Способы выявления макроструктуры
Различают следующие реактивы универсального действия для углеродистых и низколегированных сталей:
1. Водный раствор азотной кислоты: 4-10% HNO3, остальное вода. Реактив применяют в холодном состоянии. При травлении шлиф протирают ватным тампоном или погружают в реактив, периодически его протирая. После травления шлиф промывают в воде и высушивают. При выявлении волокнистой структуры или дендритов после травления рекомендуется проводить легкую шлифовку тонкой шкуркой. Продолжительность травления: от нескольких минут до получаса.
Реактив хорошо выявляет пустоты, волокнистую структуру зоны сварного соединения, флокены. Его можно использовать для выявления дендритной структуры. Реактив успешно действует на углеродистые и низколегированные стали.
2. Спиртовой раствор азотной кислоты (4%-ный раствор НNО3 в этиловом спирте). Продолжительность травления: от 20 мин до 4 ч. Реактив хорошо выявляет структуру в сварных швах.
3. Водный раствор соляной кислоты: 50 см3 НСl, 50 см3 воды. Травление производят погружением в горячий реактив. Продолжительность травления составляет от 10 до 45 мин. Основное применение – выявление пустот. Хорошо обнаруживаются также ликвация, волокнистость, пороки литья, структура сварных швов. Температура раствора 60–70°С. Применяется для травления разнообразных легированных сталей. На рис. 2.8 приведен пример применения реактива.
4. Водный раствор соляной и серной кислот: 500 см3 НС1; 70 см3 H2SO4; 180 см3 воды. Раствор применяют в горячем состоянии – при 95–100°С. Продолжительность травления до 2 ч. Травление ведут погружением.
|
|
Реактивы дают глубокое травление и их применяют для выявления пустот, ликвации, грубой волокнистой и дендритной структуры (рис. 2.9).
Рис. 2.8. Пример использования раствора 3. Структура литой углеродистой стали
Рис. 2.9. Пример применения смеси серной и соляной кислот.
Дендритное строение литой углеродистой стали
Порядок выполнения работы
1. Ознакомиться с характерными особенностями макроструктур, дефектов, образующихся при различных технологических операциях обработки материалов и изготовления деталей: металлургия, ОМД, литье, сварка, термическая обработка - путем просмотра атласов или слайдов на видеопроекторе.
2. Освоить технику приготовления и травления макрошлифов.
3. Исследовать предложенную коллекцию изломов, макрошлифов и сварных соединений. Дать заключение о причинах возникновения дефектов в исследуемых образцах металла (по макрошлифам).
4. Определить и описать виды исследуемых изломов и причины их возникновения. Дать заключения о качестве сварки, наличии дефектов и надежности сварного соединения, исследовав его макроструктуру.
|
|
5. Составить отчет по работе.
\
Содержание отчета
При составлении отчета необходимо четко указать задачи макроструктурного анализа, изложить методику приготовления и травления макрошлифов, описать дефекты исследованных макрошлифов, зарисовать их и указать причины возникновения.
Описать характер изученных изломов, макроструктуру сварных соединений и привести заключение о качестве сварки.
Контрольные вопросы
1. С какой целью проводится входной контроль металлопродукции?
2. Какие параметры качества определяется при входном контроле?
3. От каких факторов зависит объем входного контроля?
4. В каких случаях к входному контролю привлекается Центрально-заводская
лаборатория?
5. От каких факторов зависит макроструктура металла?
6. Как можно узнать, какова макроструктура внутренних участков металлических
заготовок?
7. С помощью каких технических средств можно изучать внешний вид и размеры
деталей и образцов?
8. Что такое макроструктурный анализ?
9. Расскажите, что можно выявить макроструктурным анализом.
10. Что можно обнаружить внешним осмотром поверхности металла?
|
|
11. Объясните, что дает изучение излома.
12. Зачем при анализе макроструктуры выявляют волокнистость металла?
13. Что такое горячие (кристаллизационные) трещины?
14. Объясните причины возникновения трещин напряжения.
15. Каковы характерные признаки трещин напряжений?
16. Каковы причины возникновения шлифовочных трещин?
17. Что собой представляет усадочная раковина и как она образуется?
18. В чем выражено волокнистое строение прокатанного металла?
19. Что такое дендритная ликвация и как она выявляется при анализе макроструктуры?
20. Что такое и в чем выражена зональная ликвация?
21. Чем различаются экзогенные и эндогенные неметаллические включения?
22. Что собой представляют волосовины и в каком металле их можно выявить?
23. Что такое флокены и как они выглядят?
Список использованной литературы
1. ГОСТ 10243-75. Сталь. Методы испытаний и оценки макроструктуры. М. Изд.
стандартов. 1985.
2. Ю.А. Геллер, А.Г. Рахштадт. Материаловедение. Методы анализа, лабораторные
работы и задачи. М. Металлургия. 1989. 456с.
