СПИСОК ИСПОЛЬЗОВАННЫХ ИСТОЧНИКОВ
МИНИСТЕРСТВО ОБРАЗОВАНИЯ И НАУКИ
РОССИЙСКОЙ ФЕДЕРАЦИИ
Новосибирский технологический институт (филиал)
федерального государственного бюджетного образовательного учреждения высшего образования
«Московский государственный университет дизайна и технологии»
(НТИ (филиал) МГУДТ)
УТВЕРЖДАЮ
Зав. кафедрой ТДШИ
_______Мокеева Н.С.
«_____» ______2017 г.
МЕТОДИЧЕСКИЕ УКАЗАНИЯ
к выполнению лабораторной работы
по дисциплине «Моделирование и оптимизация технологических процессов»
для студентов дневной и заочной форм обучения и экстерната
специальности 260901.65 «Технология швейных изделий»
специальности 260902.65 «Конструирование швейных изделий»
НОРМИРОВАНИЕ ВРЕМЕНИ ТЕХНОЛОГИЧЕСКИХ ОПЕРАЦИЙ
ПО ОБРАБОТКЕ ШВЕЙНЫХ ИЗДЕЛИЙ
В АВТОМАТИЗИРОВАННОМ РЕЖИМЕ
Новосибирск - 2017
Составитель: доц., к.т.н. Вершинина И. В.,
Рецензент: доц., к.т.н. Профорук Е. В.
Рассмотрено и утверждено на заседании кафедры ТДШИ
СОДЕРЖАНИЕ
1 ТЕОРЕТИЧЕСКОЕ ВВЕДЕНИЕ . . . . . . . . . . . . . . . . . . . . . | 5 |
2 МЕТОДИКА АВТОМАТИЗИРОВАННОГО НОРМИРОВАНИЯ ВРЕМЕНИ ТЕХНОЛОГИЧЕСКИХ ОПЕРАЦИЙ. . . . . . . . . . . . . . | 10 |
2.1 Общие сведения о системе . . . . . . . . . . . . . . . . . . . . . . . . 2.2 Постановка и алгоритм решения задачи автоматизированного нормирования времени технологических операций . . . . . . . . . . . . . . . | 10 15 |
3 КРАТКОЕ РУКОВОДСТВО ПОЛЬЗОВАТЕЛЯ ПРОГРАММОЙ АВТОМАТИЗИРОВАННОГО РАСЧЕТА НОРМ ВРЕМЕНИ ТЕХНОЛОГИЧЕСКИХ ОПЕРАЦИЙ. . . . . . . . . . . . . . . . . . . . | 18 |
СПИСОК ИСПОЛЬЗОВАННЫХ ИСТОЧНИКОВ . . . . . . . . . . . . . . | 22 |
ПРИЛОЖЕНИЕ А. Методика расчета нормы времени аналитически-расчетным способом . . . . . . . . . . . . . . . . . . . . . . . . . . . . . . | 23 |
|
|
ТЕМА: Нормирование времени технологических операций по обработке швейных изделий в автоматизированном режиме
ЦЕЛЬ РАБОТЫ: изучение методики автоматизированного нормирования времени технологических операций различных специальностей
СОДЕРЖАНИЕ РАБОТЫ:
1 Изучить методику нормирования времени технологических операций (ТО) аналитически-расчетным методом [1]
2 Пронормировать «вручную» заданные преподавателем 2-3 операции разных специальностей, используя «Отраслевые поэлементные нормативы времени…» [2,3] и ПРИЛОЖЕНИЕ А.
3 Ознакомиться с методикой автоматизированного нормирования времени ТО
4 Пронормировать те же ТО в автоматизированном режиме
|
|
5 Провести сравнительный анализ полученных результатов. Сделать выводы, оценить достоинства и недостатки методики автоматизированного нормирования времени ТО.
ТРЕБОВАНИЯ К ОТЧЁТУ
В отчёте необходимо представить:
1 Классификацию методов нормирования времени ТО.
