I. Say what type of machine does this or that operation.
- rams sand into the flask
- molds rapidly large castings
- draws patterns out of the mold
- lifts the mold away from the pattern
II. Describe the work done by every machine.
Unit 7. CASTING METALS
Cast Iron.— The term cast iron is applied to ferrous alloys. Among the ferrous metals, cast iron occupies first place and is recognized as one of the cheapest materials used in the manufacture of everyday life products. Cast iron is not considered a very strong or tough structural material, but it is the most economical. Its low melting point, low shrinkage, good fluidity, and machinability are properties that recommend its use.
Pig Iron.— The chief raw material for cast iron is pig iron, which is produced in a blast furnace by smelting iron ore with coke and a flux (substances promoting fusion) such as limestone. The final analysis of the pig iron is substantially determined by the kind of iron ore used in the smelting process.
Pig iron got its name from the shape of the molds in which metal from the blast furnace was cast. Originally, the pigs were cast in sand molds.
Modern large-volume production of pig iron is carried out by casting blast-furnace metal by means of a large machine, which is in principle an endless conveyer chain of pig molds.
Some pig irons are used in gray-iron foundries, and are called foundary pig irons. Pig iron used for making steel by the acid Bessemer process or the acid open-hearth process is known as Bessemer pig iron. Basic pig iron is used for the basic open-hearth process.
Non-Ferrous Metals. — The non-ferrous metals used in the foundary are usually alloys of two or more metals. Non-ferrous castings include those composed of copper-base alloys (brass and bronze), aluminium-base alloys, zinc-base alloys, tin-base alloys, lead-base alloys, bearing metals, and some special alloys composed of magnesium or nickel and other metals.
NOTES AND COMMENTARY
cast iron - чугун is applied to ferrous alloys – применяется к железистым сплавам everyday life products – предметы повседневного обихода pig iron – чушковый чугун blast furnace – доменная печь by smelting iron ore with coke and flux – путем плавки железной руды с коксом и флюсом got its name from the shape of the molds – получил это название от формы изложения | is carried out - осуществляется by means of - посредством (при помощи) endless conveyer chain – бесконечная конвейерная цепь gray - iron foundries – литейные заводы, изготавливающие серый чугун non - ferrous metals – цветные металлы aluminium - base alloys – сплавы с алюминиевой основой |
EXERCISES
|
|
I. Answer the questions.
1) What metal occupies the first place among the ferrous metals?
2) Where did pig iron get its name from?
3) What is pig iron used for?
4) What is the final analysis of iron determined by?
5) How is pig iron produced?
II. Find the sentences with these words in the text and translate them into Russian.
1) open-hearth
2) blast furnace
3) smelting
4) shrinkage
5) bearing metals
Unit 8. TYPES OF FURNACES.
Task:
- read the texts describing different types of furnaces
- make a plan to each text
- make up 5 questions to each of the texts
- retell any text you like
THE CUPOLA FURNACE
The cupola is the oldest type of furnace and the most economical. It may be obtained in different sizes and can be operated for as long a time as may be required to produce a given amount of melted metal. It is difficult to produce metal of precisely uniform quality in the cupola as compared to furnaces in which uniformity of the molten material can be controlled by frequent and periodic tests and adjustment. Cupola capacities vary from 1 to 15 tons of metal per heat (the amount of metal melted at one time).
The cupola is a cylindrical shell constructed from boiler plate and lined with firebrick. The main furnace structure is usually supported on cast-iron legs, and the opening at the bottom of the furnace may be closed by cast-iron doors, which swing up into position and are held closed by an iron upright at the center. Refractory sand protects these doors during the melting of the charge, which is placed over the layer of sand. At the end of the melting operation, the doors swing out of the way and materials remaining from the charge drop down through the opening.
|
|
On one side of the cupola, level with the bottom, is the breast opening for lighting the fire. This opening is also used as the tap hole. Opposite the tap hole, and somewhat higher, is the slag hole. The charging door is located approximately halfway up the vertical shell. The top of the cupola is open except for a metal shield.
A single row of openings or tuyeres is arranged around the circumference of the shell's interior at its base as a means of introducing air to the coke bed. A wind box, externally circling the cupola at the level of the tuyeres, supplies the air.
Cupola Zones. — A foundry cupola is generally divided into a number of zones: the crucible zone, tuyere zone, combustion zone, melting zone, preheating zone, and the stack zone.
The crucible zone is located at the bottom of the cupola; it is situated in the space between the sand bottom of the furnace and the bottom of the tuyere openings. Molten iron and slag accumulate in this space between the burning pieces of coke.
The tuyere openings are above the cruicible and take up a space from 3 to 6 inches in depth depending upon the size of furnace.
The combustion zone is that section of the cupola which extends from the bottom of the tuyeres to the top of the coke bed.
The melting and preheating zones extend from the top of the combustion zone to the charging door. The location of the charging door depends upon the size of the cupola. High charging doors, however, are recommended for large cupolas which are run all day, since greater fuel efficiency can be gained from the use of such charging doors.