3. К.Г. Шмитт-Томас. Материаловедение для машиностроения. Справочник. М.
Металлургия. 1995. 512с.
4. Контроль качества термической обработки стальных полуфабрикатов и деталей.
|
|
Справочник под. ред. В.Д. Кальнера. М. Машиностроение. 1984. 384с.
5. И. Гривняк. Свариваемость сталей. М. Машиностроение. 1984. 216с.
6. Л.П. Герасимова. Контроль качества сварных и паяных соединений: справочное
издание. М. Интермет Инжиниринг. 2007. 376с.
7. А.И. Самохоцкий, М.Н. Кунявский. Лабораторные работы по металловедению и
термической обработке металлов. М. Машиностроение. 1981. 174с.
8. Б.Г. Гринберг, Т.М. Иващенко. Металловедение и термическая обработка. Руководство
к лабораторным занятиям. М. Росвузиздат. 1963.180с.
9. Р.Н. Худокормова, Ф.И. Пантелеенко. Материаловедение. Лабораторный практикум.
Минск. Выш. шк. 1988. 224с.
10. ГОСТ 24297-2013. Верификация закупленной продукции. Организация проведения и
методы контроля. М. Стандартинформ.2014. 12с.
11. ГОСТ 20847-75 Прутки, полосы и профили горячекатаные и кованые из сталей и
сплавов. Дефекты поверхности. М. Изд. Стандартов. 44с.
12. ГОСТ 21014-88. Листы и ленты стальные. Термины и определения дефектов
поверхности. М. Изд. Стандартов. 1995.
13. ГОСТ 5521-93. Прокат стальной для машиностроения. Технические условия. Минск.
Межгосударственный стандарт. 1996. 18с.
Приложение 1
Дефекты прокатанного металла
Рис. 2.10. Закаты в толстолистовом (H-120мм) прокате стали 12ХМ в нижней части верхней поверхности листа.
![]() |
![]() |
![]() |
![]() |
![]() |
![]() |
![]() |
![]() |
![]() |
![]() |
![]() |
![]() |
![]() |
![]() |
![]() |
![]() |
Тема №3
ПРАКТИКА ПРОВЕДЕНИЯ МАКРО- И МИКРОФРАКТОГРАФИЧЕСКОГО
АНАЛИЗА ПРИ ПРОВЕДЕНИИ НИР И ЭКСПЕРТИЗНЫХ ИССЛЕДОВАНИЙ
Цель работы: Научиться определять характер разрушения по изломам. Ознакомиться с методами макро- и микрофрактографического анализа, c процессом и методами подготовки изломов; научиться использовать стереомикроскоп МБС-9 для наблюдения объемного изображения излома; изучить возможность использования растрового электронного микроскопа для анализа микрофрактографических особенностей разрушения.
Оборудование и материалы: Стереомикроскоп МБС-9; видеопроектор для коллективного просмотра фрактограмм; коллекция металлических образцов с различными типами разрушения; инструментальный микроскоп для измерения характерных зон на поверхностях разрушения.
Задания: 1. Ознакомиться с методами макро- и микрофрактографического анализа. 2. Освоить методы подготовки изломов. 3. Выяснить, какую информацию можно получать, исследуя поверхности разрушения. 4. Описать характер и механизмы разрушения предложенных для анализа образцов. 5. Сделать фотографии характерных видов изломов. 6. Составить отчет по работе.
Общие сведения
В результате приложения механических нагрузок, сопровождающихся образованием и развитием трещин, а затем и полным разрушением, нагружаемые детали или образцы разделяются на две (а иногда и большее количество) части с образованием поверхностей раздела, которые называют изломами.
Исследование строения изломов называют фрактографией, а методы их исследования - фрактографическими. Особенно важно применение фрактографии в качестве способа обнаружения дефектов при изучения и установлении причин разрушения. Такие исследования получили наименование «Фрактографический анализ». Его возможности связаны с тем, что разрушение выявляет наиболее слабые места конструкции, которые определяют очаг появления трещины и траекторию ее распространения. С этой целью проводят технологические испытания на изгиб или растяжение специально вырезанных образцов натурных размеров. Наиболее часто такие испытания осуществляют при анализе свойств сварных соединений.
При фрактографическом анализе выявляют очаг разрушения и характерные виды поверхностей разрушения. К ним относятся: вязкое и хрупкое разрушение, усталостный излом, разрушение путем среза. При анализе в стереомикроскопе можно выявить межзеренное разрушение (камневидный излом), дендритное строение излома слитка или сварного шва. В очаге часто выявляются следы подплавления, скопления шлаковых включений, флокены, крупные поры и другие особенности. По виду поверхности излома можно судить о направлении развития трещины и ее остановках.