2 Детальный расчет норм времени на заданные 2-3 операции (формулы, расчеты, результаты расчетов).
3 Логическую постановку задачи автоматизированного нормирования времени ТО.
4 Блок-схему алгоритма автоматизированного нормирования времени ТО (рисунок 1)
5 Распечатки отчетов об автоматизированном нормировании времени заданных 2-3 ТО.
4 Анализ различий, полученных при расчете норм времени различными методами
5 Выводы, в которых оценить достоинства и недостатки методики автоматизированного нормирования времени ТО, возможность промышленного использования.
1 ТЕОРЕТИЧЕСКОЕ ВВЕДЕНИЕ
Методы исследования трудовых процессов могут классифицироваться по ряду признаков: цели исследования, количеству наблюдаемых объектов, способу проведения наблюдения, форме фиксации его данных и т.п. основным методом нормирования времени технологических операций (ТО) в швейной отрасли является аналитический. Этот метод включает следующие этапы:
|
|
- разделение операции на приемы;
- проверка производственных возможностей оборудования и организации рабочего места с целью уменьшения затрат времени на каждый прием;
- проектирование наиболее производительных режимов работы, рационального состава и последовательности выполнения приемов в операции;
- определение необходимой затраты времени на каждый прием;
- установление нормы времени на операцию путем суммирования времени по каждому приему.
Общая схема-классификация методов нормирования затрат времени представлена на рисунке 1.1.
|
Рисунок 1.1 - Схема-классификация методов нормирования затрат времени
При аналитически-исследовательском методе затраты времени на приемы определяют непосредственным наблюдением.
При аналитически-расчетном методе выполняют расчет по формулам и соответствующим справочникам, разработанным на основе анализа большого количества данных, полученных аналитически-исследовательским методом.
Рассмотрим подробнее некоторые из методов нормирования времени ТО.
Хронометраж – это изучение и измерение отдельных, циклически повторяющихся элементов операции, отдельных элементов операции с помощью секундомера. Основной задачей хронометража является выявление факторов, влияющих на продолжительность каждого элемента исследуемой операции с целью проектирования ее рациональной структуры в целом и нормальной продолжительности отдельных ее элементов. Хронометражные исследования позволяют изучить, прежде всего, оперативное время. Хронометраж имеет ряд недостатков, основным их которых является субъективность результатов, т. к. норму времени устанавливают только по одному критерию – по общей продолжительности выполнения элементов трудового процесса. Достоверность результатов зависит от правильного выбора рабочих, рациональности организации трудового процесса, большая вероятность возникновения ошибок измерения. В некоторой степени эти недостатки можно уменьшить, если использовать более точные способы изучения трудовых процессов.
|
|
Фотография рабочего времени (ФРВ) – это вид наблюдений, при помощи которого изучают и анализируют затраты времени одним рабочим или группой, связанные с выполнением того или иного процесса на протяжении всего рабочего дня (смены) или его части, независимо от того, на что затрачено это время. ФРВ не раскрывает технологию и методы осуществления процесса, а лишь фиксирует его протекание. Цель ФРВ в выявлении резервов повышения производительности, улучшении использования оборудования. Назначение фотографии рабочего времени состоит в выявлении недостатков в организации труда и производства, вызывающих потери или нерациональное использование рабочего времени, проектировании более рационального распределения времени рабочей смены по категориям затрат времени, в определении фактической выработки продукции, темпа ее выпуска и равномерности работы в течение смены.
Метод моментных наблюдений. Применяется в случаях, когда предполагается охватить большое число объектов. Характерной особенностью метода моментных наблюдений является то, что наблюдатель не находится непрерывно на рабочих местах, а посещает их периодически через случайные интервалы времени. При помощи моментных наблюдений можно анализировать структуру рабочего времени практически на любом количестве объектов. По результатам моментных наблюдений можно: определить степень использования рабочего времени большим числом исполнителей и степень использования во времени большого количества оборудования; изучить структуру и установить удельный вес и абсолютные значения отдельных элементов затрат рабочего времени исполнителя; установить причины и определить простои рабочих и оборудования и разработать мероприятия по их устранению; получить необходимые исходные данные для разработки нормативов подготовительно-заключительного времени, времени обслуживания рабочего места, а также норм обслуживания. Для достоверности получаемых результатов необходимо, чтобы наблюдения были случайными и одинаково возможными, а их количество достаточно большим.
