Сезонное техническое обслуживание (СТО).
1) Вымыть автомобиль, обратив особое внимание на агрегаты и системы, обслуживание которых проводится. 2) Двигатель. а) Проверить: герметичность крана включателя гидромуфты; состояние резиновой подушки; регулировку положения поддерживающей опоры силового агрегата. б) Устранить неисправности. в) Закрепить: радиатор; насосный агрегат: котел, патрубки и впускную трубу предпускового подогревателя; фланцы приемных труб глушителя. г) Снять форсунки и отрегулировать давление подъема иглы на стенде. При необходимости отрегулировать угол опережения впрыска топлива. 3) Коробка передач. Закрепить: рычаги тяг дистанционного привода управления коробкой передач; фланец вторичного вала коробки передач. 4) Карданная передача. Проверить свободный ход в шлицевых соединениях, устранить неисправность. 5) Ведущие мосты. а) Проверить: работу механизма блокировки мостов; состояние подшипников ступиц (при снятых ступицах мостов и передней оси). б) Устранить неисправности. в) Закрепить: редукторы среднего и заднего мостов; гайки фланцев валов ведущих шестерен среднего и заднего мостов.6) Тормоза. Проверить состояние тормозных барабанов, колодок, накладок, стяжных пружин и разжимных кулаков, устранить неисправности. 7) Ходовая часть, подвеска, рама. а) Проверить: состояние рамы; свободный ход в шарнирах реактивных штанг. б) Устранить неисправности. в) Закрепить: кронштейны балансирной подвески к раме; пальцы и верхние кронштейны реактивных штанг. 8) Электрооборудование. а) Проверить: состояние аккумуляторных батарей по напряжению элементов под нагрузкой, при необходимости снять батареи для подзаряда или ремонта; напряжение в цепи электропитания при средней частоте вращения коленчатого вала двигателя, устранить неисправность. б) Разобрать выключатель "массы" аккумуляторных батарей, прочистить и смазать. 9) Кабина, платформа. Проверить состояние лакокрасочных покрытий, при необходимости подкрасить
|
|
2. Рама. Является основным несущим элементом грузового автомобиля. На нее устанавливают и закрепляют двигатель, агрегаты шасси, кабину и кузов автомобиля. Рама воспринимает нагрузки от массы автомобиля, а также нагрузки, возникающие при движении.
По конструкции рамы могут быть лонжеронными и хребтовыми. Лонжеронные рамы состоят из двух продольных балок (лонжеронов), соединенных поперечинами. Хребтовые рамы состоят из одной продольной балки с поперечинами.
На грузовых автомобилях наиболее распространены лонжеронные рамы. На легковых автомобилях роль рамы выполняет кузов, каркас которого представляет собой жесткую сварную конструкцию, усиленную наружными облицовочными панелями.
|
|
Передний неведущий мост. Передний неведущий мост грузовых автомобилей служит для установки передних управляемых колес. Он передает от колес через подвеску на раму автомобиля продольные и боковые силы, возникающие от контакта автомобиля с дорогой.
Основу переднего моста составляет двутавровая балка. Средняя часть балки выгнута вниз, что позволяет расположить ниже двигатель на раме. Верхняя полка моста имеет опорные площадки для крепления рессор подвески.
На легковых заднеприводных автомобилях с независимой подвеской передних колес передний мост образуется короткой балкой или поперечиной, закрепленной к кузову автомобиля. Она служит одновременно и для крепления двигателя.
Балка заднего ведущего моста. На автомобилях с колесной формулой 4x2 она передает через подвеску на раму или кузов автомобиля толкающие усилия от ведущих колес в режиме тяги и тормозные усилия при торможении.
В зависимости от конструкции балка ведущего моста может быть разъемной или неразъемной. Внутри балки размещаются механизмы ведущего моста, а по концам на подшипниках устанавливают ступицы ведущих колес. Балка моста имеет спереди фланец для крепления картера главной передачи и дифференциала, а сзади крышку. В верхней части на балку приварены две опорные площадки для крепления рессор.
|
|
Подвеска автомобиля осуществляет упругую связь рамы или кузова с мостами и колесами, смягчает воспринимаемые ими удары и толчки при езде по неровностям дороги. Упругие свойства подвески достигаются применением упругого элемента. Работа подвески основана на превращении энергии удара при наезде колеса на неровность дороги в перемещение упругого элемента подвески, в результате чего сила удара, передаваемого на кузов, уменьшается, и плавность хода автомобиля становится лучше. По характеру взаимодействия колес и кузова при движении автомобиля все подвески делят на зависимые и независимые. Зависимая подвеска имеет жесткую связь между левым и правым колесом, в результате чего перемещение одного из них в поперечной плоскости передается другому и вызывает наклон кузова. Независимая подвеска характеризуется отсутствием жесткой связи между колесами одного моста. Каждое колесо подвешено к кузову независимо от другого колеса. В результате при наезде одним колесом на неровности дороги колебания его не передаются другому колесу, уменьшается наклон кузова и повышается в целом устойчивость автомобиля при движении.
|
|
Амортизаторы. При движении автомобиля по неровностям дороги возникают колебания кузова, которые продолжаются некоторый промежуток времени после наезда колес на препятствие. Для гашения возникающих колебаний на автомобилях в конструкции подвески применяют амортизаторы преимущественно жидкостные телескопического типа.
Работа амортизатора основана на сопротивлении перетеканию специальной жидкости, находящейся во внутренних полостях амортизатора и перетекающей из одной полости в другую при изменении их объемов. Телескопические амортизаторы имеют двустороннее действие, т.е. гасят колебания подвески при ходе сжатия и при ходе отдачи.
Колеса автомобиля обеспечивают непосредственную связь с дорогой, участвуют в создании и изменении направления его движения, передают нагрузки от массы автомобиля на дорогу.
