Методи нормування технологічних процесів
Вступ
Машинобудівне підприємство ТОВ "МАГМА" являє собою сучасний виробничий комплекс, створений 20 серпня 2001 року, що має в своєму складі спеціалізовані виробництва і випускає складну технічну продукцію.
Протягом ряду років підприємство виготовляє нестандартне облад нання і запчастини для металургійного і кранового устаткування, ГЗК, морських і річкових портів.
За порівняно невеликий період часу підприємству вдалося успішно налагодити міцні партнерські відносини з найбільшими підприємствами України та СНД.
Маючи в своєму розпорядженні сучасне металообробне і механоскладальне виробництво, висококваліфіковані кадри, підприємство виготовляє унікальне за своїми характеристиками нестандартне обладнання і деталі різних класів точності і типорозмірів, масою від декількох кілограмів до 120 тонн.
Розвиток власного складського господарства дозволяє постійно підтримувати на складі найширший асортимент заготівель, поковок, лиття і ін. металопрокату.
На підприємстві впроваджена і застосовується система менеджменту якості відповідно до вимог міжнародного стандарту DIN EN ISO 9001: 2008, це дозволило організувати чітко налагоджений зв'язок комерційних і технічних служб на всіх етапах від закупівлі сировини, матеріалів і комплектуючих до відвантаження споживачеві кінцевої продукції. Сертификат на систему менеджменту якості є документальним підтвердженням здатності підприємства виробляти продукцію, що задовольняє вимоги замовника.
|
|
Документація системи менеджменту якості, розроблена на підприємстві, чітко визначає взаємозв'язок між підрозділами в питаннях планування, контролю технології виробництва, забезпечення якості продукції та формування основних показників діяльності підприємства.
Проводиться акредитація аналітичної лабораторії з контролю виробництва, оснащена обладнанням, приладами та методиками необхідними для виконання необхідного обсягу вхідного контролю і супроводу технологічного процесу, приймально-здавальних випробувань готової продукції.
Відділ технічного контролю (ВТК) взаємодіючи з лабораторією з контролю виробництва, в рамках підготовки виробництва, допускає до використання тільки ті вихідні матеріали, які пройшли повний вхідний контроль. Такий зв'язок дозволяє виключати придбання недоброякісної сировини, матеріалів, комплектуючих, що істотно впливає на якість готової продукції.
Організація і проведення ремонтів механічного та енергетичного обладнання виконуються безпосередньо персоналом підприємства в суворій відповідності з технічною документацією.
Використовуючи розроблену документацію для ведення технологічних процесів, контролюючи продукцію на всіх стадіях її виробництва, дозволяє при виявленні невідповідностей визначати причини і усувати їх, а головне розробляти і впроваджувати коригувальні, запобіжні заходи з метою виключення їх в подальшому.
|
|
Позитивна динаміка в роботі нашого підприємства пояснюється: розширенням технологічних можливостей, впровадженням нових технологій, навчанням виробничого персоналу, збільшенням виробничих потужностей.
Згідно з планом стратегічного розвитку підприємства, зданий в експлуатацію новий корпус ЦМК загальною площею 3024 кв.м., призначений для виробництва сталевих металоконструкцій промислового призначення. Виробнича потужність цеху - до 3000 тонн в рік.
Методи отримання заготовок
Основний напрямок підприємства ТОВ «МАГМА» - виготовлення нестандартного обладнання і запчастин для металургійних підприємств. Для виготовлення деталей використовується плоский прокат (лист товщиною до 100 мм), фасонний прокат (швелер, куточок, двотавр), круглий прокат (кола), поковки і відливки.
Всі ці матеріали ,з яких виготовляються деталі конструкції машин сприймають силові навантаження є конструкційними матеріалами. Визначальними параметрами конструкційних матеріалів є механічні властивості, що відрізняє їх від інших технічних матеріалів (оптичних, ізоляційних, мастильних, лакофарбових, декоративних, абразивних і інше).
|
|
На підприємстві ТОВ «МАГМА» використовуються - прокат, видливки , мідь і її сплави та інше. Основною заготівкою в машинобудуванні є поковки і відливки. Залежно від призначення і ступеня відповідальності деталі заготівках пред'являються певні вимоги і за видами випробувань їх поділяють на групи. Віднесення поковки до тієї чи іншої групи проводиться споживачем, номер групи вказується в технічних вимогах на кресленні деталі.
За вимогами споживача здача поковок може проводитися з додатковими видами випробувань, не передбаченими ГОСТом (перевірка на флокени, ультразвуковий контроль, визначення величини залишкових напружень, границі текучості при робочих температурах, визначення ударної в'язкості при робочих і негативних температурах, макро- і мікроаналіз структури сталі, визначення величини зерна і ін.).
