Принятый маршрут обработки детали
005 Входной контроль; 010 Токарная; 015 Доводочная; 016 Отмочка; 017 Промывка; 020 Круглошлифовальная; 025 Токарная; 030 Токарно-револьверная с ЧПУ; 035 Слесарная; 040 Доводка; 041 Отмочка; 042 Промывка; 045 Контрольная; 050 Азотирование; 055 Слесарная; 060 Доводочная; 061 Отмочка; 062 Промывка; 065 Круглошлифовальная; 070 Круглошлифовальная; | 075 Круглошлифовальная; 080 Круглошлифовальная; 085 Круглошлифовальная; 090 Круглошлифовальная; 095 Круглошлифовальная; 100 Слесарная; 105 Контрольная; 110 Маркировочная; 115 Контрольная; 120 Зубофрезерная; 125 Слесарная; 130 Проверка на отсутствие прижогов; 135 Проверка на отсутствие трещин; 140 Доводка; 141 Отмочка; 142 Промывка; 145 Контрольная; 150 Покрытие Хим.Пас; 155 Покрытие ВАП-2; 160 Контрольная; 165 Консервация и упаковка. |
Изм.
Лист
№ докум.
Подпись
Дата
Лист
17
12
1
2.7 Выбор оборудования ТМК.17.01.09 ПЗ
Рисунок 2 – Станок токарно-винторезный универсальный ИЖ 250
для операций: 010,025
Применение: станок токарно-винторезный универсальный модели 16К20 предназначен для выполнения самых разнообразных токарных работ, а также для нарезания метрической, дюймовой и питчевой резьб.
Таблица 9 – Технические характеристики токарно-винторезного станка ИЖ 250
Наименование параметров | Ед. изм. | Величины |
Основные параметры | ||
Максимальный диаметр точения над станиной | мм | 200 |
Максимальный диаметр точения над суппортом | мм | 125 |
Максимальная длинна заготовки (РМЦ) | мм | 500 |
Высота оси центров над плоскими направляющими станины | мм | 150 |
Высота от опорной поверхности резца до линии центров | мм | 20 |
Шпиндель | ||
Диаметр отверстия в шпинделе | мм | 33 |
Максимальный диаметр прутка в главном шпинделе | мм | 30 |
Частота вращения шпинделя в прямом направлении | об/мин | 16…2000 |
Число ступеней частот прямого вращения шпинделя | кол-во | 22 |
Подачи | ||
Наибольшая длина хода каретки суппорта | мм | 500 |
Наибольшее поперечное перемещение суппорта | мм | 150 |
Цена деления лимба продольного перемещения суппорта | мм | 0,05 |
Цена деления лимба поперечного перемещения суппорта | мм | 0,05 |
Габаритные размеры и масса станка | ||
Габариты станка (длина ширина высота) | мм | 2030 × 875 × 1220 |
Масса станка | кг | 1570 |
Изм.Изм. |
ЛистЛист |
№ докум.№ докум. |
ПодписьПодпись |
ДатаДата |
ЛистЛист |
18 3 13 12 1 |
ТМК.17.01.09 ПЗ ТМК17.01.09 ПЗ |
|
|
Изм. |
Лист |
№ докум. |
Подпись |
Дата |
Лист |
19 12 1 |
ТМК.17.01.09 ПЗ |
|
|
Рисунок 3 – Станок круглошлифовальный универсальный В-88
для операций: 020,065,070,075,080,085,090,095
Применение: универсальный круглошлифовальный станок В-88 предназначен для наружного и внутреннего шлифования цилиндрических и конических поверхностей деталей.
