Силы, действующие в механизмах и машинах
Силы в механизмах и машинах разделяют на шесть групп.
Движущие силы (движущие моменты). Они приложены к входному звену механизма. Совершаемая ими работа при движении машины считается положительной. Они зависят от разных параметров. Так, давление газа в цилиндре двигателя внутреннего сгорания зависит от перемещения поршня, а движущий момент в механизме, например, стрелочного перевода создаётся электродвигателем и зависит от скорости вращения мотора.
Силы сопротивления , которые машина преодолевает при работе. Эти силы всегда стремятся замедлить движение выходного звена. Они достаточно условно подразделяются на силы полезного сопротивления (при резании, прессовании и т.п.), на преодоление которых затрачивается полезная работа машины и силы вредного сопротивления (потери на трение и т.п.), на преодоление которых затрачивается работа дополнительно, сверх полезной. К вредному сопротивлению относят как силы взаимодействия между звеньями в кинематических парах (трение, удары), так и силы сопротивления среды (аэро- и гидродинамические).
Силы тяжести , равнодействующие которых приложены в центрах тяжести звеньев. В зависимости от направления движения центра тяжести звена (вниз или вверх) силы тяжести совершают либо положительную, либо отрицательную работу, которая, соответственно помогает или препятствует движению машины.
Силы инерции . Действуют на все звенья механизма, движущиеся с ускорением − линейным или угловым. В соответствии с методами теоретической механики все силы инерции приводятся к главному вектору и главному моменту сил инерции: гдеm− масса звена; aS − ускорение центра масс; ε− угловое ускорение звена;
− момент инерции звена относительно центра масс. Знак "минус" показывает, что главный вектор и главный момент сил инерции направлены противоположно соответствующим ускорениям.
|
|
Реактивные силы или реакции возникают в кинематических парах в результате действия всех, описанных выше сил в соответствии с 3-м законом Ньютона. В их обозначениях применяют два индекса, первый из которых указывает, от какого звена, а второй − на какое звено действует сила. Реакции непосредственно не влияют на характер движения механизма.
Силы трения в кинематических парах зависят от реакций. Силы (моменты) трения обычно считают вредным сопротивлением, они всегда направлены противоположно движению и рассеивают часть энергии на своё преодоление, отнимая её от полезной работы и преобразуя её в тепло. Это вызывает нежелательный нагрев деталей машин. Однако, кроме того, силы трения эффективно рассеивают энергию колебаний, понижая уровень шума и вибрации машин.
|
|
Равнодействующая всех сил, приложенная к входному звену со стороны остальных звеньев механизма называется уравновешивающей силой (моментом). Максимальная величина уравновешивающего момента определяет требуемую мощность двигателя.
Виды нагрузок, действующих на детали машин
В процессе эксплуатации каждая машина испытывает различные виды нагрузок. Познакомимся с некоторыми из них.
Рабочей (внешней) нагрузкой называют силу или момент воспринимаемые деталью или узлом в процессе эксплуатации изделия.
Рабочая нагрузка может быть постоянной или переменной в зависимости от характера ее изменения во времени. К постоянным можно отнести, например, нагрузку от собственного веса.
При эксплуатации детали машин, как правило, испытывают переменные нагрузки, характер которых зависит от систематических или случайных факторов, вызывающих эти нагрузки. Так, для машин, выполняющих в производственном процессе определенные технологические функции, характер изменения нагрузок для одного технологического цикла остается приблизительно постоянным. В некоторых случаях, например для транспортных машин, нагрузки зависят от ряда случайных факторов (сопротивления передвижению, определяемому рельефом и состоянием пути, инерционными и ветровыми воздействиями и т. д.).
|
|
В зависимости от способа воздействия на деталь нагрузки могут быть статическими и динамическими.
Статическими называют нагрузки, значение, направление и место приложения которых остаются постоянными или меняются медленно и незначительно от нуля до своего конечного значения, оставаясь в дальнейшем практически постоянными. К этому виду нагрузок относятся собственная сила тяжести изделия, давление газа или жидкости в резервуарах или трубах, сила затяжки болтов.
Динамическими называют нагрузки, характеризующиеся быстрым изменением во времени их значения, направления или места приложения. Примером динамических нагрузок могут служить нагрузки на рабочие детали кузнечного молота, на зубья звездочек цепных передач и зубчатых колес и т. д.
