Диаграмма условных напряжений
Механические характеристики материалов
Чтобы исключить влияние размеров и формы деталей, во-первых, испытания проводят на стандартных образцах ГОСТ 1497-84. Во-вторых, результаты пересчитывают на относительные величины: прикладываемую нагрузку – в механическое напряжение ; абсолютную деформацию – в относительную деформацию
.
Перестроенная таким образом диаграмма называется диаграммой условных напряжений (рис. 5). Такое название объясняется тем, что площадь образца в процессе испытания изменяется.
Рис. 5. Диаграмма условных напряжений малоуглеродистой стали
Предел пропорциональности . Значению нагрузки Рпц, при которой нарушается линейная зависимость между нагрузкой Р и удлинением Dl (закон пропорциональности), на диаграмме соответствует точка А. Напряжение, вызванное нагрузкой Рпц, называется пределом пропорциональности и вычисляется по формуле
. (1.1)
Таким образом, пределом пропорциональности называется напряжение, после которого нарушается закон Гука
s = Е e,
где Е – модуль нормальной упругости или модуль жесткости. Модуль E графически изображается тангенсом угла наклона прямолинейного участка к оси абсцисс диаграммы условных напряжений . Величина модуля зависит от природы сплава и изменяется незначительно при изменении состава, структуры или после термической обработки. Например, для стали E = (2,0¸2,2)×105 МПа, для чугуна E = (0,75¸1,6) ×105 МПа.
|
|
Предел упругости . Наибольшему значению нагрузки Руп , при которой образец еще не дает при разгрузке остаточной деформации, соответствует точка В. Упругой стадии растяжения образца – участок диаграммы ОВ.
Наибольшее напряжение, до которого остаточная деформация при разгрузке не обнаруживается, называется пределом упругости. Это напряжение вызывается силой Руп и определяется по формуле
. (1.2)
Предел упругости является характеристикой, не связанной с законом Гука. Точка В может располагаться как выше, так и ниже точки А. Эти точки, а следовательно и значения напряжений sпц и sуп близки и обычно различием между ними пренебрегают.
Предел текучести – напряжение, при котором происходит рост деформации без увеличения растягивающей нагрузки. Величина предела текучести вычисляется по формуле
. (1.3)
У большой части технических металлов и сплавов на диаграмме отсутствует явно выраженная площадка текучести. В этом случае предел текучести определяется с допуском 0,2 %, т.е. – условный предел текучести (s0,2) – напряжение, при котором образец получает остаточное (пластическое) удлинение, равное 0,2 % своей расчетной длины:
|
|
(1.4)
Предел прочности (временное сопротивление разрыву) – напряжение, соответствующее наибольшей нагрузке Рmax, которую выдерживает образец
. (1.5)
Напряжение в момент отрыва образца. Обозначив через Рк величину растягивающей нагрузки в момент разрыва, получим
. (1.6)
Определяемое таким образом напряжение при разрыве образца не может быть использовано в качестве характеристики механических свойств металлов и сплавов. Оно получено делением нагрузки в момент разрыва на первоначальную площадь поперечного сечения образца, а не на действительную его площадь при разрыве, которая значительно меньше начальной, вследствие образования шейки.
Механические характеристики sпц, sуп, sт и sв называются характеристиками прочности материалов. В практических расчетах оценка механических свойств преимущественно проводится по пределу текучести sт и пределу прочности sв. Например, для малоуглеродистой стали (0,2 % С), имеющей площадку текучести: sт = 300 МПа, sв = 450 МПа.
|
|
Кроме перечисленных выше характеристик прочности материала при испытании на растяжение определяют также относительное удлинение после разрыва d и относительное сужение после разрыва y:
(1.7)
(1.8)
где: l0 – первоначальная расчетная,
lk – конечная расчетная длина образца;
– начальная площадь поперечного сечения,
– площадь поперечного сечения в наиболее тонком месте шейки после разрыва (рис. 4).
Механические характеристики d и y являются характеристиками пластичности материала: чем они больше, тем материал пластичнее. Для сталей, например, d = 8 ¸ 45% , y = 40 ¸ 65% .
Порядок проведения испытаний
Перед испытанием необходимо ознакомиться с устройством машины МИРИ-100К и правилами поведения в лаборатории (вводный инструктаж).
До испытания проводится измерение штангенциркулем размеров образца (см. рис. 1) по рабочей части l0 и d0 с погрешностью до 0,1 мм. Для этого проводится измерение длины рабочей зоны, отмеченной на образце накерненными точками и диаметра образца в трех сечениях расчетной зоны. За расчетный диаметр принимается среднее значение по выполненным трем замерам. Рассчитывается начальная площадь поперечного сечения F о.
|
|
На рабочей части образца наносят метки на расстоянии 5 или 10 мм друг от друга. Благодаря меткам можно определить деформацию каждого 5 или 10-миллиметрового промежутка, так и всей рабочей длины образца.
