Анализ методов обработки металлов давлением (ОМД).
Министерство сельского хозяйства Российской Федерации
Федеральное государственное бюджетное образовательное учреждение высшего образования
Ульяновский государственный аграрный университет имени П.А. Столыпина
Кафедра: «Материаловедение и
технология машиностроения»
ОТЧЕТ
ПО ПРОИЗВОДСТВЕННОЙ ПРАКТИКЕ ПО ПОЛУЧЕНИЮ
ПУ И ОПД: ЗАВОДСКОЙ ПРАКТИКЕ
ООО «УЗМД» г. Ульяновска
Выполнил студент: 3 курса ПСО,
заоч.отд. направлен. «Агроинженерия»
инженерного факультета Борисов С.Г.
Руководитель: Шамуков Н.И.
Ульяновск 2017 г.
Месторасположение предприятия (подразделения), вид его хозяйственной деятельности, выпускаемая продукция и краткие сведения из его истории.
Организация ООО «Ульяновский Завод Машиностроительная Деталь» зарегистрирована 21 мая 2012 года по адресу: 432005, Ульяновская область, г. Ульяновск, ул. Пушкарева, д. 9. Компании был присвоен ОГРН: 1127327001603 и выдан ИНН: 7327063805. Основным видом деятельности является производство прочих готовых металлических изделий, не включенных в другие группировки. Компанию возглавляет Конюхов Олег Анатольевич.
|
|
Виды деятельности: основной (по коду ОКВЭД ред.2): 25.99 - производство прочих готовых металлических изделий, не включенных в другие группировки; д ополнительные (по ОКВЭД 2):
25.11 | Производство строительных металлических конструкций, изделий и их частей. |
25.29 | Производство прочих металлических цистерн, резервуаров и емкостей. |
25.61 | Обработка металлов и нанесение покрытий на металлы. |
25.62 | Обработка металлических изделий механическая. |
28.25.1 | Производство теплообменных устройств, оборудования для кондиционирования воздуха промышленного холодильного и морозильного оборудования, производство оборудования для фильтрования и очистки газов. |
28.29 | Производство прочих машин и оборудования общего назначения, не включенного в другие группировки. |
28.99.9 | Производство оборудования специального назначения, не включенного в другие группировки. |
29.31 | Производство электрического и электронного оборудования для автотранспортных средств. |
29.32 | Производство прочих комплектующих и принадлежностей для автотранспортных средств. |
45.31.1 | Торговля оптовая автомобильными деталями, узлами и принадлежностями, кроме деятельности агентов. |
46.69.9 | Торговля оптовая прочими машинами, приборами, аппаратурой и оборудованием общепромышленного и специального назначения. |
47.78.9 | Торговля розничная непродовольственными товарами, не включенными в другие группировки, в специализированных магазинах. |
2.1. Анализ применяющихся на предприятии материалов, их маркировка и область применения.
|
|
Применяющиеся на предприятии материалы, их маркировка: круг ст45 38мм, круг ст45 48мм и тд. Лист ст3 30 г∕к, лист 10 ст09Г2С, лист 10∕2000∕6000 ст09Г2С, лист 16 ст20, лист риф. 4,0 чечевица и тд. Профлист СС 10 RAL 1006 и тд. Пруток алюминий АМц круг 30мм, пруток алюминий Д16Т круг40мм и тд. Пруток латунь ЛС 59-1 круг 100мм, пруток латунь 59-1 круг 90мм и тд. Пруток нерж.12/18н10т 6 гр 17мм. Труба 1020∕12 ст17Г1С, труба 100∕100∕6 ст09Г2С, труба 22∕4 ст09Г2С и тд. 6204 подшипник (NSK), 8109 подшипник (20гпз), 874901 подшипник, 941∕12 подшипник. Фланец 4-80-63 09Г2С, фланец 7-100-160 ст20 ГОСТ12821-80 и тд. Перечень материалов представлен кратко.
По химическому составу классификация основана на указании главного или основного компонента сплава, на основе которого сплав составлен: железо, медь, алюминий и т.д. Такая классификация позволяет распределить сплавы на небольшое число основных классов:
|
|
а) сплавы на основе железа (стали, чугуны);
б) медные сплавы (бронзы и латуни);
в) алюминиевые сплавы (авиали, дюрали, силумины);
г) магниевые сплавы;
д) титановые сплавы;
е) оловянистые и свинцовистые сплавы для подшипников (баббиты) и т.д.
А самая большая группа сплавов - стали, в свою очередь, делится по химическому составу на 2 группы: углеродистые (нелегированные) стали и легированные.
