Мощность машин и её преобразование в механизмах 10 страница
Цементация (науглероживание) – насыщение углеродом поверхностных слоев на заданную глубину (после цементации рекомендуется закалка и низкий отпуск). Назначение: Получение поверхностного слоя высокой твердости 500HV-600HV, износостойкости при наличии вязкой сердцевины деталей. При таком варианте термообработки цементируемый слой может наноситься только на отдельные участки детали. На цементацию поступают детали после механообработки, так как после нее допускается только операция шлифования. Для цементации чаще всего используют низкоуглеродистые легированные стали. В результате на их поверхности образуется диффузионный слой, химический состав которого сильно зависит от глубины. Это можно объяснить тем, что проникновение диффундирующего элемента в глубинные слои оказывается затрудненным. Цементируют детали из низкоуглеродистых сталей марок 15, 20, 20Х, 12ХНЗА и других
Нитроцементация – процесс диффузионного насыщения поверхностного слоя углеродом и азотом, протекающий при температуре T=840…860 0C.
Азотирование – термохимическая обработка, при которой поверхностный слой насыщается азотом на заданную глубину. Назначение: повышение поверхностной твердости 800HV-1200HV, износостойкости, предела выносливости, коррозионной и эрозионной стойкости деталей. Азотирование сильно повышает твердость поверхности, ее износостойкость, предел выносливости и стойкость к коррозии, причем твердость сохраняется до температуры 5000С. Азотируют детали - из сталей марок 38Х2МЮА, 38Х20 и др.
|
|
Цианирование высокотемпературное (азотонауглероживание) – термохимическая обработка, при которой поверхностный слой одновременно насыщается углеродом и азотом. Назначение: Повышение поверхностной твердости 650HV-850HV, износостойкости, предела выносливости при изгибе и контактной выносливости деталей из низкоуглеродистых и среднеуглеродистых сталей (например, 35, 40, 35Х, и др.).
Борирование – термохимическая обработка, при которой поверхностный слой насыщается бором при нагревании в соответствующей среде. Глубина насыщения 0,2–1 мм. После борирования целесообразно проводить закалку и отпуск для упрочнения сердцевины. Назначение: Повышение износостойкости, твердости 1500HV-1800HV, окалиностойкости и коррозионной стойкости, теплостойкости.
Механическое упрочнение поверхностных слоев деталей методами пластического деформирования (наклепом) производят накаткой роликами или шариками, чеканкой, дробеструйным способом и др. При этом повышается предел выносливости сталей. Так упрочняют детали, работающие в ответственных узлах (гребные винты, канаты, валы, рессоры и др.).
|
|
Электротермическая обработка - термическая обработка, материалов с использованием электрического нагрева (индукционного, контактного и др.); позволяет применять большие скорости нагрева, а также нагревать отдельные участки изделия либо только его поверхностный слой.
Термомагнитная обработка - разновидность термической обработки, позволяющая улучшить некоторые магнитные свойства металлов и сплавов в результате охлаждения изделий в магнитном поле.
Патентирование - термическая обработка стальной проволоки - включает нагрев (до 870°С…950°С), охлаждение (до 450°С…550°С) обычно в солевом или свинцовом расплаве, выдержку и дальнейшее охлаждение на воздухе или в воде.
Цель патентирования - улучшение пластичности металла.
В последние годы широкое распространение получает обработка поверхностей деталей концентрированными потоками энергии (лазерная, плазменная), которые существенно повышают прочность и износостойкость поверхностных слоев деталей.
Требования к термообрабатываемым деталям
Детали должны иметь простейшие геометрические формы, без выступающих острых граней и резких переходов от одного сечения к другому.
|
|
Необходимо предусматривать технологические припуски на коробление, которые при последующей обработке позволяют исправить размеры и форму деталей.
В местах контроля твердости устанавливают более широкие допуски на размеры, так как это связано с последующей зачисткой поверхности детали.
Шероховатость поверхности деталей, подвергаемых окончательной термообработке, должна быть не менее Rz40 (при цементации и азотировании - не менее Rz20).
Шероховатость поверхности детали, на которой проводят контроль твердости, должна быть до проведения термообработки не менее Rz20 при задании твердости в единицах НRСЭ и не менее Ra2,5 при задании твердости в единицах HV.
Для цементированных деталей рекомендуется применять конструкционные низкоуглеродистые стали, содержащие не более 0,25% углерода.
Для деталей, в которых по условиям эксплуатации требуется более прочная сердцевина, допускается применение сталей с содержанием углерода до 0,35%.