Таблица 10 – Технические характеристики круглошлифовального универсального станка В-88
Наименование параметров | Ед. изм. | Величины |
Основные параметры | ||
Наибольший диаметр обрабатываемого изделия | мм | 140 |
Наибольшая длина обрабатываемого изделия | мм | 180 |
Максимальная длинна обработки наружных поверхностей | мм | 180 |
Наибольший диаметр шлифования | мм | 0…40 |
Высота центров передней бабки над столом | мм | 95 |
Станина и стол станка | ||
Скорость автоматического перемещения стола (от гидросистемы) | м/мин | нет |
Наибольший угол поворота верхнего стола по часовой стрелке | град. | 10 |
Наибольший угол поворота верхнего стола против часовой стрелки | град. | 90 |
Перемещение шлифовальной бабки во время быстрого подвода | мм | нет |
Цена деления лимба поперечной подачи на диаметр изделия | мм | 0,0025 |
Электрооборудование станка | ||
Количество электродвигателей на станке | кол-во | 4 |
Габаритные размеры и масса станка | ||
Габариты станка (длина×ширина×высота) | мм | 1140×920×1350 |
Масса станка с электрооборудованием и охлаждением | кг | 580 |
|
|
Изм. |
Лист |
№ докум. |
Подпись |
Дата |
Лист |
20 12 1 |
ТМК.17.01.09 ПЗ |
Рисунок 4 – Станок токарно-револьверный с ЧПУ CTX Alpha 500
для операции: 030
Применение: токарно-револьверный станок с ЧПУ CTX Alpha 500 из серии CTX предназначен для выполнения комплексной (токарной и фрезерной) 2-х, 3-х, 4-х и 5-и осевой обработки деталей малых и средних размеров в автоматическом или полуавтоматическом режиме. Данный станок может иметь одну, две и даже три револьверные головки с большим количеством разнообразных инструментов (резцов, сверл, зенкеров, фрез, метчиков и др.), а также может иметь в качестве дополнительной опции - противошпиндель, который позволяет расширить технологические возможности при обработке различных деталей любой сложности, повышая при этом производительность производственного процесса.
Таблица 11 – Технические характеристики токарно-револьверного станка с ЧПУ CTX Alpha 500
Наименование параметров | Ед. изм. | Величины |
Рабочая зона станка | ||
Максимальный диаметр заготовки | мм | 500 |
Максимальный диаметр точения над станиной | мм | 240 |
Максимальный диаметра при обработке в центрах | мм | 500 |
Главный шпиндель | ||
Максимальный частота вращения шпинделя | об/мин | 6000 |
Мощность (длит.вкл. 100%) | кВт | 13 |
Ускоренный ход | ||
Максимальный ход по оси Х | м/мин | 30 |
Максимальный ход по оси Y | м/мин | 22,5 |
Максимальный ход по оси Z | м/мин | 30 |
Противошпиндель (опция) | ||
Максимальная частота вращения шпинделя | об/мин | 6000 |
Мощность | кВт | 12 |
Револьверная головка (стандартное исполнение) | ||
Число инструментальных позиций по VDI/DIN 69880 | кол-во | 12 |
Кол-во приводных инструментов | кол-во | 12 |
Мощность (длит.вкл. 100%) | кВт | 3 |
Максимальная частота вращения | об/мин | 500 |
|
|
Изм. |
Лист |
№ докум. |
Подпись |
Дата |
Лист |
21 12 1 |
ТМК.17.01.09 ПЗ |
Рисунок 5 – Зубофрезерный станок Hamai 120
для операции: 120
Применение: зубофрезерный станок Hamai 120 предназначен для изготовления: прямозубых и косозубых зубчатых колёс; червяков, шнеков и червячных колёс, червячных секторов; звёздочек; а так же шлицов и мелкомодульных зубчатых соединений.
Таблица 12 – Технические характеристики зубофрезерного станка Hamai 120
Наименование параметров | Ед. изм. | Величины |
Максимальный рабочий диаметр | мм | 120 |
Максимальная фрезерная длина | мм | 160 |
Максимальная рабочая длина | мм | 210 |
Максимальный модуль | - | 2 |
Количество зубьев | кол-во | 6 до 325 |
Винтовой редуктор | мм | 7,6-3900 |
Винтовой угол | град | 0-70 |
Размер фрезы | мм | 32×10×25 |
Скорость фрезы | об/мин | 200-1500 |
Скорость фрезерования | мм/об | 0,13-9 |
Главный двигатель | кВт | 1,5 |
Габариты станка (длина ширина высота) | мм | 1120×520×1413 |
Масса станка | кг | 900 |
Изм.
