Анализ имеющегося металлорежущего оборудования.
При обследование и детальном изучение состояния парка металлорежущего оборудования по разработанным технологическим процессам изготовления корпусных деталей на базовом предприятии, выяснилось, что обработка корпусных и других деталей ведется в основном на универсальном оборудование, но морально и физически устаревшем. Следствие этого - многооперационность и трудоемкость изготовления за счет низких режимов резания, применения малых скоростей резания при небольших глубинах резания и подаче. Средний коэффициент загрузки оборудования составляет 0,59 , что объясняется низкой эффективностью его использования. Удельный вес рабочих - многостаночников в механическом производстве составляет - 30%, рабочих совмещающих профессии - 20%. Наряду с использованием прогрессивного оборудования типа 16К20ФЗС32, ИР 320 ПМФ4 ОДТ-50ш и др., применяются в основном (до 40%) модели оборудования, установленные в конце 50-ых, начала 60-ых годов (1К62, 6В11, РВ-22л, 6Н10, НС-12А, Тиль и т. д.), которые вследствие их износа, не могут обеспечить жестких требований по точности размеров, геометрии формы, получения заданных параметров по шероховатости поверхностей. Для обслуживания этих устаревших моделей станков содержится вспомогательные рабочие, что ведет к повышенной трудоемкости изготовления изделий, в устаревших моделях отсутствуют системы обильного охлаждения СОЖ, удаления стружки, смазывания и уборки станка, что также ведет к значительным потерям рабочего времени при их техническом обслуживание. Отсутствие действующих средств механизации автоматизации при транспортировке деталей, их складировании и контроле, ведет к удлинению производственного цикла изготовления деталей. Скопление большого количества универсальных станков на небольших площадях и их установка на жестких монолитных фундаментах, приводит к значительному шуму в процессе работы, а это, в свою очередь, вызывает утомляемость рабочих, снижает эффективность использования человеческого труда. Также снижается фондовая отдача оборудования, которую нельзя повысить только за счет экстенсивных факторов труда. Таким образом, анализ действующего металлообрабатывающего оборудования в механообрабатывающем производстве показывает, что прогрессивное оборудование составляет 15-20% от общего количества станочного парка.
|
|
Анализ применяющихся способов упрочнения и восстановления деталей машин.
Увеличение срока эксплуатации и износостойкости деталей машин путем упрочнения является важной задачей, решение которой способствует значительному увеличению их долговечности и обеспечивает экономию дорогих и дефицитных материалов, энергии, трудовых ресурсов. В машиностроении широко применяют разнообразные методы упрочнения, выбор которых зависит от свойств режущего и обрабатываемого материала, условий эксплуатации и экономической эффективности использования метода упрочнения, композиционные упрочняющие покрытия, лазерное упрочнение и легирование, электроискровое легирование, эпиломирование, магнитно-импульсная обработка.
|
|
Узлы изделий, работающих в «тяжелых» режимах трения, широко используют методы поверхностного упрочнения. На износостойкость пары трения влияет комплекс физико-механических характеристик: прочностные, пластические и твердость. На износостойкость особое влияние оказывает поверхностный слой, так как он воспринимает нагрузки и осуществляет контакт с внешней средой.
С другой стороны, поверхностные слои имеют и больше дефектов (поры, микротрещины, включения неординарного кристаллического строения и др.), чем весь объем детали.
В процессе изнашивания контактирующие поверхности должны успешно сопротивляться пластическим деформациям, срезу – сколу микрообъемов материала, внедрению твердых частиц (абразивные частицы из внешней среды, отделившиеся частицы или наросты при адгезии), а также воздействию агрессивных сред и температур.
|
|
Основное воздействие воспринимается тонким поверхностным слоем, а остальное сечение материала воспринимает лишь незначительную долю, вследствие инерционности материалов. Поэтому необходимо дифференцировать физико-механические свойства поверхностных слоев и остального сечения, что достигается различными методами поверхностного упрочнения. Методы, при этом за критерий оценки упрочняемых слоев принимаем твердость – единственную характеристику материала, получаемую методами неразрушающего контроля.
Применяемость методов поверхностного упрочнения деталей в зависимости от твердости упрочненных поверхностей.
