Техническое обслуживание ТО-2.
Билет №1 1. Неисправностями тормозного механизма являются: ·износ накладок тормозных колодок и барабанов и увеличение зазора между ними ·замасливание, заклинивание колодок, сопровождающееся нагревом тормозных барабанов Неисправности механического привода ручного (стояночного) тормоза заключаются в вытягивании и повреждении тяг или тросов их заеданий. В гидравлическом тормозном приводе имеют место следующие неисправности: ·подтекание жидкости через манжеты колесных тормозных цилиндров и через шланги ·недостаточный уровень тормозной жидкости в резервуаре главного тормозного цилиндра ·увеличенный свободный ход педали тормоза ·притормаживание колес на ходу Согласно действующим стандартам применяют два основных метода диагностирования тормозных систем — дорожный и стендовый. Для них установлены следующие контролируемые параметры: ·при проведении дорожных испытаний — тормозной путь; установившееся замедление; устойчивость при торможении; время срабатывания тормозной системы; уклон дороги, на котором должно неподвижно удерживаться транспортное средство ·при проведении стендовых испытаний — общая удельная тормозная сила; коэффициент неравномерности (относительная неравномерность) тормозных сил колес оси, а для автопоезда еще дополнительно коэффициент совместимости звеньев автопоезда и асинхронность времени срабатывания тормозного привода Существует несколько видов стендов и приборов, использующих различные методы и способы измерения тормозных качеств: ·статические силовые ·инерционные платформенные ·инерционные роликовые ·силовые роликовые стенды ·приборы для измерения замедления автомобиля при дорожных испытаниях Силовые роликовые стенды с использованием сил сцепления колеса с роликом позволяют измерять тормозные силы в процессе его вращения со скоростью 2.10 км/ч. Вращение колес осуществляется роликами стенда от электродвигателя. Тормозные силы определяют по реактивному моменту, возникающему на статоре мотор-редуктра стенда при торможении колес. Роликовые тормозные стенды позволяют получать достаточно точные результаты проверки тормозных систем. Есть еще одно важное условие — безопасность испытаний. Самые безопасные испытания — на силовых роликовых тормозных стендах, поскольку кинетическая энергия испытуемого автомобиля на стенде равна нулю. В случае отказа тормозной системы при дорожных испытаниях или на площадочных тормозных стендах вероятность аварийной ситуации очень высока. Следует отметить, что по совокупности своих свойств именно силовые роликовые стенды являются наиболее оптимальным решением как для диагностических линий станций техобслуживания, так и для диагностических станций, проводящих гостехосмотр. 2. Раздаточные коробки применяют на многоприводных автомобилях для передачи вращающего момента на передний мост с целью повысить проходимость и тягово-сцепные качества автомобилей. В этом случае все колеса находятся в контакте с опорной поверхностью, и вес автомобиля полностью используется в качестве сцепного. Раздаточную коробку или располагают непосредственно за коробкой передач, или крепят к раме автомобиля и соединяют с коробкой передач карданным валом. В конструкциях ряда раздаточных коробок за счет дополнительных передач расширяют диапазон передаточных чисел, чем увеличивают диапазон тяговых усилий и скоростей движения. Различают следующие раздаточные коробки: по типу привода ведущих мостов ‑ с постоянным или дифференциальным приводом; числу ступеней ‑ одно- и двухступенчатые; расположению выходных валов ‑ с соосными или несоосными валами. Если передние и задние оси постоянно включены или заблокированы, то при движении машины на повороте, когда колеса идут по дугам разного радиуса, или при возможной разнице диаметров колес может возникнуть кинематическое рассогласование. Это создает циркуляцию так называемой паразитной мощности. При кинематическом несоответствии передние колеса могут проскальзывать относительно дороги и на них действует отрицательная касательная сила (горизонтальная реакция дороги, направленная против движения машины). Эта сила образует на передних колесах вращающий момент, который передается через передний мост, карданный вал, раздаточную коробку и задний карданный вал на задние колеса, где складывается с вращающим моментом, поступающим от двигателя. 3. Визуальная проверка на отсутствие трещин. Блок проверяют на герметичность. Плоскость разъема блока цилиндров с головкой проверяется с помощью линейки и набора щупов; при этом допускается неплоскостность до 0,1 мм. Если превышает допустимую, поверхность обрабатывают на плоскошлифовальном станке, снимая слой материала, не превышающий 0,2 мм. При проверке цилиндров визуально проверяют состояние их зеркала. Наличие на зеркале выбоин и глубоких царапин не допускается. Степень износа цилиндра определяется изменением его геометрических параметров: овальностью, конусностью, бочкообразностью, а также общим износом. Для определения размеров элементов цилиндропоршневой группы измеряют диаметр цилиндра нутромером, перемещая его с небольшими качаниями и диаметр поршня микрометром. Измерение диаметра цилиндра производится на четырех поясах, первый из которых находится на расстоянии 5 мм от плоскости разъема блока цилиндров, а остальные три определяются индивидуально для каждого двигателя: средний пояс - на середине хода поршня, верхний и нижний - в пределах хода его верхнего и нижнего краев. Конусность и бочкообразность определяются по разности значений, полученных при измерениях диаметра цилиндра в трех рабочих поясах. Конусность не должна превышать 0,1 мм. Овальность цилиндра определяется по разности его диаметра в двух взаимно перпендикулярных измерениях на одном и том же поясе. В зависимости от модели двигателя она не должна превышать 0,04...0,07 мм. Зазор между поршнем и цилиндром измеряется для каждого цилиндра отдельно. Этот зазор определяется как разность между внутренним диаметром цилиндра и диаметром юбки поршня, измеренным на определенном расстоянии от днища поршня или от его нижнего края. Максимальный износ цилиндров - 0,08...0,25 мм (в зависимости от требований фирмы-изготовителя). Если измеренный зазор входит в допустимые пределы, цилиндры можно не растачивать; достаточно установить новые поршневые кольца. При зазоре, превышающем максимальное допустимое значение, необходима расточка цилиндров (гильз). Окончательный диаметр цилиндра под расточку определяется путем прибавления к измеренному диаметру монтажного зазора (0,03 мм) между поршнем и цилиндром. Кроме того, учитывают припуск 0,02...0,03 мм на хонингование. После хонингования выдерживается такой диаметр, чтобы при установке выбранного ремонтного поршня расчетный зазор (не путать с предельным!) между цилиндром и поршнем не превышал допустимого (0,025...0,070 мм). Если зазор между поршнем и цилиндром превышает допустимый, цилиндры растачивают под ближайший ремонтный размер. Билет №2 1. Характерными неисправностями системы зажигания являются: разрушение изоляции проводов высокого напряжения и свечей зажигания, нарушение контакта в местах соединений; ослабление пружины подвижного контакта; повышенный люфт валика распределителя; нагар на электродах свечей зажигания; изменение зазора между электродами свечей; межвитковые замыкания (особенно в первичной обмотке) катушки зажигания; неправильная начальная установка угла опережения зажигания; неисправность центробежного и вакуумного регуляторов. Для диагностирования системы зажигания используют стационарные неавтоматизированные и компьютеризированные мотор-тестеры с электронно-лучевой трубкой, а также переносные электронные автотестеры, достоинством которых является низкая стоимость, приспособленность для условий небольших АТП и СТО в сочетании с широкими функциональными возможностями. В ряде моделей отечественных автомобилей предусмотрен специализированный разъем для подключения мотор-тестеров. В последнее время все большее применение находят упрощенные цифровые приборы для проверки зазора в контактах прерывателя в комбинации с тахометром и вольтметром с двумя диапазонами измеряемого напряжения: до 20 В и до 0.5-1,0 В (последний используется для измерения напряжения на замкнутых контактах). Более сложные приборы, выполненные на основе микропроцессоров последних разработок, позволяют измерять величину напряжения пробоя и длительность искрового заряда. Правильнее проверку угла опережения зажигания проводить на работающем двигателе при помощи стробоскопического устройства. Принцип его работы заключается в том, что если в строго определенные моменты времени относительно угла поворота вращающейся детали освещать ее коротким импульсом света (примерно 0,0002 с), то деталь будет казаться неподвижной. Таким образом, проверяют соответствие измеряемых углов опережения их нормативным значениям на малой, средней и большой частотах вращения коленчатого вала двигателя (с учетом работы вакуумного регулятора). По результатам проверки производят регулировку или замену прерывателя. 2. Назначение КП – изменение скорости движения, обеспечение движения задним ходом, длительное отключение трансмиссии от двигателя. Чтобы обеспечить наиболее эффективную работу двигателя в определенном диапазоне частот коленчатого вала и получить необходимый ведущий момент на колесах при изменении нагрузки, в трансмиссию вводят КП с изменяемыми передаточными числами. Делитель передач обеспечивает плавное выравнивание окружных скоростей и безударное включение высшей и низшей передач Делитель состоит из картера, отлитого заодно с картером сцепления, первичного вала с шестерней, синхронизатором и подшипниками, промежуточного вала с шестерней и подшипником и механизма переключения передач 3. Автотранспортные предприятия предназначены для перевозки грузов или пассажиров, а также выполнения работ по ТО, ТР, хранению и материально-техническому обеспечению подвижного состава. По хар-ру перевозок и типу ПС делятся на пассажирские, грузовые, смешанные и специальные. По ведомственной принадлежности и характеру производственно-хоз-ной деятельности м.б.: общего пользования (республиканских ведомств автотранспорта государственных концернов), ведомственные. По организации производственной деятельности: 1. комплексные АТП – самостоятельные предприятия, кот осуществляют транспортную работу, хранение и все виды ТО и ТР ПС. 2. кооперированные АТП – предприятия, входящие в состав производственного АТ объединения (ПАТО), деятельность которых осуществляется с учетом централизации транспортной работы, а также полной или частичной централизации работ по ТО, ТР ПС. ПАТО организуются путем объединения в городе нескольких предприятий аналогичного назначения. Обычно состоят из базового (наиболее технически оснащенного) предприятия и подчиненных предприятий – филиалов. На головном АТП выполняются наиболее трудоемкие и сложные работы ТО и ТР. А в филиалах осуществляется хранение, ЕО, ТО-1 и мелкий ТР. Достоинства таких предприятий: приближение к потребителям (сокращение нулевых пробегов), эффективное использование ПТБ и повышение качества ТО и ТР. Производственно-техническая база – это совокупность зданий, сооружений, оборудования, оснастки и инструмента, предназначенного для ТО и ТР, хранения ПС, а так же для создания необходимых условий работы персонала. Основная задача АТП – обеспечение требуемого уровня тех готовности ПС для выполнения перевозок при наименьших трудовых и материальных затратах. Основные характеристики ПС, влияющие на ПТБ: тип ПС и конструкция (может различаться по уровню надежности, сложности и габаритов), пробег с начала эксплуатации. Формы развития ПТБ: 1. Организационно-технические мероприятия – это отдельные мероприятия, направленные на устранение узких мест, замену устаревшего оборудования на нескольких участках, внедрение мероприятий по научной организации труда (НОТ). 2. Техническое перевооружение – это осуществление комплекса мер по повышению тех уровня всех или большинства производственных звеньев, действующих на АТП за счет внедрения новой техники и прогрессивной технологии. Проводится без расширения произв площадей. 3. Реконструкция действующего предприятия – это проведение по единому проекту полного или частичного переустройства предприятия, вкл строительство новых цехов в замен ликвидируемых, возведение новых и расширение существующих вспомогательных объектов. 4. Расширение действующего предприятия – это строительство по новым проектам филиала предприятия, дополнительного производственного комплекса, цехов и объектов на территории действующего предприятия или примыкающих к нему площадей с целью наращивания производственной мощности. 5. Новым строительство считается возведение предприятия на новой площади по установленному в определенном порядке проекту с целью создания новой производственной мощности, которая после ввода в эксплуатацию будет состоять на собственном балансе. Преимущества реконструкции, расширения и технического перевооружения: 1. Более экономное расходование материалов, финансовых, трудовых и других ресурсов на единицу вводимой или наращиваемой производственной мощности. 2. Значительное сокращение сроков освоения капитальных вложений, что дает возможность избежать долгого незавершенного строительства и морального старения, заложенного в проект решения. 3. Инженерно-строительные работы проводятся на освоенной площадке. Нет необходимости производить крупные работы по планировке земельного участка и обустройства территории. 4. Наличие трудового коллектива, действующего АТП как средство контроля за качеством и сроками выполнения работ. Недостатки данных форм развития АТП: 1. Невозможность использования типовых проектов в целом. 2. Необходимость вписать новые планировочные и технологические решения в габариты существующей территории и объемы использующихся производственных зданий. 3. Невозможность использовать высокопроизводительные технологии в строительстве. 4. Необходимость привязки к существующим строительным конструкциям, осуществление переоборудования постов и т.д. ППАТ» Билет №3 1. В газовом редукторе на слух или с помощью прибора определяют герметичность клапана второй ступени и сливают масляный конденсат. Ежедневный слив конденсата необходим, так как скопление его на мембране второй ступени редуктора нарушает нормальную работу двигателя. Герметичность системы проверяют в рабочем состоянии, т. е. при заполнении ее сжиженным газом. Места утечек определяют с помощью мыльного (пенного) раствора или прибором. В зимнее время при заполнении системы охлаждения водой ее сливают из полости испарителя. Первое техническое обслуживание газовой системы питания включает в себя контрольно-диагностические и крепежные работы, которые выполняют при ЕО, а также смазочно-очистительные работы, к которым относятся очистка фильтрующих элементов газовых фильтров и смазка резьбовых штоков магистрального наполнительного и расходных вентилей. После выполнения отмеченных выше работ при ТО-1 проверяют герметичность газовой системы при давлении 1,6 МПа воздухом или инертным газом и работу двигателя на газовом топливе. В этом случае замеряют, а при необходимости и регулируют содержание окиси углерода в отработавших газах, определяют надежность пуска двигателя и устойчивость его работы на холостом ходу при различной частоте вращения коленчатого вала. При втором техническом обслуживании проверяют состояние и крепление газового баллона к кронштейнам, кронштейнов к лонжеронам рамы, карбюратора к впускному патрубку и впускного патрубка к смесителю. В объем контрольно-диагностических и регулировочных работ входят проверка и установка угла опережения зажигания при работе двигателя на газе, проверка и регулировка газового редуктора, смесителя газа и испарителя. В редукторе проверяют регулировку первой и второй ступеней, работу дозирующе-экономайзерного устройства и герметичность разгрузочного устройства. В смесителе проверяют состояние и действие приборов воздушной и дроссельной заслонок, в испарителе – герметичность и засоренность газовой и водяной полостей. Сезонное обслуживание газового оборудования по периодичности разделяется на три вида. К первому относятся работы, которые подлежат выполнению один раз в 6 месяцев, ко второму – работы, проводимые один раз в год, к третьему – работы, выполняемые один раз в два года. Один раз в 6 месяцев проверяют срабатывание предохранительного клапана газового баллона, продувают газопроводы сжатым воздухом и проверяют работу ограничителя максимальной частоты вращения коленчатого вала двигателя. К работам, проводимым один раз в год, относится ревизия газовой аппаратуры, магистрального вентиля, манометра и арматуры баллона. Для этого газовый редуктор, смеситель газа, испаритель, магистральный вентиль демонтируют с автомобиля, разбирают, очищают, промывают, регулируют и при необходимости заменяют негодные детали. Основные неисправности газобаллонных установок и способы их устранения.При работе двигателя на газе в системе питания могут возникнуть неисправности, которые вызывают затрудненный пуск двигателя, неустойчивую работу на холостом ходу, неудовлетворительные переходы от холостого хода к нагрузочным режимам, снижение мощности двигателя. Ниже рассмотрены признаки и способы устранения этих неисправностей. Негерметичность соединений газовой установки может быть двух видов: внутренняя и внешняя. Под внутренней негерметичностью газового оборудования понимают неплотности, в результате которых происходит утечка газа в систему питания. Наиболее часто эта неисправность встречается в подвижных запорных соединениях (клапан – седло) у расходных и магистрального вентилей, а также в клапанах первой и второй ступеней редуктора. Утечки газа через клапан первой ступени редуктора определяются по показанию манометра редуктора. В этом случае при остановке двигателя повышается давление в камере первой ступени, что может повлечь за собой открытие клапана второй ступени редуктора. При этом газ начнет выходить в подкапотное пространство. Нарушение герметичности клапана второй ступени, который выполняет роль запорного вентиля при неработающем двигателе и открытых магистральном и расходном вентилях, вызывает утечку газа из редуктора в смеситель и далее через воздушный фильтр в подкапотное пространство. Затрудненный пуск двигателя происходит при переобогащении или переобеднении горючей смеси. Причинами переобогащения горючей смеси являются негерметичность клапанов первой и второй ступеней редуктора и неплотность обратного клапана смесителя. Переобеднение горючей смеси вызывается негерметичностью шланга подачи газа в систему холостого хода и засорением или сужением проходного сечения канала системы холостого хода. При негерметичности разгрузочного устройства редуктора или трубки, соединяющей полость разгрузочного устройства с впускным трубопроводом двигателя, прекращается подача газа из редуктора в смеситель и пуск двигателя в этом случае становится невозможным. Неустойчивая работа двигателя на холостом ходу может быть вызвана следующими причинами: неправильной регулировкой подачи газа в систему холостого хода; поступлением газа через основную систему вследствие неплотности обратного клапана смесителя или клапана второй ступени редуктора; уменьшением подачи газа в систему холостого хода из-за негерметичности шланга системы или засорения его проходного сечения. Для устранения неустойчивой работы двигателя регулируют систему холостого хода или устраняют неплотности. 2. Назначение сцепления ‑ передача вращения от двигателя к трансмиссии, быстрое их разъединение, плавное соединение при трогании и переключении передач. Его устанавливают за двигателем. Сцепления также предохраняют детали двигателя и трансмиссию от динамических нагрузок и демпфируют крутильные колебания. Требования: надежно и с высоким КПД передавать энергию от двигателя к трансмиссии, предохранять двигатель и трансмиссию от динамических нагрузок; обеспечивать плавное, регулируемое и полное соединение двигателя и трансмиссии, их быстрое и полное разъединение; ведомый диск должен иметь минимальный момент инерции и высокий коэффициент трения при работе его фрикционного материала по чугуну, а также высокую износостойкость. Сцепление должно обладать хорошей уравновешенностью, достаточно быстро отводить теплоту и продукты износа, быть легко управляемым и доступным для технического обслуживания и ремонта. 3. Требования к планировочным решениям — взаимное расположение зон и участков в соответствии с технологическим процессом; - отсутствие в местах интенсивного движения ПС пересечений их потоков (при наличии 10 и более постов ТО-ТР или 50 и более мест хранения ПС движение предусматривают в одном направлении без встречных и пересекающих потоков); - возможность в перспективе изменения технологических процессов и расширения производства без существенной реконструкции здания. Технологической основой планировочного решения предприятия служат функциональная схема и график производственного процесс ТО, ТР а/м.Функциональная схема автономного АТП показывает возможные пути прохождения автомобилей различных этапов производственного процесса.(качественные пар-ры) Количественную характеристику этого процесса, т.е. мощность суточных потоков проходящих различные этапы производства (в единицах ПС) отражает график производственного процесса. Он также учитывает взаиморасположение зон АТП, График непостоянен, т.к. со временем могут изменяться нормативы, определяющие производственную программу. Функц схема и график определяют технологические маршруты, кот устанавливаются для ПС в зав-ти от его тех состояния, плана ТО и условий эксплуатации. Основные маршруты: - Вз – О – ЕО – Х – Вп – - Вз – О – ЕО – O–ТР - Х – Вп – - Вз – О – ЕО – O – Д - Х – Вп – - Вз – О – ЕО – O – Д – О – ТР – О – Д – Х – Вп – - Вз – О – ЕО – O – Д – О – ТР – О – ТО - О – Д – Х – Вп - Вз–О–ЕО–O–Д–О–ТР–О–ТО-О–ТР-О-Д – Х – Вп Если число автомобилей, возвращающихся с линии в единице времени, больше пропускной способности зоны УМР, то часть автомобилей после КПП поступает в зону хранения или зону ожидания. Эти автомобили проходят УМР по мере ее освобождения. Как правило пропускная способность зон ТО-1, ТО-2 и ТР также не позволяет принять на обслуживание все автомобили непосредственно после возвращения их с линии. Поэтому часть автомобилей ожидает ТО и ТР зоне хранения или зоне ожидания. Из зоны хранения исправные автомобили через КПП выпускаются для работы на линии. В этих маршрутах принципиально важным явл необходимость ожидания автомобилей очереди перехода его от предыдущего этапа ТО или ТР к последующему, что явл следствием неодинаковой потребности а/м в различных видах воздействия и неравномерности их поступления в те или иные зоны ТО и ТР. Поэтому практически необходимость ожидания возникает не всегда и не у каждого автомобиля. Однако, несмотря на случайный характер ожидания, рациональная планировка предприятия должна по возможности обеспечивать независимое прохождение автомобилем любого самостоятельного маршрута. Это достигается в первую очередь соответствующим взаимным расположением зон и организацией движения между ними. При этом расположение каждой, зоны должно быть достаточно универсальным. Так, например, зону диагностирования, а также зону текущего ремонта следует располагать так, чтобы автомобиль мог поступить в них из любой зоны и уйти из них в любую зону.
|
|
|
|
|
|
|
|
Билет №4
1. В отличие от дизелей диагностировать систему питания бензинового мотора несколько проще. Все – благодаря более простой конструкции и отсутствию огромного давления в магистралях.