По назначению стали делятся на 3 основные группы:
а) конструкционные;
б) инструментальные;
в) стали специального назначения.
Конструкционные стали должны обладать высокими прочностью, пластичностью и вязкостью в сочетании с хорошими технологическими свойствами: легко обрабатываться давлением, резанием, хорошо свариваться и т.д. Стали конструкционные используются для изготовления деталей машин, механизмов в машиностроении и металлоконструкций в строительстве.
Инструментальные стали должны обладать повышенной или высокой твердостью и износостойкостью, которые должны сохраняться при нагреве. Инструментальные стали применяются для изготовления инструмента для обработки металлов резанием, давлением, для изготовления мерительного инструмента.
|
|
Специальные стали должны обладать какими-либо особыми свойствами: кислотостойкостью, жаропрочностью, магнитными или, наоборот, немагнитными свойствами и т.д. Основными потребителями сталей с особыми свойствами являются приборостроение, химические производства, ракетостроение, авиастроение, военная спецтехника и т.д.
По качеству стали подразделяют на стали:
а) обыкновенного качества;
б) качественные;
в) высококачественные.
Основными признаком качества является содержание вредных примесей в сталях: серы и фосфора. Предельно допустимое содержание примесей в сталях разных категорий качества следующее:
Р | S | |
сталь обыкновенного качества | 0,040% | 0,050% |
Качественная сталь | 0,035% | 0,035% |
Высококачественная сталь | 0,025% | 0,025% |
Особовысокачественная сталь | 0,025% | 0,015% |
Категория обыкновенного качества относится только к сталям простым углеродистым (нелегированным), а две остальные категории относятся и к углеродистым, и к легированным сталям.
По степени раскисления (удаление кислорода из металла) стали могут быть спокойные (сп), полуспокойные (пс), и кипящие (кп), что указывается в марке. Кипящая < 0,05%; полуспокойная сталь 0,05-0,15%; спокойная сталь 0,15 - 0,35%. Чем больше кремния в стали, тем хуже штампуемость.
Легированные стали выплавляются только спокойными в мартеновских или электрических печах. В качестве раскислителей металлурги используют марганец, кремний, алюминий.
По способу производства различают стали конверторные, мартеновские, электросталь и стали особых методов выплавки: электрошлаковый переплав (ЭШП), вакуумно-индукционная плавка (ВИП), вакуумно-диффузионная плавка (ВДП), электронно-лучевой переплав (ЭЛП), плазменно-дуговая плавка (ПДП). Применение особых методов выплавки позволяет получить более чистый качественный материал.
Следует отметить, что это два наиболее простых и одновременно информативных способа. Специалисту для начала уже достаточно этой информации, чтобы получить представление о возможностях данного сплава. К тому же по сравнению с принципами обозначения сплавов в других странах наша система считается наиболее наглядной и простой, чего нельзя сказать о третьем способе маркировки «марка-каталог». Согласно этому способу сплавам присваиваются номера, перед которыми для углеродистых сталей общего назначения стоят буквы «Ст» (сталь), для высоколегированных сталей сложного состава - индексы «ИЭ» или «ЭП» (марки исследовательские или пробные). В этом случае для расшифровки состава или свойств нужны соответствующие ГОСТы, технические условия или каталоги марок.
Углеродистые стали. Основный продукцией черной металлургии является сталь-сплав железа с углеродом. Содержание углерода в стали колеблется в широких пределах от 0,1 до 2%. Сталь промышленного производства является сплавом сложным по химическому составу. Кроме основы - железа в ней содержится много элементов, наличие которых обусловлено различными причинами:
а) невозможностью их полного удаления: S,Р, О2, N2, Н2;
б) технологическими особенностями производства: марганец и кремний, например, вводятся как раскислители;
в) случайные примеси из руды или шихты: Сr, Мn, Ni, Сu, Аs и др.
Содержание всех этих примесей будет зависеть от состава шихты и способа выплавки стали: конверторный, мартеновский, электроплавка, специальные способы выплавки.
Один элемент - углерод вводится в простую сталь намеренно, умышленно. Объясняется это тем, что углерод очень сильно влияет на свойства сталей даже при незначительном изменении его содержания. Поэтому углерод и является основным элементом, изменяющим свойства сталей. С увеличением содержания углерода растут твердость - НВ, прочность - sв, уменьшается пластичность d и вязкость. Количество постоянных примесей в углеродистой стали ограничивается следующими пределами: Мn ≤ 0,7%; Si ≤ 0,5%; Р ≤ 0,05%; S 0 ≤ 0,5%. При большем содержании этих элементов сталь следует отнести к сорту легированных сталей, где эти элементы специально вводятся с целью изменения свойств стали.
