Конструирование и расчет режущего инстурмента
Фреза- многолезвийный инструмент, представляющий собой тело вращение, на образующей поверхности которого или на торце имеются режущие зубья.
Концевые фрезу используют для обработки плоскостей (цилиндрической частью) и для обработки пазов.
Наладчик-новатор В.Я.Карасев привнес изменения в конструкции фрез: сделал неравномерным окружной шаг (что уменьшает или вовсе уменьшает исключает вибрацию), увеличены высота зуба и радиус основания канавки и уменьшено число до 3-5 (что обеспечивает объем канавки и делает зуб более прочным) и увеличен угол наклона спирали до 45° (что облегчает отвод стружки). Во избежание выкрашивания режущих кромок у торца зубьев фрезы затачивается ленточка шириной 1-3 мм под углом 13° к оси фрезы.
Геометрические параметры концевых фрез
Геометрические параметры фрезы выбираются по рекомендации, исходя из свойств обрабатываемого материала и технологических условий обработки.
Изм. |
Лист |
№ докум. |
Подпись |
Дата |
Лист |
38 12 1 |
ТМК.17.01.09 ПЗ |


|
|
-главный задний угол-угол между главной задней поверхностью фрезы и плоскостью резания. С увеличением заднего угла уменьшается трение и, следовательно, износ зуба по задней поверхности, что увеличивает срок работы фрезы без переточки и улучшает чистоту обработанной поверхности. Однако с увеличением заднего угла уменьшается угол заострения "
", а это приводит к ослаблению зуба и может вызвать поломку (выкрашивание) его при большой стружке.
-угол заострения-этот угол образовывается между передней и задней поверхностью фрезы. Прочность зуба фрезы тем больше, чем больше угол заострения.
=10-55°-угол наклона зубьев фрезы к оси фрезы- это угол, образованный линией, касательной к спирали, и осевой плоскостью. Угол наклона ω винтовой режущей кромки служит для увеличения плавности работы фрезы и для создания направления сходящей стружки.
=10-30°-главный угол в плане угловой кромки фрезы-угол, заключенный между проекцией главной режущей кромки фрезы на осевую плоскость и направлением подачи. Этот угол оказывает влияние на толщину срезаемого слоя (при этой и той же подаче), на соотношение сил, действующих на фрезу, на стойкость фрезы и качество обработанной поверхности. Чем меньше этот угол, тем меньше толщина среза и нагрузка на единицу длины лезвия (при одной и той же подаче), тем выше стойкость фрезы, тем чище обработанная поверхность, но тем больше осевая составляющая сил резания. Поэтому работа фрезой с
рекомендуется при глубине резания не выше 3-4 мм.
|
|
Для упрочнения вершинки зуба фрезы и для получения более одинаковых элементов у всех ее зубьев, у фрез делается обычно переходная кромка f =1…2 мм, направленная под углом 0 =1/2
.
1 –вспомогательный угол в плане делается для уменьшения побочного резания и трения вспомогательной режущей кромки об обработанную поверхность.
-угол наклона главной режущей кромки влияет на прочность и стойкость зуба. При положительном значение головка зуба фрезы делается более массивной и в меньшей степени подвергается разрушению вершина режущей кромки, так как с увеличением положительного значения угла
место входа (место удара) зуба фрезы отодвигается от вершины зуба, являющейся наиболее слабой и ответственной частью. Положительное значение угла
способствует и более плавному входу зуба в заготовку и выходу из нее. Однако при увеличении угла +
уменьшается продольный передний угол, что привод к большим силам при резании и большому расходу мощности.
