Сверление отверстий по разметке и рассверливание.
Сверление по разметке выполняется в два приема - пробное (предварительное) сверление, при котором засверливают небольшое углубление для контроля правильности положения сверла, и окончательное сверление после проверки правильности расположения сверла по центру намеченного отверстия.
Для получения отверстий диаметром более 20 мм предварительно сверлят отверстия сверлом меньшего диаметра, а затем рассверливают его под размер сверлом большего диаметра. В этом случае точность сверления значительно больше, а шероховатость поверхности ниже, чем при сверлении одним сверлом.
Диаметр сверла для предварительного сверления должен быть больше длины перемычки сверла, которым будет просверлено заданное отверстие. Сверление производят в следующем порядке.
Размечают и накернивают центр, из которого затем циркулем проводят окружность заданного диаметра; устанавливают сверло в шпиндель станка, пускают станок и проверяют положение сверла на биение, устанавливают и закрепляют деталь на столе станка (в тисках, на угольнике с помощью планок или другим способом). Деталь устанавливают так, чтобы верхняя поверхность с нанесенной разметкой отверстия была горизонтальной, иначе при незначительном перекосе сверло «уведет» в сторону.
Станок настраивают на выбранную частоту вращения шпинделя, выбранную подачу и включают двигатель.
Рассмотрим прием пробного сверления. К месту обработки подводят смазочно-охлаждающую жидкость.
|
|
Ручной подачей сверло подводят к детали и осторожно просверливают отверстие на глубину, равную примерно х/4 диаметра сверла. Затем, подняв сверло, проверяют положение полученной окружности относительно размеченной круговой риски.
В случае эксцентрического расположения отверстия по отношению к разметке, его необходимо выправить. Для этого крейцмейселем с полукруглой режущей кромкой прорубают канавку в сторону, противоположную смещению сверла (рис. 74), измерительной линейкой и разметочным циркулем в прорубленной канавке размечают центр отверстия с последующим засверливанием отверстия.
Окончательное сверление производят после определения правильного расположения отверстия (рис. 75).
При работе с механической подачей начинать сверление следует только с ручной подачи. Механическую подачу надо включать, когда сверло начнет снимать стружку. Если сверлят сквозное отверстие, то при выходе сверла необходимо выключить механическую подачу и перейти на ручную, нажимая на сверло с небольшим усилием.
Рис. 74. Выправление неправильно засверленного отверстия: 1 - контрольная риска; 2 - контур размеченного отверстия 3- неправильно засверленное отверстие; 4 - канавки, надрубленные крейцмейселем.
|
|
Для обеспечения точности рассверливание отверстий производят с одной установки (рис. 76). Для этого из шпинделя станка вынимают сверло меньшего диаметра и вставляют сверло, диаметр которого соответствует диаметру рассверливаемого отверстия. Затем
ручной подачей плавно подводят сверло к отверстию по центру и производят рассверливание.
Рассмотрим порядок проверки качества сверления и рассверливания.
Диаметр отверстия проверяют калибром-пробкой и штангенциркулем, глубину сверления глухих отверстий - глубиномером штангенциркуля, межосевые размеры между отверстиями - штангенциркулем.
Рис. 75. Сверление отверстия по разметке.
Рис. 76. Рассверливание отверстия.
Зенкерование отверстий.
Зенкерование является операцией по обработке готовых отверстий в отливках, штамповках или после сверления для получения отверстий цилиндрической или конической формы большой точности и низкой шероховатости.
Зенкерование выполняется на сверлильных станках специальными инструментами - зенкерами (рис. 77). Цилиндрические зенкеры различных диаметров применяют для получения цилиндрических отверстий.
|
|
Рис. 77. Зенкеры: а - цельный; б - насадной
3. Скорость резания (м/мин) и частота вращения (об/мин) зенкера (углеродистая конструкционная сталь со,= 650 МПа; зенкеры из стали Р18; работа с охлаждением).
Конические зенкеры с углом конуса при вершине 60, 75, 90 и 120° применяют для получения конических углублений. Зенкеры имеют направляющую цапфу, которая входит в отверстие, обеспечивая точность совпадения оси отверстия с цилиндрическим отверстием, образованным зенкером.