Слесарные работы, выполняемые в участках подразделения, с описанием рабочего места слесаря, основные операции слесарной обработки, выполняемые при изготовлении определенного изделия.
Основные виды слесарных работ. Разметкой называется нанесение на поверхность заготовки границ в виде линий и точек, соответствующих размерам детали по чертежу, а также осевых линий и центров для сверления отверстий. Если разметка производится только в одной плоскости, например на листовом материале, то она называется плоскостной.
Разметка поверхностей заготовки, расположенных под разными углами друг к другу, называется пространственной. Заготовки размечают на специальной чугунной плите. Чертилка представляет собой стальной стержень с острыми закаленными концами. Чертилкой наносят тонкие линии на поверхности заготовки при помощи линейки, шаблона или угольника. Кернер служит для нанесения небольших углублений на разметочных линиях заготовки.
Рейсмас применяют для нанесения на заготовке горизонтальных линий, параллельных поверхности разметочной плиты. Рейсмас состоит из основания и укрепленной в его центре стойки, на которой имеется подвижный хомутик с чертилкой, поворачивающейся вокруг своей оси. Подвижный хомутик может перемещаться по стойке и закрепляться на ней в любом положении зажимным винтом. Применяют также разметочный циркуль. Разметочный штангенциркуль применяют для вычерчивания окружностей больших диаметров с непосредственной установкой размеров. Разметочный штангенциркуль, центроискатель предназначен для определения центра торца цилиндрической заготовки, масштабный высотомер.
Рубка металла. Слесарная рубка применяется для снятия лишнего металла в тех случаях, когда не требуется большой точности обработки, а также для грубого выравнивания шероховатых поверхностей, для разрубания металла, срубания заклепок, для вырубания шпоночных пазов и т. п.
Инструменты для рубки металла:
а) зубило;
б) крейцмейсель;
в) слесарный молоток.
Крейцмейсель применяют для прорубания шпоночных канавок, срубания заклепок, предварительного прорубания канавок для последующей рубки широким зубилом.
Правка и гибка металла. Слесарная правка применяется обычно для выравнивания искривленной формы заготовок и деталей. Правку выполняют вручную или на правильных валках, прессами, на листоправйльных и углоправйльных станках и т. д. Гибка металла применяется для получения необходимой формы изделий из листового, пруткового материала, а также из труб. Гибку осуществляют ручным или механическим способом.
Резка металла. При резке металла пользуются различными инструментами: кусачками, ножницами, ножовками, труборезами. Применение того или иного инструмента зависит от материала, профиля и размеров обрабатываемой заготовки или детали. Например, для резки проволоки применяют кусачки.
Опиливание металла. Опиливание является одним из видов слесарной обработки, заключающимся в снятии с заготовки или детали слоя металла для получения заданных форм, размеров и чистоты поверхности.
Шабрение. Шабрением называется процесс снятия очень тонкого слоя металла с недостаточно ровной поверхности специальным инструментом - шабером. Шабрение является окончательной (точной) отделкой поверхностей сопряженных деталей станков, вкладышей подшипников скольжения, валов, поверочных и разметочных плит и т. п. для обеспечения плотного прилегания частей соединения. Шаберы изготовляют из высокоуглеродистой инструментальной стали У12А или У12.
Притирка. Притирка является одним из самых точных способов окончательной доводки обрабатываемой поверхности, обеспечивающим высокую точность обработки - до 0,001- 0,002 мм. Процесс притирки заключается в снятии тончайших слоев металла абразивными порошками, специальными пастами. Для притирки применяют абразивные порошки из корунда, электрокорунда, карбида кремния, карбида бора и др. Притирочные порошки по зернистости разделяются на шлифпорошки и микропорошки. Первые применяются для грубой притирки, вторые - для предварительной и окончательной доводки.
Сверлильные станки. В ремонтных мастерских наибольшее применение имеют одношпиндельные вертикально - сверлильные станки. Также применяется пневматическая и электрическая дрель.
Нарезание резьбы. Нарезание резьбы представляет собой процесс получения на цилиндрических и конических поверхностях винтовых канавок. Совокупность витков, расположенных по винтовой линии на изделии, называется резьбой. Резьба бывает наружная и внутренняя. Основными элементами всякой резьбы являются профиль, шаг, высота, наружный, средний и внутренний диаметры.