|
|
Изм. |
Лист |
№ докум. |
Подпись |
Дата |
Лист |
39 12 1 |
ТМК.17.01.09 ПЗ |
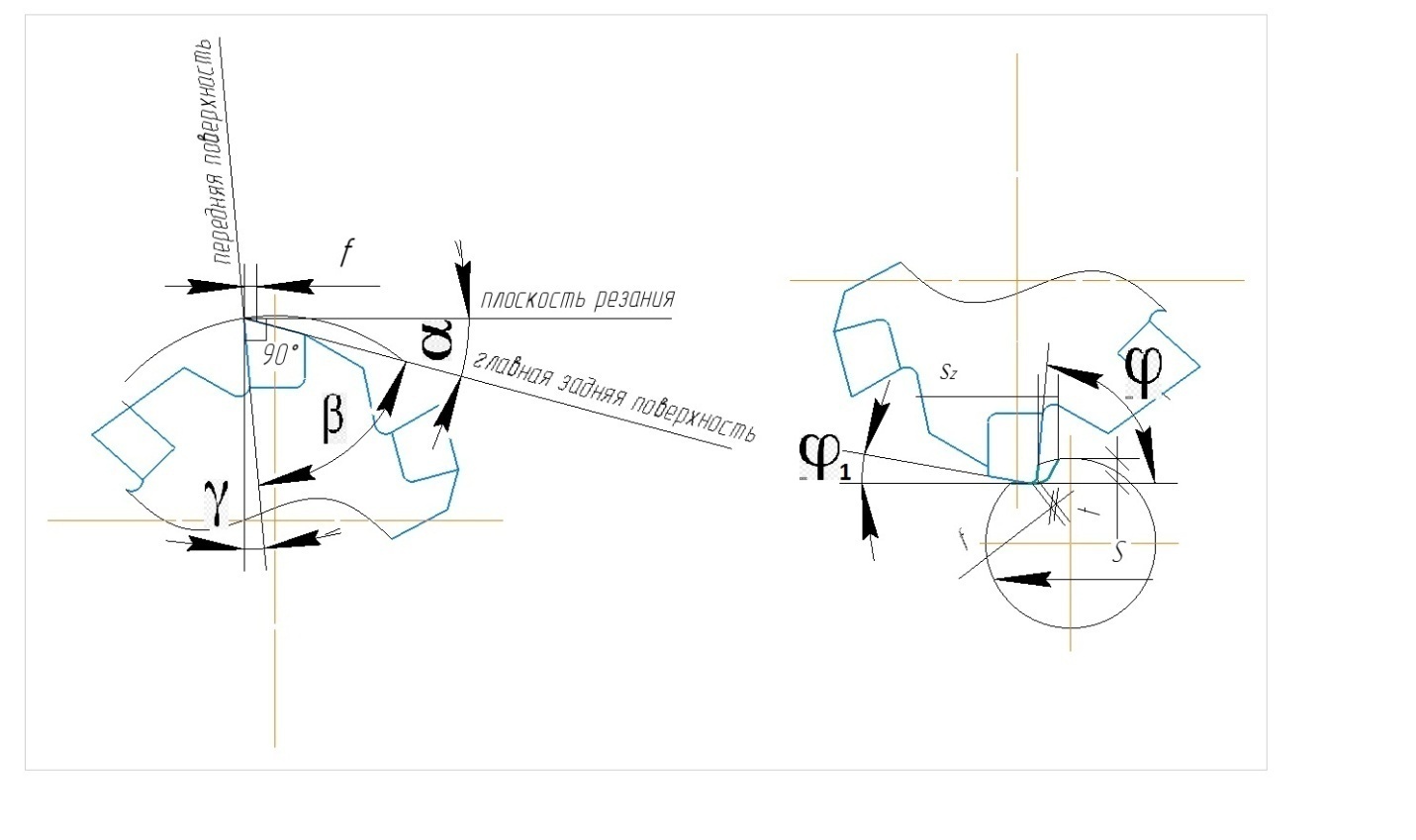
Рисунок 7 Конструкция концевых фрез
Рисунок 8 Схема переточки по задней поверхности
Изм. |
Лист |
№ докум. |
Подпись |
Дата |
Лист |
40 12 1 |
ТМК.17.01.09 ПЗ |
Основными критериями затупления режущей кромки являются ухудшение качества обработанной поверхности, шум при работе, вибрации. В этом случае фрезу необходимо переточить. Перетачивать фрезы рекомендуется на станках с ЧПУ. В зависимости от типа износа и геометрии зуба, переточка осуществляется по задней, передней или обеим поверхностям.
|
|
Рисунок 9 Схематично показаны различные типы износа зуба концевой фрезы
Переточка по задней поверхности
По задней поверхности зуб фрезы перетачивается, как только величина износа достигла регламентированной ширины. В этом случае возможна переточка без значительного уменьшения диаметра фрезы. В большинстве случаев зуб фрезы затачивается по двойной прямолинейной поверхности, образуя главный задний угол α1 и вспомогательный задний угол α2. Переточка производится по ленточке износа, заново формируя главный задний угол. Задняя поверхность формируется плоским заточным кругом, установленного таким образом, чтобы ось круга была под некоторым углом к оси фрезы. Угол α1 зависит от угла наклона заточного круга.