Рекомендуемая глубина цементованного слоя: 0,3-0,6; 0,5-0,8; 0,9-1,2; 1,2-1,5; 1,6-2; 2,1-2,5 мм.
Для сохранения твердости закаленного цементованного слоя рекомендуется припуск на шлифование назначать в следующих пределах:
|
|
не более 20% глубины слоя при полной его глубине до 2 мм,
не более 25% глубины слоя при полной его глубине свыше 2 мм.
Для деталей, работающих на изгиб и испытывающих динамические нагрузки, не рекомендуется применять азотирование.
Глубину слоя азотирования не должна превышать (5-6)% сечения (толщины) детали.
Детали простейшей формы постоянной толщины в основном подвергаются закалке с нагревом током высокой частоты.
Глубина h закаленного слоя, в зависимости от диаметра детали d, для диапазона диаметров (10-100) мм определяется по формуле:
h=2,91+0,28d-0,121d2.
Полученное значение округлить до стандартного числа (округленное значение не должно отличаться от расчетного более, чем на 30%).
Перепад между соседними диаметрами в ступенчатых валиках желательно назначать в пределах D1/D2=1,2-1,3.
Термическая обработка сварных конструкций
Проведение термической обработки сварных конструкций преследует две основные цели: снятие остаточных напряжений, восстановление свойств металла в зоне термического воздействия сварочного источника тепла.
Снятие остаточных напряжений протекает наиболее интенсивно при температуре 580°С…620°С, при которой изделие выдерживается более 1 ч.
При неравномерном охлаждении изделий в процессе термической обработки могут образоваться дополнительные остаточные напряжения, не связанные с технологическим процессом сварки.
Наибольшую опасность представляет период охлаждения от 600°С до 300°С. Если в этот период в изделии возникают перепады температур более 50°С, то после охлаждения возможно образование значительных остаточных напряжений порядка (0,4-0,6)σт.
Ниже 300°С, когда материал обладает достаточными упругими свойствами, охлаждение изделия может протекать с большей скоростью.
Для сварных конструкций из низко- и среднелегированных сталей большое значение имеет устранение закаленных зон в области сварного шва, образующихся при сварке. Восстановление свойств металла в этих зонах происходит во время отпуска при 620°С…680°С.
Композиционные материалы
Композиционные материалы представляют собой композицию из легких металлов в качестве основы (матрицы) и прочных волокон как наполнителя. В качестве металлической основы используют Al, Mg, Ni и их сплавы. Металлическая матрица связывает волокна в единое целое. Волокна располагаются таким образом, что создают определенную композицию. Композиционные материалы по отношению к обычным сплавам обладают более высокой статической прочностью и прочностью при переменном режиме нагружения. Применение этих материалов повышает жесткость конструкции и снижает ее металлоемкость. При этом прочность композиционного материала определяется прежде всего свойствами волокон, а матрица выполняет роль связующего звена.
Для упрочнения алюминия и магния и их сплавов применяют борные и углеродистые волокна. Для армирования титана и его сплавов применяют молибденовую проволоку, проволоку карбида кремния и т.д. Повышения жаропрочности никелиевых сплавов достигается за счет использования вольфрамовой и молибденовой проволок и т.д.
Для композиционных материалов характерно наличие анизотропии свойств по объему, что в конечном итоге можно эффективно использовать за счет соответствующего расположения детали.
Композиционные материалы обладают высокой статической прочностью, малой чувствительностью к концентраторам напряжений и имеют высокий предел прочности на сопротивление усталости.
Кроме металлической, иногда используют полимерную либо керамическую основы.
Порошковые материалы в последние годы находят всё более широкое применение в промышленности. Детали, изготовленные методом порошковой металлургии, не нуждаются в последующей механической обработке. Сущность метода состоит в прессовании и последующем спекании в пресс-формах композиций металлических порошков и специальных присадок. В зависимости от композиции порошков могут быть получены материалы с необходимыми прочностными, фрикционными, антикоррозионными и другими свойствами. Этот метод реализует принцип безотходной технологии. В машиностроении наибольшее распространение получили детали на основе железного порошка. Детали, изготовленные методом порошковой металлургии, не нуждаются в последующей обработке резанием. Порошковые материалы широко используют при изготовлении тормозных колодок, вкладышей подшипников скольжения, малонагруженных зубчатых колес, втулок, шайб и др.
Неметаллические материалы
Для изготовления деталей машин наряду с металлами и их сплавами широкое применение получают неметаллические материалы, полученные на основе:
1) неорганических веществ (например, минеральные стекла, силикаты, керамические материалы, асбестовые материалы);
2) органических веществ (например, пластические массы, древесные материалы, каучуки, технические резины, лакокрасочные материалы, бумага и др.).