Клепка. При ремонте машин и их сборке слесарю приходится иметь дело с различными соединениями деталей. В зависимости от способа сборки соединения могут быть разъемными и неразъемными. Одним из способов сборки деталей в неразъемное соединение является клепка. Клепка производится при помощи заклепок ручным или машинным способом. Клепка бывает холодной и горячей. Заклепка представляет собой стержень цилиндрической формы с головкой на конце, которая называется закладной. В процессе расклепывания стержня образуется вторая головка, называемая замыкающей.
Запрессовка и выпрессовка. При сборке и разборке узлов, состоящих из неподвижных деталей, применяют операции запрессовки и выпрессовки, осуществляемые при помощи прессов и специальных съемников.
Паяние. Паянием называется способ соединения металлических деталей друг с другом при помощи особых сплавов, называемых припоями. Процесс паяния заключается в том, что спаиваемые детали прикладывают одну к другой, нагревают до температуры несколько большей, чем температура плавления припоя, а жидкий расплавленный припой вводят между ними.
Рабочим местом называется определенный участок производственной площади, цеха, участка, мастерской, закрепленный за данным рабочим (или бригадой рабочих), предназначенный для выполнения определенной работы и оснащенный в соответствии с характером этой работы оборудованием, приспособлениями, инструментами и материалами. Рабочее место слесаря, в зависимости от характера производственного задания, может быть организовано по-разному. Однако большинство рабочих мест оборудуется слесарным верстаком, на котором устанавливают тиски и раскладывают необходимые для работы инструменты, приспособления, материалы; на специальных планшетах размещают документацию: технологические карты, чертежи и т. д.
2.3. Наличие на предприятии литейного производства.
Литейное производство - отрасль машиностроения, занимающаяся изготовлением фасонных деталей и заготовок путём заливки расплавленного металла в форму, полость которой имеет конфигурацию требуемой детали.
В процессе литья, при охлаждении металл в форме затвердевает и получается отливка - готовая деталь или заготовка, которая при необходимости повышение точности размеров и снижения шероховатости поверхности подвергается последующей механической обработке. В связи с этим перед литейным производством стоит задача получения отливок, размеры и форма которых максимально приближена к размерам и форме готовой детали.
Наиболее распространено в промышленности производство отливок в разовых песчаных формах. Этот способ применяется для изготовления из различных сплавов заготовок любых размеров и конфигурации.
Технологический процесс литья в песчаные формы складывается из ряда последовательных операций: подготовка материалов, приготовление формовочных и стержневых смесей, изготовление форм и стержней, простановка стержней и сборка форм, плавка металла и заливка его в формы, охлаждение металла и выбивка готовой отливки, очистка отливки, термообработка и отделка.
Материалы, применяемые для изготовления разовых литейных форм и стержней, делятся на исходные формовочные материалы и формовочные смеси. Их масса равна в среднем 5 - 6 т. на 1 т. годных отливок в год. При изготовлении формовочной смеси используют отработанную формовочную смесь, выбитую из опок, свежие песчано-глинистые или бентонитовые материалы, добавки, улучшающие свойства смеси, и воду. В стержневую смесь обычно входят кварцевый песок, связующие материалы масло, смола и др. и добавки. Приготовление смеси производят в определённой последовательности на смесеприготовительном оборудовании ситах, сушилах, дробилках, мельницах, магнитных сепараторах, смесителях и т. п.
Формы и стержни изготовляют на специальном формовочном оборудовании и станках. Насыпанная в опоки смесь уплотняется встряхиванием, прессованием или совместно тем и др. способом. Крупные формы заполняют с помощью пескомётов, реже для изготовления форм используют пескодувные и пескострельные машины. Формы в опоках, заформованные в стержневых ящиках стержни подвергаются тепловой сушке или химическому твердению, например при литье в самотвердеющие формы Тепловую сушку осуществляют в литейных сушилах, а сушку стержней производят также в нагретом стержневом ящике. Сборка форм состоит из следующих операций: установка стержней, соединение половин форм, закрепление форм скобами или грузами, устанавливаемыми на верхнюю форму и предотвращающими их раскрытие при заливке сплавом. Иногда на форму устанавливают литниковую чашу, изготовленную из стержневой или формовочной смеси.
Основные дефекты отливок. Усадочные раковины – закрытые полости, большей частью окисленные, в отливках с шероховатой поверхностью, устраняются усадочные раковины с помощью прибылей, которые затвердевают в последнюю очередь. Горячие трещины – сквозные и несквозные разрывы в теле отливки. Они возникают обычно в местах перехода от тонкого сечения к толстому, в местах резких переходов сечения под прямым или острым углом. Газовые раковины – полости в отливке округлой формы с гладкой поверхностью, размером от 1 до 10 мм, возникают при низкой газопроницаемости формы, при неправильно построенной литниковой системе. Недоливы и спай образуются от неслившихся потоков металла, потерявших жидкотекучесть и затвердевших до заполнения формы. Пригар взаимодействие литейной формы и залитого металла при недостаточной ее огнеупорности и высокой химической активности. Перекос в отливке образуется при небрежной сборке формы.