В деталях машин, подвергающихся длительное время переменным напряжениям, происходит процесс постепенного накопления повреждений, приводящий к образованию трещины, ее развитию и окончательному разрушению детали. Этот процесс называется усталостью материалов. Подробно расчеты на усталость изложены в курсе «Сопротивление материалов».
|
|
В связи с переменным характером рабочих нагрузок вводят понятия о номинальной, эквивалентной и расчетнойнагрузках.
Под номинальной понимают нагрузку, выбираемую из числа действующих в установившемся режиме рабочих нагрузок. В качестве номинальной предпочтительно принимать максимальную или наиболее длительно действующую нагрузку. Номинальные мощность, момент, частота вращения, скорость и т.д.
Эквивалентнойназывается такая постоянная нагрузка, которой можно заменить фактические действующую переменную рабочую нагрузку, считая ее равноценной в отношении соответствующих критериев надежности, (например, долговечность, прочность…).
Для зубчатой передачи Qэкв=Qном∙Kдолг,
где Кдолг – коэффициент долговечности, зависящий от графика изменения рабочей нагрузки и от того, какая из них принята в качестве номинальной.
Переменные рабочие нагрузки обычно задают в виде упорядоченных графиков. На рис. 3.1 показан в качестве примера закон изменения нагрузки F и частоты вращения п (мин-1) рассчитываемой детали (вала, оси, зубчатого колеса и т. д.) за некоторый повторяющийся период времени tc = t . Число таких периодов (блоков) за полный срок службы обозначают Σtс. Нагрузкой может быть сила F , изгибающий или крутящий момент М и т. д. Плавное изменение нагрузки можно заменить вписанными прямоугольниками со сторонами F 1 t 1 , F 2 t 2, ..., Fiti и n 1 t 1 , n 2 t 2, ..., n iti. Максимальную нагрузку и соответствующую ей частоту вращения отмечают индексом 1, а последующие нагрузки в порядке убывания обозначают 2, 3 и т. д.
Рассматриваемый закон изменения нагрузки можно представить в виде, показанном на рис. 3.2, на котором по горизонтальной оси отложены значения чисел циклов изменения напряжений NΣ, а по вертикальной – значения нагрузок в порядке убывания. На рис. 3.2 показаны три нагрузки, но рассматриваемый метод относится к любому числу нагрузок.
Числа циклов изменения напряжений при действии нагрузок F 1, F 2, F3, ..., Fi определяют по формуле NΣ= 60 n tΣ или NΣ= 573ωtΣ; здесь п – частота вращения, мин-1; ω – угловая скорость, рад/с; tΣ– суммарное время работы передачи, ч; для типичных условий работы привода tΣ= TDCtc где T –срок службы механизма, год; D – число рабочих дней в году; С – число смен; tc – продолжительность работы за смену, ч.
Рис.3.1
Рис.3.2
Заданную переменную нагрузку можно заменить постоянной, равноценной по повреждающему действию на деталь за тот же период времени. Такую нагрузку называют расчетной.
Расчетной называется условная постоянная нагрузка, определяемая (рабочей нагрузкой) с учетом ее характера воздействия на объект. Она служит для определения размеров деталей машин. Учитывает местные условия.
Размеры деталей машин определяют по расчетным нагрузкам, которые зависят не только от значения и характера изменения рабочей нагрузки, но и от особенностей ее передачи по силовой цепи: степени динамичности, равномерности распределения нагрузки по контактирующим поверхностям, особенностей взаимодействия последних (сцеплением или зацеплением); они зависят также от назначения детали (узла) и условий эксплуатации.
Qрасч=Qэкв∙Kк∙Kд∙Kу
где Кк – коэффициент, учитывающий неравномерность распределения нагрузки по контактным поверхностям;
Кд– коэффициент динамичности;
Ку – коэффициент, зависящий от условий работы и передачи нагрузки (например, за счет сил трения, сцепления и т.д.).
Предварительные расчеты можно выполнять, принимая:
Qрасч ≈ Qном .
Дата добавления: 2019-01-14; просмотров: 438; Мы поможем в написании вашей работы! |
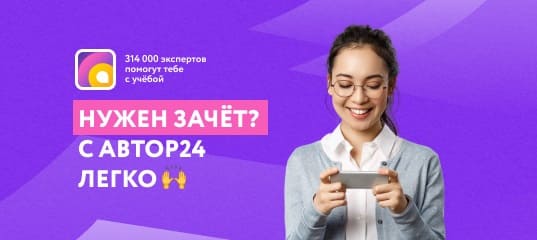
Мы поможем в написании ваших работ!