Делается это в следующей последовательности:
·Проверка бензонасоса. В подавляющем большинстве автомобилей вы сможете услышать, как он начинает накачивать бензин в магистраль при включении зажигания после стоянки (слышно характерное жужжание). Если этого не происходит, есть смысл проверить его работу, подав напряжение напрямую с АКБ.
·Измерение уровня давления топлива в системе. Оно производится при помощи специального манометра. Замер давления делается в разных местах топливной магистрали. При этом определятся производительность насоса и давление после топливного фильтра (причина некорректной работы системы может быть в его засорении), а также работа регулятора давления (если он вышел из строя – только замена: данный элемент не ремонтируется).
·Проверка форсунок. Чтобы провести предварительную оценку их работы, достаточно снять рампу и включить бензонасос. Если на соплах появятся капли, значит имеет место нарушение герметичности. Для более качественной диагностики форсунок требуется специализированное оборудование: тестеры и мотор-тестеры для диагностики без снятия, а также специальные стенды для проверки инжекторов при условии демонтажа с машины.
·Проверка системы улавливания паров бензина. Причина может быть в ее разгерметизации. Если слышен отчетливый запах бензина, возможно проблема в ней. Также в составе этой системы есть клапан, контролирующий поступление паров бензина во впускной коллектор. Если при подаче на него напряжения 12В ничего не происходит, клапан вышел из строя. Если слышен щелчок, значит все в порядке.
Машины с карбюраторными двигателями все еще встречаются на наших дорогах. Поэтому их со счетов сбрасывать не стоит. Процесс диагностики топливной системы таких авто сводится к следующему:
·Визуальный осмотр топливных магистралей на предмет протечек и подтекания топлива.
·Контроль степени засоренности фильтра тонкой очистки.
·Диагностика топливного насоса с механическим приводом. Здесь особое внимание нужно уделить целостности рабочих мембран. Диагностика производится методом разборки узла.
·Проверка работы карбюратора. Она сводится к поиску засоров, закоксованности и проверке состояния каналов холостого хода. Также в процессе диагностики оценивается состояние уплотнительных колец, насколько плотно закручены электромагнитные клапаны, степень выработки игольчатого клапана, размеры отверстий жиклеров и их засоренность, состояние поплавка. При этом, в зависимости от модели карбюратора, могут быть свои нюансы, касающиеся методики проверки уровня топлива в поплавковой камере и других моментов. Уточняйте эти вопросы в инструкции.
Видно, что продиагностировать топливную систему бензинового двигателя вполне под силу практически любому автомобилисту. Трудности могут возникнуть только с проверкой форсунок. Для этого лучше обратиться к специалистам. С остальным же, при условии наличия у вас определенных навыков и соответствующего оборудования, проблем возникнуть не должно.
2. Назначение трансмиссии ‑ передача механической энергии на ведущие колеса автомобиля, где в результате взаимодействия колес с опорной поверхностью создается касательная сила тяги, которая и обеспечивает движение машины. В трансмиссии происходят преобразование вращающего момента и одновременно изменение скорости вращения валов пропорционально передаточному числу.
По способу передачи энергии трансмиссии делят на механические, гидромеханические, электромеханические, гидрообъемные. В мех. Трансм. передача энергии происходит за счет механич трения в сцеплениях, а также соединениями валов, шарнирами и зубчатыми колесами. В гидромех. транс м\у двигателем и механической частью трансмиссии устанавливают гидротрансформатор или гидромуфту, осуществляя гидравлическую связь двигателя с трансмиссией. В электромеханической трансмиссии двигатель (как правило, дизель) вращает ротор электрогенератора, энергия которого по электрическому кабелю передается электродвигателю и далее через зубчатый редуктор ведущим колесам или электродвигателям, вмонтированным в ведущие колеса. В гидрообъемных трансмиссиях двиг. приводит в действие гидронасос, который под высоким давлением нагнетает масло в гидромоторы, расположенные в ведущих колесах и приводящие их во вращение. В гидрообъемных трансмиссиях используется гидростатический напор жидкости.
Назначение сцепления ‑ передача вращения от двигателя к трансмиссии, быстрое разъединение двигателя и трансмиссии, плавное их соединение при трогании и переключении передач. Его устанавливают за двигателем. Сцепления также предохраняют детали двигателя и трансмиссию от динамических нагрузок и демпфируют крутильные колебания.
Назначение КПП – изменение скорости движения авто, обеспечение движения задним ходом, длительное отключение трансмиссии от двигателя.
Карданная передача предназначена для передачи вращающего момента и соединения агрегатов трансмиссии, валы которых несоосны или расположены под некоторым углом один к другому, изменяющимся при движении а\м.
Ведущий мост предназначен для передачи вращающего момента от карданного вала к ведущим колесам автомобиля.
Главн передача предназнач. для увелич. вращ. момента и передачи его к ведущ. колесам.
Дифференциал – механизм трансмиссии, распределяющий подводимый к нему вращающийся момент между выходными валами и обеспечивающий их вращение с разными угловыми скор.
Полуоси служат для передачи вращающего момента от дифференциала к ведущим колесам.
3. Если некоторые детали шатунно-поршневой группы не повреждены и мало изношены, они могут быть использованы снова. Поршневые пальцы должны сниматься только с помощью пресса. Применение молотка не допускается. Перед сборкой поршневой палец подбирается к поршню. Допустимым считается такой его износ, при котором палец не выпадает из поршня, если держать последний так, чтобы палец находился в вертикальном положении, а будучи смочен моторным маслом, входил в отверстие поршня при нажатии рукой. Если поршневой палец выпадает из поршня, его заменяют пальцем следующего размерного класса.
При подборе поршня к цилиндру должен соблюдаться расчетный зазор. Он определяется измерением диаметра этих деталей и обеспечивается установкой поршней того же размерного класса, что и цилиндры. В запасные части могут поставляться поршни промежуточных классов по диаметру, например А, С или Е. Этих классов достаточно для подбора поршня к любому цилиндру, так как поршни и цилиндры разделены на классы с небольшим перекрытием размеров.
Перед установкой поршневых колец необходимо очистить поршень от нагара и удалить все отложения из смазочных каналов поршня и шатуна, а также тщательно осмотреть все детали. Трещины любого характера на поршне, поршневых кольцах, поршневом пальце, шатуне и его крышке не допускаются. Зазор между поршневыми кольцами и их канавками проверяется набором щупов; при этом кольцо со щупом вставляют в проверяемую канавку. Допустимый зазор находится в пределах 0,10...0,15 мм. При подборе колец проверяют также зазор в замке (между концами) кольца. Для измерения желательно использовать калибр, имеющий диаметр, равный номинальному диаметру кольца с допуском ±0,003 мм. При отсутствии калибра допускается проверка зазора в замке кольца, вставленного в цилиндр. Предельный зазор для колец автомобилей всех марок составляет 1 мм. Кольцо при проверке зазора должно располагаться в плоскости, перпендикулярной к оси цилиндра, поэтому продвигать его следует с помощью перевернутого поршня.
Билет №5
1. Негерметичность впускной системы,приводит к тому, что датчик массового расхода или абсолютного давления воздуха дает "неправильный" сигнал электронному блоку, который посылает форсунке неверные управляющие импульсы.
Признаком этой неисправности будет неустойчивая работа двигателя, плохая приемистость автомобиля.
Для устранения неисправности необходимо подтянуть хомуты крепления, проверить герметичность резиновых соединений и переходов впускного тракта системы питания. Следует также проверить электрические разъемы и состояние проводки, очистить клеммы от окислов и грязи. Необходимо удалить отложения, которые мешают свободному перемещению заслонок и регуляторов.
Работу "подозрительного" датчика можно проверить, установив на его место заведомо исправный. Метод временной подмены помогает провести быструю диагностику в "полевых условиях".
Холодный или горячий двигатель не запускается. Включение стартера не обеспечивает запуск двигателя. В таком случае нет смысла повторять попытки без проверки системы.
Возможные причины могут быть в ненадежности электрических соединений, негерметичности топливной системы, неисправности датчика температуры воздуха, датчика массового расхода воздуха, повреждении шланга между регулятором давления и топливным баком, негерметичности форсунок.
Устранение неисправностей заключается в проверке соединений электрических разъемов, соединений топливной системы, замене неработающих датчиков, поврежденных шлангов и форсунок.
При возникновении в системе впрыска какой-либо неисправности на щитке приборов загорается красный сигнал с соответствующим предупреждением. Система "умеет" сама себя диагностировать и записывать коды неисправностей, которые можно прочитать, имея соответствующее оборудование. Для этого предусмотрен специальный диагностический вывод, при подключении к которому неисправный датчик будет тотчас определен.
2. Генератор служит для питания потребителей и заряда аккумуляторной батареи во время работы двигателя. Требования: обеспечение питанием всех потребителей при полной нагрузке; стабильное напряжение в широком диапазоне изменения частоты вращения двигателя (13,2...15,5 В); минимальные масса и стоимость; надежность при работе в условиях вибрации, запыленности и повышенной температуры. В современные автомобили устанавливают генераторы переменного тока, которые обладают следующими преимуществами: работают в большем диапазоне частот вращения; имеют больший срок службы; при той же мощности легче в 1,8...2,5 раза; на их изготовление требуется в 3 раза меньше меди; обладают большей надежностью, меньшей трудоемкостью их технического обслуживания.
Для получения постоянного тока в генераторы встраивают выпрямительные устройства с электронными регуляторами напряжения и все вместе называют генераторной установкой. Эти установки обладают свойствами самоограничения максимальной силы тока, а выпрямительное устройство предотвращает разряд аккумулятора через обмотки генератора.
Типы генераторов. В автомобилях применяют генераторы индукторного типа и с укороченными полюсами (с клювообразным ротором). Существенных различий в их работе нет. В таких генераторах питание обмотки возбуждения ОВ происходит через регулятор напряжения РН непосредственно от генератора, а при его малом напряжении и при пуске — от аккумулятора. Обмотка возбуждения находится на роторе, а на статоре — неподвижная трехфазная силовая обмотка. Обычно три фазы А, В и С соединены по схеме «звезда», т.е. начала всех трех обмоток соединены вместе. Ток каждой фазы проходит через диодные выпрямители. Регулятор напряжения включен в цепь обмотки возбуждения. Он стабилизирует напряжение генератора при постоянно изменяющихся частоте вращения, времени и числе подключаемых потребителей.
3. Коренные и шатунные подшипники (вкладыши) могут подразделяться на классы по толщине центральной части. Разбивка на классы для каждой модели двигателя индивидуальна. Обозначение класса также может быть различным: по идентификационной окраске (например, 0 - черный, 1 - коричневый, 2 - синий и т. д.) или по номеру класса, указанному на подшипнике и блоке цилиндров. Существуют также подшипники ремонтного размера с увеличением (уменьшением) диаметра шеек коленчатого вала на 0,25 мм, 0,50 мм и т. д.
Для подшипников некоторых моделей двигателей могут применяться промежуточные (уменьшенные) размеры между основными; индекс на таких подшипниках обозначается в виде меток.
На поверхности подшипников не допускаются задиры, отслоения и повышенный износ. Для определения пригодности подшипников к дальнейшей эксплуатации проверяют зазор между ними и шейками коленчатого вала. Для этого измеряют диаметр шеек, постелей под подшипники и толщину подшипников.
Для определения зазора в шатунных подшипниках сначала устанавливают подшипник в нижнюю головку шатуна, затягивают гайки крепления крышки головки сборочным моментом (как правило, это делается в два этапа: 1-й - небольшим моментом, 2-й - в 2...3 раза большим) и измеряют внутренний диаметр установленного подшипника. После этого измеряют наружный диаметр соответствующей шатунной шейки коленчатого вала и по разности двух полученных значений определяют зазор. Таким же образом измеряют зазор и в остальных шатунных подшипниках.
Для определения зазора в коренных подшипниках их устанавливают на свои места в блоке цилиндров и закрепляют крышками (используя сборочный момент затяжки болтов крепления). Затем с помощью нутромера последовательно измеряют внутренний диаметр подшипников, диаметр соответствующих им коренных шеек коленчатого вала и по разности двух полученных значений определяют зазор.
Вышеуказанными методами проверяют зазор для каждого коренного и каждого шатунного подшипника.
Проверять зазор в подшипниках коленчатого вала можно также с помощью специальной калиброванной пластмассовой проволоки (Plastigage). Проверку выполняют следующим образом:
·тщательно очищают рабочие поверхности подшипника и соответствующей шейки вала, на поверхность шейки кладут отрезок проволоки (после этого не допускается проворачивание вала);
·на шейку осторожно, чтобы не сдвинуть проволоку, устанавливают шатун с крышкой или крышку коренного подшипника (в зависимости от вида проверяемого подшипника) и закрепляют с использованием сборочного момента затяжки;
·снимают крышку проверяемого подшипника, и по шкале, нанесенной на упаковке от проволоки, определяют зазор.
Одним из простых, хотя и недостаточно точных, методов проверки зазора в подшипниках скольжения является ручная проверка. В этом случае исходят из того, что при нормальном зазоре в шатунном подшипнике шатун без поршня, собранный на шейке вала с полностью затянутой крышкой, должен плавно опускаться под действием собственного веса из горизонтального положения в вертикальное, а при нормальном зазоре в коренных подшипниках (при полностью затянутых их крышках) коленчатый вал (без установленных шатунов) должен легко проворачиваться вручную. Перед проверкой шатунных подшипников должны быть смазаны моторным маслом шатунные шейки вала, а коренных - коренные.
Если после проверки зазор окажется больше допустимого, необходимо заменить подшипники на подшипники следующего ремонтного размера с перешлифовкой шеек коленчатого вала.
Ремонтные подшипники, как правило, имеют увеличенную толщину под шейки коленчатого вала, расточенные на 0,25, 0,50, 0,75 или 1,00 мм.
Билет №6
1. Процесс диагностики топливной системы дизельного движка сводится к следующему:
·Проверка работоспособности топливного насоса высокого давления (ТНВД).
·Оценка состояния форсунок.
·Проверка магистралей на предмет утечек в них.
·Диагностика электрооборудования.
Топливный насос высокого давления диагностируется в 3 этапа:
·Визуальный осмотр. В ходе него узел осматривается на предмет наличия подтеканий, механических повреждений и других проблем.
·Механическая диагностика ТНВД. Для этого насос нужно демонтировать с авто и частично разобрать. Механическая диагностика сводится к поиску заклинивших толкателей или плунжерных пар, дозаторов и других элементов. Также оценивается, насколько изношены втулки, плунжеры и другие компоненты.
·Проверка ТНВД на стенде. К ней, как правило, прибегают, если в ходе механической диагностики ничего выявить не удалось. Специализированный стенд позволяет имитировать работу топливного насоса высокого давления в реальных условиях и точно оценить состояние всех его элементов.
Регулировка форсунки – это самый ответственный момент. Для начала ее нужно собрать и установить на стенд. Затем регулировочным винтом необходимо добиться положения пружины, при котором внутри форсунки создастся избыточное давление топлива. Первый тест – осмотр качества распыления. Для этого можно взять лист бумаги и подставить под форсунку в момент открытия. На бумаге должен отпечататься нормальный круг.
Если параметры давления и качество распыления в норме, то можно законтрить регулировочный винт и ставить форсунку на место.
Иногда случается ухудшение работы двигателя после выполненной самостоятельной регулировки насос-форсунок. Причиной может оказаться не столько качество регулировки, сколько отношение к замене всех прокладок. Если на холодном двигателе это будет незаметно, то на прогретом дефект сразу проявится. Другой темой такого подвоха может быть дефект регулировочного винта или болта фиксации.
2. Бесконтактные системы зажигания — это электронные системы второго поколения. В них отсутствуют недостатки классической и контактно-транзисторной систем. Прерыватель заменен бесконтактным датчиком VD (чаще магнитоэлектрическим), который вырабатывает импульсы в строго определенные моменты времени. Через блок управления, представляющий собой блок транзисторов VT, импульсы поступают в катушку зажигания. Распределитель передает импульсы высокого напряжения на свечи. Это системы зажигания повышенной энергии искры (до 50 мДж) и высокого вторичного напряжения (до 30 кВ).
Током базы Б транзистора управляет датчик VD углового положения коленчатого вала. В системе применяют магнитоэлектрические датчики и датчики Холла. Магнитоэлектрический датчик представляет собой катушку с сердечником. При прохождении мимо сердечника полюса магнита (диск с зубцами) в катушке возникает ЭДС, которая подается на базу Б транзистора.