Лист
№ докум.
Подпись
Дата
Лист
22
12
1
2.8 Выбор технологического оснащения ТМК.17.01.09 ПЗ
Таблица 13 – Выбор режущего, вспомогательного, мерительного инструмента и приспособления
Режущий инструмент | |
№ операции | Инструмент |
010 | резец проходной отогнутый правый 2102-1106 Т15К6 ГОСТ 18877-73 |
015,040,060,140 | притир |
020,065,070,075,080 085,090,095 | шлифовальные круги: 7.600×80×305 25AF904 1.250×2×75 25AF904 1.250×8×75 25AF904 1.250×32×75 25AF904 |
025 | резец подрезной с напаянной пластиной 2101-0007 ВК6 ГОСТ 18879-73 |
030 | резец проходной (для черновой обточки) CNMG 1204-04-GS PC8110 Пластина Korloy DCL NL 2020-K12 Державка Korloy резец проходной (для чистовой обточки) CNGG 120402-ML TT15080 Пластина Taegu Tec TCL NR 2020-K12 Державка Taegu Tec резьбовой резец 3ER 1,5 ISO VTX Пластина Vargus AL20-3 Державка Vargus шпоночная двухперая фреза UNTM2/2.0200 HA0500 Технополис фреза концевая UR03M4.0600 Технополис канавочный резец PENTA24N230J050 Пластина ISCAR PCHL-12-24-JHP Державка ISCAR канавочный резец PENTA24N050J000 Пластина ISCAR PCHL-12-24-JHP Державка ISCAR канавочный резец 313.00235.47 Пластинка Horn М313.ST10.01A Державка Horn |
035,055,100,125 | шкурка 15АМ50 |
110 | электрограф ГОСТ 18620-86 |
120 | червячная фреза m=0,4 32х13х16 класс АА Р18 2510-4449 ГОСТ 10331-81 |
продолжение таблицы 13 | |
Вспомогательный инстурмент | |
030 | оправка под шпоночную фрезу |
120 | оправка под червячную фрезу |
Приспособления | |
010 | 3х кулачковый патрон 70100-0001 ГОСТ 2675-80 центр А-1-4-НГОСТ 8742-75 центр 7032-0013 Морзе 4ГОСТ 13214-79 |
015,040,060,140 | паста М28-Т ГОСТ 25593-83 |
020,065,070,075,080 085,090,095 | центр А-1-4-НГОСТ 8742-75 центр 7032-0013 Морзе 4ГОСТ 13214-79 поводковый патрон 7108-0021 ГОСТ 2571-71 |
025 | 3х кулачковый патрон 70100-0001 ГОСТ 2675-80 |
030 | 3х кулачковый патрон 70100-0001 ГОСТ 2675-80
центр А-1-4-НГОСТ 8742-75
центр 7032-0013 Морзе 4ГОСТ 13214-79
поводковый патрон 7108-0021 ГОСТ 2571-71
спец.оправка под глубокое отверстие ![]() |
120 | центр А-1-4-НГОСТ 8742-75
центр 7032-0013 Морзе 4ГОСТ 13214-79
спец.оправка под глубокое отверстие ![]() |
Измерительные инстурменты | |
010,025 | штангенциркуль ШЦ-1-125-0,1 ГОСТ 166-89 |
015,040,060,140 | пневмодлиномер |
020,065,070,075,080 085,090,095 | штангенциркуль ШЦ-1-125-0,01 ГОСТ 166-89 биениемер Б-10М индикатор 2МИГ ц.д.0,002 ПБМ-200 штатив ШМ-2 миникатор ИРПВ ц.д.0,002 плита поверочная 400×400 |
Изм. |
Лист |
№ докум. |
Подпись |
Дата |
Лист |
24 12 1 |
ТМК.17.01.09 ПЗ |
030,045,105,115,145 | штангенциркуль ШЦ-1-125-0,01 ГОСТ 166-89 калибр-скоба Ø14f7 8118-0003 ГОСТ 2216-84 калибр-скоба Ø12f7 8118-0003 ГОСТ 2216-84 калибр-скоба Ø11h8 8118-0003 ГОСТ 2216-84 калибр-кольцо для резьбы М12×1,5-6e ГОСТ 24997-81 радиусный шаблон радиусный шаблон для R2,35 микрометр МК 25 ГОСТ 6507-90 биениемер Б-10М индикатор ИЧ 10 ц.д 0,01 идикатор ИЧ10 ц.д.0,001 ПБМ-200 штатив ШМ-2 миникатор ИРПВ ц.д.0,002 плита поверочная 400×400 |
Изм.