Литье в оболочковые (корковые, скорлупчатые) формы. Литье в оболочковые формы – процесс получения отливок путем свободной заливки расплавленного металла в оболочковые песчано-смоляные формы, изготовленные формовкой по горячей модели. Разновидностей данного способа литья много. Плакированные смеси содержат смолу в виде тонкой пленки, покрывающей поверхность зерен кварца. Оболочковые формы из плакированной смеси имеют более высокую прочность при минимальном расходе смеси. Смола обладает способностью при нагревании до 160 - 200°С оплавляться, переходить в термопластическое состояние, что способствует получению четкого отпечатка модели. При нагревании до 290 - 350°С смола переходит в стойкое термореактивное (необратимое) состояние.
Литье в кокиль – процесс получения фасонных отливок путем свободной заливки расплавленного металла в металлические формы – кокили. Литье в кокиль широко применяется в серийном и массовом производстве отливок для самых разнообразных изделий с толщиной стенки 3 - 100 мм. из медных, алюминиевых и магниевых сплавов, а также из чугуна и стали, масса которых колеблется в широких пределах – от нескольких граммов, до нескольких тонн; например, крупные лопасти, головки и блоки двигателей внутреннего сгорания, корпуса нагнетателей реакторов, диффузора и др. Литьем в кокиль обеспечивается повышенная точность геометрических размеров, снижается шероховатость поверхности отливок, уменьшаются припуски на механическую обработку, улучшаются механические свойства отливок в сравнении с отливками, полученными в песчано-глинистых формах. Недостаток литья в кокиль – большая стоимость изготовления и высокая теплопроводность формы, приводящая к понижению заполняемости ее металлом вследствие быстрой потери текучести. Конструкции кокилей чрезвычайно разнообразны. Кокиль для простых отливок изготовляют из двух частей, соответствующих верхней и нижней опокам при литье в песчано-глинистые формы. Для сложных отливок форму изготовляют из разъемных частей, каждая из которых образует часть отливки, при этом поверхность разъема формы определяется конструкцией отливки; при этом поверхность разъема формы определяется конструкцией отливки. Кроме этого, толщина стенок кокиля влияет на скорость затвердевания и последующее охлаждение отливки, а следовательно, на образование структуры отливки. Для получения внутренней полости отливки применяют стержни: для отливок из легкоплавких сплавов – преимущественно металлические, для чугунных и стальных отливок – песчаные. Газ, находящийся в форме, отводится через выпор и вентиляционные отводные каналы, расположенные вдоль разъема формы. Для извлечения отливки в форме имеются выталкиватели. Технология литья в кокиль имеет ряд специфических особенностей, обусловленных конструкцией металлической формы и требованиями к заливаемому металлу. В целях получения качественной отливки и удлинения срока службы кокиля его покрывают огнеупорной облицовкой или краской.
Центробежное литье. Использование центробежных сил для заполнения и кристаллизации металла в полости формы – отличительная особенность центробежного литья. Центробежные силы образуются в результате вращения литейной формы. Этот способ литья применяют преимущественно для изготовления полых отливок, имеющих форму тела вращения (трубы, втулки, кольца), из чугуна, стали, цветных сплавов (медных, алюминиевых, титановых и др.), фасонных отливок с малой толщиной стенок, но повышенной плотностью материала (лопатки турбин, корпуса, детали гидроаппаратуры и т.д.). Для получения отливок используют установки с горизонтальной и вертикальной осью вращения формы. Под действием центробежных сил жидкий металл прижимается в внутренней поверхности вращающейся формы, увлекается ею и в таком состоянии кристаллизуется. При центробежном литье возможно применять не только металлическую форму, но и оболочковую песчано-глинистую и форму, получаемую по выплавляемой модели. Центробежное литье по сравнению с литьем в неподвижные формы имеет ряд преимуществ:
- отливки обладают большой плотностью материала;
- исключаются затраты на изготовление стержней для получения полости в цилиндрических отливках;
- улучшается заполняемость форм металлом;
- возможно получение отливок из сплавов, обладающих низкой жидкотекучестью.
