured, will be in its final position in the structure. Besides restraining the plastic mass until solidification occurs, the forms serve a less obvious purpose which should not be overlooked. They support the solidified mass until it has attained sufficient strength to support itself without undue deflection or complete collapse.
Concrete does not solidify or attain appreciable strength instantaneously. The chemical reaction of cement and water is slow and requires time for its completion. The reaction continues for many years. It is frequently divided, for purposes of description, into, three distinct phases. The first, called the initial setting time, requires approximately 45 min. to 8 hr. for completion. During this time, the freshly mixed concrete gradually decreases in plasticity and develops pronounced resistance to flow Disturbance of the mass, or remixing during this time, may cause serious damage. The second phase is an interval during which the concrete may be considered as a soft solid without surface hardness. It will support light loads without indentation, but it is easily abraded. Its surface can be scored, roughened, or otherwise marred without appreciable effort. This phase is frequently termed the interval of final set. Its duration is very indefinite but may be considered to exist for approximately 5 to 20 hr. after the original mixing operation. The third phase is one of progressive hardening and increase in strength. For concrete of good quality this progressive improvement continues indefinitely. It is rapid during early ages until about one month after mixing, at which time the mass has attained the major portion of its potential hardness and strength. After one month the improvement continues at a greatly reduced rate.
|
|
Vocabulary notes :
maintains a unique position | посідає унікальне місце |
which are partially or entirely prefabricated | які частково або повністю попередньо виготовлені |
reinforced-concrete structures | залізобетонні конструкції |
structural strength | будівельна міцність |
it is a custom of long standing | давно вже стало традицією |
are always indicated in the same order | завжди наводяться в тому самому порядку |
a non-specified amount of water | невизначена кількість води |
when mixed together in properly predetermined proportions | коли вони змішуються в заздалегідь визначених пропорціях |
is ... capable of being poured or cast into molds | здатна до розливки чи бетонування в формах |
a less obvious purpose which should not be overlooked | другорядна ціль, яку проте не можна ігнорувати |
the initial setting time | початкове тужавлення бетону |
pronounced resistance to flow | виражений опір деформації |
without indentation | без порушення цілісності, без западин |
is easily abraded | легко шліфується |
final set | остаточне тужавлення |
progressive hardening and increase in strength | поступове твердіння й нарощування міцності |
is rapid during early ages | це відбувається швидко на початкових стадіях |
Text 9. Bricks and Brickwork
The traditional brick of the building trade consists of blocks of clayey earth which have been baked or burnt. Other more modern types include concrete and sand-lime bricks. The quality and properties of a clay brick depend on three factors, namely: a) the chemical and mineralogical composition of the earth used; b) the processes through which it passes prior to burning or baking; c) the temperature of burning and the care with which the burning is carried out.
Material suitable for the making of clay bricks consists essentially of clay and sand, i. e. of silica and alumina. Other constituents include oxides of iron, iron pyrites, chalk or limestone, salt, and small proportions of various minerals which yield manganese, sodium,, potassium and traces of other metals, together with a certain amount of organic matter.
The colour of a brick is largely governed by the chemical composition of the brick earth, but the temperature of burning is also important. Shades of orange and red are found in bricks made from clay containing oxides of iron, the exact shade depending on the amount of the iron and the temperature of burning while blue bricks are made from clay with a high iron content and a very high temperature of, burning. Clays which are free from iron yield white bricks; yellow bricks are obtained by the addition of magnesia to an iron-free clay, but in clamp burnt bricks a yellow colour may be due to sulphur released from the breeze during burning. The colour of facing bricks is often varied by sprinkling selected sand, sometimes with specially added pigments such as manganese dioxide, either on the raw brick or in the brick mould prior to firing. The surface of the brick then takes on the required colour during burning.
The actual making of a brick consists of two main processes, namely: 1) the preparation of the unburnt brick and 2) the burning or baking of the brick. The preparation of the brick may further be considered in three distinct stages, i. e. 1) the preparation of the earth, 2) the shaping of the brick, and 3) the drying of the brick prior to burning.