Датчик Холла представляет собой полупроводниковую пленку (ПП), вдоль которой в одной плоскости проходит ток. При прохождении магнитного поля поперек плоскости пленки на ее краях возникает ЭДС, которая через усилитель подается на базу Б транзистора. Магнитное поле создается постоянным магнитом (от которого датчик экранирован) вращающимся диском с прорезями. Эффект Холла возникает при прохождении прорези диска мимо датчика. Датчик Холла состоит из постоянного магнита, полупроводниковой пластины и интегральной микросхемы. Между полупроводниковой пластиной и магнитом вращается стальной экран с четырьмя прорезями, что соответствует числу цилиндров. Когда прорезь экрана проходит между магнитом и пластиной, в ней возникает эффект Холла.
Коммутатор служит для увеличения силы тока в первичной цепи (тока разрыва) и формирования нужного импульса высокого напряжения независимо от режима работы двигателя.
3. В общем планировочном решении возможны различные варианты расположения постов ТО, ТР и помещений, производственных участков. Расположение производственных участков и складов определяется их технологическим тяготением к основным зонам ТО и ТР.
Принципы расположения постов:
·Посты уборочно-моечных работ располагаются в отдельных помещениях, а при Т воздуха 0ОС посты ЕО можно размещать на открытых площадках, под навесом
·Посты общего диагностирования Д-1 располагаются в отдельных помещениях или в одном помещении с постами ТО,ТР, а поточные линии Д-1 – в отдельном помещении.
·Посты углубленного диагностирования Д-2 располагаются в отдельном помещении. На АТП до 200 а/м I категории можно размещать Д-2 в помещении с постами ТО, ТР.
·Посты ТО-1 можно располагать в общем помещении с постами ТО-2, ТР. Линии ТО-1 – в отдельных помещениях.
·Посты ТО-2 – совместно с постами ТО-1, ТР. Линии ТО-2 – в отдельном помещении или в общем с линией ТО-1.
·Посты ТР – в общем с постами ТО-1,ТО-2.
·Посты ТО, ТР для автопоездов и сочлененных автобусов обязательно делают проездными.
По однородному характеру работ на участках технологически связанных с постовыми работами ТО и ТР выделяются группы:
1. Посты уборочно-моечных работ, помещения насосной и сушки спецодежды, аппаратная, очистные сооружения.
2. Сварочные и жестяницкие участки с постами, арматурный участок, склады ацетилена и кислорода (в отдельном помещении или под навесом вне опасных производствен. зон).
3. Кузнечно-рессорный, медницкий и склад металла.
4. Посты ТР, шиномонтажный и вулканизационный участки, снятие и установка колес ПС, склад шин.
5. Посты разборочно-сборочных работ ТР, агрегатный участок, склад агрегатов, инструментально-раздаточная кладовая, слесарно-механический участок, склад з/ч и материалов.
6. Посты ТО-1 и ТО-2.
7. Окрасочный участок с постами подготовки, окраски и сушки, краскоприготовительная, склад красок, насосная пожаротушения, очистные сооружения.
8. Деревообрабатывающий участок, обойный участок, склад пиломатериалов.
По противопожарным требованиям не допускается непосредственное сообщение зоны хранения с участками: аккумуляторным, вулканизационным, сварочным, медницким, деревообрабатывающим, обойным, окрасочным и складом масел.
При планировке целесообразно блокировать помещения в пределах перечисленных групп и между группами следующим образом:
- кузнечно-рессорный, медницкий и сварочный участки располагаются смежно (в одном блоке помещений),
- окрасочный, жестяницкий, арматурный, обойный и деревообрабатывающий участки(по условиям технологического процесса) так же размещаются смежно;
- слесарно-механический и агрегатный участки группируют вместе рядом со складами запчастей, агрегатов и материалов; смежно размещают инструментально-раздаточную кладовую;
Другие помещения и участки меньше зависят от общего технологического процесса, но их размещение должно быть увязано единой компоновочной схемой производственного корпуса АТП.
Сетка колонн измеряется расстоянием между осями рядов в продольном и поперечном направлениях: меньшее расстояние — шаг колонн, а большее — пролет. Пролеты и шаг колонн должны быть кратны 6 м. При соответствующем обосновании допускается принимать пролеты 9 м. Здание должно иметь однотипную сетку колонн.
Одноэтажные производственные здания АТП проектируются с сеткой колонн 12*12, 12*18 и 12*24, 12*36 м. (первое число шаг колонн, второе пролет) Шаг колонн 12 м улучшает использование производственных площадей и снижает стоимость строительства на 4-5% ( в сравнении с шагом 6 м).
Многоэтажные здания разрабатываются с сеткой колонн 6*6, 6*9, 6*12 и 9*12 м, на верхнем этаже допускается укрупненная сетка колонн (6*18 и 12*18 м).
Для зданий небольших АТП допускается сетка колонн 6*9, 6*12, 6*15 м.
Административно-бытовые помещения размещаются в отдельном здании или в корпусе, примыкающем к производственному. Отдельно стоящие здания ухудшают связи между корпусами и вызывают дублирование бытовых помещений!
Билет №7
1. ???
2. Мощность и экономичность двигателя зависят от угла впрыскивания. Каждый двигатель на любом нагрузочном и скоростном режиме имеет оптимальный угол опережения впрыскивания. Поэтому в процессе работы его необходимо менять.Если кулачковый вал повернуть вперед по ходу вращения, то кулачок набежит раньше на толкатель, подача топлива плунжером, а следовательно, и впрыск его форсункой начнутся раньше. Относительный поворот кулачкового вала производится муфтой опережения угла впрыскивания, которая в зависимости от частоты вращения двигателя меняет взаимное положение кулачкового и коленчатого валов. Это обеспечивает работу двигателя с оптимальным углом опережения впрыскивания в широком диапазоне частот вращения.
. Привод насоса высокого давления осуществляется через муфту опережения впрыскиванияи вал с двумя полужесткими карданными муфтами от распределительных шестерен двигателя. Частота вращения кулачкового вала в 2 раза меньше частоты коленчатого вала.
Ведомая полумуфта установлена на кулачковом валу насоса. В ней закреплены оси двух грузов. Пружины стремятся прижать их к оси муфты.
При максимальной частоте вращения грузы под действием центробежной силы поворачиваются на осяхи, преодолевая силу пружин, прижимаются к корпусу . При этом они за счет фигурной поверхности через проставку воздействуют на упорный палец и слегка поворачивают ведомую часть, а вместе с ней и вал насоса вперед по ходу вращения на некоторый угол. Это приводит к увеличению угла опережения впрыскивания. При снижении частоты вращения проставка занимает промежуточное положение, обеспечивая соответствующий угол опережения впрыскивания.
3. Площади АТП по функциональному назначению подразделяются на:
- производственно-складские (зоны ТО, ТР, производственные участки, склады, технические помещения энергетических и санитарно-технических служб(компрессорные, трансформаторные и т. д.))
- для хранения ПС (площади стоянок, с учетом площади оборудования для подогрева ПС (для открытых стоянок)), рамп и поэтажных проездов (для закрытых многоэтажных стоянок)
- вспомогательные ( административно-бытовые помещения, пункты питания, медпункты, помещения для учебных занятий).
Уборочно-моечные работы ЕО на больших АТП выполняются на тупиковых или проездных постах. При наличии в парке > 50 единиц ПС мойка осуществляется механизированным способом. На крупных и средних АТП уборочно-моечные работы, как правило, выполняются на поточных линиях непрерывного действия с применением механизированных установок для мойки и сушки автомобиля.
Число постов ЕОС кроме механизированных, ЕОТ, Д-1, Д-2, ТО-1, ТО-2 определяем по формуле:
Xi = Т i Г · φ / (Драб.г. · Тсм · с · Рср · ηИ) ,
где φ – коэффициент неравномерности загрузки постов; Тсм– продолжительность смены, ч; с – количество смен; Рср – среднее число рабочих одновременно работающих на одном посту, чел; ηИ – коэффициент использования рабочего времени поста.
Количество постов ТР, работающих в несколько смен, рассчитываем по наиболее загруженной смене:
Xi = Т i Г · φ · КТР / (Драб.г. · Тсм · Рср · ηИ) ,
где КТР– коэффициент учитывающий долю работ в наиболее загруженную смену.
Количество постов контрольно-пропускного пункта:
X КПП = АИ · αТ · КП / (Т · Ач) ,
где Т – продолжительность работы поста, ч; Ач – пропускная способность поста, авто/ч.
Число постов ожидания перед ТО и ТР принимается для поточных линий ТО и диагностирования – по одному для каждой линии; для индивидуальных постов ТО, Д и ТР – 20% от числа соответствующих рабочих постов.
При полной механизации работ на линии количество линий определяется числом основных моечных установок. Для обеспечения максимальной производительности линии пропускная способность постовых установок должна быть равна пропускной способности основной линии. Если на линии предусматриваются кроме полностью механизированных (обычно моечных) и работы, выполняемые вручную, то число линий определяется:
m ЕО = τЕОл / R ЕО ,
где τЕОл – такт работы линии, мин; R ЕО – ритм производства, мин.
τЕОл = ( La + a ) / v к ,
где La - габаритная длина автомобиля (автопоезда), м; a - расстояние между автомобилями на постах линии, м (по ОНТП выбирается в зависимости от категории автомобиля); v к - скорость конвейера (назначается для возможности выполнения работ вручную на движущемся автомобиле 2-3 м/мин).
R ЕО = 60 · Твоз / (0,7 · N ЕОс ) ,
Число постов на линии ЕО, назначается из условий их специализации по видам работ (уборка, мойка, сушка и т.д.).
Пропускная способность линии:
N ЕОл = 60 / τЕОл , авто/ч.
Поточные линии периодического действия используются в основном для работ ТО-1 и ТО-2. При выборе поточного метода производства рассчитывается количество линий исходя из ритма производства и такта поста.
m ТО = τТОл / R ТО .
Такт линии ТО:
τЕОл = 60 · ti / (Рср · X л ) + t п ,
где ti - трудоемкость работ данного вида обслуживания, чел-ч; Рср - общее число технологически необходимых рабочих на линии, t п - время передвижения автомобиля с поста на пост линии, мин; X л - число постов линии.
Количество постов линии для данного вида обслуживания назначается по содержанию, технологической последовательности и объема работ, а так же возможной специализации постов по виду работ. Для этого используют операционно-технологические карты, содержащие весь перечень операций по данному виду обслуживания. На их основе ориентировочно группируют работы по намечаемому числу постов с учетом специализации работ, последовательности их выполнения и трудоемкости по постам.
Кол-во линий д.б. целым либо близким к нему (но не > целого, отклонение не > 0,08). На постах линии к концу смены не должно оставаться а/м.
Условия организации поточного метода ТО и Д:
Количество рабочих постов | ||
Одиночные а/м | Автопоезда | |
ТО-1, Д-1 | 3 и > | 2 и > |
ТО-2 | 4 и > | 3 и > |
| ||
Вид организации ТО ПС | Суточная произв программа по технологич совместимому ПС | |
Одиночные а/м | Автопоезда | |
На поточных линиях | 12…15 и > | 5…6 и > |
На отдельных постах | менее 12 | менее 5 |
Состав помещений автономного АТП (схема).
При расчете по удельным площадям, площадь зоны ТО или ТР:
F З = fa · Х3 · КП ,
где fa‑ площадь, занимаемая автомобилем в плане (по габаритным размерам), м2; Х3 - число постов в зоне; КП‑ коэффициент плотности расстановки оборудования постов.
При выполнении планировки зон ТО-ТР их площади уточняются изображением в масштабе постов ТО-ТР и мест ожидания с соблюдением нормативных расстояний.
Площади участков рассчитывают по площади, занимаемой оборудованием, и коэффициенту плотности его расстановки. Площадь участка:
F У = F об · КП ,
где F об - суммарная площадь по габаритным размерам оборудования на участке, м2; КП‑ коэффициент плотности расстановки оборудования (определяется по ОНТП-01-91).
Для приближенных расчетов площади участков могут быть определены по числу работающих на участке в наиболее загруженную смену:
FУ = f 1 + f 2 · (PТ – 1) ,
где f 1 – площадь на одного работающего, м2; f 2 – площадь на каждого последующего работающего, м2; (значения f 1 и f 2 принимаются по нормам ОНТП-01-91); PТ – число технологически необходимых рабочих в наиболее загруженную смену.
Точный расчет площадей производственных участков осуществляется при разработке планировочных решений с учетом норм расстановки оборудования.
Расчет площадей административно-бытовых помещений. Это объект архитектурного проектирования
Билет №8
1. Для автомобилей в рабочий период система ТО включает в себя ЕТО, ТО-1, ТО-2, СТО и ТО в особых условиях эксплуатации.
Для автомобилей ТР носит заявочный характер.
Капитальный ремонт КР автомобилей проводят через установленные нормы пробега (в километрах), зависящие от категории дорожных условий эксплуатации и природно-климатических зон.
Ежедневное обслуживание (ЕО) включает в себя:
- проверку прибывающего с линии и выпускаемого на линию автомобиля;
- внешний уход за ним и заправочные операции.
Сезонное техническое обслуживание (СО) проводится 2 раза в год. Оно является подготовкой автомобиля к эксплуатации в холодное и теплое время года, преимущественно совмещается с ТО-2 с соответствующим увеличением трудоемкости работ.
Текущий ремонт предназначен для устранения возникших отказов и неисправностей автомобиля и агрегатов (прицепов и полуприцепов) и должен способствовать выполнению установленных норм пробега до капитального ремонта при минимальных простоях. Текущий ремонт выполняется путем проведения разборочно-сборочных, слесарно-подгоночных и других необходимых работ с заменой: у агрегата отдельных изношенных или поврежденных деталей кроме базовых (корпусных); у автомобиля (прицепа, полуприцепа) отдельных узлов и агрегатов, требующих текущего или капитального ремонта.
Капитальный ремонт предназначен для восстановления работоспособности автомобилей и агрегатов и обеспечения пробега до последующего капитального ремонта или списания не менее 80% от нормы для новых автомобилей или агрегатов. При капитальном ремонте обязательна полная разборка агрегатов на детали и ремонт базовых деталей.
К базовым (корпусным) деталям автомобиля относятся блок цилиндров, картер коробки передач, трубы карданного вала, картер ведущего моста, балка переднего моста или поперечина при независимой подвеске, картер рулевого механизма и гидроусилителя, каркас кабины, продольные балки рамы.
Трудоемкость представляет собой затраты труда на выполнение работ операции (группы операций) технического обслуживания или ремонта, измеряемые в человеко-часах;
Для сопоставимости условий работы АТП в различных регионах страны осуществляется корректировка нормативов, учитывающая условия эксплуатации, типаж подвижного состава, климатические условия, «возраст» автомобиля и мощность АТП. Необходимо указать на два основных вида корректирования нормативов. Первый (ресурсный) имеет целью корректирование нормативов в зависимости от изменения уровня надежности автомобилей, работающих в различных условиях эксплуатации. Это корректирование приводит к изменению материальных ресурсов, необходимых для проведения ТО и ремонта автомобилей в различных условиях эксплуатации.
При этом АТП, работающие в различных условиях, ставятся в сопоставимые условия.
При первом виде корректирования учитываются пять основных факторов.
Категория условий эксплуатации учитывается с помощью коэффициента К1 и влияет на периодичность ТО, ресурсы до капитального ремонта (К1изменяется от 1,0 до 0,6) и трудоемкость ТР (К1 изменяется от 1,0 до 1,5).
Модификация подвижного состава и особенности организации его работы (автомобили с прицепами, самосвалы и т. д.) учитываются коэффициентом К2, который применяется для корректирования трудоемкости ТО и ТР (К2=1,0¸1,25) и ресурсов до капитального ремонта (К2=1¸0,75).
Природно-климатические условия учитываются при определении периодичности ТО, удельной трудоемкости ТР и норм пробега до капитального ремонта с помощью коэффициента К3, который соответственно изменяется: при определении периодичности — от 0,8 до 1,0; удельной трудоемкости ТР — от 0,9 до 1,3; при определении ресурсов до первого капитального ремонта соответственно от 0,7 до 1,1.
Коэффициент К4 учитывает изменение трудоемкости ТР автомобилей в ремонте в зависимости от пробега автомобиля с начала эксплуатации. Этот коэффициент изменяется для трудоемкости от 0,4 (для пробега, составляющего 25% и менее ресурса автомобиля до капитального ремонта) до 2 и более при пробеге автомобиля в 1,75¸2 раза, превышающем ресурс до капитального ремонта.
В зависимости от пробега с начала эксплуатации до капитального ремонта изменяется и продолжительность простоев автомобиля на ТО и ремонте, которое учитывается коэффициентом К’4 равным 0,7 - 1,4. При пробеге автомобиля, превышающем его значение до первого капитального ремонта, величина К’4 принимается равной 1,4.
Второй вид корректирования (оперативный) Проводится непосредственно на АТП и имеет целью повысить работоспособность автомобилей путем изменения состава операций ТО с учетом конструкций, условий работы автомобилей и особенностей данного АТП. Оперативное корректирование осуществляется только после внедрения на АТП исходных нормативов, рекомендуемых Положением. Этот вид корректирования основывается на объективных данных действующей системы учета по отказам и неисправностям, затратам на ТО и ремонт, а также результатах контрольно-диагностических работ (Д-1 и Д-2). Основным методом корректирования является совместный анализ фактически выполняемых на данном АТП операций ТО, диагностирования и возникающей при этом потребности в ТР, которые непосредственно связаны с режимами и качеством выполнения профилактических работ. При этом, в перечень профилактических операций могут переноситься часто повторяющиеся операции ТР, снижающие работоспособность автомобиля, и исключаются нехарактерные в данных условиях эксплуатации операции ТО. Целесообразность корректирования оценивается технико-экономическим методом.
2. Условия пуска двигателя определяют тип и конструкцию аккумуляторных батарей. Режим пуска наиболее тяжелый. Автомобильные аккумуляторные батареи называют стартерными.
Требования, предъявляемые к стартерным батареям: максимальное рабочее напряжение (12 или 24 В); минимальное внутреннее сопротивление, т. е. они должны давать большой ток; малое изменение напряжения в процессе разряда; максимальное количество энергии, снимаемое с единицы массы (удельная масса); быстрое восстановление емкости в процессе разряда; большая механическая прочность, надежность и простота обслуживания.
Важным показателем считают напряжение.
Аккумулятор, как и любой источник тока, имеет внутреннее сопротивление R, которое противодействует прохождению через него зарядного и разрядного токов.
Следующий важный параметр батареи – ее разрядная емкость Ср, представляющая собой количество электричества, которое аккумулятор может отдать в сеть при полном разряде от начального напряжения U0 до конечного UK за время t. На практике емкость измеряют в ампер-часах (А∙ч).
Уровень электролита проверяют с помощью стеклянной трубки диаметром 5...6 мм. Уровень должен быть 10...15 мм. При меньшем уровне доливают в отсек аккумулятора дистиллированную воду.
