Choosing a perforation strategy
The ultimate success of the well- its productivity and life expectancy –rests on making the best possible connection between the wellbore and formation. Each of the three main types of completions- natural, stimulated and sand control – has different perforating requirements. In the natural completion (in which perforating is followed directly by production) many deep shots are most effective. In stimulated completions – hydraulic fracturing and matrix acidizing- a small angle between shots is critical to effectively create hydraulic fractures and link perforations with new pathways in the reservoir. And in gravel packing, many large-diameter perforations effectively filled with gravel are used to keep the typically unconsolidated formation from producing sand and creating damage that would result in large pressure drops during production. To meet the broad requirements of perforating, there are many perforating guns and gun conveyance systems. Optimizing perforating requires selection of hardware best suited to the job.
Natural Completion is often defined as that in which little or no stimulation is required for production. This approach is usually chosen for reservoirs that are less prone to damage, have good transmissibility and are stable. Of primary importance in selecting the perforating gun are its depth of penetration and effective shot density. Depth is important because the deeper the perforation, the greater the effective wellbore radius; also flow is less likely to be influenced by formation damaged during drilling. Shot density also ranks high because more holes mean more places for hydrocarbon to enter the wellbore and a greater likelihood that perforations will intersect productive intervals. After shot density and depth of penetration, most important is phasing because when properly chosen, it provides hydrocarbon with the most direct path to the wellbore.
A key consideration in perforation design of natural completions is the selection of overbalance versus underbalance perforating. Overbalance means the pressure of wellbore fluids exceeds reservoir pressure at the time of perforating. Under this condition, wellbore fluids immediately invade the perforation. For this reason, clean fluids without solids are preferred to prevent plugging o perforations. Cleanup can occur only when production begins. Wells that have sufficient reservoir pressure to flow to surface unassisted are completed in underbalance conditions. Underbalance provides cleaner perforations – therefore better production – and because of greater availability of gun systems that allow it. The question is how much underbalance is appropriate. Excessive underbalance risks mechanical damage to the completion or test string by damaged or stuck casing or a packer. It can also encourage migration of fines within the reservoir, reducing its permeability.
|
|
Stimulated Completion falls into two categories: acidizing and hydraulic fracturing. Occasionally, the two are combined in an acid-frac, which improves productivity by using acid preventing full closure. Success of stimulaion depends largely on how well the perforation allows delivery of treatment fluids and frac pressures into the reservoir. Because these fluids and pressure-induced fractures are intended to move beyond the perforation, shot phasing, density and hole diameter are of higher priority than depth of penetration. Underbalance perforating is often used because cleaner perforation tunnels give fluids more direct paths to the reservoir. In some cases, such as TCP (tubing conveyed perforator) with high shot density guns, underbalance can be increased to where stimulation is not required to improve productivity.
Perforation plays a key role in the success of hydraulic fracturing. HF has two main steps: fracture creation by application of pressure, and injection of fluid carrying proppant, which holds open the fractures to allow production. Once the fracture is created, perforations provide the entrance to the fracture for the proppant. Perforation diameter must be sufficient to prevent “bridging”, accumulation of proppant that blocks the entrance hole, preventing further treatment.
Sand Control Completion is a problem in weak or unconsolidated sandstones. The objective of a sand control completion is to eliminate sanding while maintaining a production rate. Near the wellbore, sand movement can reduce permeability locally. Produced sand can erode downhole and surface equipment and its removal ca be costly. In sufficient quantities, sand can plug the completion or surface facilities. An objective of perforating in these highly productive and often unconsolidated sands is t reduce the near-wellbore pressure gradient during production.
|
|
Once it has been established that at planned production rates sand is likely to be produced, the next step is to choose a completion strategy to limit sanding. A first option is to minimize shocks to the reservoir by changing drawdown and production rate slowly and I small increments. Production rate may be reduced to ensure that drawdown is below the point at which the formation grains become detached. The most popular options for completing sand-prone reservoirs physically restrain sand movement. The main classes of completion are resin injection, slotted liners and gravel packing.
Perforation Cleaning
The high-pressure jet from a perforating gun pierces the casing and forms a hole by pulverizing cement and formation into compacted particles. Cement and material from the jet charge are mixed with the formation material in the compacted zone while loose debris fills the perforation tunnel. It is necessary to remove this debris from the perforation tunnel to increase the probability of success in sand consolidation or gravel packing.
