Ленточный конвейер. Устройство.
Рис.1.
1-выгрузка, 2-привод, 3-приводная секция, 4-опорные ролики, 5-промежуточная секция, 6-лента, 7-натяжная секция, 8-натяжной барабан, 9-загрузка, 10-датчики контроля скорости.
Принцип действия ленточного конвейера
При помощи специальной направляющей воронки или лотка на ленточный агрегат подают сырье. Далее оно поступает до приводного барабана и сгружается с ленты.
Работая на ленточном оборудовании, сотрудники должны придерживаться определенных инструкций:
- Рабочие, обслуживающие ленточные агрегаты для транспортировки сырья, должны быть в подходящей спецодежде и обуви.
- Персонал должен следить за тем, чтобы сырье транспортировалось без просыпания с ленточного устройства.
- Все подшипники нужно равномерно и своевременно смазывать, чтобы они не перегревались. Чтобы транспортировка сырья проходила в штатном режиме, подшипники не должны нагреваться более чем на 50 градусов (сравнивать нужно с окружающей температурой).
- Ленточный конвейер нельзя нагружать более 750 кг/м3.
- После рабочей смены с ленты необходимо счистить все сырье, которое могло остаться там.
Нормальная транспортировка сырья при помощи оборудования невозможна в определенных ситуациях:
- Агрегат плохо закреплен.
- Электропитание подключено к устройству с нарушением правил.
- Агрегат не заземлен.
- При пробном запуске проявилась вибрация или слышны посторонние шумы.
|
|
- Обнаружены следы масляных подтеков из подшипниковых узлов, на корпусе выявлены трещины.
- Пока ленточный агрегат подключен к сети, нельзя проводить никакие манипуляции с электрическим приводом – это смертельно опасно.
12. Опишите стекло, его состав, получение, свойства, применение.
Стекло — Физико-химически — твёрдое тело, структурно — аморфно, изотропно; все виды стёкол при формировании преобразуются в агрегатном состоянии — от чрезвычайной вязкости жидкого до так называемого стеклообразного — в процессе остывания со скоростью, достаточной для предотвращения кристаллизации расплавов, получаемых плавлением сырья (шихты). Температура варки стёкол, от 300 до 2500 °C, определяется компонентами этих стеклообразующих расплавов (оксидами, фторидами, фосфатами и др.).
Состав:
По своей сути, стекло – это не твердое тело в привычном понимании, а жидкая субстанция, которая просто находится в застывшем состоянии. Около 65-70% в составе любого вида стекла занимает кремнезем, он же SiO2. В природе это вещество можно найти в составе песка, кварца и некоторых разновидностей песчаника.
В состав стекла, кварц добавляется в измельченном виде, как кварцевый песок. Для создания стеклянных изделий, пригодны самые различные виды песка, где присутствие сторонних минералов сведено к минимуму. Нежелательно использовать песок со значительными примесями железа, так как это может придать стеклу зеленоватый оттенок.
|
|
Для изготовления стекла следует использовать песок в чистом виде, при этом температура плавления должна быть не менее 1700°С. Такой температуры можно достигнуть лишь в электрической печи, и хотя кварцевое стекло очень термостойкое, его производство зачастую оказывается нерентабельным.
Обычно в состав стеклянного сплава входит сода. Она позволяет снизить температуру плавления и придать массе вязкость, однако в таком случае стекло будет очень неустойчивым. Для того чтобы получить качественное стекло, в смесь соды и песка, дополнительно добавляется известь.
Получение:
Основным сырьем для изготовления стекла являются кварцевый песок, известняк, сода и сульфат натрия. Высококачественные стекольные белые пески содержат немного примесей, в частности оксида железа, придающего стеклу зеленоватую окраску. В стекольную шихту вводят соду, сульфат натрия, поташ, которые понижают температуру варки стекла и ускоряют процесс стеклообразования. При варке смеси чистого песка SiО2 и соды Na2CО3 образуется полупрозрачная стеклообразная масса Na2SiO3, растворяющаяся в воде («растворимое стекло»). Благодаря введению в шихту СаО в виде известняка СаСО3 или доломита стекло становится нерастворимым в воде.
|
|
Варка строительного силикатного стекла производится в стекловаренных печах при температуре до 1500°С. В процессе стекловарения, начиная с температур 800-900°С протекает стадия силикатообразования. К концу следующей стадии стеклообразования (1150-1200°С) масса становится прозрачной, но в ней еще содержится много газовых пузырей. Дегазация заканчивается при 1400-1500 °С, к ее концу стекломасса освобождается от газовых включений, свилей и становится однородной. Для достижения необходимой для формования рабочей вязкости температуру массы снижают на 200-300 °С. Вязкость стекломассы зависит от химического состава: оксиды SiО2, Al2О3, ZrО2 повышают вязкость, Na2О, СаО, Li2О, наоборот, понижают ее.
Переход от жидкого состояния в стеклообразное является обратимым. При длительном нахождении на воздухе и нагревании некоторых стекол обычная для них аморфная структура может переходить в кристаллическую, это явление называют расстекловыванием («заруханием»).
|
|
В процессе изготовления в стекло вводят соединения, придающие ему специальные свойства. Глинозем Аl2О3, вводимый в шихту в виде каолина и полевого шпата, повышает механическую прочность, а также термическую и химическую стойкость стекла. При замене части диоксида кремния борным ангидридом В2О3 повышается скорость стекловарения, улучшается осветление и уменьшается склонность к кристаллизации. Оксид свинца PbO, вводимый, главным образом, при изготовлении оптического стекла и хрусталя, повышает показатель светопреломления. Оксид цинка ZnO понижает температурный коэффициент линейного расширения стекла, благодаря чему повышается его термическая стойкость.
Вспомогательные сырьевые материалы делят по своему назначению на следующие группы: осветлители — вещества, способствующие удалению из стекломассы газовых пузырей (сульфат натрия, плавиковый шпат); обесцвечиватели — вещества, обесцвечивающие стекольную массу; глушители — вещества, делающие стекло непрозрачным.
В 20 в. были разработаны различные способы вытягивания бесконечной ленты стекла. Толщина стекла регулировалась путем изменения скорости вытягивания. При изготовлении витринных и зеркальных стекол тянутое и прокатное стекло подвергали шлифованию и полированию. Только в 1960 г. удалось изготовить стекло, которое полируется в процессе формования ленты стекла на плоской поверхности расплавленного олова. Качество поверхности такого стекла не уступает полированному.
Подготовка сырья
Смесь сырьевых компонентов (куда добавляется стекло для снижения температуры точки плавления) заряжается в топку и разбавляется водой, чтобы отделить нужные компоненты от грязи.
Расплав сырья
В топке процесс производства стекла проходит 3 главные стадии:
- плавка, когда сырье плавится при температуре 1550 С
- очищение, когда расплавленное стекло гомогенизируется (становится однородным) и из него удаляются пузырьки газа;
- смена температурного режима, когда расплав охлаждается до вязкого состояния, удобного для протягивания его через ванну с оловом.
Дата добавления: 2018-11-24; просмотров: 430; Мы поможем в написании вашей работы! |
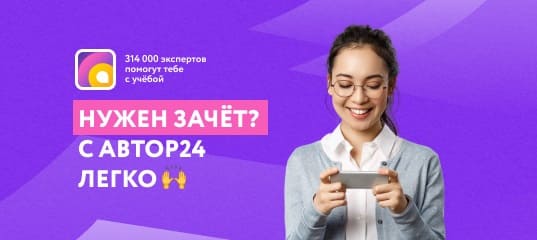
Мы поможем в написании ваших работ!