Самофотография. Метод изучения трудовых процессов, при котором сами исполнители регистрируют продолжительность и причины потерь рабочего времени на специальных бланках называется самофотографией. Хотя самофотография характеризует потери рабочего времени по организационно-техническим причинам не менее объективно, чем ФРВ, она не дает представление о потерях рабочего времени по вине самого исполнителя. Поэтому наряду с самофотографией нужно проводить и ФРВ.
Фотохронометраж. Посредством фотохронометража рабочее время изучают тогда, когда по организационно-техническим причинам или в связи с особыми правилами производственных работ не представляется возможным проведение хронометража. Фотохронометраж представляет собой комбинированный способ изучения рабочего времени, основанный на совмещении хронометража и фотографии рабочего времени. Сущность его в том, что ФРВ в отдельные периоды времени дополняется хронометражем.
Видеосъемка. Иногда детальное исследование трудовых процессов некоторыми вышеперечисленными методами затруднено или вообще невозможно, т.к. наблюдатель не успевает в короткие отрезки времени, за которые происходят некоторые действия, следить за показаниями приборов, одновременно записывая их показания в бланк. В этом случае помогает видеосъемка, т.к. она позволяет точно фиксировать трудовой процесс, а при воспроизведении просматривать некоторые детали в замедленном режиме.
Осциллографирование характеризуется непрерывной механической фиксацией трудовых процессов, выполняемых на электрическом оборудовании при помощи специального прибора – осциллографа. Данный метод характеризуется высокой точностью фиксации трудовых действий. Применяется для определения основного времени выполнения операции.
Результаты аналитически-исследовательских методов должным образом собранные и обработанные являются основой для составления справочников. Для того чтобы пронормировать время аналитически-расчетным способом, необходимо разделить операцию на простейшие, заранее пронормированные и содержащиеся в справочниках приемы, действия и движения исполнителей. Это является основой микроэлементного нормирования. Рассмотрим, из каких элементов состоит любая технологическая операция. Время технологической операции включает в себя подготовительно-заключительное, оперативное и время обслуживания рабочего места.
Подготовительно-заключительное время – это время, которое затрачивается на подготовку себя и своего рабочего места к выполнению производственного задания, а также на все действия по его завершению.
Оперативное время – это время, в течение которого рабочий выполняет задание (изменяет свойства предмета труда). Оно делится на основное (технологическое) и вспомогательное. Основное или технологическое время – это время, затраченное непосредственно на изменение предмета труда. В течение вспомогательного времени выполняются действия, необходимые для осуществления основной работы.
Затраты времени, связанные с уходом за рабочим местом и поддержанием оборудования, инструментов и приспособлений в рабочем состоянии в течение смены относят ко времени обслуживания рабочего места. К времени технического обслуживания рабочего места относится время на обслуживание рабочего места в связи с выполнением данной операции или конкретной работы (замена затупившегося инструмента и др.). К организационному обслуживанию относится уход за рабочим местом в течение смены, а также уборка рабочего места в конце смены. В норму времени обязательно должен быть заложен перерыв на отдых и личные надобности [1,4].
Аналитически-расчетные методы включают в себя более десятка различных систем микроэлементных нормативов. В настоящее время наиболее прогрессивным и широко используемым является аналитически-расчетный метод с использованием сборников «Отраслевые поэлементные нормативы времени по видам работ и оборудования…» [2, 3]. Эти сборники разработаны ЦНИИШПом. В одном из них [1] собраны затраты времени на приемы операций по пошиву верхней одежды, в другом [2] – по пошиву легких женских платьев и белья с учетом видов тканей, используемого оборудования и методов обработки. Расчет нормы времени проводится по ряду формул, составляющих методику. Методика расчета нормы времени указанным способом представлена в ПРИЛОЖЕНИИ А.