Расчет на прочность фрезы
Диаметр оправки (отверстия фрезы) можно рассчитать исходя из сил, действующих на фрезу. Диаметр отверстия под оправку рассчитывается по формуле:
;
где:
=25 кгс×мм –суммарный момент при изгибе и скручивании оправки;
=25 кгс/мм2 –допустимое напряжение на изгиб оправки для
конструкционных сталей (180…250 МПа ×106 ) 18..25 кгс/мм2 ;
=
=314 кгс×мм-
суммарный момент при изгибе и скручивании оправки;
где:
P=1,411 H-равнодействующая сил
;
=78,65 H- тангенциальная составляющая сила резания;
D=8 мм-диаметр фрезы;
l=35 мм-расстояние между опорами фрезерной оправки (длина посадочного
участка оправки);
Изм. |
Лист |
№ докум. |
Подпись |
Дата |
Лист |
41 12 1 |
ТМК.17.01.09 ПЗ |
Определение окружного шага зубьев фрезы:
5,02 мм;
Определение окружного шага зубьев фрезы при =20°-угол наклона винтовой
канавки, 2,75
=5,02×2,75=13,82 мм
Проверка величин z и на условие равномерного фрезерования:
-это число должно быть целым или величиной, близкой нему,
полученное значение обеспечивает условие равномерного фрезерования.
Изм.
Лист
№ докум.
Подпись
Дата
Лист
42
12
1
3.2 Конструирование и расчет мерительного инструмента ТМК.17.01.09 ПЗ
Определить исполнительные размеры рабочих и контрольных калибров-скоб для вала диаметром D=12 мм с полем допуска f7 ( ).
Наибольший и наименьший предельные размеры вала:
=11,984 мм;
=11,966 мм
В разделе 4 ГОСТ 24853— 81 для квалитета 7 и интервала 10— 18 мм находим
данные для расчета искомых калибров:
=0,0025 мм
=0,002 мм
=0
=0,003 мм
=0,0012 мм
Расчет размеров калибров производится по формулам, находящимся в разделе 3
ГОСТ 24853— 81.
Расчет рабочих калибров-скоб:
Проходная сторона новая рассчитывается по формуле:
11,984-0,0025 ± =11,9815±0,0015 мм;
На чертеже скобы проставляется размер
Проходная сторона изношенная рассчитывается по формуле:
11,984+0,002=11,986
Непроходная сторона рассчитывается по формуле:
11,966± =11,966±0,0015
На чертеже скобы проставляется размер
Изм. |
Лист |
№ докум. |
Подпись |
Дата |
Лист |
43 12 1 |
ТМК.17.01.09 ПЗ |
Проходная сторона новая рассчитывается по формуле:
11,984-0,0025 ± =11,9821 ±0,0006 мм;
Проходная сторона изношенная рассчитывается по формуле:
11,984+0,002± =11,986±0,0006 мм;
Непроходная сторона рассчитывается по формуле:
11,966± =11,966±0,0006 мм;
Рисунок 10 Схема полей допусков измеряемого вала и исполнительных размеров рабочих и контрольных калибров-скоб
Изм.
Лист
№ докум.
Подпись
Дата
Лист
44
12
1
3.3 Конструирование и расчет приспособления ТМК.17.01.09 ПЗ
Фрезерное приспособление проектируется для учебных целей.
Назначение приспособления
Фрезерное приспособление с ручным зажимом (гайка с шайбой) предназначен для фрезерных работ.
Схема сборки и разборки приспособления
Приспособление фрезерное состоит из корпуса (1) 325×155×11, на который приваривают опору (14) под гидроцилиндр (13), который в свою очередь прикручивается четырьмя болтами (3). Гидроцилиндр стоит из штока, опоры (15) и стопорной гайки (7). На поверхность корпуса приваривается площадка под призму (16) и стойка под установ (17). Две призмы фиксируются на четырех винтах (5,6) и на четырех штифтах (19,20). Штифт (21) запрессовывается в корпус (1). В стойку ввертывается шпилька (12) и насаживается пружина (9), затем устанавливается шайба (11), прихват (2), надевается шайба (10) и закручивается гайкой (8). В основании, для ориентации шпонок приспособления, ввинчивается винт (4) в шпонку (18).
Лишение детали 6 степеней свободы
Базирование детали на двух призмах (16) лишает четырех степеней свободы, штифт (21) лишает 5 степень.
Принцип работы
Деталь устанавливается на две призмы (16) и левым торцом поджимается к штифту (21). Затем прихватом (2) деталь поджимается сверху. Обработка начинается при настройки фрезы с «первого касания» щупа на установе «17».
Центрирование приспособления
Для ориентации приспособления имеются две шпонки (18).
Зажимные элементы приспособления
Приспособление состоит из следующих элементов: установочные-две призмы (16) и штифт (21) ;зажимные элементы-прихват(2), гайка(8), шайба(10), гидроцилиндр (13); направляющие элементы-установ (17);второстепенных и делительных элементов нет.
