Разъемные соединения деталей машин
Соединения деталей машин и механизмов, допускающие многократную разборку и сборку без повреждения соединяемых деталей и соединительных элементов называются разъемными соединениями. Разъемные соединения в свою очередь делятся на подвижные и неподвижные.
С помощью подвижных соединений можно обеспечить определенное перемещение одних деталей относительно других. К ним относятся различные опоры и направляющие.
Неподвижные соединения обеспечивают фиксированное положение одних деталей по отношению к другим.
К разъемным соединениям относят резьбовые, штифтовые, шпоночные, шлицевые и некоторые другие соединения. Выбор типа соединения зависит от предъявляемых к нему требований: конструктивных, технологических и экономических.
Резьбовые соединения
Резьбовыми называют соединения составных частей изделия с применением деталей, имеющих резьбу. Они наиболее распространены в приборо- и машиностроении. Резьбовые соединения бывают двух типов: соединения с помощью специальных резьбовых крепежных деталей (болтов, винтов, шпилек, гаек) и соединения свинчиванием соединяемых деталей, т.е. резьбы, нанесенной непосредственно на соединяемые детали.
Достоинствами резьбовых соединений являются простота, удобство сборки и разборки, широкая номенклатура, стандартизация и массовый характер производства крепежных резьбовых деталей, взаимозаменяемость, относительно невысокая стоимость и высокая надежность.
|
|
Недостатками резьбовых соединений являются наличие концентраций напряжений во впадинах резьбы, что снижает прочность соединений; чувствительность к вибрационным и ударным воздействиям, которые могут привести к самоотвинчиванию и низкая точность взаимоположения соединяемых деталей.
Основным элементом соединения является резьба, т.е. поверхность, которая образуется при винтовом движении плоской фигуры по цилиндрической или конической поверхности. Соответственно различают цилиндрическую и коническую резьбы.
По профилю выступа и канавки резьбы в плоскости осевого сечения резьбы делятся на треугольные, трапецеидальные симметричные, трапецеидальные несимметричные или упорные, прямоугольные и круглые.
По назначению резьбы разделяют на крепежные, крепежно-уплотнительные и ходовые.
Крепежные резьбы применяют для соединения деталей, а ходовые – в передаточных механизмах.
Крепежные резьбы имеют, как правило, треугольный профиль с притупленными вершинами и дном впадин. Это повышает прочность резьбы и стойкость инструмента при получении резьбы.
Крепежная резьба бывает метрической, дюймовой и трубной.
|
|
Наиболее широко применяется метрическая резьба. Угол профиля, т.е. угол между смежными боковыми сторонами резьбы в плоскости осевого сечения, метрической резьбы α = 60°.
Стандартом предусмотрена резьба с крупным и мелким шагом.
Резьбу с крупным шагом обозначают М (метрическая), при этом указывают значения наружного диаметра, например, М6, М8 и т.д. Для резьб с мелким шагом дополнительно указывают значение шага, например, М6×0,75, М8×1 и т.д.
Дюймовая резьба используется при замене деталей устройств, импортируемых из стран с дюймовой системой мер. Угол профиля дюймовой резьбы - α = 55°.
Основными крепежными деталями резьбовых соединений являются болты, винты, шпильки, гайки, шайбы и стопорные устройства, предохраняющие гайки от самоотвинчивания.
Болт – цилиндрический стержень с шестигранной головкой на одном конце и резьбой – на другом. Болты в соединении используют в комплекте с гайкой, при этом резьба в соединяемых деталях не используется (рис. 1, а).
Винты – цилиндрические стрежни с головкой на одном конце и резьбой – на другом. Винт ввертывается в резьбовое отверстие одной из скрепляемых деталей (рис. 1, б), головки винтов могут иметь различную форму (цилиндрическую, полукруглую и др.).
|
|
Шпилька – цилиндрический стержень с резьбой на обоих концах, одним концом она ввертывается в одну из скрепляемых деталей, а на другой ее конец навертывается гайка (рис. 1, в).
Соединения при помощи шпилек применяют в тех случаях, когда в одной из соединяемых деталей нельзя выполнить сквозное отверстие и материал этой детали (с резьбой) не обладает высокими прочностными свойствами (пластмасса, алюминиевые, магниевые сплавы). Поэтому применение винта при частой разборке и сборке соединения из-за малой прочности резьбы не рекомендуется.
Гайки служат для соединения скрепляемых с помощью болта или шпильки деталей. Как и головки винтов, гайки могут иметь разнообразную форму.
Назначение шайб, подкладываемых под гайку, головку винта или болта, – предохранение поверхностей деталей от задира при затягивании, увеличение опорной поверхности и стопорение.