Использование этого метода дает обоснованные нормы времени, однако он трудоемок, требует опыта работы и не исключает ошибки при выполнении расчета. Это связано с большим количеством формул и возможных значений параметров, используемых в этих формулах.
Перечисленные проблемы могут быть решены с помощью автоматизации аналитически-расчетного метода нормирования технологических операций.
2 МЕТОДИКА АВТОМАТИЗИРОВАННОГО НОРМИРОВАНИЯ
ВРЕМЕНИ ТЕХНОЛОГИЧЕСКИХ ОПЕРАЦИЙ
2.1 Общие сведения о системе
В основу методики автоматизированного нормирования времени положен аналитически-расчетный метод. Работа пользователя с системой осуществляется в диалоговом режиме – путем ввода или выбора запрашиваемых данных. Реализуются следующие задачи:
- расчет норм времени операций, выполняемых на универсальных, специальных и специализированных машинах;
- расчет норм времени операций, выполняемых на полуавтоматах;
- расчет норм времени операций, выполняемых с помощью утюга;
- расчет норм времени операций, выполняемых с помощью ножниц, мела, приспособлений и без них.
Методика предусматривает:
1 Автоматический расчет отдельных составляющих норм времени и ее окончательного значения.
2 Автоматический расчет оперативного времени в зависимости от ее структуры (проектной ситуации).
3 Расчет основного, вспомогательного времени, времени на проверку качества в диалоговом режиме.
4 Возможность корректировки любых составляющих норм времени на любой стадии.
5 Возможность ввода технологической последовательности и нормирования времени всех операций, в нее входящих, с записью полученных норм в соответствующие строки технологической последовательности.
6 Вывод на печать отчета о расчете нормы времени.
Для правильного проектирования нормы времени каждой технологической операции предварительно исследовались их структуры (работы Т.А Железняковой). Например, для машинно-ручных операций было выявлено 5 различных структур, оперативное время в каждом случае считается по определенным правилам и формулам. Примеры выявленных структур схематично представлены на рисунках 2.1 – 2.5. Для задания нужной структуры в автоматизированном режиме они получили название проектных ситуаций (ПС).
![]() |
Рисунок 2.1 – Структурная схема машинно-ручной операции,
отображающей проектную ситуацию 1 (ПС1)
Вспомогательные приемы – состав 1 – это приемы по взятию пачек и деталей и подготовке их к работе (расправление, укладывание под лапку машины и т.д.)
Вспомогательные приемы – состав 2 – это приемы, необходимые для поворотов и перехватов деталей во время машинной работы.
Вспомогательные приемы – состав 3 – это приемы по откладыванию деталей и пачек деталей.
ТП – это выход пронормированной технологической операции в технологический процесс изготовления изделия.
Итак, ПС1 моделирует ситуацию, когда операция в изделии выполняется один раз. Например, «стачать средние срезы спинки» или «подшить низ юбки». В этом случае каждая составляющая оперативного времени будет вычислена один раз:
, (2.1)
где tоп – оперативное время, с;
tмр – время работы на швейной машине, включая время на перехваты и повороты, если они имеются, с;
tвсп – время на выполнение вспомогательных приемов, с;
tкач – время на проверку качества выполнения операции, с.
Операция в изделии может выполняться дважды – на симметричных деталях. Это необходимо учесть в структуре тенологической операции. Например, «стачать локтевые срезы рукавов» или «стачать подборта из частей». Каждая составляющая оперативного времени такой операции будет удвоена:
(2.2)
Условием задания проектной ситуации 2 (ПС2) является то, что симметричные детали изделия еще не присоединены к полуфабрикату – рисунок 2.2.