Изм. |
Лист |
№ докум. |
Подпись |
Дата |
Лист |
45 12 1 |
ТМК.17.01.09 ПЗ |
Составление уравнения проекции сил на ось Х:
Рисунок 11 Составление уравнения проекции сил на ось Х
где:
k-коэффициент запаса прочности;
коэффициент трения(f×N=0,25).
Выбор значения коэффициента надежности К:
;
где:
-коэффициент, гарантированного запаса надежности закрепления (
;
-коэффициент, учитывающий увеличение силы резания из-за неровностей
на заготовках ( );
коэффициент, учитывающий увеличения силы резания вследствие
затупления инструмента ( =1,4);
-коэффициентувеличения силы резания при прерывистом резании(
;
-коэффициент непостостоянства зажимного усилия (
;
-
удобства расположения рукояток в ручных зажимных
устройствах ( ;
-коэффициент неопределенности неровностей места контакта заготовки с
опорным элементом ( ;
;
;
Изм. |
Лист |
№ докум. |
Подпись |
Дата |
Лист |
46 12 1 |
ТМК.17.01.09 ПЗ |

где:
=71,5 Н- осевая составляющая сила;
где:
где:
мм-диаметр, на котором фрезеруется шпоночные пазы;
-равнодействующая усилия;
Расчет усилия гидроцилиндра
Рисунок 13 Расчет усилия гидроцилиндра
Изм. |
Лист |
№ докум. |
Подпись |
Дата |
Лист |
47 12 1 |
ТМК.17.01.09 ПЗ |

где:
-исходное усилие, развиваемое гидроцилиндром, в Н;
D-диаметр поршня, в мм;
р-давление масла в гидроцилиндре, в МПа(6 бар= ;
-коэффициент полезного действия (
-при уплотнении манжетами).
Вывод: -зажим приспособления является надежным.
Изм.
Лист
№ докум.
Подпись
Дата
Лист
48
12
1
Заключение ТМК.17.01.09 ПЗ
В результате выполненного курсового проекта были проведены, все необходимые расчеты по разработке технологического процесса детали типа валик.
В первой части было выполнено описание данной детали, принадлежащей к классу валов, подклассу валикам. Было описана конструкция и ее назначение, а также выбрана характеристика материала. К данной детали предъявляются высокие требования по шероховатости и точности изготовления, а также высокие требования по радиальному биению поверхностей, имеется центральное глубокое отверстие малого диаметра. Выполнен был и анализ детали на технологичность с целью определения сложности ее изготовления, было выявлено, что деталь является нетехнологичной, и ее можно отнести к трудоемким, так как имеет сложную технологию изготовления.
Во второй части для данной детали были выполнены следующие пункты: тип производства (среднесерийное), выбор заготовки (прокат трубы), определение припусков табличным методом, обоснование баз, маршрут обработки детали, анализ заводского технологического процесса, принятый маршрут обработки детали, выбор оборудования, выбор режущего/вспомогательного/мерительного инструмента и приспособления, расчет режимов резания (на две операции 010 и 030), нормирование операций (на две операции 010 и 030), расчет управляющей программы на станок с ЧПУ (операция 030 на первый установ, без фрезерной части). Для увеличения производительности технологического процесса было предложено: объединить две токарно-револьверные с ЧПУ операции (040 и 050) в одну, так как имеется возможность применения более производительного оборудования (токарно-револьверный станок с ЧПУ CTX Alpha 500 из серии CTX). Такой станок обладает в качестве дополнительной опции-противошпиндель (задний шпиндель), который позволяет расширить технологические возможности при обработке различных деталей любой сложности, повышая при этом в несколько раз производительность производственного процесса. Общий вывод по второй главе: было разработано и подобрано оптимальное технологическое решение.
В третьей части, конструкторской, было проведено конструирование и расчеты режущего, мерительного инструмента, а также конструирование приспособления. Вывод по третьей части: были сконструированы режущий (фреза концевая диаметром 8), мерительный (калибр-скоба диаметром 12f7) инструменты и спроектировано станочное приспособление фрезерное (для учебных целей) для фрезерования двух небольших пазов. Также были проведены расчеты режущего инструмента на прочность, которая применяется на операции 030;мерительного на исполнительные размеры рабочих и контрольных калибр-скоб: проходная (новая и изношенная) и непроходная сторона, которая используется в измерениях на операции 085,105 и 145.
Подводя итог, можно сказать, что много было проделано работы для достижения цели курсового проекта: разработка оптимального технологического процесса изготовления детали «Валик управления».