Лист
№ докум.
Подпись
Дата
Лист
25
12
1
2.9 Расчет режимов резания ТМК.17.01.09 ПЗ
010 Токарная
Переходы:
1.УЗС;
2. Точить поверхность до кулачков;
3.Повернуть деталь на 180°;
4.Точить поверхность до кулачков;
5. Контроль;
Расчетные данные:
1. Чертеж детали «Валик управления»;
2. Оборудование «ИЖ 250»;
3. t = 1,5 мм-глубина резания;
4. S=0,4 мм/об – подача ;
5. Переход: 2.Точить поверхность до кулачков.
1) =
-скорость резания;
где:
=360,2 м/мин – скорость резания;
Сv= 350-поправочный коэффициент,
x=0,15,y= 0,35,m=0,20 – показатели степени в формуле скорости резания;
T= 60 –период стойкость инструмента;
Kv= 0,85 – поправочный коэффициент состоящий из произведения
коэффициентов:
где:
=0,65-коэффициент, учитывающий качество обрабатываемого материала,
определяется по формуле:
;
где:
-показатель степени обработки инструментом (для резца из тв.сплава-1,0);
;
Knv= 1,0 - коэффициент учитывающий состояние поверхности заготовки;
Kuv= 1,9 - коэффициент учитывающий материал инструмента;
=770 МПа-предел текучести для данного материала;
2) =
= 6037,55 об/мин-число оборотов шпинделя;
Изм. |
Лист |
№ докум. |
Подпись |
Дата |
Лист |
26 12 1 |
ТМК.17.01.09 ПЗ |
=360,2 м/мин – скорость резания;
D=19,0 мм-диаметр, получаемый при точении;
=3,14-постоянная;
Принимаем = 1500 об/мин-число оборотов шпинделя;
3) =
= 89,49 м/мин- действительная скорость резания;
где:
=3,14-постоянная;
D=19,0 мм-диаметр, получаемый при точении;
=1500 об/мин-число оборотов шпинделя;
4) =
= 0,73 кВт - мощность резания;
где:
Pz=10 Cp
tx
Sy
n
Kp= 10
300
1,51,0
0,40,75
156-0,15
0,93 =989,9 H-
тангенциальная составляющая сила;
где:
Ср=300 – поправочный коэффциент;
х=1; y=0,75;n=-0,15 – показатели степени;
Кр=0,93– поправочный коэффициент состоящий из произведения
коэффициентов:
Кр=Кмр
Кg р
Кl р
Кr р= 1,18
1
1
1
1=0,93;
где:
=
=1,18- поправочный коэффициент, учитывающий
влияние качества обрабатываемого материала на силовые зависимости;
где:
=770 МПа-предел текучести для данного материала;
-показатель степени обработки инструментом (для резца из тв.сплава-1,0);
-общие поправочные коэффициенты (1,0);
5) =
=0,86 кВт - мощность двигателя;
где:
КПД ( =0,85) должно согласовываться с условием
-условие
выполняется
6) =
1,0= 0,1 мин- основное машинное время;
Изм. |
Лист |
№ докум. |
Подпись |
Дата |
Лист |
27 12 1 |
ТМК.17.01.09 ПЗ |
L=60 мм– расчётная длина обработки, мм;
l=120 мм– длина обработки детали, мм;
l 1= 1,0 мм– длина врезания, мм;
i=1,0 – число проходов.