Припуск на зенкерование зависит от диаметра зенкера:
Диаметр зенкера D, мм......до 15 15 20 25 30 40 50.
Припуск на сторону, мм...... 0,5 1 1 1,5 1,5 2 2,5.
Зная диаметр, материал, из которого сделан зенкер, и марку обрабатываемого металла, можно выбрать режим резания.
Пример. Выбрать скорость резания и частоту вращения по таблице при зенкеровании просверленного отверстия 0,13 мм на 0,15 мм в углеродистой конструкционной стали в 650 МПа (зенкер D - 15 мм цельный, t = 1 мм, изготовлен из стали Р18; работа с охлаждением; сверлильный станок 2118).
Порядок выбора:
Установив подачу s= 0,2 мм/об и зная D = 15 мм, по таблице находим скорость резания v - 41,6 м/мин и частоту вращения = 883 об/мин.
По кинематической схеме подбираем подходящую частоту вращения шпинделя (735 об/мин), переводим ремень и настраиваем станок на выбранную подачу.
|
|
Коническое зенкерование (рис. 78) производят в определенной последовательности.
1. Выбор конического зенкера производят по конусности головки винта или заклепки, которая должна точно соответствовать углу зенкера. Прежде чем приступить к работе, необходимо проверить наличие всех зубьев зенкера и заостренность режущих кромок.
2. При установке зенкера в шпиндель сверлильного станка учитывают конус на зенкере и конус в шпинделе станка (при необходимости подбирают переходные конусные втулки); протирают конусный хвостовик зенкера и конус шпинделя; вводят хвостовик зенкера в коническое отверстие шпинделя станка так же, как и сверло с конусным хвостовиком; включают электродвигатель и проверяют зенкер на биение. Причинами биения зенкера могут быть изношенность хвостовика или неплотная посадка в конусное отверстие шпинделя.
3. Закреплять деталь на столе станка можно различными способами в зависимости от конфигурации изделия и удобства крепления. При установке детали необходимо обратить внимание на горизонтальное расположение плоскости, точность совпадения оси зенкера с осью выполненного отверстия и надежность закрепления детали.
4.-Операция зенкерования заключается в следующем:
а) включают двигатель станка и, опуская пиноль со шпинделем, зенкер подводят к отверстию детали;
б) при ручной подаче выполняют пробное зенкерование;
в) окончательно обрабатывают отверстие на необходимую глубину. При этом глубину зенкерования определяют по ограничителю или измерительной линейке.
Для получения конической поверхности малой шероховатости зенкерование выполняют при небольшой ручной подаче и с применением охлаждающей жидкости (как и при сверлении).
Цилиндрическое зенкерование (рис. 79) выполняют в той же последовательности, что и коническое, но оно имеет некоторые особенности.
Диаметр цилиндрического зенкера должен быть на 0,2-0,5 мм больше диаметра цилиндрической головки винта. Направляющий конус зенкера должен соответствовать диаметру Винта. При меньшем диаметре направляющего конца зенкера цилиндрическую часть углубления может уводить в сторону.
Рис. 78. Коническое зенкерование отверстий.
Рис. 79. Цилиндрическое зенкерование отверстий.
Точность выполнения цилиндрических углублений проверяют калибром-пробкой, а глубину - глубиномером штангенциркуля (при цилиндрическом зенкеровании). При закладывании в конусное углубление потайной головки винта плоскость головки должна совпадать с плоскостью детали и плотно прилегать к углублению (при коническом зенкеровании).
Дата добавления: 2018-08-06; просмотров: 2812; Мы поможем в написании вашей работы! |
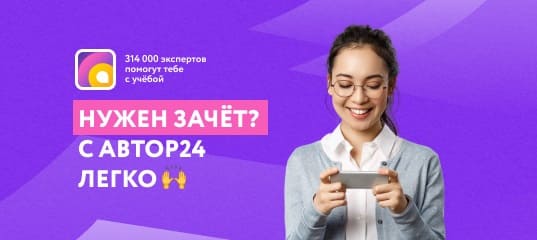
Мы поможем в написании ваших работ!