Список литературы
1. Аршинов В А., Алексеев Г.А. "Резание металлов и режущий инструмент". Изд.3-е. М.: Машиностроение, 1975
2. Балабанов А.Н. "Краткий справочник технолога машиностроителя" – М.,1992
3. Белоусов А.П. "Проектирование станочных приспособлений" – М., 1980
4. Горбацевич А.Ф., Шкред В.А. "Курсовое проектирование по технологии машиностроения" – М.,1983
5. Единая система допусков и посадок в машиностроении и приборостроении. Справочник Том 2. Контроль деталей – М., 1989
6. Косилова А.Г. "Справочник технолога-машиностроителя" том 2 – М., 1986
7. Нефедов Н.А., Осипов К.А. "Сборник задач и примеров по резанию металлов и режущему инструменту". - М.1990
8. Общемашиностроительные нормативы времени и режимов резания для нормирования работ, выполняемых на универсальных и многоцелевых станках с числовым программным управлением Часть1 "НОРМАТИВЫ ВРЕМЕНИ"- М., 1990
9. "Обработка металлов резанием. Справочник технолога" Г.А.Монахов, В.Ф.Жданович, Э.М.Радинский и др./Под ред. Г.А.Монахова.
М,: Машиностроение,1974
10. Панов А.А. "Обработка металлов резанием". – М., 1990
11.
Изм. |
Лист |
№ докум. |
Подпись |
Дата |
Лист |
49 12 1 |
ТМК.17.01.09 ПЗ |
12. ГОСТ 14.004-83. Технологическая подготовка производства. Термины и определения основных понятий
13. ГОСТ 25142-82 Шероховатость поверхности. Термины и определения
14. ГОСТ 2789-73 Шероховатость поверхности. Параметры и характеристики
15. ГОСТ 2.308-2011 ЕСКД. Указание допусков формы и расположения поверхностей
16. ГОСТ 2.309-73 ЕСКД. Обозначение шероховатости поверхности
17. ГОСТ 166-89. Штангенциркули. Технические условия
18. ГОСТ 2216-84. Калибры-скобы гладкие регулируемые. Технические условия
19. ГОСТ 21401-75. Калибры гладкие для размеров до 500 мм. Исполнительные размеры
20. ГОСТ 18880-73. Резцы токарные подрезные отогнутые с пластинами из твердого сплава. Конструкция и размеры
21. ГОСТ 2209-90. Пластины твердосплавные напаиваемые для режущего инструмента. Технические условия
22. ГОСТ 30893.1-2002. Основные нормы взаимозаменяемости. Общие допуски. Предельные отклонения линейных и угловых размеров с неуказанными допусками
23. ГОСТ 30893.2-2002 Основные нормы взаимозаменяемости. Общие допуски. допуски формы и расположения поверхностей, не указанные индивидуально
24. ГОСТ 6636-69 Основные нормы взаимозаменяемости. нормальные линейные размеры
25. ГОСТ 8908-81 Основные нормы взаимозаменяемости. нормальные углы и допуски углов
26. ГОСТ 3.1118-82. Единая система технологической документации (ЕСТД). Формы и правила оформления маршрутных карт
Изм. |
Лист |
№ докум. |
Подпись |
Дата |
Лист |
50 12 1 |
ТМК.17.01.09 ПЗ |
27. https://booktech.ru/ «Поиск. Техническая литература»
28. http://stanki-katalog.ru/ «Каталог станков»
29. https://technopolice.ru/tools/ «Режущий инструмент от Технополиса»
30. Статья на тему: «Технологи машиностроения: творцы машиностроения»
http://www.stolichnoe-obrazovanie.ru/professiya/878-texnologi-mashinostroeniya-
tvorczy-czivilizaczii/
31. Видео-канал на Youtube «Веселый инженер»:
https://www.youtube.com/channel/UCAZ5lcoZ3rSglDncOdHJcvQ
32. Блок инженера технолога:
http://mextexnologii.ru/
Дата добавления: 2021-02-10; просмотров: 157; Мы поможем в написании вашей работы! |
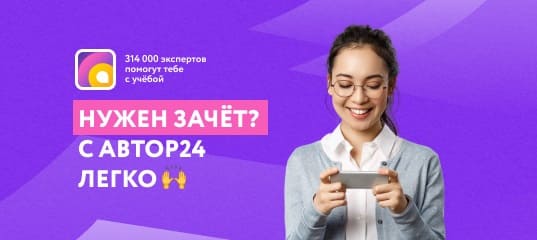
Мы поможем в написании ваших работ!