Болты, винты, гайки изготавливают из углеродистых и легированных сталей.
Крепежные детали общего применения изготавливаются чаще всего из стали марок Ст3, Ст4, Ст5без последующей термообработки. Более ответственные детали изготавливаются из сталей 35, 45, 40Х, 40ХН с поверхностной или общей термообработкой.
Мелкие винты делают из латуни ЛС59-1, дюралюминия Д1, Д16.
Для защиты поверхности крепежных деталей от коррозии, придания им необходимого цвета применяют цинкование, хромирование, кадмирование.
|
|
Угол подъема винтовой линии резьбы (j = 1,5 … 2,5°) меньше угла трения в резьбовом соединении(r » 3°). Этим обеспечиваются условия самоторможения и предохранения от самоотвинчивания. Однако при вибрации, тряске, динамических и транспортных воздействиях наблюдаются ослабления резьбовых соединений, поэтому предусматривают их стопорение.
Для стопорения резьбовых соединений используют увеличение трения по поверхности контакта, пластическое деформирование, постановка резьбы на краску, лак, а также введение запирающих элементов - пружинных или стопорных шайб, специальных разрезных гаек с повышенным трением при стягивании, корончатых гаек, закрепленных шплинтом, отгибных шайб и т. п.
Шпоночные соединения
Шпоночные соединения служат для передачи вращающего (крутящего) момента от вала к ступице насаженной на него детали (зубчатого колеса, шкива, муфты и др.) или наоборот – от ступицы к валу. Шпоночные соединения осуществляют с помощью вспомогательных деталей – шпонок, устанавливаемых в пазах между валом и ступицей.
Достоинствами шпоночных соединений являются простота, надежность конструкции, невысокая стоимость, удобство сборки и разборки.
Недостатки шпоночных соединений – ослабление вала и ступицы шпоночными пазами, неустойчивость положения шпонки в пазах (выворачивание шпонки) и трудность обеспечения взаимозаменяемости, повышенные требования к точности изготовления, отсутствие фиксации деталей в осевом направлении.
В приборостроении применяют в основном соединения призматическими (рис. 3, а), сегментными(рис. 3, б) и цилиндрическими (рис. 3, в) шпонками.
Клиновые шпонки в точных механизмах не применяют.
Конструкция и форма шпонки связаны с технологичностью изготовления пазов под шпонку. Пазы на валах фрезеруют, а в ступицах – прорезают протяжками.
Шпонки могут применять в качестве направляющих, обеспечивающих легкое перемещение деталей вдоль вала.
Нагрузку у шпонок воспринимают боковые поверхности, которые сопрягаются с пазами по соответствующим посадкам.
Призматическую шпонку с валом обычно соединяют по переходной посадке, а со ступицей – по посадке с зазором. Это препятствует перемещению шпонки вдоль вала и компенсирует с помощью зазора неточности размеров, формы и взаимного расположения пазов. Такой характер соединения обеспечивает достаточную точность центрирования вала и ступицы. В радиальном направлении предусматривается зазор.
Призматические шпонки имеют прямоугольное сечение, они могут быть с округленными, плоскими и смешанными торцами. Паз под шпонку на валу делают на глубину около 0,6 от ее высоты, а паз во втулке – на длину всей ступицы.
Ширина и высота шпонки определены ГОСТом и выбираются в зависимости от диаметра вала. Размеры высоты и ширины стандартных шпонок подобраны так, что прочность на сдвиг обеспечивается с избытком, и при необходимости проверку шпонок на прочность проводят на деформацию смятия.
Сегментные шпонки требуют более глубоких пазов в валах, что уменьшает их прочность. Их применяют в случае передачи незначительных усилий, работают они как призматические, но более удобны в изготовлении.
Цилиндрические шпонки чаще всего используют для закрепления деталей на конце вала. Отверстие для шпонки обрабатывают в соединяемых деталях (вал и ступица) совместно.
Шпонка устанавливается с натягом.
Шпоночные соединения применяют обычно при передаче значительных вращающих моментов при диаметре вала не менее 6 мм. В кинематических передачах и передачах с высоким требованием по точности рекомендуют использовать штифтовые соединения. Шпонки изготавливают из среднеуглеродистых сталей 40, 45, Ст6.
Шлицевые соединения
Шлицевые соединения служат для передачи вращающего момента между валами и установленными на них деталями.
Шлицевое соединение можно условно представить как многошпоночное, шпонки которого выполнены вместе с валом. С помощью этого соединения можно обеспечить как подвижное (с осевым относительным перемещением), так и неподвижное скрепление деталей.
По сравнению со шпоночными шлицевые соединения имеют значительно большую нагрузочную способность, прочность валов, точность центрирования и направления ступиц в подвижных соединениях.
