Мощность машин и её преобразование в механизмах 9 страница
- нагревательные элементы, нити накаливания электроламп, электрические контакты;
- наконечники артиллерийских снарядов.
Изделия из вольфрамовых сплавов обычно изготавливаются методами высокотемпературной порошковой металлургии. Вольфрамовые сплавы плохо поддаются обработке резанием и обрабатываются инструментом высокой твердости. При соединении элементов из вольфрамовых сплавов с другими металлами возможна сварка, однако предпочтительна пайка твердым припоем. Вольфрамовые сплавы относительно стойкие к коррозии, однако при работе в агрессивных средах рекомендуется применять гальванические покрытия, такие, как кадмирование, хромирование и никелирование.
Магнитно-твердые сплавы
Магнитно-твердые сплавы предназначены для изготовления постоянных магнитов. Наиболее распространены сплавы типа Алнико. Это сплав железа, никеля, алюминия и кобальта с добавками меди и кремния. Постоянные магниты из этих сплавов изготавливаются литьем или спеканием. Сплавы Алнико очень твердые, крупнозернистые и хрупкие; они не поддаются обработке резанием. Некоторая корректировка поверхности возможна с помощью шлифования.
Магнитно-мягкие сплавы
Магнитно-мягкие сплавы – это сплавы, которые имеют низкую коэрцитивную силу, высокую магнитную проницаемость и низкие потери на перемагничивание.
Магнитно-мягкие сплавы разделяются на две основные группы:
|
|
- техническое железо и электротехнические стали (ферритные стали с содержанием 0.8-2.5% Si). Эти материалы предназначены для изготовления сердечников трансформаторов, магнитопроводов электрических машин и аппаратов и др.;
- железоникелевые сплавы (пермаллои), содержащие около 78% Ni. Эти сплавы имеют исключительно высокую начальную магнитную проницаемость и предназначены для приборов, работающих в слабых магнитных полях (радио, телефон, телеграф).
Алюминий и сплавы на его основе
Алюминий – это металл серебристо-белого цвета с температурой плавления 600 0С. Он имеет гранецентрированную кристаллическую решетку с периодом а=0,4041 нм. Так как алюминий обладает низкой плотностью ρ=2,7 гр/см3, то сплавы на основе алюминия называются легкими. Алюминий, как и медь, имеет высокую электро- и теплопроводность. Модуль упругости E=(7,0…7,5)∙104 МПа.
Алюминий является коррозийно-стойким материалом, так как на его поверхности появляется пленка окислов, защищающая основной металл от коррозии. Чистый алюминий имеет низкую прочность и применяется для производства деталей, не воспринимающих силового воздействия. Он хорошо деформируется пластически, успешно сваривается, но плохо обрабатывается механически. По этой причине из алюминия изготавливают трубопроводы, резервуары, палубные надстройки речных и морских судов и т.п. Из чистого алюминия изготавливают также металлическую фольгу, токопроводящие и кабельные материалы.
|
|
Чистый алюминий применяется редко, так как имеет низкую прочность. Чаще при изготовлении деталей применяют сплавы на основе алюминия. Они обладают малой плотностью, высокой электро- и теплопроводностью, коррозийной стойкостью и удельной прочностью. Наибольшее распространение получили сплавы Al-Cu, Al-Si, Al-Mg, Al-Cu-Mg, Al-Cu-Mg-Si, Al-Mg-Si, Al-Zn-Mg-Si. По технологическим признакам алюминиевые сплавы подразделяются на деформируемые, т.е. получаемые пластическим деформированием, и литейные, предназначенные для получения фасонных деталей методом литья. Деформируемые сплавы по способности упрочняться термической обработкой подразделяют на сплавы, не упрочняемые термической обработкой, и сплавы, упрочняемые термической обработкой.