Preparation of the brick earth. Brick earths are quarried or dug from open pits. Stone-picking, i. e. the removal of large stones, is carried out by hand and then the clay is spread out to expose it to the action of the weather. The weathering is facilitated by placing alternate layers of materials such as sand, chalk or breeze with the brick earth, piled in banks up to a height of some 6 feet. Tempering follows weathering and in big brickfields it is carried out by means of pug-mills
If the clay as dug is not suitable for brickmaking purposes, but requires conversion to malm, it is placed in a wash- mill, immediately it is dug. This machine resembles a pug-mill, but the cylinder is made of brick instead of iron. The other materials to be added, such as sand and chalk, are ground in water and added to the clay in the wash-mill. The mixture is reduced to a liquid of a creamy consistency, known as slurry, and then passed through iron gratings to retain any large particles, and then into settling pits, or backs. The water is allowed to evaporate until the clay is almost solid.
The shaping of the brick may be done by hand or by machine. The hand-made brick is shaped by means of a wooden mould. Thus this mould is larger than the finished burnt brick, to allow for shrinkage.
In moulding the brick, the inside of the wooden mould is sprinkled with either water (slop-moulded) or sand (sand- moulded) to prevent the clay from sticking to the wood. In the best-quality bricks, the sand is carefully chosen so as to give the required colour and finish to the burnt brick.
The moulder throws a clot of clay into the prepared mould, with sufficient force to fill the mould, and removes excess clay from the top with a wooden strike, leaving a level top surface.
Slop-moulded bricks are wetter than sand-moulded ones, and they are left in the mould on covered drying-floors or drying-rooms for some 48 hours before being taken to the hacks for the final airdrying. Sand-moulded bricks are taken directly to the hacks, which are simply long rows of bricks so placed that they are dried by winds, but are protected from rain by pent roofs.
The machine-made bricks may be moulded, pressed or wire-cut. Moulded machine-made bricks go through the same processes as the hand-made bricks, i. e. weathering, grinding and pugging, but the pugged material is mixed with enough water to make it of a workable consistency and this mix is run by machinery into moulds. The moulded brick is dried and fired in the normal way.
A pressed brick made by the stiff plastic, process needs little or no drying when it comes from the press. A suitable clay is ground when dry, and then passes from mixer, into a rough shaper and finally to a die box. Here the brick is pressed, sometimes twice, then fired.
The semi-dry process for pressed bricks consists in running the ground, screened clay mechanically into a container which passes under the press head.
A wire-cut brick is made by extruding the clay from a machine through a shaped die. This gives a continuous block of clay which is cut by wire into brick lengths. This may be done by hand or in more modern types of machinery the cutting may be automatic. Some wire-cut bricks are partially dried and then pressed.
The drying of bricks often takes place naturally in the hacks. Artificial drying is, however, used where waste heat is available from the kilns. Hot air flues or steam pipes are led from closed kilns to the shed in which the bricks are stacked, and this gives quicker drying, in from 8 to 10 days, than if wind drying alone is utilised. In general it is not possible to hasten the process of drying without damaging the quality of the brick, since too rapid drying produces flaws and cracks.
The burning of the bricks may be carried out in either a clamp or a kiln, the latter being either of the intermittent, the continuous or the tunnel type.
Дата добавления: 2019-02-12; просмотров: 244; Мы поможем в написании вашей работы! |
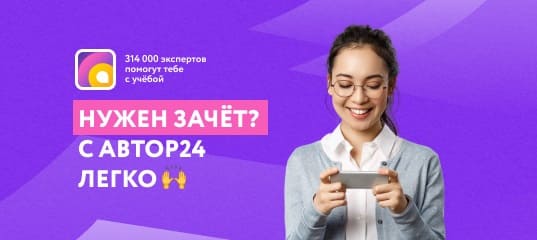
Мы поможем в написании ваших работ!