МЕТОДОЛОГИЯ ИСПЫТАНИЙ И АНАЛИЗОВ В ПРАКТИКЕ ЗаводсКИХ ИССЛЕДОВАНИЙ
Министерство образования и науки Российской Федерации
Федеральное государственное автономное образовательное учреждение
высшего профессионального образования
Национальный исследовательский ядерный университет «МИФИ»
Волгодонский инженерно-технический институт – филиал НИЯУ МИФИ
Колоколов Е.И., Подрезов Н.Н.
Практическое материаловедение
Учебные пособия
К лабораторно-практическим занятиям
По предметам материаловедческого цикла
Ч.1
Металлография, механические свойства и испытания
Для студентов изучающих курсы:
- Материаловедение.
- Материаловедение и ТКМ.
- Технологии и оборудование термической обработки металлов.
- Материалы и их поведение при сварке.
- Сварка специальных сталей и сплавов.
- Новые конструкционные материалы.
Пособие предназначено для самостоятельного повышения квалификации линейного персонала цехов и служб качества машиностроительных и энергетических предприятий, курсов повышения квалификации ИТР и преподавателей и может быть использовано обучения студентов по программе магистратуры и бакалавриата машиностроительных и энергетических специальностей ВУЗов.
Москва
2017
УДК
ББК
Рецензенты:
Колоколов Е.И., Подрезов Н.Н.
Практическое материаловедение. Учебные пособия к лабораторным работам и практическим занятиям по предметам материаловедческого цикла. Ч.1. Металлография, механические свойства и испытания/ Колоколов Е.И., Подрезов Н.Н.; Волгодонский инженерно-технический институт НИЯУ МИФИ. –
|
|
Учебные пособия содержит ряд разделов, необходимых для ознакомления студентов с теоретическим материалом и современными методами анализа и испытаний по указанной тематике. Используя настоящий практикум и другие источники, указанные в списке литературы, можно трансформировать и акцентировать перечень лабораторных работ, приведенных в содержании. Предназначено для студентов изучающих курсы: « Материаловедение», «Материаловедение и ТКМ», «Технологии и оборудование термической обработки металлов», «Материалы и их поведение при сварке», «Сварка специальных сталей и сплавов», «Новые конструкционные материалы».
Работа оформлена в соответствии с требованиями и правилами оформления текстовых документов в учебном процессе.
УДК 620.22(076.5)
© Колоколов Е.И. Подрезов Н.Н., 2017
© Волгодонский инженерно-технический
институт НИЯУ МИФИ, 2017
| |||||||||||||||||||||||||||||||||||||||||||||||||||||
ВВЕДЕНИЕ
|
|
Учебные пособия составлены в соответствии с рабочими программами предметов материаловедческого цикла: «Материаловедение», «Материаловедение и ТКМ», «Технологии и оборудование термической обработки металлов», «Материалы и их поведение при сварке», «Сварка специальных сталей и сплавов», «Новые конструкционные материалы» для студентов машиностроительных и энергетических направлений подготовки, слушателей курсов повышения квалификации ИТР, работников цехов и служб технического контроля машиностроительных и энергетических предприятий.
Целью учебных пособий является практическое изучение поведения материалов в различных условиях и анализ влияния технологических и эксплуатационных параметров на их свойства. В результате изучения теоретического материала, выполнения лабораторных и практических работ студенты приобретают компетенции, связанные с практическим применением знаний, полученных при изучении соответствующих лекционных курсов.
Предусмотрено частичное выполнение работ в производственных условиях и на базовой кафедре, созданной на ведущем энергомашиностроительном предприятии, оснащенном современным технологическим и исследовательском оборудовании.
В рамках каждой темы приведены относящиеся к ней основные теоретические сведения, устройство, принцип действия и возможности современного оборудования, применяемого для изучения и получения результатов, порядок выполнения работ, содержание отчета, контрольные вопросы для самопроверки. В конце каждого раздела приведен список стандартов, использованной или рекомендованной литературы по теме, в т.ч. методические указания к имеющимся лабораторным работам по теме.
Перед началом работы в лаборатории студент или учащийся должен самостоятельно ознакомиться с теоретическим и практическим материалом по указанной теме, используя настоящее пособие или другие источники, рекомендованные преподавателем, а также с правилами техники безопасности, которые приведены в (Приложении № 1). По окончании лабораторной работы или практического занятия студент представляет отчет по установленной форме (Приложение № 2).