Наиболее известным представителем класса деформируемых сплавов является дюралюминий (Al-Cu-Mg), который получил распространение в авиационной технике и транспортном машиностроении (марки Д1, Д16). Марганец добавляется в состав сплава для повышения коррозионной стойкости. Часто в такие сплавы добавляют присадки в виде Cr, Zn, Fe, Si. Сплав хорошо деформируется в горячем и холодном состояниях. А также удовлетворительно обрабатывается резанием в закаленном и состаренном состояниях и плохо – в отожженном состоянии, хорошо сваривается точечной сваркой и не сваривается сваркой плавлением вследствие склонности к образованию трещин. Дюралюминий широко используется в производстве листового и профильного проката. Для повышения прочности такие сплавы часто подвергаются закалке при температуре 500-520 0С с последующим охлаждением в воде и выдержкой при нормальной температуре в течение 75...100 часов (естественное старение). Кроме того, деформируемые сплавы подвергаются обработкой давлением с последующей механической обработкой. Такую технологию применяют для изготовления деталей с высокой прочностью, например, дисков центробежных машин, деталей компрессоров и т.д.
|
|
К деформируемым сплавам, не упрочняемым термической обработкой, относятся алюминиево-магниевые сплавы. Эти сплавы добавочно легируют марганцем, который упрочняет сплав. Эффект от закалки и старения этих сплавов невелик, и их применяют в отожженном состоянии. Повышение прочности при некотором уменьшении пластичности изделий простой формы достигается нагартовкой. Упрочнение, создаваемое нагартовкой снимается в зоне сварки. Сплавы легко обрабатываются давлением. Хорошо свариваются и обладают высокой коррозионной стойкостью. Обработка резанием затруднена. Сплавы применяются для сварных и клепаных элементов конструкций, испытывающих небольшие нагрузки и требующие высокого сопротивления коррозии. Из алюминиево-магниевых сплавов наиболее часто применяется сплав марки АМг6. К деформируемым сплавам относится высокопрочный алюминиево-магниево-цинковый сплав В95.
|
|
Деформируемыми являются так называемые спеченные алюминиевые сплавы, отличающиеся очень высокими прочностными свойствами. Они бывают двух видов: САП (спеченная алюминиевая пудра) и САС (спеченный алюминиевый сплав). САП упрочняется дисперсными частицами окиси алюминия Al2O3, образуемой в процессе помола алюминиевой пудры в атмосфере азота с регулируемой подачей кислорода. Пудру брикетируют, спекают и подвергают деформации – прессованию, прокатке, ковке. В зависимости от содержания Al2O3 (прочность сплава возрастает при увеличении окиси алюминия до 20 – 22%) различают 4 марки САП (САП-1, САП-2, САП-3 и САП-4). Сплавы САС содержат до 25% кремния и 5% железа. Их получают распылением жидкого сплава, брикетированием полученных гранул и последующей деформацией.
Литейные сплавы на базе алюминия (Al-Cu, Al-Mg, Al-Si, Al-Zn-Mg-Si) благодаря низкой плотности и хорошей технологичности широко используются в самолетостроении, судостроении, автомобилестроении, строительстве и других областях.
Литейные сплавы применяются для фасонного литья. Такие сплавы должны обладать высокой жидкотекучестью, сравнительно небольшой усадкой, малой склонностью к образованию горячих трещин и пористости в сочетании с хорошими механическими свойствами, сопротивлением коррозии. Высокими литейными свойствами обладают сплавы, содержащие в своей структуре эвтектику. Эвтектика образуется во многих сплавах, в которых содержание легирующих элементов больше предельной растворимости в алюминии. Чаще применяют сплавы алюминия с: кремнием (Al – Si), медью (Al – Cu), магнием (Al – Mg), которые дополнительно легируют небольшим количеством меди и магния (Al – Si), кремния (Al – Mg), марганца, никеля, хрома (Al – Cu).
Сплавы Al – Si получили наибольше распространение. Эти сплавы, получившие название силумины, близки по составу к эвтектическому и потому отличаются высокими литейными свойствами и средними механическими свойствами, а отливки – большей плотностью. Обладают высокой коррозийной стойкостью.