Плотность электролита измеряют денсиметром. Температура электролита должна быть 20...З0°С. При меньшей температуре надо пересчитать плотность с учетом поправки приведения к плотности при 25°С. Ориентировочно изменение температуры на 15°С соответствует изменению плотности на 0,01 г/см3. Если плотность электролита в отдельных банках отличается более чем на 0,01 г/см3, ее следует выровнять, доливая электролит плотностью 1,4 г/см3 или дистиллированную воду. Доливать этот электролит нужно в полностью заряженную батарею. После проверки батарею подвергают непродолжительному заряду (на двигателе) и дают ей постоять 1...2 ч, чтобы плотность во всех аккумуляторах выровнялась.
Напряжение батареи проверяют нагрузочной вилкой в режиме, соответствующем пуску горячего двигателя. При этой проверке напряжение должно быть постоянным в течение не менее 5 с. Пробки должны быть завернуты.
Маркировка батарей. Первая цифра 3 или 6 характеризует число аккумуляторов и, соответственно, напряжение батареи 6 или 12 В. Буквы СТ означают стартерная, ТСТ — тракторная стартерная, следующая цифра — номинальная емкость в ампер-часах (А · ч) при 20-часовом режиме разряда. Последующие буквы: материал моноблока (Э — эбонит, Т — термопласт, П — полиэтилен), материал сепараторов (М — мипласт, Р — мипор, П — пластипор, С — стекловолокно) и исполнение (Н — несухозаряженная, А —с общей крышкой). Например, марка 6СТ-55ЭМ означает, что батарея стартерная напряжением 12 В и емкостью 55 А-ч, моноблок выполнен из эбонита, сепараторы — из мипласта, исполнение — сухозаряженная.
3. Основным параметром, определяющим состояние направляющих втулок клапанов, является зазор между ними и стержнями клапанов. Для определения зазора необходимо измерить диаметр стержня клапана и диаметр отверстия его направляющей втулки, а затем вычесть из второго значения первое.
Направляющие втулки, как и клапаны, могут иметь ремонтные размеры. Соответствующий индекс маркируется на стержнях клапанов.
Диаметр стержня клапана измеряют с помощью микрометра в центральной, верхней и нижней частях его стержня. Внутренний диаметр направляющей втулки клапана измеряют нутромером.
Разность между внутренним диаметром втулки и наименьшим из трех значений диаметра стержня клапана, измеренных в разных его частях, есть максимальный зазор между стержнем и направляющей. Другим, менее точным, является метод измерения зазора без снятия головки цилиндров. К клапану, установленному в направляющей втулке, прикладывают ножку индикатора часового типа и устанавливают его на нуль. Затем сдвигают стержень клапана по направлению к индикатору и по его показаниям определяют зазор между стержнем и направляющей. Стержень клапана при измерении рекомендуется перемещать в направлении, параллельном коромыслу, поскольку именно в этом направлении наблюдается наибольший износ направляющей втулки.
При снятой головке цилиндров зазор между направляющей втулкой и клапаном может быть проверен следующим образом. Клапаны и направляющие втулки очищают от отложений, вставляют клапаны во втулки и устанавливают на поверхность блока цилиндров индикатор часового типа. Передвигая тарелку клапана в радиальном направлении, определяют зазор, который не должен превышать 1,0 мм для впускного клапана и 1,3 мм для выпускного.
Промеряют клапаны на деформацию, отсутствие трещин, а также состояние фасок, которые при необходимости шлифуют.
Для проверки пятна контакта рабочей фаски клапана и его седла на фаску наносят тонкий слой свинцового сурика. Клапан устанавливают на место, после легкого прижатия к седлу снимают, затем проверяют отпечаток на его фаске. При нормальном контакте этот отпечаток (пятно контакта) должен занимать всю ширину фаски и не иметь разрывов. Если обнаружены разрывы, необходимо произвести притирку клапана к его седлу.
Проверить герметичность клапанов можно специальным прибором. При проверке закрывают отверстия для свечей зажигания и с помощью груши создают давление 0,5 кг/см2. В течение по крайней мере 100 с не должно наблюдаться падения давления.
Герметичность клапанов можно проверить также с помощью керосина (бензина), налив его во впускные и выпускные полости головки цилиндров, предварительно установив под клапаны пружины. В течение минимум 3 мин утечки керосина (бензина) не должно быть. Кроме того, проверяют биение (изгиб) клапанов, которое не должно превышать 0,02 мм. Клапаны с большим биением заменяют новыми. Шлифовать стержень клапана нецелесообразно, так как возникает необходимость в изготовлении новых сухарей под клапанную пружину (пружины).
Пружины клапанов проверяют на упругость по длине в сжатом и свободном состояниях. Нагрузка при проверке может быть ступенчатой.
Пружины клапанов проверяют и на отклонение от перпендикулярности с помощью стального угольника.
Проверяют выработку толкателей на сферической поверхности пяты и износ юбки, погнутость штанг, погнутость осей коромысел.
Измеряют износ опорных шеек вала, износ и задиры кулачков и изгиб вала, зазоры в подшипниках распределительного вала.
Изгиб (биение) распределительного вала измеряют индикатором часового типа. Вал устанавливают на две призмы или в центрах токарного станка. Биение проверяют, как правило, на средней шейке. Номинальная величина биения на ней обычно устанавливается в пределах 0,02... 0,03 мм, предельно допустимая - не более 0,10 мм. Если биение превышает допустимое, необходимо произвести правку вала.
Для измерения осевого люфта вал укладывается в коренные подшипники головки цилиндров и закрепляется, как при сборке. Ножка индикатора часового типа ставится на торец вала, индикатор сбрасывается на нуль, и вал сдвигается вдоль оси в ту или другую сторону. Суммарный осевой люфт не должен превышать 0,15 мм. В противном случае опорные поверхности крышек подшипников считаются изношенными.
После очистки и промывки распределительного вала проверяют зазор между его шейками и отверстиями опор на головке цилиндров. Этот зазор определяют следующим образом. Измеряют диаметр шейки распределительного вала, устанавливают соответствующий ей подшипник, закрепляют его корпус сборочным моментом и измеряют внутренний диаметр подшипника. После этого вычитают второе значение из первого. Полученная цифра и есть величина зазора. Кроме того, зазор можно измерить с помощью калиброванной пластмассовой проволоки (методика аналогична описанной выше). Максимальный допустимый зазор составляет 0,2 мм.
Проверяют и при необходимости регулировать зазор между рычагами (коромыслами) клапанов и кулачками распределительного вала.
Проверяют и регулируют тепловые зазоры клапанов.
Билет №9
1. Внешними признаками неисправности системы являются потеря герметичности, загрязнение масла и несоответствие давления в системе нормативным значениям.
В процессе работы в системе смазки накапливаются осадки, состоящие из продуктов неполного сгорания топлива и окисления масла. Присадки масел также способствуют отложениям.
Удаление осадков, т.е. промывка системы смазки, является необходимой технологической операцией, особенно при сезонном переводе работы двигателя на масло другой марки. Промывка замедляет ухудшение физико-химических показателей моторного масла, повышает компрессию двигателя (особенно ненового) за счет более свободного положения колец на поршне, уменьшает расход топлива и угар масла, обеспечивает лучшее функционирование смазочной системы.
Промывочные масла - это маловязкие жидкости с особыми присадками. У каждой марки масла своя технология применения, но эффект примерно одинаков. Последовательность промывки системы следующая:
- слить отработанное масло при горячем двигателе;
- залить требуемый объем промывочного масла, обычно несколько выше нижней метки щупа;
- запустить двигатель (избегая резких ускорений) и дать поработать требуемое время на малой частоте вращения;
- слить промывочное масло;
- заменить, очистить, промыть керосином (в зависимости от конструкции) фильтры;
- залить требуемый объем свежего масла, завести двигатель и дать ему поработать на малой частоте, чтобы масло заполнило всю систему;
- проверить уровень масла и при необходимости довести его до нормы.
Некоторые марки промывочных масел после отстаивания можно еще использовать 1-2 раза. При отсутствии промывочных масел можно использовать обычные маловязкие масла, время промывки - примерно 10 мин, или, как исключение, летнее дизельное топливо, время промывки - не более 5 мин.
Пониженное давление в системе является результатом недостаточного уровня масла, разжижения или применения масла пониженной вязкости, загрязнения сетки маслозаборника, фильтров, износа деталей, заедания перепускного клапана в открытом положении.
Повышенное давление является результатом применения масла с большой вязкостью, например, летнего в зимний период, заедания перепускного клапана в закрытом состоянии.
Надежность работы системы во многом зависит от состояния фильтров. Многие двигатели грузовых автомобилей имеют два фильтра: полнопоточный (грубой очистки) и центробежный (тонкой очистки). При ТО-2 у полнопоточных фильтров заменяют фильтрующие элементы, а центробежные разбирают, осматривают и промывают.
2. Преимущества системы впрыскивания бензина: высокая литровая мощность двигателя и улучшенная экономичность за счет точного распределения доз топлива по цилиндрам и меньшего сопротивления впускного тракта (нет карбюратора), возможность точного регулирования состава горючей смеси, минимальная токсичность отработавших газов.
Системы питания с впрыскиванием бензина классифицируют по следующим признакам:
по месту подвода топлива — центральный (моно) впрыск, распределенный (форсунки у каждого впускного клапана), непосредственный (форсунки в головке цилиндров).
Рассмотрим систему питания с впрыскиванием бензина. Бензин из бака под давлением подается через гидроаккумулятор и топливный фильтр к дозатору-распределителю, а от него к рампе — специальному трубопроводу, в котором поддерживается постоянное давление. В рампе установлены форсунки, которые впрыскивают бензин во впускной коллектор. Так как в рампе поддерживается постоянное давление, то количество впрыскиваемого форсункой топлива будет зависеть только от времени ее открытия. Зная расход воздуха и требуемый на данном режиме коэффициент α, можно подать точную дозу топлива. Количество воздуха замеряет датчик-расходомер. Он же воздействует на регулятор давления топлива, а тот, в свою очередь, на дозатор-распределитель, обеспечивая заданное давление и цикловую подачу. Насос рассчитан на подачу топлива в 5...10 раз большую, чем нужно для работы двигателя при полной нагрузке, поэтому большая часть топлива от регулятора давления идет на слив, что обеспечивает прокачку топлива через фильтр несколько раз в час.
При пуске двигателя в работу включается пусковая форсунка, а воздух в цилиндры поступает через специальный дополнительный канал во впускном коллекторе.
В системе с впрыском топлива функции управления и обработки сигналов по системе питания и зажигания выполняет электронный блок управления. В него введены сложные программы, учитывающие все возможные режимы работы двигателя. Обращаясь к заложенной к его памяти программе, микропроцессор обеспечивает точные сигналы управления форсунками и другими блоками.
3. Зубчатый ремень должен иметь рабочую поверхность с четким профилем зубьев, без износа, складок, трещин, порезов и отслоений ткани от резины. Ни на одной поверхности ремня не допускаются следы масла.
На торцах ремня не должно наблюдаться расслоений и разлохмачивания. Наружная плоская поверхность должна быть ровной, без складок, трещин, углублений и выпуклостей.
Зубчатый ремень необходимо заменять после пробега каждых 50...100 тыс. км в зависимости от модели двигателя.
Для снятия ремня необходимо удалить его защитный кожух и ременный шкив с коленчатого вала, ослабить крепление натяжителя, снять его пружину, отвести натяжитель в сторону от ремня, освободив ремень от натяжения, и снять сам ремень. После снятия ремня не рекомендуется проворачивать распределительный вал, чтобы избежать контакта клапанов с поршнями. Если все же возникает необходимость поворота распределительного вала, то нужно предварительно осторожно повернуть коленчатый вал в положение, при котором поршни будут находиться в середине хода (для 4-цилиндровых двигателей это поворот на угол 90° при поршне 1-го цилиндра, находящемся в ВМТ), и только после этого проворачивать распределительный вал.
Установка зубчатого ремня привода распределительного вала осуществляется по меткам. Эти метки на разных двигателях могут различаться как по количеству, так и по форме. Зубчатые шкивы коленчатого вала, распределительного вала и топливного насоса высокого давления (в дизельных двигателях) устанавливают на свои места в монтажное положение (как правило, по-другому их установить невозможно). Метки для установки различных приводных деталей двигателя обычно следующие:
·коленчатый вал - метка положения поршня 1 -го цилиндра в ВМТ на такте сжатия, шпоночная канавка для установки зубчатого шкива, метка на зубчатом шкиве, метка на корпусе масляного насоса;
·распределительный вал - шпоночная канавка для установки зубчатого шкива, штифт на торцевой поверхности, метка на зубчатом шкиве, метка на фланце торцевого подшипника или его корпусе;
·топливный насос высокого давления (ТНВД) - метка на зубчатом шкиве, метка на корпусе;
·зубчатый ремень - полосы совмещения (например, белого цвета), стрелка, указывающая направление установки, и стрелка, указывающая направление вращения ремня.
Билет №10
1. Внешними признаками неисправности системы охлаждения являются перегрев или недостаточный прогрев двигателя, потеря герметичности. Перегрев возможен даже при небольшом снижении уровня охлаждающей жидкости в системе. Особенно это проявляется при применении антифризов, которые могут вспениваться из-за наличия в системе воздуха и замедлять отвод тепла. Для предотвращения замерзания антифриза необходимо поддерживать его нормативную плотность.
Неисправный термостат также может быть причиной неисправного функционирования системы охлаждения. Жидкостные термостаты некоторых грузовых автомобилей при потере герметичности заполняют 15% раствором этилового спирта и запаивают мягким припоем. Многие двигатели оснащены порошковыми (фракция церезина в смеси с алюминиевой пудрой) термостатами. При отказе их заменяют на новые. Проверяют термостаты в горячей воде.
У двигателей с принудительным отключением-включением вентилятора может быть отказ датчика, управляющего его работой.
Если охлаждающей жидкостью является вода, в системе образуется накипь, ухудшающая теплообмен. Удаляют накипь специальными составами. При их отсутствии в условиях АТП для двигателей с чугунной головкой блока можно использовать раствор каустика (700-1000 г каустика и 150 г керосина на 10 л воды), для двигателей с головкой и блоком из алюминиевого сплава ‑ раствор хромпика или хромового ангидрида (200 г на 10 л воды). Раствор заливают и выдерживают в системе охлаждения 7-10 ч. Затем запускают двигатель на 15-20 мин (на малой частоте вращения) и раствор сливают. Для удаления шлама систему промывают водой в направлении, обратном циркуляции охлаждающей жидкости.
Герметичность радиаторов восстанавливают пайкой мест повреждения. Сильно поврежденные трубки заменяют на новые или удаляют (заглушают), места установки пропаивают.
Пайка радиаторов из латунных сплавов сложностей не вызывает. Труднее ремонтировать радиаторы из сплавов алюминия. Для этого используют газовые горелки, специальный присадочный материал и припой. По некоторым технологиям место для пайки надо нагреть до 400-560ºС. Если деталь прогрета недостаточно, то припой будет распределяться по поверхности не равномерно, как требуется, а отдельными наплывами.
2. Гидромуфта вентилятора предназначена для передачи и автоматического регулирования вращающего момента от коленчатого вала к вентилятору, а также для гашения колебаний нагрузки, которые возникают при резком изменении частоты вращения коленчатого вала.
Ведущая часть гидромуфты вращается в шариковых подшипниках. Ведомое колесо в сборе с валом, на котором крепится ступица вентилятора, составляют ведомую часть гидромуфты, передающую вращающий момент валу вентилятора.
3 режима работы вентилятора: 1. автоматический – температура охлаждающей жидкости в двигателе поддерживается в пределе 80...95°С, кран выключения гидромуфты установлен в положении В; 2. вентилятор отключен – кран установлен в положении 0, при этом вентилятор может вращаться с небольшой частотой; 3.вентилятор включен постоянно – работа на этом режиме допустима лишь кратковременно в случае возможных неисправностей гидромуфты и ее выключателя (положение П).
Выключатель гидромуфты с термосиловым датчиком золотникового типа. Его устанавливают на патрубке, подводящем охлаждающую жидкость к водяному насосу от радиатора. При температуре охлаждающей жидкости 81...95°С шток термосилового элемента перемещает золотник, благодаря чему масло из смазочной системы через сообщающиеся полости выключателя подводится в полость гидромуфты. Далее через трубку, каналы в ведущем валу и отверстие в ведомом колесе масло поступает в межлопастные полости рабочих колес, откуда затем сливается через отверстия в кожухе. От степени заполнения маслом полостей рабочих колес зависит передаваемый вращающий момент.
При температуре охлаждающей жидкости ниже 80°С золотник под действием возвратной пружины закрывает полость в корпусе и отключает вентилятор.
3. Генплан предприятия — это план отведенного под застройку земельного участка, ориентированный в отношении сторон света, проездов общего пользования и соседних владений, с указанием на нем зданий и сооружений по их габаритному очертанию, площадки для хранения ПС, основных и вспомогательных проездов и путей движения ПС по территории.
Площадь застройки — определяется как сумма площадей зданий, сооружений, навесов, открытых стоянок, складов, резервных участков под строительство; не включаются площади, занятые отмостками, тротуарами, автодорогами, площадками отдыха, зелеными насаждениями, стоянками для личных автомобилей.
Плотность застройки территории — определяется как отношение площади застройки к площади участка АТП.
Способы застройки участка: а) объединенная (блокированная); б) разобщенная (павильонная).
- при объединенной (блокированной) застройке все основные производственные помещений АТП распологают в одном общем здании. Движение ПС между помещениями осуществляется по внутренним проездам в здании и по наружным проездам на участке; -Более экономична по строительству, удобством организации производственных процессов; -обеспечивает меньшие тепловые потери и создаёт лучшие производственные условия; -стоимость строительства снижается на 15-20 % (в сравнении с павильонной застройкой)
- при разобщенной (павильонной) застройке основные помещения АТП располагаются в отдельно стоящих зданиях. Движение между зданиями происходит по наружным проездам; -уменьшает пожарную опасность; -упрощает планировочное решение; -выгодна для крупногабаритного ПС; - в условиях тёплого и жаркого климата.
Разобщённая застройка часто применяется для малых и средних АТП. Быстрота и последовательность ввода отдельных зданий сокращает сроки окупаемости.
Билет №11
1. Определить неисправность можно по внешним признакам без разборки двигателя. К признакам неисправности КШМ относятся появление посторонних стуков и шумов, падение мощности двигателя повышенный расход масла, перерасход топлива, появление дыма в отработавших газах и др.стуки и шумы в двигателе возникают в результате износа его основных деталей и появления между сопряженными деталями увеличенных зазоров. Стуки в двигателе прослушиваются при помощи стетоскопа, что требует определенного навыка.
При износе поршня и цилиндра, а также при увеличении зазора между ними возникает звонкий металлический стук, хорошо прослушиваемый при работе холодного двигателя. Резкий металлический стук на всех режимах работы двигателя свидетельствует об увеличении зазора между поршневым пальцем и втулкой верхней головки шатуна. Усиление стука при резком увеличении числа оборотов коленчатого вала свидетельствует об износе вкладышей коренных или шатунных подшипников, причем стук более глухого тона указывает на износ вкладышей коренных подшипников.