3. Наиболее часто встречающаяся неисправность ведущего моста - появление шума при различных режимах его работы. Для определения причин возникновения шума можно провести следующие испытания.
Испытание I. Чтобы точно определить характер шума, развивают на автомобиле скорость приблизительно 20 км/ч. Затем постепенно увеличивают ее до 90 км/ч, прислушиваясь к различным видам шума и отмечая скорость, при которой он появляется и исчезает. Отпускают педаль управления дросселем и без притормаживания снижают скорость двигателем. Во время замедления следят за изменением шума, а также за моментом, когда шум усиливается. Обычно шум возникает и исчезает при одних и тех же скоростях как при ускорении, так и при замедлении.
Испытание 2. Разгоняют автомобиль до 100 км/ч, ставят рычаг переключения передач в нейтральное положение, выключают зажигание и дают автомобилю возможность свободно катиться до остановки. При этом следят за характером шума на различных скоростях замедления. При выключении зажигания следует быть внимательным и аккуратным. Нельзя поворачивать ключ больше, чем нужно для выключения зажигания, так как при дальнейшем повороте ключа в положение «Стоянка» может сработать противоугонное устройство. Шум, замеченный во время этого испытания и соответствующий замеченному при первом испытании, исходит не от шестерен главной передачи, поскольку они без нагрузки не могут вызывать шум. Напротив, шум, отмеченный при втором испытании, может исходить от шестерен редуктора или подшипников ведущей шестерни либо дифференциала.
Испытание 3. При неподвижном и заторможенном автомобиле включают двигатель и, увеличивая постепенно частоту вращения его коленчатого вала, сравнивают возникающие шумы с замеченными в предыдущих испытаниях. Шумы, похожие на шумы, возникающие при первом испытании, указывают на то, что они исходят не от редуктора, а вызваны другими узлами.
Испытание 4. Шумы, обнаруженные при первом испытании и не повторяющиеся при последующих, исходят от редуктора. Для подтверждения этого поднимают задние колеса, пускают двигатель и включают IV передачу. При этом можно убедиться, что шумы действительно исходят от редуктора, а не от других узлов, например подвески или кузова.
Более точные данные можно получить при испытании ведущего моста с применением соответствующего оборудования. Наиболее простым способом является проверка редуктора с помощью стетоскопа, представляющего собой металлический стержень с чашкой. Испытываемый автомобиль вывешивают на подъемнике, включают одну из передач и стетоскопом определяют конкретные места шума. При отсутствии стетоскопа можно использовать деревянный брусок.
С помощью люфтомера проверяют зазоры в главной передаче. Для этого люфтомер крепят к задней крестовине карданного вала и поворачивают в обе стороны с целью полного выбора люфта. Задние колеса при этом должны быть заблокированы стояночным или рабочим тормозом.
Проверку ведущего моста можно производить и с помощью стенда для определения тягово-экономических качеств автомобиля. Стенд представляет собой беговые барабаны, на которых и имитируется движение автомобиля («автомобиль стоит, дорога бежит»). На стенде определяют потери на прокручивание моста, «выбег» автомобиля после его разгона до полной остановки, локализуют шумы. Полученные данные сравнивают с нормативными и делают заключение о техническом состоянии моста.
Билет №21
1. К основым неисправностям трансмиссии относятся:
Неисправности сцепления проявляются в пробуксовывании, неполном выключении и резком включении.
1.Сцепление пробуксовывает, когда отсутствует или мал свободный ход педали, замаслились или износились фрикционные накладки ведомого диска, ослабли или поломались нажимные пружины.
2.Сцепление «ведет» (не полностью выключается) при большом свободном ходе педали, попадании воздуха в систему гидравлического привода, перекосе или короблении дисков, отрыве фрикционных накладок. Резкое включение сцепления происходит при заедании муфты выключения.
Основные неисправности коробки передач и раздаточной коробки:
·произвольный выход шестерен из зацепления,
·затрудненное включение передач,
·шум шестерен.
Самопроизвольное выключение передач происходит при большом износе зубьев шестерен, шариков-фиксаторов и выемок в ползунах, износе деталей синхронизаторов, ослаблении и поломке пружин фиксаторов. Шум шестерен возникает при недостатке масла, износе зубьев шестерен и подшипников, перекосе валов.
К основным неисправностям карданной передач и относятся вибрации и рывки, вызываемые износом шлицевых соединений, карданов и подшипников промежуточной опоры, ослаблением креплений карданных валов. Биение карданного вала возникает при его погнутости.
Неисправности главной передачи, дифференциала и полуосей проявляются шумом в заднем мосту, поломкой полуосей, износом сальников.
Для устранения неисправностей механизмов трансмиссии выполняют моечно-очистные, крепежные, смазочные и регулировочные работы, в случае необходимости заменяют изношенные детали новыми.
Для своевременного обнаружения неисправностей и предупреждения отказов агрегатов трансмиссии применяются различные методы диагностирования: метрический, акустический, виброакустический, термический и др.
К метрическому методу диагностирования технического состояния агрегатов трансмиссии можно отнести способы контроля по параметрам, количественные значения которых измеряются сравнительно несложными приборами — люфтомером или индикатором
Сущность акустического метода заключается в том, что работа любого агрегата трансмиссии сопровождается ударными нагрузками деталей, соединенных в кинематические пары: шестерен, подшипников, шлицевых соединений и др. Звуковые волны, вызванные ударами сопряженных деталей друг 8 о друга, являются сигналами, несущими информацию к диагностической аппаратуре. Приемником этих волн является диагностический датчик, который крепится в наиболее удобном месте на картере агрегата.
Виброакустический метод диагностирования состоит в следующем. В подвижных сопряжениях агрегата трансмиссии энергия, передаваемая от одной детали к другой, и амплитуда вибраций пропорциональны величинам зазора или надлома, количеству трещин и осколков в деталях данной пары.