Сплавы Al – Si сравнительно легко обрабатываются резанием. Заварку дефектов можно производить газовой и аргонодуговой сваркой.
Сплавы Al – Cu. Эти сплавы после термической обработки имеют высокие механические свойства при комнатной и повышенных температурах и хорошо обрабатываются резанием. Литейные свойства сплавов низкие. Эти сплавы используют для отливки небольших деталей простой формы. Они склонны к хрупкому разрушению. Если от отливок требуется повышенная прочность. То их после закалки подвергают искусственному старению при 150ºС. Алюминиево-медные сплавы малоустойчивы против коррозии, поэтому отливки обычно анодируют.
Сплавы Al – Mg. Сплавы алюминий с магнием имеют низкие литейные свойства, так как не содержат эвтектики. Характерной особенностью этих сплавов является хорошая коррозийная стойкость, повышенные механические свойства и обрабатываемость резанием. Добавление к сплавам модифицирующих присадок (титан, цирконий) улучшает механические свойства, а бериллия уменьшает окисляемость расплава, что позволяет вести плавку без защитных флюсов. Эти сплавы предназначены для отливок, работающих во влажной атмосфере, например в судостроении и авиации. Добавление к сплавам Al – Mg кремния улучшает литейные свойства в результате образования тройной эвтектики.
Сплавы алюминия широко применяют в тех случаях, когда важно снижение массы машины (конструкции). Алюминий и его сплавы трудно паяются.
Маркировка алюминиевых сплавов включает в себя начальные буквы, входящих в состав сплава компонентов и цифры, указывающие содержание легирующего элемента в процентах.
Дуралюмины маркируются буквой "Д" и порядковым номером, например: Д1, Д12, Д18.
Литейные алюминиевые сплавы маркируются буквами "АЛ" с последующим порядковым номером: АЛ2, АЛ9, АЛ13, АЛ22, АЛЗО.
Иногда маркируют по составу: АК7М2; АК21М2, 5Н2,5; АК4МЦ6. В этом случае "М" обозначает медь, "К" - кремний, "Ц" - цинк, "Н" - никель; цифра - среднее % содержание элемента.
Алюминиевые антифрикционные сплавы маркируют буквой "А" и начальными буквами входящих в них элементов: А09-2, А06-1, АН-2,5, АСМТ. В первые два сплава входят указанное количество олова и меди (первая цифра-олово, вторая-медь в %), в третий 2,7-3,3% Ni и в четвертый медь сурьма и теллур.
Дуралюмин и алюминиево-магниевые сплавы применяют для средненагруженных деталей типа стоек, крышек, втулок и т.д. Сплавы марки В65, Д18 – для заклепок. Спеченные алюминиевые сплавы применяют для изготовления высоконагруженных деталей и различных профилей. Силумины марок АЛ-2, АЛ-4, АЛ-9 применяют для изготовления литьем корпусов, крышек, кронштейнов и других сложных средненагруженных деталей. Алюминиево-магниево-цинковый сплав В95 применяют для деталей с повышенными статическими нагрузками (валы, зубчатые колеса). Из алюминиевых антифрикционных сплавов изготовляют подшипники и вкладыши.
Помимо вышеперечисленных, в машиностроении используется ряд других металлических сплавов, как правило, предназначенных для изготовления деталей с особыми свойствами. Например, сплав олова и свинца – баббит – обладает высокими антикоррозионными свойствами и применяется как материал при производстве вкладышей подшипников скольжения.
Термическая и термохимическая обработка металлических материалов
Термообработка металлов - процесс тепловой обработки металлов и сплавов с целью изменения их структуры, а, следовательно, и свойств, заключающийся в термической (совокупность операций нагрева, выдержки и охлаждения) или химико-термической обработке (процесс диффузии в поверхностный слой материала углерода, азота, кремния и др. элементов за счет воздействия среды на нагретую заготовку). Возможно также механическое упрочнение поверхностных слоев деталей. К основным видам термической обработки относятся: отжиг, нормализация, закалка, отпуск и улучшение. Данную обработку проводят для повышения механических свойств металлов (прочности, износостойкости, исправления структуры).