В учебных пособиях к работам содержатся достаточно обширные теоретические сведения, изложенные в доступной форме с большим количеством иллюстраций и пояснений, описаний механизмов явлений, которые позволяют студенту разобраться в сущности и практической значимости получаемых знаний. Преподаватель при подготовке к занятиям в соответствии со структурой и требованиями курса, а также уровнем подготовки учащихся, может корректировать содержание работ для наиболее полного их усвоения. На основе данных методических пособий в рамках каждой темы возможно проведение различных практических занятий, разбивка лабораторных работ на независимые части, их сокращение или расширение.
Во многих случаях «пособия» не заменяют существующие руководства к лабораторным работам, а дополняет и расширяет рамки их проведения с учетом возможностей нового лабораторного оборудования, уровня достижений современных наук материаловедческой направленности и методов контроля качества. Приведенными ссылками на имеющиеся пособия к лабораторным работам, можно воспользоваться при подготовке и проведении занятий.
Сделан акцент на практическую направленность работ, многие из которых имеют конкретное применение при проведении входного контроля материалов, поступающих на машиностроительное предприятие для дальнейшего передела и выпуска продукции, а также текущего контроля состояния полуфабрикатов в процессе изготовления и при сдаче продукции ОТК, контролирующим органам и Заказчикам. В соответствующих местах сделаны ссылки и указания на стандарты, требования которых обязательны при проведении контроля.
В пособии приведено большое количество оригинальных фотографий макро- и микроструктур, характера разрушения, а также дефектов, иллюстрирующих возможные отклонения в качестве заготовок, полуфабрикатов, сварных соединений и деталей, влияющих на уровень технологичности и работоспособность продукции, выпускаемой энергомашиностроительными предприятиями.
Учебные пособия могут быть полезно руководителям и линейному персоналу энергомашиностроительных и энергетических предприятий, занимающимся изготовлением, эксплуатацией и контролем металлопродукции и желающим повысить свою квалификацию.
В Ч.1 пособий рассмотрены вопросы, касающиеся методов исследований и анализов, применяемых в материаловедении и технологии конструкционных материалов, а также способов испытаний и оценки механических свойств металлов и сплавов.
Ч.2 пособий посвящена анализу взаимосвязей между технологическими и эксплуатационными параметрами, структурой и свойствами материалов изготавливаемого или эксплуатируемого оборудования, возможными отклонениями в качестве изделий, а также методами проведения соответствующих анализов и испытаний в производственных условиях.
Тема № 1
МЕТОДОЛОГИЯ ИСПЫТАНИЙ И АНАЛИЗОВ В ПРАКТИКЕ ЗаводсКИХ ИССЛЕДОВАНИЙ
Цель работы: Ознакомление с методологией исследований и контроля, применяемых в технологических процессах изготовления и эксплуатации сложных изделий, подведомственных органам Госатомнадзора, Гостехнадзора и других соответствующих государственных органов, при аттестации новых материалов и технологий, проведении экспертизных исследований брака и неудовлетворительных свойств материалов изделий и полуфабрикатов, а также при исследовании состояния и свойств металлических материалов, применяющихся при проведении лабораторных и практических работ по предметам материаловедческого цикла.
Оборудование и материалы. Оборудование для механических испытаний: испытательная машина для растяжения Р-10, маятниковый копер для испытаний на ударную вязкость МК-30, твердомеры Роквелла и Бринелля. Оборудование для металлографических исследований: стереомикроскоп МБС-9, металлографические микроскоп МИМ-8, микротвердомер ПМТ-3, цифровой микроскоп «Микровизор металлографический», станок для приготовления микрошлифов «Нерис», вытяжной шкаф для травления микро- и макрошлифов. Оборудование для термической обработки: лабораторные термические печи, закалочные ванны, технологическая оснастка, установка для определения прокаливаемости методом торцевой закалки. Образцы: для механических испытаний и микроструктурного анализа, темплеты для анализа макроструктуры. Оборудование для вырезки и изготовления образцов: токарно-винторезный станок, фрезерный станок, плоскошлифовальный станок, точильно-шлифовальный станок.