Рисунок 2.2 – Структурная схема машинно-ручной операции,
отображающей проектную ситуацию 2 (ПС2)
Из схемы видно, что вход в каждый блок осуществляется дважды. Это подтверждает правильность формулы 2.2.
Примером для следующей структурной схемы – рисунок 2.3 – могут служить операции «стачать боковые срезы юбки» или «втачать рукава в проймы изделия».
Рисунок 2.3 – Структурная схема машинно-ручной операции,
отображающей проектную ситуацию 3 (ПС3)
Хотя набор вспомогательных приемов из состава 1 будет разным: в первом случае: взять детали, подготовить их к работе и подложить под лапку швейной машины, а после выполнения строчки – переместить полуфабрикат к следующему участку работы, а во втором случае: еще и взять второй рукав, структура операции будет для них постоянной.
Формула, определяющая время оперативной работы для ПС3, имеет вид:
(2.3)
Операции «стачать срезы шести полотен юбки-годе» или «проложить три отделочные строчки по воротнику» могут служить примерами для следующей проектной ситуации – ПС4 – рисунок 2.4.
Рисунок 2.4 – Структурная схема машинно-ручной операции,
отображающей проектную ситуацию 4 (ПС4)
Если сравнить рисунки 2.3 и 2.4, можно заметить, что структуры операций схожи и отличаются лишь количеством входов и выходов из одинаковых блоков. Количество входов и выходов зависит от количества выполняемых строчек. Для ПС3 строчек всегда две, а для ПС4 – их число может меняться от трех до любого значения. Если обозначить число строчек N, то формулу для определения оперативного времени для ПС4 можно записать так:
(2.4)
Примерами следующей структуры могут служить операции «Застрочить по пять защипов на накладных карманах» или «Застрочить по три складки на кокетках переда». В этих случаях требуется выполнить по N строчек на двух симметричных, не соединенных с полуфабрикатом, деталях – рисунок 2.5.
Рисунок 2.5 – Структурная схема машинно-ручной операции,
отображающей проектную ситуацию 5 (ПС5)
Из рисунка 2.5 видно, что схема объединяет структуру ПС2 и ПС4. Поэтому формула для определения времени оперативной работы для ПС5 будет иметь вид:
(2.5)
Из аналогичных исследований, проведенных над операциями других специальностей, выяснено, что для них справедливы структуры ПС 1, ПС2, ПС4, а для полуавтоматов – еще ПС5 и ПС6. Для операций, выполняемых на полуавтоматах, существует ситуация, когда требуется пришить несколько пуговиц (установить несколько кнопок и т.п) на две симметричные детали уже после того, как они соединены с изделием. В этом случае структура операции видоизменяется – рисунок 2.6.
Рисунок 2.6 – Структурная схема машинно-ручной операции, отображающей проектную ситуацию 6 (ПС6)
Оперативное время для операции, выполняемой на полуавтомате при ПС6 определяется по формуле:
(2.6)
Таким образом, учет структуры операции путем выбора той или иной проектной ситуации позволит выполнить расчет времени правильно и обоснованно.
2.2 Постановка и алгоритм решения задачи автоматизированного
нормирования времени технологических операций
Целью автоматизированного нормирования времени ТО является определение нормы времени (в секундах) по набору формул (ПРИЛОЖЕНИЕ А). В качестве исходных данных используются основные сведения о технологической операции, содержащиеся в технологической последовательности: номер, наименование (идентификационные параметры); специальность, применяемое оборудование (необходимы для выбора соответствующих формул для расчета); а также дополнительные сведения о технологической операции, устанавливаемые нормировщиком (зависят от вида операции: для машинных, например, это конфигурация строчки и ее длина, наличие закрепок, количество поворотов, размеры и количество обрабатываемых деталей, сложность операции и т.д.).
Для нормирования времени в автоматизированном режиме необходимо формализовать методику «ручного» расчета, составив алгоритм процесса нормирования. Для этого необходимо проанализировать порядок выполнения расчетов по известным формулам и четко распределить функции между пользователем и компьютером.