Образец устанавливается в захваты испытательной машины и производится его растяжение.
1. Определение предела текучести и предела прочности. После проведения испытания по машинной диаграмме растяжения определяют нагрузку Рт , соответствующую пределу текучести, и наибольшую разрушающую нагрузку Pmax . Используя значения Рт , Pmax и площадь F0 по формулам (1.3 и 1.4) определяют прочностные характеристики материала sт и sв .
2. Определение характеристик пластичности материала. После испытания части разорванного образца складывают и штангенциркулем измеряют конечную расчетную длину lk . а также толщину в наиболее тонком месте шейки dk. При разрыве образца в средней части расчетной длины измерение lk производится между крайними рисками, как показано на рис. 8. Измерив lk по формулам (1.7–1.8) определяют характеристики пластичности материала на растяжение d и y:
Рис. 8. Определение конечной расчетной длины при разрыве образца
в средней части
3. Определение предела пропорциональности. Условный предел пропорциональности находится тогда, когда по диаграмме трудно точно определить точку, до которой сохраняется линейная зависимость между прикладываемой нагрузкой и удлинением образца.
Величину нагрузки Рпц можно с некоторым приближением определить графически на диаграмме растяжения (см. рис. 9,а). Отклонение от линейной зависимости между нагрузкой и удлинением должно достигнуть такой величины, когда тангенс угла наклона кривой деформации с осью нагрузок увеличится на 50% своего значения на линейном упругом участке.
· Из начала координат проводят прямую OM, совпадающую с начальным линейным участком диаграммы растяжения.
· Проводят прямую линию АВ, параллельную оси абсцисс.
· На прямой АВ откладывают отрезок kn, равный половине отрезка mk.
· Через точку n и начало координат проводят прямую О n. Тангенс угла наклона прямой О n к оси ординат (b) и будет на 50 % больше тангенса угла наклона прямолинейного участка диаграммы растяжения OM (a ).
· Параллельно линии О n проводят касательную линию CD к диаграмме растяжения.
· Точка касания К определяет нагрузку Рпц .
· В соответствии с формулой (1.1) рассчитывают значение предела пропорциональности sпц .
4. Определение условного предела текучести с допуском 0,2 %. Вследствие неполного контакта между головками образца и гнездами для них в траверсе, в начале диаграммы получается криволинейный участок, который следует исключить, продолжив прямолинейный участок диаграммы до пересечения с осью абсцисс в точке О (рис. 9,б).
· Вычисляют величину пластической деформации, которая составляет 0,2%, от начальной расчетной длины l0 .
· Найденную величину увеличивают пропорционально масштабу диаграммы и отрезок ОЕ = 0,002 l0 (см. рис. 9,б) откладывают от точки О.
· Из точки Е проводят прямую, параллельную ОА. Точка пересечения прямой с диаграммой соответствует нагрузке Р0,2.
· По формуле (1.6) рассчитывают значение условного предела текучести s0,2.
5. Определение работы, затраченной на деформацию образца. Для оценки качества испытанного материала необходимо определить работу, затраченную на разрыв образца.
· Работу деформации в пределах упругости можно выразить через площадь диаграммы ОАА1О (см. рис. 10).
· Работа, затраченная на образование пластической деформации, графически определяется площадью OACDК K 1.
· Полная работа (А), затраченная при растяжении образца до его разрушения, численно равна площади диаграммы растяжения OACD KK2O с учетом тех же масштабов сил и удлинений: 1 см2 площади диаграммы соответствует работе деформации 1 кг×см.
Рис. 9. Начальные участка диаграммы растяжения:
а– для определения условного предела пропорциональности;
б– для определения условного предела текучести
· Удельная работа (а) – отношение полной работы А, затраченной на разрушение образца, к начальному объему средней цилиндрической части образца V
а = А / V
характеризует способность материала образца поглощать энергию разрыва, вязкость материала и сопротивляемость его динамическим воздействиям нагрузки.
Для упрощения расчетов, работу, затраченную на пластическое деформирование, определяют как площадь прямоугольника с основанием Dl ост и высотой Рmax (см. рис. 3).
Рис. 10. Полная диаграмма растяжения
Дата добавления: 2019-01-14; просмотров: 1548; Мы поможем в написании вашей работы! |
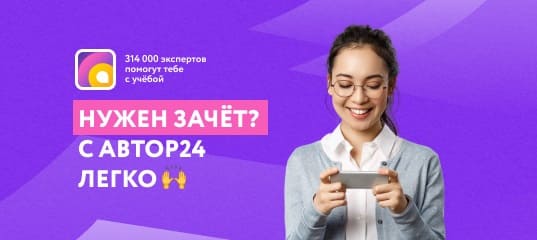
Мы поможем в написании ваших работ!