Центробежный способ литья имеет следующие недостатки:
- загрязнение свободной поверхности отливки неметаллическими включениями (более легкими, чем сплав отливки);
- наличие дефектов в отливке в виде химической неоднородности по радиальному направлению из-за ликвации составляющих сплава по плотности.
С увеличением скорости вращения возрастает ликвация элементов по плотностям в сечении отливки.
Скорость вращения форм является важным параметром технологии центробежного литья. При заниженной скорости вращения внутренняя поверхность получается негладкой, не происходит достаточного очищения отливок от неметаллических включений. При завышенной скорости сильно возрастает внутреннее давление жидкого металла, что приводит к образованию трещин и усиливается ликвация компонентов сплава по плотностям. Оптимальную скорость вращения для каждой отливки определяют по эмпирическим формулам или номограммам.
Литье по выплавляемым моделям – это процесс получения отливок в неразъемных разовых огнеупорных формах, изготавливаемых с помощью моделей из легкоплавящихся, выжигаемых или растворяемых составов. Используют как оболочковые (керамические), так и монолитные (гипсовые) формы. При этом рабочая полость формы образуется выплавлением, растворением или выжиганием модели. Модельные составы, применяемые при литье по выплавляемым моделям, должны обладать минимальными значениями усадки и коэффициента термического расширения, иметь высокую жидкотекучесть в вязкопластичном состоянии, хорошо смачиваться керамической или гипсовой суспензией, наносимой на модель, но химически с ней не взаимодействовать, обладать температурой размягчения, превышающей 40°С. Изготовление моделей осуществляется посредством заливки или запрессовки модельного состава в пастообразном (подогретом) состоянии в специальные пресс-формы. В частности, литьевой способ получения пенополистероловых моделей на специальных термопластавтоматах включает в себя пластификацию нагревом (100 – 220°С) гранул полистирола, впрыскивая его в пресс-форму с последующим вспениванием и охлаждением модели. Для производства пресс-форм используют как металлические (стали, алюминиевые и свинцово-сурьмянистные сплавы), так и неметаллические (гипс, эпоксидные смолы, формопласт, виксинт, резина, твердые породы дерева) материалы. Пресс-формы, используемые для получения моделей, должны обеспечивать им высокие параметры точности размеров и качества поверхности, быть удобными в изготовлении и эксплуатации, а также иметь соответствующий уровню серийности ресурс работы. Так, при единичном, мелкосерийном и серийном производствах используются, в основном, литые металлические, гипсовые, цементные, пластмассовые, деревянные, а также полученные методами металлизации пресс-формы, изготавливаемые с помощью механической обработки.
Способ литья под давлением и выжиманием. Литьем под давлением называется способ получения фасонных отливок в металлических формах, при котором форму принудительно заполняют металлом под давлением, превосходящим атмосферное. Литые под давлением обеспечивает высокую точность геометрических размеров и малую шероховатость поверхности, значительно снижает объем механической обработки отливок и в некоторых случаях полностью ее исключает, обеспечивает высокие механические свойства отливок, позволяет получить сложные по конфигурации отливки с малой толщиной стенок. Этим способом получают отливки из алюминиевых, магниевых, цинковых и медных сплавов с толщиной стенок от 0,7 до 6,0 мм, массой от нескольких граммов до 50 кг. Он находит применение для изготовления деталей электронно-счетных машин, оптических приборов, блоков цилиндров, тормозных дисков и др. При литье под давлением металлические формы имеют более сложную конструкцию и их изготовляют более точно и тщательно, чем при кокильном литье. Формы при литье под давлением делают стальными со стальными стержнями. Применение песчаных стержней исключено. Для создания давления при заполнении формы металлов применяют весьма сложные машины. Существуют машины компрессорного действия и поршневого. Давление на металл в разных конструкциях машин колеблется в широких пределах (от 60 до 2000 Па). Литье выжиманием используют для получения тонкостенных крупногабаритных отливок панельного типа размерами до 10002500 мм с толщиной стенки 2,5 - 5 мм. Способ позволяет также изготовлять отливки типа тонкостенных цилиндрических оболочек. Точность отливок приближается к точности отливок, получаемых при свободном литье в металлические формы, уступая им из-за неточности стыковки полуформ. Характерной особенностью литья выжиманием является отсутствие литниковой системы и возможности заливки металла при более низких температурах в суспензионном состоянии, т.е. в начальной стадии кристаллизация).
Литейные свойства сплавов должны обязательно учитываться при конкретной разработке технологии получения отливки, а также в процессе создания и проектирования литых конструкций. Надежность и долговечность изделий в значительной степени предопределяются литейными свойствами используемого для их изготовления сплава.