№ п/п | Методы упрочнения | Твердость, МПа |
1 | Поверхностное пластическое деформирование (ППД) | 3000 - 5500 |
2 | Термическая обработка (ТО) | 5500 - 7600 |
3 | Химико-термическая обработка (ХТО) | 5700 - 20000 |
4 | Борирование | 20000 - 22000 |
5 | Фрикционно-диффузионное упрочнение | 11000 - 13000 |
6 | Электроискровое упрочнение (ЭЛ) | 6500 - 30000 |
7 | Наплавляемые покрытия | 6000 - 16000 |
8 | Напыляемые покрытия | 6500 - 3000 |
9 | Лазерное упрочнение (ЛУ) | 7500 - 13500 |
10 | Детонационное покрытие | 10000 - 14500 |
11 | Композиционные покрытия | 6000 - 22000 |
|
|
Из таблицы видно, что твердость покрытий упрочняемых слоев выше более чем в два раза. Однако только по твердости поверхности нельзя полностью судить о достоинствах метода. Необходимо учитывать положительные и отрицательные составляющие других методов, сравнивая механические свойства, необходимые для области применения.
ППД – повышает твердость, снижает пластичность, имеет низкую абразивную износостойкость.
ТО – «рабочим» порогом режима изнашивания является температура в зоне трения, которая составляет С.
ХТО – увеличивает износостойкость, которая определяется температуростойкостью химических соединений. Так, азотирование выдерживает температуру до 600-650, а борирование до 9000◦С и выше.
Наплавленные и напыленные покрытия отличаются высокой износостойкостью, которая зависит от химического состава наносимого покрытия, но требует усложненной технологии, включая подготовительные операции и операции для снятия внутренних напряжений. Для напыления требуется также вводить операцию по увеличению прочности сцепления покрытия с основой (термодеформированное расслаивание).
Лазерное упрочнение позволяет получать тонкие слои, отличные от структуры ТО, вследствие высоких скоростей нагрева слоев. Недостаток этого способа упрочнения – низкий температурный порог, который составляет температуру около 2000◦С.
Детонационная обработка позволяет получить более качественное по сравнению с напыленным покрытие, не требует деформационного рассасывания. К недостаткам метода можно отнести сложность реализации технологического процесса и трудность установки детали в технологическом оборудовании.
Композиционные покрытия в настоящее время получили наибольшее применение. Основные достоинства: возможность получения достаточно толстых слоев (до 4 мм); использование износостойких композиций порошков из твердого сплава, релита, боридов и специальных сплавов; создание покрытий с твердой смазкой, где в качестве наполнителей используются графит, дисульфид молибдена, сульфиды, селениды и др.
Несмотря на существенные преимущества, методы не получили широкого применения из-за ряда существенных недостатков: сложность технологии нанесения покрытия, включая операции специальной подготовки для герметизации зоны упрочнения; применение высоких температур (до 12000); наблюдаются температурные деформации и напряжения, так как вся система упрочнения подвергается нагреву; применение дорогостоящих материалов как в качестве матрицы (серебро, никель, кобальт, медь), так и в качестве наполнителей (бориды, карбиды, твердый сплав); необходимость включения операций по снятию внутренних напряжений. Анализируя методы поверхностного упрочнения, следует отметить, что, увеличивая твердость, снижаем пластичность, которая приводит к уменьшению опасности схватывания сопряженных поверхностей, с одной стороны. С другой стороны, снижение пластичности повышает чувствительность к местным высоким давлениям, которые могут привести даже к местному разрушению поверхности.
Итак, в упрочненном поверхностном слое необходимо обеспечить достаточную пластичность, высокую твердость и прочность. Эти требования можно реализовать только в композиционном покрытии, организуя упрочненный слой, состоящий из пластичной основы (матрицы) с твердыми включениями.
Дата добавления: 2018-11-24; просмотров: 774; Мы поможем в написании вашей работы! |
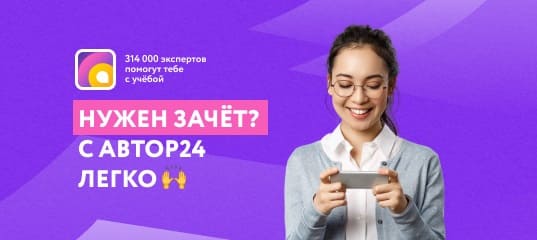
Мы поможем в написании ваших работ!