В основе термического метода диагностирования состояния агрегатов трансмиссии автомобиля лежит измерение температурных полей. Сравнивая полученное при измерении температуры выбранного на агрегате поля с эталонным, можно дать заключение о техническом состоянии диагностируемого агрегата. Главным недостатком акустического, виброакустического и термического методов диагностирования является высокая стоимость оборудования, поэтому они не нашли широкого практического применения
2. Составные части подвески: упругие элементы, направляющие, амортизаторы.
Упругие элементы воспринимают и гасят динамические нагрузки со стороны дороги. Различают рессорные (листовые, витые пружинные, торсионные), пневматические (резинокордные баллоны, диафрагменные, комбинированные), гидропневматические и резиновые (работают на кручение и сжатие).
Направляющее устройство воспринимает продольные и боковые силы и моменты. Схема направляющего устройства определяет зависимую и независимую подвески.
Форма набора листов рессор соответствует эпюре изгибающих моментов, т.е. рессора представляет собой балку равного сопротивления.
Листовая рессора состоит из коренного листа, который соединен с рамой, и притянутых к нему хомутами остальных листов. Рессору крепят к мосту стремянками с накладками, один конец коренного листа крепят к кузову шарнирно, а другой через серьгу. Применяют также крепление рессор на резиновых подушках. Такое крепление не требует смазки и снижает скручивание рессоры при перекосе рамы.
Листовые рессоры просты в изготовлении и ремонте. В них нет рычажных направляющих приспособлений в отличии от пружинных и торсионных.
Спиральные рессоры (пружины) применяют на легковых автомобилях при независимой подвеске колес.
Торсионы представляют собой вал или пучок валов, скручивающийся во время воздействия дороги на подвеску. Их применяют при независимой подвеске колес многоосных автомобилей, в прицепах и малолитражных автомобилях.
Упругие пневматические элементы наиболее часто применяют на автомобилях с меняющейся подрессореной массой (автобусах, контейнеровозах, трейлерах). Характеристика пневматической подвески нелинейная, параметры которой можно менять за счет изменения давления воздуха. Меняя давление воздуха, можно регулировать положение кузова относительно дороги, а при независимой подвеске – дорожный просвет.
Гидропневматические элементы телескопического типа передают давление газовой подушке через жидкость, эти устройства компактнее пневматических, т.к. работают при давлении до 20 МПа.
При независимой подвеске каждое колесо может совершать колебания независимо от других. Такую подвеску часто применяют при разрезном мосте в легковых автомобилях и автомобилях повышенной проходимости.
Рычажно-телескопическая подвеска «качающая свеча» обеспечивает незначительное изменение колеи и развала колес, имеет малую массу, большое расстояние между опорами правого и левого колес, большой ход по высоте.
Зависимая подвеска передает через мост колебания одного колеса другому. Оба колеса жестко соединены с балкой моста. При изменении положения одного из колес по высоте меняется угол. В этом случае при вращении колеса возникает гироскопический эффект, стремящийся вернуть ось в предыдущее положение, что приводит к износу шин и осей. Эту подвеску применяют для двух- и многосоосных грузовых автомобилей и прицепов. Зависимые балансирные подвески подрессоривают два близкорасположенных моста.
Балансирные подвески применяют на многосоосных автомобилях.
Стабилизаторы. При повороте автомобиля под действием центробежной силы кузов накреняется, положение центра масс изменяется, что может привести к опрокидыванию. Для компенсации этого явления подвеска должна иметь угловую жесткость в поперечном направлении, что достигается установкой стабилизаторов. Часто стабилизатор представляет собой торсион, который при наклоне кузова закручивается. На легковых автомобилях стабилизатор устанавливают на переднем мосту и редко ‑ на заднем. Иногда функцию стабилизатора на задней подвеске выполняет U-образная задняя балка (ВАЗ).
Амортизаторы поглощают энергию колебаний рессор, кузова и колес за счет дросселирования жидкости через комбинированные отверстия в специальных шайбах. В независимых подвесках амортизатор часто используют как направляющий элемент. Различают гидравлические, газонаполненные и комбинированные амортизаторы. По конструктивному исполнению бывают рычажные и телескопические.
3. Для регулировки зазора в подшипниках червяка поворачивают рулевое колесо на 1…1,5 оборота влево, отвертывают болты крепления нижней крышкии сливают масло из картера рулевого механизма. Сняв крышку, удаляют регулировочную прокладкуили заменяют ее более тонкой. После этого, закрепив нижнюю крышку, снова проверяют, нет ли осевого перемещения червяка в подшипниках. При отсутствии перемещения заливают в картер масло и проверяют усилие поворота рулевого колеса (установив передние колеса на гладкой плите), которое не должно превышать 20 кгс.
В случае обнаружения повышенного люфта в рулевом механизме и после проверки и устранения люфтов в деталях рулевого привода регулируют зацепления ролика с червяком. Для этого ослабляют контргайку регулировочного винта и, приподняв шайбу, завертывают регулировочный винт до установления зазора. Слишком затягивать регулировочный винт не рекомендуется. Затем, придерживая регулировочный винт отверткой, затягивают контргайку. Убедившись в том, что рулевой механизм имеет допустимый люфт, проверяют усилие поворота рулевого колеса. Если оно превышает 20 кгс, ослабляют регулировочный винт.
ДЕТАЛИ РУЛЕВОГО МЕХАНИЗМА ЧЕРВЯЧНОГО ТИПА
Проверяют наличие на рабочих поверхностях ролика и червяка видимых следов износа, заедания, вмятин или рисок; регулируют зазор между втулками и валом сошки, который не должен превышать 0,10 мм; легкость вращения ролика вала сошки и подшипников червяка; осевой зазор между головкой регулировочного винтаи пазом вала сошки; зазор не должен превышать 0,05 мм; если он больше, заменяют регулировочную пластину 1 пластиной большей толщины.