Данная методика реализована в диалоговом режиме. В памяти компьютера имеется база данных о нормативах времени на отдельные приемы (в соответствии с [1]). Также система выполняет все расчеты, формирует выходные документы и дает возможность их распечатать. Пользователь осуществляет ввод исходных данных, обеспечивает выбор из предложенных машиной вариантов, оценивает правильность и достоверность выполненных расчетов, имеет возможность внесения корректив в случае принятия неправильного решения.
Базы данных технологических операций и применяемого оборудования открыты для изменения и постоянного пополнения в ходе работы. Справочники, изменения в которых недопустимы (поэлементные нормативы времени) закрыты для пользователя.
На рисунке 2.7 представлена блок-схема алгоритма автоматизированного расчета норм времени на технологические операции.
Рисунок 2.7 – Блок-схема алгоритма автоматизированного нормирования времени ТО
На рисунке 2.7 представлен неполный алгоритм, в нем намеренно не раскрыт детально процесс нормирования времени ручных, утюжильных операций и операций, выполняемых на полуавтомате. Предлагается после изучения работы программы студентам самостоятельно дополнить блок-схему алгоритма необходимыми блоками для указанных операций.
Алгоритм реализован с использованием MS Excel. Для работы программы на компьютере должна быть установлена операционная система Windows, пакет MS Office; должен быть подключен принтер.
Для правильной работы программы необходимо настроить «безопасность компьютера». В MS Excel 2003 и более ранних версиях необходимо выбрать «Сервис» à «Макрос» à «Безопасность» à «Степень безопасности» - выбрать «средняя». Перезапустить MS Excel еще раз. В MS Excel 2007, открывая программу, ответить на предупреждение системы безопасности «Запуск макросов отключен» - выбрать «Параметры» à «Включить это содержимое». После этого работать с программой в обычном режиме.
После выполнения нормирования времени на заданные операции, необходимо распечатать отчет (на одном или двух листах по согласованию с преподавателем).
3 КРАТКОЕ РУКОВОДСТВО ПОЛЬЗОВАТЕЛЯ ПРОГРАММОЙ
АВТОМАТИЗИРОВАННОГО РАСЧЕТА НОРМ ВРЕМЕНИ
ТЕХНОЛОГИЧЕСКИХ ОПЕРАЦИЙ
Работа с программой начинается с запуска файла «Расчет норм времени.xls». Работа осуществляется в диалоговом режиме. От пользователя требуется внимательно читать подсказки, перемещаться между вкладками, пользуясь кнопками, осуществлять ввод и выбор соответствующих данных. На рисунке 3.1 представлено главное меню программы.
Рисунок 3.1 – Главное меню программы «Расчет норм времени»
В режиме ввода технологической последовательности – рисунок 3.2 - можно вводить любые технологически операции, копировать их из других документов MS Office. Этот режим является необязательным – можно нормировать операции, не встречающиеся в технологической последовательности. В любом случае – далее осуществляется переход в режим нормирования времени – рисунок 3.3.
В этом режиме необходимо следовать указаниям программы, выполняя пошагово расчет нормы времени. Ввод данных осуществляется в желтых ячейках, все расчеты ведутся в белых. Ввод осуществляется с клавиатуры или выбором из выпадающего списка.
Рисунок 3.2 – Режим ввода технологической последовательности
Рисунок 3.3 – Режим нормирования времени.
Начать работу программы необходимо с кнопки «Обнулить все», затем задать все необходимые исходные данные и перейти в один из режимов расчета оперативного времени, нажав соответствующую кнопку. Например, окно расчета оперативного времени для машинной или спецмашиной операции выглядит так - рисунок 3.4.
Из данного режима возможен переход в другие необходимые – например – в режим «Группировка машинных операций по видам швов и строчек и сложности» или в режим выбора вспомогательных приемов, нажимая соответствующие кнопки.