Отжиг – вид термообработки, устраняющий химическую и физическую неоднородности, полученные в результате предшествующей обработки. Отжиг бывает низкотемпературным и высокотемпературным. В первом случае температура нагрева не превышает температуру фазовых превращений, а во втором – выше этой температуры. Отжиг дает возможность уменьшить в заготовках остаточные внутренние напряжения (снятие остаточных напряжений в стальных деталях после литья, сварки, пластической деформации или механической обработки) и тем самым улучшить их структуру перед последующей механической обработкой. Отжиг достигается их нагревом (для углеродистых и легированных сталей до температуры 800... 900°С) и медленным охлаждением вместе с печью или на воздухе. В результате такой термообработки увеличивается пластичность и снижается твердость. Такая операция является необходимой для выполнения последующей операции механообработки.
Нормализация (отжиг нормализационный) отличается от отжига технологией охлаждения заготовок и обеспечивает несколько большую твердость и прочность материала. Нормализация достигается нагревом, выдержкой и последующим охлаждением на спокойном воздухе. Обеспечивает исправление структуры перегретой стали, снятие внутренних напряжений в деталях из конструкционных сталей и улучшение их обрабатываемости; увеличение глубины прокаливаемости инструментальных сталей перед закалкой.
Закалка представляет собой процесс нагрева стали до температуры выше температуры фазовых изменений, выдержке при этой температуре и последующего охлаждения с большой скоростью. При этом материал упрочняется, но остается хрупким. Закалка не является окончательной операцией термообработки. Чтобы уменьшить хрупкость, снять остаточные напряжения и получить требуемые механические свойства, закаленные детали подвергают отпуску.
Виды закалки:
Непрерывная - нагрев, выдержка и последующее резкое охлаждение. Назначение: Получение в сочетании с отпуском высокой твердости и износоустойчивости стальных деталей.
Прерывистая - нагрев, выдержка и последующее охлаждение в воде, а затем в масле. Назначение: Уменьшение остаточных напряжений и деформаций в деталях из высокоуглеродистой инструментальной стали.
Изотермическая - нагрев, выдержка и последующее охлаждение в расплавленных солях, а затем на воздухе. Назначение: Получение после закалки минимальной деформации изделий, повышение пластичности, предела выносливости и сопротивления изгибу деталей из легированной инструментальной стали.
Ступенчатая - то же (отличается от изотермической закалки меньшим временем пребывания изделия в охлаждающей среде). Назначение: Уменьшение напряжений, деформаций (коробления) и предупреждение образования трещин в мелком инструменте и углеродистой инструментальной стали, а также в более крупном инструменте и легированной инструментальной и быстрорежущей стали (Р18, Р12, Р9 и др.).
Поверхностная - нагрев поверхностного слоя и последующее быстрое охлаждение. Назначение: Для деталей, к которым предъявляю-то требования поверхностной твердости.
С самоотпуском - отличается от непрерывной закалки тем, что детали охлаждаются не полностью, вследствие чего под действием тепла, сохранившегося внутри детали, обеспечивается отпуск закаленного наружного слоя. Назначение: Для местной закалки ударного инструмента несложной конфигурации, изготовленного из углеродистой инструментальной стали, а также при индукционном нагреве.
С обработкой холодом - глубокое охлаждение после закалки до температуры -20 °С…-80 °С. Назначение: Повышение твердости и получение стабильности размеров деталей из высоколегированных сталей.
С подстуживанием - нагретые детали перед погружением в охлаждающую среду некоторое время охлаждаются на воздухе или выдерживаются в термостате с пониженной температурой. Назначение: Сокращение цикла термической обработки стали; применяется обычно после цементации.
Светлая - отличается от непрерывной закалки применением контролируемых сред при нагреве и охлаждении. Назначение: Защита от окисления и обезуглероживания сложных деталей пресс-форм, штампов и приспособлений, не подвергаемых шлифованию.