Неметаллические материалы органического происхождения представляют собой в основном природные или синтетические высокомолекулярные соединения.
К природным высокомолекулярным соединениям относятся: целлюлоза, натуральный каучук, природные смолы.
Синтетические высокомолекулярные соединения получаются, как правило, из низкомолекулярных соединений полимеризацией или поликонденсацией.
Керамика
Поликристаллический материал на основе соединений металлов. Если такой материал смешивается с металлами, то в результате получаются металлокерамические материалы.
Металлокерамические материалы изготовляются методами порошковой металлургии. В основе эти материалы представляют смесь керамики с металлами. Такое сочетание позволяет создавать материалы, имеющие высокие термическую прочность, износостойкость, коррозионную стойкость и стойкость к агрессивным химическим средам.
Технология изготовления таких изделий включает получения порошков металлов (а также их смесей с неметаллическими порошками), прессование и последующее спекание в пресс-формах. Полученные таким образом детали не требуют дальнейшей механической обработки. В результате такой технологии обработки материалы могут получаться пористыми, причем пористость достигает 10...30%. Такие материалы, имеющие низкий коэффициент трения который для контакта f=0,05…0,09, целесообразно использовать в качестве фильтров и антифрикционных материалов, а также вкладышей подшипников.
Металлокерамические материалы используются также и в других случаях, где их применение оправдано благодаря описанным выше свойствам.
Пластмассы (пластические массы)
Все более широкое применение получают пластмассы. Пластмассами называют материалы, получаемые на основе природных или синтетических смол (полимеров), которые при определенных температуре и давлении приобретают пластичность, а затем затвердевают, сохраняя форму при эксплуатации. Кроме связующего вещества (полимера) в состав пластмасс входят наполнители, пластификаторы, отвердители, красители. Наполнители вводят в смолы для повышения механической прочности, теплостойкости, уменьшения усадки и снижения стоимости пластмассы. Наполнители могут быть в газовой (пенопласты) и твердой фазе, иметь органическое (древесная мука, хлопковые очесы, целлюлоза, бумага, хлопчатобумажная ткань) и неорганическое (графитная, асбестовая и кварцевая мука; углеродное и стекловолокно; стеклоткань) происхождение. Механическая прочность пластмасс существенно зависит от наполнителя. Пластмассы с порошкообразными, коротковолокнистыми, длиной 2…4 мм, наполнителями по прочности приближаются к дуралюмину и некоторым сортам стали. Для деталей, работающих в узлах трения, широко применяют теплопроводящие наполнители, например, графит.
Пластификаторы увеличивают текучесть, эластичность и уменьшают хрупкость пластмасс. Отвердители ускоряют процесс затвердевания пластмасс, красители придают пластмассам нужный цвет.
Пластмассы обладают ценными свойствами: легкостью, прочностью, тепло- и электроизоляцией, стойкостью против действия агрессивных сред, фрикционностью или антифрикционностью, высоким коэффициентом линейного расширения (в 10...30 раз больше, чем у стали), возможностью получать изделия сложной формы высокопроизводительными методами (литьем под давлением, штамповкой). Отрицательными свойствами пластмасс является невысокая теплостойкость, низкий модуль упругости, склонность к так называемому старению, которое сопровождается постепенным изменением механических характеристик в процессе эксплуатации.
По поведению при нагреве полимеров пластмассы делят на термопластичные (термопласты) и термореактивные (реактопласты).
Термопласты (полиэтилен, фторопласт, полистирол, полиамиды и др.) имеют свойства обратимости: при повторных нагреваниях они переходят в пластическое или вязкотекучее состояние и им можно придать необходимую форму, а затем они вновь затвердевают при охлаждении. Переход термопластов из одного физического состояния в другое может осуществляться неоднократно без изменения химического состава. Термопласты легко формуются и надежно свариваются в изделия сложных форм, устойчивы к ударным и вибрационным нагрузкам, обладают хорошими антифрикционными свойствами. Свойства термопластов сильно зависят от температуры.
Фторопласт – полимерный материал, получаемый химическим путём. Фторопласт содержит атомы фтора, благодаря чему имеет высокую химическую стойкость. Плохо растворяется или не растворяется во многих органических растворителях, не растворим в воде и не смачивается ею. Фторопласты характеризуются широким диапазоном механических свойств, хорошими диэлектрическими свойствами, высокой электрической прочностью, низким коэффициентом трения, низкими значениями износа; стойки к действию различных агрессивных сред при комнатной и повышенной температуре, атмосферо-, коррозионно- и радиационностойки, слабо газопроницаемы, не горючи или самозатухают при возгорании. Очень высокая нагревостойкость (до 300°С). Материал обладает холодной текучестью.
