Определение режимов резания аналитическим методом
2.1 Глубина резания:
t = мм, где
D = 25 мм - диаметр фрезы
t = = 12,5 мм
2.2 Подача [5], [6]:
мм/об, где
мм/об - табличное значение подачи;
- поправочный коэффициент подачи.
- коэффициент, зависящий от глубины фрезерования;
- коэффициент, зависящий от жесткости технологической системы;
- коэффициент, зависящий от материала режущей части инструмента;
- коэффициент, зависящий от типа обрабатываемого отверстия;
- коэффициент, зависящий от марки обрабатываемого материала
мм/об
2.3 Скорость резания [5], [6]:
м/мин, где
м/мин - табличное значение скорости резания;
- коэффициент, завиясящий от материала обрабатываемой детали;
- коэффициент, завиясящий от материала режущей части инструмента;
- коэффициент, завиясящий от типа обрабатываемого отверстия;
- коэффициент, завиясящий от условий обработки;
- коэффициент, завиясящий от длины сверления
м/мин
2.4 Частота вращения шпинделя:
мин-1, где
м/мин - скорость резания;
мм - диаметр сверла
мин-1
В соответствии с паспортными данными станка [5, стр. 165] Принимаем n = 355 мин-1
Расчет приспособления на точность
Согласно операционному эскизу рис.2 требуется обработать радиуса, расположенный на фланце , выдержав размер: радиус - 50 мм, диаметр 76 мм. Допуск симметричности для размера ϕ76 составляет 0,16. Относительно этого параметра ведется расчет на точность.
|
|
Рис.2. Операционный эскиз заготовки
Рассчитать на точность выполнения условия симметричности размера
Проверка допуска на симметричность
Т=0,16 мм
Погрешность выполнения размера , мм
= 1,2
=
= 1,2
- погрешность обработки – погрешности технологической системы СПИД, принимаем
= 0,02 мм
- погрешность базирования равна
= 0 мм
- погрешность закрепления
= 0 мм
- погрешность износа приспособления принимаем т.к грани изнашиваются равномерно.
= 0 мм
- погрешность изготовления приспособления
= 0,02 мм т.к
= 0.025 мм т.к
- погрешность установки тисков на станке
= 0 мм
1,2
= 1,2
= 0,003 мм
= 0,003 ≤ Т= 0,16 – условие обеспечение допуска выполняется.
Расчет приспособления на надежность закрепления заготовки
|
|
Конструирование и расчет приспособления
На операцию 035 спроектировано приспособление.
7.1.1 Расчет на усилие зажатия
Определение силы резания при фрезерование
Материал заготовки – Серый чугун 30
σв= 280 МПа
HB 10 -1 =217 МПа
Станок фрезерный с ЧПУ МА655
Фреза 2223-0147 ГОСТ 17026-71
Глубина резания при фрезерование t, мм
t= 12,5 мм
Диаметр фрезы D, мм
D = 25 мм
Подача S, мм/об
S = 0,4 мм/об (выбрана из операционной карты)
Сила резания P z, Н
Pz = [17]
Pz =
Сила резания P у,Н = 395 Н [26]
3.1.2 Определение усилия зажима
Условия неподвижности заготовки в процессе обработки – условие статистического равновесия;
М = М
×К, где
М - момент трения
Сумма проекций сил по оси х (Fx), уравнение:
∑F = 0 = Q-R-P
= 0
Силы, действующие на тело:
W = R × sin45
= (P
- Q)× sin45
W = Q × sin45
= (P
+ R)× sin45
Силы трения, уравнения:
Fтр = W
× f
Fтр = W
× f
f = 0.16
Усилие зажима (Q) = =
= 2765,6 Н
∑М = 0
Pz ×Кз + R×l2×Кз - Py×l1×Кз-Q×l2×Кз+2Fтрwr×l3+2 FтрwQ× l3 = 0
Pz ×Кз + R×l2×Кз - Py×l1×Кз-Q×l2×Кз-2(Pz-Q)×l3-2(Pz+Q)× l3 = 0
Pz ×Кз + R×l2×Кз - Py×l1×Кз ≤ Q×l2×Кз+2(Pz-Q)×l3+2(Pz+Q)× l3
1180 ×1,5 + 2765,6× 80×1,5 - 395×90×1,5 ≤ 2765,6 ×80×1.5 + 2×(1180-2765,6) × 45 + 2×(1180+2765,6)
|
|
2803,17 Н ≤ 5442,72 Н
Следовательно, неподвижность данной заготовки обеспечивается.