Наиболее опасным является хрупкое разрушение, которое часто определяло жизнь людей с самих истоков человеческого существования. Доисторический человек использовал хрупкое разрушение для придания формы каменным орудиям труда; он ощущал на себе его менее благотворные последствия в случае перелома конечностей. Добыча камня, придание ему формы, подгонка камней в строительных сооружениях, т. е. все существенные процессы древнего строительства, так же как и искусство ваяния, всецело зависят от умения управлять хрупким разрушением. И в наши дни многие процессы в промышленности и строительстве, например, обработка материалов, связаны на определенном этапе с хрупким разрушением.
Однако происхождение большинства аварий связано с менее благоприятными проявлениями хрупкого разрушения, главным образом с внезапным катастрофическим выходом из строя конструкций в результате неожиданного хрупкого разрушения их составных частей. История техники, начиная с середины девятнадцатого столетия и даже несколько более раннего времени, изобилует подобными примерами. Например, в течение второй половины девятнадцатого и первой четверти двадцатого столетий в США было зарегистрировано большое количество случаев разрушений, связанных с мостовыми конструкциями, нефтепроводами, газгольдерами, водопроводными магистралями, водными резервуарами, оружием малого и большого калибров, рельсовыми путями и прочим железнодорожным оборудованием, а также многими другими подобными конструкциями, находившимися под действием как активных, так и пассивных нагрузок.
В зависимости от реальных условий эксплуатации – качества материала деталей конструкций, наличия поверхностных и внутренних дефектов, характера действующих напряжений – σэкспл, вибраций, рабочих температур, - детали могут разрушаться при напряжениях,
Таблица 2.1- Характеристика прочности материалов с учетом реальных условий их эксплуатации
Материал | Характеристика предельного состояния материала | σэкспл / σв |
Углеродистые стали | Предел прочности | 1,0 |
Предел текучести | 0,5‑0,9 | |
Предел выносливости на базе 107 циклов гладких образцов | 0,3‑0,7 | |
С концентрацией напряжений | 0,2‑0,5 | |
При наличии мелких поверхностных трещин | 0,1‑0,3 | |
В условиях фреттинг-коррозии | 0,2‑0,4 | |
Жаропрочные сплавы | Предел длительной прочности на базе 10 ч | 0,3‑0,7 |
Сопротивление термической усталости на базе 104 циклов | 0,3‑0,5 |
значительно меньших, чем их предел прочности σв (табл. 2.1).
Для исследования причин эксплуатационных повреждений начал применяться уже с 50-х годов 20-го века фрактографический анализ, т.е. изучение характера излома разрушившихся конструкций, Однако, по мере накопления знаний о характере и механизмах разрушения, их связи со структурой материала, этот метод начал широко использоваться и в заводской практике крупных энергомашиностроительных и металлургических предприятий.
В настоящее время фрактографический анализ применяется, в основном, для:
- изучения закономерностей процесса разрушения, его механизмов, влияния структурных и других факторов на результаты, полученные при проведении научно-исследовательских и экспертизных исследований;
- установления причин эксплуатационных повреждений, выявления очага и характера повреждаемости;
- выявления характера и морфологии дефектов, образующихся в заготовках в процессе технологических переделов;
- оценки качества материала в соответствии с имеющейся нормативно-технической документацией.
Изломы можно классифицировать по виду и условиям нагружения, по характеру разрушения. По виду нагружения различают изломы, возникшие от однократно приложенных нагрузок (статические кратковременные или длительные, ударные) и от циклических нагрузок. Условия нагружения определяются действием температуры, при которой происходит разрушение, наличием коррозионно-активной среды наличием внутренних напряжений или запаса упругой энергии в системе, ее податливостью и др. Под характером разрушения понимают: а/ степень участия в процессе разрушения пластической деформации (хрупкое или вязкое, усталостное); б/ механизм распространения трещины (межзеренный, ямочный, скол по плоскостям спайности, расслоение, образование усталостных бороздок и пр.).
Приведенная классификация является, в значительной степени, условной, главным образом из-за неоднородности строения изломов, которая связана и с условиями нагружения и с неоднородностью структуры, изменением напряженно-деформированного состояния материала в процессе развития трещины и изменением внешних условий в процессе разрушения.
Дата добавления: 2019-01-14; просмотров: 853; Мы поможем в написании вашей работы! |
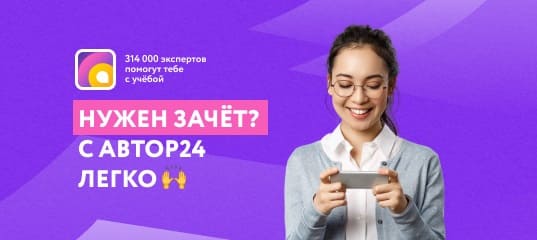
Мы поможем в написании ваших работ!