Таблица 14 – Основное машинное время на операцию 010, мин
То2 | То4 |
0,1 | 0,4 |
То= То2+ То4=0,1+0,4=0,5 мин -общее основное машинное время на операцию 010.
030 Токарно-револьверная с ЧПУ
Переход:
6.Фрезеровать паз , выдерживая размеры
.
Расчетные данные:
1. Чертеж детали «Валик управления»
2. Оборудование «CTX Alpha 500»;
3. t=1,1 мм-глубина шпоночного паза;
4. B=2 мм-ширина шпоночного паза;
5. =0,1 мм/на зуб-подача на 1 зуб фрезы;
6.
Переход: 6.Фрезеровать паз , выдерживая размеры
1) м/мин-скорость
резания;
где:
=8,2 м/мин – скорость резания;
Сv= 12-поправочный коэффициент,
q=0,3,x=0,3, y=0,25, u=0, p=0, m=0,26-показатели степени в формуле скорости
резания;
T= 80 –период стойкость инструмента;
коэффициентов;
D=2 мм-диаметр фрезы;
t=1,1 мм-глубина резания;
=0,1-подача на 1зуб фрезы;
B=2,0 мм-ширина шпоночного паза;
Z=2,0-количество зубьев;
Kv= 1,0 – поправочный коэффициент состоящий из произведения
коэффициентов:
Изм. |
Лист |
№ докум. |
Подпись |
Дата |
Лист |
28 12 1 |
ТМК.17.01.09 ПЗ |
=0,65-коэффициент, учитывающий качество обрабатываемого материала,
определяется по формуле:
;
где:
-показатель степени обработки инструментом (для фрезы из быстр.сплава-
0,9);
;
Knv= 0,9 - коэффициент учитывающий состояние поверхности заготовки;
Kuv= 1,0 - коэффициент учитывающий материал инструмента;
=770 МПа-предел текучести для данного материала;
2) =
= 1306 об/мин-число оборотов шпинделя;
где:
=8,2 м/мин – скорость резания;
D=2 мм-диаметр фрезы;
=3,14-постоянная;
Принимаем n= 1000 об/мин-число оборотов шпинделя;
3) =
= 6,28 м/мин- действительная скорость резания;
где:
=3,14-постоянная;
D=14,2 мм-диаметр, получаемый при точении;
n=1000 об/мин-число оборотов шпинделя;
-тангенальная
составляющая сила;
где:
=12,5-поправочный коэффициент;
x=0,85, y=0,75, n=1, q=0,73, w=-0,13-покатели степени;
В=2 мм-ширина шпоночного паза;
z=2-количество зубьев фрезы;
D=2 мм-диаметр фрезы;
n=1000 об/мин-число оборотов шпинделя;
=1,0-поправочный коэффициент;
Px:Pz=0,5:0,55 соотношение составляющих сил;
4) =
= 0,007 кВт - мощность резания (эффективная);
где:
Pz=71,5 H-тангенциальная составляющая сила;
Px=78,65 H- осевая составляющая сила;
=6,28 м/мин- действительная скорость резания;
5) -крутящий момент;
где:
Pz=71,5 H-тангенциальная составляющая сила;
D=2 мм-диаметр фрезы;
6) =
=0,008 кВт - мощность двигателя;
Изм. |
Лист |
№ докум. |
Подпись |
Дата |
Лист |
29 12 1 |
ТМК.17.01.09 ПЗ |
КПД ( =0,85) должно согласовываться с условием
-условие
выполняется;
7) мм/мин-минутная подача;
где:
=0,1-подача на 1зуб фрезы;
z=2,0-количество зубьев;
n= 1000 об/мин-число оборотов шпинделя;
8) мин-основное машинное время для
шпоночного паза ;
где:
h =t=1,1 мм-глубина шпоночного паза;
=1 мм/мин –вертикальная подача;
=200 мм/мин-минутная подача;
l =6-длина шпоночного паза;
D=2 мм-диаметр фрезы;
мин-основное машинное время для
шпоночного паза ;
где:
h =t=1,1 мм-глубина шпоночного паза;
=1 мм/мин –вертикальная подача;
=200 мм/мин-минутная подача;
l =13-длина шпоночного паза;
D=2 мм-диаметр фрезы;
Изм. |
Лист |
№ докум. |
Подпись |
Дата |
Лист |
30 12 1 |
ТМК.17.01.09 ПЗ |
То2 | То3 | То4 | То5 | То6 | То8 | То9 | То10 | То11 | То12 | То13 | То14 | То15 |
0,07 | 0,14 | 0,007 | 0,065 | 1,6+1,65=3,25 | 0,02 | 0,04 | 0,2 | 0,01 | 0,2 | 0,01 | 0,5 | 0,02 |
То= То2+То3+То4+То5+То6+То8+То9+То10+То11+То12+То13+То14+То15=4,5мин -общее
основное машинное время на операцию.