3.1.3 Расчет параметров цилиндра
Расчет предварительного диаметра поршня пневмоцилиндра, необходимого для создания усилия закрепления заготовки
Dц =
Где ρ = 0,4 МПа – давление в сети подачи сжатого воздуха,
η = 0,85 – коэффициент, учитывающий потери на трение.
Dц = = 101,79 мм
Принимаем диаметр цилиндра приспособления равным 110 мм
D = 110 мм
dшт = 20 мм
3.1.4 Определяем силу на штоке Ри:
Для цилиндра двустороннего действия выходное усилие на штоке Ри при уплотнении поршня одним круглым резиновым кольцом
Ри = (
)
Ри = (
)
0.4
0.85= 3122,73 H
Ри = 3122,73 Н > Q = 2765,6 Н
При D = 110 мм усилие на штоке Pи больше, чем необходимое усилие зажима Q, значит, заготовка при обработке будет гарантированно закреплена.
3.1.5 Расчет на точность
Необходимо произвести расчет на точность для фрезерования контура. Допуск симметричности обработанной поверхности заготовки не более Т = 0,05 мм.
𝜔 = 1,2 =
𝜔 = 1,2
- погрешность обработки – погрешности технологической системы СПИД, принимаем
ωб - погрешность базирования равна наибольшему зазору между диаметрами заготовки базовой поверхности приспособления.
|
|
ωб = 0 мм
ωз - погрешность закрепления. ωз = 0 мм, так как механизированный зажим обеспечивает постоянство усилия зажима.
Погрешность износа приспособления ωи при базировании равна нулю, т.к грани изнашиваются равномерно. Принимаем
ωи = 0 мм
Погрешность установки приспособления ωу.пр равна нулю.
=
= мм
Условие точности обработки заготовки в приспособлении выполняется
Используемые источники
1.Справочник технолога машиностроителя. В 2-х т. Т. 2/ под ред. А. Г. Косиловой и Р. К. Мещерякова. - 4-е изд., перераб. и доп. - М.: Машиностроение, 1986. 496 с., ил.
2.Гжиров Р. И. Краткий справочник конструктора: Справочник - Л: Машиностроение, Ленингр. отд-ние, 1984. - 464 с., ил.
3.Белоусов А. Л. Проектирование станочных приспособлений: Учебное пособие для учащихся техникумов. - 3-е изд., перераб. и доп. - М.: Высшая школа, 1980. - 240 с., ил.
4.Методические указания к выполнению контрольной работы по проектированию станочных приспособлений для студентов специальностей: 7.090202, 7.090203, 7.090204 для всех форм обучения / сост. Г.С.Чумаков, отв. за выпуск А.У. Захаркин Сумы 1997 г. - с. 34.
5.Горбацевич А. Ф., Шкред В. А. Курсовое проектирование по технологии машиностроения: [Учеб. пособие для машиностроит. спец. вузов]. - 4-е изд., перераб. и доп. - мн.: Выш. школа, 1983. - 256 с., ил.
6. Горошкин А.К., Приспособления для металлорежущих станков , справочник - 7 изд., перераб. и дополн. - М.: Машиностроение , 1979г.
Дата добавления: 2019-01-14; просмотров: 147; Мы поможем в написании вашей работы! |
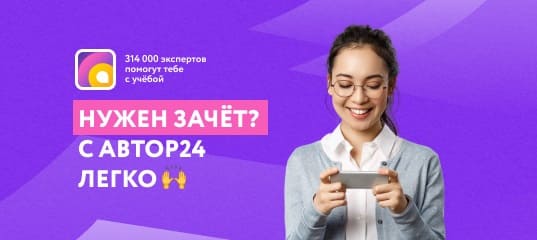
Мы поможем в написании ваших работ!