Падение мощности двигателя возникает при износе или залегании в канавках поршневых колец, износе поршней и цилиндров, а также плохой затяжке головки цилиндров. Эти неисправности вызывают падение компрессии в цилиндре.
При проверке компрессии компрессометром вывертывают свечу зажигания только проверяемого цилиндра и вместо нее устанавливают наконечник компрессометра. Полностью открывают дроссель, воздушную заслонку карбюратора. Провертывают коленчатый вал двигателя при помощи стартера в пределах 3 с. Величина компрессии в исправном двигателе должна быть в пределах 7,0-7,2 кг/см. Разница в величине компрессии в разных цилиндрах не больше 1 кг/см2.
Повышенный расход масла, перерасход топлива, появление дыма в отработавших газах обычно бывает при залегании поршневых колец или износе. Залегание кольца можно устранить без разборки двигателя, для чего в каждый цилиндр горячего двигателя следует залить на ночь через отверстие для свечи зажигания по 20 г смеси равных частей денатурированного спирта и керосина. Утром двигатель следует пустить, дать проработать 10-15 мин, после чего заменить масло.
Отложение нагара на днищах поршней и камер сгорания, расположенных в головках цилиндров, снижает теплопроводность, что вызывает перегрев двигателя, падение его мощности и повышение расхода топлива. Для удаления нагара необходимо выпустить воду, снять приборы, укрепленные на головке цилиндров и, отвернув гайки, осторожно отделить головку цилиндров, при этом не повредив прокладку. Если прокладка приклеилась к блоку или головке цилиндров, то ее следует отделить, пользуясь тупым ножом или широкой и тонкой металлической полоской.
Нагар следует удалять деревянными скребками или скребками из мягкого металла для того, чтобы не повредить днище поршней или станок камеры сгорания. Удалять нагар следует поочередно, закрывая чистой ветошью соседние цилиндры. Для того чтобы легче удалить нагар, его следует размягчить, положив на него ветошь, смоченную керосином. После удаления нагара все детали необходимо очистить и установить на место.
Трещины в стенках рубашки охлаждения блока и головки цилиндров могут появиться в результате замерзания воды или заполнения рубашки охлаждения горячего двигателя холодной водой.
Основные работы, выполняемые при техническом обслуживании кривошипно-шатунного механизма
Ежедневное обслуживание (ЕО): 1. Пустить двигатель и прослушать его работу на разных режимах. Очистить двигатель от грязи и пыли.
Двигатель очищают от грязи скребками, моют керосином при помощи кисти, после чего вытирают насухо. Мыть двигатель бензином нельзя, так как это может привести к пожару.
Первое техническое обслуживание (ТО-1). Проверить крепление двигателя к раме. При проверке крепления опор двигателя гайки расшплинтовать, подтянуть их до отказа и вновь зашплинтовать. Подтягивая гайки крепления необходимо пользоваться исправными инструментами, подбирая ключи точно по размерам гаек.
Второе техническое обслуживание (ТО-2). 1.Закрепить двигатель па раме. 2. Закрепить поддон картера. 3. Проверить компрессию в цилиндрах двигателя. 4. Проверить герметичность соединения головки с блоком цилиндров, при необходимости подтянуть гайки и болты ее крепления специальным динамометрическим ключом, позволяющим контролировать момент затяжки.
Подтягивать резьбовые соединения следует равномерно, без рывков, в строго определенном порядке для каждого типа двигателя. Затягивать нужно от центра, постепенно перемещаясь к краям. После подтяжки гаек головки цилиндров нужно вновь затянуть гайки впускного трубопровода и отрегулировать зазоры между клапанами и коромыслами.
Основные неисправности газораспределительного механизма
Внешними признаками неисправности газораспределительного двигателя являются: уменьшение компрессии, хлопки во впускном и выпускном трубопроводах, падение мощности двигателя и металлический стук.
Уменьшение компрессии, хлопки во впускном и выпускном трубопроводах также падение мощности двигателя возможно вследствие плохого прилегания клапанов к седлам. Плохое прилегание клапана к седлу возможно вследствие отложения нагара на клапанах и седлах, образования раковин на рабочих поверхностях, коробления головок клапанов, поломки клапанных пружин, заедания стержня клапана в направляющей втулке, а также отсутствия зазора между стержнем клапана и коромыслом.
Падение мощности двигателя и резкие металлические стуки возможны вследствие неполного открытия клапанов. Эта неисправность возникает вследствие большого теплового зазора между стержнем клапана и коромыслом.
К неисправностям газораспределительного механизма также относят износ шестерен распределительного и коленчатого валов, направляющих втулок клапанов и толкателей втулок и осей коромысла, а также увеличенное осевое смещение распределительного вала.
Клапаны притирают в следующей последовательности: сливают воду из системы охлаждения, снимают головку цилиндров, помечают каждый клапан с тем, чтобы не перепутать их местами, а затем, пользуясь съемником снимают клапанные пружины. Под притираемый клапан устанавливают слабую пружину. На фаску клапана наносят тонкий слой пасты состоящей из абразивного порошка и масла, и при помощи коловорота или притирочного приспособления клапану сообщают вращательное движение, переменное по направлению. При каждом изменении направления вращения клапана его необходимо приподнимать с тем чтобы притирочная паста вновь попала на фаску клапана и седла. Притирку считают оконченной, если на фасках клапана и седла появятся сплошные матовые пояски шириной 2—3 мм.
Герметичность клапана проверяют на специальном приборе или при помощи керосина. Для этого клапан устанавливают в седло, надевают пружину и приспособления, удерживающие ее на стержне, переворачивают головку цилиндров и в камеры сгорания заливают керосин. Появление керосина на стержне и направляющей втулке свидетельствует о плохой притирке.
В случае коробления головки клапана или больших дефектов на ее фаске клапан следует заменить, так как эти дефекты нельзя устранить притиркой.
2. В зависимости от нагрузки двигатель должен развивать различную мощность, которая, прежде всего, зависит от количества подаваемого топлива, качества его сгорания и момента подачи топлива. В соответствии с этим необходимо обеспечить: 1) подачу при высоком давлении (большем, чем требуется для открытия форсунки); 2) регулирование цикловой подачи; 3) регулирование момента начала подачи. Все эти функции выполняет ТНВД, основой которого является плунжерная пара. Плунжерная пара представляет собой поршневой (плунжерный) гидронасос и состоит из двух деталей: плунжера и втулки. Эти детали прецизионные.
Втулка имеет два окна: верхнее — впускное и нижнее — перепускное. На плунжере выполнена канавка специального профиля, верхний край которой острый — отсечная кромка. Сверху в плунжере сделано сверление, соединяющееся с этой канавкой. Плунжер движется вверх под действием кулачка, а вниз — под действием пружины. На выходе из плунжерной пары установлен нагнетательный клапан.
Когда плунжер находится в нижнем положении, топливо поступает из впускного окна под давлением 0,12...0,15 МПа, которое создает подкачивающий насос. При набегании кулачка на ролик толкателя плунжер начинает двигаться вверх, при этом часть топлива выходит обратно во впускное окно.
Когда плунжер перекроет впускное окно, топливо в полости окажется запертым, что приведет к резкому нарастанию давления — это момент начала нагнетания. Дальнейшее движение плунжера приводит к открытию нагнетательного клапана, и топливо идет к форсунке — это момент начала подачи. Затем отсечная кромка откроет перепускное окно. Топливо из полости под действием перепада давления по сверлению в плунжере и отсечной канавке начнет перетекать в перепускное окно. Нагнетательный клапан садится в гнездо. Подача топлива прекращается — это момент конца подачи топлива. Плунжер продолжает двигаться дальше, но подачи топлива нет, оно перетекает в перепускное окно.
Второе требование — регулирование цикловой подачи. При повороте плунжера вокруг оси начало подачи происходит в одно и то же время (перекрытие верхней кромкой плунжера впускного окна), но отсечная кромка подходит к перепускному окну по-разному, а потому конец подачи может произойти раньше или позже. Соответственно объем топлива будет подан меньше или больше. Таким образом, регулирование цикловой подачи во время работы двигателя осуществляется поворотом плунжера вокруг оси.
Третье требование — регулирование момента начала подачи. Если удлинить плунжер, то момент перекрытия впускного окна произойдет раньше, подача начнется раньше и наоборот. При регулировке изменяют не длину плунжера, а длину толкателя, у которого есть регулировочный винт.
3. Работоспособность термостата можно проверить без его снятия с двигателя (с меньшей достоверностью) и после его снятия с двигателя (с большей достоверностью). В первом случае запускают двигатель и прогревают его до рабочей температуры. В ходе прогрева проверяют температуру отводящего патрубка радиатора. Если патрубок и сам радиатор нагреваются медленно, это указывает на заклинивание термостата в открытом состоянии или вообще на отсутствие термостата. Во втором случае термостат снимают с двигателя и помещают в емкость с жидкостью, имеющей температуру окружающего воздуха. Можно использовать обычную воду, но учитывая, что температура охлаждающей жидкости в современных двигателях может превышать 100°С (это приблизительная точка кипения воды), желательно применять технический глицерин, температура кипения которого выше этой точки. В случае же использования воды можно проверить только начало открытия клапана (правда, это относится не ко всем двигателям). Жидкость постепенно нагревают. При температуре 70...80°С (в зависимости от модели двигателя) должно начаться открытие клапана термостата. За температуру начала открытия принимается та, при которой ход клапана, расположенного со стороны входного патрубка радиатора, составляет 0,1 мм. Для более точного определения величины хода можно использовать индикатор часового типа на кронштейне. Дальнейшее повышение температуры до 90...110°С (в зависимости от модели двигателя) должно привести к полному открытию клапана (0,6...0,8 мм). Если после проведения вышеописанной проверки термостат не удовлетворяет указанным условиям, его заменяют на новый, так как ремонту он не подлежит.
Билет №12
1. В соответствии с СТБ 1848-2009 под «экологическим классом» понимают классификационный код, характеризующий транспортное средство в зависимости от уровня выбросов, заложенного в конструкцию транспортного средства. Экологический класс транспортного средства напрямую зависит от уровня токсичности установленного на нем двигателя. Код экологического класса совпадает с номером экологического стандарта, используемого ЕКМТ. Например, экологический класс 4 соответствует стандарту Евро4 и т.д.
В зависимости от уровня выбросов, предусмотренного конструкцией, ТС подразделяют на
шесть экологических классов.
Соответствие ТС определенному экологическому классу удостоверяется одним из следующих
документов:
– сообщением, касающимся официального утверждения типа ТС и двигателя, предусмотренным
Правилами ЕЭК ООН;
– одобрением типа ТС;
– сертификатом соответствия на ТС и двигатель по Правилам ЕЭК ООН или Директивам ЕС;
– паспортом ТС/шасси ТС.
Примечания
1 В настоящем стандарте использованы ссылки на Правила ЕЭК ООН № 49 и Правила ЕЭК ООН № 83, действовавшие на момент выпуска ТС.
2 В настоящем стандарте использованы ссылки на Правила ЕЭК ООН № 96, планируемые к введению на
территории Республики Беларусь.
4.2 К экологическому классу 1 относятся ТС категорий М и N, предельный уровень выбросов
которых выше уровня экологического класса 2.
4.3 К экологическому классу 2 относятся ТС категорий М и N, предельный уровень выбросов
которых соответствует требованиям ТНПА.
4.4 К экологическому классу 3 относятся ТС категорий М и N, предельный уровень выбросов
которых соответствует требованиям ТНПА.
4.5 К экологическому классу 4 относятся ТС категорий М и N, предельный уровень выбросов
которых соответствует требованиям ТНПА.
4.6 К экологическому классу 5 относятся ТС категорий М и N, предельный уровень выбросов
которых соответствует требованиям ТНПА.
4.7 К экологическому классу 6 относятся ТС категорий М и N, предельные значения выбросов
которых соответствуют значениям.
2. При установившемся режиме работы вращ. момент двигателя равен моменту сопротивления. Во время работы непрерывно изменяется нагрузка на а/м, а следовательно, и на двигатель. Однако водитель не всегда может среагировать на колебания нагрузки. Для поддержания показателей двигателя (заданного скоростного режима) в определенных пределах применяют систему регулир, основным элементом которой является регулятор частоты вращения.
Чтобы изменить частоту вращения, которую поддерживает регулятор, нужно изменить соотношение сил Рс (центробежной силы) и Рпр (силы пружин). Этого можно достичь, изменяя массу грузов или длину их рычагов, или силу пружины. Последнее выполнить легче. Сила пружины изменяется рычагом, который связан с педалью акселератора в кабине. Таким образом, водитель, изменяя положение рычага (педали) акселератора в кабине, изменяет натяжение пружины, т.е. дает регулятору команду поддерживать новый скоростной режим. Регулятор, перемещая рейку топливного насоса, обеспечивает постоянную заданную частоту вращения.
Мощность и экономичность двигателя зависят от угла впрыскивания. Каждый двигатель на любом нагрузочном и скоростном режиме имеет оптимальный угол опережения впрыскивания. Поэтому в процессе работы его необходимо менять. Если кулачковый вал повернуть вперед по ходу вращения, то кулачок набежит раньше на толкатель, подача топлива плунжером, а следовательно, и впрыск его форсункой начнутся раньше. Относительный поворот кулачкового вала производится муфтой опережения угла впрыскивания, которая в зависимости от частоты вращения двигателя меняет взаимное положение кулачкового и коленчатого валов. Это обеспечивает работу двигателя с оптимальным углом опережения впрыскивания в широком диапазоне частот вращения.
Привод ТНВД осуществляется через муфту опережения впрыскивания и вал с двумя полужесткими карданными муфтами от распределительных шестерен двигателя.
Ведомая полумуфта установлена на кулачковом валу насоса. В ней закреплены оси двух грузов. Пружины стремятся прижать их к оси муфты.
При максимальной частоте вращения грузы под действием центробежной силы поворачиваются на осях и, преодолевая силу пружин, прижимаются к корпусу. При этом они за счет фигурной пов-ти воздействуют на упорный палец и слегка поворачивают ведомую часть, а вместе с ней и вал насоса вперед по ходу вращения на некоторый угол. Это приводит к увеличению угла опережения впрыскивания. При снижении частоты вращения проставка занимает промежуточное положение, обеспечивая соответствующий угол опережения впрыскивания.
3. Компрессия измеряется с помощью компрессометра или компрессографа.
Компрессометр и компрессограф представляют собой манометр с рукояткой, трубкой, наконечником и золотниковым устройством. Компрессограф обеспечивает запись показаний на специальных покрытых воском карточках, на которых остается информация о компрессии в каждом цилиндре. Он может иметь кнопку и электропроводку для подсоединения к реле включения стартера, что позволяет проверять компрессию самостоятельно, без помощника. Компрессографы удобны в работе, повышают культуру труда и облегчают сбор информации о двигателе.
Компрессию в бензиновых двигателях проверяют при прогретом двигателе. Наконечник компрессографа или компрессометра вставляют в свечное отверстие, предохраняют от запуска двигатель, отсоединив, например, центральный провод от катушки зажигания, и проворачивают коленчатый вал стартером с частотой 200...250 об/мин, что обеспечивается полностью заряженным аккумулятором.
Компрессию в дизельных двигателях можно проверять как при прогретом, так и при холодном двигателе (температура 20 °С). Для этого топливные трубки высокого давления отсоединяют от форсунок, предварительно ослабив их крепление и соблюдая осторожность, так как в трубках может быть остаточное высокое давление. После этого от форсунок отсоединяют трубку для слива топлива и выворачивают их. Затем в отверстие проверяемого цилиндра с помощью переходника подсоединяют компрессометр или компрессограф и отсоединяют разъем от электромагнитного клапана прекращения подачи топлива (для исключения подачи топлива в процессе проверки). Выполнив все это, до отказа нажимают педаль акселератора и с помощью стартера проворачивают коленчатый вал двигателя. Проверка компрессии должна производиться по возможности быстро, не более 10 с.
Для более полной оценки технического состояния двигателя при снижении давления в конце такта сжатия нужно залить в проверяемый цилиндр 10... 15 см3 моторного масла и вторично произвести измерение. Если давление в конце такта сжатия возросло, то это указывает на износ поршневых колец, если же оно осталось прежним - на неплотное прилегание клапанов к седлам или подгорание клапанов. Пониженное давление в двух соседних цилиндрах, не повышающееся при повторной проверке, указывает на пробой прокладки головки цилиндров.
Для более точного определения состояния цилиндропоршневой группы все чаще применяются пневмотестеры типа К-272. Принцип их работы заключается в том, что воздух в цилиндр двигателя подается под определенным давлением, значение которого регистрируется манометром. В случае износа цилиндров или неплотностей посадки клапанов компрессия начинает падать.
Билет №13
1. Прослушивание шумов. Характерные звуки, возникающие в различных сопряжениях, являются следствием нарушения зазоров, износа или поломки деталей, нарушения ре- жима смазки и т.п. Прогрессирующий стук говорит о зазоре в сопряжении твердый металл – мягкий (коленвал – вкладыши), если стук не меняется, то стучит твердый металл о твердый (распредвал – кулачки). Прослушивание производится с помощью стетоскопа, который прикла- дывается к ближайшей к сопряжению поверхности двигателя. Прослуши- ваются сопряжения поршень – цилиндр, поршень – кольца, палец – втулка шейки коленчатого и распределительного валов – подшипники, клапан – втулка и рычаг и др. В качестве стетоскопа можно использовать сухую де- ревянную палку. Свист может возникнуть из-за ослабления, замасливания или перекру- чивания ремня привода генератора или вентилятора, износа шкивов, недоста- точной смазки подшипников генератора, насосов системы охлаждения и гид- роусилителя рулевого управления (эту причину можно установить, пустив двигатель со снятым ремнем, если свист исчезнет, то виноваты подшипники). Причиной возникновения свиста может быть подсос воздуха в месте крепления карбюратора к впускному коллектору. Проверить можно либо у- образным манометром, или проливом мест соединения водой (вода в этом случае будет всасываться внутрь). На высокой ноте могут гудеть перетянутые ремни привода и стартер, шестерня которого не вышла из зацепления с зубчатым венцом маховика. Большое количество периодически действующих источников шума двигателя образуют сплошной акустический спектр, который состоит из от- дельных частотных составляющих, кратных частоте вращения коленвала.
Бестормозной метод проверки двигателя основан на измерении механических потерь в выключенном цилиндре. Достоинство метода в его малой трудоемкости, недостатком является сложность аппаратуры и малая точность. Мощность и крутящий момент двигателя можно также определить при его свободном разгоне без нагрузки. В этом случае измеряют угловое ускорение коленчатого вала при полной подаче топлива от минимально устойчивой частоты вращения на холостом ходу до максимальной. На таком принципе работают приборы типа ИМД (измеритель мощно- сти двигателя), которые включают в себя индуктивный датчик угловой ско- рости и преобразователь сигналов.
