Основные механические свойства материалов.
Свойства материалов, которые выявляются испытаниями при воздействии внешних нагрузок, называются механическими. Знание количественных характеристик механических свойств необходимо для выбора материалов и режимов их технологической обработки, расчетов на прочность деталей и конструкций, контроля и диагностики их прочностного состояния в процессе изготовления и эксплуатации.
При проведении механических испытаний стремятся воспроизвести такие условия воздействия на материал, которые имеют место при эксплуатации изделия, изготовленного из этого материала. Очевидно, что многообразие условий службы материалов обусловливает проведение большого числа механических испытаний. Тем не менее, основными признаками, позволяющими классифицировать виды механических испытаний, являются:
· способ нагружения (растяжение, сжатие, изгиб, кручение, срез, циклическое нагружение и др.);
· скорость нагружения (статическая, динамическая);
· протяженность процесса испытания во времени (кратковременная, длительная).
Существуют и другие признаки классификации, которые характеризуются сложностью напряженно-деформированного состояния, режимами нагружения, типами образцов, агрессивностью среды.
В результате механических испытаний материалов определяют следующие их характеристики: упругость, пластичность, прочность, твердость, вязкость, усталость, трещиностойкость, хладостойкость, жаропрочность.
|
|
При испытаниях на растяжение определяют:
· Модуль нормальной упругости E(МПа), модуль сдвига G(МПа) и коэффициент Пуассона μ, известные из курса общей физики для случая упругой деформации.
· Показатели прочности и пластичности. Показатели прочности материалов характеризуются удельной величиной – отношением напряжения к площади поперечного сечения образца. Под напряжением понимается нагрузка в характерных точках диаграммы растяжения (в координатах нагрузка – абсолютное удлинение образца).
Прочность - способность тела сопротивляться деформациям и разрушению. Удельная прочность - отношением характеристик прочности к плотности материала.
Наиболее часто используемыми показателями прочности являются:
o Предел текучести σт (МПа)=Рт/F0, где Рт – нагрузка, соответствующая площадке текучести на диаграмме растяжения, F0 –площадь поперечного сечения испытуемого образца. Предел текучести характеризует наименьшее напряжение, при котором материал деформируется (течет) без заметного изменения нагрузки. Если на диаграмме растяжения нет площадки текучести, то задаются допуском на остаточную деформацию образца и определяют условный предел текучести.
|
|
o Условный предел текучести σ02(МПа) = Р02/F0, где Р02 — нагрузка, соответствующая остаточному удлинению, равному 0,002. Условный предел текучести характеризует напряжение, при котором остаточное удлинение достигает 0,2% от начальной расчетной длины образца.
o Временное сопротивление (предел прочности) σв (МПа) = Pmax/F0. Это напряжение, соответствующее наибольшей нагрузке Рmax , предшествующей разрыву образца.
o Истинное сопротивление разрыву Sк (МПа) = Рк/Fк. Это напряжение, определяемое отношением нагрузки в момент разрыва Рк к площади поперечного сечения образца в месте разрыва Fк.
Пластичность – способность материала сохранять остаточные деформации, не разрушаясь. Пластичность – одно из важных механических свойств металла, которое в сочетании с высокой прочностью делает его основным конструкционным материалом.
Наиболее часто используемыми показателями пластичности материалов являются:
- Относительное предельное равномерное удлинение:
δр(%) = (Δlp/l0)100 = [(lр-l0)/l0]100— это наибольшее удлинение, до которого образец деформируется равномерно по всей его расчетной длине.
- Относительное предельное равномерное сужение:
ψp(%)= (ΔFp/F0)100 = [(Fр-F0)/F0]100,
|
|
где Fp = πdp2/4 - площадь поперечного сечения образца, соответствующая Pmax . Из условия постоянства объема образца при растяжении можно получить соотношение: ψp=δр/(1+δр).
Свойство материала оказывать сопротивление контактной деформации или хрупкому разрушению при внедрении твердосплавного наконечника (индентора) в его поверхность называется твердостью.