Закалка может быть выполнена по всему объему или по поверхности. Поверхностная закалка повышает твердость материала, его износостойкость и т.д. При таком виде закалки основная объемная часть материала остается пластичной, что благоприятным образом сказывается на конструкции в целом. По этой причине такой вид термообработки часто используется на практике. Нагрев поверхности детали производят с большой скоростью токами высокой частоты (ТВЧ), электронным лучом, газовой горелкой. При этом сердцевина детали не прогревается до температуры закаливания стали. Повышается твердость и прочность только поверхностных слоев, а сердцевина стали остается вязкой, что предохраняет деталь от поломок, уменьшает коробление. Так закаливают валы, кулачки, зубья крупномодульных колес из сталей 40, 45, 50, 40Х, 40ХН и др.
Малоуглеродистые стали с содержанием углерода до 0,25 % закалке не подлежат. Для повышения их механических свойств проводят химико-термическую обработку поверхностных слоев деталей на глубину 0,2...2 мм, что обеспечивает после закалки их высокую контактную прочность при сохранении вязкой сердцевины.
Отпуск заключается в нагреве металла до температуры ниже критической, выдержке при этой температуре и охлаждения с определенной скоростью.
Виды отпуска:
Низкотемпературный - нагрев в интервале температур 150°С…250°С и последующее ускоренное охлаждение. Назначение: Снятие внутренних напряжений и уменьшение хрупкости режущего и мерительного инструмента после поверхностной закалки, после закалки цементуемых изделий.
Среднетемпературный - нагрев в интервале температур 350°С…500°С и последующее медленное или ускоренное охлаждение. Назначение: Повышение предела упругости пружин рессор и других упругих элементов.
Высокотемпературный - нагрев в интервале температур 500°С…680°С и последующее медленное или быстрое охлаждение. Назначение: Для деталей из конструкционных сталей как правило, при термическом улучшения.
Улучшение - термообработка, состоящая из закалки и высокотемпературного (нагрев до 500... 670°С) отпуска. Его используют для повышения прочности деталей машин при сохранении или повышении вязкости материала. Улучшение обеспечивает большую твердость стали, чем нормализация. Например, нормализованная сталь 45 имеет твердость 170... 217 НВ, улучшенная - 269... 302 НВ. Назначение: обеспечение сочетания высокой прочности и пластичности при окончательной термообработке деталей из конструкционных сталей, испытывающих в работе ударные и вибрационные нагрузки.
Термомеханическая обработка - нагрев, быстрое охлаждение до 400оС…500оС. Многократное пластическое деформирование, закалка и отпуск. Назначение: Обеспечение для проката и простых деталей, не подвергаемых сварке, повышенной прочности по сравнению с прочностью, получаемой при обычной термической обработке.
Старение - нагрев и длительная выдержка при повышенной температуре. Назначение: Стабилизация размеров деталей и инструментов из различных сталей.
Кроме термической, металлы могут подвергаться химико-термической обработке (поверхностному легированию), т.е. термическому и химическому воздействию на поверхностный слой. При химико-термической обработке происходит, в основном, изменение структуры поверхностного слоя материала, в результате чего повышаются твердость, износоустойчивость и устойчивость против коррозии. Наиболее распространенными видами химико-термической обработки являются цементация, азотирование, цианирование.
Дата добавления: 2019-01-14; просмотров: 241; Мы поможем в написании вашей работы! |
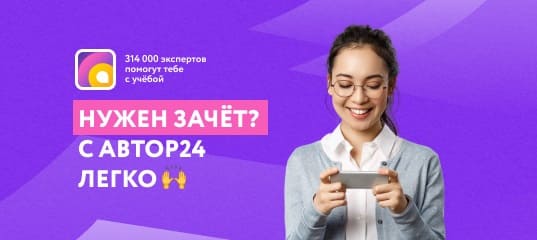
Мы поможем в написании ваших работ!