Задания: 1. Ознакомиться с содержанием и основными требованиями «Правил устройства и безопасной эксплуатации …» сложных изделий, подведомственных органам Госатомнадзора, Гостехнадзора и других соответствующих государственных органов, приведенных в списке литературы. 2. Ознакомиться с методами исследования структуры и определения свойств материалов. 3. Ознакомиться с оборудованием для исследования материалов на кафедре «Машиностроение и прикладная механика» ВИТИ НИЯУ МИФИ, 4. Ознакомиться с современным оборудованием ЦЗЛ завода «Атоммаш» для исследования материалов и лабораторного контроля. 5. Провести поиск в «Интернете» данных по оборудованию и современным методам контроля и исследования материалов. 6. Подготовить отчет по работе.
Общие сведения
В природе атомы в чистом виде не встречаются. Как правило, присутствуют вещества в разных агрегатных состояниях: химические соединения, сплавы, жидкости или газы, в самых различных сочетаниях, к тому же загрязненные примесями. Существует огромное количество различных веществ. Выделить из них какие-то определенные типы атомов или соединений очень сложно. Вещества, которые доступны, и которым человек нашел практическое применение, могут быть учтены и использованы, называются сырьем. Способ преобразования сырья в полезный продукт называется технологией обработки сырья. Этот продукт, получаемый из сырья с использованием разработанной для этого технологии, называется материалом. Для получения идентичных материалов из разного сырья технологию приходится менять или модифицировать. Изменение технологии обработки одного и того же сырья меняет свойства получаемого материала. Все эти факторы необходимо учитывать для получения материалов с требуемыми свойствами.
Для получения из материала готового изделия применяют другие технологии, называемые технологиями обработки материалов. Для получения изделий используют полуфабрикаты или заготовки из требуемых материалов. При их обработке возникают свои сложности. Зачастую, одинаковые технологии нельзя или трудно применять для разных материалов, обладающих различными свойствами. В зависимости от функционального назначения и условий работы изделий применяют различные материалы и разные технологические операции. Оказывается, что разница свойств определяется изменениями в химическом составе и структуре данного материала – их внутреннем строении. Знание соответствующих закономерностей позволяет осуществить выбор материалов и применить нужные для получения требуемых свойств технологии. Изучению и применению этих закономерностей посвящена специальная наука, называемая материаловедением. Можно сформулировать:
Материаловедение – это наука, которая показывает, что свойства материалов определяются их внутренним строением, а изменение технологических и эксплуатационных факторов при изготовлении изделий и конструкций приводит к изменению внутреннего строения и свойств применяемых материалов. Внутреннее строение материалов определяется их химическим составом, макро-, микро- и мезоструктурой, а также атомно-кристаллическим строением.
- Химический состав – это количество химических элементов в данном материале, определенное с помощью строго определенных процедур и методик в соответствии с утвержденными стандартами.
- Макроструктура – это внешний вид поверхностей полуфабрикатов, деталей или элементов конструкций, поверхностей разрушения (изломов) и макрошлифов, изучаемых визуально или при небольших увеличениях в стереомикроскопе с целью выявления особенностей строения, наличия дефектов, химической неоднородности.
- Микроструктура – внутреннее строение материалов полуфабрикатов, деталей и элементов конструкций, изучаемое на специально приготовленных микрошлифах в оптических и растровых электронных микроскопах при увеличениях от 20 до 2000 раз. При этом анализируют особенности распределения структурных элементов, фазовое состояние, особенности строения дефектов. Растровые электронные микроскопы для изучения микроструктуры, а также изломов, получили широкое распространение только в последние годы.
- Мезоструктура – это те особенности строения материалов, которые необходимо изучать при увеличениях от 5000 до 100000 раз в электронных микроскопах. При этом изучаются более тонкие детали строения микрошлифов или изломов (чем при анализе микроструктуры), особенности деформации и строения фаз, осуществляется локальный химический анализ в микрообъемах.
- Атомно-кристаллическое строение (в последнее время часто применяют термин – наноструктура) характеризует характер пространственного распределения атомов в микрообъемах, сопоставимых с их размерами (10-8 см). До настоящего времени методы прямого наблюдения атомов не разработаны. Для этих целей используют косвенные методики физических и физико-химических методов исследования: рентгеноструктурный и рентгеноспектральный анализ, Оже-спектроскопия, эффект Мессбауэра, ионная спектроскопия, метод электросопротивления и др. Изучаются искажения кристаллических решеток материалов, дефекты кристаллического строения, характер взаимодействия с примесными атомами и т.д.