Испытания на твердость — самый доступный и распространенный вид механических испытаний. Наибольшее применение в технике получили статические методы испытания на твердость при вдавливании индентора: методы Бринелля, Виккерса и Роквелла (Рис. 1.14).
Рис. 1.14. Схемы испытаний на твердость по Бринеллю (а); Виккерсу (б); Роквеллу (в).
При испытании на твердость по методу Бринелля (ГОСТ 9012 - 59) в поверхность материала вдавливается твердосплавный шарик диаметром D под действием нагрузки Р и после снятия нагрузки измеряется диаметр отпечатка d (рис.1.14, а). Число твердости по Бринеллю (НВ) в кгс/мм2 подсчитывается как отношение нагрузки Р к площади поверхности сферического отпечатка М.
Для получения сопоставимых результатов при определении твердости НВ шариками различного диаметра необходимо соблюдать условие подобия. В результате:
|
|
Чем более твердый материал, тем рекомендуется большее отношение P/D2. Исходя из этого в ГОСТ 9012 - 59 приведены следующие значения отношений P/D2 (МПа): 294 (сталь, чугун, высокопрочные сплавы); 98 (алюминий, медь, никель и их сплавы); 49 (магний и его сплавы); 24,5 (подшипниковые сплавы); 9,8 (олово, свинец). При D =10 мм, P=29400 Н (P/D2 = 294 МПа) и времени выдержки под нагрузкой 10с. твердость по Бринеллю обозначается символом НВ с указанием числа твердости. При этом размерность (кгс/мм2) не ставится, например 200 НВ. При использовании шариков других диаметров (1, 2, 2,5 и 5мм) изменяется нагрузка вдавливания, а символ твердости НВ дополняется тремя индексами. Например, 180 НВ2,5/187,5/30 обозначает, что при D = 2,5мм, P=187,5 кгс (1839 Н) и времени выдержки под нагрузкой 30с. число твердости по Бринеллю равно 180.
Метод Бринелля не рекомендуется применять для материалов с твердостью более 450 НВ, так как стальной шарик может заметно деформироваться.
При испытании на твердость по методу Виккерса (ГОСТ 2999 - 75) в поверхность материала вдавливается алмазная четырехгранная пирамида с углом при вершине φ = 136°(рис. 1.14, б). После снятия нагрузки вдавливания измеряется диагональ отпечатка d1. Число твердости по Виккерсу HV подсчитывается как отношение нагрузки Р к площади поверхности пирамидального отпечатка М:
Число твердости по Виккерсу обозначается символом HV с указанием нагрузки P и времени выдержки под нагрузкой, причем размерность числа твердости (кгс/мм2) не ставится. Продолжительность выдержки индентора под нагрузкой принимают для сталей 10—15 с, а для цветных металлов — 30 с. Например, 450 HV10/15 означает, что число твердости по Виккерсу 450 получено при Р =10 кгс (98,1 Н), приложенной к алмазной пирамиде в течение 15 с.
В результате применения алмазной пирамиды методом Виккерса можно испытывать материалы более высокой твердости, чем методом Бринелля.
При испытании на твердость по методу Роквелла (ГОСТ 9013 - 59) в поверхность материала вдавливается алмазный конус с углом при вершине 120° или стальной шарик диаметром 1,588мм (рис. 1.14, в). Однако здесь за условную меру твердости принимается глубина отпечатка. Вначале прикладывается предварительная нагрузка Р0, под действием которой индентор вдавливается на глубину h0. Затем прикладывается основная нагрузка Р1, под действием которой индентор вдавливается на глубину h1. После этого снимают нагрузку P1, но оставляют предварительную нагрузку Р0. При этом под действием упругой деформации индентор поднимается вверх, но не достигает уровня h0. Разность (h – h0) зависит от твердости материала; чем тверже материал, тем меньше эта разность. Глубина отпечатка измеряется индикатором часового типа с ценой деления 0,002мм. При испытании мягких металлов методом Роквелла в качестве индентора применяется стальной шарик. Последовательность операций такая же, как и при испытании, алмазным конусом. Число твердости, определенное методом Роквелла, обозначается символом HR. Однако в зависимости от формы индентора и значений нагрузок вдавливания к этому символу добавляется буква A, С или В, обозначающая соответствующую шкалу измерений. Обозначения твердости и значения нагрузок вдавливания для разных шкал измерений методом Роквелла приведены ниже.
