Теоретические основы химико-термической обработки.
Химико-термической обработкой(ХТО) называется процесс изменения химического состава, микроструктуры и свойств поверхностных слоев деталей. Изменение химического состава поверхностных слоев достигается в результате их взаимодействия с окружающей средой, твердой, жидкой или газообразной, в которой осуществляют нагрев. В результате изменения химического состава поверхностного слоя изменяются также его фазовый состав и микроструктура.
Основные параметры ХТО — температура нагрева и продолжительность выдержки. Основные процессы любого вида ХТО: диссоциация—абсорбция—диффузия.
Диссоциация — получение насыщающего элемента в более активном, атомарном состоянии: 2NH3 = 2N + 3Н2; СН4 = С + 2Н2 и т. д.
Абсорбция — захват поверхностью детали атомов насыщающего элемента.
Диффузия—перемещение захваченного поверхностью атома в глубь изделия.
Термодинамика и кинетика ХТО. Теоретические и экспериментальные данные, полученные с помощью прецизионных методов исследования фазового и химического состава диффузионных слоев, указывают на то, что по многих случаях формирование диффузионного слоя протекает в условиях, значительно отличающихся от равновесных (при больших пересыщениях). В этой связи можно выделить совокупность физико-химических и кинетических факторов, определяющих механизм формирования диффузионного слоя с неравновесными составом и структурой.
|
|
Физико-химические факторы: термодинамические функции фаз в системе взаимодействующих элементов; равновесный состав насыщающей среды; степень неравновесности состояния окружающей среды; адсорбционные характеристики элементов и соединений; структурно-энергетические условия образования фазы на поверхности сплава; степень пластической деформации в зоне диффузии.
Кинетические факторы: соотношение между скоростью поступления элемента на поверхность и скорость его диффузии в твердом материале: скорость реакции взаимодействия на границе сплав - насыщающая среда; скорость нагрева до изотермы процесса и скорость охлаждения по окончании насыщения; продолжительность процесса диффузии на изотерме; соотношение между скоростью диффузии инородного элемента в поверхностном слое и скоростью самодиффузии компонентой насыщаемого сплава.
Учесть влияние всех перечисленных факторов на механизмы формирования диффузионных слоев с помощью теоретических методик исследования не представляется возможным, поэтому при анализе процессов насыщения широко применяют методы планирования эксперимента. Например, с их помощью изучалось влияние теоретических параметров процесса насыщения на скорость формирования диффузионного слоя, его фазовый и химический состав, оптимизировались по свойствам многие способы нанесения диффузионных покрытий, исследовалась корреляционная связь между структурными характеристиками модифицированного слоя и его свойствами и т.д.
|
|
При анализе кинетических закономерностей процессов ХТО обычно используется эмпирическая зависимость глубины диффузионного слоя d от продолжительности t процесса:
δ = κ t n (13.1)
где k и n - постоянные, определяемые экспериментальным путем. 206-208 с.[5].
Теоретические основы термической обработки.
Диаграмма состояния железо—углерод в интервале концентраций от железа до цементита представлена на рис. 13.1. Железоуглеродистые сплавы, содержащие менее 2,14% С, называют сталями, а более 2,14 % С — чугунами.
Фазовые превращения, которые совершаются в стали, также вызваны тем, что вследствие изменившихся условий, например температуры, одно состояние оказывается менее устойчивым, чем другое. Этим и вызываются превращения, протекающие в стали.
Рассматривая структурные превращения в стали, мы прежде всего должны указать, что основными являются три структуры, а переход их из одной в другую характеризуют основные превращения.
|
|
Укажем эти структуры:
аустенит (А) — твердый раствор углерода в γ-железе FeY (С);
мартенсит (М) — твердый раствор углерода в α-железе Fea (С);
перлит (П) — эвтектоидная смесь из одновременно образующихся феррита и карбида: Feα + Fe3 С (ничтожно малой равновесной растворимостью углерода в феррите пренебрегаем).
Различают три группы сталей: эвтектоидные, содержащие около 0,8 % С, структура которых состоит только из перлита; доэвтектоидные, содержащие меньше 0,8 % С, структура которых состоит из феррита и перлита, и заэвтектоидные, содержащие от 0,8 до 2 % С, структура которых состоит из перлита и цементита.
У всех сплавов, содержащих менее 2,14 % С, в результате первичной кристаллизации получается структура аустенита; у всех сплавов, содержащих более 2,14 % С, структура состоит из ледебурита с избыточным аустенитом или цементитом.
Это различие в структуре при высокой температуре и создает существенное различие в технологических и механических свойствах сплавов. Наличие эвтектики делает сплав нековким. Вместе с тем высокоуглеродистый сплав имеет низкую температуру плавления и его применяют как литейный материал.
|
|
Рис. 13.1 - Диаграмма Fe-C
Приведем общепринятые обозначения критических точек.
Критические точки обозначаются буквой А.
Нижняя критическая точка, обозначаемая A1, лежит на линии PSK и соответствует превращению аустенит ↔ перлит. Верхняя критическая точка А3 лежит на линии GSE и соответствует началу выпадения или концу растворения феррита в доэвтектоидных сталях или цементита (вторичного) в заэвтектоидных сталях.
Чтобы отличить критическую точку при нагреве от критической точки при охлаждении, рядом с буквой А ставят букву с, в первом случае и r — во втором.
Следовательно, критическая точка превращения аустенита в перлит обозначается Аr1, а перлит в аустенит Ас1; начало выделения феррита из аустенита обозначается Аr3 ; конец растворения феррита в аустените Ас3 . Начало выделения вторичного цементита из аустенита обозначается также Ar3 , а конец растворения вторичного цементита в аустените — Ас3 (эту точку часто обозначают Аст).