Анализ методов обработки металлов давлением (ОМД).
Процесс обработки металлов давлением - это придание материалу требуемой формы, размеров и физико-механических свойств без нарушения его сплошности путем пластической деформации.
Достоинствами ОМД являются: возможность значительного уменьшения отхода металла (до 20-70 %) по сравнению с обработкой резанием; возможность повышения производительности труда, т. к. в результате однократного приложения усилия можно значительно изменить форму и размеры деформируемой заготовки; изменение физико-механических свойств металла заготовки в процессе пластической деформации, которое можно использовать для получения деталей с наилучшими служебными свойствами (прочностью, жесткостью, сопротивлением износу и т. д.) при наименьшей их массе.
Виды обработки металлов давлением: прокатку, прессование, волочение, ковку и штамповку.
Обработке металлов давлением поддаются только пластичные металлы и сплавы, а хрупкие (марганец, чугун) пластически не деформируются.
Деформацией называется изменение форм и размеров тела под действием напряжений. Различают упругую и пластическую деформации.
Упругой называется деформация, которая устраняется после снятия нагрузки. Остаточных изменений структуры и свойств металла упругая деформация не вызывает. Она характеризуется смещением атомов относительно друг друга на величину меньшую межатомных расстояний и после снятия внешних сил возвращается в исходное положение. Пластической называют такую деформацию, которая не устраняется после снятия нагрузки.
Пластическая деформация вызывает необратимое изменение структуры и свойств металла. Она характеризуется смещением атомов относительно друг друга на величину большую межатомных расстояний и после снятия внешних сил не возвращается в исходное положение. Тело принимает новую форму и размеры. Процесс пластической деформации обычно представляет собой процесс скольжения одной части кристалла относительно другой по кристаллографическим плоскостям скольжения с более плотной упаковкой атомов. В таких условиях атомы не выходят из зоны силового взаимодействия, и деформация происходит без нарушения сплошности (без образования трещин, разрывов). При пластической деформации поликристаллических тел кристаллиты (зерна) меняют свою форму и ориентировку, образуя волокнистую структуру с преимущественной ориентировкой кристаллов. Зерна деформируются и сплющиваются, вытягиваясь в направлении деформации. Преимущественная кристаллографическая ориентировка зерен вдоль направления деформации называется текстурой. Образование текстуры способствует появлению анизотропии свойств вдоль и поперек направления волокон.
С ростом степени деформации увеличивается число дефектов кристаллического строения в металле, что оказывает значительное влияние на механические и физико-химические свойства: механические свойства, характеризующие сопротивление деформации, повышаются, а свойства, характеризующие способность к пластической деформации, падают.
Прокатка - вид обработки металлов давлением, при котором металл пластически деформируется между вращающимися валками. При этом силы трения Р тр . между валками и заготовкой втягивают ее в межвалковый зазор, а нормальные силы, перпендикулярные к поверхности валков, производят деформирование заготовки. В процессе прокатки уменьшается толщина заготовки при одновременном увеличении ее длины и ширины. µ- коэффициентом вытяжки. ℰ - относительное обжатие.
Эти величины (µ, ℰ) являются основными количественными характеристиками деформации при прокатке. Коэффициент вытяжки при прокатке обычно составляет 1,1 - 2,0 за проход. Выделяют три основные вида прокатки: продольную, поперечную и поперечно-винтовую (косую).
Форма поперечного сечения прокатанного изделия называется профилем. Совокупность различных профилей разных размеров называется сортаментом. Сортамент разделяют на 4 основные группы: сортовой прокат, листовой, трубы и специальные виды проката.
Профили сортового проката подразделяют на группы: простой геометрической формы (квадрат, круг, шестигранник, прямоугольник и т. д.); сложной, фасонной формы (швеллеры, двутавровые балки, рельсы, уголки и т. д.).
Ковка - вид горячей обработки металлов давлением, при котором металл деформируется ударами универсального инструмента - бойков. Ковкой получают заготовки для последующей механической обработки. Эти заготовки называют поковками. Ковка применяется в индивидуальном и мелкосерийном производстве и разделяется на ручную и машинную. Ручной ковкой получают мелкие поковки в единичном производстве и при ремонтных работах с помощью наковальни и кувалды. Машинная ковка осуществляется на молотах и прессах и является пока единственным способом изготовления тяжелых поковок из слитков весом до 350 тонн. Молотами называются машины ударного действия. Продолжительность деформации на них составляет тысячные доли секунды. Для привода молотов используют пар, сжатый воздух или газ, жидкость под давлением, горючую смесь, взрывчатые вещества, магнитные и гравитационные поля. Основными типами молотов для ковки являются пневматические и паровоздушные. Паровоздушные молоты приводятся в действие соответственно паром или сжатым воздухом. Пневматические молоты используют сжатый воздух, но воздух является пружиной, связывающей два поршня: рабочий и компрессорный. Гидравлические прессы. Прессы развивают статическое усилие, и продолжительность деформации у них может составлять десятки секунд.