Шкала ............. А С В Индентор ...................... Алмазный конус Алмазный конус Стальной шарик Обозначение твердости HRA HRC HRB Нагрузки вдавливания, кгс(Н): Р0 10(98,1) 10(98,1) 10(98,1) P 1 50(490,5) 140(1373,4) 90(882,9) Р 60(588,6) 150(1471,5) 100(981) |
Различие в нагрузке Р1 для шкал А и С объясняется тем, что по шкале А измеряют твердость особо твердых материалов и в этом случае во избежание повреждений алмазного конуса рекомендуется меньшая нагрузка вдавливания.
Числа твердости по Роквеллу подсчитывают по формулам:
HRA(HRC) = 100 - [(h – h0 / 0,002]; HRB = 130 - [(h – h0) / 0,002],
где 100 и 130 — предельно заданное число делений индикатора часового типа с ценой деления 0,002мм. Например, 50 HRC означает, что твердость, определенная методом Роквелла по шкале С при вдавливании алмазного конуса, равна 50 (размерность не ставится).
Значение твердости по методу Роквелла фиксируется непосредственно стрелкой индикатора. При этом отпадает необходимость в оптическом измерении размеров отпечатка. В этом заключается преимущество метода Роквелла по сравнению с методами Бринелля и Виккерса.
Для измерения твердости тонких слоев материалов и даже их отдельных структурных составляющих применяют метод микротвердости ГОСТ (9450 - 76). Этот метод аналогичен методу Виккерса, но при этом используют малые нагрузки вдавливания в интервале от 0,049Н (0,005 кгс) до 4,9Н (0,5 кгс).
Текучесть. Текучесть – свойство пластических металлов и сплавов при постоянном увеличении давления уступать действию сдвигающих сил и течь подобно вязким жидкостям. Для конструкционных материалов текучесть является нежелательным свойством. Например, крыло самолёта постоянно находится под механической нагрузкой. Если сплав, из которого изготовлено крыло, поддастся постоянным механическим нагрузкам и начнет изменять свою форму, то может возникнуть аварийная ситуация. Конструкторам в расчётах приходится закладывать необходимые толщины изделий. Среди металлов наименьшей текучестью характеризуется титан, что в сочетании с другими его свойствами определяет применение титана в авиации.
Трещиностойкость. Свойство материалов сопротивляться развитию трещин при механических и других воздействиях называют трещиностойкостью. Трещины в материалах могут быть металлургического и технологического происхождения, а также возникать и развиваться в процессе эксплуатации.
Количественной характеристикой трещиностойкости материала является критический коэффициент интенсивности напряжений в условиях плоской деформации (развивающейся в одной плоскости и запрещенной по толщине образца) в вершине трещины KIc. На практике KIc используют для определения связи между разрушающими напряжениями и размерами дефектов в элементе конструкции. Определяют KIc испытанием специальных образцов с предварительно выращенной усталостной трещиной (ГОСТ 25506 - 85).
Для оценки склонности материалов к хрупкому разрушению определяют ударную вязкость. Из самого этого названия (ударная) следует, что данное механическое свойство можно определить при динамическом нагружении. Для этого проводят испытания на ударный изгиб образцов с надрезом специальной формы. Согласно ГОСТ 9454 - 78, для определения ударной вязкости применяют призматические образцы с надрезами различных типов (обычно с U-образным и V-образным надрезами).
Ударная вязкость оценивается отношением работы, затраченной на ударный излом образца к площади его поперечного сечения в месте надреза и обозначается символом КС, МДж/м2. Если образец с U-образным надрезом, то к символу добавляется буква U (KCU), а если с V-образным надрезом, то добавляется буква V (KCV).
Вместе с тем ударная вязкость является сложной механической характеристикой и состоит из двух составляющих: удельной работы зарождения трещины КСз и удельной работы ее распространения КСр, т. е.
КС = КСз + КСр.