Изучение макро- и микроструктурных параметров материалов не является самоцелью. Как следует из определения понятия «материаловедение», основное назначение этих исследований – установление связи структурных превращений с изменениями свойств материалов изделий при изменении технологических и эксплуатационных параметров. Без таких исследований установить причины изменений свойств, зачастую важнейших, невозможно. Только структурные исследования позволяют целенаправленно изменять и улучшать технологические и эксплуатационные свойства изделий.
Различают три основные группы свойств материалов: технологические, эксплуатационные, стоимость.
К технологическим относятся свойства материалов, определяющие возможность осуществления различных видов технологических операций, а также трудности, возникающие при их реализации. К технологическим свойствам относятся: литейные свойства, штампуемость, свариваемость, закаливаемость, обрабатываемость резанием и т.д. Эти свойства оцениваются при появлении дефектов, изменении механических и теплофизических свойств и других факторов, влияющих на сложность осуществления технологических операций.
Эксплуатационные свойства характеризуют возможность использования материалов в качестве конструкционных или для специального применения в заданных условиях. К ним относятся: механические свойства, определяемые в различных условиях действия механических нагрузок – упругость, твердость, прочность, пластичность, износостойкость, хрупкость, жаропрочность и др., физические свойства – модуль упругости, плотность, электропроводность, теплоемкость, магнетизм, радиационная стойкость и др., химические свойства – коррозионная стойкость, жаростойкость, возможность потери устойчивости материалов при взаимодействии с жидкими легкоплавкими металлами и др.
Стоимость материалов – характеризует себестоимость сырья и его обработки, возможность и целесообразность применения различных технологий получения материалов путем нормирования технологических операций и пр.
Существуют и другие принципы классификации свойств. Например, механическое поведение материалов характеризуют способностью сопротивляться развитию трещин, сложностью напряженно-деформированного состояния, особенностями режимов нагружения, типами образцов, температурой испытания, агрессивностью среды и другими параметрами. Для характеристики физических или магнитных свойств используют свои параметры и т.д.
Материаловедение изучает закономерности формирования структуры материалов при:
‑ затвердевании или плавлении (выплавка сталей и сплавов, литье, сварка, модифицирование поверхности);
‑ пластической деформации (механические испытания, обработка давлением);
‑ термической, термомеханической и химико-термической обработке;
- эксплуатации (воздействие низких и высоких температур, химически-активных сред, облучения и др.).
Материаловедение показывает взаимосвязь между технологическими параметрами изготовления и обработки материалов, комплексом их физико-механических свойств, определяемые их внутренним строением; обосновывает обеспечение прочности, надежности и долговечности деталей при рациональном выборе материалов с учетом условий эксплуатации.
Применение современных методов контроля и исследований материалов на энергомашиностроительных предприятиях
Материаловедение начинает применяться сразу при поступлении на завод металлопродукции – проката, поковок, литья - при осуществлении входного контроля. Устанавливается соответствие поступивших материалов требованиям нормативной документации; по химическому составу, механическим и коррозионным свойствам, наличию недопустимых дефектов. Последнее проверяется путем осуществления контроля макроструктуры, которое будет подробно рассмотрено в лабораторной работе №2. Контроль осуществляется визуально или с применением специального оборудования: стереомикроскопов (Рис.1.1), видеоэндоскопов (Рис.1.2) и др. Обнаруженные дефекты характеризуются по внешним признакам и сравниваются с эталонными. Химический состав можно оценивать непосредственно на поверхности
![]() |
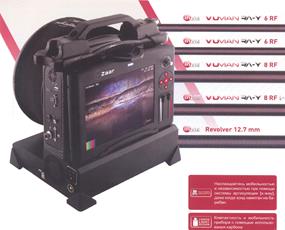
![]() |


![]() |
точный оптико-эмиссионый спектрометр «Foundry-Master LAB». Возможности определения химического состава сталей с помощью этого прибора приведена в табл.1.1. Важно отметить высокую точность определения содержания вредных примесных элементов: P, S, As, Sn, и др. Для контроля содержания легких элементов, таких как H, O, N и др., используют другие приборы, Наиболее качественные результаты обеспечивают приборы фирмы «Leco».