При сборке запрессовывают наружное кольцо верхнего подшипника червяка. После установки червяка в картер рулевого механизма и закрепления нижней крышки проверяют с помощью динамометра и головки момент трения вала червяка, который должен находиться в пределах 2...5 кгс-см; если момент трения окажется меньше указанного, уменьшают толщину регулировочных прокладок, а если больше - увеличивают.
Установив вал сошки, убеждаются в отсутствии зазора в зацеплении ролика с червяком в положениях вала червяка, повернутого вправо и влево на 30° от нейтрального положения сошки, возможный зазор устанавливают регулировочным винтом и затягивают контргайку.
После регулировки зазора в зацеплении ролика и червяка снова проверяют динамометром момент трения вала червяка, который должен быть равен 7...9 кгс см при повороте вала червяка на 30° как влево, так и вправо от среднего положения и плавно снижаться до 5 кгс-см при повороте от угла 30° до упора.
По окончании сборки проверяют углы поворота сошки от нейтрального положения, которые должны составлять 32°10'±1° как влево, так и вправо до упора сошки в головки болтов.
ДЕТАЛИ РУЛЕВОГО МЕХАНИЗМА РЕЕЧНОГО ТИПА
Внимательно осматривают, нет ли на рабочих поверхностях шестерни и рейки следов износа, задиров или рисок. Незначительные повреждения устраняют мелкозернистой шлифовальной шкуркой или бархатным напильником. Изношенные и поврежденные детали заменяют.
Шариковый подшипник должен вращаться свободно, без заеданий. На поверхности колец и шариков не должно быть следов износа и заеданий. Иглы и обойма роликового подшипника не должны иметь износа и повреждений. При малейшем сомнении подшипники заменяют.
При сборке реечных рулевых механизмов необходимо соблюдать определенное расстояние от конца рейки до центра шестерни для установки шестерни в положение прямолинейного движения.
После установки гайкии упора рейкинеобходимо отрегулировать момент вращения шестерни. Для этого рейку устанавливают в положение прямолинейного движения. Затягивают гайку (регулировочный винт) упора рейки моментом около 1 кгс-м (в зависимости от конструкции), затем ослабляют и снова затягивают моментом, меньшим первоначального на 10 %, чтобы обеспечить зазор 0,10 мм между гайкой (винтом) и упором рейки для компенсации теплового расширения деталей и неточности их изготовления. Момент проворачивания шестерни определяют с помощью динамометра. Он должен находиться в пределах 5...20 кгс-м. Если момент проворачивания не укладывается в указанные пределы, проводят дополнительную регулировку. В случае невозможности достижения требуемого результата регулировкой меняют пружину упора рейки или весь механизм. После регулировки контрят винт или закернивают гайку в двух противоположных точках.
Билет №22
1. - Люфт рулевого колеса (руль может люфтить в любую сторону).
- Выработка элементов рулевой системы, в результате чего они выходят из строя.
- Заедание руля, либо слишком затрудненный его ход.
- Неисправность ГУР или ЭУР.
Описанные проблемы препятствуют комфортному управлению транспортным средством и создают реальную угрозу безопасности движения. В связи с этим, их необходимо устранять в срочном порядке. Люфт руля является одной и наиболее распространенных неисправностей системы. Зачастую его вызывают: износ червячной передачи, втулок, маятникового рычага или его кронштейна, плохое крепление картера. Установить причину люфта можно как при визуальном осмотре рулевого управления, так и при движении. Также в определении местоположения причины люфта руля поможет его скрип при вращении.
Суммарный люфт в рулевом управлении в регламентированных условиях испытаний не должен превышать предельных значений, установленных изготовителем в эксплуатационной документации, а при отсутствии таких данных не должен превышать:
·10° для легковых автомобилей и созданных на их базе агрегатов грузовых автомобилей и автобусов
·20° для автобусов
·25° для грузовых автомобилей
Начало поворота управляемого колеса — это угол поворота управляемого колеса на (0,06 ± 0,01)°, измеряемый от положения прямолинейного движения.
При проверке суммарного люфта должны выдерживаться следующие предварительные условия:
·шины управляемых колес должны быть чистыми и сухими
·управляемые колеса должны находиться в нейтральном положении на сухой ровной горизонтальной асфальто- или цементо- бетонной поверхности
·испытания автомобилей, оборудованных усилителем рулевого привода, проводятся при работающем двигателе
Натяжение ремня привода насоса усилителя рулевого управления и уровень рабочей жидкости в бачке должны соответствовать требованиям, установленным изготовителем транспортного средства в эксплуатационной документации.
Осевое перемещение и качание плоскости рулевого колеса, качание рулевой колонки определяются путем приложения к рулевому колесу знакопеременных сил в направлении оси рулевого вала и в плоскости рулевого колеса перпендикулярно к колонке, а также знакопеременных моментов сил в двух взаимно перпендикулярных плоскостях, проходящих через ось рулевой колонки.
Взаимные перемещения деталей рулевого привода, крепление картера рулевого механизма и рычагов поворотных цапф определяются поворачиванием рулевого колеса относительно нейтрального положения на 40…60° в каждую сторону, а также приложением непосредственно к деталям рулевого привода знакопеременной силы.
2. Датчик измерения кислорода в отработавших газах (λ - зонд) предназначен для точного определения коэффициента избытка воздуха в цилиндре. Датчик дает эффект только при установке на двигатель нейтрализатора. Применяют в основном датчики, у которых чувствительным элементом является двуокись циркония, покрытая с двух сторон пленкой платины. Двуокись циркония представляет собой твердый электролит. К одной стороне этого чувствительного элемента подводится чистый воздух, а к другой – отработавшие газы. Элемент реагирует на разность парциальных давлений кислорода в воздухе и отработавших газов. В зависимости от этой разности он вырабатывает ЭДС разной величины, посылая сигнал в микропроцессор.