Для охрупченных материалов основная часть работы идет на зарождение трещины, а работа распространения трещины незначительна. Для пластичных материалов работа распространения трещины имеет преобладающее значение. Анализ составляющих ударной вязкости позволяет более рационально выбрать материал и определить его назначение.
Существует несколько методов определения составляющих ударной вязкости. Наиболее широкое распространение получили методы Б. А. Дроздовского и А. П. Гуляева, дающие достаточно близкие значения составляющих ударной вязкости.
При динамическом нагружении определяют хладноломкость и критическую температуру хрупкости. Хладноломкостью называют способность некоторых металлов охрупчиваться при низких температурах. К хладноломким металлам можно отнести металлы с ОЦК решеткой, например α-Fe, и гексагональной, например Zn. Для этой группы металлов при определенной минусовой температуре наблюдается резкое снижение ударной вязкости. К нехладноломким металлам можно отнести металлы с ГЦК решеткой, например γ-Fe, A1, Ni.
Деление металлов на хладноломкие и нехладноломкие является условным. Например, аустенитные стали, имеющие ГЦК решетку тоже подвержены охрупчиванию, но только в меньшей степени и при более низких температурах, чем углеродистые и низколегированные стали, имеющие ОЦК решетку. Испытания на ударную вязкость при низких температурах позволяют получить хрупкое разрушение металла в результате одновременного действия надреза, повышенной скорости деформирования и температуры.
Характер падения ударной вязкости в координатах «КС – температура» напоминает порог, что привело к выражению «порог хладноломкости». Температура, при которой происходит определенное падение ударной вязкости, называется критической температурой хрупкости Ткр. Количественно ее можно определить по температуре, соответствующей началу порога хладноломкости, концу порога хладноломкости или по заданному значению ударной вязкости КС2.
Критическую температуру хрупкости можно определить и другим способом по характеру строения излома. Вязкий излом имеет волокнистое, а хрупкий излом кристаллическое строение. При переходе из вязкого состояния в хрупкое состояние доля волокнистого строения в изломе уменьшается, а кристаллического увеличивается. Изменение доли волокнистого строения при температурах хладноломкости также имеет вид порога. За критическую температуру хрупкости принимают температуру, соответствующую равным долям волокнистого и кристаллического изломов.
Хладноломкость является одной из технически значимых характеристик материалов. Более 40 % территории России находится в зоне северных широт с температурами в зимний период до минус 40 – 50 градусов. Материалы конструкций и машин должны обеспечивать их работоспособность в условиях эксплуатации.
При циклическом нагружении механизмов и конструкций определяют такое механическое материалов как усталость. Усталостью называют процесс постепенного накопления повреждений, в материале приводящий к образованию трещин и разрушению при действии циклических нагрузок.
Хорошо известно, что большинство разрушений деталей и конструкций при эксплуатации происходит в результате именно циклического нагружения. Металл, подверженный такому нагружению, может разрушаться при более низких напряжениях, чем при однократном плавном нагружении.
Свойство материалов противостоять усталости называют выносливостью. Количественно сопротивление усталости характеризуется пределом выносливости, под которым понимают максимальное напряжение, которое не вызывает разрушения образца при любом числе циклов (физический предел выносливости) или заданном числе циклов (ограниченный предел выносливости). Предел выносливости при симметричном цикле обозначается σ-1.
Методика проведения испытаний материалов на усталость регламентирована ГОСТ 25.502 - 79.
Разрушение материалов при усталости отличается от разрушения при однократных нагрузках. Оно характеризуется отсутствием в изломе внешних признаков пластической деформации, т. е. в целом усталостный излом имеет характер хрупкого излома. На процесс разрушения при циклических нагрузках существенное влияние оказывают концентраторы напряжений. Концентраторы напряжений могут быть конструктивными (резкие переходы от сечения к сечению), технологическими (царапины, трещины, риски от резца), металлургическими (поры, раковины, неметаллические включения). Независимо от своего происхождения концентраторы напряжений в той или иной степени снижают предел выносливости при одном и том же уровне переменных напряжений. Для количественной оценки влияния концентратора напряжений на усталость используют эффективный коэффициент концентрации напряжений:
Кσ= σ-1/ σ-1н,
где σ-1 -предел выносливости, определенный на гладких образцах;
σ-1н – предел выносливости, определенный на надрезанных в виде острой круговой выточки образцах. σ-1 и σ-1н определяют при симметричном цикле напряжений.