Изм.
Лист
№ докум.
Подпись
Дата
Лист
31
12
1
2.10 Нормирование операций ТМК.17.01.09 ПЗ
Нормирование на операцию 010 Токарная
=
+
+
- мин, штучного времени;
- мин, основное машинное время;
=
- мин, сумма ручного вспомогательного времени;
- мин, время на установку и снятия детали;
- мин, время на закрепление и открепление детали;
- мин, время на приемы управления;
- мин, время на измерения детали;
- мин, общее время на обслуживание рабочего места и отдыха;
- мин, время на обслуживание рабочего места;
- мин, время перерывов на отдых и личные надобности;
=
+
-мин, оперативное время.
Таблица 16 – Расчет ручного вспомогательного времени на операцию 010, мин
Элементы времени | 1 переход | 2 переход | 3 переход | 4 переход | 5 переход |
1. Временя на УЗС | 0,015 | 0,015 | |||
2. Время на приемы управления станком | |||||
2.1 Вкл./Выкл. станок | 0,01 ![]() | ||||
2.2 Время подвода и отвода инструмента к детали при обработке | 0,025×2=0,05 | 0,025×2=0,05 | |||
3. Время на приемы управления станком, связанные с перемещением рабочих органов станка | 0,04 | 0,04 | |||
4. Время на измерения | |||||
4.1 Штангенциркуль ШЦ-1-125-0,1 ГОСТ 166-89 | 0,18 | ||||
Итого | 0,015 | 0,11 | 0,015 | 0,09 | 0,18 |
С учетом коэффициента серийности К=1,85 | 0,027 | 0,2 | 0,027 | 0,2 | 0,33 |
Изм. |
Лист |
№ докум. |
Подпись |
Дата |
Лист |
32 12 1 |
ТМК.17.01.09 ПЗ |


машинное время;
=
+
=0,5+0,78=1,28 мин, оперативное время;
=
=
=0,089 мин, общее время на отдых и личные надобности;
где:
-7%
=
+
+
=0,5+0,78+0,089=1,369 мин, штучное время;
Расчет подготовительно-заключительного времени
=12 мин, время на наладку станка, инструмента и приспособлений;
=4 мин, время на получение инструмента и приспособлений до начала и
сдача после обработки;
=
+
=12+4=16 мин, общее время подготовительно-заключительного
времени.
Нормирование на операцию 030 Токарно-револьверная с ЧПУ
мин,штучное время;
где:
- мин, время автоматического работы станка по программе;
- мин, основное машинное время;
- мин, поправочный коэффициент на время, связанное с операцией
(невошедшее в управляющую программу)
,
,
-6 % от оперативного времени, время на техническое и
организационное обслуживание рабочего места, на отдых и личные потребности
при одностороннем обслуживании;
=
+
- мин;
где:
-мин, основное машинное время;
- мин. машинно-вспомогательное время по программе ( на подвод детали или
инструмента от исходных точек в зоны обработки и отвод, установку инструмента
на размер, смену инструмента, изменение величины и направление подачи , время
технических пауз, остановок);
=
+
+
где:
-мин, время на установку и снятие детали вручную;
-мин, вспомогательное время, связанное с операцией (не вошедшее в
управляющую программу;
-мин, вспомогательное неперекрываемое время на измерения.