Perforation-cleaning methods include:
· Backflow – flowing the well may not clean up more than a few perforations and, if enough differential is available to purge debris from the perforations, the well may sand up. Backflow must be done slowly and carefully.
· Underbalance – perforating with hydrostatic pressure less than formation pressure allows tunnel debris to be carried into the wellbore with the first surge of fluid from the formation.
· Backsurging – techniques dislodge gun debris and loose material from perforation tunnels by sudden exposure of a perforated zone to an open chamber at atmospheric pressure. The differential pressure created causes formation fluids to surge through the perforations into the casing, flushing the perforation tunnels. It has proved to be very successful in improving productivity.
· Perforation washing – is achieved by straddling a small increment of the perforated interval with a special tool and injecting non-damaging fluids into the perforations in the increment. The fluid circulates outside the casing and back through the perforations nearest the tool seals, removing debris and formation sand from the perforations and from behind the casing. The tool is moved in increments equal to the seal spacing until the entire perforated interval is washed. After the perforations are washed or surged and debris is circulated out, a positive-depth indicator is placed in the well below the perforations to establish a reference point from which the string is accurately spaced out. This is especially important in multiple completions with closely spaced producing intervals.
|
|
· Overflush – completion or workover brine should not be used as an overflush for mud acid because of the possible precipitation of sodium, potassium o calcium fluosilicates. The use of dilute HCI, ammonium-chloride solution, light oil or nitrogen as the overflush agent is recommended.
Sand Control
Sand control are those procedures used to minimize or prevent the entry of unconsolidated sand or related sediments into the wellbore during production operations. Control of sand has been a major problem in the production of petroleum since the first wells started producing over a century ago. It is usually associated with shallow to medium- depth well in poorly compacted formations. Sand problems may result in loss of production, possible formation damage, increased abrasion and wear on all tools and equipment, possible casing collapse and severe damage to surface equipment. In order to control and reduce sand problems, three basic mechanisms are employed:
1 minimizing drag forces when producing a well;
2. mechanical bridging;
3. physically increasing the strength of formation around the wellbore.
Sand problem wells can generally be divided into two basic types:
- heaving wells, in which large amounts of sand suddenly enter the wellbore causing plugging up of perforations, accumulation at the valves and operating parts of any subsurface pumping units;
- constant sand producers , in which fluids, constantly carrying sand, increase wear and erosion on all major areas of the well, including the producing zone, the tubing arrangement, wellhead and any artificial lift equipment, as well as the field processing and storage facilities.
|
|
Basic sand control methods
Mechanical method can be done using two methods:
A perforated steel liner – a perforated steel liner is inserted at the bottom of the production string. The liner acts as a sieve, minimizing or preventing entry of sand particles into the wellbore.
Gravel packing – is a method in which a perforated steel liner is inserted at the bottom of the production string and then surrounded by small sized gravel that further restricts the migration of any into the well. The gravel is suspended in viscous fluid and pumped under pressure behind the steel line. This creates a second barrier beyond the liner surrounding the wellbore.
- the production zone is cleaned out in preparation or inserting the gravel and liner. This may be accomplished by reverse circulation, as the tubing and packer are moved past the perforations.
- once the zone has been prepared, the gravel – bearing fluid is slowly pumped down the production string and squeezed through the perforations, filling the cavity spaces within and near the producing zone.
- the liner or screen is the inserted into the wellbore and washed through the previously positioned gravel inside the casing, until it reaches a position opposite the perforations. The liner is then set.
- after the screen and gravel are in place, the washpipe is removed. The production string is set and the well is returned to production.
Chemical method : consolidation (resin injection) – consolidation is a sand control procedure in which epoxy resin is uniformly injected into the area around the producing zone in the wellbore. After setting, it forms a consolidated mass, strengthening the formation and reducing the migration of any sand.
Workovers
The term workover is used to refer to any kind of oil well intervention involving invasive techniques, such as wireline, coiled tubing or snubbing. More specifically though, it will refer to the expensive process of pulling and replacing a completion.
Workover rig
Reason to perform a workover
Workovers rank among the most complex, difficult and expensive types of wellwork there is. They are only used performed if the completion of a well is terminally unsuitable for the job at hand. The production tubing may have become damaged due to operational factors like corrosion to the point where well integrity is threatened. Downhole components such as tubing retrievable downhole safety valves or electrical submersible pumps may have malfunctioned, necessitating replacement.