В последнее время все большее применение получил так называемый безобразцовый метод определения механических свойств.
Этот метод основан на инденторных испытаниях материалов, в результате которых определяют специальные характеристики твердости и пересчитывают их на показатели других механических свойств. Исходная информация для оценки механических свойств металла безобразцовым методом содержится в диаграмме вдавливания индентора. Диаграмма вдавливания может быть представлена в координатах нагрузка вдавливания — геометрический параметр отпечатка (первичная диаграмма) или в координатах контактное напряжение — контактная деформация. Геометрическим параметром отпечатка может являться его диаметр или глубина. Главное достоинство метода заключается в возможности ускоренной оценки механических характеристик металла готовых изделий, не выводя их из строя и не вырезая из них образцов. Безобразцовый метод, как более экономичный и простой, представляет большой научный и практический интерес в области исследования, контроля и диагностики качества металла. В некоторых случаях безобразцовый метод является пока единственно пригодным для оценки механических свойств малых объемов или локальных зон обработанного металла (упрочненный слой, сварные соединения и др.). Этот метод особенно эффективен при оценке остаточного ресурса оборудования, пробывшего длительное время в эксплуатации и выработавшего свой расчетный срок службы.
Резюме.
Материаловедение— наука, изучающая связь между составом, структурой и свойствами материалов, а также изменением свойств материалов при внешних воздействиях. Для создания материалов может быть использовано 86 химических элементов Периодической системы. Научной основой создания материалов на основе нескольких химических элементов являются диаграммы состояния соответствующих двух, трёх, четырёх и более многокомпонентных систем. Реально человечество использует приблизительно 65 000 материалов.
По назначениютехнические материалы делят на следующие группы: конструкционные, электротехнические, инструментальные, рабочие тела, топливо, технологические материалы.
Кристаллами называют твердые тела, обладающие упорядоченной трехмерно-периодической пространственной атомной структурой и имеющие вследствие этого при определенных условиях образования форму многогранника.
Элементарная ячейка является частью структуры кристалла, путем её переноса (трансляции) в пространстве параллельно самой себе, можно построить всю кристаллическую решетку. По признаку точечной симметрии элементарной ячейки все кристаллические структуры группируются в семь сингоний.
В реальной кристаллической структуре имеются точечные и объемные дефекты. К точечным дефектам (I рода) относятся дефекты атом в междоузлье, вакансия в положении атома, катион, занимающий кристаллографическую позицию аниона и наоборот. В объемных дефектах (II рода) участвуют тысячи атомов. К ним относятся винтовая дислокация, краевая дислокация, внутренняя пустота.
Физико-химический анализ (ФХА) - учение на стыке нескольких естественных наук, целью которого является изучение зависимостей состав – свойство при непрерывном изменении состава.
Сплавы металлов создают для формирования у материалов необходимого комплекса свойств. В металлических сплавах имеется два основных типа твёрдых растворов: замещения и внедрения.
Вещества с кристаллической структурой характеризуются зёренной структурой. Химические соединения, твёрдые растворы образованы из однородных зёрен. Сплавы могут состоять из зёрен нескольких фаз. В двухфазных областях кристаллы фаз взаимно располагаются по эвтектической смеси кристаллов фаз, либо по типу перитектики.
Свойства материалов, которые выявляются испытаниями при воздействии внешних нагрузок, называются механическими. Знание количественных характеристик механических свойств необходимо для выбора материалов и режимов их технологической обработки, расчетов на прочность деталей и конструкций. В результате механических испытаний материалов определяют следующие их характеристики: упругость, пластичность, прочность, твердость, вязкость, усталость, трещиностойкость, хладостойкость, жаропрочность.
Вопросы для самопроверки.
1. Как можно кратко сформулировать цель материаловедения?
2. По каким признакам рассматриваемый объект следует отнести к сырью или материалу?