Рисунок 3.4 – Режим расчета оперативного времени для машинных и
Спецмашинных операций.
После расчета всех составляющих оперативного времени можно вернуться к режиму нормирования времени, предварительно проверив правильность всех расчетов – рисунок 3.5.
Рисунок 3.5 – Проверка составляющих оперативного времени
Аналогичным способом можно рассчитать оперативное время на операцию любой специальности – нажав в режиме нормирования соответствующую кнопку – рисунок 3.6.
Рисунок 3.6 – Кнопки выбора режима расчета оперативного времени
После расчета оперативного времени необходимо выбрать проектную ситуацию, чтобы правильно учесть структуру операции. Для этого осуществляется переход из режима нормирования времени в режим выбора проектной ситуации – открывается окно со справочным материалом, в выделенной ячейки нужно выбрать номер проектной ситуации, а для ПС4 – ПС6 еще ввести параметр N – число выполняемых строчек (или других действий) – рисунок 3.7.
Рисунок 3.7 – Режим выбора проектной ситуации
После расчета нормы времени можно записать эту норму в технологическую последовательность и пронормировать другие ТО из последовательности, а можно распечатать полученный результат. На рисунке 3.8 представлен внешний вид выходного документа
Рисунок 3.8 – Выходной документ (лист 1 и лист 2)
Таким образом, выполняется полный расчет нормы времени на операцию любой специальности.
СПИСОК ИСПОЛЬЗОВАННЫХ ИСТОЧНИКОВ
1 Основы функционирования технологических процессов швейного производства: Учеб. пособие для ВУЗов и СУЗов / В.Е. Мурыгин, Е.А. Чаленко. - М.: Компания Спутник+, 2001. – 299с.
2 Отраслевые поэлементные нормативы времени по видам работ и обо-
рудования при пошиве верхней одежды. - М.: ЦНИИТЭИЛегпром,1983. – 263с.
3 Отраслевые поэлементные нормативы времени по видам работ и обо-
рудования при пошиве легкой и пляжной одежды, одежды и швейных изделий для новорожденных и детей ясельного возраста, нательного и постельного белья. - М.: ЦНИИТЭИЛегпром,1983. – 161с.
4 Справочник по организации труда и производства на швейных предприятиях./ Кокеткин П.П., Доможиров Ю.А., Никитина И.Г.,
Басалыго Л.И. -М.: Легпромбытиздат, 1985. – 312 с.
ПРИЛОЖЕНИЕ А
(обязательное)
Методика расчета нормы времени аналитически-расчетным способом
Норма времени на выполнение технологической операции Нвр, с, складывается из:
- tоп – времени основной (оперативной) работы, с ;
- АПЗО – времени подготовительно – заключительной работы и обслуживания рабочего места;
- АОЛН – времени на отдых и личные надобности исполнителя;
, с (А.1)
Время tоп, Аолн, Апзо определяется по-разному в зависимости от специализации работ и применяемых материалов.
Время АПЗО определяется путем суммирования времени приемов работы, направленной на чистку и смазку машины, уборку рабочего места, смену сломанной иглы, заправку ниток и пр. Перечень приемов и время на их выполнение, а также время на отдых и личные надобности приведены для разных специальностей в таблицах 27-31 [2] в % к времени оперативной работы и в секундах.
Время tоп для разных специальностей определяется следующим образом:
Дата добавления: 2019-01-14; просмотров: 275; Мы поможем в написании вашей работы! |
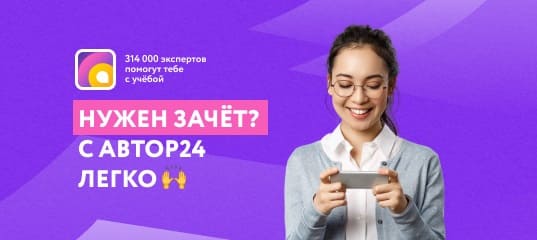
Мы поможем в написании ваших работ!