По форме поперечного сечения шлицев различают прямобочные (рис. 4, а), эвольвентные (рис. 4, б) и треугольные (рис. 4, в) шлицевые соединения. Наибольшее распространение получили прямобочные шлицевые соединения, выполненные с четным числом шлицев (6, 8, 10).
Эвольвентное шлицевое соединение (см. рис.) отличается от прямобочного повышенной точностью центрирования и прочностью. Центрирование осуществляют по боковым сторонам, реже – по наружному диаметру.
Соединение с треугольными шлицами (см. рис.) применяют для неподвижных соединений при небольших нагрузках и тонкостенных конструкциях. Число шлицев z = 20 … 70, углы впадин вала равны 60, 72 и 90°.
19. Объясните назначение, устройство, принцип действия пластинчатых конвейеров, перечислите требования охраны труда при их обслуживании.
Пластинчатый конвейер — автоматизированная транспортировка тяжелых грузов на складе
Пластинчатый конвейер — это конвейер, в котором на роль грузового полотна взяты стальные пластины. Пластины крепятся к цепному тяговому механизму. Этот агрегат чаще всего используют для перемещения горных масс, тяжелых единичных тяжестей, горячего агломерата, известняка, большой кусковой руды, горячих полуфабрикатов. Один из видов такого конвейера — багажная карусель. Она смонтирована во многих аэровокзалах для транспортировки и выдачи багажа. Часто этот механизм входит в конструкцию сельхоз машин. Пластинчатый конвейер — атрибут многих мощных производств, участник множественных технологических процессов.
Устройство
Пластинчатый конвейер по своему устройству и принципу действия больше всего похож на обычный ленточный конвейер. Он имеет в конструкции один или несколько двигателей, систему управления, ленту. Опоры и механизм могут крепиться к корпусу или металлической конструкции, которая может легко перемещаться или разбираться. Основные рабочие органы — станция для натяжения и станция для привода, ходовые валики, полотно из пластин, тяговый орган. Стандартный источник питания в условиях склада — электрический ток.
Если груз конвейера не имеет большого веса — оптимально использовать вместо стальных пластин пластины из пластика. Это снизит цену, вес и энергозатраты. Необходимы защитные кожухи, ограждения.
Стандартные параметры:
ширина пластин — от 0,5 метра,
толщина пластин — от 3 миллиметров,
максимальный угол подъёма установки — до 45 градусов,
эффективность — от 250 до 2100 тонн в час,
скорость перемещения полотна — не менее 0,6 метров в секунду.
Плюсы и минусы
В качестве положительных сторон пластинчатый транспортер характеризуется:
Способностью перемещать груз под большим углом. Если это обычные пластины, то угол может составлять до 45 градусов. Для перемещения на более отвесный угол необходимы ковшеобразные пластины. В противном случае груз будет падать. С таким ковшом угол может доходить до 70 градусов.
Способностью перемещать широкий спектр груза. Эта возможность у ленточного конвейера отсутствует.
Надёжностью, безотказностью.
Способностью перемещать груз по сложной траектории.
Для эксплуатации нет необходимости привлекать рабочего высокой квалификации.
Из неудобств можно считать:
Предельная скорость перемещения груза — 1,26 метров в секунду.
Энергозатратный транспорт. Это объясняется высокой массой самого конвейера, много энергии уходит не на груз, а на перемещение механизма. КПД низкий.
Большое количество шарнирных узлов в цепи требует постоянной смазки и ухода.
Шум.
Источник травматизма.
20. Опишите устройство, принцип работы, область применения гравитационного транспорта (наклонных и винтовых спусков).
В бункерных и транспортных установках широко применяют средства гравитационного (самотечного) транспорта, к которым относятся спускные желоба, лотки и трубы, каскадные и винтовые спуски. Гравитационные устройства предназначены для подачи насыпных грузов из бункеров и штучных грузов на погрузочных установках.
Распространенные на практике сечения лотков и желобов показаны на (рис. 22.1, а-г).
Рис. 22.1. Схемы спусковых устройств:
а и б – стальные открытые полукруглый и прямоугольный желоба; в и г – деревянные открытые желоба; д и е – круглая и квадратная стальные трубы; ж – деревянная квадратная труба; з – стальной закрытый прямоугольный желоб; и – поворотный спуск
Желоба бывают:
- открытые,
- закрытые.
Открытые желоба применяют для транспортирования кусковых, зернистых и порошкообразных материалов, не склонных к сильному пылению.
Для перемещения пылящих грузов, материалов, загрязнение которых недопустимо, а также вредных для здоровья веществ, используют спускные трубы или закрытые желоба (рис. 22.1, д-ж).
