Определение предела прочности
Пластичных (консистентных) смазок
Пластичные смазки, являясь коллоидными образованиями, могут проявлять механические свойства (табл. 2, 3), характеризуемые рядом признаков, одним из которых является предел прочности.
Под пределом прочности смазки понимается то минимальное давление (напряжение сдвига), которое вызывает разрушение коллоидной структуры каркаса, в результате чего происходит сдвиг смазки и она начинает течь, как вязкая жидкость. Предел прочности определяют с помощью капиллярного пластометра по методу К.И. Климова (рис. 5 и 6).
Предел прочности характеризует способность смазок не вытекать из узлов трения, противостоять сбросу с движущихся деталей (например, с подшипников) под влиянием инерционных сил и удерживаться на наклонных и вертикальных поверхностях, не стекая и не сползая.
Когда напряжение сдвига превышает предел прочности, смазка начинает течь. Предел прочности смазки зависит:
- от температуры (с ее повышением он снижается);
- скорости приложения силы.
Таблица 2. Основные показатели качества пластичных смазок
Описание прибора. Основной частью пластометра (см. рис. 5) является корпус, в который вставляется рабочий капилляр в специальной оправке. Корпус соединен трубкой, нагреваемой электропечкой. Для заполнения масляной системы маслом служит воронка, отключаемая от системы игольчатым краном. Давление в масляной системе замеряется манометром.
|
|
Рабочий капилляр представляет собой разрезанную вдоль оси латунную трубку длиной 50 или 100 мм и внутренним диаметром 4 мм. Внутренняя поверхность капилляра нарезьбована с глубиной резьбы 0,5 мм.
При давлении на смазку вдоль капилляра происходит разрушение структуры смазки и сдвиг смазки по поверхности, образуемой концами резьбы. Давление на смазку осуществляется маслом («жидкий поршень») при завертывании зажимной гайки или подогреве масла в замкнутой масляной системе.
Сущность метода заключается в определении давления, при котором происходит сдвиг смазки в капилляре пластометра при заданной температуре.
Таблица 3. Классификация пластичных смазок
Перед проведением испытаний необходимо:
1. Все детали пластометра, соприкасающиеся со смазкой, промыть бензином и высушить;
2. Цилиндр мешалки 14 (см. рис. 6) заполнить смазкой, не допуская воздушных пустот, и закрыть крышками с двух сторон;
3. Перед установкой верхней крышки отверстие в поршне также заполнить испытуемой смазкой;
4. Мешалку со смазкой выдержать в термостате при температуре 20 ± 1°С в течение 30 мин, после чего перемешать смазку, сообщив поршню 100 двойных ходов;
![]() | ![]() |
5. Поршень поставить в крайнее верхнее положение и снять нижнюю крышку мешалки;
|
|
6. Заполнить длинный капилляр (100 мм), состоящий из двух половин 13, испытуемой смазкой и соединить их;
7. Смазать наружную поверхность капилляра и внутреннюю поверхность оправки;
8. Вставить капилляр в оправку, медленно вращая и поднимая его вдоль оси;
9. Короткий (50 мм) капилляр применить в том случае, когда при испытании на длинном капилляре давление превышает допустимое для манометра;
10. Надеть на нижний обрез буртика оправки резиновую прокладку и установить оправку на выступ в корпусе пластометра 10;
|
|
11. Заполнить пластометр маслом, для чего открыть кран 4 воронки с маслом 5 и держать его открытым, пока уровень масла в корпусе не достигнет верхнего буртика оправки капилляра, следя за тем, чтобы в воронке всегда было масло;
12. Закрепить оправку с капилляром в корпусе 10 гайкой 9. При этом нужно следить за манометром и в случае повышения давления открывать кран воронки;
13. На верхнюю часть корпуса закрепить защитное стекло 8;
14. Поместить корпус пластометра в термостат, уровень жидкости в котором не должен превышать 30 мм верхнего конца капилляра;
15. Заданная температура (20 ± 1°С) должна поддерживаться в течение 29 мин. При этом кран 4 должен быть открытым;
16. Время после перемешивания смазки и до начала испытаний не должно превышать 30–40 мин;
Порядок испытаний:
1. Закрыть кран 4 воронки 5.
2. Включить электропечь 2, обогревающую резервуар 3 с маслом, и наблюдать за манометром 6.
3. Следить, чтобы скорость повышения давления в системе была не более 5 кПа (0,005 кг/см2) в минуту при использовании длинного (100 мм) капилляра 11. Если будет использоваться короткий (50 мм) капилляр 12, то давление в системе должно повышаться со скоростью не более 2,5 кПа (0,025 кг/см2) в минуту.
|
|
4. Скорость повышения давления регулировать подниманием и опусканием электропечи 2 или, не убирая термостат, начинать завертывать зажимную гайку 9 с такой скоростью, чтобы давление повышалось так же, как описано в п.п. 3. При этом резиновая прокладка оправки будет сжиматься и давление в масляной системе будет повышаться.
5. Если при завертывании зажимной гайки созданного давления будет достаточно для разрушения структуры смазки, тогда из капилляра выдавится столбик смазки и давление в масляной системе упадет до нуля.
Испытание прекратить и записать величину достигнутого давления с точностью до 0,01 кг/см2.
6. Если давление, создаваемое завертыванием зажимной гайки, окажется недостаточным для разрушения смазки, то в дальнейшем его повышать подогревом масляной системы электропечью.
7. Вычисляют предел прочности, в кг/см2:
τ = Р·r/(2·l),
где: Р – максимальное давление при разрушении смазки, кг/см2;
r – радиус капилляра, см;
l – длина капилляра, см.
Заключение
1. По результатам анализов заполняют таблицы по установленным формам.
2. Показатели качества оцениваемых образцов, полученные на основании проведенных анализов, необходимо сравнить с показателями ГОСТ (см. табл. 1П) и сделать заключение о пригодности данных образцов к применению в конкретных узлах и агрегатах.
Дата добавления: 2018-11-24; просмотров: 570; Мы поможем в написании вашей работы! |
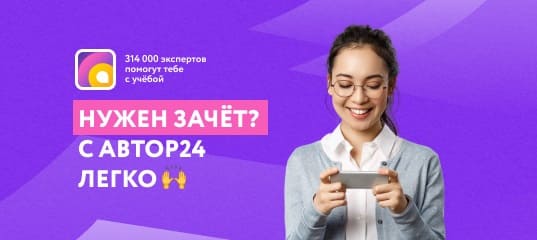
Мы поможем в написании ваших работ!