В цьому випадку поковки також відносяться до однієї з груп: II, III, IV та V відповідно до таблиці 1.
|
|
Таблиця 1
Група поковок | Види випробувань | Умови комплектування партії | Здавальні характеристики |
I | Без випробувань | Поковки однієї або різних марок сталі | - |
II | Визначення твердості | Поковки однієї марки сталі,які спільно пройшли термічну обробку. | Твердість |
III | Визначення твердості | Поковки однієї марки сталі,які спільно пройшли термічну обробку за однаковим режимом. | Твердість |
IV | 1.Випробування на розтягнення. 2.Визначення ударної в'язкості. 3.Визначення твердості. | Поковки однієї плавки сталі,які спільно пройшли термічну обробку. | Межа текучості; Відносне звуження; Ударна в'язкість. |
- | |||
V | 1.Випробування на розтягнення 2. Визначення ударної в'язкості 3.Визначення твердості. | Приймається індивідуально кожна поковка. | Межа текучості;Відносне звуження;Ударна в'язкість |
- |
Норми часу та їх структура
Норма часу - це кількість робочого часу,який потрибен для виконання певної роботи (операції) в найбільш раціональних для даного підприємства організаційних, технічних, господарських умовах. Норма часу встановлюється в годинах, хвилинах. Під структурою норми часу розуміється склад витрат робочого часу, необхідного для виконання одиниці роботи. Норма часу складається з:
- Норма підготовчо-заключного часу(Тпз)( витрати часу на підготовку та роботи, пов'язані з її завершенням);
- Норма штучного часу(Тшт)( витрати часу на одиницю роботи),який включає:
- оперативний час(Топ) – поділяється на:
- основний час (То) витрачається на зміну предмета праці, його властивостей, форм, розмірів, складу, стану;
- допоміжний час(Тв) - це час, протягом якого відбувається завантаження сировини, заготовок, знімання готової продукції, управління обладнанням, контроль за ходом технологічного процесу і якістю продукції;
- час обслуговування робочого місця(Тобс);
- час технічного обслуговування(Ттех) - це час, протягом якого проводиться заміна інструменту,що затупилося, регулювання пристроїв та обладнання, а також правка інструменту, видалення відходів, що проводяться в процесі роботи;
- час організаційного обслуговування(Торг) - це час, що витрачається на підтримання робочого місця в робочому стані протягом всієї зміни;
- час регламентованих перерв:
- час на відпочинок і особисті потреби(Твід);
- час перерв, встановлених технологією і організацією виробничого процесу(Тпт), включає час перерв, викликаних специфічними умовами протікання технологічних процесів.
Методи нормування технологічних процесів
Аналітичний метод - сутність якого полягає в тому, що час, необхідний для виконання заданої операції, визначається розрахунковим шляхом, виходячи із заданих режимів, технічних характеристик обладнання, що застосовується, а також встановлених нормативів для даних організаційно-технічних умов виробництва. Аналітичний метод є найбільш точним і об'єктивним.
Метод хронометрування і фотографування процесу виконання роботи, сутність якого полягає в тому, що в процесі виконання заданого технологічного процесу нормувальник фіксує витрати робочого часу за елементами, підсумовує його з декількох спостережень визначає середнє значення, яке приймається за норму, а також для встановлення нормативів на різні елементи в складі норми.
Експертний (наочний) метод, сутність якого полягає в тому що, нормувальник подумки уявляє собі процес виконання заданої роботи за елементами і переходах і відповідно до цього поданням подумки визначає час виконання по кожному елементу і переходу, фіксує цей час, підсумовується знаходить середнє з 3 - 4 показань, яке приймається за норму.
Цей метод приймається головним чином при нормуванні таких технологічних процесів, які не піддаються нормуванню аналітичним методом. Надалі норми, встановлені цим методом, зазвичай коригуються за допомогою методу хронометрування. Крім цих основних методів нормування, існує ряд прийомів спрощеного нормування за існуючими середніми і укрупненим даним.
Нормування токарних робіт
Дата добавления: 2019-01-14; просмотров: 235; Мы поможем в написании вашей работы! |
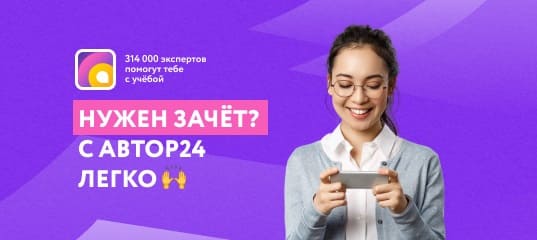
Мы поможем в написании ваших работ!