In other circumstances, the reason for a workover may not that the completion itself is in a bad condition, but that changing reservoir conditions make it unsuitable. For example, a high productivity well may have been completed with 5½" tubing to allow high flow rates (a narrower tubing would have unnecessarily choked the flow). Some years on, declining productivity means the reservoir can no longer support stable flow through this wide bore. This may lead to a workover to replace the 5½" tubing with 4½" tubing. The narrower bore makes for a more stable flow.
Operation
Before any workover, the well must first be killed. Since workovers are long planned in advance, there would be much time to plan the well kill and so the reverse circulation would be common. The intense nature of this operation often requires no less than the capabilities of a drilling rig.
The workover begins by removing the Xmas tree and lifting the tubing hanger from the wellhead and thus beginning to pull the completion out of the well. The string will almost always be fixed in place by at least one production packer. If the packer is retrievable it can be released easily enough and pulled out with the completion string. If it is permanent, then it is common to cut the tubing just above it and pull out the upper portion of the string. If necessary, the packer and the tubing left in hole can be milled out, though more commonly; the new completion will make use of it by setting a new packer just above it and running new tubing down to the top of the old.
Workovers on casing
Although less exposed to wellbore fluids, casing strings too have been known to lose integrity. On occasion, it may be deemed economical to pull and replace it. Because casing strings are cemented in place, this is significantly more difficult and expensive than replacing the completion string. If in some instances the casing cannot be removed from the well, it may be necessary to sidetrack the offending area and recomplete, also an expensive process. For all but the most productive well, replacing casing would never be economical.
Snubbing
Snubbing is a type of heavy well intervention performed on oil and gas wells. It involves running the BHA on a pipe string using a hydraulic workover rig. Unlike wireline or coiled tubing, the pipe is not spooled off a drum but made up and broken up while running in and pulling out, much like conventional drill pipe. Due to the large rigup, it is only used for the most demanding of operations when lighter intervention techniques do not offer the strength and durability. Unlike conventional drilling and completions operations, snubbing can be performed with the well still under pressure (not killed). When done so, it is called hydraulic workover. It can also be performed without having to remove the Xmas tree from the wellhead.
Rigup
A snubbing rigup is a very tall structure. It consists of a hydraulically powered snubbing unit, which provides the force on a pipe, above string of multi-layered pressure control components.
At the top of the snubbing unit is the basket, which serves as the control post for the rigup. Below the basket are the hydraulic jacks, which power the pipe into an out of the hole. It consists of two mechanisms for applying force to the pipe in either direction. Each mechanism consists of traveling and stationary slips. The traveling slips are used to move the pipe, while the stationary slips are used to hold the pipe while the traveling slips are repositioned between strokes.
Primary pressure control during snubbing operations is provided by a self-energizing stripper and through an assembly of stripping rams. The stripping rams consists of two sets of rams, one on top of the other. There are opened one at a time to allow the collar of the connections between joints of pipe to pass through the rams. Below the stripping rams are the safety rams, which may consist of a shear/blind blowout preventer and an annular BOP. The tertiary barrier, a shear/seal BOP, sits below this directly above the Xmas tree.
Stripping the pipe
Unlike coiled tubing or wireline, where the wire or tubing is always the same diameter allowing for a single unmoving primary barrier (stuffing box or stripper), snubbing uses a pipe, which will have an enlarged collar at the connection between the joints. Therefore, the pressure control system must be able to accommodate this variable diameter. The stripping rams accomplish this. The first stage of lowering a collar through the stripping system is to close the lower rams so as to seal off the mechanism above from wellbore pressure. The space between the rams can then be bled off allowing the upper rams to be opened. The collar can then pass through the opened upper rams. Once the collar is in between the rams, the upper rams and closed and pressure is equalised either side of the lower rams. The lower rams are then safely opened and the collar is lowered through the rams.
This process is repeated as successive collars are lowered into the well. When pulling out of hole,
Heavy-pipe and light-pipe
Because snubbing is normally done under pressure, initially, the weight of pipe in wellbore is less than the force due to the wellbore pressure. This is light-pipe. This means that downward force is required on the pipe to force it in against resistance. Once a sufficient amount of pipe has been run in hole, the weight becomes sufficient to overpower the wellbore pressure and the pipe naturally wants to fall in the hole. This is heavy-pipe. At this point, the snubbing mechanism is changed over to the one, which provided upward force to hold the pipe and lower it controllably in the well.