![]() |
Для анализа микроструктуры, в основном, используют оптические микроскопы. Современные приборы оснащены встроенной системой управления и компьютерной обработки результатов, что позволяет, например, осуществлять цифровую обработку и количественный анализ структуры материалов. На рис. 1.5 приведен комплекс для количественного анализа микроструктуры на базе оптического микроскопа «Carl Zeiss».
Значительно расширяют возможности микроструктурного анализа растровые электронные микроскопы. Принцип действия таких приборов основан на сканировании анализируемой поверхности остро сфокусированным электронным лучом в вакууме. При этом в облученном участке возбуждается вторично-электронная эмиссия, которая фиксируется регистрирующей аппаратурой (Рис.1.6). Компьютерная обработка сигнала, регистрируемого датчиком вторичной электронной эмиссии позволяет получить качественное изображение поверхности анализируемого объекта.
В последнее время произошло резкое развитие аппаратуры микрозондового анализа с высокими показателями локальности и разрешающей способности, Для этих целей используют различные типы РЭМ, снабженные дополнительным оборудованием: рентгеновскими спектрометрами для микрорентгеноспектрального анализа (МРСА), с программами качественного и количественного элементного анализа, датчиками отраженных электронов, Оже- электронов и других видов вторичного излучения. Локальность метода зависит от размера сферической области, в которой возбуждается излучение (голубое пятно на рис.1.6).
![]() |
Высокая точность при определении распределения компонентов в сталях достигается при использовании метода МРСА, который основан на анализе рентгеновского характеристического излучения, возникающего при облучении исследуемого объекта узким (до 1 мкм) пучком электронов (зондом). По длине волны и интенсивности рентгеновского излучения определяют, какие элементы и в каком количестве присутствуют в выбранном зондом микрообъеме (Рис.1.6). Для выбора исследуемого участка на образце применяют встроенный световой микроскоп. С помощью МРСА определяются все элементы от бора (порядковый номер Z ‑ 5) до урана (Z ‑ 92). В настоящее время они выпускаются, как правило, в виде приставок к РЭМ (Рис.1.7); при этом оба прибора удачно дополняют друг друга. Например, имеется возмож-
ность выяснения причины охрупчивания с учетом химической неоднородности (сегрегации атомов в зоне начала разрушения ‑ очаге), что позволяет достоверно выяснить причину возникновения разрушения. Так, на рис. 1.8 показано хрупкое разрушение многопроходного сварного соединения низколегированной стали в центральной части излома образца при испытаниях на ударный изгиб, наблюдаемое в стереомикроскопе. Фрактографический анализ (исследование поверхности излома) в РЭМ участка под надрезом уже при небольшом увеличении выявил дендритный характер хрупкого разрушения (Рис. 1.9). При большем увеличении видно (Рис.1.10), что наряду с междендритным, присутствует хрупкое разрушение тела дендритов по плоскостям спайности. Такие детали изображения при малом увеличении неразличимы. Дополнительное исследование методом МРСА может при этом выявить химсостав включений, образовавшихся на границах дендритов.
Одним из наиболее важных и распространенных методов изучения строения металлов и сплавов является рентгеноструктурный анализ. В основе этого метода лежит рассеяние рентгеновских лучей (обычно используют рентгеновские лучи с длиной волны порядка размера атома) электронами твердого тела. Для этих целей используют рентгеновские дифрактометры. Анализ дифракционной картины (Рис.1.11б) позволяет определить атомно-кристаллическую структуру вещества. Разработаны специальные методы прикладного рентгеноструктурного анализа, которые предоставляют возможность исследовать различные нарушения кристаллического строения, устанавливать напряжения в металлах, проводить качественный и количественный фазовый анализ сплавов, исследовать характер колебания атомов (динамику решетки).
Для анализа механических свойств сталей и сплавов проводят механические испытания по стандартным методикам на специализированном оборудовании. При этом определяют характеристики прочности, упругости, пластичности, ударную вязкость, твердость, циклическую прочность и др. На рис. 1.12 показан современный автоматический твердомер VH 3100 фирмы «Wilson», позволяющий осуществлять измерения макро- и микротвердости с высокой точностью и локальностью.