Полиэтилен – продукт полимеризации бесцветного газа этилена, относящийся к кристаллизующимся полимерам. Теплостойкость полиэтилена невысока, поэтому длительно его можно применять при температурах до 60 - 100ºС. Морозостойкость полиэтилена достигает - 70ºС и ниже. Полиэтилен используют для изготовления труб, литых и прессованных несиловых деталей, полиэтиленовых пленок для изоляции проводов и кабелей, чехлов, облицовки водоемов; кроме того, полиэтилен служит покрытием на металлах для защиты от коррозии, влаги, электрического тока и др.
Полистирол – твердый, жесткий, прозрачный, аморфный полимер. По диэлектрическим характеристикам близок к полиэтилену, удобен для механической обработки, хорошо окрашивается. Недостатками полистирола являются его невысокая теплостойкость, склонность к старению, образование трещин. Из полистирола изготовляют детали для радиотехники, телевидения и приборов, детали машин, сосуды для воды и химикатов, пленки стирофлекс для электроизоляции.
Полиамиды – это кристаллизующиеся полимеры. У них низкая плотность. Полиамиды имеют низкий коэффициент трения, продолжительное время могут работать на истирание; кроме того, полиамиды ударопрочны и способны поглощать вибрацию. Они стойки к щелочам, бензину, спирту; устойчивы в тропических условиях. Из полиамидов изготовляют шестерни, втулки, подшипники, болты, гайки, шкивы, детали ткацких станков, уплотнители гидросистем, колеса центробежных насосов, турбин, турбобуров, буксирные канаты и т. д. Полиамиды используют в электротехнической промышленности, медицине и, кроме того, как антифрикционные покрытия металлов.
Реактопласты не переходят в пластическое состояние при повторном нагревании. Они имеют более высокие, чем термопласты, показатели по твердости, модулю упругости, теплостойкости, сопротивлению усталостной прочности. Их свойства не так резко зависят от температуры. В зависимости от наполнителя различают монолитные (карболит), слоистые (текстолит, гетинакс) и композиционные пластмассы, где наполнителем используются волокна. В термореактивных пластмассах связующими являются эпоксидные, кремнийорганические и другие смолы.
Карболит, один из видов синтетических фенолоальдегидных смол, получаемый поликонденсацией фенола (крезолов) с формальдегидом в присутствии нефтяных сульфокислот.
Текстолиты (наполнитель – хлопчатобумажная ткань) широко используют в машиностроении как конструкционный и антифрикционный материал: В них выгодно сочетаются высокая механическая прочность с низкой плотностью, износостойкостью и хорошими диэлектрическими свойствами. Текстолит применяют для изготовления подшипников, зубчатых колес и различных силовых деталей общего и специального машиностроения.
Древолиты — древеснослоистые пластики (ДСП). Древолит представляет собой пластики, состоящие из правильно уложенных слоев тонкого (0,6.....1 мм) древесного шпона, пропитанных фенольной смолой и термически обработанных под высоким давлением.
Гетинакс (в качестве наполнителя применяется бумага) обладает высокими диэлектрическими свойствами и удовлетворительной механической прочностью. Выпускается в виде листов, плит, труб и различных прессованных деталей. Широко применяется как электроизоляционный материал.
Алкиды. Это семейство литьевых компаундов, изготавливаемых из ненасыщенных полиэстерных смол. Свойства алкидов: высокая твердость и жесткость, стабильность размеров при повышенных температурах; низкое влагопоглощение; высокая диэлектрическая прочность и стойкость к электрическим разрядам; сохранение электроизоляционных свойств в условиях влажности. Типичное применение: держатели щеток автомобильных электромоторов, электроизоляторы, элементы телевизоров, электрические выключатели, элементы систем зажигания в автомобилях; оболочки резисторов и конденсаторов.
Дата добавления: 2019-01-14; просмотров: 231; Мы поможем в написании вашей работы! |
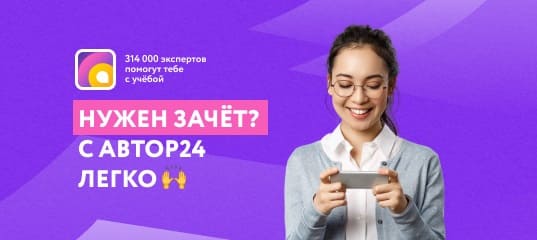
Мы поможем в написании ваших работ!