When pulling out of hole, upward force is initially used to lift the pipe until the equilibrium point, when the downward force is used to prevent wellbore pressure from blowing the light-pipe out of hole.
Risks
The more complex method of pressure control, as compared to coiled tubing and wireline, naturally invites more opportunity for things to go wrong. One such peril was seen in June 2007 on the Shearwater platform. Snubbing was being used to clean out large pebble, which had entered the well through a collapsed liner. While pulling out of hole, one stripping ram was not opened sufficiently and a collar on the pipe string caught on the ram. The excessive force applied to the pipe caused it to break apart, dropping the string below the failure into the well. In the time it took to prepare to fish out the pipe, the pebbles in the process of being circulated out, settled on the pipe, preventing successful fishing.
Coiled Tubing
Coiled tubing refers to metal piping, normally 1" to 2" in diameter, used for interventions in oil and gas wells, which comes spooled on a large drum. The main benefits over wireline are the ability to pump chemicals through the coil and the ability to push it into hole rather than relying on gravity. However, it consumes more space and offshore requires a larger and more robust rig, which can make it much more expensive on small platforms, which could support wireline but not coil, and subsea wells, where wireline can be run off a smaller and cheaper light intervention vessel. Onshore, they can be run using smaller service rigs and for light operations, the mobile self-contained coiled tubing rig.
The tool string at the bottom of the coil is often called the bottom hole assembly (BHA). It can range from something as simple as a jetting nozzle, for jobs involving pumping chemicals or cement through the coil, to a larger string of logging tools, depending on the operations.
Uses
Circulation
The most popular use for coiled tubing is circulation. A hydrostatic head (a column of fluid in the well bore) may be inhibiting flow of formation fluids due to its weight (the well is said to have been killed). The safest (though not the cheapest) solution would be to attempt to circulate out the fluid using a gas, frequently nitrogen. By running in coiled tubing to the bottom of the hole and pumping in the gas, the kill fluid can be forced out to production. Circulating can also be used to clean out light debris, which may have accumulated in the hole.
Pumping
Pumping through coiled tubing can also be used for dispersing fluids to a specific location in the well such as for cementing perforations or performing chemical washes of downhole components such as sandscreens. In the former case, coiled tubing is particularly advantageous compared to simply pumping the cement from surface as allowing it to flow through the entire completion could potentially damage important components, such as the downhole safety valve.
Drilling
A relatively modern drilling technique involves using coiled tubing instead of conventional drill pipe. This has the advantage of required less effort to trip in and out of the well (the coil can simply be run in and pulled out while drill string must be assembled and dismantled joint by joint while tripping in and out). Instead of rotating the drill bit by using a rotary table or top drive at the surface, it is turned by a downhole motor, powered by the motion of drilling fluid pumped from surface.
Logging and perforating
These tasks are by default the realm of wireline. Because coiled tubing is rigid, it can be pushed into the well from surface. This is an advantage over wireline, which is gravity dependent and depends on the weight of the toolstring to be lowered into well. For highly deviated and horizontal wells, gravity may be insufficient. However, roller stem and tractors can often overcome this disadvantage at greatly reduced cost, particularly on small platforms and subsea wells where coiled tubing would require mobilising an expensive mobile drilling rig. The use of coiled tubing for these tasks is usually confined to occasions where it is already on site for another purpose, e.g. using it for a logging run following a chemical wash.
Coiled tubing rigup
The main engine of a coiled tubing intervention is the injector head. This component contains the mechanism to push and pull the coil in and out of hole. An injector head has a gooseneck on top, which is simply a curved guide beam, which threads the coil into the injector body. Below the injector is the stripper, which contains rubber pack off elements, which seal tightly around the tubing to isolate the pressure in the well.
Below the stripper is the blowout preventer, which provides the ability to cut the coiled tubing pipe and seal the well bore (shear-blind) and hold and seal around the pipe (pipe-slip). Older quad-BOPs have a different ram for each of these functions (blind, shear, pipe, slip). Newer dual-BOPs combine some of these functions together to need just two distinct rams (shear-blind, pipe-slip).
The BOP sits on top of the riser, which provides the pressurized tunnel down to the top of the Xmas tree. Just between the Xmas tree and the riser is the final pressure barrier, the shear-seal BOP, which can cut and seal the pipe.