2. Усилители предназначены для снижения усилия на рулевом колесе и повышения безопасности движения автомобиля, так как помогают удерживать управляемые колеса в заданном положении при действии со стороны дороги неуравновешенных сил.
Конструкция усилителя должна удовлетворять ряду требований: обладать следящим действием, высокой чувствительностью и достаточным запасом динамической устойчивости, который выражается в отсутствии автоколебаний управляемых колес; обеспечивать возможность управления автомобилем в случае выхода усилителя из строя; не допускать включение усилителя от случайных воздействий со стороны дороги при прямолинейном движении.
Кинематическое слежение заключается в повороте управляемых колес в соответствии с поворотом рулевого колеса и его направлением. Силовое слежение обеспечивает пропорциональность усилия на рулевом колесе усилию, необходимому для поворота управляемых колес.
Гидроусилитель автомобиля ЗИЛ-431410, встроенный непосредственно в рулевой механизм. Давление жидкости в системе гидроусилителя создается лопастным насосом, приводимым от двигателя. При прямолинейном движении автомобиля, когда золотник рулевого управления находится в нейтральном положении, обе полости картера рулевого механизма справа и слева от поршня — рейки соединены с насосом и бачком. Циркулирующая через эти полости жидкость не влияет на положение поршня — рейки.
При повороте рулевого колеса в правую сторону в этом же направлении перемещается и золотник. При перемещении он отключает правую полость картера от линии слива. Поступающая от насоса жидкость давит на поршень — рейку, который, перемещаясь, поворачивает зубчатый сектор на валу сошки и способствует повороту колес автомобиля направо. В то же время проходное сечение, соединяющее левую полость картера рулевого механизма с линией слива, увеличивается и жидкость из нее свободно перетекает в бачок насоса.
При повороте рулевого колеса в левую сторону давление в левой полости картера повышается, а в его правой полости снижается. Гидроусилитель создает дополнительное усилие для поворота колес в левую сторону.
Для обеспечения управления автомобилем при неработающем усилителе в корпусе распределителя предусмотрен клапан, перепускающий жидкость из одной полости цилиндра в другую.
3. При недостаточной производительности или после длительной эксплуатации масляный насос снимают и разбирают, все его детали промывают в керосине и продувают сжатым воздухом. При наличии трещин в корпусе или крышке насоса эти детали заменяют новыми. После этого осматривают ведущую и ведомую шестерни насоса и при наличии значительного износа также заменяют их новыми. Обе шестерни, установленные в корпусе насоса, должны легко вращаться рукой при прикладывании усилия к ведущему валику.
Затем в обычных шестеренчатых насосах с наружным зацеплением шестерен щупом проверяют зазор между корпусом насоса и зубьями шестерен. В шестеренчатых насосах с внутренним зацеплением шестерен проверяют зазор между наружным диаметром ведомой шестерни и расточкой в корпусе насоса. Предельно допустимый зазор составляет (в зависимости от модели двигателя) 0,22...0,25 мм, номинальный - 0,105... 0,175 мм.
Для насосов с внутренним зацеплением шестерен проверяют зазор между наружным диаметром ведущей шестерни и корпусом насоса.
У обычных шестеренчатых насосов измеряют диаметр шестерен и определяют зазор между осью и ведомой шестерней, а также зазор между валиком насоса и отверстием в корпусе.
Крышка насоса в зоне прилегания шестерен не должна иметь уступов. В случае необходимости крышку фрезеруют или шлифуют; при этом максимальная толщина снимаемого слоя не должна превышать 0,2 мм.
Некоторые насосы имеют прокладку между корпусом и крышкой. При ремонте такого насоса прокладка, изготовленная из паронита или картона (обычно толщиной 0,3 мм), заменяется новой. Применение лака, краски или других герметизирующих средств при установке прокладки, равно как и установка более толстой прокладки, не допускается, так как это приводит к снижению производительности насоса.
При ремонте насосов с шестеренчатым приводом от распределительного вала необходимо произвести дополнительные измерения: определить износ зубьев ведомой шестерни привода насоса путем, измерения толщины ее зубьев зубомером. При уменьшении толщины более чем на 0,15 мм по сравнению с номинальным размером шестерню необходимо заменить. Кроме того, следует определить зазор между опорной шайбой и торцом корпуса привода (он не должен превышать 0,25 мм).
В двигателях, имеющих привод масляного насоса типа вал-шестерня, проверяют овальность втулок вала, их запрессовку в гнездах, а также совпадение смазочного отверстия во втулке с каналом в блоке цилиндров. Проворачивание втулок в блоке цилиндров не допускается. Измеряют также диаметры втулок и валика и определяют зазор между ними. Если он больше 0,15 мм, а также если имеются повреждения поверхностей этих деталей, втулки заменяют новыми. После запрессовки втулок их обрабатывают развертками до получения надлежащего диаметра.
Вал привода масляного насоса не должен иметь повреждений опорных шеек, а шестерня вала - визуально заметного износа и выкрашивания зубьев. Не допускается ослабление запрессовки и овальность втулки шестерни привода масляного насоса и распределителя зажигания. Внутренняя поверхность втулки не должна иметь задиров.
Редукционный клапан при ремонте масляного насоса разбирают с промывкой растворителем его гнезда. На клапане и его гнезде не должно быть продольных рисок. Небольшие царапины и сколы плунжерных клапанов можно зашлифовать наждачной бумагой. В случае необходимости проверяют упругость пружины клапана. При нажатии на пружину с усилием 4 кгс ее длина не должна уменьшиться более чем на 11... 13 мм.
Более простым, но неточным методом проверки работоспособности редукционного клапана является проверка нажатием на пружину (шарик, плунжер) прутком из мягкого металла. Пружина (шарик, плунжер) должна перемещаться без помех с некоторым сопротивлением.
Билет №14
1. Диагностирование двигателя по давлению масла, удельному расходу топлива. Повышенный расход масла, перерасход топлива, появление дыма в отработавших газах обычно бывает при залегании поршневых колец или износе. Залегание кольца можно устранить без разборки двигателя, для чего в каждый цилиндр горячего двигателя следует залить на ночь через отверстие для свечи зажигания по 20 г смеси равных частей денатурированного спирта и керосина. Утром двигатель следует пустить, дать проработать 10-15 мин, после чего заменить масло.
Колесная мощность автомобиля снижается в процессе эксплуатации вследствие износа цилиндропоршневой группы, неисправностей газораспределительного механизма, систем питания, зажигания, охлаждения, смазки, состояния трансмиссии и ходовой части. Величина снижения мощности при несвоевременных регулировках может достигать 10...15 %.
Наиболее полно техническое состояние двигателя определяется экспериментально полученной внешней скоростной характеристикой. Однако в целях экономии топлива и времени достаточно снять одну ее точку. Как правило, это либо максимальная мощность, либо мощность на режиме максимального крутящего момента.
Для оценки эффективной мощности могут использоваться стенды тяговых качеств (СТК). Они предназначены для имитации работы автомобиля в различных скоростных и нагрузочных режимах и измерения тяговых показателей. Конструкция стендов включает опорно-приводные, нагрузочные и измерительные устройства. На стендах измеряются колесная мощность, параметры разгона и выбега, а при наличии топливного расходомера — часовой и удельный расход топлива на различных скоростных и нагрузочных режимах. Имитация дорожных условий осуществляется опорно-приводных устройствах (ОПУ) ленточного или роликового типа. Наибольшее распространение получили одно-, двух-, трех- или четырехроликовые устройства, так как при достаточной простоте их конструкции они обеспечивают сопоставимые условия качения колеса на стенде и на дороге.
Обычно один ролик (ведущий) связан с нагрузочным устройством, и другой является поддерживающим. Ведущие ролики жестко связаны между собой с помощью валов и фланцевой муфты, чтобы обеспечить синхронное вращение ведущих колес. Отсутствие такой связи приведет к тому, что в работу будет включаться межколесный дифференциал и второе ведущее колесо может просто остановиться. Поскольку в ведущих мостах автомобилей используются, как правило, симметричные дифференциалы, крутящий момент на первом ведущем колесе тоже снизится до нуля. Замер колесной мощности в этом случае будет в принципе невозможным.
2.Угол развала управляемых колес образуется между плоскостью колеса и вертикальной плоскостью, параллельной продольной оси автомобиля. Если колесо отклонено наружу, угол развала считается положительным, а при обратном наклоне ‑ отрицательным. Для нормальной работы управляемого колеса угол развала всегда должен быть положительным. Он способствует уменьшению усилия на поворот управляемых колес, что облегчает управление автомобилем.
При установке с развалом передние колеса стремятся катиться в сторону от автомобиля по дуге радиусом R вокруг точки О. Но поскольку колеса жестко связаны между собой балкой переднего моста, качение их должно происходить с боковым проскальзыванием. Чтобы исключить это явление, колеса устанавливают под некоторым углом к продольной оси, т.е. со схождением.
Угол схождения совместно с углом развала управляемых колес позволяет предотвратить увод а/м от прямолинейного движения. Установка колес с правильным развалом и схождением обеспечивает прямолинейное качение, что непосредственно влияет на срок службы шин и расход топлива
У грузовых автомобилей конструкцией предусмотрена регулировка только схождения колес, у большинства легковых автомобилей регулируются все параметры установки управляемых колес.
Кроме углов развала и схождения при установке управляемых колес предусматривают угол наклона оси шкворня в поперечной плоскости и угол у наклона оси шкворня в продольной плоскости. Углы наклона шкворня способствуют возврату колес в прямолинейное направление движения после их поворота, что улучшает маневренность и устойчивость автомобиля, повышает накат и срок службы шин.
3. Наиболее достоверные сведения о техническом состоянии системы впрыска можно получить с помощью автомобильных тестеров, позволяющие определять напряжение, силу тока, сопротивление и т. д. Кроме того, для проверки необходимы набор для измерения топлива и мерная небьющаяся емкость.
Для измерения давления в большинстве случаев необходим манометр с набором различных переходников и адаптеров, имеющий пределы измерения 0,40...45 МПа.
Измерение количества подаваемого бензонасосом топлива производится по схеме, т. е. используется топливная магистраль обратного слива. Для этого необходимо отсоединить шланг, идущий от регулятора давления (бензопровод обратного слива), и опустить его в емкость вместимостью не менее 1,0...1,5 л. Встречается достаточно много конструкций, где трубка обратного слива, идущая от регулятора давления, металлическая и не подлежит каким-либо изгибам. В этом случае можно расположить мерную емкость в любом удобном для расстыковки обратного топливопровода месте либо вместо штатного топливопровода подсоединить к регулятору подходящий резиновый шланг, обеспечив при этом надежное герметичное соединение. Затем нужно включить бензонасос и измерить объем топлива, поступившего в мерную посуду за 30 с; в зависимости от типа системы он составляет 0,75... 1,0 л. Если по каким-либо причинам включение бензонасоса без запуска двигателя затруднено, его можно проверить на работающем двигателе, так как количество топлива, потребляемого прогретым двигателем в режиме холостого хода, незначительно (практически все топливо перепускается обратно в бак). Однако в этом случае необходимо вынести мерную емкость из подкапотного пространства во избежание случайного воспламенения топлива.
Проверка регулятора давления выполняется в зависимости от системного давления. Если давление нормальное или пониженное, необходимо на двигателе, работающем в режиме холостого хода, снять вакуумный шланг с регулятора. Давление должно увеличиться на 0,05...0,06 МПа. Если этого не произошло, кратковременно пережимают шланг обратного слива. Увеличение давления топлива до 0,4...0,5 МПа свидетельствует о неисправности регулятора давления. Если при пережатии шланга обратного слива давление не возрастает, следует проверить производительность бензонасоса.
В моделях автомобилей последних лет выпуска резиновые шланги для подвода и слива топлива практически не применяются. Вместо них используются металлические трубки, соединенные с топливной магистралью. В этом случае рекомендуется отсоединить штатную трубку обратного слива и подсоединить на ее место специально подобранный или изготовленный штуцер с надетым на него резиновым шлангом необходимой длины, плотно закрепленным червячным хомутом. После такой замены можно опустить шланг в подходящую емкость (например, канистру) и, запустив двигатель, осуществлять кратковременное пережатие шланга, наблюдая за измеряемым давлением в топливной магистрали.
При повышенном системном давлении следует отсоединить от регулятора шланг обратного слива и временно подсоединить к нему подходящий штуцер с плотно надетым резиновым шлангом, опустив его в емкость. Если давление после запуска двигателя нормализуется, необходимо проверить бензопровод обратного слива. Если бензопровод не засорен и не помят, значит, неисправен регулятор давления.
Для контроля остаточного давления необходимо прогреть двигатель до рабочей температуры и выключить его. Ориентировочно можно руководствоваться следующим: после двадцатиминутной паузы давление в системе не должно быть менее 0,1 МПа. Более быстрое падение давления свидетельствует об утечке топлива, которая может происходить в регуляторе давления, обратном клапане бензонасоса, а также в пусковой и основных форсунках.
Проверка пусковой форсунки и термовыключателя. Для проверки работы пусковой форсунки необходимо измерить напряжение на подсоединенном к ней разъеме при прокрутке коленчатого вала холодного (<20 °С) двигателя. Напряжение должно быть не ниже 8...9 В. Если оно существенно меньше или равно нулю, следует проверить сопротивление проводников, подходящих к форсунке, и сопротивление контактов термовыключателя. При значениях, близких к нулю, проверяют поступление напряжения питания к пусковой форсунке от реле бензонасоса или системного реле при прокрутке стартером. В случае отсутствия напряжения следует заменить реле.
Если при прокрутке стартером на форсунку подается нормальное напряжение питания, необходимо визуально проверить распыление топлива форсункой. Для этого форсунку следует снять с впускного коллектора, не отсоединяя от нее бензопровод, и опустить в прозрачную емкость. Если при прокрутке стартером факел топлива отсутствует, проверяют наличие системного давления на бензопроводе форсунки. Когда давление в норме, форсунку следует заменить, в противном случае - проверить бензопровод пусковой форсунки.
В большинстве электронных систем распределенного впрыска пусковая форсунка может включаться путем коммутации на «массу» транзисторным ключом блока управления. В этом случае термовыключатель не применяется. Отсутствие напряжения питания на клеммах пусковой форсунки при пуске холодного двигателя говорит либо об обрыве или коротком замыкании в проводке, либо о неисправности в цепи датчика температуры охлаждающей жидкости или блока управления (прежде всего необходимо проверить наличие напряжения питания блока).
Проверка форсунок. Работоспособность электромагнитных форсунок распределенного впрыска в первом приближении может быть проверена по внешним признакам их работы. Сначала производится проба на вибрацию. Регулярное открытие и закрытие клапана работающей форсунки создает равномерную вибрацию, которую можно определить на ощупь или с помощью стетоскопа, а при его отсутствии - шлангом или деревянным бруском. Равномерная вибрация свидетельствует об исправной форсунке, а отсутствие вибрации или перебои в ней указывают на отклонения в работе проверяемой форсунки. Работоспособность форсунки можно определить при отключении ее на холостом ходу отсоединением ее электропитания. При исправно работающей форсунке частота вращения коленчатого вала не должна измениться. Однако следует иметь в виду, что на некоторых автомобилях устанавливается стабилизатор холостого хода, который необходимо отключать во время указанной проверки. В случае обнаружения отклонения работы форсунки в первую очередь следует проверить состояние соленоидной обмотки. Для этого необходимо определить ее сопротивление и убедиться в отсутствии обрыва. Номинальное сопротивление должно соответствовать данным фирмы-изготовителя; если таких данных нет, сопротивления проверяемых форсунок можно сравнить между собой.
Следует проверять также герметичность и производительность форсунок. Для проверки герметичности необходимо установить проверяемые форсунки в емкость, подать на них рабочее напряжение и выключить. Из распылителей форсунки в течение одной минуты не должно вытекать более одной капли топлива. Производительность форсунок проверяют по объему топлива, вытекающего из форсунки (176 см3/мин - «LE-Джетроник»), Угол конуса распыла должен быть около 30°. При проверке необходимо использовать мензурки с делениями.
Очистка форсунок. Очищать форсунки можно как со снятием их с двигателя, так и непосредственно на работающем двигателе. Эффективная очистка снятых с двигателя форсунок возможна лишь на специальных ультразвуковых установках. В условиях небольших мастерских это можно сделать, подавая в форсунку под давлением 0,5... 1,0 МПа спирт или жидкость для очистки карбюраторов, хотя эффективность этого метода невысока. Для очистки форсунок на работающем двигателе применяются автономные устройства как замкнутого, так и одностороннего цикла, подающие специальный состав в топливную магистраль под необходимым давлением. Штатные бензопроводы (как подающий, так и обратного слива) при этом отсоединяются, а бензонасос отключается, чтобы не переносить растворенные отложения из насоса и топливного бака к форсункам. Эффективность очистки этим методом полностью определяется свойствами состава и лежит в пределах 60...90 %.
Билет №15
1. Трудоемкость - это затраты труда на выполнение в заданных
условиях операции или группы операций ТО или ремонта. Трудоемкость измеряется в нормо-единицах (человеко-часах, человеко-минутах).
Нормативная трудоемкость является официальной юридической
нормой, принятой на данном предприятии, фирме и т.д., используется для определения численности исполнителей; оплаты труда исполнителей (тарифная ставка, руб./ч); расчетов с клиентурой.
Фактическая трудоемкость - затраты труда на выполнение конкретной операции конкретным исполнителем является случайной величиной и может отличаться от нормативной.
В общем виде технология представляет собой совокупность знаний о способах и средствах изменения или обеспечения.
Норма трудоемкости tн складывается из следующих составляющих:
tн = (tоп + tп.з + tобс + tотд)К
Оперативное время tоп, подготовительно-заключительное время tп.з, время обслуживания рабочего места tобс, время на отдых и личные надобности tотд, коэффициент повторяемости К.
Коэффициент повторяемости К учитывает вероятность выполнения,
помимо контрольной, и исполнительской части операции.
Для определения фактического времени (трудоемкости выполнения
операций) ТО и ремонта используются различные методы нормирования.
При использования метода микроэлементных нормативов (МЭН):
- операции ТО и ремонта разбивают на простейшие движения и действия оператора (взять предмет на расстоянии 1 м массой 5 кг и перенести его на расстояние 3 м и т.д.);
- эти простейшие движения (их порядка 100-150) нормируют в
относительных или абсолютных единицах – микроэлементных нормативах, содержащихся в справочниках;
- все микроэлементные нормативы, составляющие определенную
операцию, суммируются и определяется микроэлементная норма времени операции;
- определяют фактическую норму времени.
2. А\м двигатели могут работать на сжатом и сжиженном газе. Компоновоч. схема системы пит. при работе на сжатом газе: баллон ‑ подогреватель ‑ редуктор высокого давл. ‑ редуктор низкого давл. ‑ смеситель-карбюратор.
При работе на сжиженном газе компоновочная схема такая: баллон ‑ испаритель ‑ редуктор низкого давления ‑ смеситель-карбюратор. Каждый двигатель, работающий на газе, имеет дополнительно обычную бензиновую систему как резервный вариант.