Штамповка - способ изготовления изделий давлением с помощью специального инструмента (штампа), рабочая полость которого определяет конфигурацию конечной штампованной поковки (изделия).
По сравнению с ковкой штамповка имеет ряд преимуществ: можно получать поковки сложной конфигурации без напусков. При этом допуски на штампованную поковку в 3-4 раза меньше, чем на кованую. Следовательно, значительно сокращается отход металла в стружку при последующей обработке резанием. Производительность штамповки значительно выше - десятки и сотни поковок в час.
К недостаткам относятся: дорогостоящий штамповый инструмент – штамп используется для изготовления только одной, конкретной поковки. Для штамповки требуются гораздо большие усилия деформирования, чем для ковки таких же поковок.
Следовательно, штамповка экономически целесообразна при серийном производстве поковок массой до 20-30 кг.
Процессы штамповки разделяют на объемную и листовую штамповку. Объемную штамповку подразделяют на горячую и холодную.
Процесс волочения заключается в протягивании заготовки через постепенно сужающееся отверстие в инструменте, называемом волокой. Волока (фильера, матрица) представляет собой кольцо, рабочее отверстие которого состоит из входной (или смазочной) зоны I, деформирующей зоны II, калибрующего пояска III и выходного конуса IV. Ее изготавливают из инструментальной стали, металлокерамических сплавов, и алмазов (для волочения проволоки диаметром менее 0,2 мм). Волочильные станы разделяют на два типа: барабанные и цепные. Барабанные станы служат для волочения проволоки и труб небольшого диаметра, наматываемых на вертушку. Цепные станы с прямолинейным движением тянущего устройства применяют для волочения прутков и труб, которые не могут наматываться в бунты. Волочение, как правило, осуществляют в холодном состоянии, а потому оно сопровождается упрочнением (наклепом) металла. Исходными заготовками служат прокатанные или прессованные прутки и трубы из стали, цветных металлов и их сплавов. Величина деформации за один проход ограничена: µ= 1,25-1,45. Если для получения необходимых профилей требуется большая деформация, то применяют волочение за несколько переходов протягиванием через ряд постепенно уменьшающихся по величине отверстий. Для снятия наклепа после каждого перехода металл подвергают промежуточному отжигу. Для уменьшения силы трения металла об инструмент полируют отверстие в волоке и применяют различные смазки - минеральные масла олифу, графит, тальк, мыла, фосфатные и металлические покрытия и др. Сортамент изделий, изготовленных волочением, очень разнообразен: проволока 0,002-10 мм и фасонные профили , трубы диаметром от 0,3 до 500 мм с толщиной стенки от 0,05 до 5-6 мм.
Прессование - получения изделий путем выдавливания нагретого металла из замкнутой полости через отверстие инструмента. Различают два метода прессования: прямой и обратный. В прямом прессовании металл выдавливается в направлении движения пуансона. В обратном прессовании металл движется из контейнера навстречу движению пуансона. Для прессования применяют гидравлические прессы с горизонтальным или вертикальным расположением пуансона. Инструмент для прессования состоит из контейнера, матрицы, пуансона (штемпеля), иглы и иглодержателя (при прессовании полых профилей и труб). Инструмент работает в очень тяжелых условиях: при температурах 800-1200°С и при высоких удельных нагрузках. Его изготавливают из высококачественных инструментальных сталей и жаропрочных сплавов. Износ инструмента уменьшают применением смазок: графит, стекло, порошки меди, никеля, окись цинка, дисульфид молибдена и др.
Дата добавления: 2018-11-24; просмотров: 1352; Мы поможем в написании вашей работы! |
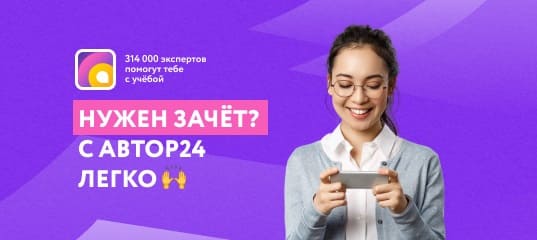
Мы поможем в написании ваших работ!