Датчик устанавливают на выпускном коллекторе. С этой целью на корпусе датчика выполнена резьба. Внутри защитного колпака с прорезями помещен активный колпак с платиновыми контактами из спеченного с керамикой диоксида циркония. Внутри керамического патрона есть канал для подвода к элементу чистого воздуха. Отработавшие газы подводятся к элементу через прорези колпака. Через контакт и разъем сигнал от датчика поступает в микропроцессор.
Датчик расхода воздуха.
Применяют следующие расходомеры: механический с напорным диском; термоанемометрический; пневмодинамический.
Расходомер с напорным диском расположен во впускном коллекторе. Его напорный диск закреплен на рычаге. Рычаг имеет ось и балансир. Вся эта система хорошо сбалансирована, рычаг на оси установлен на шариковом подшипнике, поэтому система реагирует на малейшее изменение скорости воздуха. При увеличении скорости воздуха напорный диск поднимается и поворачивает рычаг. Он перемещает золотник дозатора-распределителя, который изменяет подачу топлива. Форма камеры, где помещен диск, обеспечивает линейную зависимость перемещения рычага от скорости и, следовательно, от расхода воздуха. С помощью винта на рычаге регулируют цикловую подачу.
Термоанемометрический датчик основан на изменении сопротивления нагретой проволоки при охлаждении ее проходящим воздухом. В корпусе датчика размещены формирователь потока воздуха с сетками, платиновая нить и электронный модуль. Платиновая нить нагревается электрическим током. При прохождении по датчику воздуха температура нити уменьшается: чем больше скорость воздуха, тем ниже температура нити. Для температурной компенсации имеется еще одна такая же нить вне датчика в неподвижном воздухе. Электронный модуль определяет силу тока через нить, сравнивает с сопротивлением внешней нити и дает сигнал в процессор о расходе воздуха.
Пневмодинамический датчик основан на измерении перепада давления до и после дроссельной заслонки. Проходное сечение зависит от угла поворота дроссельной заслонки. Компьютер системы питания, получая сигналы датчиков давления и угла поворота дроссельной заслонки, вычисляет расход топлива и коэффициент избытка воздуха. Угол поворота дроссельной заслонки измеряется специальным реохордным датчиком. Для учета влияния температуры на плотность воздуха применяют датчик внешней температуры.
Датчик положения коленчатого вала, состоит из магнита и катушки и расположен около зубчатого венца маховика. Датчик передает блоку информацию об угле поворота коленчатого вала (положение поршня). На основании информации выходного сигнала этого датчика блок вычисляет частоту вращения двигателя и положение коленчатого вала.
Датчик положения коленчатого вала является электромагнитным датчиком, по которому в системе впрыска топлива производится синхронизация работы топливных форсунок и системы зажигания. В этой связи ДПКВ является основным, без которого работа системы впрыска топлива невозможна.
Датчик детонации предназначен для преобразования механических вибраций двигателя в электрический синусоидальный сигнал, амплитуда которого пропорциональна мощности вибраций. Информация датчика позволяет блоку управления откорректировать угол опережения зажигания до устранения детонационных стуков в двигателе.
Датчик представляет пьзоэлектрический акселерометр, который под действием механических вибраций вырабатывает ЭДС переменного тока.
Конструктивно датчик состоит из следующих элементов: металлический корпус датчика цилиндрической формы, в котором размещен чувствительный элемент в виде пьезоэлектрической пластины; двухконтактная вилка электрического соединителя, объединенная с корпусом.
Сигнальные провода от датчика должны быть экранированы для обеспечения защиты от электрических помех системы зажигания.
3. При замене тормозных колодок отгибают угол стопорной шайбы с грани нижнего болта, отвертывают его, придерживая ключом за грани направляющий палец. Затем поворачивают суппорт в сборе с цилиндром относительно другого пальца, вынимают тормозную колодку со стороны поршня и опускают суппорт в рабочее положение. Осторожно, чтобы не повредить пылезащитный колпачок и не допустить выплескивания тормозной жидкости из бачка главного цилиндра, перемещают через окно 1 поршень как можно дальше внутрь цилиндра, отталкиваясь отверткой от поверхности тормозного диска. Подняв суппорт, заменяют изношенную наружную колодку новой и опускают суппорт в рабочее положение. Еще раз перемещают поршень внутри цилиндра и, подняв суппорт, заменяют внутреннюю тормозную колодку. Опустив суппорт, завертывают и контрят болт, резьба которого имеет покрытие, предотвращающее самоотворачивание направляющего пальца.
Если в процессе эксплуатации автомобиля в бачок доливалась тормозная жидкость, то перед утапливанием поршня удаляют часть тормозной жидкости из бачка, чтобы не допустить ее выливания из горловины бачка.
При замене колодок проверяют состояние и посадку в гнездах защитных колпачков поршней и чехлов направляющих пальцев. При необходимости заменяют их или обеспечивают правильную посадку в гнездах. После замены колодок проверяют состояние и крепление штуцера, колпачкаи шланга.
Билет №23
1. Шиноремонтный участок предназначен для демонтажа и монтажа колес и шин, замены покрышек, ТР камер и дисков колес, а также балансировки колес в сборе. При этом мойку и сушку колес перед их демонтажем при необходимости выполняют здесь же или в зоне УМР, где имеется шланговая моечная установка. Технологический процесс на шиномонтажном участке выполняют в порядке Приёмка шин → Определение неисправностей → Операции по восстановлению, устранению неисправностей и балансировка → Проверка и контроль качества → Выдача с ремонта.