Система питания двигателей, работающих на сжатом газе. Входящие в состав системы баллоны выполнены из стали и рассчитаны на рабочее давление 19,6 МПа. Вместимость их 50 л, масса 93 кг. Вентили используют для перекрытия магистралей при неработающем двигателе. Подогреватель газа служит для предотвращен возможного замерзания влаги, находящейся в газе. Он выполнен в виде нескольких витков газопровода высокого давления на выпускном коллекторе.
Газовый редукт. высокого давления (ГРВД) служит для снижения давлен. газа до 1,2 МПа. Газовый редуктор низкого давления (ГРНД) снижает давление до рабочего значения, необходимого для подачи в смеситель (0,085-0,08 МПа).
К ГРНД газ поступает через электромагнитный клапан-фильтр, который при выключении зажигания перекрывает подачу газа.
Газовый смеситель-карбюратор служит для приготовления горючей смеси при работе на газе и бензине. Смеситель-карбюратор выполнен на базе основного карбюратора. На основном режиме средних нагрузок газ поступает от редуктора через открытый под действием разрежения в диффузорах обратный клапан в газовые форсунки и далее в двигатель. При полной нагрузке экономайзер подает дополнительное количество газа.
При работе на холостом ходу газ поступает за дроссель. Общее количество газа, подаваемого в систему холостого хода, регулируется винтом.
Система питания двигателей, работающих на сжиженном газе. Баллоны общей вместимостью 225 л рассчитаны на давление 1,6 МПа. Они имеют расходные вентиля для парообразной и жидкой фаз газа, предохранительный клапан, манометры. Магистральный вентиль служит для отключения баллона.
Испаритель обеспечивает перевод газа из жидкого состояния. По шлангам подходит вода из системы охлаждения. Фильтр улавливает смолистые вещества и серу. Он может быть установлен отдельно или в газовом редукторе. Газовый редуктор снижает давление до 0,1 МПа. Устройство его аналогично ГРНД системы для сжатого газа. Дозатор и смеситель образует горючую смесь, которая поступает в двигатель. Резервный бак предусмотрен для запаса бензина. Манометры позволяют контролировать давление в баллоне и редукторе.
3. Проверка аккумуляторных батарей заключается в определении уровня электролита, его плотности и напряжения на каждом элементе. Визуально устанавливают степень загрязнения аккумулятора, окисление клемм, наличие трещин.
Уровень электролита определяют мерной стеклянной трубкой диаметром 3...5 мм с двумя отметками на уровне 10 и 15 мм. Трубку опускают в заливное отверстие и верхний конец ее закрывают пальцем. Столбик электролита в поднятой трубке характеризует его высоту над предохранительным щитком. Нормальным следует считать уровень электролита, находящийся между указанными отметками на трубке. При отсутствии стеклянной трубки можно использовать чистую эбонитовую или деревянную палочку. В современных аккумуляторных батареях, имеющих прозрачный корпус, уровень электролита можно определить визуально.
Плотность электролита проверяют с помощью денсиметров. Они бывают двух видов: с непрерывной шкалой (от 1,10 до 1,30 г/см3) и с отдельными пластинами для измерения определенной плотности. Наконечник денсиметра опускают в наливное отверстие аккумулятора, засасывают электролит с помощью резиновой груши и по делениям поплавка или отдельным пластинам, помещенным в стеклянную колбу, определяют его плотность. Справочные данные о плотности электролита приводятся для температуры +15 °С, поэтому при определении плотности для другой температуры необходимо вносить поправку (0,0007 г/см3 на каждый градус). Ее прибавляют, если температура превышает 15 °С, и вычитают при более низкой температуре.
Напряжение на каждом элементе измеряют с помощью нагрузочной вилки типа Э108. Для этого устанавливают нагрузочное сопротивление, соответствующее емкости батареи, и острие контактной ножки и штыря с учетом полярности в течение 5 с прижимают к выводным штырям. При напряжении, меньшем 1,6 В, батарею следует подзарядить. При зарядке аккумуляторной батареи положительный ее вывод подсоединяют к клемме «+» зарядного устройства, а отрицательный - к клемме «-». Зарядка производится током силой, равной 0,1 номинальной емкости батареи, при температуре электролита не выше 30 °С в условиях холодного и умеренного климата и не более 35 °С при жарком и теплом климате.
Батарею заряжают до тех пор, пока не начнется обильное газовыделение во всех аккумуляторах («кипение») и в течение 2 ч напряжение и плотность электролита будут оставаться постоянными. Во время зарядки периодически (через каждые 2 ч) необходимо проверять напряжение, плотность и температуру электролита и следить за тем, чтобы температура не превышала 45 °С (при жарком и теплом климате - до 50 °С). Если она окажется выше, зарядный ток следует уменьшить вдвое на время, необходимое для снижения температуры до 30...35 °С, или временно отключить до охлаждения до 30 °С.
Если в конце зарядки плотность электролита (с учетом температурной поправки) будет отличаться от нормы, ее корректируют, доливая дистиллированную воду при превышении нормы и кислоту плотностью 1,4 г/см3, если плотность ниже нормы. После корректировки зарядку нужно продлить на 30 мин до полного перемешивания электролита. Окончательно измерение уровня электролита производят через 30 мин после зарядки. Если уровень ниже нормы, в аккумулятор добавляют электролит такой же плотности, которая должна быть при полностью заряженном аккумуляторе, при избытке излишек удаляют резиновой грушей.
Общее напряжение аккумуляторной батареи и сила тока, потребляемого стартером от батареи, могут быть определены при комплексном диагностировании мотор-тестером.
Билет №16
1. Технологический процесс – совокупность операций, выполняемых планомерно и последовательно во времени и пространстве над а/м (агрегатом, узлом).
Трудоемкость - это затраты труда на выполнение в заданных
условиях операции или группы операций ТО или ремонта. Трудоемкость измеряется в нормо-единицах (человеко-часах, человеко-минутах).
Нормативная трудоемкость является официальной юридической
нормой, принятой на данном предприятии, фирме и т.д., используется для определения численности исполнителей; оплаты труда исполнителей (тарифная ставка, руб./ч); расчетов с клиентурой.
Фактическая трудоемкость - затраты труда на выполнение конкретной операции конкретным исполнителем является случайной величиной и может отличаться от нормативной.
В общем виде технология представляет собой совокупность знаний о способах и средствах изменения или обеспечения.
Операция - это комплекс последовательных действий по обслуживанию агрегата или группы агрегатов автомобиля (например, смена масла в картере двигателя, регулировка сцепления и др.).
Территория помещения, предназначенная для выполнения одной или
нескольких однородных работ или операций процесса ТО или ремонта, оснащенная приборами, приспособлениями, инструментами и другим оборудованием, называется рабочим постом.
Производственный участок на рабочем посту, обслуживаемый одним
рабочим, называется рабочим местом.
2. Главная передача служит для увеличения крутящего момента и изменения его направления под прямым углом к продольной оси автомобиля. С этой целью главную передачу выполняют из конических шестерен. В зависимости от числа шестерен главные передачи разделяют на одинарные конические, состоящие из одной пары шестерен, и двойные, состоящие из пары конических и пары цилиндрических шестерен. Одинарные конические, в свою очередь, подразделяют на простые и гипоидные передачи.
Одинарные конические простые передачи применяют преимущественно на легковых автомобилях и грузовых автомобилях малой и средней грузоподъемности. В этих передачах ведущая коническая шестерня соединена с карданной передачей, а ведомая с коробкой дифференциала и через механизм дифференциала с полуосями.
Для большинства автомобилей одинарные конические передачи имеют зубчатые колеса с гипоидным зацеплением. Гипоидные передачи по сравнению с простыми обладают рядом преимуществ; они имеют ось ведущего колеса, расположенную ниже оси ведомого, что позволяет опустить ниже карданную передачу, понизить пол кузова легкового автомобиля. Вследствие этого снижается центр тяжести и повышается устойчивость автомобиля. Кроме того, гипоидная передача имеет утолщенную форму основания зубьев шестерен, что существенно повышает их нагрузочную способность и износостойкость. Но это обстоятельство обусловливает применение для смазки шестерен специального масла (гипоидного), рассчитанного для работы в условиях передачи больших усилий, возникающих в контакте между зубьями шестерен.
Двойные главные передачи устанавливают на автомобилях большой грузоподъемности для увеличения общего передаточного числа трансмиссии и повышения передаваемого крутящего момента. В этом случае передаточное число главной передачи подсчитывается как произведение передаточных чисел конической и цилиндрической пар.
3. Генератор можно проверять мотор-тестером, оборудованным осциллографом, или отдельным осциллографом, а также непосредственно на автомобиле.
Проверка на стенде позволяет определять исправность генератора и соответствие его характеристик номинальным. У проверяемого генератора щетки должны быть хорошо притерты к контактным кольцам коллектора, а сами кольца - чистыми.
Для проверки следует установить генератор на стенд и выполнить соединения так, как показано на рис. 8.5. Включить электродвигатель стенда реостатом, установить на выходе генератора напряжение 13 В и довести частоту вращения ротора до 5000 об/мин. Дать генератору поработать в этом режиме не менее 10 мин, а затем измерить силу тока отдачи. У исправного генератора она должна быть не менее 55 А. Если измеренная сила тока отдачи меньше, это свидетельствует о неисправностях в обмотках статора и ротора, о повреждении вентилей. В этом случае необходима тщательная проверка обмоток и вентилей, чтобы определить место неисправности.
Напряжение на выходе генератора проверяют при частоте вращения ротора 5000 об/мин. Реостатом следует установить ток отдачи силой 15 А и измерить напряжение на выходе генератора, которое должно быть (14,1±0,5) В при температуре окружающего воздуха и генератора 15…35 °С. Когда напряжение не укладывается в указанные пределы, необходимо заменить регулятор напряжения новым, заведомо исправным, и повторить проверку. Если напряжение окажется нормальным, значит, старый регулятор напряжения поврежден и его необходимо заменить. В случае если напряжение по-прежнему не будет укладываться в указанные выше пределы, следует проверить обмотки и вентили генератора.
Билет №17
1. Эффективность технической эксплуатации автомобилей (автомобильных парков) и транспортного процесса характеризуется набором комплексных показателей, наиболее полно характеризующих организацию работ в АТП. К ним в первую очередь относятся коэффициенты выпуска, технической готовности и использования подвижного состава.
Коэффициент выпуска - представляет собой отношение числа дней нахождения автомобиля (парка автомобилей) в эксплуатации к календарному числу дней за рассматриваемый период, т. е. это доля календарного времени, в течение которого автомобиль (парк автомобилей) осуществлял транспортную работу.
Коэффициент технической готовности - представляет собой отношение числа дней нахождения автомобиля (парка автомобилей) в эксплуатации к сумме числа дней, кода он находился в работоспособном состоянии и был готов выполнять транспортную работу, т. е. это доля календарного времени, в течение которого автомобиль (парк автомобилей) выполняет и технически готов выполнять транспортную работу.
2. Тормозные краны предназначены для управления подачей сжатого воздуха, поступающего из ресиверов к исполнительным органам тормозной системы автомобиля или автопоезда, и обеспечивают следящее действие системы.
По числу обслуживаемых контуров привода различают одно-, двух-, трех- и многосекционные тормозные краны. Управление тормозным краном осуществляется механически с помощью рычагов и тяг или гидроприводом.
Основные элементы тормозного крана: впускной (воздушный) и выпускной (атмосферный) клапаны, следящий механизм. Следящий механизм крана ‑ это элемент, обеспечивающий изменение давления воздуха в его полости в зависимости от входного воздействия. Этот механизм состоит из упругого элемента (пружины или резиновой втулки) и чувствительного элемента (поршня или диафрагмы).
В отторможенном состоянии атмосферный клапан открыт и тормозная камера сообщается с атмосферой. При этом клапан сжатого воздуха закрыт. Нажатие на тормозную педаль приводит к перемещению вправо полого штока, закрывающего клапан. Одновременно открывается клапан, сообщая тормозную камеру с ресивером. Давление в тормозной камере пропорционально усилию на тормозной педали. Следящее действие обусловлено равновесием сил, действующих на поршень при постоянном усилии на тормозной педали.
Двухсекционный тормозной кран прямого действия имеет две последовательно расположенные секции, плоские резиновые клапаны и поршневой следящий механизм с резиновой втулкой. Выводы крана соединены с ресиверами и с тормозными камерами автомобиля. При нажатии на педаль тормоза усилие передается через систему рычагов и тяг рычагу крана и далее через толкатель и резиновую втулку верхнему следящему поршню. Подвижное седло клапана, перемещаясь вниз вместе с поршнем, закрывает выпускное окно этого клапана и перекрывает сообщение через вывод тормозных камер с атмосферой, а затем отрывает клапан от неподвижного седла. Сжатый воздух через вывод и открытый клапан поступает в полость крана и далее к выводу. К нему, как правило, подключается магистраль управления тормозами передней оси автомобиля, а также трубопровод, соединяющий эту магистраль с одной из управляющих полостей крана управления тормозами прицепа с двухпроводным приводом. Давление в верхней полости крана возрастает до тех пор, пока сила нажатия на резиновую втулку не уравновесится усилием, действующим на следящий поршень. В этом случае клапан садится на неподвижное седло, и воздух в тормозные камеры не поступает.
3. В процессе эксплуатации могут происходить обрывы обмоток стартера, отказы тягового реле, межвитковые замыкания, окисление контактов, щеток, отказы муфты свободного хода, изнашивание втулок подшипников, заедание рычага привода.
При включении стартера тяговое реле не срабатывает, якорь не вращается: Неисправна или полностью разряжена аккумуляторная батарея - Зарядить или заменить батарею; Сильно окислены полюсные выводы аккумуляторной батареи и наконечники проводов, слабо затянуты наконечники - Зачистить полюсные выводы батареи и наконечники проводов, смазать техническим вазелином и затянуть; Неисправна контактная часть выключателя зажигания, не замыкаются контакты «30» и «50» - Заменить контактную часть; Заедание якоря тягового реле - Снять реле, проверить и обеспечить легкость перемещения якоря.
При включении стартера тяговое реле срабатывает, но якорь не срабатывает или вращается недостаточно интенсивно: Разряжена аккумуляторная батарея - Зарядить или заменить батарею; Окислены полюсные выводы аккумуляторной батареи и наконечники соединительных проводов, ослабла затяжка крепления наконечников проводов - Зачистить полюсные выводы батареи и наконечники проводов. Смазать их техническим вазелином и обеспечить надежную затяжку крепежных элементов; Окислены контактные болты тягового реле стартера - Зачистить контактные болты; Окислены наконечники проводов и ослабло их крепление на контактных болтах тягового реле стартера - Зачистить наконечники и затянуть их крепление; Подгорание коллектора, зависание щеток или их большой износ - Зачистить коллектор, промыть щеткодержатели, заменить щетки; Обрыв в обмотке статора или якоря - Заменить катушку статора или якоря; Замыкание между пластинами коллектора, межвитковое замыкание в обмотках якоря либо статора или замыкание их на «массу» - Заменить неисправные детали; Замыкание изолированного щеткодержателя плюсовой щетки на «массу» - Устранить замыкание или заменить заднюю крышку статора; Масло в картере двигателя по вязкости не соответствует сезону - Заменить масло рекомендуемым для данного сезона.
При включении стартера якорь вращается, а коленчатый вал двигателя не прокручивается: Пробуксовка муфты свободного хода - Проверить стартер на стенде, муфту заменить; Поломка рычага выключения муфты или выскакивание его оси - Заменить рычаг или установить на место его ось; Поломка поводкового кольца муфты или буферной пружины - Заменить муфту; Заедание или тугое перемещение привода на винтовой нарезке вала якоря стартера - Промыть и зачистить нарезку вала, смазать ее моторным маслом.
Повышенный шум стартера при вращении якоря: Чрезмерный износ втулок подшипников или шеек вала якоря - Заменить втулки или крышки стартера, заменить якорь; Ослабло крепление стартера или оно осуществлено с перекосом, поломана крышка со стороны привода - Проверить правильность установки стартера, подтянуть крепление, заменить дефектную крышку; Ослабло крепление полюса в корпусе стартера (якорь задевает при вращении за полюс) - Затянуть и зачеканить винт крепления полюса; Повреждены зубья шестерни привода или венца маховика двигателя - Зачистить или заменить дефектные детали.
Стартер не отключается после пуска двигателя: Заедание рычага привода - Выявить причину, устранить ее или заменить рычаг; Заедание привода на валу якоря стартера или слипание контактов тягового реле - Немедленно остановить двигатель, снять и разобрать стартер и устранить причину заедания. Зачистить шлицы и смазать их моторным маслом; Ослабли или поломаны возвратные пружины муфты свободного хода либо тягового реле стартера - Заменить муфту или реле; Заедание якоря тягового реле - Устранить заедание или заменить реле; Неисправна контактная часть выключателя, не размыкаются контакты «30» и «50» - Проверить правильность замыкания контактов при различных положениях ключа, неисправную контактную часть заменить; Поломана возвратная пружина выключателя зажигания - Заменить дефектный выключатель.
Билет №18
1. Характерными неисправностями являются: нарушение герметичности и течь топлива, особенно топливопроводов высокого давления; загрязнение воздушных и особенно топливных фильтров; попадание масла в турбонагнетатель; износ и разрегулировка плунжерных пар насоса высокого давления; потеря герметичности форсунками и снижение давления начала подъема иглы; износ выходных отверстий форсунок, их закоксовывание и засорение. Эти неисправности приводят к изменению момента начала подачи топлива, неравномерности работы топливного насоса по углу поворота коленчатого вала и количеству подаваемого топлива, ухудшению качества распыливания топлива, что прежде всего вызывает повышение дымности отработавших газов и приводит к незначительному повышению расхода топлива и снижению мощности двигателя на 3-5%.
Контроль системы питания включает в себя: проверку герметичности системы и состояния топливных и воздушных фильтров, проверку топливоподкачивающего насоса, насоса высокого давления и форсунок.
Негерметичность части системы, находящейся под высоким давлением, проверяется визуально по подтеканию топлива при работающем двигателе. Негерметичность впускной части (от бака до топливоподкачивающего насоса), приводящая к подсосу воздуха и нарушению работы топливоподкачивающей аппаратуры, проверяют с помощью специального прибора-бачка. Часть магистрали, находящейся под низким давлением, можно проверить на негерметичность и при неработающем двигателе путем опрессовки ручным топливоподкачивающим насосом.
Состояние сухих воздушных фильтров, устанавливаемых на всех последних моделях автомобилей, проверяют по разрежению за фильтром при помощи водяного пьезометра (должно быть не более 700 мм.вод.ст.). Состояние топливных фильтров можно проверить в первом приближении на холостом ходу двигателя по давлению за фильтром (допускается не менее 150 кПа), а более точно ‑ по перепаду давлений перед фильтром и за ним (не более 20 кПа). Более низкое давление свидетельствует также о неисправной работе топливоподкачивающего насоса.