Изм. |
Лист |
№ докум. |
Подпись |
Дата |
Лист |
33 12 1 |
ТМК.17.01.09 ПЗ |
Элементы времени | 2 переход | 3 переход | 4 переход | 5 переход | 6 переход | 7 переход |
Время холостого хода | 0,09 | 0,09 | 0,082 | 0,082 | 0,088 | 0,07 |
Время на смену инструмента | 0,07 | 0,07 | 0,07 | 0,07 | 0,07 | - |
Время изменения подачи | - | 0,07 | 0,07 | - | 0,07 | - |
Время изменения скорости | - | 0,07 | 0,07 | - | 0,07 | 0,07 |
ИТОГО | 0,16 | 0,3 | 0,292 | 0,152 | 0,298 | 0,14 |
продолжение таблицы 17
Элементы времени | 8 переход | 9 переход | 11 переход | 12 переход | 13 переход | 14 переход |
Время холостого хода | 0,088 | 0,088 | 0,088 | 0,087 | 0,087 | 0,081 |
Время на смену инструмента | 0,07 | 0,07 | - | 0,07 | 0,07 | 0,07 |
Время изменения подачи | 0,07 | 0,07 | 0,07 | 0,07 | 0,07 | 0,07 |
Время изменения скорости | 0,07 | 0,07 | 0,07 | 0,07 | 0,07 | 0,07 |
ИТОГО | 0,298 | 0,298 | 0,228 | 0,297 | 0,297 | 0,291 |
Изм. |
Лист |
№ докум. |
Подпись |
Дата |
Лист |
34 12 1 |
ТМК.17.01.09 ПЗ |
Элементы времени | 14 переход | 15 переход |
Время холостого хода | 0,083 | 0,062 |
Время на смену инструмента | 0,07 | 0,07 |
Время изменения подачи | - | 0,07 |
Время изменения скорости | - | 0,07 |
ИТОГО | 0,153 | 0,272 |
=
+
+
+
+
+
+
+
+
+
+
+
+
+
=0,16+0,3+0,292+0,152+0,298+0,14+0,298+0,298+0,228+0,297+0,297+0,291+0,153+0,272=3,476 мин, общее машинно-вспомогательное время;
Таблица 18 – Расчет ручного вспомогательного времени на операцию 030, мин
Элементы времени | 1 переход | 16 переход |
1. Время на УЗС | 0,37 | |
2.Вспомогательное время на управление станком | ||
2.1. Установить заданное взаимное положение детали и инструмента по X, Y, Z и в случае необходимости произвести подналадку | 0,32 | |
2.2. Проверить приход детали или инструмента в заданную точку после обработки | 0,15 |
Изм. |
Лист |
№ докум. |
Подпись |
Дата |
Лист |
35 12 1 |
ТМК.17.01.09 ПЗ |
2.3. Установить и снять щиток от забрызгивания эмульсией | 0,03 | |
3. Время на измерения: | ||
Штангенциркуль ШЦ-1-125-0,01 ГОСТ 166-89 | 0,23 | |
Калибр-скоба Ø12f7 8118-0003 ГОСТ 2216-84 | 0,13 | |
Калибр-скоба Ø14f7 8118-0003 ГОСТ 2216-84 | 0,12 | |
Калибр-скоба Ø11h8 8118-0003 ГОСТ 2216-84 | 0,09 | |
Калибр-кольцо М12×1,5-6e ГОСТ 24997-81 | 0,19 | |
Радиусный шаблон | 0,11 | |
Радиусный шаблон (R2,35) | 0,06 | |
Микрометр МК 25 ГОСТ 6507-90 | 0,12 | |
Биениемер Б-10М Индикатор ИЧ-10 | 0,08 | |
ПБМ-200 Штатив ШМ-2 Микатор ИРПВ | 0,08 | |
ИТОГО | 0,87 | 1,21 |
=
+
+
=0,87+1,21=2,08 мин, общее вспомогательное время;
=
+
=4,5+3,3=7,8 мин, время автоматического работы станка
по программе;
где:
То=4,5 мин, основное машинное время;
=3,476,мин-машинно-вспомогательное время;
=
-количество деталей в партии;
где:
D – количество деталей по годовой программе вместе с запасными
частями (4500);
t – число дней, на которое необходимо иметь запас деталей на складе (6 дней);
Ф – число рабочих дней в году;
=0,93- мин, поправочный коэффициент на время, связанное с операцией
(невошедшее в управляющую программу);
=
-штучно время.