Подобно технологическому процессу ремонта покрышек технологический процесс ремонта камер состоит из подготовки поврежденных участков для наложения заплат, наложения заплат и вулканизации.
Отремонтированные камеры должны отвечать следующим требованиям:
1) камера, наполненная воздухом, должна быть герметична как по телу камеры, так и в месте крепления вентиля;
2) заплаты должны быть плотно привулканизованы, не иметь пузырей и пористости, их твердость должна быть одинаковой с резиной камеры;
3) края заплат и фланцев не должны иметь утолщений и отслоений;
4) резьба вентиля должна быть исправной.
185/80R15 — 185 -ширина профиля шины в миллиметрах; 15 — посадочный диаметр шины (наружный диаметр обода) в дюймах; 80 серия шины (отношение высоты профиля к его ширине в процентах); R – ширина радиальной конструкции.
Статический дисбаланс - это неравномерное распределение масс по оси вращения, При этом колесо бьет в вертикальной плоскости. При вращении колеса неуравновешенная масса создает свою центробежную силу F, которая при вращении колеса создаёт переменный по направлению вращающий момент на оси, что ведет к разбиванию подвески. Такой дисбаланс устраняется приложением силы Fу равной силе F по величине, но противоположной по направлению. Это достигается прикреплением дополнительного грузика в точке противоположной точке нахождения неуравновешенной массы. Это и называется статической балансировкой.
Динамический дисбаланс появляется из-за неравномерного распределение масс в плоскостях колеса. При динамическом дисбалансе на колесо действует пара противоположно направленных сил F , действующих на определенном плече относительно плоскости вращения колеса. Динамическая балансировка проводится на специальных балансировочных стендах. В основном при балансировке колеса мы сталкиваемся с комбинированным дисбалансом ("комбинация" статического и динамического дисбалансов).
2. Форсунка предназначена для дробления топлива до мелкодисперсного состояния и подачи его в камеру сгорания.
К форсунке предъявляют следующие требования: высокая степень дробления топлива на капли, т.к. чем меньше диаметр капель, тем больше их общая поверхность, быстрее нагрев и сгорание, но меньше длина факела топлива; обеспечение длины факела до краев камеры сгорании, поэтому капли не должны быть очень мелкими – средний их размер 30-50 мкм; распределение топлива по всему объему камеры сгорания; резкое начало впрыскивания и резкое прекращение процесса.
Различают форсунки открытые и закрытые. Открытые форсунки обеспечивают постоянную подачу топлива. В дизелях применяют закрытые форсунки, которые открываются только в момент подачи топлива в камеру сгорания. Закрытые форсунки применяют двух типов: одно- и многодырчатые.
Многодырчатые устанавливают на двигателях с нераздельными камерами сгорания. Основная часть форсунки – распылитель. Он состоит из корпуса и иглы. Распылитель притянут к корпусу форсунки накидной гайкой. Сверху на иглу давит пружина. Топливо в полость форсунки подаётся по каналу. Когда нет поддачи топлива насосом, давление в полости составляет 2-4 МПа. Оно давит на нагрузочный поясок иглы, но его сила меньше чем силы пружины, которая прижимает иглу к распылителю, игла распорным конусом перекрывает сопла.
При подаче топлива насосом сила давления топлива на поясок становится больше силы пружины, игла поднимается и через сопло с большой скоростью топливо впрыскивается в камеру сгорания. После окончания подачи давление падает, пружина возвращает иглу на место. Игла перекрывает сопло, впрыск прекращается.
Однодырчатые устанавливают на двигателях с вихревыми камерами сгорания. Распылитель этих форсунок имеет одно сопло. Конец иглы выполнен в виде штифта конусной формы, выступающего за пределы корпуса распылителя. Штифт служит для формирования факела топлива в виде конуса.
3. Перед удалением воздуха из тормозной системы убеждаются в герметичности всех узлов привода тормозов и их соединений, очищают крышку и поверхность вокруг крышки бачка, заполняют бачок жидкостью «Томь» или «Роса» до метки «МАХ». Затем тщательно очищают штуцера и снимают с них защитные колпачки. Не рекомендуется применять для заполнения бачка жидкость, слитую из системы, так как она насыщена воздухом, содержит много влаги и, возможно, загрязнена. Воздух из системы удаляют сначала из одного контура, затем из другого, начиная с колесных цилиндров задних тормозов.
Надевают на головку штуцера резиновый шланг для слива жидкости, а его свободный конец опускают в прозрачный сосуд, частично заполненный жидкостью. Резко нажав на педаль тормоза 3...5 раз с интервалами 2...3 с, отвертывают на 0,50...0,75 оборота штуцер при нажатой педали. Продолжая нажимать на педаль, вытесняют находящуюся в системе жидкость вместе с воздухом через шланг в сосуд. После того как педаль тормоза достигнет переднего крайнего положения и истечение жидкости через шланг прекратится, завертывают штуцер выпуска воздуха до отказа. Повторяют эти операции до тех пор, пока не прекратится выход пузырьков из шланга. Удерживая педаль в нажатом положении, завертывают штуцер до отказа и снимают шланг. Протирают штуцер насухо и надевают защитный колпачок. Затем повторяют операции на других колесах: сначала на втором колесе этого же контура, а затем последовательно на обоих колесах другого контура. При удалении воздуха следят за наличием жидкости в бачке, не допуская обнажения его дна, так как при этом в бачок попадает воздух. При отсутствии воздуха в приводе тормозов педаль тормоза проходит примерно 0,5 своего хода. Чтобы исключить влияние вакуумного усилителя на прокачку тормозов, воздух удаляют при нет работающем двигателе.