The purpose of the stack, which is another zone of the cupola, is to carry off the waste gases. It is located above the charging door. A roof hood is usually fastened to the stack to prevent leaks around the cupola.
Diagram of a Foundary Cupola for Melting Cast Iron
NOTES AND COMMENTARY
cupola furnace - вагранка at one time - одновременно lined with firebrick – облицованный огнеупорным кирпичом is usually supported on cast-iron legs – обычно поддерживается чугунными опорами swing up into position - закрываются held closed – держатся закрытыми iron upright – чугунной подпоркой refractory sand – огнеупорный песок melting of the charge – плавка загрузки swing out of the way - открываются drop down – падать вниз on one side – с одной стороны level with the bottom – на уровне с днищем breast opening – окно, летка tap hole – выпускное отверстие slag hole – шлаковая летка charging door – загрузочное отверстие | except for a metal shield – кроме металлического щита coke bed – коксовая колоша wind box – воздушная коробка the crucible zone – тигельная зона tuyere zone – фурменная зона combustion zone – зона горения preheating – (предварительный) нагрев stack zone – шахта (печи), зона отвода газов take up a space – занимать пространство the top of the coke b е d – верхний слой коксовой колоши to carry off the waste gases – выводить лишние газы roof hood - покрышка, зонт |
THE BLAST FURNACE
|
|
The modern blast furnace is a tall circular structure about 100 ft. high built of firebrick and reinforced by a steel shell on the outside. The interior form is circular. A heavy concrete and brick foundation is built either on bedrock or upon heavy pilings driven deep into the earth if bedrock is too far below the surface.
Iron is reduced from the ore in the furnace by means of coke charged with ore, and the impurities are fluxed or slagged by means of limestone also charged with the ore. The air blown through the furnace is heated by means of stoves that constitute an important part of the apparatus of the blast furnace. These stoves heat the brickwork in them to about 1150°C and the air pumped through the stoves is thus heated to about 900°C before it is blown into the furnace.
|
|
The ore, coke, and limestone are conveyed from the ground to the top of the furnace by means of two cars running on an inclined hoist. The cars dump the charge into a hopper from which it is then dropped into the furnace by lowering first the upper bell, then lowering the lower bell. The use of these two bells prevents gases and flame from being blown into the air from the top of the furnace every time it is charged. Hot air is blown into the furnace through the tuyeres in the hearth of the furnace.
As the iron and slag are formed, they drop to the hearth at the bottom of the furnace. Since the iron is heavier than the slag, it settles to the bottom while the slag floats on the top of the molten iron. There are two holes in the hearth of the blast furnace. The iron is tapped from the lower hole; the slag is tapped from the upper hole. Many of the impurities in the ore are collected and removed with the limestone in the form of molten slag.
The iron runs from the furnace into troughs which convey it to a ladle. The iron in the ladle is then cast into pigs or else taken while molten to the steel making furnaces.
NOTES AND COMMENTARY
blast furnace – доменная печь reinforded by a steel shell on the outside – укрепленная стальным кожухом извне upon heavy pilings driven deep into the earth – на тяжелых сваях, вбитых глубоко в землю bedrock – скальная порда by means of coke charged with ore – при помощи кокса, загружаемого с рудой constitute an important part – составляют важную часть brickwork – кирпичная кладка to the top of the furnace – на колошник печи | cars running on an inclined hoist – тележки, движущиеся по наклонному подъемнику dump the charge into the hopper – сбрасывает загрузку в хоппер upper bell – верхний конус lower bell – нижний конус as the iron and slag are formed – по мере образования чугуна и шлака is cast into pigs – отливается в чушки or else taken while molten to the steel making furnaces – или же отправляется в печи для изготовления стали |
THE BESSEMER CONVERTER
In the Bessemer process of making steel air is blown through the molten pig iron, and the oxygen of the air combines with the carbon, manganese, and silicon of the pig iron. This action generates heat and frees the iron from the major part of its impurities thus converting the iron into steel.
The Bessemer converter, in which the process takes place, is a pear-shaped tilting vessel made of steel plates and lined with heat-resisting bricks and clay. The top of the converter is cut off to form a mouth through which molten metal is charged and discharged. In the bottom of the vessel are a number of holes through which air is blown.
When the air blast is turned on, a shower of sparks bursts from the mouth of the converter. Immediately thereafter appear short ruddy flames and a dense cloud of reddish-brown fumes caused by the burning of the silicon and manganese in the iron. In about five minutes this part of the refining action is accomplished, and the next stage, the removal of carbon, begins.
The ruddy flames become more luminous, changing to a
yellowish white.
For about ten minutes the glare continues, and during that time the converter emits a deep roar caused by the violent generation of gas within it.
Suddenly the flame drops, and the operator must diminish the blast of air and remove the metal from the converter.
Bessemer steel is used because of the low cost of the process.