Onshore light coiled tubing unit
A Coil Tubing Unit is a self contained multi-use machine that can approximately do anything a conventional service rig is capable of - with the exception of tripping jointed pipe. There are generally two types in shallow service - Arch and Picker. One uses a vertical elevator with a horsehead on top, and an injector hanging by winch line off it. The Picker units have a picker, and a horsehead bolted directly to the injector.
These type of coil tubing units have a permanent drum mounted amidships (They are generallly tandem drive Class 3 trucks, 40 feet long or so), and a large air compressor, usually good for 2500 psi at 660 CFM, mounted between the drum and cab. In lower pressure, natural gas wells, with no hydrocarbons, the compressor is actually used to blow air to bottom hole in these live natural gas wells, for the purpose of "cleaning out" mud and fluid from the wellbore and perforations. In higher pressure wells, or oil wells, nitrogen or carbon dioxide is the preferred and much safer method.
Wireline
The term wireline usually refers to a cabling technology used by operators of oil and gas wells to lower equipment into the well for the purposes of a well intervention. In its simplest and most used form, the wireline simply consists of a single strand of metal wire most commonly 0.108" or 0.125" in diameter (sometimes referred to as slickline). In other cases, the wire will be composed of braided strands, rendering it stronger and heavier (called braided line). Braided line can contain an inner core of insulated wires which provide power to equipment located at the end of the cable (called electric line or E-line) and provides a pathway for electrical telemetry for communication between equipment at each end of the cable. The first use of wireline in a wellbore was as a measuring device. Measuring systems using rope or flat section steel tape, were over time replaced by wire
Uses
Slickline
The nature of slickline requires any tools to be able to operate independently of electrical communication from surface. This limits slickline to jobs such as setting plugs and straddes, which require mechanical action. Some completion components may be deployed and retrieved on slickline such as wireline retrievable safety valves, downhole gauges (assuming that communication and power requirements met by other means) and gas lift valves. Slickline can also be used for fishing, the process of trying to retrieve other equipment and wire, which has been dropped down the hole.
Braided line
Braided line is generally used when the strength of slickline is insufficient for the task. Most commonly, this is for heavy fishing such as retrieving broken drill pipe.
Electric line
Electric line is used for well logging, involving deploying sensory tools designed to provide some information about the properties of the well. Electric line operations can be divided in two domains : Reservoir Evaluation (or "open hole"), which operates in the borehole just after it has been drilled, and Production (or "cased hole"), which operates after the well has been completed and lined with a metal pipe (the "casing").
Reservoir evaluation focuses in recording the properties of the formation around the borehole (density, porosity, oil and water saturation, moveability of hydrocarbons, presence of fractures, etc.) while production logging is here to maximize the production of an already-completed well through perforation services, plug setting and production fluid evaluation.
The recent developments of wireline tractors have allowed wireline to be used in highly deviated and horizontal wells, operations which historically have required coiled tubing or drillpipe-conveyed logging (TLC - "tough logging conditions"). These require a source of electrical power and so are always run on E-line. Tractors also enable wireline to expand into the operation of milling by being able to provide rotary motion.
Wireline images
![]() | ![]() | ![]() | ![]() |
![]() |
Oil Recovery
Drive mechanisms
The term “oil pools” is used to refer to deposits of petroleum as though there were underground lakes of oil. A more accurate term, however, is one that is often used in the petroleum industry- oil sands. In other words, the deposits are more often like piles of sand or porous rock that have been saturated with oil. Oil does not really flow rapidly through sand or rock, so it must be pushed or driven. Natural flow is when the reservoir delivers the fluid to the wellbore. Sufficient pressure energy is needed to lift the fluid to the surface. There are three types of natural drives, as the forces that push the oil are called. Each drive involves the gas and water that are almost always found with oil.
Дата добавления: 2019-01-14; просмотров: 278; Мы поможем в написании вашей работы! |
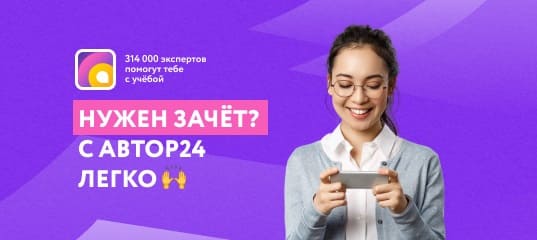
Мы поможем в написании ваших работ!