Общие задачи создания долговечных узлов трения
Разработка конструкции различных узлов трения вначале шла независимо от развития науки. В современных условиях одновременное развитие фундаментальных наук, технических дисциплин и трибологии позволило на практике создавать узлы трения высочайшего качества, работающие не только в обычных транспортных, технологических и других машинах, но и в экстремальных режимах, при высоких и низких температурах, в вакууме, при радиации, в химически агрессивных средах на земле и в космических условиях.
Однако и сегодня решения многих проблем создания оптимальных по характеристикам узлов трения и научные достижения в этой области далеки от совершенства так же, как узлы трения, созданные инженерами, далеки по совершенству от творений природы.
Проблема обеспечения высокой работоспособности узлов трения охватывает системную группу задач, каждый элемент которой должен получить оптимальное разрешение. Основные требования к конструкции узлов трения изложены в литературе.
Круг основных действий конструктора при создании узлов трения и смазки показан на схеме (рис.18).
Приведенная схема по-разному реализуется в структурах конструкторских подразделений. На крупных предприятиях существует разделение служб, разрабатывающих новые изделия и сопровождающих выпуск изделий, переданных в серийное производство. Например, разработку новых моделей автомобилей ВАЗ осуществляет департамент развития, включающий в себя научный центр, систему лабораторий, опытных производств, испытательных баз (включая треки и полигоны дорожных испытаний), аэродинамическую трубу и другие подразделения, имеющие необходимые средства для разработки, исследования, испытания и доводки узлов трения.
|
|
| Определение назначения узла трения Разработка технического задания на проектирование |
| ||||||||||||||||||||||||||||||||
|
| |||||||||||||||||||||||||||||||||
Разработка конструкции узла. Использование прототипов и аналогов | ||||||||||||||||||||||||||||||||||
|
|
|
|
|
|
|
|
| ||||||||||||||||||||||||||
Обеспечение кинематических характеристик | Обеспечение прогноза работоспособности |
| Обеспечение температурной устойчивости | Обеспечение динамической устойчивости |
|
| Обеспечение экологических требований | |||||||||||||||||||||||||||
|
|
|
|
|
|
|
| |||||||||||||||||||||||||||
Выбор конструкционных характеристик | Выбор смазочных материалов и проектирование системы смазки |
| Выбор технологических методов изготовления и сборки | Организация узловых, стендовых и эксплуатационных испытаний
| ||||||||||||||||||||||||||||||
|
|
|
|
|
|
|
|
| ||||||||||||||||||||||||||
| Разработка системы обеспечения качества согласно ISO - 9000 |
| ||||||||||||||||||||||||||||||||
|
|
|
| |||||||||||||||||||||||||||||||
| Разработка технологии ремонта и реновации |
| ||||||||||||||||||||||||||||||||
|
|
|
| |||||||||||||||||||||||||||||||
| Решение вопросов утилизации отработанных узлов трения и смазки |
| ||||||||||||||||||||||||||||||||
| ||||||||||||||||||||||||||||||||||
Рис. 18. Общая схема основных элементов создания конструкции, узлов трения и смазки | ||||||||||||||||||||||||||||||||||
В серийном производстве, кроме служб технического контроля, также имеются лаборатории и другие службы, входящие в схему обеспечения качества и надежности.
Ресурсные характеристики узлов трения регламентированы в нашей стране классами износостойкости (табл. 3). Значения износостойкости ν колеблются в широких пределах: 103-1013.
В табл. 4 представлены данные о классах износостойкости ряда узлов трения автомобилей.