Ниже дана характеристика основных видов термической обработки стали в соответствии с приведенной классификацией.
Основные виды термической обработки стали .
Отжиг— фазовая перекристаллизация, заключающаяся в нагреве выше Ас3 с последующим медленным охлаждением. При нагреве выше Ас1 но ниже Ас3 полная перекристаллизация не произойдет; такая термическая обработка называется неполным отжигом. При отжиге состояние стали приближается к структурно равновесному; структура стали после отжига: перлит + феррит, перлит или перлит + цементит.
Если после нагрева выше Ас3 провести охлаждение на воздухе, то это будет первым шагом к отклонению от практически структурного равновесного состояния. Такая термическая операция называется нормализацией.
Отпуск — нагрев закаленной стали ниже Ас1.
Закалка — нагрев выше критической точки Ас3 с последующим быстрым охлаждением. При медленном охлаждении аустенит распадается на феррит + цементит при Аr1. С увеличением скорости охлаждения превращение происходит при более низких температурах. Феррито-цементитная смесь по мере снижения Аr1 становится все более мелкодисперсной и твердой. Если же скорость охлаждения была так велика и переохлаждение было так значительно, что выделение цементита и феррита не произошла то и распада твердого раствора не происходит, а аустенит (γ-твердый раствор) превращается в мартенсит (пересыщенный твердый раствор углерода в α-железе). Неполная закалка — термическая операция, при которой нагрев проводят до температуры, лежащей выше Ас1 но ниже Ас3 и в структуре стали сохраняется доэвтектоидный феррит (заэвтектоидный цементит).
Распад аустенита
Превращение аустенита в перлит заключается в распаде аустенита— твердого раствора углерода в γ-железе, на почти чистое α -железо и цементит:
Fev (С) → Fea + Fe3C.
Превращение может начаться не в точке А1, а при некотором переохлаждении, когда свободная энергия феррито-карбидной смеси (перлита) окажется меньшей, чем свободная энергия аустенита.
Чем ниже температура превращения, тем больше переохлаждение, тем больше разность свободных энергий, тем быстрее происходит превращение.
В случае перлитного превращения образуются фазы, резко отличающиеся по составу от исходной: феррит, почти не содержащий углерода, и цементит, содержащий 6,67 % С. Поэтому превращение аустенит → перлит сопровождается диффузией, перераспределением углерода. Скорость диффузии резко уменьшается с понижением температуры, следовательно, с этой точки зрения увеличение переохлаждения должно замедлять превращения.
Описанное находит отражение на диаграмме изотермического распада аустенита.
На рис. 13.2 показана диаграмма изотермического распада аустенита для доэвтектоиднои стали в полном виде. На ней приведены кривая начала выделения феррита, кривая начала и кривая конца превращения аустенита в перлит, а также горизонтали A3, А1, Мн и Мк .
По этой диаграмме основные сведения об изотермическом превращении можно получить для данной стали при любой степени переохлаждения. Например, при переохлаждении до 650 °С превращение начинается через некоторое время выделением из раствора феррита. Феррит выделяется в течение определенного времени, после чего начинается распад аустенита на перлит, который заканчивается на кривой, характеризующей конец превращения. Если быстро охладить аустенит до 550 °С, то превращение начнется прямо с образования перлита. Превращение при 550 °С протекает значительно скорее, чем при 650 °С.
Если взять не доэвтектоидную, а заэвтектоидную сталь, то при малых переохлаждениях распаду аустенита будет предшествовать предварительное выделение цементита.
Если же охлаждать аустенит с большой скоростью, то превращение в верхнем районе температур не успеет произойти, аустенит переохладится до низких температур и произойдет его превращение в мартенсит, т. е. такое охлаждение приведет к закалке. Следовательно, чтобы закалить сталь, ее следует охлаждать с такой скоростью, чтобы не успели пройти процессы распада аустенита в верхнем районе температур.
Все скорости, большие, чем vK ( vK — кривая охлаждения, касательная к выступу С-кривой), приводит к образованию мартенсита, а меньшие — к распаду аустенита в верхнем районе температур.
Минимальная скорость охлаждения, необходимая для переохлаждения аустенита до мартенситного превращения, называется крити ческой скоростью закалки. Чтобы закалить сталь, ее следует охлаждать со скоростью не меньшей, чем критическая. Чем правее лежит кривая начала превращения, тем меньше величина vK . Другими словами, чем медленнее происходит превращение аустенита в перлит, тем легче переохладить аустенит до температур мартенситного превращения и тем меньше критическая скорость закалки.
Если охлаждать со скоростью, немного меньшей критической, то аустенит в верхнем районе температур превратится лишь частично,и структура будет состоять из продуктов превращения в верхнем районе температур (троостит) и мартенсита.
Рис.13.2- Диаграмма изотермического распада аустенита для доэвтектоидной стали (0,4 % С).
Для более точной оценки превращений, совершающихся при непрерывно меняющейся температуре, пользуются так называемыми термокинетическими или анизотермическими диаграммами превращений аустенита, диаграммами, характеризующими превращение аустенита при различных скоростях охлаждения. 142-244 с.[6].
Дата добавления: 2019-02-12; просмотров: 215; Мы поможем в написании вашей работы! |
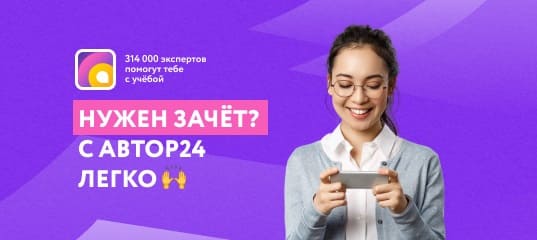
Мы поможем в написании ваших работ!