Контроль насоса высокого давления и форсунок непосредственно на автомобиле проводят при превышении двигателем норм по дымности и с целью выявления и устранения неисправностей. Наибольшее распространение получил метод, основанный на анализе изменения давления, фиксируемого при помощи специального накладного (зажимного) датчика, устанавливаемого у форсунки на нагнетательный топливопровод.
Монтаж насоса высокого давления на двигателе производят при помощи моментоскопа (стеклянной трубки с внутренним диаметром 1,5-2,0 мм), устанавливаемого на выходном штуцере первой или предыдущей по порядку работы секции насоса, по появлению топлива в котором производится закрепление муфты привода таким образом, чтобы угол опережения составлял 16-19º до ВМТ первого цилиндра. Выполнение указанных работ обеспечивает (при правильной регулировке клапанов и хорошей компрессии в цилиндрах двигателя) минимальную дымность и максимальную экономичность работы дизеля.
2. Если передние и задние оси постоянно включены или заблокированы, то при движении машины на повороте, когда колеса идут по дугам разного радиуса, или при возможной разнице диаметров колес может возникнуть кинематическое рассогласование (кинематическое несоответствие). Это создает циркуляцию так называемой паразитной мощности.
При кинематическом несоответствии передние колеса могут проскальзывать относительно дороги и на них действует отрицательная касательная сила (горизонтальная реакция дороги, направленная против движения машины). Эта сила образует на передних колесах вращающий момент, который передается через передний мост, карданный вал, раздаточную коробку и задний карданный вал на задние колеса где складывается с вращающим моментом, поступающим от двигателя. Оба момента образуют суммарную положительную касательную силу тяги, вызывающую движение машины. Часть касательной силы задних колес через остов машины передается на передние колеса и преодолевает сопротивление касательной силы передних колес.
Циркулирующая таким образом мощность не создает положительной работы, а дополнительно нагружает детали трансмиссии, вызывая изнашивание шин, на что расходуется дополнительная мощность. Чтобы избежать этого, в раздаточную коробку вводят межосевой дифференциал, который позволяет колесам передних и задних осей вращаться с разной скоростью. Если дифференциала нет, то при движении по дороге с твердым покрытием необходимо выключать передний мост.
Такое же явление наблюдается и в ведущих колесах одной оси. В этом случае устанавливают межколесный дифференциал.
3. Принцип работы стробоскопических приборов основан на том, что если в строго определенные моменты времени направлять на вращающуюся или движущуюся возвратно-поступательно деталь короткий импульс света (примерно 1:5000 с), то вследствие инерции человеческого зрения деталь будет казаться неподвижной.
При проверке угла установки зажигания высоковольтный провод стробоскопа подсоединяют с помощью накладного датчика к высоковольтному проводу, идущему к свече первого цилиндра, а пружинные зажимы - к цепи низкого напряжения. Запустив двигатель на минимальной частоте вращения коленчатого вала, луч от неоновой лампы стробоскопа, вспыхивающий синхронно с вращением коленчатого вала, направляют на шкив. При этом трубка вакуумного регулятора должна быть отсоединена. Если угол опережения зажигания установлен правильно, то вследствие стробоскопического эффекта подвижная метка будет казаться неподвижной и находиться напротив неподвижной метки.
При несовпадении меток следует ослабить винт скобы крепления распределителя и поворачивать его корпус вправо или влево до совпадения меток, после чего винт скобы затянуть. Для проверки центробежного регулятора прерывателя-распределителя плавно увеличивают частоту вращения коленчатого вала. Подвижная метка при этом должна плавно смещаться в сторону, противоположную направлению его вращения. При неисправной работе метка будет сдвигаться рывками или оставаться неподвижной.
Для более точной проверки работоспособности центробежного регулятора опережения зажигания постепенно увеличивают частоту вращения коленчатого вала и определяют угол опережения относительно первоначального значения, в зависимости от частоты вращения коленчатого вала. Полученные данные сравнивают с характеристикой прерывателя (рис. 9.3, а). Вакуумный регулятор опережения зажигания проверяют при частоте вращения коленчатого вала 2000...2500 об/мин с отсоединенной трубкой. После присоединения трубки вакуумного регулятора подвижная метка должна отклониться в сторону, противоположную направлению его вращения.
Точная проверка вакуумного регулятора опережения зажигания производится при плавном увеличении разрежения.
Билет №19
1. Текущий ремонт
При этом виде ремонта необходимо заменять и восстанавливать изношенные или повреждённые детали. Речь идёт об отдельных, достигших предельного износа, или уже отказавшиеся работать элементах, кроме базовых. То есть текущему ремонту не подлежат: блок цилиндров в моторе; задний мост — в коробке передач; картер — в механизме руля; поперечина подвески или балка переднего моста; корпус — в кузове; продольные балки — в раме. При текущем ремонте меняют и восстанавливают детали, отдельные агрегаты и узлы. Также возможно выполнение других операций для устранения неисправностей.
Средний ремонт
Если же предполагается выполнение более сложной работы, то потребуются другие виды ремонта автомобилей. Средний вариант включает в себя замену или восстановление повреждённых узлов, агрегатов и отдельных элементов с проверкой технического состояния и устранения всех остальных неисправностей, выявленных при проверке. Выполняются и специально предусмотренные работы по техническому обслуживанию. Средний ремонт включает в себя замену от двух и более агрегатов. Но общее их число не должно превышать половины базовых.
Капитальный ремонт
В основные виды ремонта автомобилей входит и капитальный ремонт. Его осуществляют для восстановления исправности транспортного средства. При этом меняются и восстанавливаются любые части, в том числе базовые. Если выполняется капитальный ремонт агрегата, то это обеспечивает его полное восстановление, в соответствии с техусловиями. Сборка и испытания проводятся при соблюдении норм и правил техобслуживания. Агрегат направляют в капремонт в тех случаях, когда базовую деталь необходимо восстановить. Если её отремонтировать и восстановить не представляется возможным посредством текущего ремонта, производится его полная разборка. Капитальный ремонт восстанавливает работоспособность агрегата, согласно техусловиям на ремонт, сборку и испытание. Его делают при достижении установленного пробега или при соблюдении правил техобслуживания, текущего ремонта и эксплуатации. Таковы главные виды ремонта автомобилей.
2. Рулевое управление состоит из рулевого механизма и рулевого привода. Рулевой механизм служит для передачи усилия от водителя к рулевому приводу и для увеличения вращающего момента, приложенного к рулевому колесу.
Рулевая трапеция является частью рулевого привода, ее образуют поворотные рычаги и поперечная тяга вместе с балкой моста. Чтобы автомобиль двигался на повороте без бокового скольжения колес, все колеса должны совершать качение по дугам, описанным из одного центра, лежащего на продолжении задней оси автомобиля. При этом передние управляемые колеса должны поворачиваться на разные углы: внутреннее поотношению к центру поворота на больший угол, наружное — на меньший угол. Такая схема поворота достигается применением в рулевом приводе трапеции с шарнирными соединениями.
В зависимости от расположения относительно оси вращения колес различают передние и задние рулевые трапеции. Обычно рулевую трапецию располагают сзади управляемых колес. По конструкции рулевые трапеции могут быть неразрезные и разрезные.
Автомобили с зависимой подвеской имеют неразрезную поперечную тягу. При независимой подвеске эту тягу выполняют разрезной, состоящей из двух или трех звеньев. Это обеспечивает возможность независимого перемещения управляемых колес. Для регулировки схождения колес тяги имеют резьбовые наконечники.
3. Пригодность нажимного диска в сборе с кожухом к дальнейшей эксплуатации может быть определена с помощью простого приспособления, представляющего собой основание, имитирующее маховик двигателя. Под нажимной диск устанавливают кольцо, толщина которого соответствует толщине ведомого диска. Толщину кольца выбирают на основании справочных данных на конкретный автомобиль. Для легковых автомобилей производства России и Украины она составляет 8,2...8,3 мм.
Сначала проверяют нажимную пружину. Для этого, закрепив на основании кожух сцепления, делают 3...4 хода выключения, прикладывая нагрузку не более 140 кгс на упорный фланец (лепестки) нажимной пружины. Ходу выключения 7,5...8,0 мм должно соответствовать перемещение нажимного диска не менее 1,4 мм. Замеряют также расстояние от основания приспособления до плоскости концов лепестков пружины. Оно должно находиться в пределах 29...35 мм в зависимости от модели двигателя, предельное расстояние 38...43 мм.
Лепестки тарельчатой пружины должны лежать на одной высоте с точностью ±0,5 мм. Выгнутые концы выпрямляют с помощью пластины с узким пазом или используют специальное приспособление. Проверяют также износ внутренних концов тарельчатой пружины. На них не должно быть видно значительно вытертых мест. По краям нажимной пружины допускается износ до 0,3 мм. Нажимной диск необходимо проверить на неплоскостность, которая не должна превышать 0,2...0,3 мм.
Разбирать ведомый диск сцепления и заменять его детали, исключая фрикционные накладки, не рекомендуется. При износе или поломке деталей ведомого диска (кроме износа рабочих поверхностей фрикционных накладок), потере упругости пружинных пластин, короблении ведомого диска (если его не удается выпрямить), наличии трещин на пластине демпфера или ведомом диске диск в сборе необходимо заменить новым.
Фрикционные накладки ведомого диска сцепления заменяют новыми при появлении растрескиваний. Износ считается максимальным, если расстояние между заклепкой и рабочей поверхностью меньше 0,2 мм или углубления головок фрикционного материала меньше 0,3 мм. Накладки меняют при неравномерном износе и односторонних задирах, а также при сильном замасливании, если не удается очистить замасленные поверхности уайт-спиритом или бензином.
При осмотре диска проверяют состояние торцов и наружного диаметра пружин демпфера. По торцам и наружному диаметру пружины демпфера не должны иметь следов натиров и выработки глубиной более 2 мм. В запасные части и торговую сеть фрикционные накладки поступают вместе с заклепками для соответствующей модели автомобиля.
Ведомый диск после приклепывания к нему пластин проверяют на торцевое биение и дисбаланс.
Дисбаланс ведомого диска не должен превышать 150 г-см. При отсутствии станка для балансировки ее можно выполнить на двух горизонтально расположенных призмах, на которых устанавливается оправка. Повышенный дисбаланс устраняется установкой грузиков, которые укрепляют в отверстиях ведомого диска.
Применяемые в приводе сцепления защитные резиновые чехлы и демпферы (буферы) независимо от их технического состояния рекомендуется заменять новыми через 150 тыс. км пробега (или через 5 лет эксплуатации, если к этому сроку пробег меньше указанного) из-за старения и усталостных разрушений резины.
При обнаружении заедания при перемещении троса в оболочке рекомендуется заложить в наконечники оболочки смазку «Литол-24» и произвести 10... 15 перемещений троса в оболочке из одного крайнего положения в другое.
Билет №20
1. Техническое обслуживание в основной период эксплуатации подразделяется на следующие виды:
· ежедневное обслуживание (ЕО);
· первое техническое обслуживание (ТО-1);
· второе техническое обслуживание (ТО-2);
· сезонное техническое обслуживание (СТО).
Ежедневное техническое обслуживание (ЕО):
1)При необходимости вымыть автомобиль и произвести уборку кабины и платформы.; Проверить
: состояние запоров бортов платформы; состояние буксирного прибора и шлангов подсоединения тормозной системы прицепа; состояние колес и шин; состояние привода рулевого управления (без применения специального приспособления); действие приборов освещения и световой сигнализации;работу стеклоочистителей. 2)Устранить неисправности. 3)Довести до нормы: уровень масла в картере двигателя; уровень жидкости в системе охлаждения. 4)Слить конденсат из воздушных баллонов тормозной системы (по окончании смены).
Техническое обслуживание ТО1.
1) Вымыть автомобиль. 2) Внешним осмотром элементов и по показаниям соответствующих приборов автомобиля проверить исправность тормозной системы, устранить неисправности. 3) Закрепить гайки колес. 4) Отрегулировать величину хода штоков тормозных камер. 5) Слить отстой из фильтров грубой и тонкой очистки топлива. 6) При температуре ниже 5° С заменить спирт в предохранителе от замерзания. 7) Довести до нормы: давление в шинах; уровень масла в бачке гидроусилителя руля; уровень электролита в аккумуляторных батареях. 8) Смазать: шкворни поворотных кулаков; шарниры рулевых тяг; пальцы передних рессор; втулки валов разжимных кулаков; регулировочные рычаги тормозных механизмов; оси передних опор кабины. 9) Дополнительно по самосвалу и тягачу проверить: герметичность и состояние трубопроводов и узлов механизма подъема платформы; состояние опорно-сцепного устройства; целостность прядей страховочного троса в зоне контакта с оттяжной кружиной. 10) Устранить неисправности. 11) Довести до нормы уровень масла в бачке гидроподъемника. 12) Промыть масляный фильтр сливной магистрали механизма подъема платформы. 13) Смазать опорные пальцы самосвала,
Техническое обслуживание ТО-2.
1) Вымыть автомобиль, обратив особое внимание на агрегаты и системы, обслуживание которых проводится. 2) Двигатель. а) Проверить: состояние и действие жалюзи радиатора; состояние и действие троса ручного управления подачей топлива; состояние и действие троса останова двигателя; состояние пластины тяги регулятора (в окне пластины не должно быть глубоких канавок). б) Устранить неисправности. в) Закрепить: поддон картера двигателя; передние и задние опоры двигателя. г) Отрегулировать: натяжение ремней генератора и водяного насоса; тепловые зазоры между стержнями клапанов и коромыслами клапанного механизма (предварительно проверив момент затяжки болтов головок цилиндров и гаек стоек коромысел). 3) Сцепление. а) Проверить: герметичность привода выключения сцепления; действие оттяжных пружин педали сцепления и рычага вала вилки выключения сцепления. б) Устранить неисправности. в) Отрегулировать свободный ход толкателя поршня главного цилиндра привода и свободный ход рычага вала вилки выключения сцепления. г) Закрепить пневмогидравлический усилитель. 4) Коробка передач. а) Проверить: состояние и действие троса крана управления делителем; герметичность коробки передач. б) Устранить неисправности. в) Отрегулировать зазор между торцом крышки и ограничителем хода штока клапана управления делителем. г) Закрепить десятиступенчатую коробку передач к поддерживающей поперечине и поперечину к раме. 5) Карданная передача. а) Проверить состояние и зазор в шарнирах карданных валов, устранить неисправности. б) Закрепить фланцы карданных валов. 6) Ведущие мосты. а) Проверить герметичность среднего и заднего мостов. б) Устранить неисправности. 7) Ходовая часть, подвеска, рама. а) Проверить: осевой свободный ход буксирного прибора; состояние амортизаторов (внешним осмотром); состояние реактивных штанг (внешним осмотром). б) Устранить неисправности. в) Закрепить: стремянки передних и задних рессор; болты отъемных ушков передних рессор; болты клеммовых зажимов пальцев передних рессор; стяжные болты задних кронштейнов передних рессор. г) При необходимости переставить колеса. 8) Передняя ось и рулевое управление. а) Проверить: шплинтовку гаек шаровых пальцев, сошки руля, рычагов поворотных кулаков (внешним осмотром);зазор в шарнирах рулевых тяг; зазор в шарнирах карданного вала руля; состояние шкворневых соединений (при вывешенных колесах). б) Устранить неисправности. в) Отрегулировать: величину схождения передних колес; свободный ход рулевого колеса; подшипники ступиц передних колес (при вывешенных колесах). 9) Тормозная система. а) Проверить: работоспособность тормозной системы манометрами по контрольным выводам; шплинтовку пальцев штоков тормозных камер. б) Устранить неисправности. в) Закрепить тормозные камеры и их кронштейны. г) Отрегулировать положение педали тормоза относительно пола кабины, обеспечив полный ход рычага тормозного крана. 10) Электрооборудование. а) Внешним осмотром проверить: состояние электропроводки (надежность крепления проводор скобами, отсутствие провисания, потертостей, налипания комьев грязи или льда); состояние и надежность крепления соединительных колодок выключателя массы, привода спидометра, общих колодок задних фонарей и подфарников, датчиков давления четвертого контура и включения блокировки мостов. б) Устранить неисправности. в) Закрепить электропровода к выводам стартера. г) Отрегулировать направление светового потока фар. д) Довести до нормы плотность электролита в аккумуляторных батареях. 11) Кабина, платформа. а) Проверить: состояние и действие упорно-ограничительного устройства кабины; работу стеклоочистителей; состояние и действие замков дверей; состояние сидений; действие системы отопления и устройства для обдува и обогрева ветрового стекла (в холодное время года); целостность сварного соединения кронштейна в стыке составных крыльев; состояние платформы. б) Устранить неисправности. в) Закрепить: рессоры и амортизаторы задней опоры кабины; оси опор рычагов торсионов. г) При необходимости отрегулировать положение рычагов торсионных валов.12) Смазочные, очистительные и заправочные работы. а) Заменить масло в системе смазки двигателя. б) Сменить фильтрующие элементы масляного фильтра. в) Заменить фильтрующие элементы фильтра тонкой очистки топлива. г) Промыть фильтр центробежной очистки масла. д) Промыть фильтр грубой очистки топлива. е) Снять и промыть фильтр насоса гидроусилителя рулевого управления. ж) Проверить показания индикатора засоренности воздушного фильтра, при необходимости очистить бумажный фильтрующий элемент воздушного фильтра. з) Смазать: подшипник муфты выключения сцепления; подшипники вала вилки выключения сцепления; опоры продольного вала рычага управления коробки передач; шарниры карданных валов среднего и заднего мостов; клеммы и перемычки аккумуляторных батарей; стебель крюка буксирного прибора. и) Довести до нормы уровень масла: в картере коробки передач; в картере среднего и заднего мостов. к) Довести до нормы уровень жидкости в главном цилиндре привода сцепления. л) Очистить от грязи сапуны коробки передач и мостов. м) Слить конденсат из пневматического усилителя сцеплеция. 13) Дополнительные работы по самосвалу и тягачу. а) Проверить: состояние и работу крана управления и клапана ограничения подъема платформы; стрелу прогиба страховочного троса; состояние и крепление пружин захватов, запорного кулака и пружины защелки седельного устройства. б) Устранить неисправности. в) Закрепить: передние кронштейны надрамника; стяжные болты надрамника; ловитель-амортизатор; амортизаторы платформы; коробку отбора мощности; масляный насос. г) Слить отстой из гидроцилиндра механизма опрокидывания платформы. д) Смазать опорную плиту седельного устройства тонким слоем солидола.
Дата добавления: 2018-11-24; просмотров: 300; Мы поможем в написании вашей работы! |
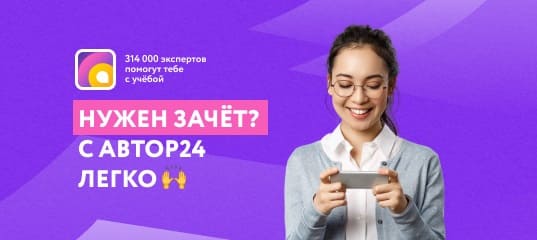
Мы поможем в написании ваших работ!