Today we have a new, more perfect technology of converting pig iron into steel in which the blast of air is replaced by a jet of nearly pure oxygen.
NOTES AND COMMENTARY
generates heat – производит тепло frees the iron from the major part of its impurities – освобождает чугун от большей части примесей thus converting the iron into steel – таким образом, превращая чугун в сталь pear-shaped tilting vessel – грушеобразный наклоняющийся сосуд made of steel – сделан из стали lined with - облицован | the top of the converter is cut off to form a mouth – верх конвертера срезан, образуя горловину turned on - включен a shower of sparks bursts from the mouth – поток искр вырывается из горловины the converter emits a deep roar caused by the violent generation of gas within it – конвертер издает сильный рев, вызванный бурным образованием газа в нем |
THE OPEN HEARTH FURNACE
The name open hearth is given to it because the hearth of the furnace is exposed to the sweep of the flames which melt the steel.
The open-hearth process is one of the most important methods of making steel. It is much slower than the Bessemer but it is easier to control, and for that reason it is more frequently used.
The furnace is lined with firebrick to withstand the very high temperatures used. The charge consists of molten pig iron, scrap iron and steel and some hematite. Lime is added to the charge to take out the phosphorus and sulphur as slag. Manganese, carbon, nickel, vanadium, or other materials are added to make the kind of steel desired.
The fuel is blown into furnace through one of the two large openings, or ports, located on each end of the furnace. To facilitate combustion, previously heated air is blown through the port along with the fuel. Combustion occurs above the hearth, and the smoke and other products of combustion escape through the ports at the other end of the furnace.
Beneath the furnace are two large chambers through which air or gas flows freely.
There are three stages in the operation of this furnace. The first is known as the process of charging; the second — as the melting down process; the third — the period of refining. The period of refining is especially important and requires the constant supervision of the operator. The refining consists first in removing objectionable impurities and then controlling the elements other than iron which the final product must contain. Alloying elements are added to the steel before it is tapped or when it is in the ladle.
NOTES AND COMMENTARY
open-hearth furnace – мартеновская печь for that reason - по этой причине the hearth is exposed to the sweep of the flames – дно печи подвергается воздействию факела пламени the charge consists of molten pig iron, scrap iron and steel and some hematite – загрузка состоит из расплавленного чугуна, лома и стали и небольшого количества красного железняка to take out – чтобы перевести to make the kind of steel desired – чтобы получить нужный сорт стали | to facilitate combustion previously heated air is blown – чтобы ускорить горение, вдувается заранее нагретый воздух с ombustion occurs above the hearth – горение происходит над подиной (ванной) melting down process – процесс плавления the period of refining – период рафинирования the constant supervision of the operator – постоянное наблюдение оператора the elements other than iron which the final product must contain – элементы кроме чугуна, которые должны содержаться в окончательном продукте |
THE ELECTRIC FURNACE
The finest grades of steel are produced by the electric furnace method. Stainless and heat resistant steels are made almost exclusively by that process.
Electricity is used only for the production of heat and does not of itself impart any superior quality of steel. Nevertheless, the electric furnace method gives certain advantages impossible in other steel melting processes. The electric furnace generates extremely high temperatures. The temperature is at all times under precise control and is easily regulated.
The production of heat by electricity is unique, oxygen is not necessary to support combustion and the atmosphere within an electric furnace may be regulated at will.
The electric furnace is a circular steel shell resembling a huge tea-kettle in general appearance. It is mounted on rockers so that the furnace can be tilted to pour off molten metal and slag. The bottom of the furnace consists of a layer of heat resistant materials below which it is lined with refractory bricks. The side walls which are also lined with refractory bricks contain three or more openings.
The roof of the furnace is lined with 250 mm or more of refractory bricks and is shaped like a flat dome. Through this dome great columns of carbon reach into the furnace. These are the electrodes which carry the current to the steel charge.
NOTES AND COMMENTARY
finest grades of steel – лучшие марки стали does not of itself impart any su perior quality of steel – само по себе не придает стали какого-либо высшего качества is at all times under precise control and easily regulated – все время находится под точным контролем и легко регулируется at will – по желанию | Is mounted on rockers so that the furnace can be tilted to pour off molten metal – установлена на поворотных опорах так, что печь может наклоняться для слива расплавленного металла is lined with - облицована is shaped like flat dome – имеет форму, похожую на плоский колпак |
Дата добавления: 2019-01-14; просмотров: 700; Мы поможем в написании вашей работы! |
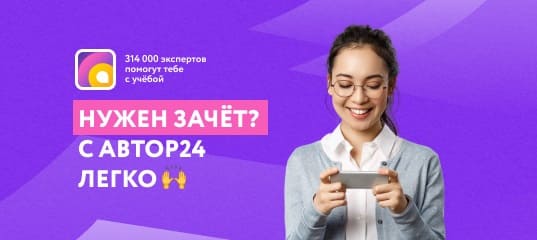
Мы поможем в написании ваших работ!