Если в гидравлическом приводе отсутствует тормозная жидкость, систему заполняют следующим образом: заливают в бачок тормозную жидкость; отвертывают на 1,5...2 оборота штуцера на цилиндрах всех колес; резко нажимая на педаль тормоза и плавно отпуская ее, завертывают штуцера по мере вытекания из них жидкости. Затем прокачивают тормозную систему. При удалении воздуха на автомобиле, тормозная система которого проработала длительный срок, находящуюся в системе жидкость заменяют новой.
Замена тормозной жидкости. Для того чтобы в систему гидравлического привода не попадал воздух и на замену тормозной жидкости затрачивалось минимальное время, придерживаются следующих правил:
·действуют в том же порядке, как и при прокачке тормозов, но используют шланг со стеклянной трубкой на конце, которую опускают в сосуд с тормозной жидкостью;
·нажимая на педаль тормоза, выкачивают старую тормозную жидкость до тех пор, пока в трубке не покажется новая тормозная жидкость; после этого выполняют два полных хода педалью тормоза и, удерживая ее в нажатом положении, завертывают штуцер; при прокачке следят за уровнем жидкости в бачке и своевременно доливают жидкость до максимального уровня; повторяют эту же операцию на каждом рабочем цилиндре в том же порядке, что и при прокачке;
наполняют бачок до максимального уровня и проверяют работу тормозов на ходу автомобиля.
Билет №24
1. Метод специализированных бригад предусматривает формирование производственных подразделений по признаку их технологической специализации по видам технических воздействий.
Специализация бригад по видам воздействий (ЕО, ТО-1, ТО-2, диагностирование, ТР, ремонт агрегатов) способствует повышению производительности труда рабочих за счет применения прогрессивных технологических процессов и механизации, повышения навыков и специализации исполнителей на выполнение закрепленной за ними ограниченной номенклатуры технологических операций.
При таком методе организации работ обеспечивается технологическая однородность каждого участка, (зоны) создаются предпосылки к эффективному оперативному управлению производством, за счет маневра людьми, запчастями, технологическим оборудованием и инструментом, упрощается учет и контроль над выполнением тех или иных видов технического воздействия.
Однако отрицательной стороной данного метода является недостаточ-ная персональная ответственность исполнителей за выполненные работы.
Метод комплексных бригад предусматривает формирование производственных подразделений по признаку их предметной специализа-ции, т.е. закрепления за бригадой определенной группы автомобилей (например, автомобилей одной колонны, автомобилей одной модели, прицепов и полуприцепов) по которым бригада проводит работы ТО-1, ТО-2 и ТР. Централизованно же выполняются ЕО, диагностирование и ремонт агрегатов.[1]
Комплексные бригады укомплектовываются исполнителями различных специальностей (автослесарями, слесарями-регулировщиками, электриками, смазчиками), необходимыми для выполнения закрепленных за бригадой работ.
Каждая бригада, как правило, имеет закрепленные за ней рабочие места, посты для ТО и ремонта, свое технологическое оборудование и инструменты, запас оборотных агрегатов и запасных частей, что приводит к распылению материальных средств АТП, усложняет руководство производством ТО и ремонта автомобилей. При этом методе сохраняется обезличка ответственности за качество работ по ТО и ремонту.
Более того, между бригадами могут возникать трения из-за очередности проведения работ ЕО, диагностирования, использования общего оборудования (кран-балки, подъемника, специализированного инструмента). Могут возникать ситуации, когда рабочие одной бригады перегружены, а другой недогружены, но бригады не заинтересованы во взаимопомощи. Важным положительным качеством этого метода является бригадная ответственность за качество проводимых работ по ТО и ремонту.
Сущность агрегатно-участкового метода заключается в том, что все работы по ТО и ремонту подвижного состава АТП распределяются между производственными участками, ответственными за выполнение всех работ ТО и ремонта одного или нескольких агрегатов (узлов, механизмов и систем) по всем автомобилям АТП.
Моральная и материальная ответственность за качество ТО и ремон-та закрепленных за участком агрегатов, узлов и систем становится конкрет-ной. Работы, закрепленные за основными производственными участками, выполняются входящими в состав их бригад исполнителями как на постах ТО и ремонта, так и в соответствующих цехах и участках. Недостатком этого метода является децентрализация производства, затрудняющая оперативное управление им.
Кроме того, возможны трения между отдельными участками из-за очередности выполнения работ, что приводит к скоплению рабочих на одних автомобилях и излишнего простоя других автомобилей, требующих обслуживания и ремонта.
2. Бесконтактные системы зажигания — это электронные системы второго поколения. В них отсутствуют недостатки классической и контактно-транзисторной систем. Прерыватель заменен бесконтактным датчиком (чаще магнитоэлектрическим), который вырабатывает импульсы в строго определенные моменты времени.
Током базы транзистора управляет датчик VD углового положения коленчатого вала. В системе применяют магнитоэлектрические датчики и датчики Холла.
Магнитоэлектрический датчик представляет собой катушку с сердечником. При прохождении мимо сердечника полюса магнита (диск с зубцами) в катушке возникает ЭДС, которая подается на базу транзистора.
Датчик Холла представляет собой полупроводниковую пленку (ПП), вдоль которой в одной плоскости проходит ток. При прохождении магнитного поля поперек плоскости пленки на ее краях возникает ЭДС, которая через усилитель подается на базу транзистора. Магнитное поле создается постоянным магнитом, от которого датчик экранирован вращающимся диском с прорезями. Эффект Холла возникает при прохождении прорези диска мимо датчика.