Испытания на растяжение при различных нагрузках и режимах нагружения при повышенных и пониженных температурах осуществляют на универсальных разрывных машинах. На рис.1.13 показано современные разрывные машины фирмы «Zwick» с электронных силоизмерением, компьютерным управлением и обработкой результатов, которые позволяют получать характеристики прочности и пластичности при испытаниях на растяжение и сжатие.
Для испытаний на ударную вязкость при различных температурах и определения критических температур хрупкости используют маятниковые копры. На рис. 1.14 показан маятниковый копер фирмы «Zwick» с энергией маятника 450 Дж. Копер оснащен криостатом и позволяет осуществлять испытания в автоматическом режиме.
![]() |
Для оценки технологических и эксплуатационных свойств материалов используют специализированное оборудование и стенды. Например, при термической обработке, сварке, обработке давлением, важнейшими параметрами являются скорость нагрева и охлаждения, температурно-временной интервал превращений и другие параметры. Для анализа таких процессов проводят термический анализ. Одним из его методов является дилатометрия. На рис. 1.15 показан дилатометр DIL805, позволяющий автоматически определять изменение размеров об разцов в условиях контролируемого нагрева и охлаждения. На рис. 1.16 показан один из примеров использования дилатометрического анализа: построенные с его помощью термокинетические диаграммы - графики изменения температур превращений в сталях во времени.
В ряде случаев для оценки технологических или эксплуатационных свойств материалов проводят натурные испытания полномасштабных образцов или изделий. Иногда внутри работающего оборудования помещают специальные образцы-свидетели, которые после эксплуатационной выдержки подвергают стандартным испытаниям для оценки влияния условия работы на свойства материалов. Для оценки свариваемости в различных условиях проводят сварку специально сконструированных проб с последующим исследованием образующихся дефектов и макроструктуры материалов.
Для анализа износостойкости сталей и сплавов, обрабатываемости резанием, способности к горячей деформации, коррозионной стойкости, оценки литейных свойств и т.д. проводят другие специальные испытания.
Порядок анализа свойств ответственных деталей и сварных металлоконструкций изделий, при поломке которых или выходе их из строя в процессе эксплуатации могут произойти аварии с человеческими жертвами, значительным ущербом экологии и объектам жизнедеятельности, регламентирован нормами и правилами соответствующих ведомств и надзорных органов. Регламентируются объекты, на которые распространяются «правила», требования к конструкции, применяемым материалам и технологиям, монтажу, правилам контроля, эксплуатации и ремонта и т.д. Регламентирован порядок расследования причин появления дефектов и аварий в процессе изготовления и эксплуатации. Так, в атомной энергетике действуют «Правила устройства и безопасной эксплуатации оборудования и трубопроводов атомных энергетических установок (НП-089-15)» и другие нормы. На тепловых электростанциях и других объектах, эксплуатирующих установки с водой и паром высоких параметров, действуют «Правила устройства и безопасной эксплуатации трубопроводов пара и горячей воды (ПБ 10-573-03)». На объектах, где эксплуатируются сосуды под высоким давлением, руководствуются «Правилами устройства и безопасной эксплуатации сосудов, работающих под давлением (ПБ 03-576-03)». Для морских судов и буровых платформ, в шахтах, объектах нефте- и газодобычи и т д., действуют свои нормативные документы, нарушение которых влечет для ответственных работников и руководителей наказания вплоть до судебных.
В последние годы проводится активная работа по адаптации действующих в России стандартов и правил к нормам, действующим в Евросоюзе (Правила ISO», переход на работу по этим правилам.
Дата добавления: 2019-01-14; просмотров: 312; Мы поможем в написании вашей работы! |
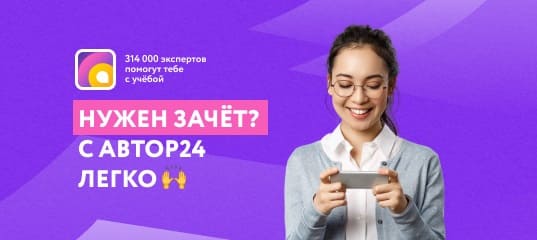
Мы поможем в написании ваших работ!