3. В чём отличие первичного сырья от полуфабрикатов?
4. Почему из 110 элементов Периодической системы для создания материалов используется только 86 элементов?
5. Сколько материалов известно в настоящее время и сколько материалов используется человечеством в практической деятельности?
6. Какие основные требования предъявляются к конструкционным материалам?
7. Для каких целей используются триботехнические материалы?
8. Какие материалы входят в номенклатуру инструментальных материалов?
9. В виду, каких свойств ртути её применяют в качестве рабочего тела? В каких устройствах применяется ртуть?
10. Для каких целей используются электротехнические материалы?
11. Назовите технологические материалы, используемые при эксплуатации автотранспорта?
12. Какие основные химические элементы содержатся в топливе?
13. Назовите основные характеристики агрегатных состояний веществ?
14. Чем характеризуется кристаллическая структура вещества?
15. Дайте определение элементарной ячейки?
16. Сколько видов элементарных ячеек известно, в чём их сходства и различия?
17. Какие виды элементарных ячеек характерны для металлов? Какие координационные числа имеют атомы металлов в гранецентрированной и объемно-центрированной элементарных ячейках? Как обозначаются данные кристаллические структуры?
18. Какое число атомов содержится в гексагональной элементарной ячейке?
19. Приведите примеры полиморфных переходов у металлов и сплавов. Какими структурными преобразованиями они вызваны?
20. В чём причина проявления анизотропии кристаллов? Для какого состояния материала анизотропия имеет максимальное значение?
21. В чём причина возникновения в материале точечных дефектов? По каким механизмам возникают дефекты Френкеля и Шоттки?
22. Как образуется винтовая дислокация, и какое количество атомов участвует в её образовании?
23. В чём схожесть и различие краевой и винтовой дислокаций?
24. Какие размеры имеют зёрна и субзёрна и как они относительно друг друга расположены в кристаллах?
25. В каких областях зернистой структуры металлов формируются поверхностные дефекты?
26. Как соотносятся энергии атомов, находящихся в слое поверхностного дефекта во внутренней области зерна в междоузельном пространстве?
27. Что представляется на диаграмме состояния системы?
28. Какими основными методами осуществляется построение фазовых диаграмм?
29. Чем первичные кристаллы отличаются от эвтектических?
30. Охарактеризуйте поля фазовых равновесий в системе Pb – Sb?
31. Зачем создают сплавы металлов?
32. При каких размерных соотношениях атомов образуются твёрдые растворы внедрения?
33. Почему непрерывные твёрдые растворы между двумя компонентами образуются только при соблюдении нескольких условий?
34. Какие отличительные признаки характерны для химических соединений?
35. Как относительно друг друга располагаются зёрна фаз в двухфазных областях, в которых образуется эвтектика и перитектика?
36. Какие механические характеристики определяют у материалов?
37. Какое свойство материала называется твёрдостью?
38. Какими методами определяют твёрдость?
39. Почему у материалов необходимо формировать такое свойство как трещиностойкость?
40. У каких материалов необходимо определять такое свойство как хладноломкость?
41. Почему на Крайнем севере в зимние месяцы существует такое понятие как актированные дни, в которые работа с техникой на открытом воздухе не проводится?
Глава 2. Стали.
Стали – основной материал
машиностроения, конструкционный материалв строительстве.
Цели и задачи изучения темы.
Цель состоит в формировании представлений о составе структуре и свойствах сталей, их классификации, маркировки, областях примене6ния.
Задачи:
Дата добавления: 2019-02-22; просмотров: 4195; Мы поможем в написании вашей работы! |
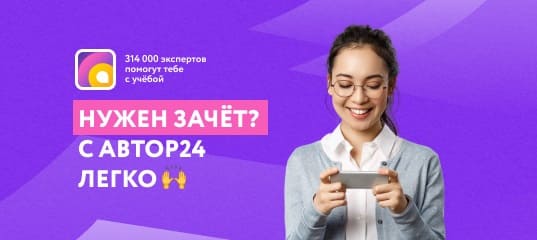
Мы поможем в написании ваших работ!