На (рис. 22.1, з) показано сечение закрытого желоба, по эксплуатационной характеристике подобного спускной трубе. Съемная крышка облегчает осмотр желоба и ремонт его днища. Стальные желоба и трубы изготовляют из листов толщиной 3...8 мм, а деревянные желоба - из досок толщиной 20...30 мм.
Преимуществом спускных желобов и труб, как транспортных средств, является то, что они не имеют приводного устройства, просты по конструкции, надежны и дешевы в эксплуатации.
Недостатком спускных труб является их большая длина, что вызывает неудобство в размещении обслуживаемого ими оборудования и ограничивает область их применения. Для устранения этого недостатка применяют составные трубы с поворотными коленами А и В (рис. 22.1, и), расположенными под заданными углами наклона к горизонту. Поворотом этих колен в горизонтальной плоскости можно установить центр разгрузочного патрубка Р в любой точке заштрихованной зоны, ограниченной окружностью, имеющей центр в точке загрузки О. В частности, разгрузочное отверстие трубы может находиться на одной вертикали с загрузочным отверстием.
Для вертикального самотечного транспортирования насыпных грузов с заданной скоростью применяют также каскадные и спиральные спуски.
Каскадный спуск составляют из нескольких расположенных одна над другой полок, расстояние между которыми равно допустимой высоте падения кусков данного груза (например, для картофеля допустимая высота падения равна 0,3 м). Поступающий сверху в каскадный спуск материал пересыпается с полки на полку и движется вниз с допустимой скоростью.
Спиральный спуск представляет собой открытый желоб, продольная ось которого изогнута по винтовой линии.
Для штучных грузов применяют вертикальные, наклонные и спиральные спуски.
Рис.22.2. Схемы к расчету спускных устройств:
а – винтовая поверхность с вертикальным бортом; б – то же с наклонной образующей; в – схема спускного устройства; г – схема определения угла поворота струи груза; д – схема определения высоты свободного падения частицы груза; е – схема определения скорости истечения наклонной струи; ж – составной желоб
Вертикальные спуски в виде труб применяют при небольшой высоте спуска для грузов, не боящихся ударов при большой скорости падения в условиях допустимости шума от ударов падающего груза.
При перемещении одинаковых по форме и размерам грузов сечение вертикальной трубы выполняют по форме груза.
При движении груза в такой трубе под ним происходит сжатие воздуха и создается воздушная подушка, амортизирующая удары груза в нижнем положении.
Наклонные спуски имеют форму открытых прямолинейных лотков, угол наклона которых к горизонтали должен превышать угол трения штучного груза о поверхность лотка.
Углы наклона спусков: для штучных грузов значительно меньше, чем для насыпных. Если для последних углы наклона спусков превышают 45°, то для первых угол наклона обычно составляет 20...25°.
Для уменьшения скорости выхода штучных грузов с наклонных лотков последние выполняют криволинейными или ломаными в вертикальной плоскости, причем угол наклона к горизонтали верхней части спуска превышает угол наклона нижней; последний в основном равен углу трения груза о поверхность лотка.
Спиральные спуски применяют, например, для перемещения штучных грузов между этажами. При движении груза по спиральному спуску возникает центробежная сила, стремящаяся переместить груз к периферии винтовой поверхности.
Для предохранения груза от сбрасывания центробежной силой применяют винтовые поверхности с вертикальным наружным бортом или винтовые поверхности с наклонной образующей (рис. 22.2, а, б).
Для перемещения грузов под действием силы тяжести способом качения по направляющим применяют скаты.
Различают скаты двух видов:
1 - для грузов круглого сечения (цилиндров, бочек и т. п.), которые сами катятся по ним,
2 - для грузов на тележках, перемещающихся по рельсам.
Направляющие у скатов первого вида выполняют часто из двух параллельно расположенных труб, а у скатов второго вида из рельсов или профильного проката (из швеллеров, уголков и т. п.).
21. Перечислите признаки классификации подъемно-транспортного оборудования. Укажите область применения различного подъемно-транспортного оборудования в пищевой промышленности. Приведите примеры.
Дата добавления: 2018-11-24; просмотров: 987; Мы поможем в написании вашей работы! |
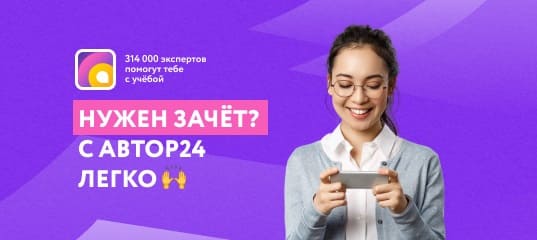
Мы поможем в написании ваших работ!