Датчик Холла состоит из постоянного магнита, полупроводниковой пластины и интегральной микросхемы. Между полупроводниковой пластиной и магнитом вращается стальной экран количеством прорезей, соответствующим числу цилиндров. Когда прорезь экрана проходит между магнитом и пластиной, в ней возникает эффект Холла. ЭДС усиливается, ее сигнал формируется микросхемой в самом датчике, а затем сигнал поступает в коммутатор. Напряжение питания подается от коммутатора через одну из клемм колодки штекерного разъема. С другой клеммы разъемы выводится сигнал, а третья клемма соединена с «массой». Экран закреплен на втулке центробежного регулятора, благодаря чему может слегка поворачиваться и изменять угол опережения зажигания в зависимости от частоты вращения.
3. Неисправности электрической схемы устраняют в два этапа. Сначала ищут неисправный участок схемы, а затем восстанавливают его. Наиболее сложный первый этап. Умение выявить место неисправности в наиболее короткий срок и с наименьшими затратами труда имеет очень важное значение, так как позволяет значительно сократить простои автомобиля. Восстановление поврежденного участка обычно сводится к замене неисправного элемента (контакта, провода, катушки, предохранителя, реле) или соединению оборванной электропроводки.
Неисправности электрических схем можно разделить на четыре группы: обрыв электрической цепи; короткое замыкание в цепи; замыкание на корпус (пробой изоляции); возникновение обходной цепи при замыкании между собой проводов. Все эти неисправности могут иметь различные внешние проявления в зависимости от особенностей электрической схемы крана. Поэтому при устранении неисправности следует тщательно проанализировать работу схемы во всех режимах, выявить отклонения в работе отдельных механизмов автомобиля и только после этого приступить к поиску повреждений в той части схемы, которая может вызвать эти отклонения.
Нельзя дать методику, пригодную для поисков любого случая неисправности, поскольку даже одинаковые схемы привода для разных механизмов автомобиля имеют свои особенности.
Защита электрических цепей автомобиля от короткого замыкания обеспечивается применением совокупности предохранителей, прерывателей цепей и плавких вставок. Сгоревший предохранитель легко отличить от исправного путем осмотра его прозрачного пластмассового корпуса. Необходимо внимательно осмотреть предохранитель для выявления его перегорания. Если предохранитель внешне выглядит нормально, но подозрения на его неисправность сохранились, произведите проверку проводимости между ножевыми клеммами, выступающими из его корпуса. Следите за тем, чтобы маркировка на корпусе предохранителя соответствовала силе тока, на которую рассчитана соответствующая цепь. Если замененный предохранитель немедленно перегорает, не разумно будет продолжать его замену. Прежде всего, следует выявить и устраните причину его перегорания. В большинстве случаев таковой оказывается короткое замыкание в электрической цепи, вызванное обрывом или повреждением изоляции провода.
Плавкие вставки похожи на предохранители в том смысле, что выход их из строя (оплавление) легко определяется визуально.
Для замены плавкой вставки отсоедините отрицательный провод от аккумуляторной батареи. Извлеките сгоревшую вставку и установите на ее место новую. Перед заменой вставки обязательно постар Тепловые реле служат для защиты таких компонентов, как электроприводы стеклоподъемников, замков дверей и регулировки положения фар (электрокорректоры). Некоторые из прерывателей цепей установлены в монтажном блоке. Возврат тепловых реле в исходное состояние на некоторых моделях осуществляется автоматически, т.е. при возникновении перегрузки в цепи тепловое реле мгновенно размыкается, затем, после остывания, возвращается в исходное состояние. Если возврата контура в рабочее положение не происходит, следует немедленно произвести его проверку. Нормальное функционирование теплового реле подтверждает исправность контура. Некоторые из прерывателей оборудованы кнопками для ручного принудительного возврата в исходное состояние.
Для определения обрыва проводов в электрической цепи необходимо подать напряжение на проверяемую цепь и при помощи контрольной лампы найти место обрыва. Для этого один провод от лампы присоединить на "массу" автомобиля, а концом другого провода касаться поочередно зажимов, клемм или жилы провода, начиная от аккумуляторной батареи. Место, где лампочка погаснет, укажет, что цепь имеет обрыв на участке от неработающего прибора до данной точки присоединения.
Обрыв провода можно определить и так. Отсоединить концы проверяемого провода от зажимов крепления и присоединить его концы последовательно с лампой к источнику тока. При наличии обрыва лампа не будет гореть.
Стартер и генератор можно проверить на замыкание на массу или перегорание прозвонкой.
Для определения замыкания провода на "массу" автомобиля необходимо отсоединить концы проверяемого провода от зажимов крепления и присоединить один его конец последовательно с лампой к плюсовому выводу аккумуляторной батареи. При наличии замыкания на "массу" лампа будет гореть.
Для подачи электрического тока к некоторым элементам электрооборудования автомобиля используются реле. Нарушение исправности функционирования реле приводит к отказу обслуживаемого им элемента. В случае возникновения подозрения на неисправность какого-либо из реле, оно должно быть снято и подвергнуто проверке на станции технического обслуживания или в специализированной автомастерской. Замена вышедшего из строя реле производится в сборе.
![]() | |||||||||||||||||||||||||||||||||||||||||||||
![]() | ![]() | ![]() | ![]() | ![]() | ![]() | ![]() | ![]() | ![]() | ![]() | ![]() | ![]() | ![]() | ![]() | ![]() | ![]() | ![]() | ![]() | ![]() | ![]() | ![]() | ![]() | ||||||||||||||||||||||||
Дата добавления: 2018-11-24; просмотров: 209; Мы поможем в написании вашей работы! |
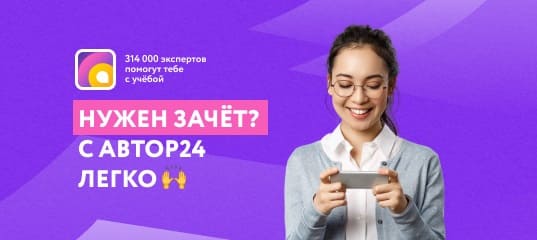
Мы поможем в написании ваших работ!