Приведем пример вычисления линейного износа в конце эксплуатационного срока в парах трения «коренной подшипник-вкладыш» и «поршень-цилиндр». При путевом ресурсе в 100000 км и средней скорости 60 км/ч временной ресурс составляет 2000 ч. Примем частоту вращения коленвала n=6000 об/мин и диаметр шейки вала 60 мм, тогда линейная скорость составит V=π dn/60≈2,0 м/с. Путь трения L=V∙t=14,4∙106 м. Для 7-го класса износостойкость ν=107…108, а величина линейного износа ∆h=L∙I=14,4∙10-6x10-8=14,4∙10-2≈0,14 мм.
|
|
Для пары «поршень-цилиндр» при эксцентриситете коленвала 75 мм путь поршня за один оборот составит L1=4∙75=300 мм. Скорость V = 180 м/мин. Путь за 2000 ч – L=3,6∙104 м. Величина линейного износа к концу срока эксплуатации достигнет ∆h= 0,036 мм. Как видно, расчеты дают вполне реальные значения износа.
Таблица 3. Классы износостойкости | ||||
Класс | U | Класс | U | |
3 | 103-104 | 8 | 108-109 | |
4 | 104-105 | 9 | 109-1010 | |
5 | 105-106 | 10 | 1010-1011 | |
6 | 106-107 | 11 | 1011-1012 | |
7 | 107-108 | 12 | 1012-1013 | |
| ||||
| ||||
Таблица 4. Износостойкость некоторых узлов трения | ||||
Узел трения | Класс | |||
Цилиндро-поршневая группа | 11-12 | |||
Колодочный тормоз | 6-7 | |||
Дисковый тормоз | 6-10 | |||
Подшипники скольжения коренные, латунные | 11-12 | |||
Зубчатые передачи | 5-8 | |||
При создании узлов трения решается ряд характерных триботехнических задач, на которые необходимо обращать особое внимание.
|
|
Выбор типа подшипников является одним из основных вопросов конструирования узлов трения.
В качестве критерия предварительного выбора типа подшипников используют показатель - произведение скорости вращения n (c-1) и нагрузки Р (H), действующей на узел трения. В зависимости от величины этого произведения выбирают тип подшипника.
Общий диапазон реальных значений n∙P составляет 10-2-107 Н∙с-1.
Для удобства и быстроты решений на основе практики конструкторской работы созданы номограммы, по которым предварительно выбирают тип подшипника, - для радиальных (рис. 19) и для осевых упорных (рис. 20).
Номограммы ориентируют на выбор типов подшипников: скольжения и качения: скольжения без смазки, гидродинамических, гидростатических, пористых, из самосмазывающихся материалов и др.
Пример. Средняя номинальная скорость вращения n коленчатого вала - 2000 об/мин или 33,3 с-1.
Расчетная нагрузка P на коренной подшипник - 3000 Н.
Диаметр вала - 70 мм.
![]() | ![]() ![]() ![]() ![]() |
![]() | ![]() ![]() ![]() |
Рис. 20. Области применения различных типов упорных подшипников |
По номограмме для нашего примера (см. рис. 19) находим пересечение трех характеристик: Р (Н), n (мин-1) и n (с-1). Оно указывает, что рассматриваемый случай относится к области применения подшипников скольжения.
При окончательном выборе типа подшипников тщательно изучают прототипы проектируемых узлов трения, опыт их эксплуатации и особенности конструкции. После выбора базовой схемы ее дорабатывают по условиям технического задания.
В целом конструкторы придерживаются ряда общих правил отработки узлов трения. Так, одним из общих правил проектирования узлов трения-скольжения является правило выбора материалов пары и структуры. Оно содержит, в свою очередь, правило выбора твердости и правило различия структуры.
Дата добавления: 2019-01-14; просмотров: 373; Мы поможем в написании вашей работы! |
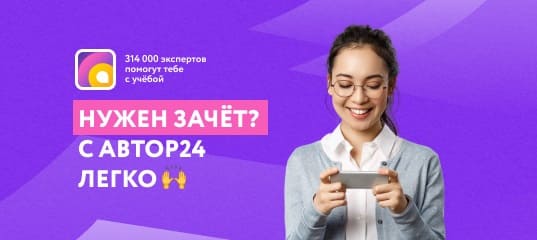
Мы поможем в написании ваших работ!