Таблица 19 – Расчет подготовительно-заключительного времени на операцию 030, мин
Элементы времени | Тпз |
1 На организационные подготовки: 1.1 Получить наряд чертежей, технологическую документацию. 1.2 Получить инструмент и сдать его после работы. 1.3 Ознакомиться с работой, чертежами и документацией. 1.4 Инструктаж мастера. | 4 9 2 2 |
2 На наладку станка, приспособлений, инструмента, программных устройств . 2.1 Установить, снять приспособление. 2.2 Установить рабочие режимы станка. 2.3 Установить и снять инструментальный блок или отдельный режущий инструмент. | 2,5 0,15 |
2.4 Набрать программу кнопками на пульте управления устройства ЧПУ и проверить ее. 2.5 Установить исходные координаты x и z. | 0,4 2 |
3 СОЖ. | 0,2 |
4 Время на установку пробного прохода поправочного коэффициента. 4.1 Поправочный коэффициент на пробный проход детали. | 9,8 1,15 |
Итого: | 35,7 |
Изм.
Лист
№ докум.
Подпись
Дата
Лист
36
12
1
2.11 Расчет управляющей программы на станок с ЧПУ ТМК.17.01.09 ПЗ
030 Токарно-револьверная с ЧПУ
Первый контрур (подпрограмма)
N5 G1 X10.3 Z0
N10 Z-1
N15 X11.95 Z-1.85
N20 Z-14
N25 X11.975
N30 Z-62
N35 X13.785
N40 Z-74
N45 X18.74 CHF=0.5
N50 Z-75.5
N55 X21
N60 M17
Программа
N5 T1 D1 M6
N10 S500 M3
N15 G0 X25 Z1 M8
N20 LIMS=1500
N25 G96 S75
N30 G1 X21 F0.3
N35 CYCLE95("kontyr",2,0.2,0.8,0,0.4,0.2,0.25,1,0,0,0)
N40 G97
N45 G0 X100 Z0 M9
N50 T2 D1 M6
N55 S800 M3
N60 G0 X14 Z1 M8
N65 G96 S90
N70 CYCLE95("kontyr",2,0.2,0.8,0,0.4,0.2,0.25,5,0,0,0)
N75 G97
N80 G0 X100 Z0 M9
N85 T3 D1 M6
N90 S400 M3
N95 G0 X14 Z3
N100 CYCLE97(1.5,0,-1,-14,12,12,3,0,0.92,0,30,0,8,1,3,1,0)
N105 G0 X100 Z0 M9
N110 M30
Изм.
Лист
№ докум.
Подпись
Дата
Лист
37
1
3 Конструкторская часть ТМК.17.01.09 ПЗ
Дата добавления: 2021-02-10; просмотров: 316; Мы поможем в написании вашей работы! |
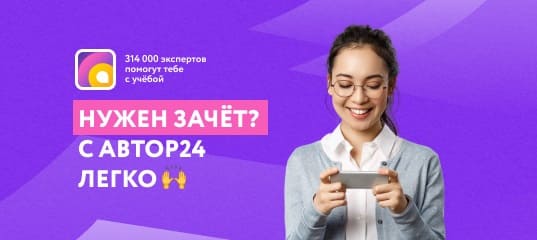
Мы поможем в написании ваших работ!